DATSUN 210 1979 Service Manual
Manufacturer: DATSUN, Model Year: 1979, Model line: 210, Model: DATSUN 210 1979Pages: 548, PDF Size: 28.66 MB
Page 461 of 548
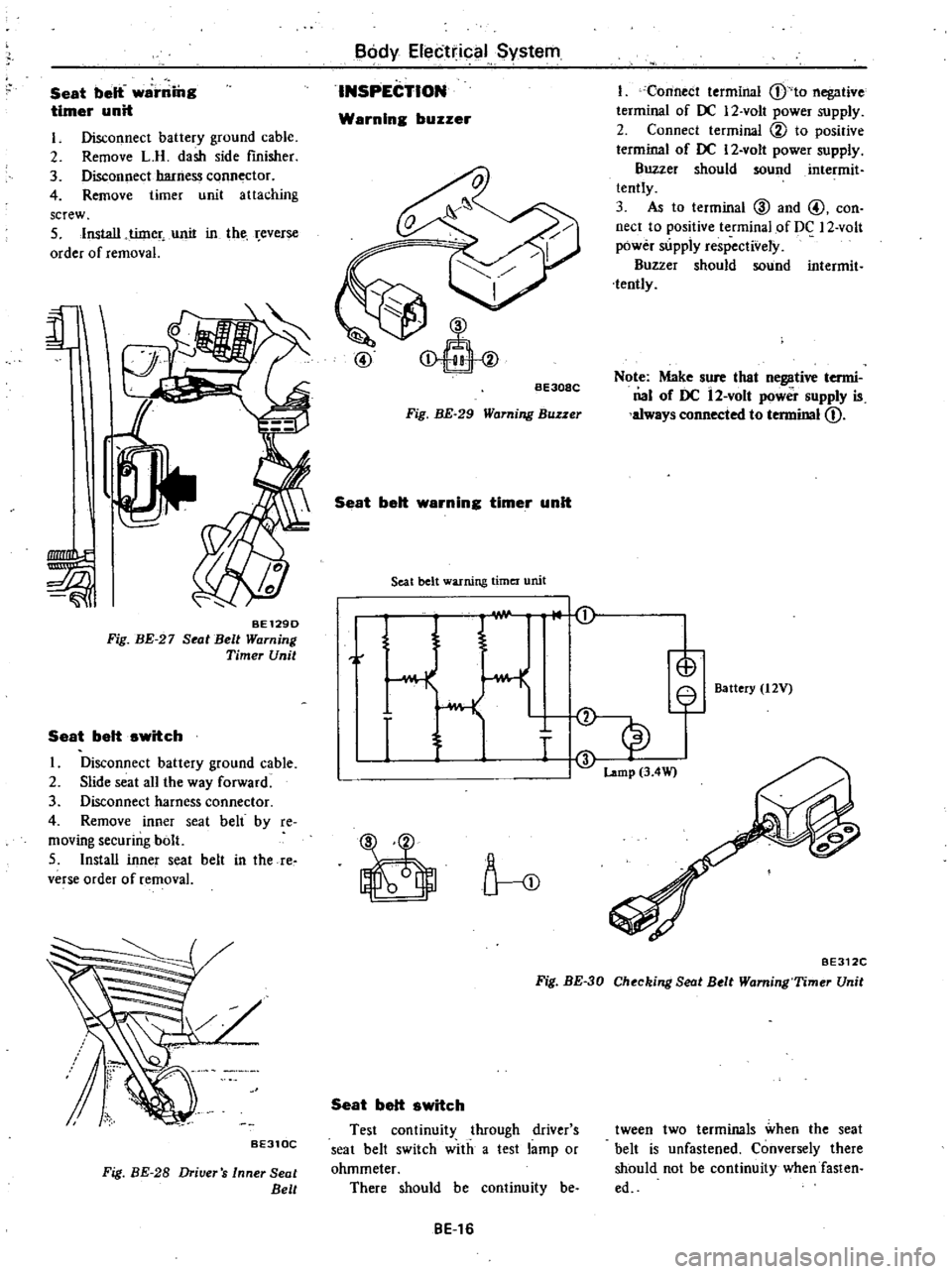
Seat
belt
wammg
timer
unit
1
Disconnect
battery
ground
cable
2
Remove
L
A
dash
side
finisher
3
Disconnect
b
arness
conn
ctor
4
Remove
timer
unit
attaching
screw
S
Install
timer
unit
in
the
everse
order
of
removal
BE1290
Fig
BE
27
Seat
Belt
Warning
Timer
Unit
Seat
belt
switch
I
Disconnect
battery
ground
cable
2
Slide
seat
all
the
way
forward
3
Disconnect
harness
connector
4
Remove
inner
seat
belt
by
re
moving
securing
bolt
5
Install
inner
seat
belt
in
the
re
verse
order
of
removal
BE31QC
Fig
BE
28
Driver
s
Inner
Seat
Belt
Body
Electrical
System
INSPECTION
Warning
buzzer
BE308C
Fig
BE
29
Warning
Buzzer
Seat
belt
warning
timer
unit
Seat
belt
warning
timer
unit
I
Y
o
j
r
tIT
I
Connect
terminal
j
to
negative
terminaI
of
DC
12
volt
power
supply
2
Connect
terminal
to
positive
terminal
of
DC
12
volt
power
supply
Buzzer
should
sound
intermit
tent
y
3
As
to
terminal
@
and
@
con
nect
to
positive
terminal
of
DC
12
volt
power
supply
respectively
Buzzer
should
sound
intermit
tently
Note
Make
sure
that
negative
termi
nal
of
DC
12
volt
power
supply
is
a1ways
connected
to
tenninal
CD
Q
e
Battery
t2V
Lamp
3
4W
BE312C
Fig
BE
30
Checking
Seat
Belt
Warning
Timer
Unit
Seat
belt
switch
Test
continuity
through
driver
s
seat
belt
switch
with
a
test
lamp
or
ohmmeter
There
should
be
continuity
be
BE
16
tween
two
terminals
when
the
seat
belt
is
unfastened
Conversely
there
should
not
be
continuity
when
fasten
ed
Page 462 of 548
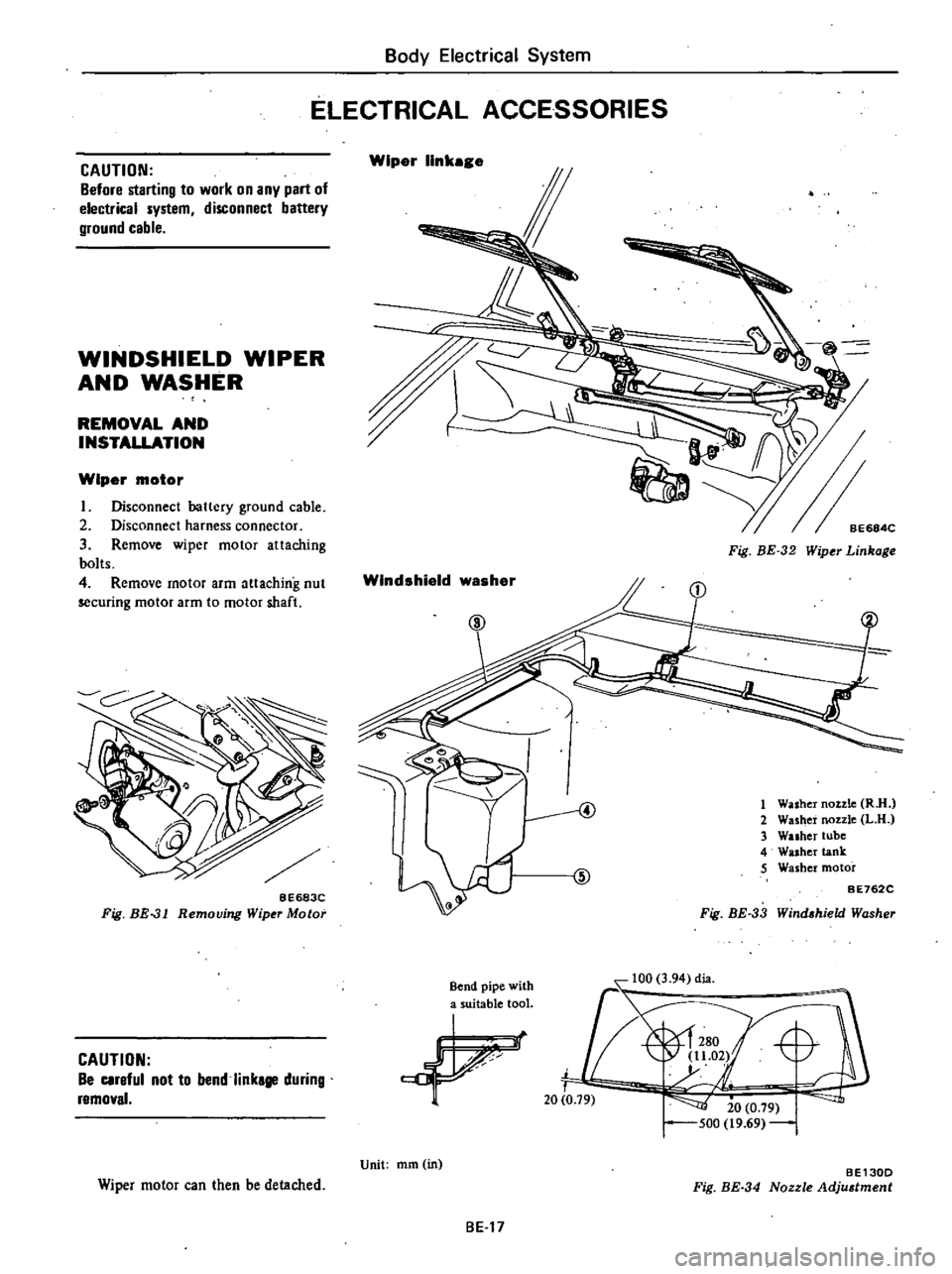
CAUTION
Before
starting
to
work
on
any
part
of
electrical
system
disconnect
battery
ground
cable
WINDSHIELD
WIPER
AND
WASHER
REMOVAL
AND
INSTALLATION
Wiper
motor
I
Disconnect
battery
ground
cable
2
Disconnect
harness
connector
3
Remove
wiper
motor
attaching
bolts
4
Remove
motor
arm
attaching
nut
securing
motor
arm
to
motor
shaft
BE683C
Fig
BE
31
Removing
Wiper
Motor
CAUTION
Be
careful
not
to
bend
linkage
during
removal
Wiper
motor
can
then
be
detached
Body
Electrical
System
ELECTRICAL
ACCESSORIES
Wiper
linkage
Fig
BE
32
Wiper
Linkage
Windshield
washer
J
I
d4
ID
1
Washer
nozzle
R
n
2
Washer
nozzle
L
U
3
Wuher
tube
4
Washer
tank
5
Washer
motor
BE762C
Fig
BE
33
Wind
hield
Washer
Bend
pipe
with
a
suitable
tool
4
Unit
mm
in
BE130D
Fig
BE
34
Nozzle
Adju
tment
BE
17
Page 463 of 548
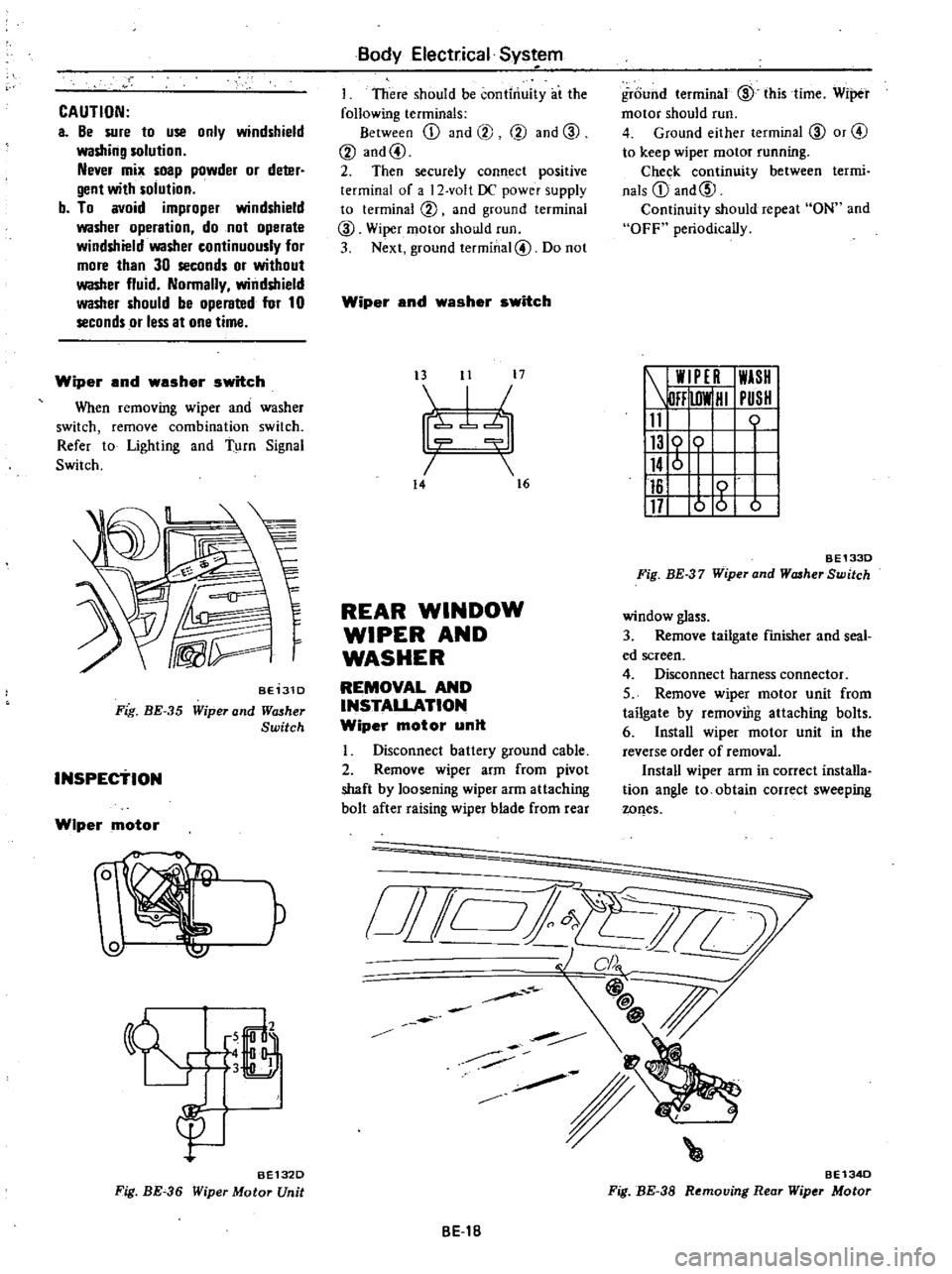
CAUTION
a
Be
sure
to
use
only
windshield
washing
solution
Never
mix
soap
powder
or
deter
gent
with
solution
b
To
avoid
improper
windshield
washer
operation
do
not
operate
windshield
washer
continuously
for
more
than
30
seconds
or
without
washer
fluid
Normally
windshield
washer
should
be
operated
for
10
seconds
or
less
at
one
time
Wiper
and
washer
switch
When
removing
wiper
and
washer
switch
remove
combination
switch
Refer
to
Lighting
and
Turn
Signal
Switch
BE131D
Fig
BE
35
Wiper
and
Wll5her
Switch
INSPEctiON
Wiper
motor
W
P
6
LJ
3
B
gu
BE132D
Fig
BE
36
Wiper
Motor
Unit
Body
Electrical
Sys
em
I
There
should
be
continuity
at
the
following
terminals
Between
ill
and
@
@
and
CID
@
and@
2
Then
securely
connect
positive
terminal
of
a
2
volt
DC
power
supply
to
terminal
@
and
ground
terminal
CID
Wiper
motor
should
run
3
Next
ground
terminal@
Do
not
Wiper
and
washer
switch
t3
11
17
I
7b
14
16
REAR
WINDOW
WIPER
AND
WASHER
REMOVAL
AND
INSTALLATION
Wiper
motor
unit
Disconnect
battery
ground
cable
2
Remove
wiper
arm
from
pivot
shaft
by
loosening
wiper
arm
attaching
bolt
after
raising
wiper
blade
from
rear
o
i
Jill
BE1B
ground
terminal
CID
this
time
Wiper
motor
should
run
4
Ground
either
terminal
CID
or
@
to
keep
wiper
motor
running
Chec
k
continuity
between
termi
nals
ill
and@
Continuity
should
repeat
ON
and
OFF
periodically
W
PE
I
WASH
DFF
lOW
HI
PUSH
11
0
116
117
o
g
b
BE1330
Fig
BE
37
Wiper
and
WcuherSwitch
window
glass
3
Remove
tailgate
finisher
and
seal
ed
screen
4
Disconnect
harness
connector
5
Remove
wiper
motor
unit
from
tailgate
by
removiDg
attaching
bolts
6
Install
wiper
motor
unit
in
the
reverse
order
of
removal
Install
wiper
arm
in
correct
installa
tion
angle
to
obtain
correct
sweeping
wQes
BE134D
Fig
BE
38
Removing
Rear
Wiper
Motor
Page 464 of 548
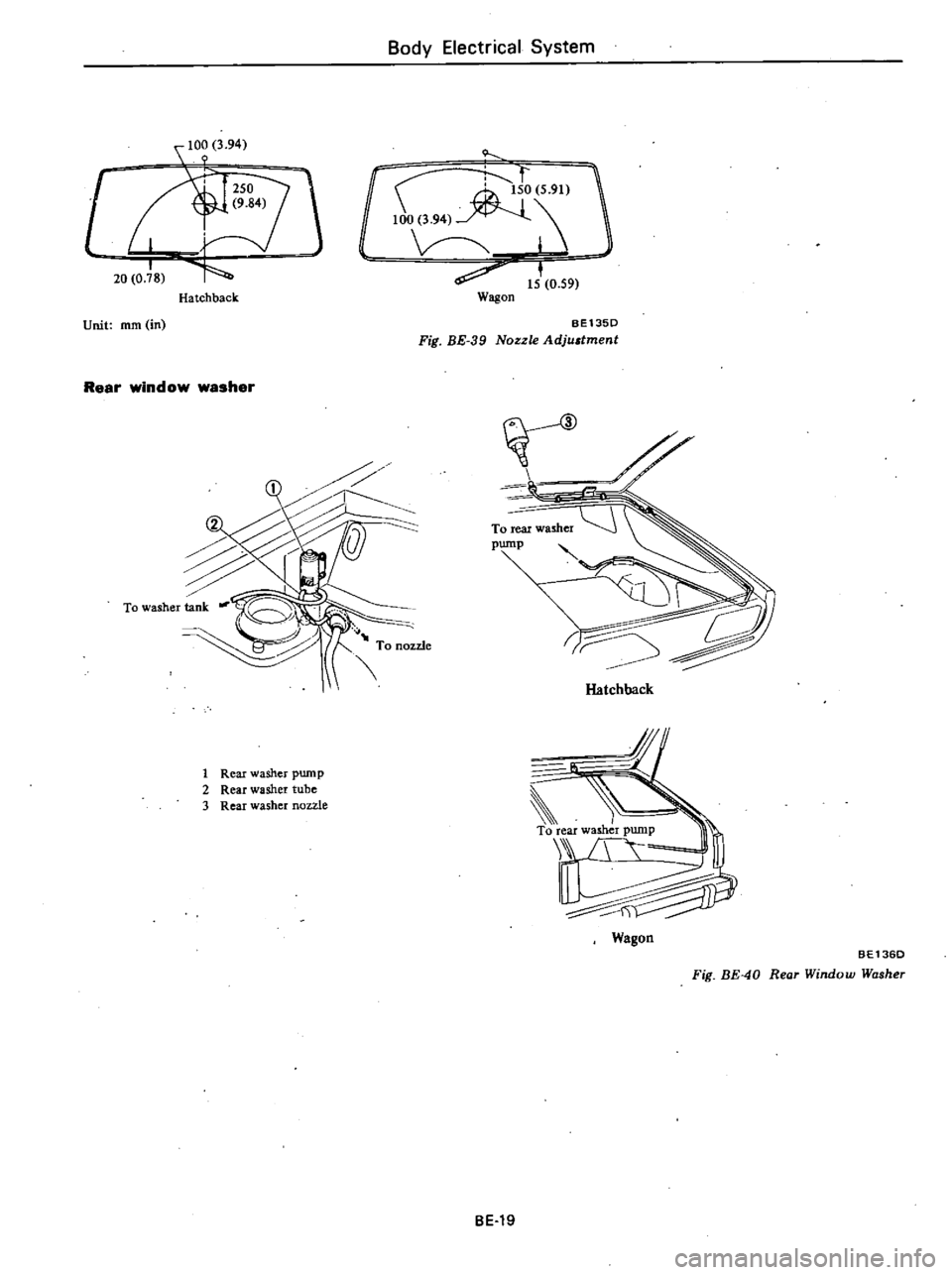
Body
Electrical
System
1
1
0
5
91
100
G
I
20
0
78
Hatchback
Unit
mm
in
Wagon
BE135D
Fig
BE
39
Nozzle
Adju
tment
Rear
window
washer
To
nozzle
1
Rear
washer
pump
2
Rear
washer
tube
3
Rear
washer
nozzle
I
c
Hatchback
r
To
rear
washer
pump
1
I
Wagon
BE136D
Fig
BE40
Rear
Window
Washer
BE
19
Page 465 of 548
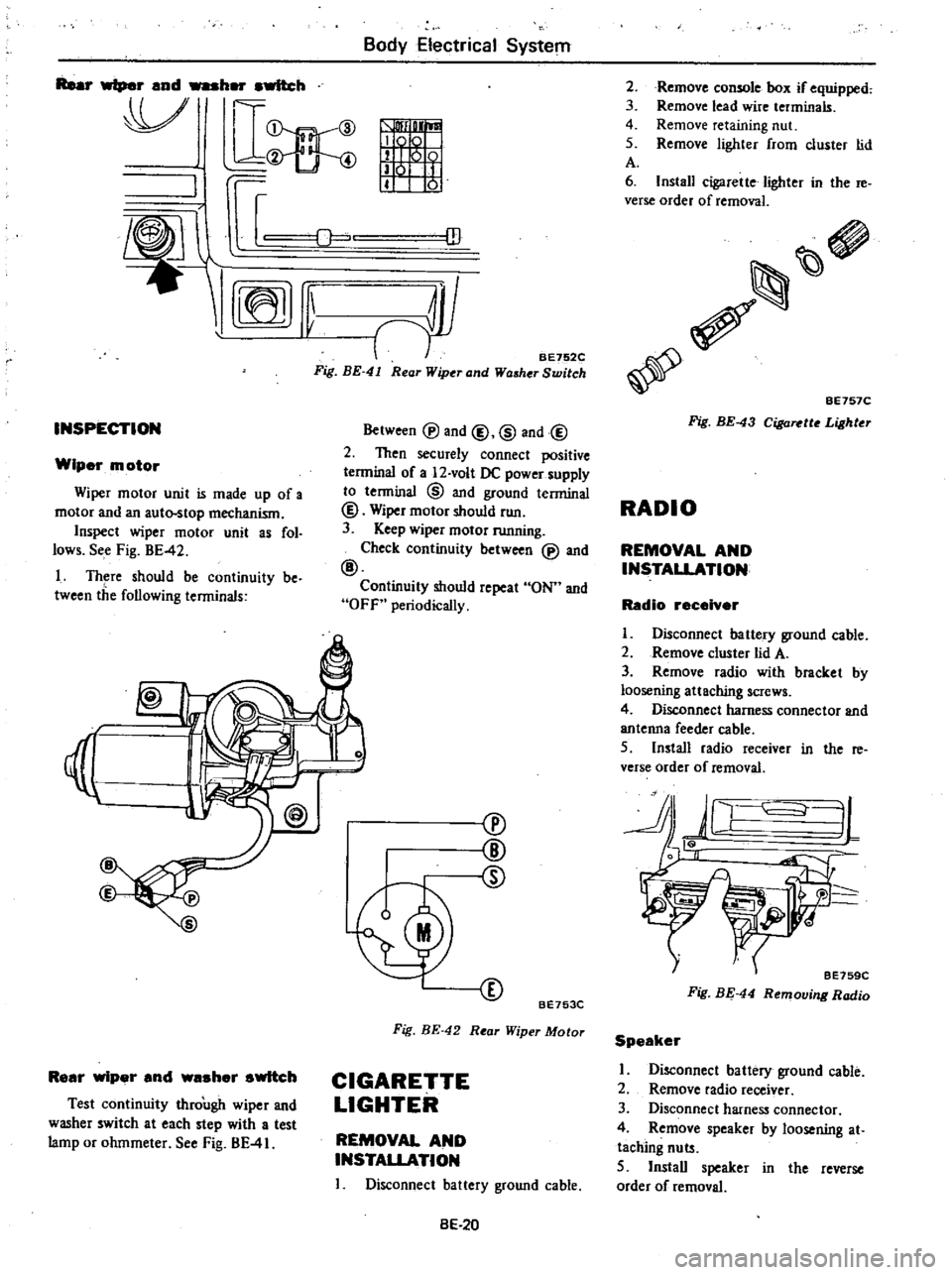
Rear
wiper
and
her
awltch
V
D
mn
ID
I
INSPECTION
Wiper
motor
Wiper
motor
unit
is
made
up
of
a
motor
and
an
auto
stop
mechanism
Inspect
wiper
motor
unit
as
fol
lows
See
Fig
BE
42
I
Th
re
should
be
continuity
be
tween
the
following
terminals
Body
Electrical
System
ill
BE752C
Fig
BE
41
Rear
Wiper
and
Washer
Switch
Between
@
and
@
@
and@
2
Then
securely
connect
positive
terminal
of
a
12
volt
DC
power
supply
to
tenninal
@
and
ground
terminal
@
Wiper
motor
should
run
3
Keep
wiper
motor
running
Check
continuity
between
@
and
@
Continuity
should
repeat
ON
and
OFf
periodically
I
Rear
wiper
and
waaher
switch
Test
continuity
through
wiper
and
washer
switch
at
each
step
with
a
test
lamp
or
ohmmeter
See
Fig
BE
41
cv
@
CD
BE753C
Fig
BE
42
Rear
Wiper
Motor
CIGARETTE
LIGHTER
REMOVAL
AND
INSTALLATION
I
Disconnect
battery
ground
cable
BE
20
Remove
comole
box
if
equipped
Remove
lead
wire
terminals
Remove
retaining
nut
Remove
lighter
from
cluster
lid
2
3
4
5
A
6
Install
cigarette
lighter
in
the
re
verse
order
of
removal
BE757C
Fig
BE
43
CiI
a
tto
Lighter
RADIO
REMOVAL
AND
INSTALLATION
Radio
receiver
I
Disconnect
battery
ground
cable
2
Remove
cluster
lid
A
3
Remove
radio
with
bracket
by
loosening
attaching
screws
4
DiscOnnect
harness
connector
and
antenna
feeder
cable
5
Install
radio
receiver
in
the
re
verse
order
of
removal
JL
J
tf
BE759C
Fig
BE
44
Removing
Radio
Speaker
I
Disconnect
battery
ground
cable
2
Remove
radio
receiver
3
Disconnect
harness
connector
4
Remove
speaker
by
loosening
at
taching
nuts
5
Install
speaker
in
the
reverse
order
of
removal
Page 466 of 548
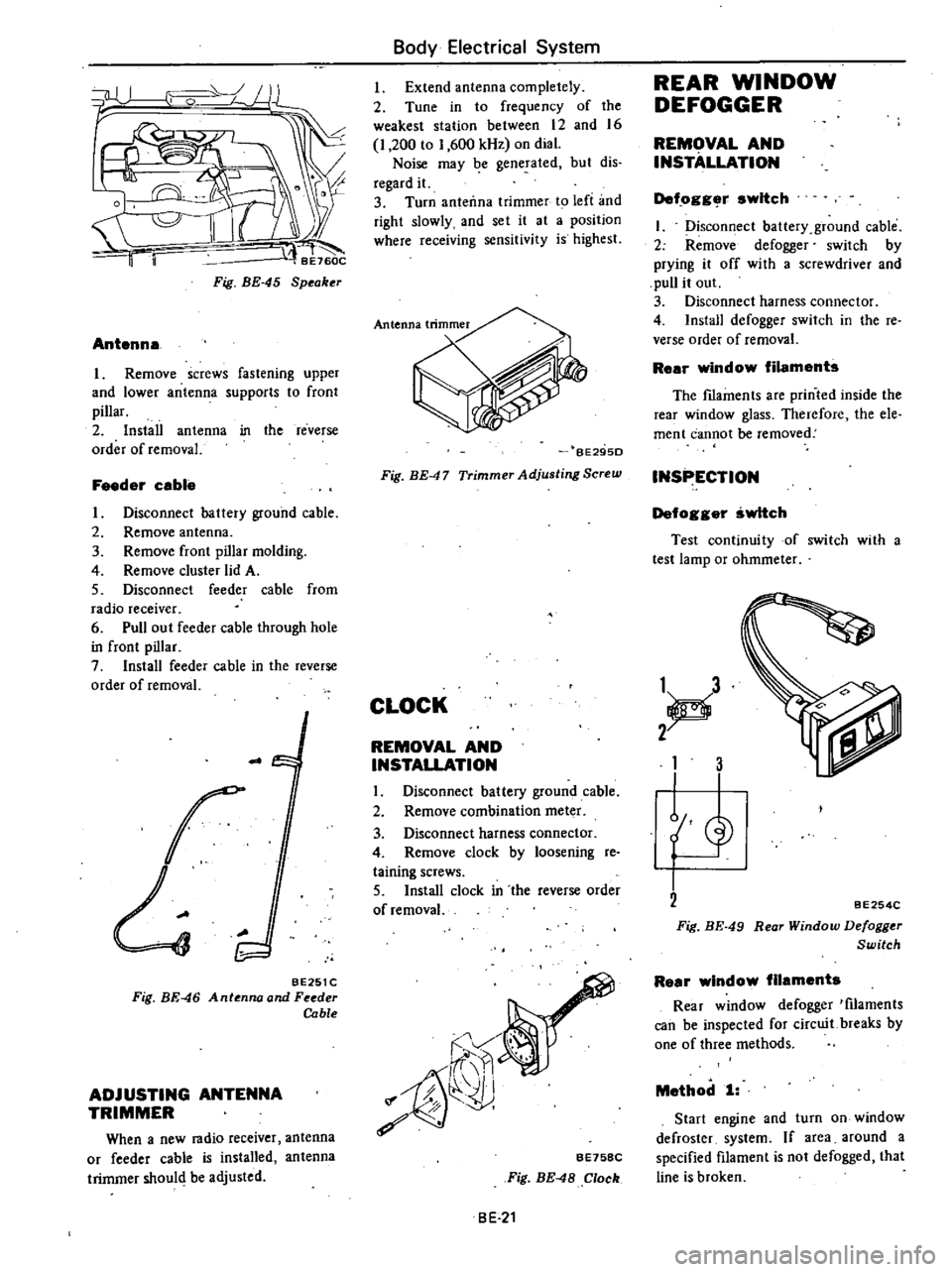
t
Fig
BE
45
Speaker
Antenna
Remove
screws
fastening
upper
and
lower
antenna
supports
to
front
pillar
2
Install
antenna
in
the
reverse
order
of
removal
Feeder
cable
I
Disconnect
battery
ground
cable
2
Remove
antenna
3
Remove
front
pillar
molding
4
Remove
cluster
lid
A
5
Disconnect
feeder
cable
from
radio
receiver
6
Pull
out
feeder
cable
through
hole
in
front
pillar
7
Install
feeder
cable
in
the
reverse
order
of
removal
r
BE251C
Fig
BE
46
Antenna
and
Feeder
Cable
ADJUSTING
ANTENNA
TRIMMER
When
a
new
radio
receiver
antenna
or
feeder
cable
is
installed
antenna
trimmer
shoul
be
adjusted
Body
Electrical
System
Extend
antenna
completely
2
Tune
in
to
frequency
of
the
weakest
station
between
12
and
16
I
200
to
1
600
kHz
on
dial
Noise
may
be
generated
but
dis
regard
it
3
Turn
anteiln3
trimmer
to
left
and
right
slowly
and
set
it
at
a
position
where
receiving
sensitivity
is
highest
BE29SD
Fig
BE
47
Trimmer
Adjusting
Screw
CLOCK
REMOVAL
AND
INSTALLATION
I
Disconnect
battery
ground
cable
2
Remove
combination
meter
3
Disconnect
harness
connector
4
Remove
clock
by
loosening
re
taining
screws
5
Install
clock
in
the
reverse
order
of
removal
r
Jf
rr
i1
b
Ii
f
7
8
eE758C
Fig
BE
48
Clock
BE
21
REAR
WINDOW
DEFOGGER
REMOVAL
AND
INSTALLATION
Def
ogg
r
switch
I
Disconfi
ect
battery
ground
cable
2
Remove
defogger
switch
by
prying
it
off
with
a
screwdriver
and
pull
it
out
3
Disconnect
harness
connector
4
Install
defogger
switch
in
the
reo
verse
order
of
removal
Rear
window
filaments
The
fIlaments
are
printed
inside
the
rear
window
glass
Therefore
the
ele
ment
cannot
be
removed
INSPECTION
Defogger
switch
Test
continuity
of
switch
with
a
test
lamp
or
ohmmeter
1
d
2
1
3
L
BE254C
Fig
BE
49
Rear
Window
Defogger
Switch
Rear
window
filaments
Rear
window
defogger
tfilaments
can
be
inspected
for
circuit
breaks
by
one
of
three
methods
Method
1
Start
engine
and
turn
on
window
defroster
system
If
area
around
a
specified
filament
is
not
defogged
that
line
is
broken
Page 467 of 548
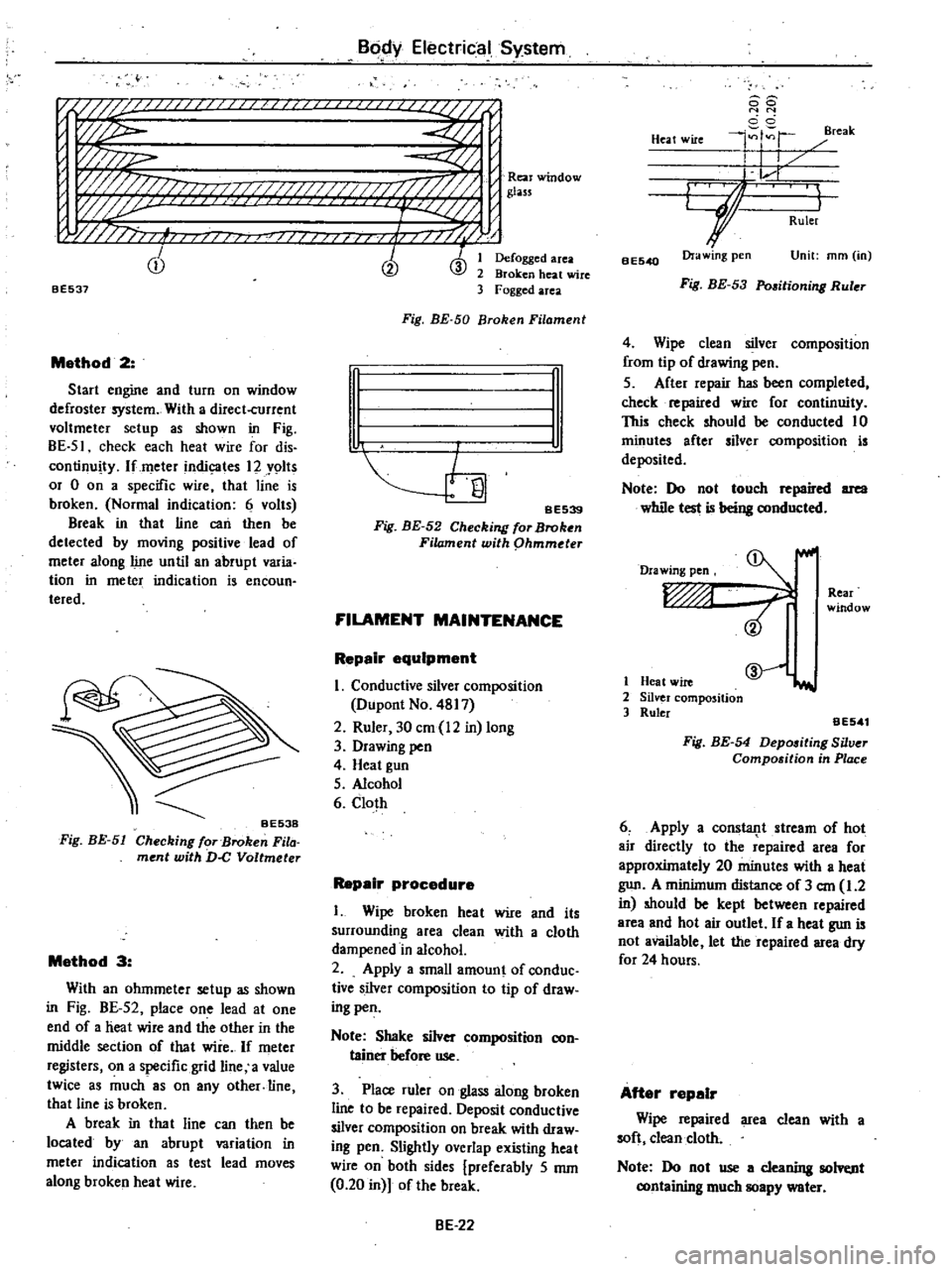
B6
Y
Electrica
System
f
EIIII
I
I
I
11111111
111
777
Rea
window
1
j
glass
W
777
n
1
r7
U
u
T
t
I
I
I
j
T
cD
t
ID
3
BE537
Method
2
Start
engine
and
turn
on
window
defroster
system
With
a
direct
current
voltmeter
setup
as
shown
in
Fig
BE
51
check
each
heat
wire
for
dis
continuity
lfmeter
indic
ates
12
Y9lts
or
0
on
a
specific
wire
that
line
is
broken
Normal
indication
6
volts
Break
in
that
line
can
then
be
detected
by
moving
positive
lead
of
meter
along
line
until
an
abrupt
varia
tion
in
meter
indication
is
encoun
teredo
Fig
BE
51
Method
3
With
an
ohmmeter
setup
as
shown
in
Fig
BE
52
place
one
lead
at
one
end
of
a
heat
wire
and
the
other
in
the
middle
section
of
that
wire
If
meter
registers
on
a
specific
grid
line
a
value
twice
as
much
8S
on
any
other
line
that
line
is
broken
A
break
in
tha
t
line
can
then
be
located
by
an
abrupt
variation
in
meter
indication
as
test
lead
moves
along
broken
heat
wire
Defogged
area
Broken
heat
wire
Fogged
area
Fig
BE
50
Broken
Filament
n
I
I
SE539
Fig
BE
52
Checking
for
Broken
Filament
with
phmmder
FILAMENT
MAINTENANCE
Repair
equipment
I
Conductive
silver
composition
Dupont
No
4817
2
Ruler
30
em
12
in
long
3
Drawing
pen
4
Heat
gun
5
Alcohol
6
Cloth
Repair
procedure
I
Wipe
broken
heat
wire
and
its
surrounding
area
clean
with
a
cloth
dampened
in
alcohol
2
Apply
a
small
amount
of
conduc
tive
silver
composition
to
tip
of
draw
ing
pen
Note
Shake
silver
composition
con
tainer
before
use
3
Place
ruler
on
glass
along
broken
line
to
be
repaired
Deposit
conductive
silver
composition
on
break
with
draw
ing
pen
Slightly
overlap
existing
heat
wire
on
both
sides
preferably
5
mm
0
20
in
of
the
break
BE
22
88
N
N
cci
4
r
reak
Heat
wire
I
I
L
r
GJ
I
Ruler
BE540
Ora
wing
pen
Unit
mm
in
Fig
BE
53
Pmitioning
Ruler
4
Wipe
clean
silver
composition
from
tip
of
drawing
pen
5
After
repair
has
been
completed
check
repaired
wire
for
continuity
This
check
should
be
conducted
10
minutes
after
silver
composition
is
deposited
Note
Do
not
touch
repaired
area
while
test
is
being
conducted
Drawing
pen
Rear
window
1
Heat
wire
2
Silver
composition
3
Ruler
@
iI
aE541
Fig
BE
54
Depositing
Silver
Compo
ition
in
Place
6
Apply
a
consla11t
stream
of
hot
air
directly
to
the
repaired
area
for
approxUnately
20
minutes
with
a
heat
gun
A
minilnum
distance
of
3
em
1
2
in
should
be
kept
between
repaired
area
and
hot
air
outlet
If
a
heat
gun
is
not
available
let
the
repaired
area
dry
for
24
hours
After
repair
Wipe
repaired
area
clean
with
a
soft
clean
cloth
Note
Do
not
use
a
cleaning
solvt
nt
containing
much
soapy
water
Page 468 of 548
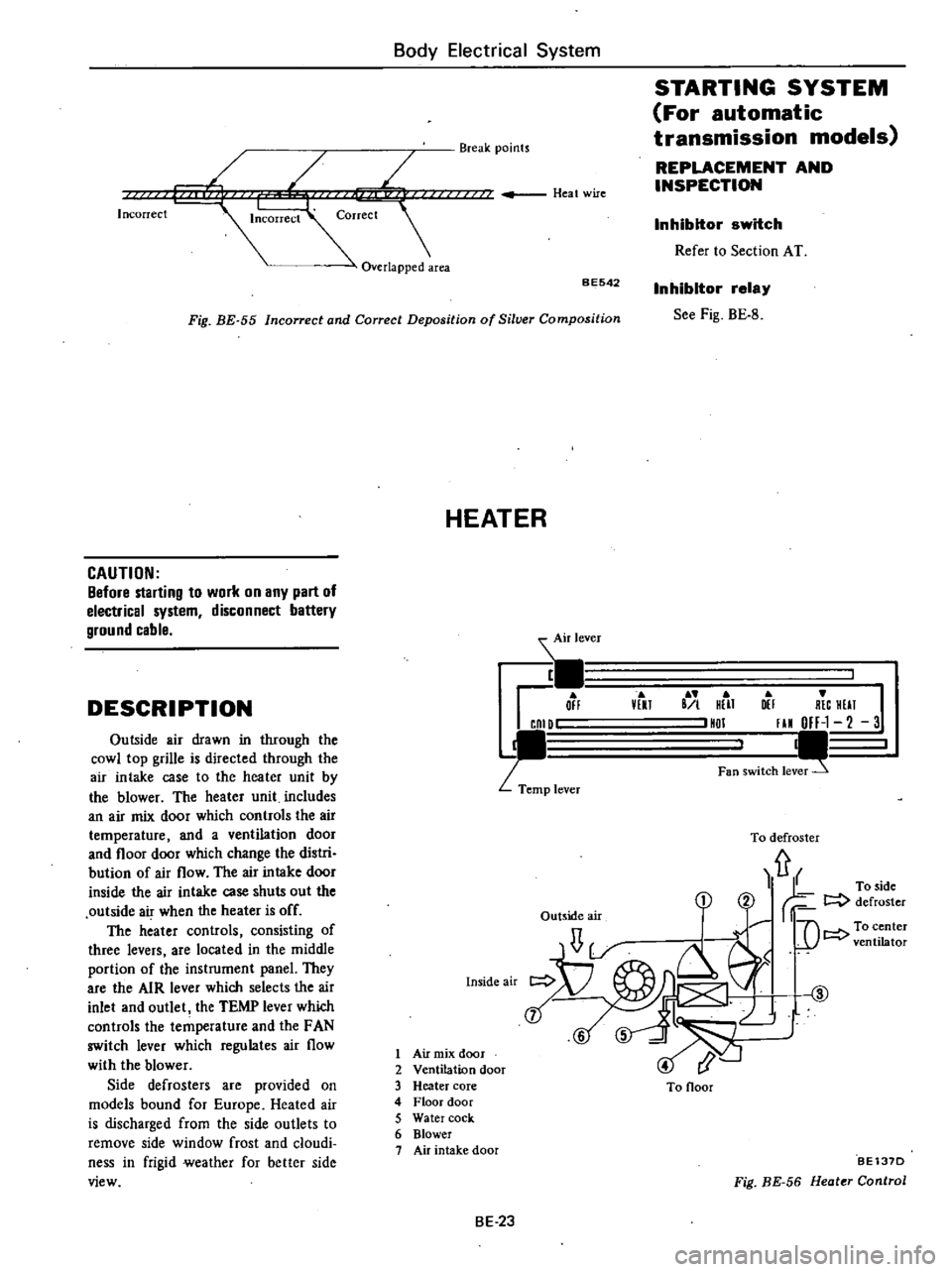
Body
Electrical
System
Incorrect
Overlapped
area
Hea
t
wire
STARTING
SYSTEM
For
automatic
transmission
models
REPLACEMENT
AND
INSPECTION
Break
points
Inhibitor
switch
Refer
to
Section
AT
BE542
Inhibitor
relay
See
Fig
BE
B
Fig
BE
55
Incorrect
and
Correct
Deposition
of
Silver
Composition
HEATER
CAUTION
Before
starting
to
work
on
any
part
of
electrical
system
disconnect
battery
ground
cable
DESCRIPTION
Air
lever
1
Off
CnID
p
lever
lEU
B
I
HUT
HDI
DEI
R
C
HUT
I
III
OFF
1
2
3
I
Fan
switch
lev
Outside
air
drawn
in
through
the
cowl
top
grille
is
directed
through
the
air
intake
case
to
the
heater
unit
by
the
blower
The
heater
unit
includes
an
air
mix
door
which
controls
the
air
temperature
and
a
ventilation
door
and
floor
door
which
change
the
distri
bution
of
air
flow
The
air
intake
door
inside
the
air
intake
case
shuts
out
the
outside
air
when
the
heater
is
off
The
heater
controls
consisting
of
three
levers
are
located
in
the
middle
portion
of
the
instrument
panel
They
are
the
AIR
lever
which
selects
the
air
inlet
and
outlet
the
TEMP
lever
which
controls
the
temperature
and
the
FAN
switch
lever
which
regulates
air
flow
with
the
blower
Side
defrosters
are
provided
on
models
bound
for
Europe
Heated
air
is
discharged
from
the
side
outlets
to
remove
side
window
frost
and
cloudi
ness
in
frigid
weather
for
better
side
view
Inside
air
To
defroster
fr
1
rf
To
side
r
2
t
defroster
1
U
C
D
i
LJ
t
@
6
5
Outside
air
1
Air
mix
door
2
Ventilation
door
3
Heater
core
4
Floor
door
5
Water
cock
6
Blower
7
Air
intake
door
To
Ooor
BE137D
Fig
BE
56
Heater
Control
BE
23
Page 469 of 548
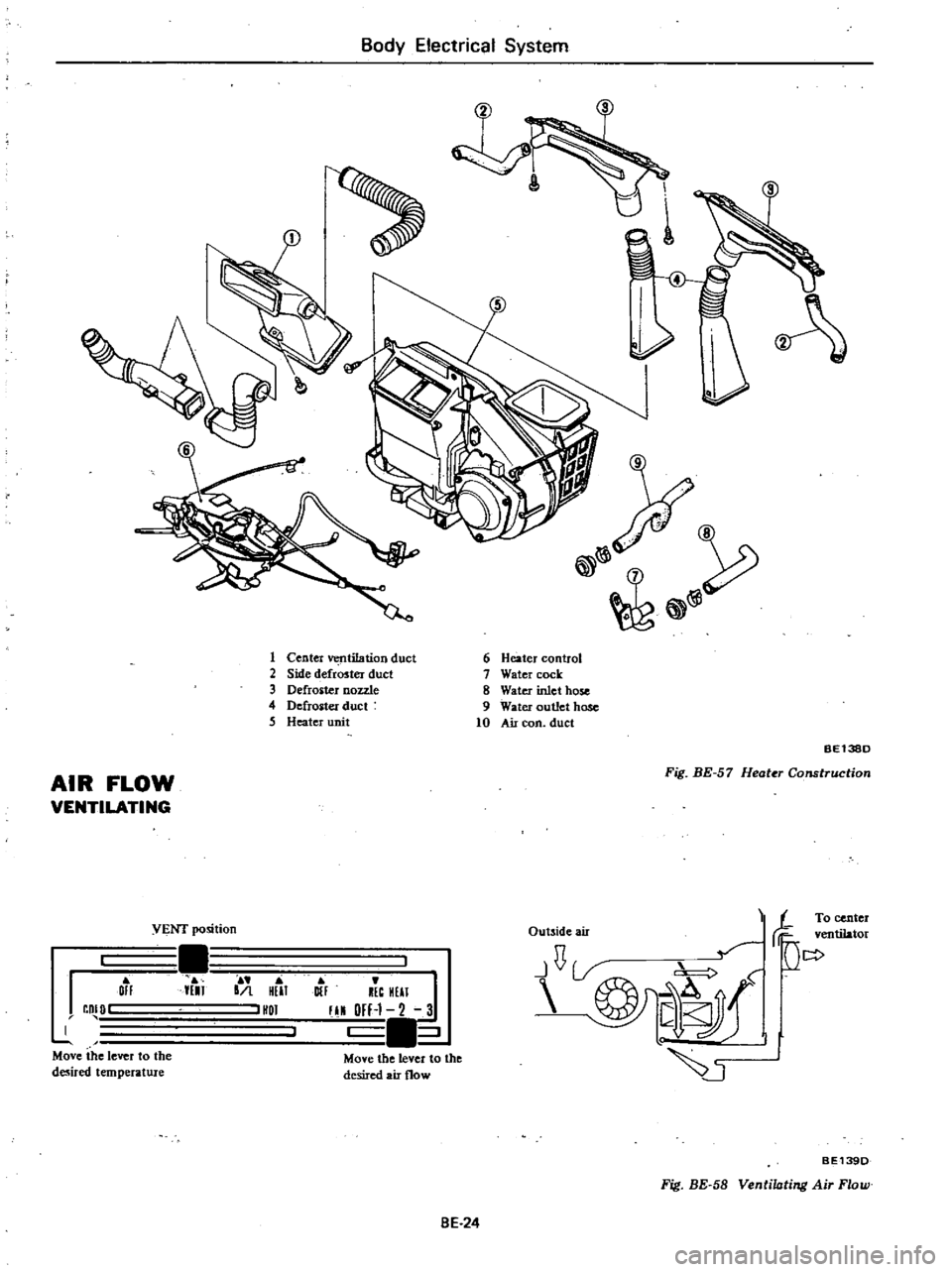
Body
Electrical
System
t
to
liP
1
ill
1
Center
V
t
fltilation
duct
2
Side
defroster
duct
3
Defroster
nozzle
4
Defroster
duct
5
Heater
unit
6
Heater
control
7
Water
cock
8
Water
inlet
hose
9
Water
outlet
hose
10
Air
con
duct
BEl38D
AIR
FLOW
VENTILATING
Fig
BE
57
Heater
Construction
I
Off
COlD
r
IUl
1
1
HUT
HOl
y
OIF
HEC
HEll
fll
OFl
l
2
3
J
Move
the
lever
to
the
desired
air
flow
i
To
center
Duwde
air
ventilator
J
U
V
D
ir
VENT
position
Move
the
lever
to
the
desired
temperature
BEl39D
Fig
BE
58
VentiIDting
Air
Flow
BE
24
Page 470 of 548
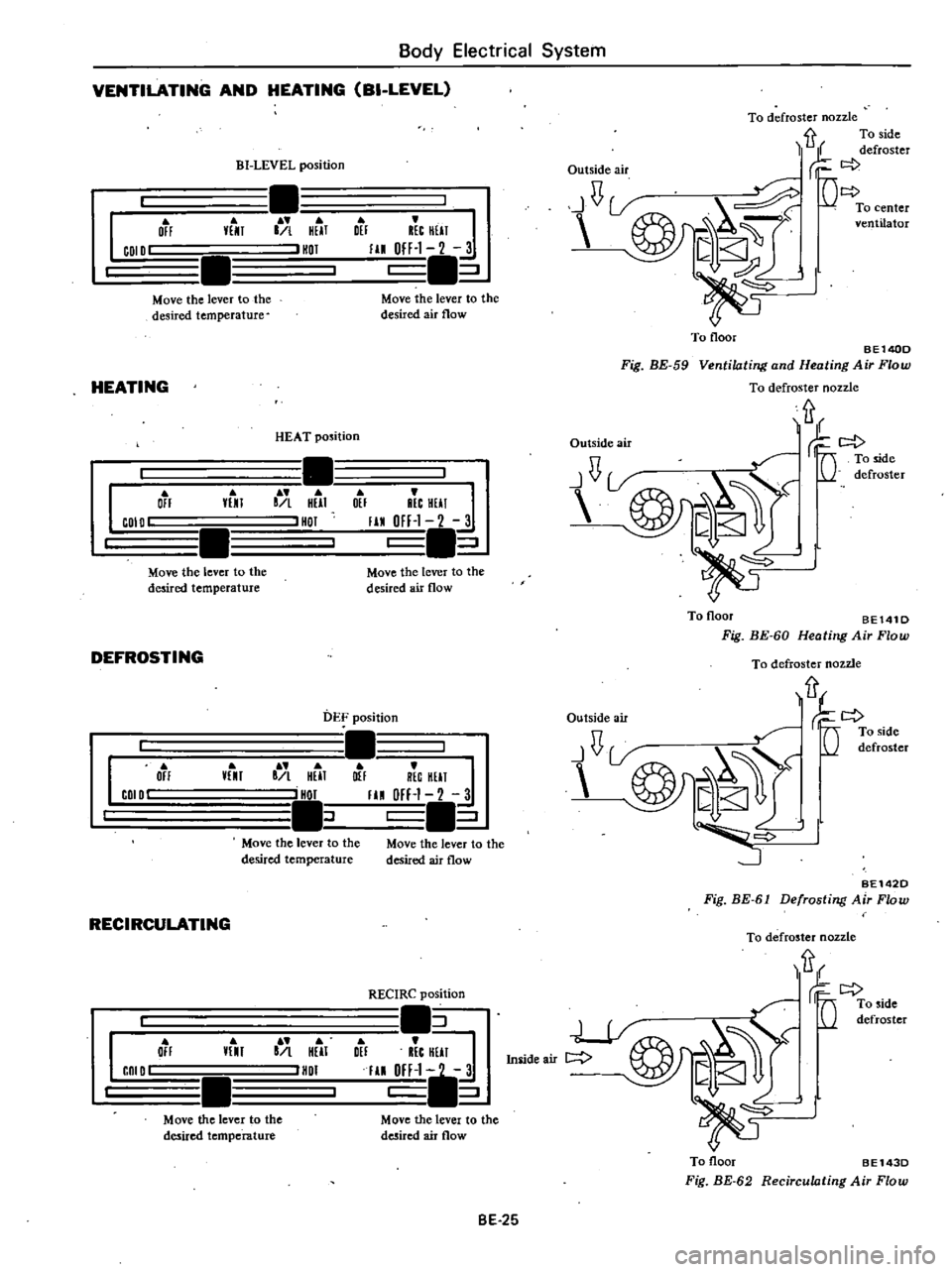
Body
Electrical
System
VENTILATING
AND
HEATING
BI
LEVEL
BI
LEVEL
position
COl
OFF
VENT
B
l
HElT
HOT
Move
the
lever
to
the
desired
temperature
HEATING
HEAT
position
OFF
IINl
COlO
L
HElT
HOT
Move
the
lever
to
the
desired
temperature
DEFROSTING
OFF
VENT
L
HElT
HOT
J
COlf
Move
the
lever
to
the
desired
temperature
RECIRCULATING
OFF
COlOr
VENT
L
HEll
HOT
Move
the
lever
to
the
desired
temperature
RECHEIl
fIN
OfF
1
2
3
Olf
Move
the
lever
to
the
desired
air
flow
I
Olf
RECHll
FIN
OfF
1
2
3
Move
the
lever
to
the
desired
air
flow
OEF
position
Olf
RECHll
fIN
OFH
2
3
Move
the
lever
to
the
desired
air
flow
RECIRC
position
J
1
OEf
RECHEIl
fIN
PfF
I
3
J
Move
the
lever
to
the
desired
air
flow
BE
25
To
defroster
nozzle
ft
To
side
L
defroster
Outside
air
L
c
U
D
l
To
floor
BEl40D
Fig
BE
59
Ventilating
and
Heating
Air
Flow
To
defroster
nozzle
fr
Outside
air
c
t
Ul
B
yO
Toflaor
BE141D
Fig
BE
60
Heating
Air
Flow
To
defroster
nozzle
fr
Outside
air
Ul
@Jtc
Y
D
l
1
BE142D
Fig
BE
61
Defrosting
Air
Flow
To
defroster
nozzle
LJ
Iniideair
c
@
To
floor
BE143D
Fig
BE
62
Recirculating
Air
Flow