DATSUN 210 1979 Service Manual
Manufacturer: DATSUN, Model Year: 1979, Model line: 210, Model: DATSUN 210 1979Pages: 548, PDF Size: 28.66 MB
Page 521 of 548
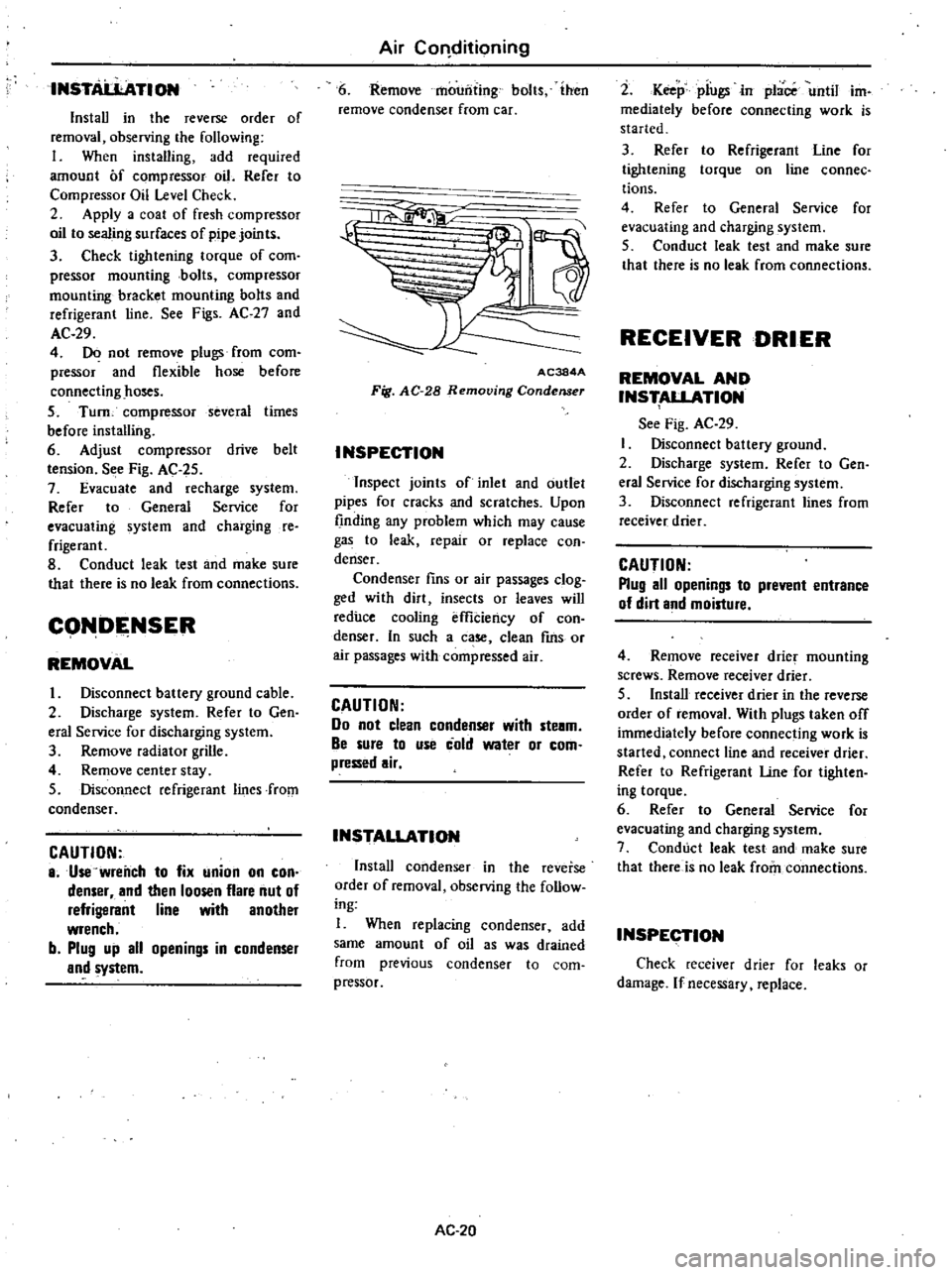
INSTA
L1ATION
InstaU
in
the
reverse
order
of
removal
observing
the
following
I
When
installing
add
required
amount
Of
compressor
oil
Refer
to
Compressor
Oil
Level
Check
2
Apply
a
coat
of
fresh
compressor
oil
to
sealing
surfaces
of
pipe
joints
3
Check
tightening
torque
of
com
pressor
mounting
bolts
compressor
mounting
bracket
mounting
bolts
and
refrigerant
line
See
Figs
AC
27
and
AC
29
4
DO
not
remove
plugs
from
com
pressor
and
flexible
hose
before
connecting
hoses
S
Turn
compressor
several
times
before
installing
6
Adjust
compressor
drive
belt
tension
See
Fig
AC
2S
7
Evacuate
and
recharge
system
Refer
to
General
Service
for
evacuating
system
and
charging
re
frigerant
8
Conduct
leak
test
and
make
sure
that
there
is
no
leak
from
connections
CONDE
NSER
REMOVAL
Disconnect
battery
ground
cable
2
Discharge
system
Refer
to
Gen
eral
Service
for
discharging
system
3
Remove
radiator
grille
4
Remove
center
stay
5
Disconnect
refrigerant
lines
from
condenser
CAUTION
8
Use
wrench
to
fix
union
on
con
denser
and
then
loosen
flare
nut
of
refrigerant
line
with
another
wrench
b
Plug
up
all
openings
in
condenser
and
system
Air
COl1ditioning
6
Remove
mounting
bolts
ihen
remove
condenser
from
car
1a
11
AC384A
Fig
AC
28
Removing
Condenser
INSPECTION
Inspect
joints
of
inlet
and
outlet
pipes
for
cracks
and
scratches
Upon
finding
any
problem
which
may
cause
gas
to
leak
repair
or
replace
con
denser
Condenser
fins
or
air
passages
clog
ged
with
dirt
insects
or
leaves
will
reduce
cooling
effiCiency
of
con
denser
In
such
a
case
clean
fms
or
air
passages
with
compressed
air
CAUTION
Do
not
clean
condenser
with
ste8m
Be
sure
to
use
cold
water
or
com
pressed
air
INSTALLATION
Install
condenser
in
the
reverse
order
of
removal
observing
Ihe
follow
ing
I
When
replacing
condenser
add
same
amount
of
oil
as
was
drained
from
previous
condenser
to
com
pressor
AC
20
2
Keep
piugsin
place
until
im
mediately
before
connecting
work
is
started
3
Refer
to
Refrigerant
Line
for
tightening
torque
on
line
connec
tions
4
Refer
to
General
Service
for
evacuating
and
charging
system
5
Conduct
leak
test
and
make
sure
that
there
is
no
leak
from
connections
RECEIVER
DRIER
REMOVAL
AND
INS
ALLATION
See
Fig
AC
29
Disconnect
battery
ground
2
Discharge
system
Refer
to
Gen
eral
Service
for
discharging
system
3
Disconnect
refrigerant
lines
from
receiver
drier
CAUTION
Plug
all
openings
to
prevent
entrance
of
dirt
and
moisture
4
Remove
receiver
drier
mounting
screws
Remove
receiver
drier
5
Install
receiver
drier
in
the
reverse
order
of
removal
With
plugs
taken
off
immediately
before
connecting
work
is
started
connect
line
and
receiver
drier
Refer
to
Refrigerant
Une
for
tighten
ing
torque
6
Refer
to
General
Service
for
evacuating
and
charging
system
7
Conduct
leak
test
and
make
sure
that
there
is
no
leak
from
connections
INSPECTION
Check
receiver
drier
for
leaks
or
damage
If
necessary
replace
Page 522 of 548
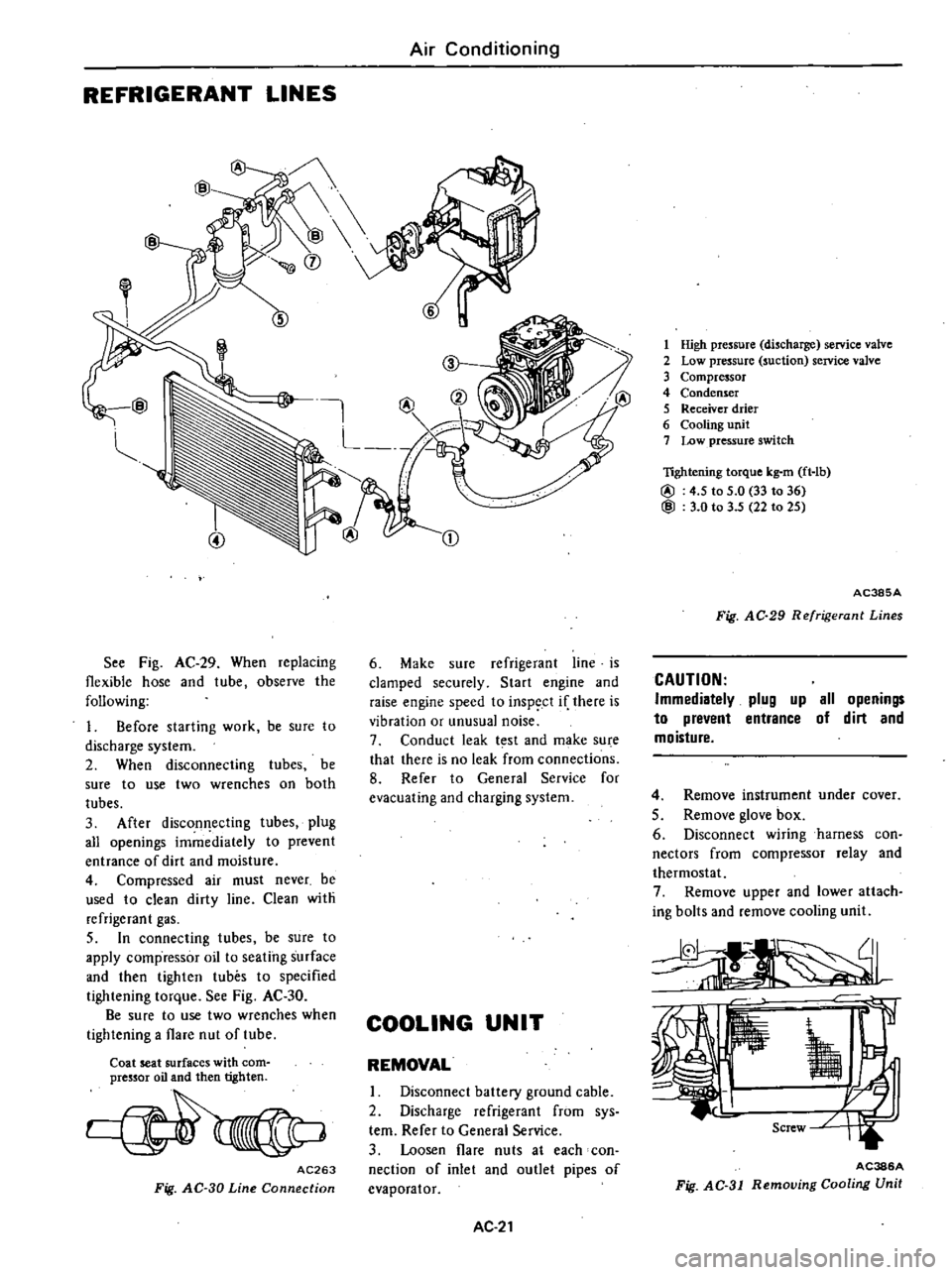
REFRIGERANT
LINES
Air
Conditioning
@
I
J
L
S
r
Z
S
t
@
See
Fig
AC
29
When
replacing
flexible
hose
and
tube
observe
the
following
1
Before
starting
work
be
sure
to
discharge
system
2
When
disconnecting
tubes
be
sure
to
use
two
wrenches
on
both
tubes
3
After
discon
ecting
tubes
plug
all
openings
immediately
to
prevent
entrance
of
dirt
and
moisture
4
Compressed
air
must
never
be
used
to
clean
dirty
line
Clean
with
refrigerant
gas
5
In
connecting
tubes
be
sure
to
apply
compressor
oil
to
seating
surface
and
then
tighten
tubes
to
specified
tightening
torque
See
Fig
AC
30
Be
sure
to
use
two
wrenches
when
tightening
a
flare
nut
of
tube
Coat
seat
surfaces
with
com
pressor
oil
and
then
tighten
AC263
Fig
AC
30
Line
Connection
CD
6
Make
sure
refrigerant
line
is
clamped
securely
Start
engine
and
raise
engine
speed
to
inspect
if
there
is
vibration
or
unusual
noise
7
Conduct
leak
t
st
and
make
su
e
that
there
is
no
leak
from
connections
8
Refer
to
General
Service
for
evacuating
and
charging
system
COOLING
UNIT
REMOVAL
I
Disconnect
battery
ground
cable
2
Discharge
refrigerant
from
sys
tern
Refer
to
General
Service
3
Loosen
flare
nuts
at
each
con
nection
of
inlet
and
outlet
pipes
of
evaporator
AC
21
1
High
pressure
discharge
service
valve
2
Low
pressure
suction
service
valve
3
Compressor
4
Condenser
5
Receiver
drier
6
Cooling
unit
7
Low
pressure
switch
lightening
torque
kg
m
ft
lb
@
4
5
to
5
0
33
to
36
@
3
0
to
3
5
22
to
25
AC385A
Fig
AC
29
Refrigerant
Lines
CAUTION
Immediatelv
plug
up
all
openings
to
prevent
entrance
of
dirt
and
moisture
4
Remove
instrument
under
cover
5
Remove
glove
box
6
Disconnect
wiring
harness
con
nectors
from
compressor
relay
and
thermostat
7
Remove
upper
and
lower
attach
ing
bolts
and
remove
cooling
unit
AC386A
Fig
AC
31
Removing
Cooling
Unit
Page 523 of 548
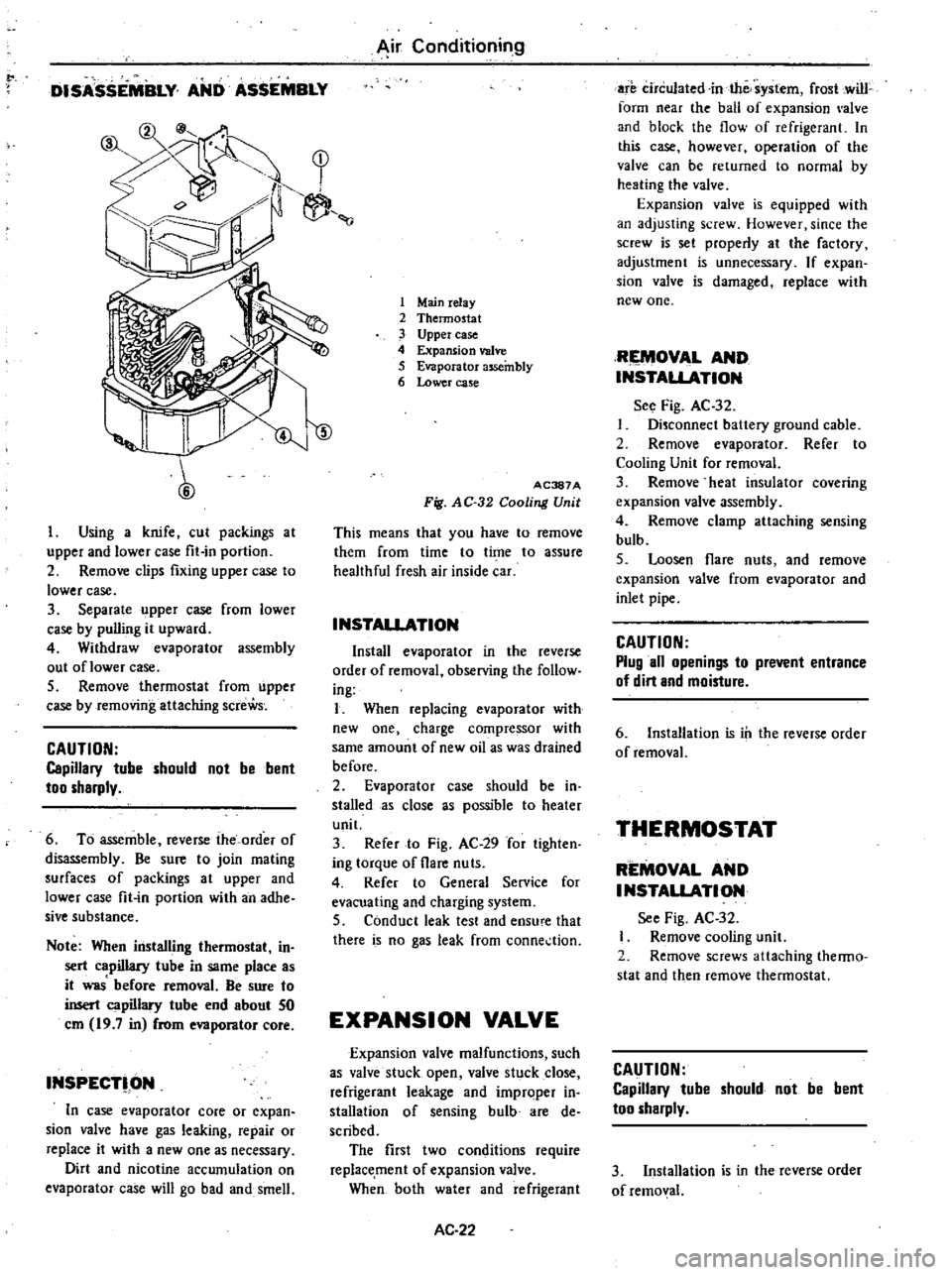
to
DISASSEMBLY
AND
ASSEMBLY
y
1
7
1
r
II
l
1
Using
a
knife
cut
packings
at
upper
and
lower
case
fit
in
portion
2
Remove
clips
fixing
upper
case
to
lower
case
3
Separate
upper
case
from
lower
case
by
pulling
it
upward
4
Withdraw
evaporator
assembly
out
oflower
case
5
Remove
thermostat
from
upper
case
by
removing
attaching
screWs
CAUTION
Capillary
tube
should
not
be
bent
too
sharply
6
To
assemble
reverse
the
order
of
disassembly
Be
sure
to
join
mating
surfaces
of
packings
at
upper
and
lower
case
fit
in
portion
with
an
adhe
sive
substance
Note
When
installing
thermostat
in
sert
capillary
tube
in
same
place
as
it
was
before
removal
Be
sure
to
insert
capillary
tube
end
about
50
em
19
7
in
from
evaporator
core
INSPECT
ON
In
case
evaporator
core
or
expan
sion
valve
have
gas
leaking
repair
or
replace
it
with
a
new
one
as
necessary
Dirt
and
nicotine
accumulation
on
evaporator
case
will
go
b
d
and
smell
Air
Conditioning
1
Mainrelay
2
Thermostat
3
Upper
case
4
Expansion
valve
5
Evaporator
assembly
6
Lower
case
ID
AC387A
Fig
AC
32
Cooling
Unit
This
means
that
you
have
to
remove
them
from
time
to
time
to
assure
healthful
fresh
air
inside
car
INSTAllATION
Install
evaporator
in
the
reverse
order
of
removal
observing
the
follow
ing
I
When
replacing
evaporator
with
new
one
charge
compressor
with
same
amount
of
new
oil
as
was
drained
before
2
Evaporator
case
should
be
in
stalled
as
close
s
possible
to
heater
unit
3
Refer
to
Fig
AC
29
for
tighten
ing
torque
of
flare
nuts
4
Refer
to
General
Service
for
evacuating
and
charging
system
5
Conduct
leak
test
and
ensu
e
that
there
is
no
gas
leak
from
conne
tion
EXPANSION
VALVE
Expansion
valve
malfunctions
such
as
valve
stuck
open
valve
stuck
close
refrigerant
leakage
and
improper
in
stall
tion
of
sensing
bulb
are
de
scribed
The
first
two
conditions
require
replacement
of
expansion
valve
When
both
water
and
refrigerant
AC
22
are
circulated
in
the
system
frost
cwill
form
near
the
ball
of
expansion
alve
and
block
the
flow
of
refrigerant
In
this
case
however
operation
of
the
valve
can
be
returned
to
normal
by
heating
the
valve
Expansion
valve
is
equipped
with
an
adjusting
screw
However
since
the
screw
is
set
properly
at
the
factory
adjustment
is
unnecessary
If
expan
sion
valve
is
damaged
replace
with
new
one
RIEMOV
L
AND
INSTALlATION
See
Fig
AC
32
Disconnect
baltery
ground
cable
2
Remove
ev
porator
Refer
to
Cooling
Unit
for
removal
3
Remove
heat
insulator
covering
expansion
valve
assembly
4
Remove
clamp
attaching
sensing
bulb
5
Loosen
flare
nuts
and
remove
expansion
valve
from
evaporator
and
inlet
pipe
CAUTION
Plug
all
openings
to
prevent
entrance
of
dirt
and
moisture
6
Installation
is
ill
the
reverse
order
of
removal
THERMOSTAT
REMOVAL
AND
INSTALlATION
See
Fig
AC
32
Remove
cooling
unit
2
Remove
screws
attaching
thenno
stat
and
then
remove
thermostat
CAUTION
Capillary
tube
should
not
be
bent
too
sharply
3
Installation
is
in
the
reverse
order
of
removal
Page 524 of 548
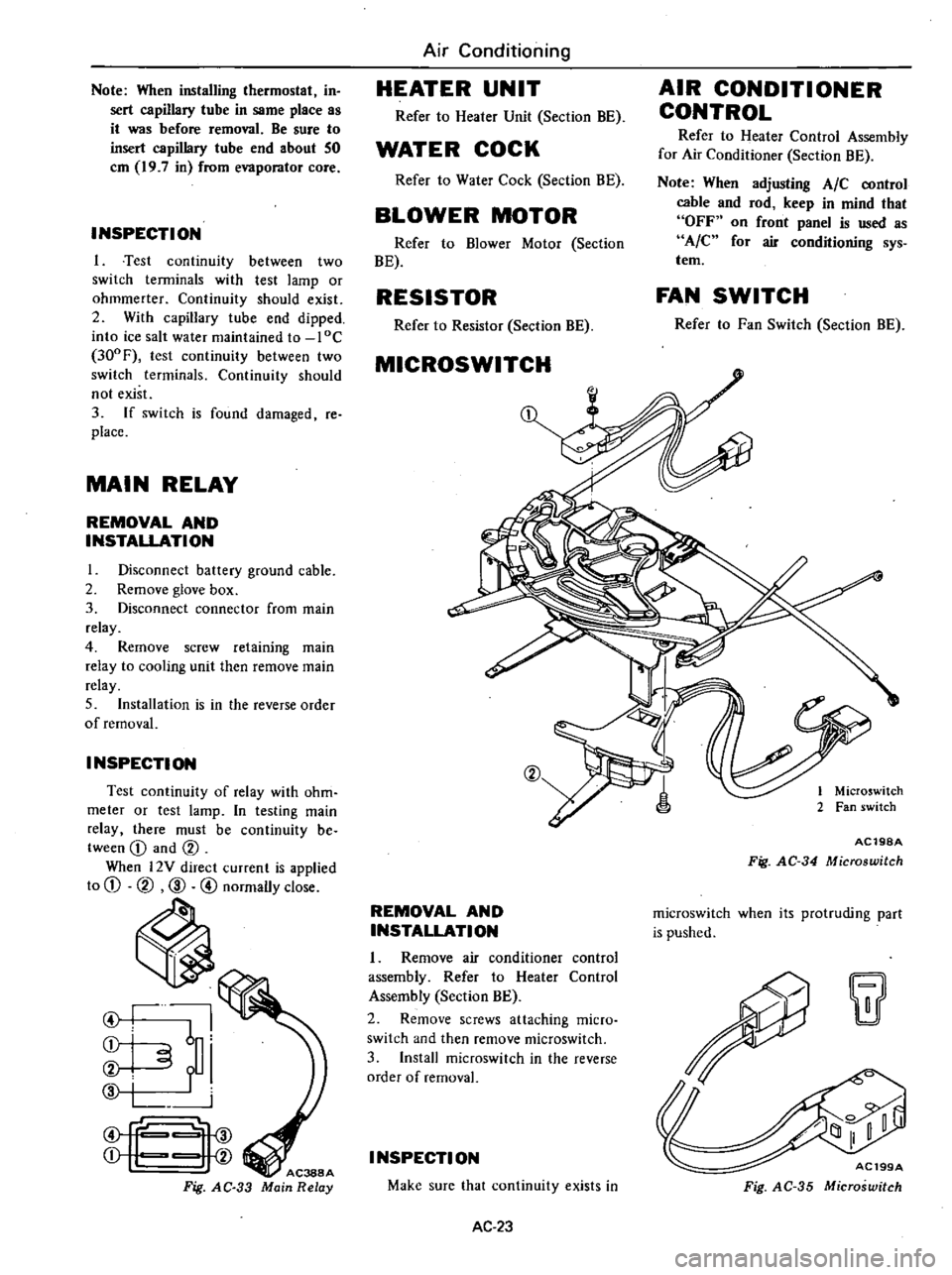
Note
When
installing
thermostat
in
sert
capillary
tube
in
same
place
as
it
was
before
removal
Be
sure
to
insert
capillary
tube
end
about
SO
em
19
7
in
from
evaporator
core
INSPECTION
1
Test
continuity
between
two
switch
terminals
with
test
lamp
or
ohmmerter
Continuity
should
exist
2
With
capillary
tube
end
dipped
into
ice
salt
water
maintained
to
I
oc
300
F
test
continuity
between
two
switch
terminals
Continuity
should
not
exist
3
If
switch
is
found
damaged
re
place
MAIN
RELAY
REMOVAL
AND
INSTALLATION
I
Disconnect
battery
ground
cable
2
Remove
glove
box
3
Disconnect
connector
from
main
relay
4
Remove
screw
retaining
main
relay
to
cooling
unit
then
remove
main
relay
5
Installation
is
in
the
reverse
order
of
removal
INSPECTION
Test
continuity
of
relay
with
ohm
meter
or
test
lamp
In
testing
main
relay
there
must
be
continuity
be
tween
CD
and
CV
When
l2Y
direct
current
is
applied
to
CD
CV
CID
@
normally
close
ti
I
I
6
i
i
f
i
f
Fig
AC
33
Air
Conditioning
HEATER
UNIT
Refer
to
Heater
Unit
Section
BE
WATER
COCK
Refer
to
Water
Cock
Section
BE
BLOWER
MOTOR
Refer
to
Blower
Motor
Section
BE
RESISTOR
Refer
to
Resistor
Section
BE
MICROSWITCH
CV
REMOVAL
AND
INSTALLATION
1
Remove
air
conditioner
control
assembly
Refer
to
Heater
Control
Assembly
Section
BE
2
Remove
screws
attaching
micro
switch
and
then
remove
rnicroswitch
3
Install
rnicroswitch
in
the
reverse
order
of
removal
I
NSPECTI
ON
Make
sure
that
continuity
exists
in
AC
23
AIR
CONDITIONER
CONTROL
Refer
to
Heater
Control
Assembly
for
Air
Conditioner
Section
BE
Note
When
adjusting
AIC
control
cable
and
rod
keep
in
mind
that
OFF
on
front
panel
is
used
as
A
C
for
air
conditioning
sys
tem
FAN
SWITCH
Refer
to
Fan
Switch
Section
BE
1
Microswitch
2
Fan
switch
AC19SA
Fig
AC
34
Microswitch
rnicroswitch
when
its
protruding
part
is
pushed
w
AC199A
Fig
AC
35
Microswitch
Page 525 of 548
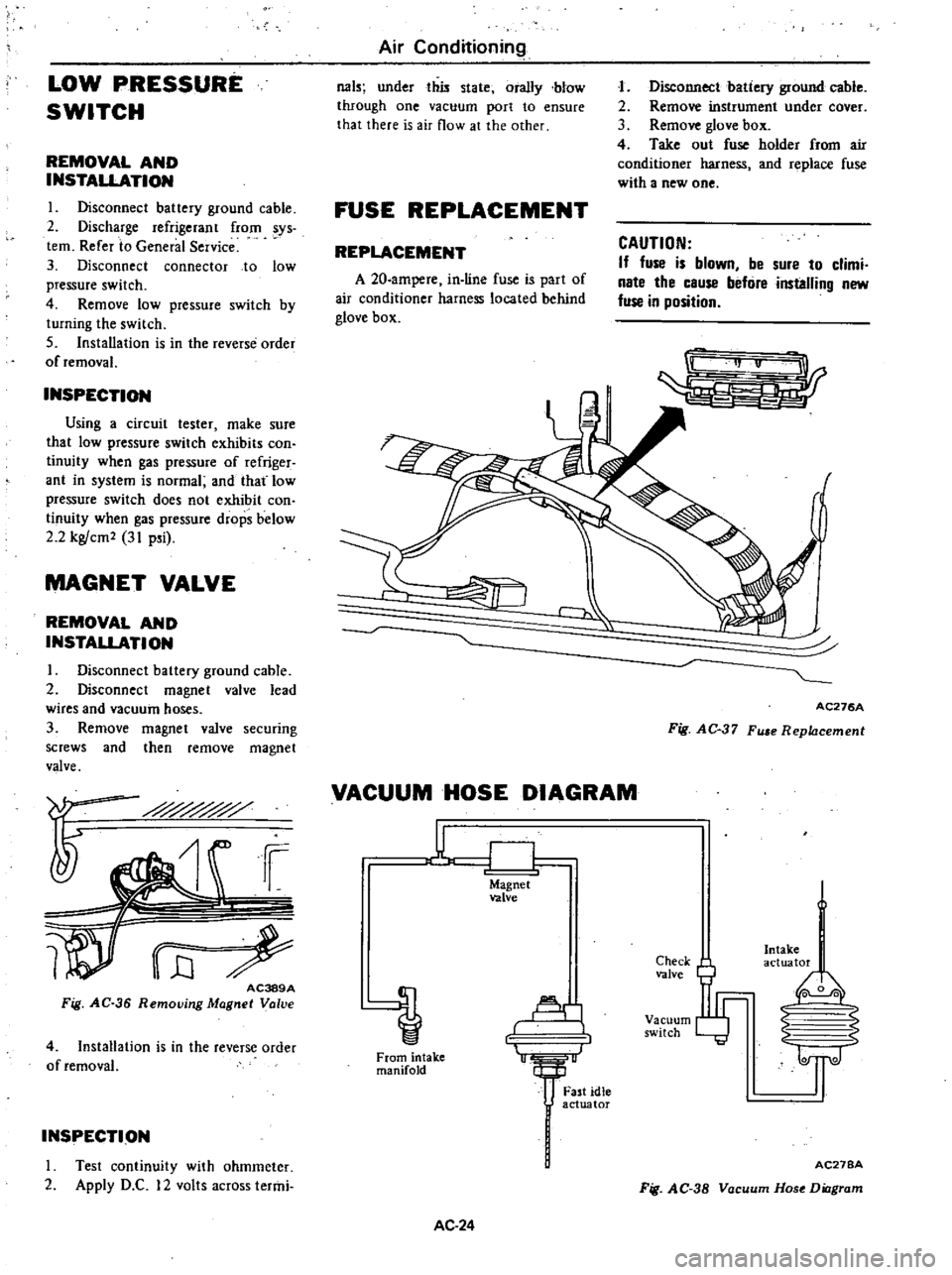
LOW
PRESSURE
SWITCH
REMOVAL
AND
INSTALLATION
I
Disconnect
battery
ground
cable
2
Discharge
refrigerant
from
sys
tem
Refer
to
General
Service
3
Disconnect
connector
to
low
pressure
switch
4
Remove
low
pressure
switch
by
turning
the
switch
5
Installation
is
in
the
reverse
order
of
removal
INSPECTION
Using
a
circuit
tester
make
sure
that
low
pressure
switch
exhibits
con
tinuity
when
gas
pressure
of
refriger
ant
in
system
is
normal
and
that
low
pressure
switch
does
not
exhibit
con
tinuity
when
gas
pressure
drops
below
2
2
kg
cm2
31
p
i
MAGNET
VALVE
REMOVAL
AND
INSTALLATION
I
Disconnect
battery
ground
cable
2
Disconnect
magnet
valve
lead
wires
and
vacuum
hoses
3
Remove
magnet
valve
securing
screws
and
then
remove
magnet
valve
i
i
WrE
AC389A
Fig
AC
36
Removjng
Magnet
Valve
4
Installation
is
in
the
reverse
order
of
removal
INSPECTION
I
rest
continuity
with
ohmmeter
2
Apply
D
C
12
volts
across
termi
Air
Conditioning
031
under
this
state
orally
blow
through
one
vacuum
port
to
ensure
that
there
is
air
flow
at
the
other
FUSE
REPLACEMENT
REPLACEMENT
A
20
ampere
in
line
fuse
is
part
of
air
conditioner
harness
located
behind
glove
box
J
Disconnect
batiery
ground
cable
2
Remove
instrument
under
cover
3
Remove
glove
box
4
Take
out
fuse
holder
from
air
conditioner
harness
and
replace
fuse
with
a
new
one
CAUTION
If
fuse
is
blown
be
sure
to
climi
nate
the
cause
befure
installing
new
fuse
in
position
r
AC276A
Fig
AC
37
Fu
e
Replacement
VACUUM
HOSE
DIAGRAM
u
CJ
Magnet
valve
Al
1
From
intake
manifold
AC
24
Fast
idle
actuator
Check
valve
Vacuum
switch
Intake
actuator
I
0
0
2
S
1l
AC27BA
Fig
AC
38
Vacuum
Hose
Diagram
Page 526 of 548
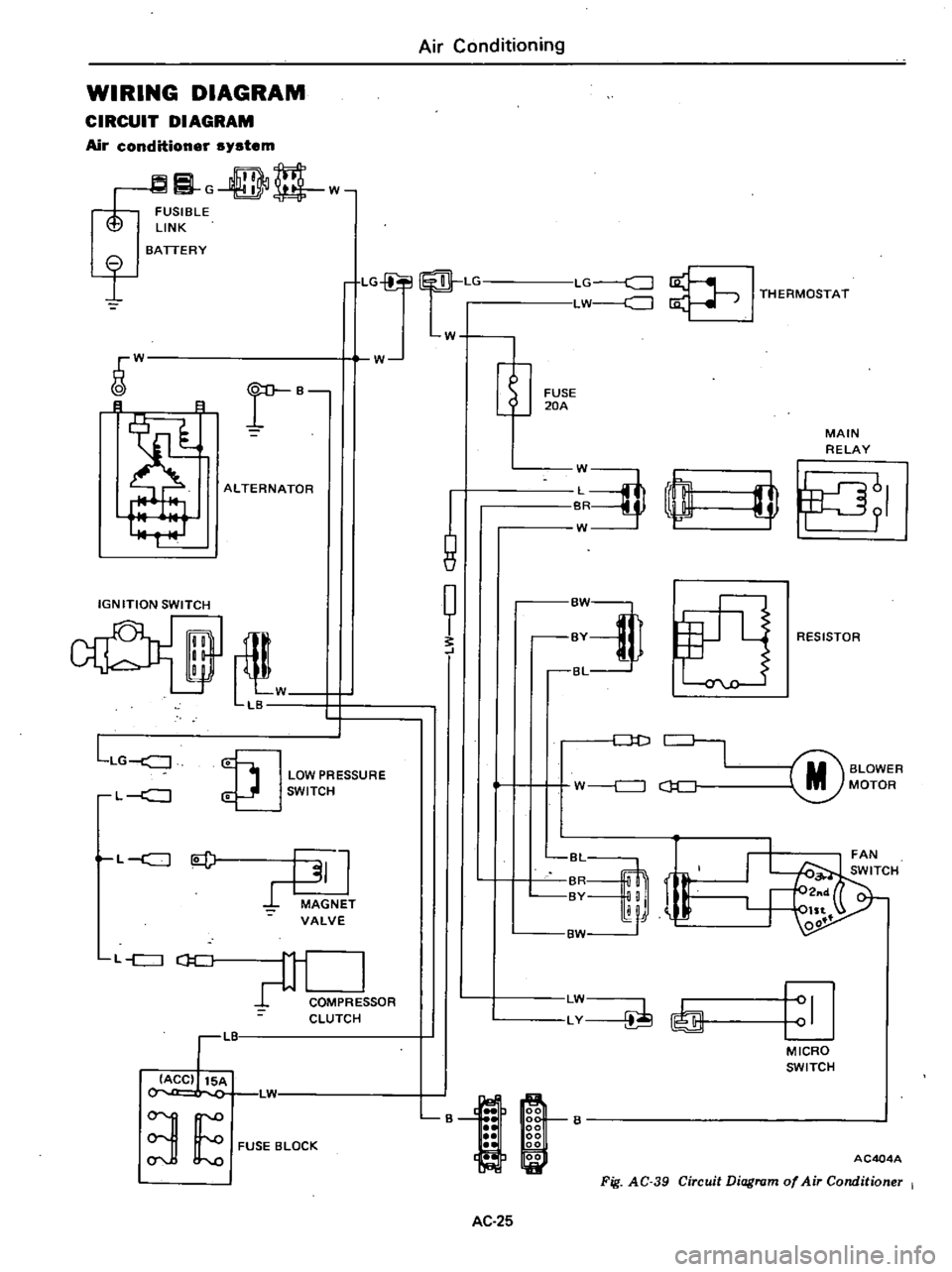
WIRING
DIAGRAM
CIRCUIT
DIAGRAM
Air
conditioner
system
G
DD
w
FUSIBLE
LINK
I
BATTERY
LG
Lr
LG
c
J
LW
J
I
THERMOSTAT
W
W
r
B
B
8
ALTERNATOR
IGNITION
SWITCH
il
W
LB
LLG
J
LOW
PRESSURE
SWITCH
L
c
J
L
c
J
l
J
MAGNET
VALVE
L
c
J
CJ
C
COMPRE
SOR
CLUTCH
LIT
IACC
15A
L1
3
E
FUSE
BLOCK
Air
Conditioning
W
1
8
t
FUSE
20A
MAIN
RELAY
J
rn
W
I
fJ
RESISTOR
Dt
J
M
BLOWER
MOTOR
W
c
J
c
J
C
r
BvM
LW
LY
I
MICRO
SWITCH
B
AC404A
Fig
AC
39
Circuit
Diagram
of
Air
Conditioner
I
AC
25
Page 527 of 548

0
@
o
s
xl
m
u
U
0
0
xJ
l
1
I
9
0
I
K
s
0
0
en
o
o
l
me
0
r
U
0
I
@
0
0
Tightening
torque
kg
m
ft
Ib
I
Clutch
wheel
bearing
10
Valve
pla
te
assembly
2
Snap
ring
11
Cylinder
gasket
@
i
1
to
3
2
IS
to
23
C
l
3
Clutch
wheel
alsembly
12
Cylinder
head
assembly
@
O
to
1
0
5
1
to
7
2
0
4
Magnetic
coil
13
B
plate
gasket
@
1
5
11
5
Shaft
seal
assembly
14
Bale
plate
@
0
7
5
1
6
Connector
IS
a
ting
7
O
ring
16
au
filler
plug
i
8
Cylindet
head
17
Clutch
assembly
o
Q
9
CyUhder
head
gasket
18
Compreslor
assembly
Page 528 of 548
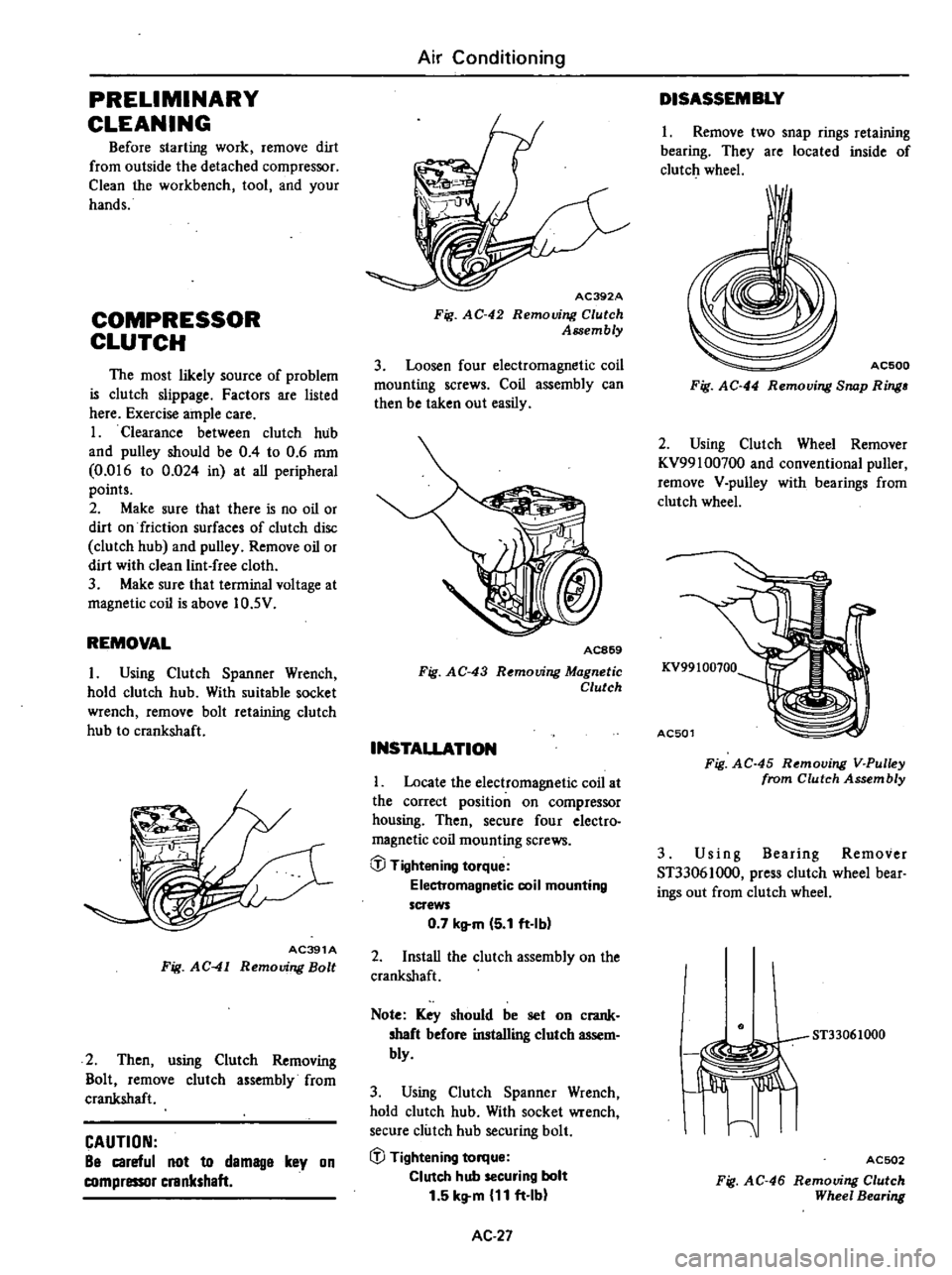
PRELIMINARY
CLEANING
Before
starting
work
remove
dirt
from
outside
the
detached
compressor
Clean
the
workbench
tool
and
your
hands
COMPRESSOR
CLUTCH
The
most
likely
source
of
problem
is
clutch
slippage
Factors
are
listed
here
Exercise
ample
care
1
Clearance
between
clutch
hub
and
pulley
should
be
0
4
to
0
6
mm
0
016
to
0
024
in
at
aU
peripheral
points
2
Make
sure
that
there
is
no
oil
or
dirt
on
friction
surfaces
of
clutch
disc
clutch
hub
and
pulley
Remove
oil
or
dirt
with
clean
lint
free
cloth
3
Make
sure
that
terminal
voltage
at
magnetic
coil
is
above
10
5V
REMOVAL
I
Using
Clutch
Spanner
Wrench
hold
clutch
hub
With
suitable
socket
wrench
remove
bolt
retaining
clutch
hub
to
crankshaft
AC391A
Fig
AC
41
Removing
Bolt
2
Then
using
Clutch
Removing
Bolt
remove
clutch
assembly
from
crankshaft
CAUTION
Be
careful
not
to
demage
key
on
compressor
crankshaft
Air
Conditioning
AC392A
Fig
AC
42
Removing
Clutch
Assembly
3
Loosen
four
electromagnetic
coil
mounting
screws
Coil
assembly
can
then
be
taken
out
easily
AC869
Fig
AC
43
R
mouing
Magnetic
Clutch
INSTALLATION
Locate
the
electromagnetic
coil
at
the
correct
position
on
compressor
housing
Then
secure
four
electro
magnetic
coil
mounting
screws
@
Tightening
torque
Electromagnetic
coil
mounting
screws
0
7
kltm
5
1
ft
Ibl
2
InstaU
the
clutch
assembly
on
the
crankshaft
Note
Key
should
be
set
on
crank
shaft
before
installing
clutch
assem
bly
3
Using
Clutch
Spanner
Wrench
hold
clutch
hub
With
socket
wrench
secure
clutch
hub
securing
bolt
iJJ
Tightening
torque
Clutch
hub
securing
bolt
1
5
kg
m
11
ft
Ib
AC
27
DISASSEMBLY
1
Remove
two
snap
rings
retaining
bearing
They
are
located
inside
of
clutch
wheel
I
AC500
Fig
AC
44
Removing
Snap
Ring
2
Using
Clutch
Wheel
Remover
KV99100700
and
conventional
puller
remove
V
pulley
with
bearings
from
clutch
wheel
KV99100100
AC501
Fig
AC
45
Removing
V
Pulley
from
Clutch
Assembly
3
Us
i
n
g
Bearing
Remover
ST33061000
press
clutch
wheel
bear
ings
out
from
clutch
wheel
ST33061000
I
Jiffi
I
ACSD2
Fig
AC
46
Removing
Clutch
Wheel
Bearing
Page 529 of 548
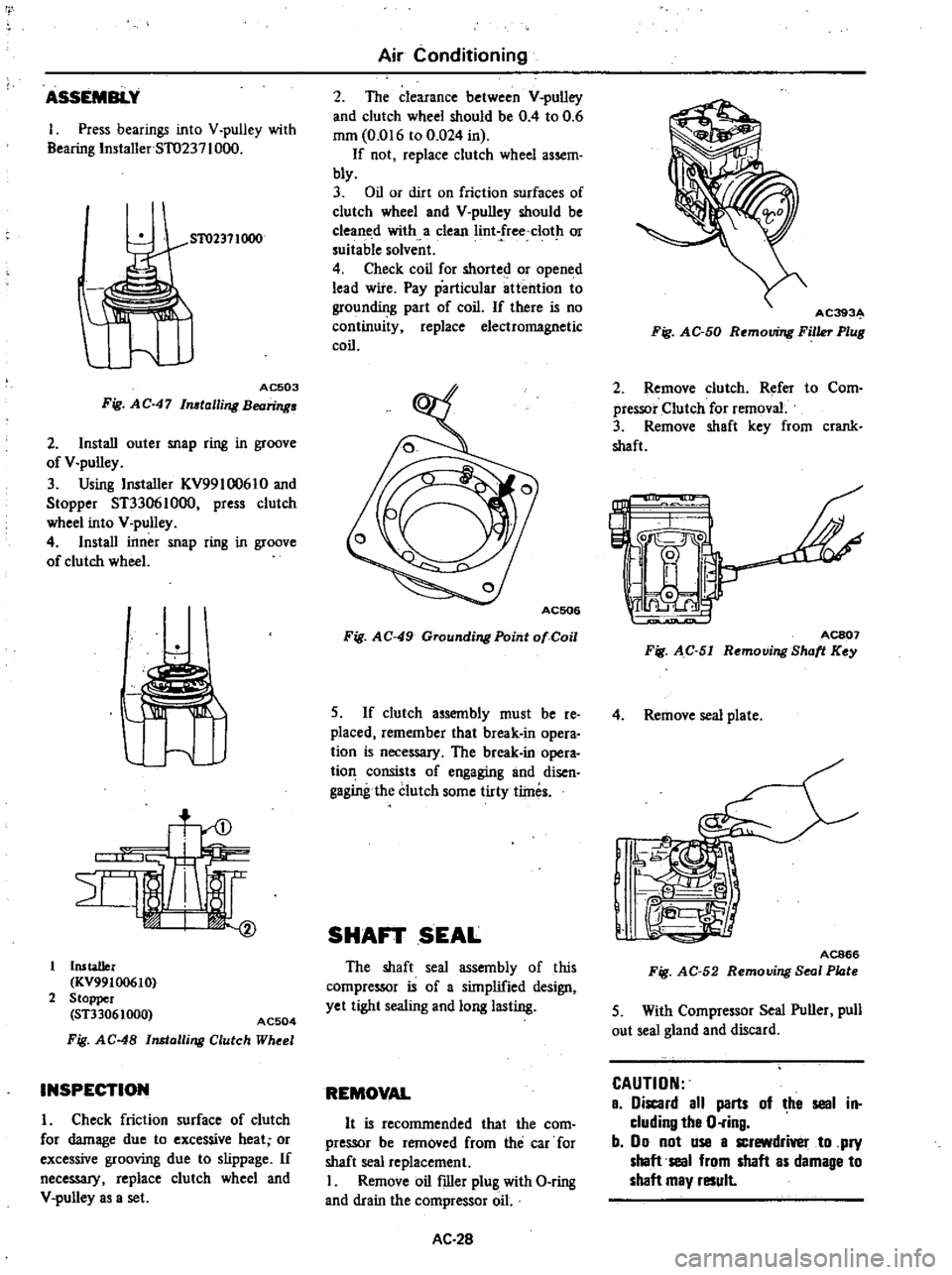
rt
ASSEMBLY
1
Press
bearings
into
V
pulley
with
Bearing
Installer
5T0237
1000
51
02371000
AC503
Fig
AC
47
In
talling
Bearing
2
Install
outer
snap
ring
in
groove
of
V
pulley
3
Using
Installer
KV99l
0061
0
and
Stopper
ST33061000
press
clutch
wheel
into
V
pulley
4
Install
inner
snap
ring
in
groove
of
clutch
wheel
u
Installer
KV99100610
2
Stopper
ST33061000
AC504
Fig
AC
48
Installing
Clutch
Wheel
INSPECTION
I
Check
friction
surface
of
clutch
for
damage
due
to
excessive
heat
or
excessive
grooving
due
to
slippage
If
neceSS3I
replace
clutch
wheel
and
V
pulley
as
a
set
Air
Conditioning
2
The
clearance
between
V
pulley
and
clutch
wheel
should
be
0
4
to
0
6
mm
0
016
to
0
024
in
If
not
replace
clutch
wheel
assem
bly
3
Oil
or
dirt
on
friction
surfaces
of
clutch
wheel
and
V
pulley
should
be
cleaned
with
a
clean
Iint
free
clot
or
suitable
solvent
4
Check
coil
for
shorted
or
opened
lead
wire
Pay
particular
attention
to
grounding
part
of
coil
If
there
is
no
continuity
replace
electromagnetic
coil
Fig
AC
49
Grounding
Point
01
Coil
S
If
clutch
assembly
must
be
re
placed
remember
that
break
in
opera
tion
is
neceSS3I
The
break
in
opera
tion
consists
of
engaging
and
disen
gagingthe
clutch
some
tirty
tlines
SHAFT
SEAL
The
shaft
seal
assembly
of
this
compressor
is
of
a
simplified
design
yet
tight
sealing
and
long
lasting
REMOVAL
It
is
recommended
that
the
com
pressor
be
removed
from
the
car
for
shaft
seal
replacement
I
Remove
oil
filler
plug
with
O
ring
and
drain
the
compressor
oil
AC
28
AC393
Fig
AC
50
Removing
Filler
Plug
2
Remove
clutch
Refer
to
Com
pressor
Clutch
for
removal
3
Remove
shaft
key
from
crank
shaft
L
IJ
C
I
0
ACS07
Fig
AC
51
Removing
Shott
Key
4
Remove
seal
plate
J
e
I
@
IR
n
1
j
AC866
Fig
AC
52
Removing
Seal
Plote
5
With
Compressor
Seal
Puller
pull
out
seal
gland
and
discard
CAUTION
a
iscard
all
parts
of
he
seal
in
cluding
tha
O
ring
b
00
not
use
a
screwdrivel
to
pry
shaft
seal
from
shaft
as
damage
to
shaft
may
result
Page 530 of 548
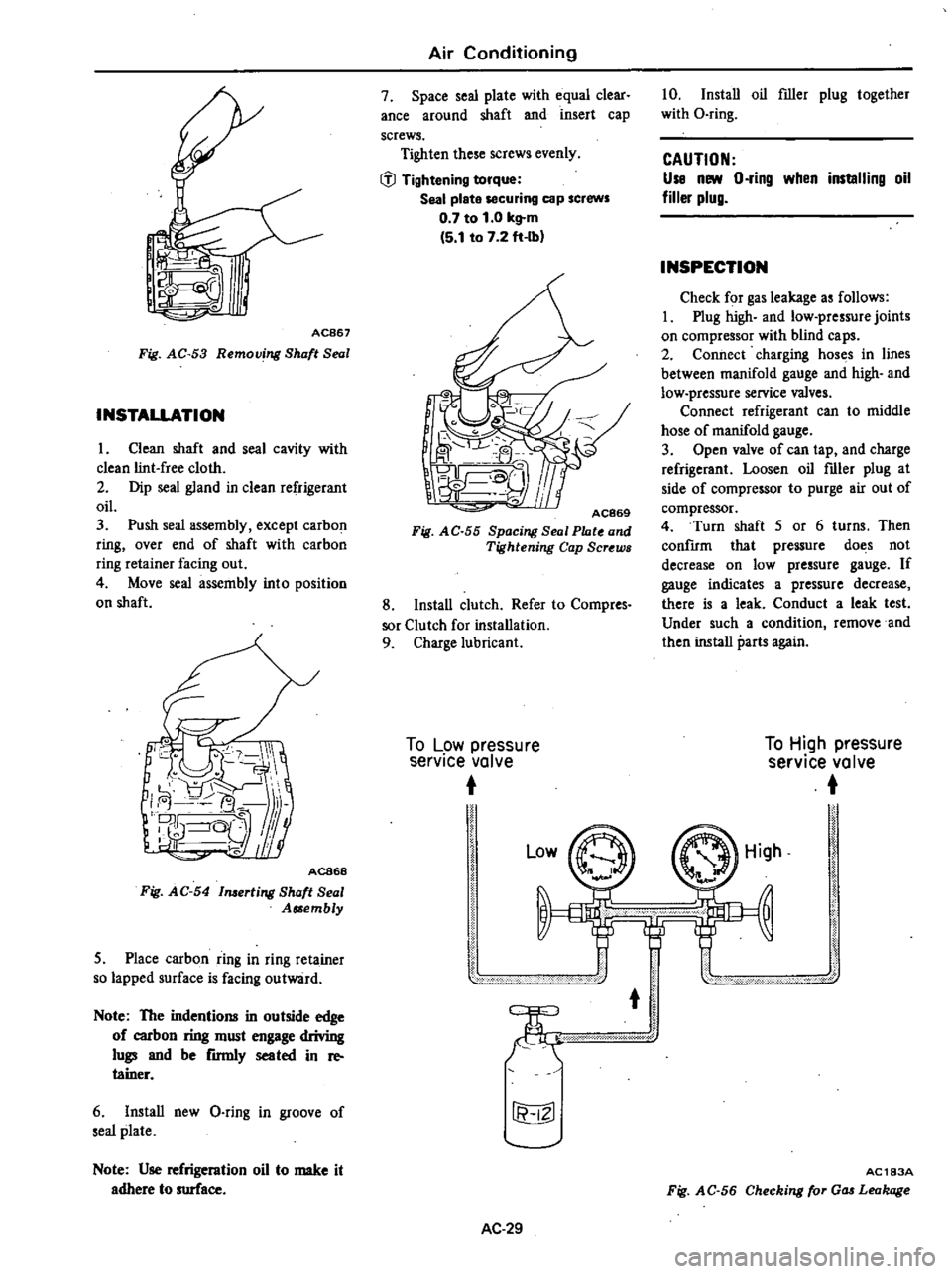
AC867
Fig
AC
53
Removing
Shaft
Seal
INSTALLATION
1
Clean
shaft
and
seal
cavity
with
clean
lint
free
cloth
2
Dip
seal
gland
in
clean
refrigerant
oil
3
Push
seal
assembly
except
carbon
ring
over
end
of
shaft
with
carbon
ring
retainer
facing
out
4
Move
seal
assembly
into
position
on
shaft
ACB68
Fig
AC
54
1merting
Shaft
Seal
Assembly
5
Place
carbon
ring
in
ring
reta
iner
so
lapped
surface
is
facing
outward
Note
The
indentions
in
outside
edge
of
carbon
ring
must
engage
driving
lugs
and
be
rmnly
seated
in
re
tainer
6
Install
new
Q
ring
in
groove
of
seal
plate
Note
Use
refrigeration
oil
to
make
it
adhere
to
surface
Air
Conditioning
7
Space
seal
plate
with
equal
clear
ance
around
shaft
and
insert
cap
screws
Tighten
these
screws
evenly
IiJ
Tightening
torque
Seal
plate
securing
cap
screws
0
7
to
1
0
kg
m
5
1
to
7
2
ft
Ibl
AC869
Fig
AC
55
Spacing
Seal
Plate
and
Tightening
Cap
Screws
8
Install
clutch
Refer
to
Compres
sor
Clutch
for
installation
9
Charge
lubricant
To
Low
pressure
service
valve
10
Install
oil
filler
plug
together
with
O
ring
CAUTION
Use
new
O
ring
when
installing
oil
filler
plug
INSPECTION
Check
for
gas
leakage
as
follows
I
Plug
high
and
low
pressure
joints
on
compressor
with
blind
caps
2
Connect
charging
hoses
in
lines
between
manifold
gauge
and
high
and
low
pressure
service
valves
Connect
refrigerant
can
to
middle
hose
of
manifold
gauge
3
Open
valve
of
can
tap
and
charge
refrigerant
Loosen
oil
filler
plug
at
side
of
compressor
to
purge
air
out
of
compressor
4
Turn
shaft
5
or
6
turns
Then
confIrm
that
pressure
does
not
decrease
on
low
pressure
gauge
If
gauge
indicates
a
pressure
decrease
there
is
a
leak
Conduct
a
leak
test
Under
such
a
condition
remove
and
then
install
parts
again
To
High
pressure
service
valve
Low
r
fi
IZl
AC
29
High
AC183A
Fig
AC
56
Checking
for
Gas
Leakage