MITSUBISHI SPYDER 1990 Service Repair Manual
Manufacturer: MITSUBISHI, Model Year: 1990, Model line: SPYDER, Model: MITSUBISHI SPYDER 1990Pages: 2103, PDF Size: 68.98 MB
Page 1511 of 2103
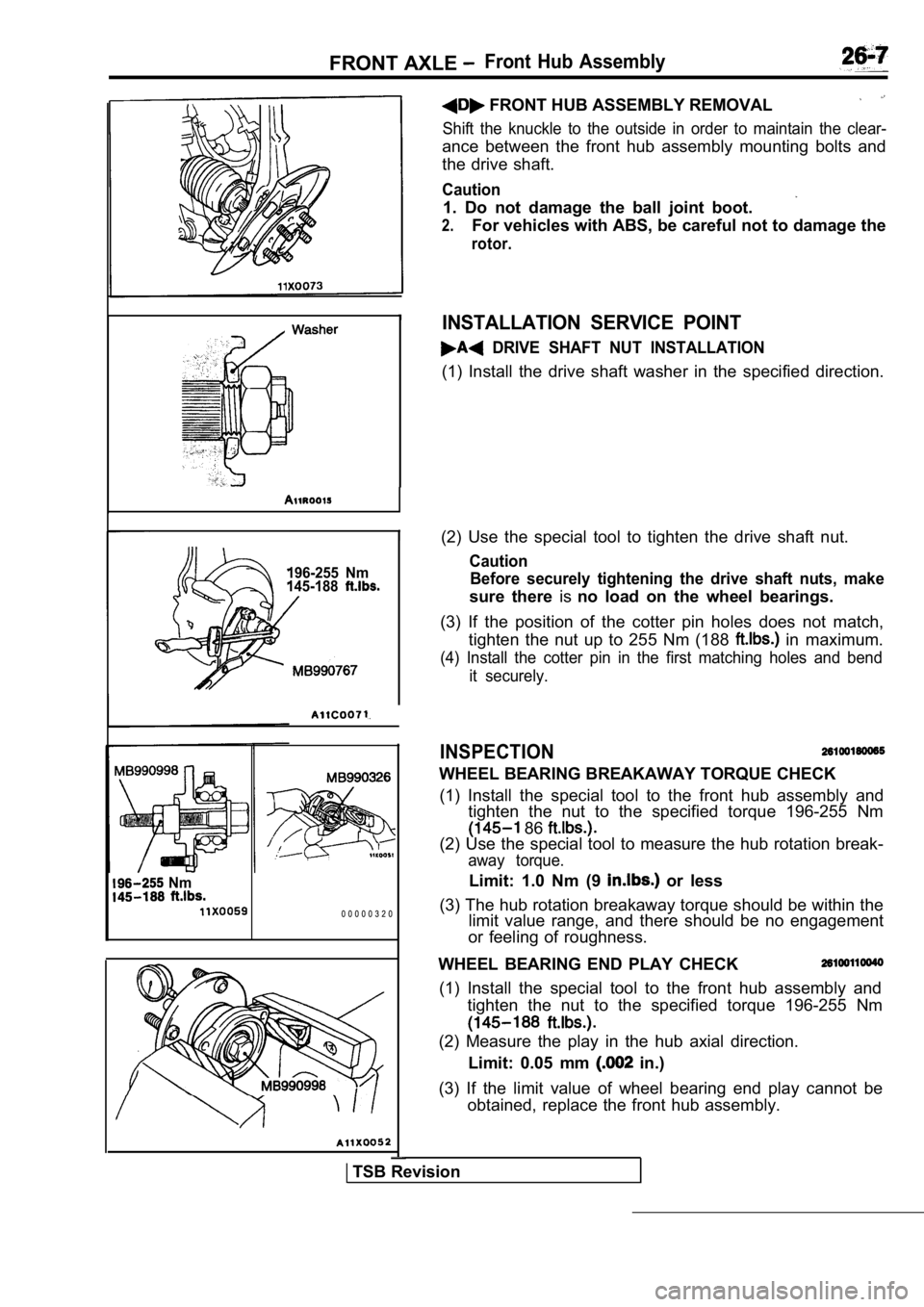
FRONT AXLE Front Hub Assembly
196-255 Nm
145-188
I(2) Use the special tool to tighten the drive shaft nut.
Caution
Before securely tightening the drive shaft nuts, ma ke
sure there isno load on the wheel bearings.
(3) If the position of the cotter pin holes does no t match,
tighten the nut up to 255 Nm (188
in maximum.
(4) Install the cotter pin in the first matching ho les and bend
it securely.
INSPECTION
WHEEL BEARING BREAKAWAY TORQUE CHECK
(1) Install the special tool to the front hub assem bly and
tighten the nut to the specified torque 196-255 Nm
86
(2) Use the special tool to measure the hub rotatio n break-
away torque.
Limit: 1.0 Nm (9 or less
(3) The hub rotation breakaway torque should be wit hin the
limit value range, and there should be no engagemen t
or feeling of roughness. Nm
0 0 0 0 0 3 2 0
FRONT HUB ASSEMBLY REMOVAL
Shift the knuckle to the outside in order to mainta in the clear-
ance between the front hub assembly mounting bolts and
the drive shaft.
Caution
1. Do not damage the ball joint boot.
2.For vehicles with ABS, be careful not to damage the
rotor.
INSTALLATION SERVICE POINT
DRIVE SHAFT NUT INSTALLATION
(1) Install the drive shaft washer in the specified direction.
WHEEL BEARING END PLAY CHECK
(1) Install the special tool to the front hub assem bly and
tighten the nut to the specified torque 196-255 Nm
(2) Measure the play in the hub axial direction.
Limit: 0.05 mm
in.)
(3) If the limit value of wheel bearing end play ca nnot be
obtained, replace the front hub assembly.
TSB Revision
Page 1512 of 2103
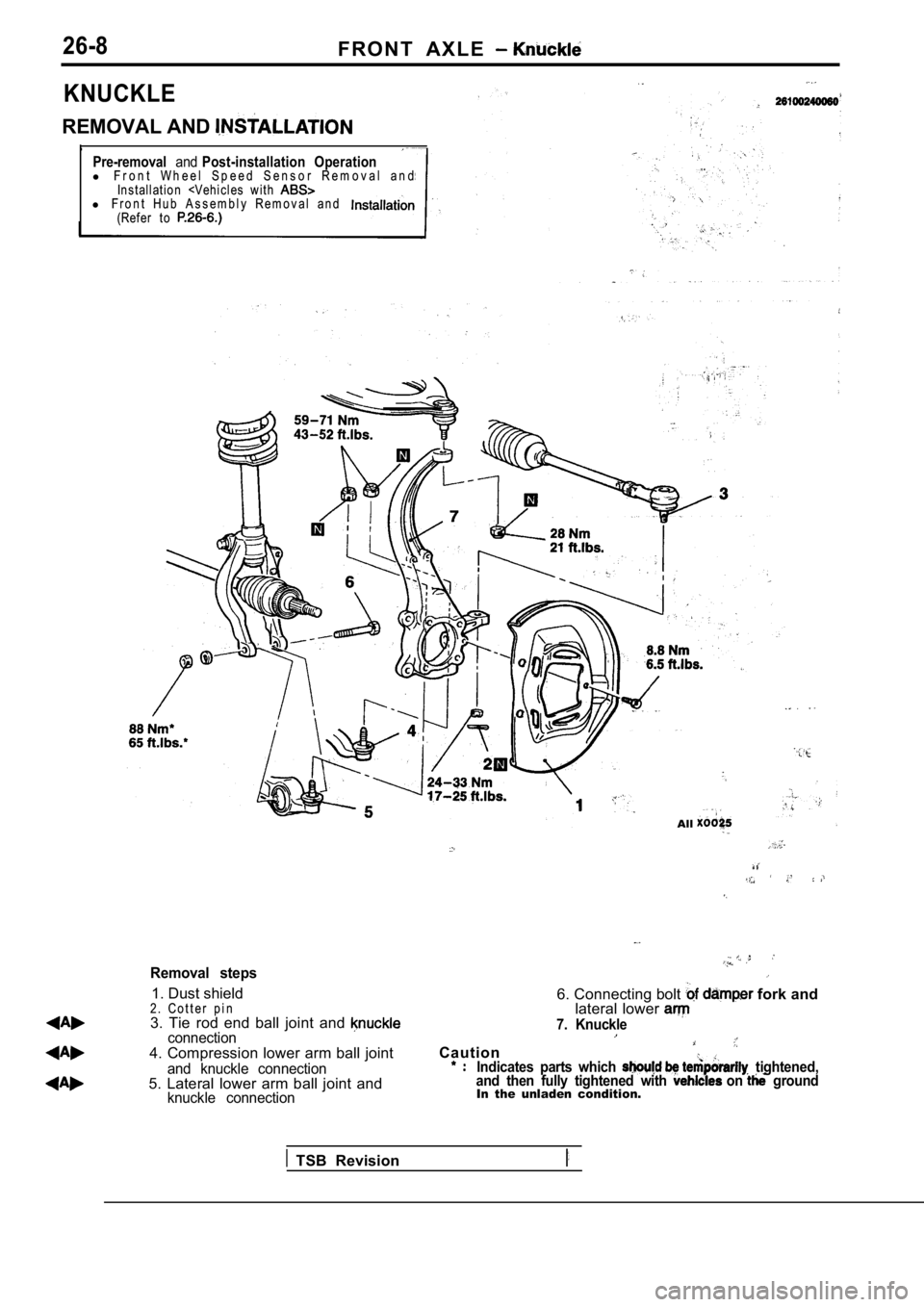
26-8F R O N T A X L E
KNUCKLE
REMOVAL AND
Pre-removalandPost-installation Operationl F r o n t W h e e l S p e e d S e n s o r R e m o v a l a n d
Installation
(Refer to
All
Removal steps
1. Dust shield
2. Co t t er p i n 6. Connecting bolt fork and
3. Tie rod end ball joint and lateral lower
7. Knuckleconnection4. Compression lower arm ball joint Caution
and knuckle connectionIndicates parts which tightened,
5. Lateral lower arm ball joint andand then fully tightened with on ground
knuckle connectionIn the unladen condition.
TSB Revision
Page 1513 of 2103
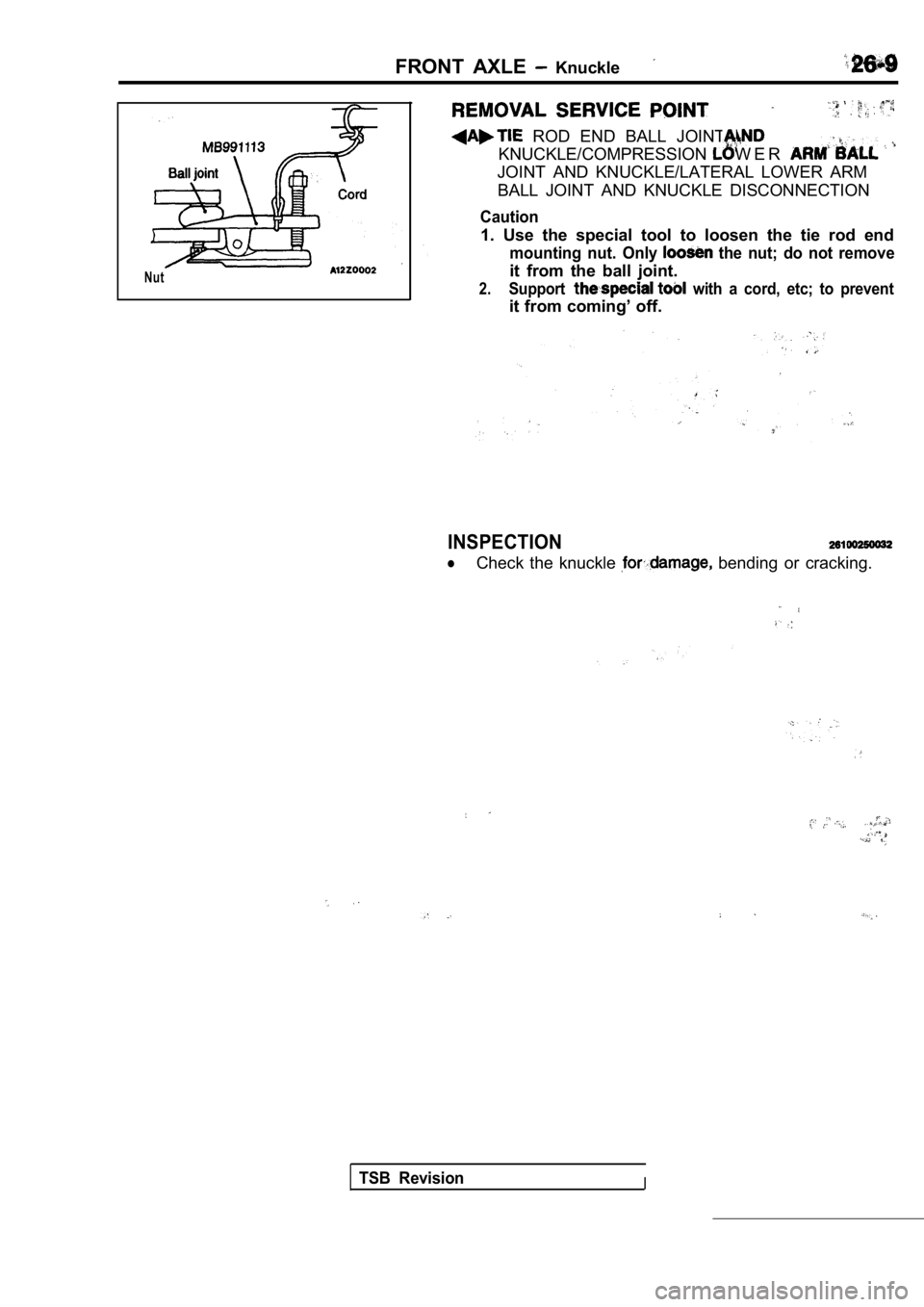
FRONT AXLE Knuckle
Nut
ROD END BALL JOINT
KNUCKLE/COMPRESSIONW E R
JOINT AND KNUCKLE/LATERAL LOWER ARMBALL JOINT AND KNUCKLE DISCONNECTION
Caution
1. Use the special tool to loosen the tie rod end
mounting nut. Only the nut; do not remove
it from the ball joint.
2.Support with a cord, etc; to prevent
it from coming’ off.
INSPECTION
lCheck the knuckle bending or cracking.
TSB RevisionI
Page 1514 of 2103
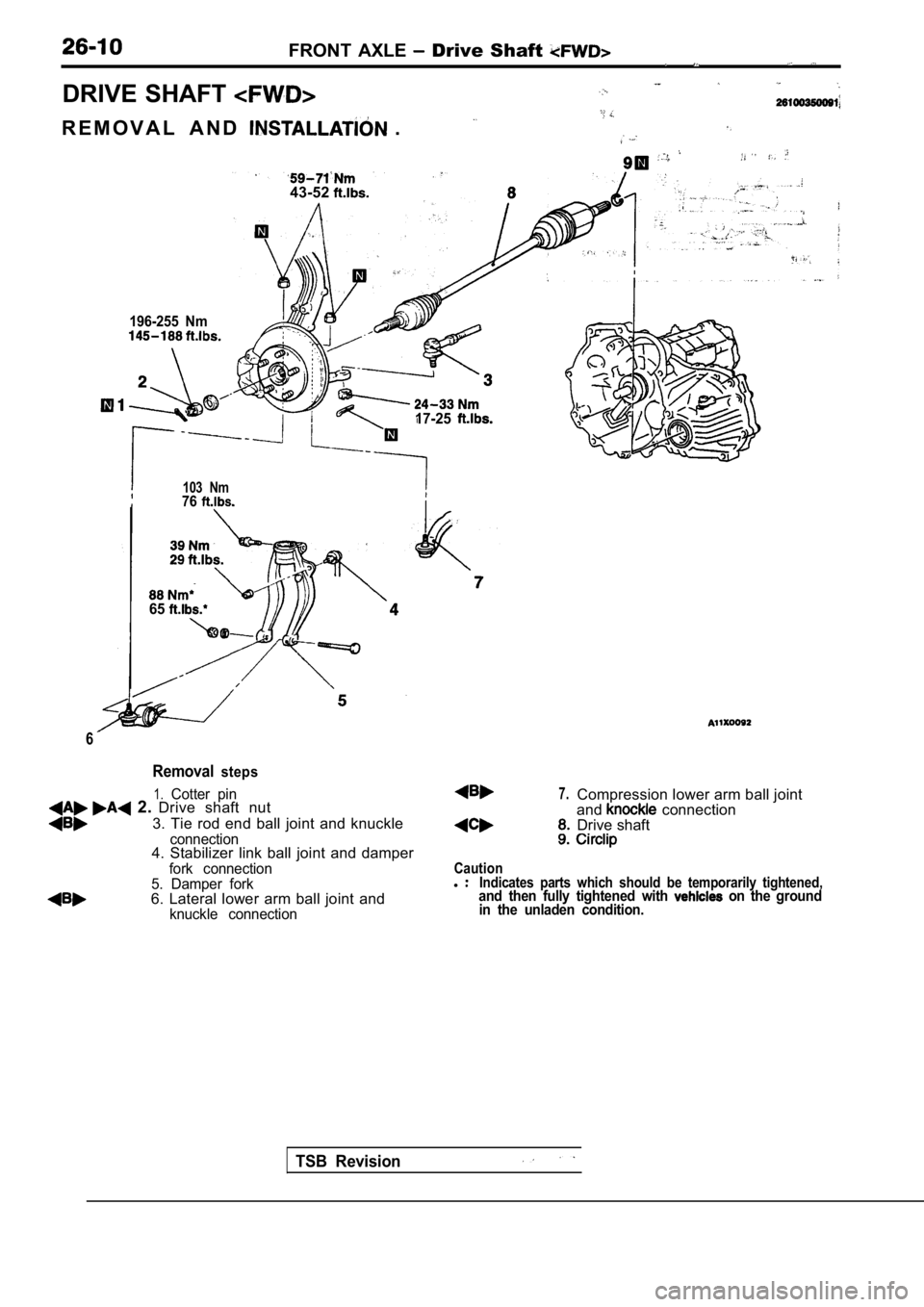
FRONT AXLE Drive Shaft
DRIVE SHAFT
R E M O V A L A N D .
43-52
196-255 Nm
17-25
103 Nm76
65
6
Removalsteps
1.Cotter pin 2. Drive shaft nut
3. Tie rod end ball joint and knuckle
connection4. Stabilizer link ball joint and damper
fork connection
7.
Caution
Compression lower arm ball joint
and connection
Drive shaft
5. Damper forkl Indicates parts which should be temporarily tighten ed,
6. Lateral lower arm ball joint andand then fully tightened with on the ground
knuckle connectionin the unladen condition.
TSB Revision
Page 1515 of 2103
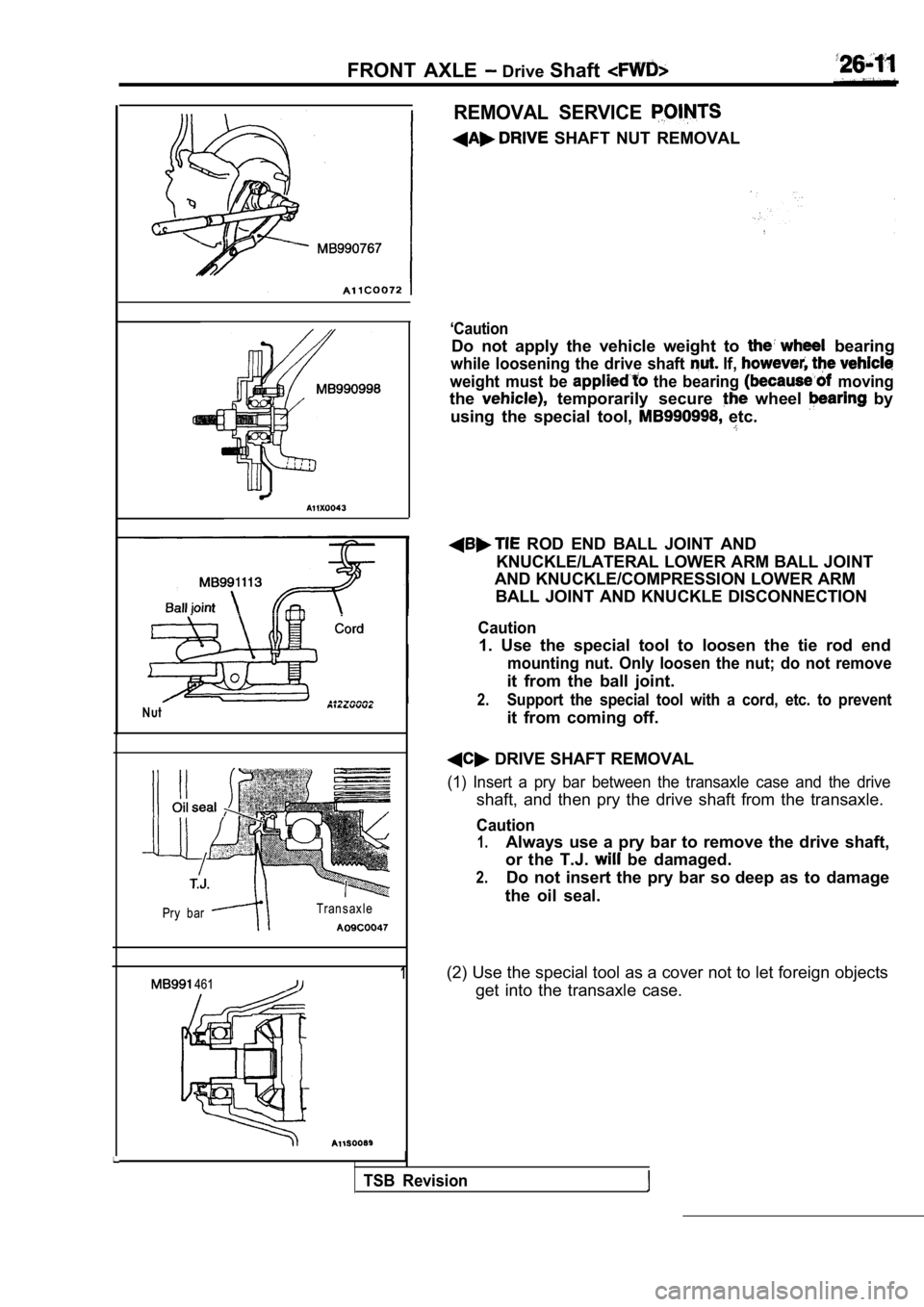
FRONT AXLE Drive Shaft
Nut
Pry bar Transaxle
1 461
I
REMOVAL SERVICE
SHAFT NUT REMOVAL
‘Caution
Do not apply the vehicle weight to bearing
while loosening the drive shaft If,
weight must be the bearing moving
the temporarily secure wheel by
using the special tool,
etc.
ROD END BALL JOINT AND
KNUCKLE/LATERAL LOWER ARM BALL JOINT
AND KNUCKLE/COMPRESSION LOWER ARM
BALL JOINT AND KNUCKLE DISCONNECTION
Caution
1. Use the special tool to loosen the tie rod end
mounting nut. Only loosen the nut; do not remove
it from the ball joint.
2.Support the special tool with a cord, etc. to preve nt
it from coming off.
DRIVE SHAFT REMOVAL
(1) Insert a pry bar between the transaxle case and the drive
shaft, and then pry the drive shaft from the transaxle.
Caution
1.Always use a pry bar to remove the drive shaft,
or the T.J.
be damaged.
2.Do not insert the pry bar so deep as to damage
the oil seal.
(2) Use the special tool as a cover not to let fore ign objects
get into the transaxle case.
TSB Revision
Page 1516 of 2103
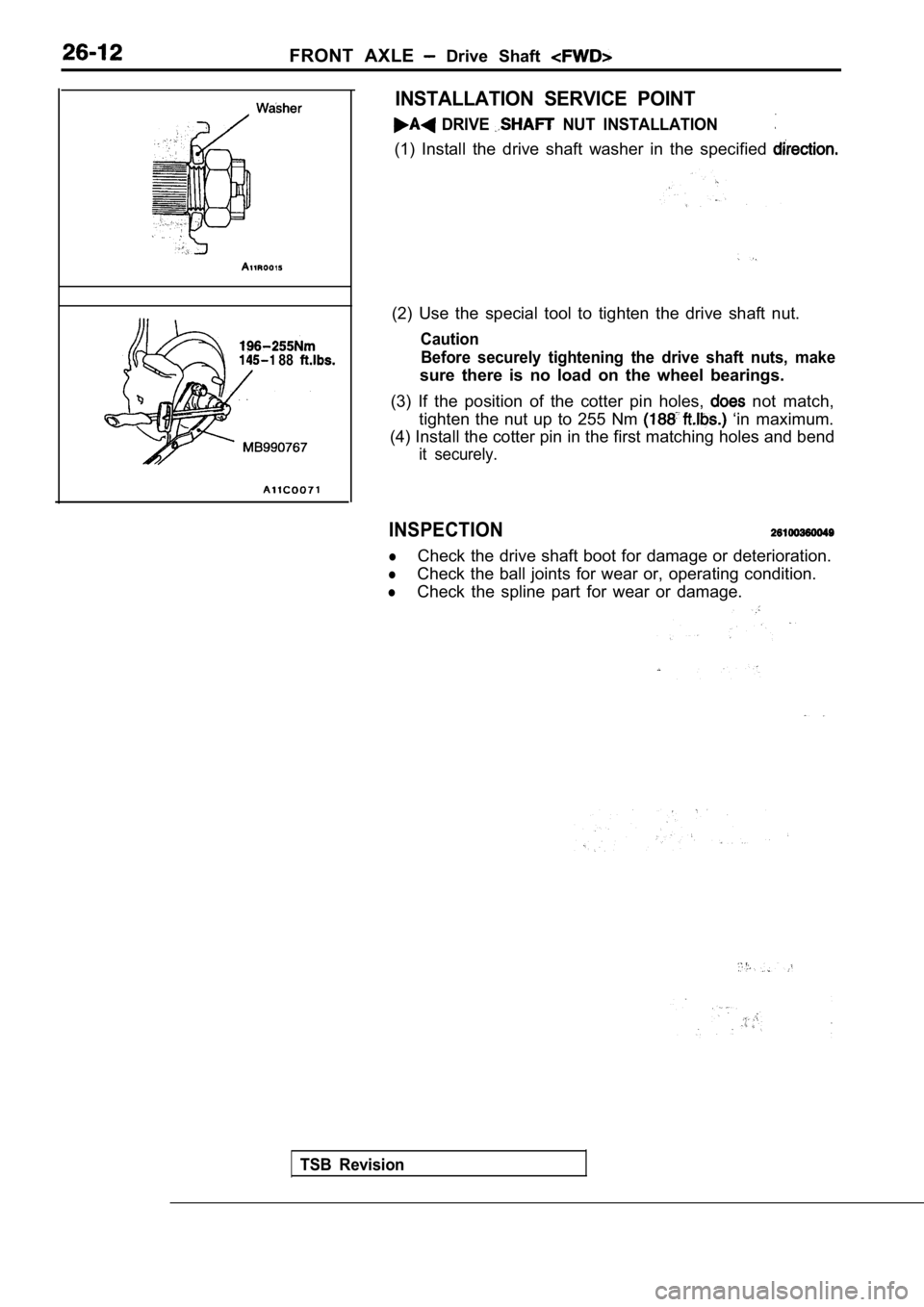
FRONT AXLE Drive Shaft
88
INSTALLATION SERVICE POINT
DRIVE NUT INSTALLATION
(1) Install the drive shaft washer in the specified
(2) Use the special tool to tighten the drive shaft nut.
Caution
Before securely tightening the drive shaft nuts, ma ke
sure there is no load on the wheel bearings.
(3) If the position of the cotter pin holes,
not match,
tighten the nut up to 255 Nm
‘in maximum.
(4) Install the cotter pin in the first matching ho les and bend
it securely.
INSPECTION
lCheck the drive shaft boot for damage or deteriorat ion.
lCheck the ball joints for wear or, operating condition.
lCheck the spline part for wear or damage.
TSB Revision
Page 1517 of 2103
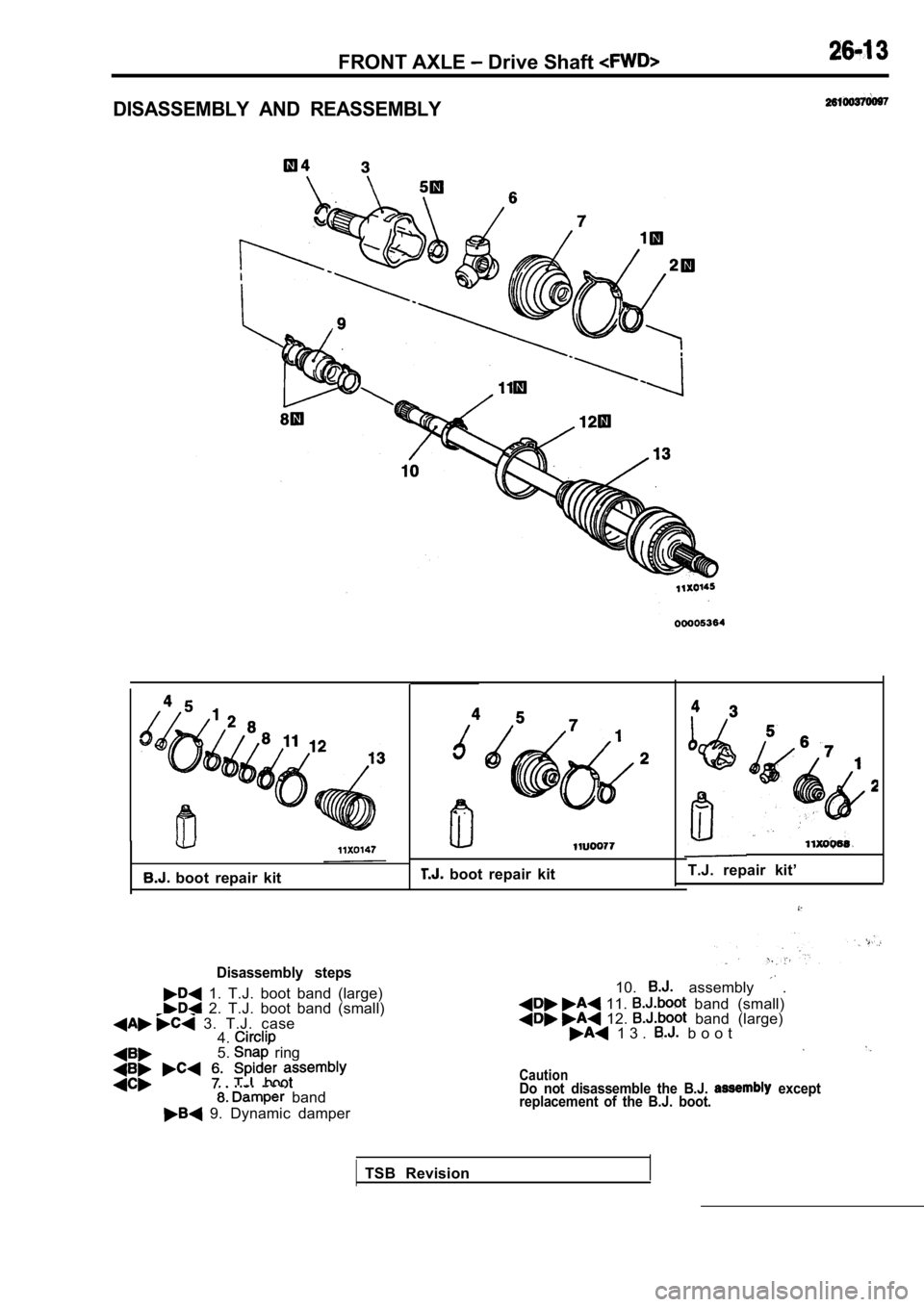
FRONT AXLE Drive Shaft
DISASSEMBLY AND REASSEMBLY
boot repair kit
Disassembly steps
1. T.J. boot band (large) 2. T.J. boot band (small) 3. T.J. case4.
5. ring
band
9. Dynamic damper
T.J. repair kit’ boot repair kit
10. assembly .
11. band (small) 12. band (large) 1 3 . b o o t
CautionDo not disassemble the B.J. except
replacement of the B.J. boot.
TSB Revision
Page 1518 of 2103
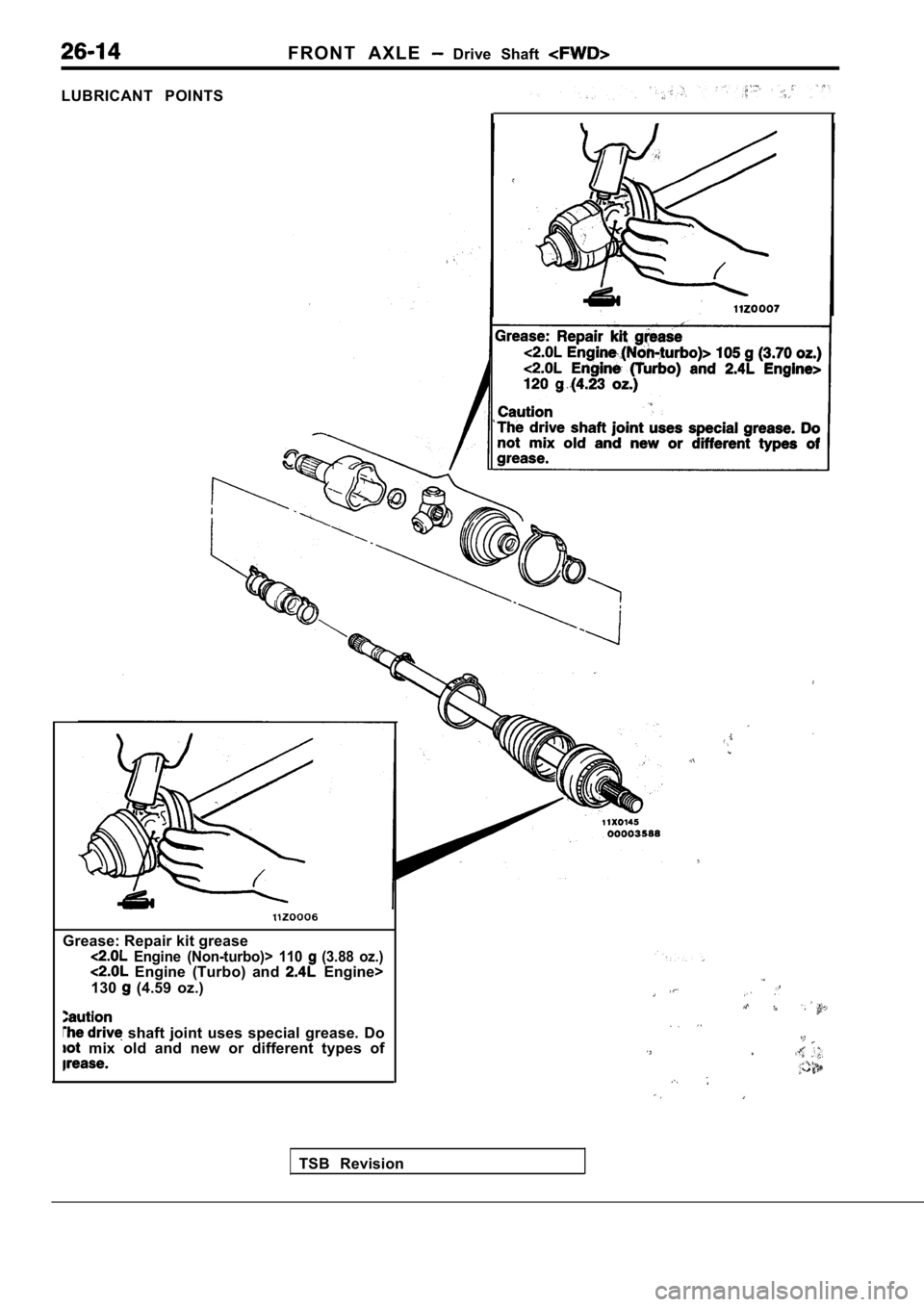
F R O N T A X L E Drive Shaft
LUBRICANT POINTSTSB Revision
Grease: Repair kit grease
Engine (Non-turbo)> 110 (3.88 oz.) Engine (Turbo) and Engine>
130
(4.59 oz.)
shaft joint uses special grease. Do mix old and new or different types of
,
Page 1519 of 2103
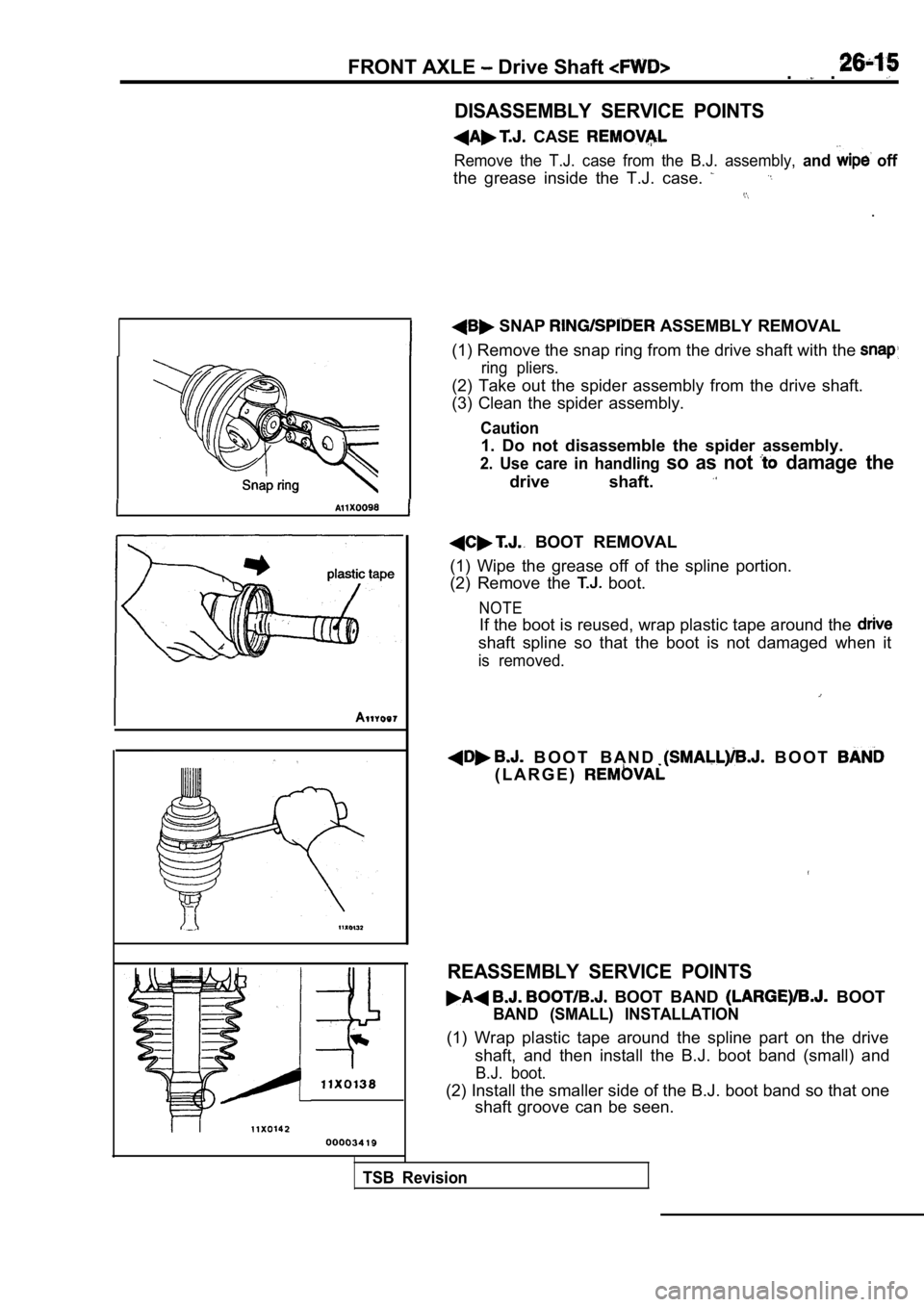
FRONT AXLE Drive Shaft ..
DISASSEMBLY SERVICE POINTS
CASE
Remove the T.J. case from the B.J. assembly, and off
the grease inside the T.J. case.
.
SNAP ASSEMBLY REMOVAL
(1) Remove the snap ring from the drive shaft with the
ring pliers.
(2) Take out the spider assembly from the drive sha ft.
(3) Clean the spider assembly.
Caution
1. Do not disassemble the spider assembly.
2. Use care in handling so as not damage the
drive shaft.
BOOT REMOVAL
(1) Wipe the grease off of the spline portion.
(2) Remove the
boot.
NOTE
If the boot is reused, wrap plastic tape around the
shaft spline so that the boot is not damaged when i t
is removed.
B O O T B A N D B O O T
( L A R G E )
REASSEMBLY SERVICE POINTS
BOOT BAND BOOT
BAND (SMALL) INSTALLATION
(1) Wrap plastic tape around the spline part on the drive
shaft, and then install the B.J. boot band (small) and
B.J. boot.
(2) Install the smaller side of the B.J. boot band so that one
shaft groove can be seen.
TSB Revision
Page 1520 of 2103
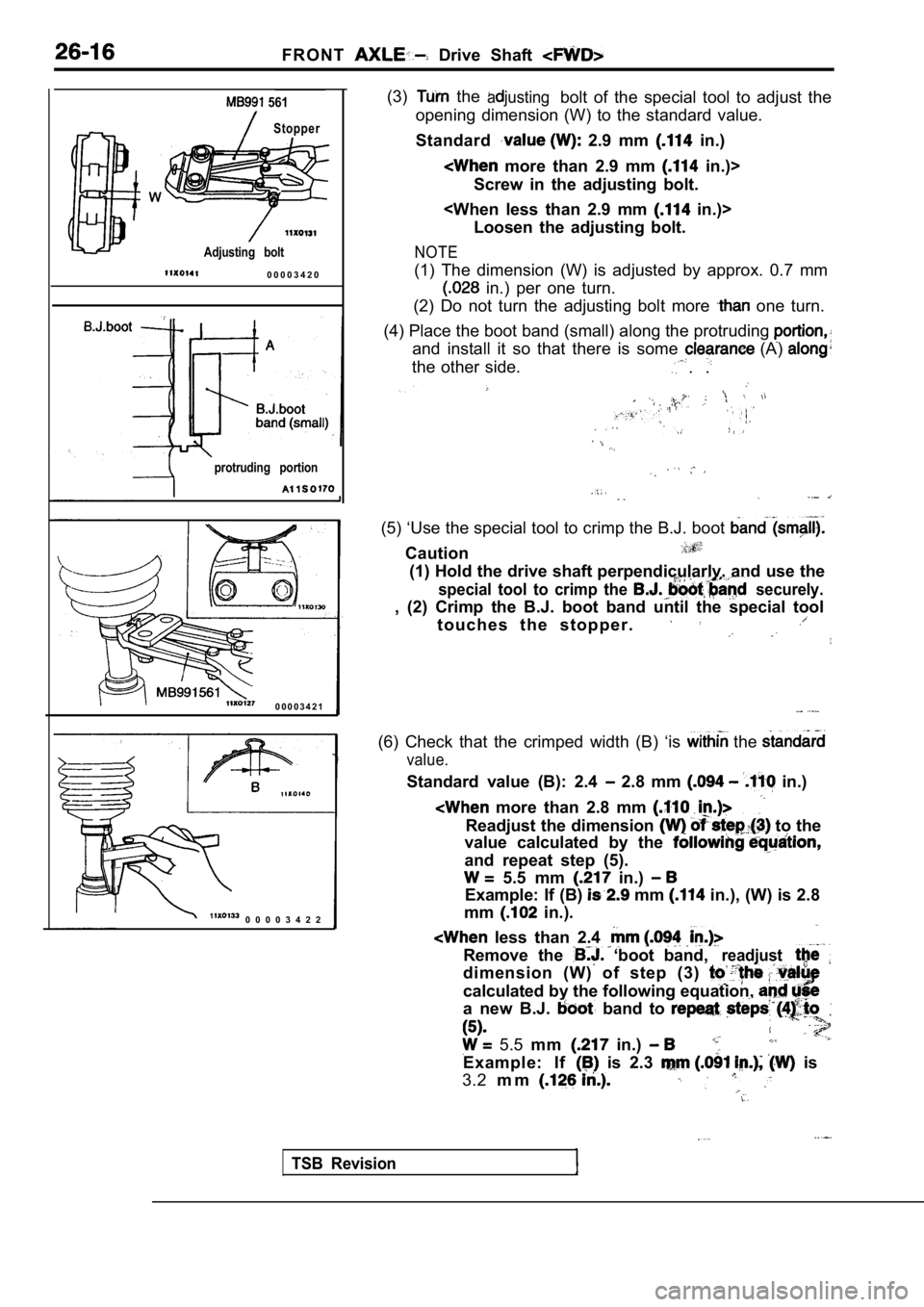
F R O N T Drive Shaft
561
Stopper
Adjusting bolt
0 0 0 0 3 4 2 0
protruding portion
0 0 0 0 3 4 2 1
0 0 0 0 3 4 2 2(3)
the ajustingbolt of the special tool to adjust the
opening dimension (W) to the standard value.
Standard
2.9 mm in.)
more than 2.9 mm in.)>
Screw in the adjusting bolt.
Loosen the adjusting bolt.
NOTE
(1) The dimension (W) is adjusted by approx. 0.7 mm
in.) per one turn.
(2) Do not turn the adjusting bolt more
one turn.
(4) Place the boot band (small) along the protrudin g
and install it so that there is some (A)
the other side. . .
(5) ‘Use the special tool to crimp the B.J. boot
Caution
(1) Hold the drive shaft perpendicularly, and use t he
special tool to crimp the securely.
, (2) Crimp the B.J. boot band until the special to ol
t o u c h e s t h e s t o p p e r .
(6) Check that the crimped width (B) ‘is the
value.
Standard value (B): 2.4 2.8 mm in.)
more than 2.8 mm
Readjust the dimension to the
value calculated by the
and repeat step (5).
5.5 mm in.)
Example: If (B) mm in.), (W) is 2.8
mm
in.).
less than 2.4
Remove the ‘boot band,readjust
dimension (W) of step (3)
calculated by the following equation,
a new B.J. band to
5.5 mm in.)
Example: If is 2.3 is
3.2 m m
TSB Revision