MAZDA PROTEGE 1992 Owners Manual
Manufacturer: MAZDA, Model Year: 1992, Model line: PROTEGE, Model: MAZDA PROTEGE 1992Pages: 1164, PDF Size: 81.9 MB
Page 91 of 1164
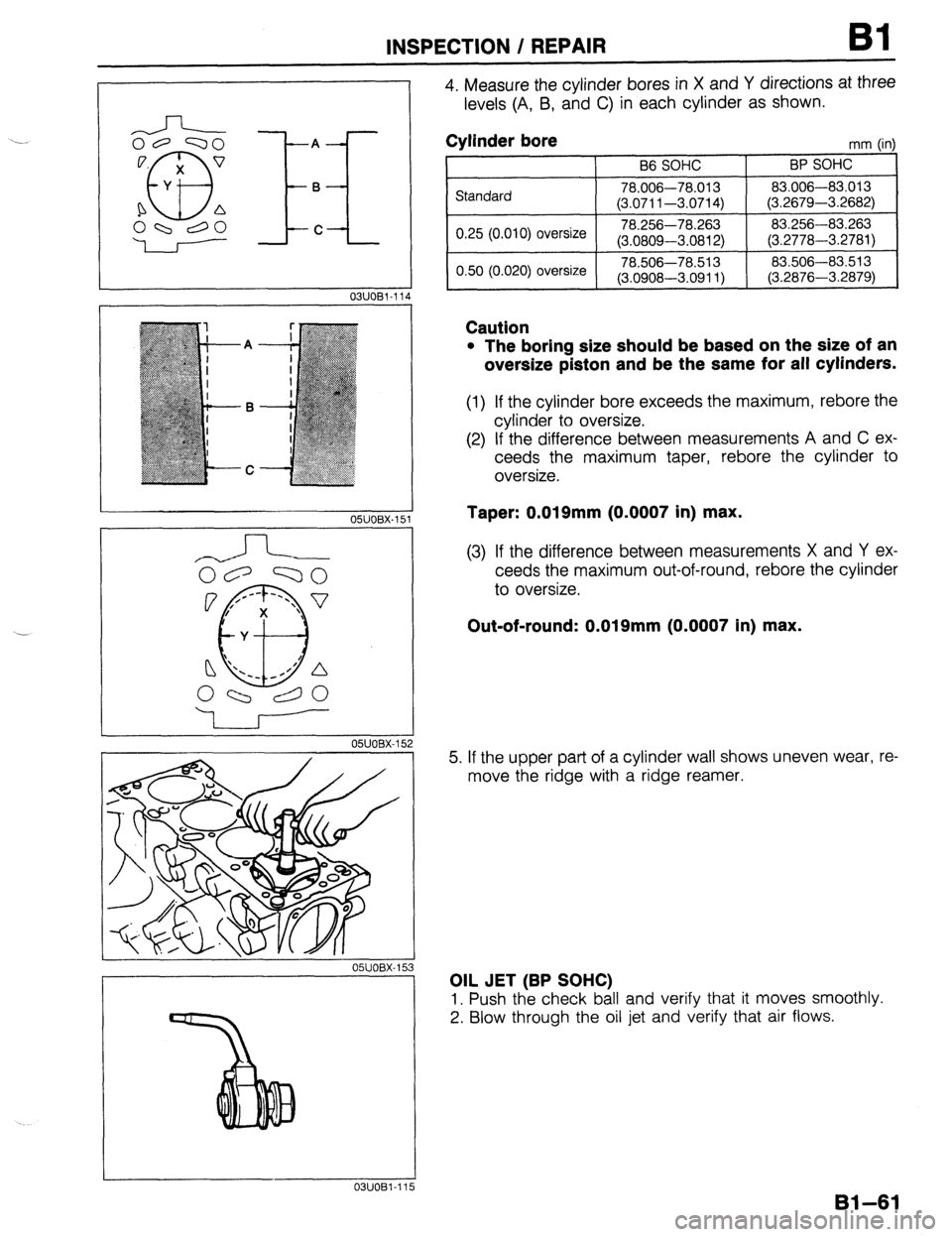
INSPECTION / REPAIR Bl
.-J-
03UOBl-11
05UOBX-1:
OWOBX-15 4
il
2
3
_I
5
OWOBX-15:
03UOBl-11:
4. Measure the cylinder bores in X and Y directions at three
levels (A, B, and C) in each cylinder as shown.
Cylinder bore mm h-d
I I B6 SOHC I BP SOHC ’ ‘I
,r jtanciard 1 78.006-78.013 1 83.006-83.013
(3.0711-3.0714) (3.2679-3.2682)
0.25 (0.010) oversize 78.256-78.263 83.256-83.263
(3.0809-3.0812) (3.2778-3.2781)
I 0.50 (0.020) oversize 78.506-78.513 83.506-83.513
(3.0908-3.0911) (3.2876-3.2879)
I
Caution
l The boring size should be based on the size of an
oversize piston and be the same for all cylinders.
(1) If the cylinder bore exceeds the maximum, rebore the
cylinder to oversize.
(2) If the difference between measurements A and C ex-
ceeds the maximum taper, rebore the cylinder to
oversize.
Taper: 0.019mm (0.0007 in) max.
(3) If the difference between measurements X and Y ex-
ceeds the maximum out-of-round, rebore the cylinder
to oversize.
Out-of-round: 0.019mm (0.0007 in) max.
5. If the upper part of a cylinder wall shows uneven wear, re-
move the ridge with a ridge reamer.
OIL JET (BP SOHC)
1. Push the check ball and verify that it moves smoothly.
2. Blow through the oil jet and verify that air flows.
81-61
Page 92 of 1164
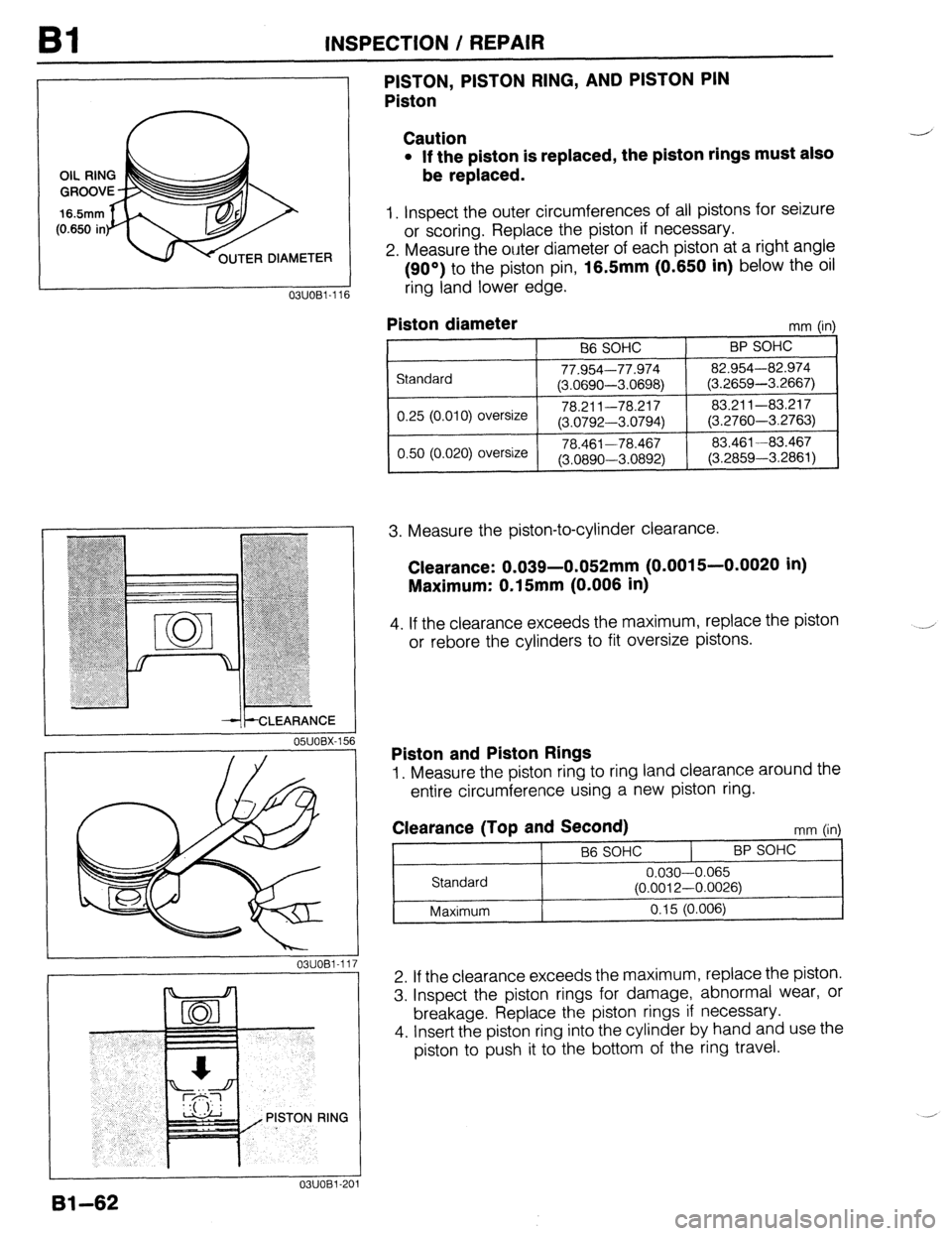
ER DIAMETER
03UOBl-116
Bl INSPECTION / REPAIR
PISTON, PISTON RING, AND PISTON PIN
Piston
Caution
l If the piston is replaced, the piston rings must also
be replaced.
1. inspect the outer circumferences of all pistons for seizure
or scoring. Replace the piston if necessary.
2. Measure the outer diameter of each piston at a right angle
(90°) to the piston pin,
16Smm (0.650 in) below the oil
ring land lower edge.
Piston diameter mm (in)
B6 SOHC BP SOHC
Standard 77.954-77.974 82.954-82.974
(3.0690-3.0698) (3.2659-3.2667)
0.25 (0.010) oversize 78.21 I-78.21 7 83.211-83.217
(3.0792-3.0794) (3.2760-3.2763)
0.50 (0.020) oversize 78.461-78.467 83.461-83.467
(3.0890-3.0892) (3.2859-3.2861)
-+-CLEARANCE
05UOBX-156
Bl-62
-A”’
3. Measure the piston-to-cylinder clearance.
Clearance: 0.039-0.052mm (0.0015-0.0020 in)
Maximum: 0.15mm (0.006 in)
4. If the clearance exceeds the maximum, replace the piston
or rebore the cylinders to fit oversize pistons. -I
Piston and Piston Rings
1. Measure the piston ring to ring land clearance around the
entire circumference using a new piston ring.
Clearance (Top and Second) mm (in)
7
B6 SOHC BP SOHC
Standard 0.030-0.065
(0.0012-0.0026)
Maximum 0.15 (0.006)
2. If the clearance exceeds the maximum, replace the piston.
3. Inspect the piston rings for damage, abnormal wear, or
breakage. Replace the piston rings if necessary.
4. Insert the piston ring into the cylinder by hand and use the
piston to push it to the bottom of the ring travel.
Page 93 of 1164
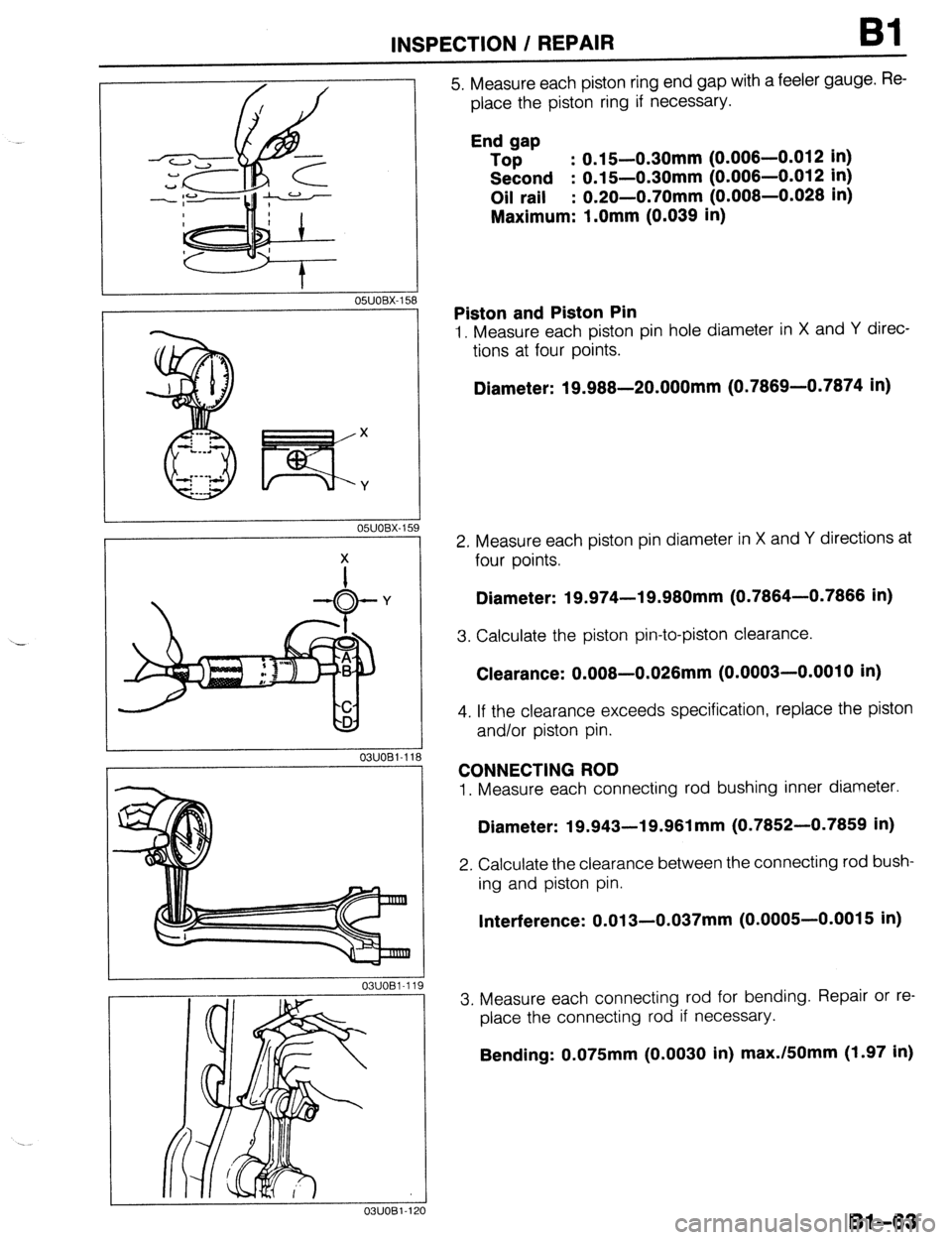
.-
INSPECTION / REPAIR Bl
I O!YJOBX-158
X
03UOB1-118
03UOBl-11 9
03UOBl-1: -A
‘0
5. Measure each piston ring end gap with a feeler gauge. Re-
place the piston ring if necessary.
End gap
Top : 0.15--0.30mm (0.006-0.012 in)
Second : 0.1 S-0.30mm (0.006-0.012 in)
Oil rail : 0.20-0.70mm (0.006-0.028 in)
Maximum: l.Omm (0.039 in)
Piston and Piston Pin
‘1. Measure each piston pin hole diameter in X and Y direc-
tions at four points.
Diameter: 19.988--2O.OOOmm (0.7869-0.7874 in)
2. Measure each piston pin diameter in X and Y directions at
four points,
Diameter: 19,974-l 9.980mm (0.7864-0.7866 in)
3. Calculate the piston pin-to-piston clearance.
Clearance: 0.008-0.026mm (0.0003-0.0010 in)
4. If the clearance exceeds specification, replace the piston
and/or piston pin.
CONNECTING ROD
1. Measure each connecting rod bushing inner diameter.
Diameter: 19.943-l 9.961 mm (0.7852-0.7859 in)
2. Calculate the clearance between the connecting rod bush-
ing and piston pin.
Interference: 0.013-0.037mm (0.0005-0.0015 in)
3. Measure each connecting rod for bending. Repair or re-
place the connecting rod if necessary.
Bending: 0.075mm (0.0030 in) max./fiOmm (1.97 in)
81-63
Page 94 of 1164
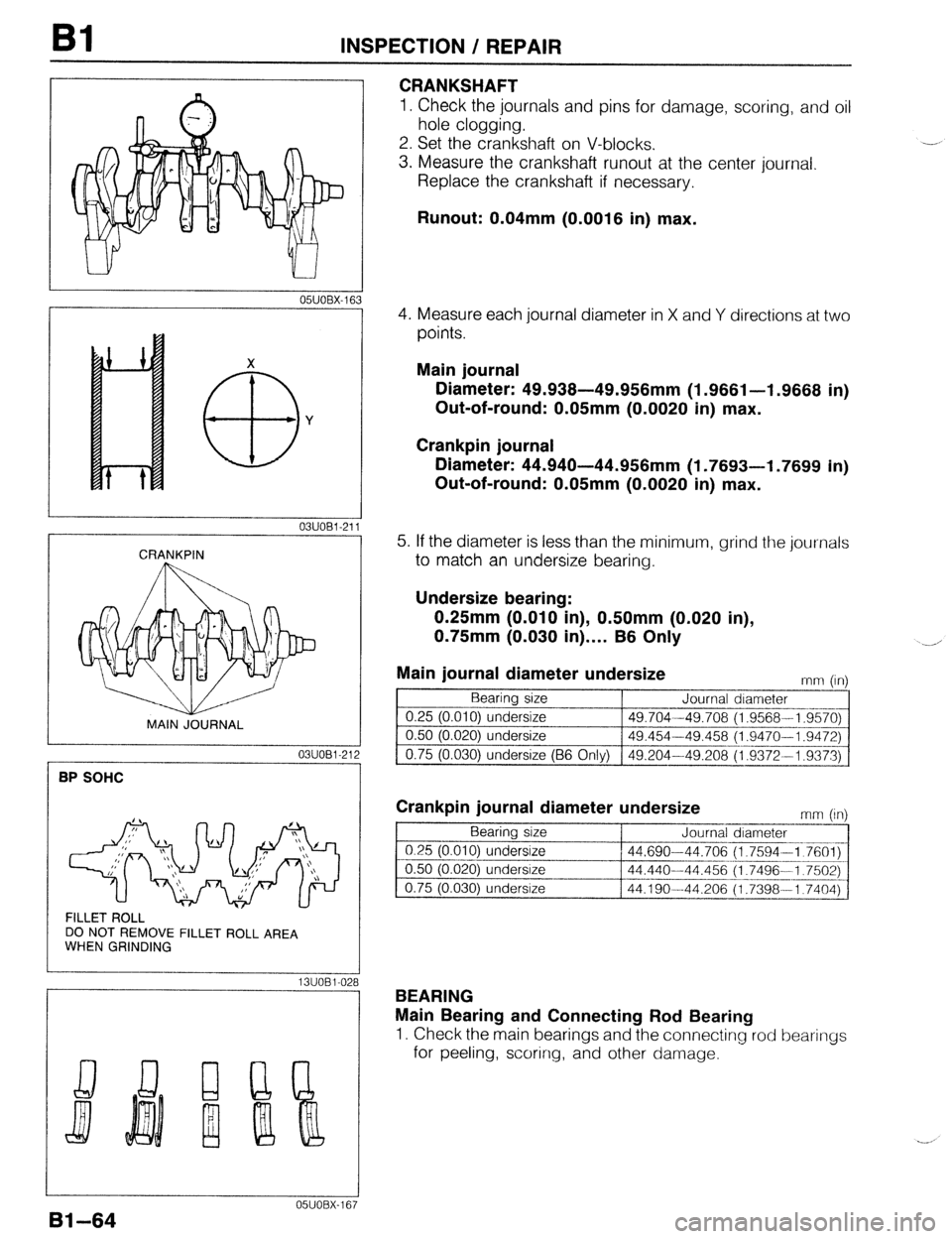
INSPECTION / REPAIR
05UOBX-1E
X
8 Y
03UOBl-21
CRANKPIN
MAIN JOURNAL
03UOBl-21
BP SOHC .r -
FILLET ROLL
DO NOT REMOVE FILLET ROLL AREA
WHEN GRINDING
1311081-028
CRANKSHAFT
1. Check the journals and pins for damage, scoring, and oil
hole clogging.
2. Set the crankshaft on V-blocks.
3. Measure the crankshaft runout at the center journal.
Replace the crankshaft if necessary. -.
Runout: 0.04mm (0.0016 in) max.
4. Measure each journal diameter in X and Y directions at two
points.
Main journal
Diameter: 49.938-49.956mm (1.9661-l .9668 in)
Out-of-round: 0.05mm (0.0020 in) max.
Crankpin journal
Diameter: 44.940-44.956mm (1.7693-l .7699 in)
Out-of-round: 0.05mm (0.0020 in) max.
5. If the diameter is less than the minimum, grind the journals
to match an undersize bearing.
Undersize bearing:
0.25mm (0.010 in), 0.50mm (0.020 in),
0.75mm (0.030 in).... B6 Only
Main journal diameter undersize
mm iin) 1. Bearing size Journal diameter
_-.---
0.25 (0.010) undersize 49.704.-49.708 (1.9568-l .9570)
---.-___
0.50 (0.020) undersize 49.454-49.458 (1.9470-l .9472)
0.75 (0.030) undersize (B6 Only) 49.204-49.208(1.9372--l .9373)
Crankpin journal diameter undersize ” ” ” 1” Bearing size Journal diameter
-_ ____~_.
0.25 (0.010) undersize 44.690-44.706
(1.7594 -1 7601) .--.._-.~.--~-.~
0.50
(0.020) underslze 44.440-44.456 (1.7496-I .7502) -- _____----.
0.75 (0.030) undersize 44.190--44.206 (1.7398---i .7404)
BEARING
Main Bearing and Connecting Rod Bearing
1. Check the main bearings and the connecting rod bearings
for peeling, scoring, and other damage.
05UOBX-167
Bl-64
Page 95 of 1164
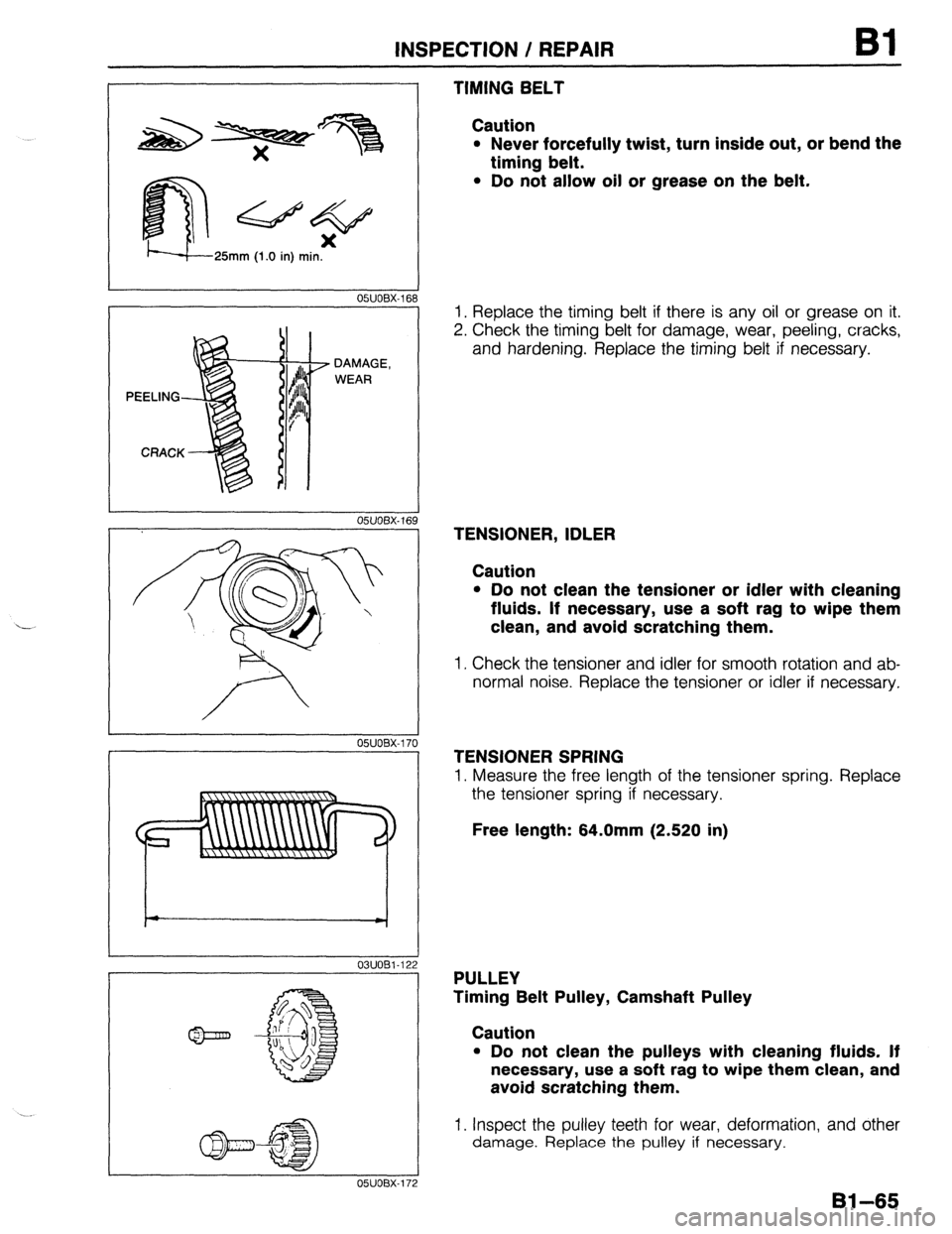
INSPECTION / REPAIR 81
---
L
25mm (1 .O in) min.
OSJOBX-161
DAMAGE,
WEAR
05UOBX-16!
03UOEl-12: 7
05UOBX-17: 2 05UOBX-170
TIMING BELT
Caution
l Never forcefully twist, turn inside out, or bend the
timing belt.
l Do not allow oil or grease on the belt.
1. Replace the timing belt if there is any oil or grease on it.
2. Check the timing belt for damage, wear, peeling, cracks,
and hardening. Replace the timing belt if necessary.
TENSIONER, IDLER
Caution
l Do not clean the tensioner or idler with cleaning
fluids. If necessary, use a soft rag to wipe them
clean, and avoid scratching them.
1. Check the tensioner and idler for smooth rotation and ab-
normal noise. Replace the tensioner or idler if necessary,
TENSIONER SPRING
1. Measure the free length of the tensioner spring. Replace
the tensioner spring if necessary.
Free length: 64.0mm (2.520 in)
PULLEY
Timing Belt Pulley, Camshaft Pulley
Caution
l Do not clean the pulleys with cleaning fluids. If
necessary, use a soft rag to wipe them clean, and
avoid scratching them.
1. Inspect the pulley teeth for wear, deformation, and other damage. Replace the pulley if necessary.
Bl-65
Page 96 of 1164
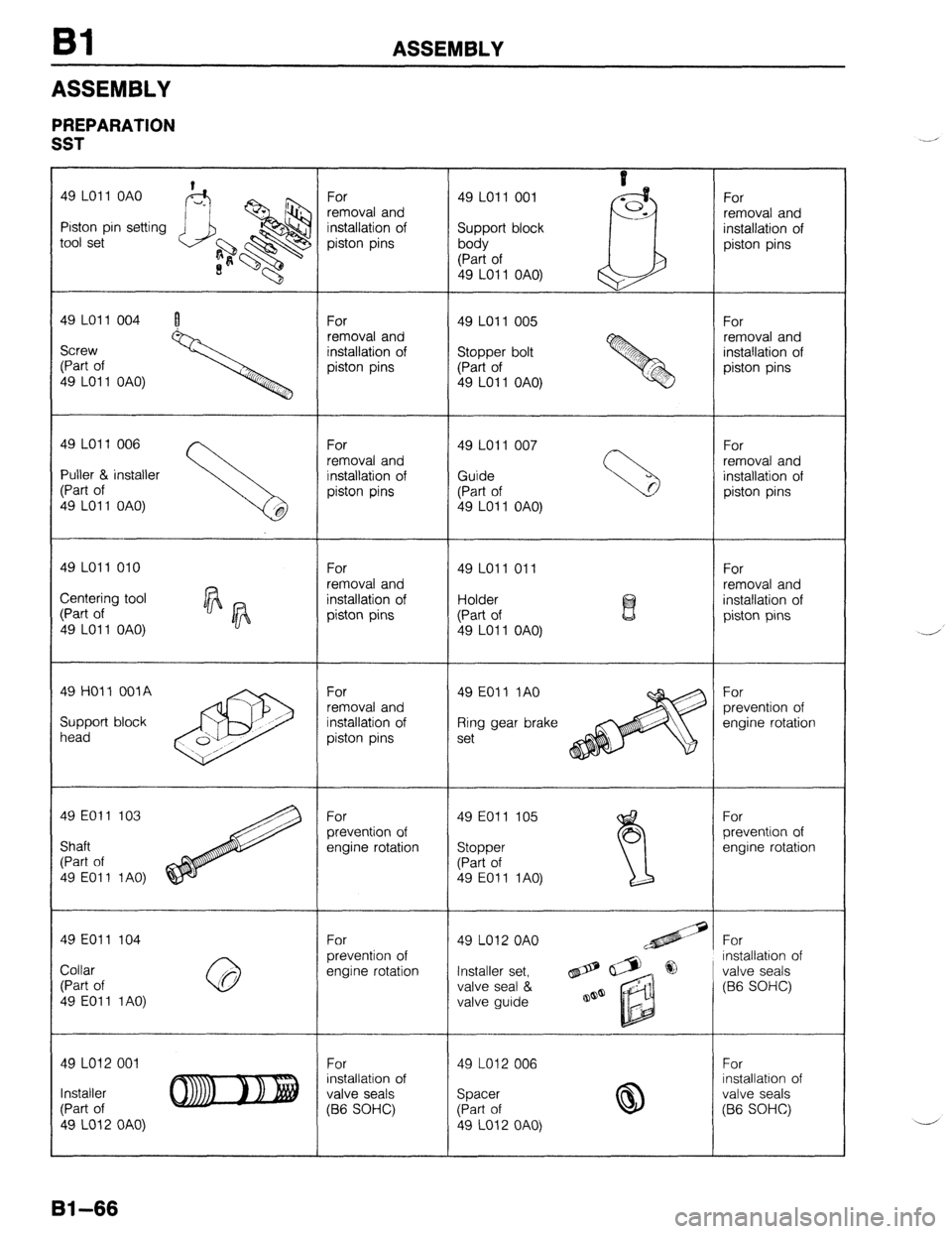
Bl ASSEMBLY
ASSEMBLY
PREPARATION
SST
49 LO1 1 OAO
Piston pin setting
tool set
49 LO1 1 004 I
Screw
(Part of
49 LO1 1 OAO)
49 LO1 1 006
Puller & installer
49 LO1 1 OAO) For
removal and
installation of
piston pins 49 LO11 001
Support block
body
(Part of
49 LO11 OAO)
49 LO1 1 005
Stopper bolt
(Part of
49 LO1 1 OAO)
49 LO1 1 007 For
removal and
installation of
piston pins
For
removal and
installation of
piston pins
Centering tool
49 LO1 1 OAO)
49 HO11 OOlA
Support block
49 EOll 103
49 EOll 104
installation of
Collar
49 LO12 001
installation of
Page 97 of 1164
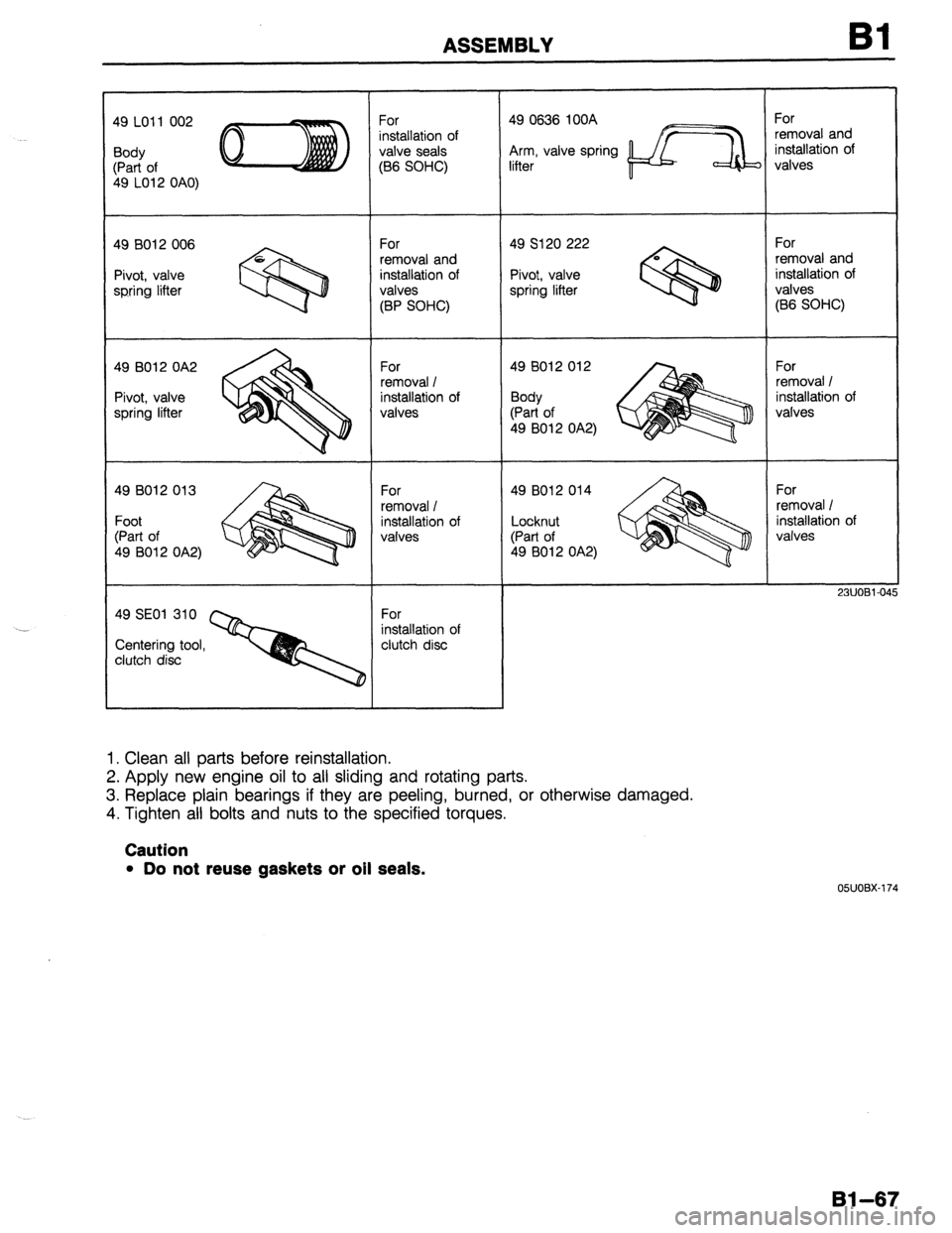
ASSEMBLY Bl
19 LO11 002
Body
:Part of
49 LO12 OAO)
49 8012 006
Pivot, valve
spring lifter
49 8012 OA2
Pivot, valve
spring lifter
49 8012 013
Foot
(Part of
49 B012 OA2)
49 SE01 310
Centering tool,
clutch disc For
installation of
valve seals
(B6 SOHC)
For
removal and
installation of
valves
(BP SOHC)
For
removal I
installation of
valves
For
removal I
installation of
valves
For
installation of
clutch disc 49 0636 1OOA
Arm, valve spring
lifter
49 s120 222
0
Pivot, valve
spring lifter
%
49 8012 012
Body
(Part of
49 8012 OA2)
49 B012 014
Locknut
(Part of
49 8012 OA2)
1. Clean all parts before reinstallation.
2. Apply new engine oil to all sliding and rotating parts.
3. Replace plain bearings if they are peeling, burned, or otherwise damaged.
4. Tighten all bolts and nuts to the specified torques.
Caution
l Do not reuse gaskets or oil seals.
I
3 For
removal and
installation of
valves
For
removal and
installation of
valves
(B6 SOHC)
For
removal I
installation of
valves
For
removal I
installation of
valves
23UOBl-0,
05UOBX-174
Bl-67
Page 98 of 1164
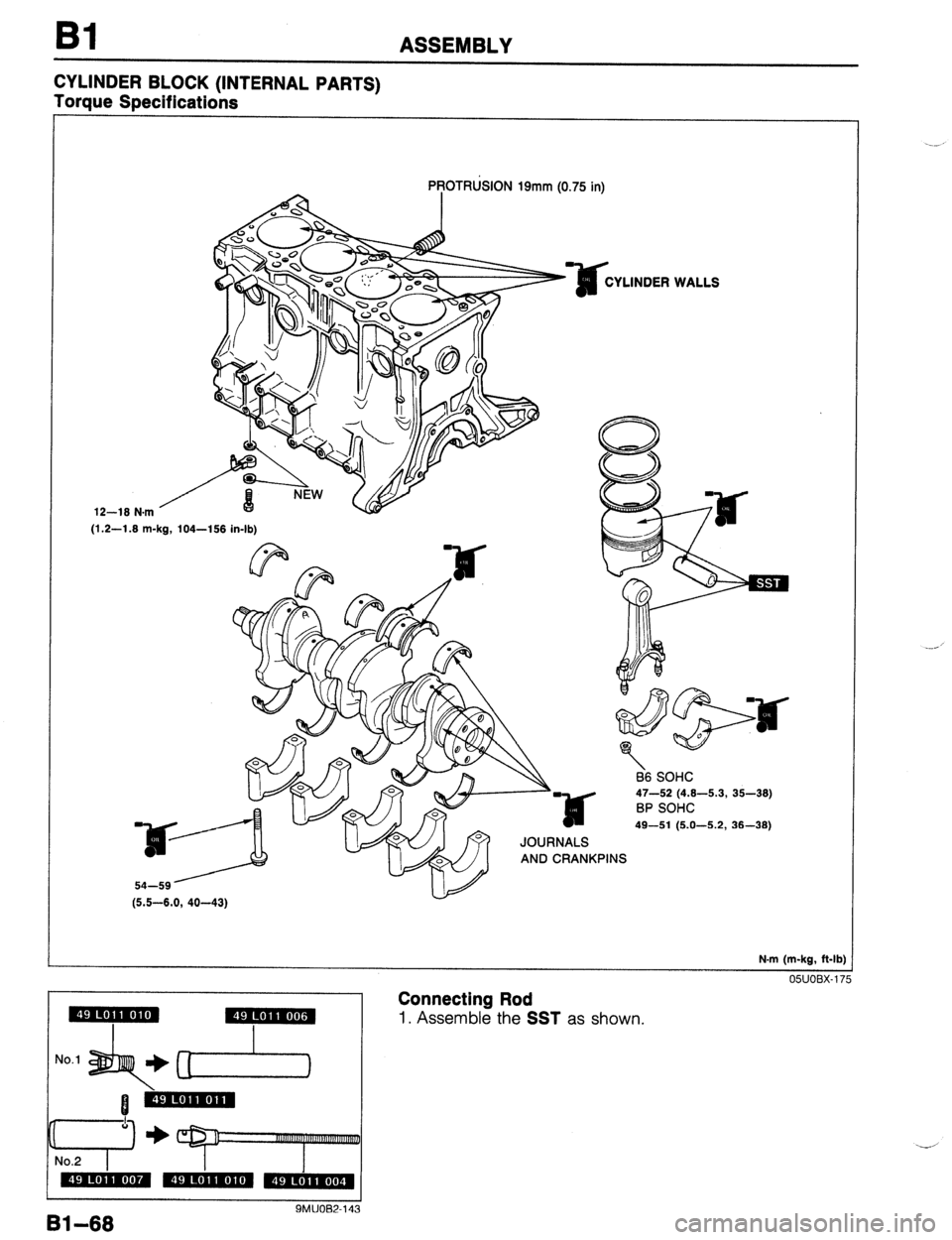
Bl ASSEMBLY
CYLINDER BLOCK (INTERNAL PARTS)
Torque SPecifications
12-18 N.m PROTRLklON 19mm (0.75 in)
YLINDER
(1.2-1.8 m-kg, 104-158 in-lb)
JOURNALS
AND CRANKPINS
(5.5-8.0, 40-43) WALLS
66 SOHC
47-52 (4.8-5.3, 35-38)
BP SOHC
49-51 (5.0-5.2, 36-38)
N.m (m-kg, ft-lb)
05UOBX-171
Connecting Rod
1. Assemble the SST as shown.
9MUOW143
Page 99 of 1164
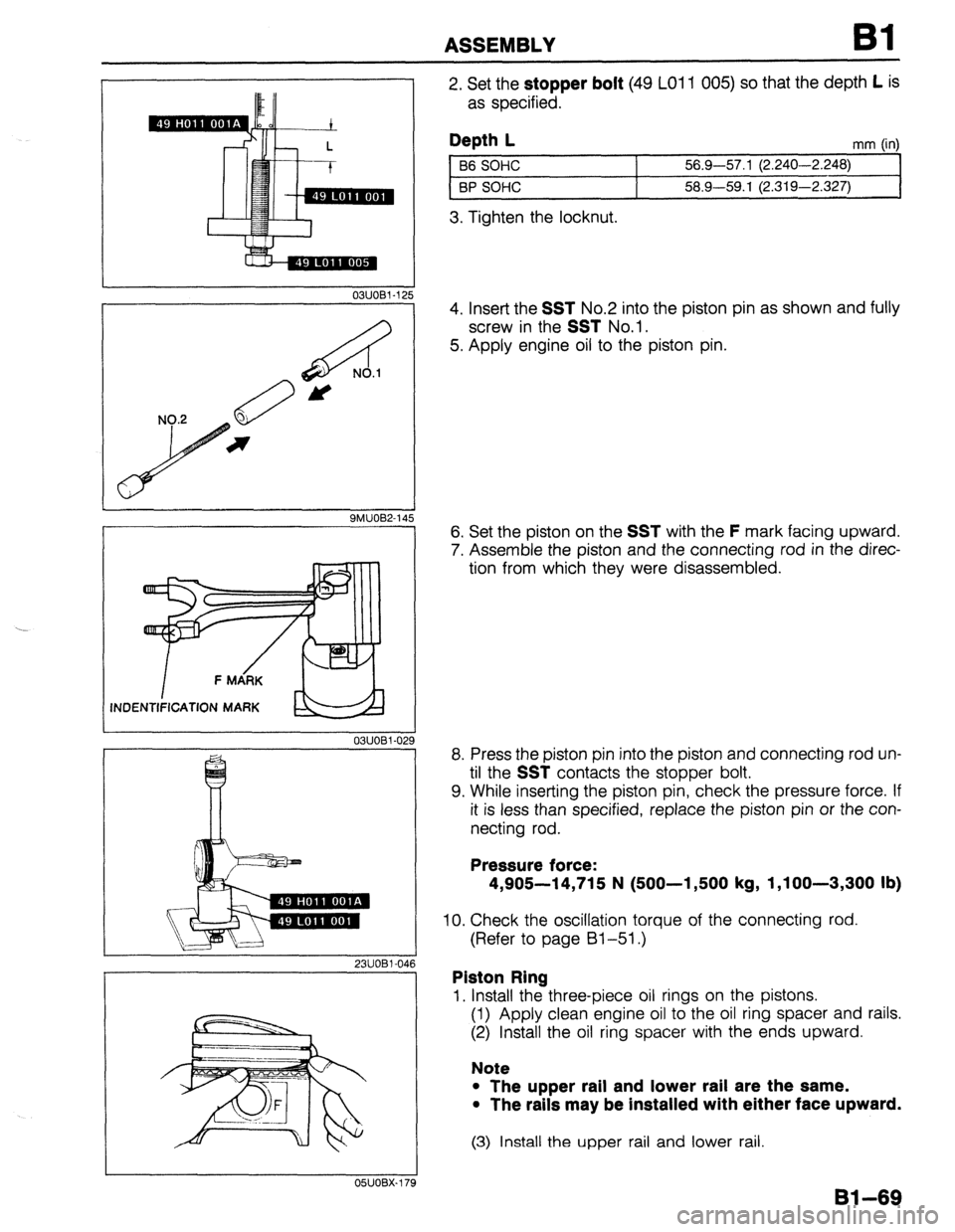
ASSEMBLY Bl
I-
r
I 03UOBl-12
A NO.1
M
9MUOB2-14 I ‘NDENTIFICATION MARK
03UOBl-02
I
23UOBl-04
05UOBX.179
2. Set the stopper bolt (49 LO1 1 005) so that the depth L is
as specified.
Depth L
B6 SOHC
BP SOHC mm (in)
I 56.9-57.1 (2.240-2.248)
58.9-59.1 (2.319-2.327)
3. Tighten the locknut.
4. Insert the
SST No.2 into the piston pin as shown and fully
screw in the
SST No.1.
5. Apply engine oil to the piston pin.
6. Set the piston on the
SST with the F mark facing upward.
7. Assemble the piston and the connecting rod in the direc-
tion from which they were disassembled.
8. Press the piston pin into the piston and connecting rod un-
til the SST contacts the stopper bolt.
9. While inserting the piston pin, check the pressure force. If
it is less than specified, replace the piston pin or the con-
necting rod.
Pressure force:
4,905-14,715 N (500-l ,500 kg, 1 ,lOO-3,300 lb)
10. Check the oscillation torque of the connecting rod.
(Refer to page Bl-51.)
Piston Ring 1,
Install the three-piece oil rings on the pistons.
(1) Apply clean engine oil to the oil ring spacer and rails.
(2) Install the oil ring spacer with the ends upward.
Note
l The upper rail and lower rail are the same.
l The rails may be installed with either face upward. (3) Install the upper rail and lower rail
Bl-69
Page 100 of 1164
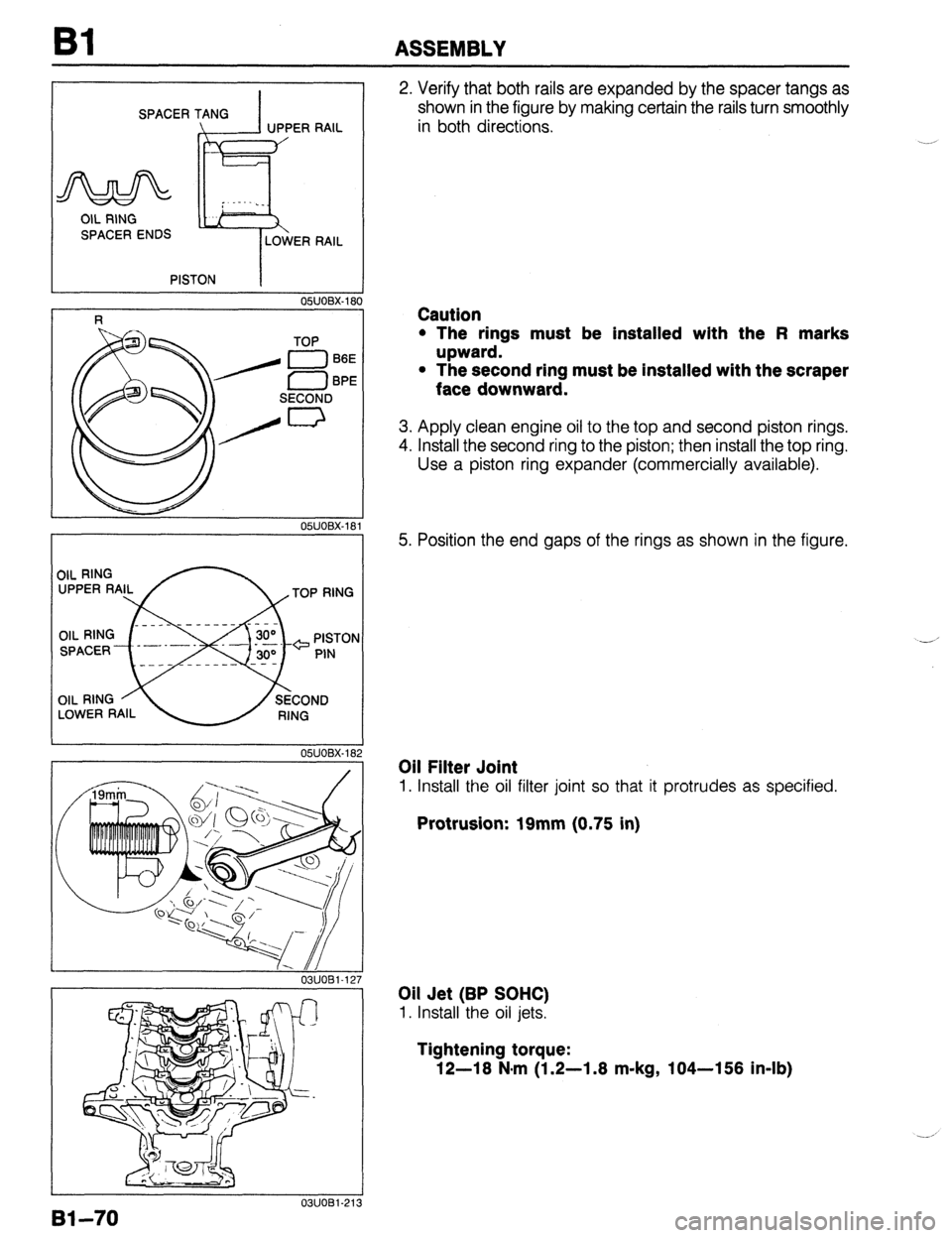
Bl ASSEMBLY
SPACER TANG
OIL RING
SPACER ENDS
PISTON
I
05u0Bx-180
R I
OWOBX-18.
81-70
2. Verify that both rails are expanded by the spacer tangs as
shown in the figure by making certain the rails turn smoothly
in both directions.
Caution
l The rings must be installed with the R marks
upward.
l The second ring must be installed with the scraper
face downward.
3. Apply clean engine oil to the top and second piston rings.
4. Install the second ring to the piston; then install the top ring.
Use a piston ring expander (commercially available).
5. Position the end gaps of the rings as shown in the figure.
05UOBX-182 Oil Filter Joint
1. Install the oil filter joint so that it protrudes as specified
03UOBl-21:
Protrusion: 19mm (0.75 in)
Oil Jet (BP SOHC)
1. Install the oil jets.
Tightening torque:
12-18 N*m (1.2-1.8 m-kg, 104-158 in-lb)