DODGE NEON 1999 Service Repair Manual
Manufacturer: DODGE, Model Year: 1999, Model line: NEON, Model: DODGE NEON 1999Pages: 1200, PDF Size: 35.29 MB
Page 791 of 1200
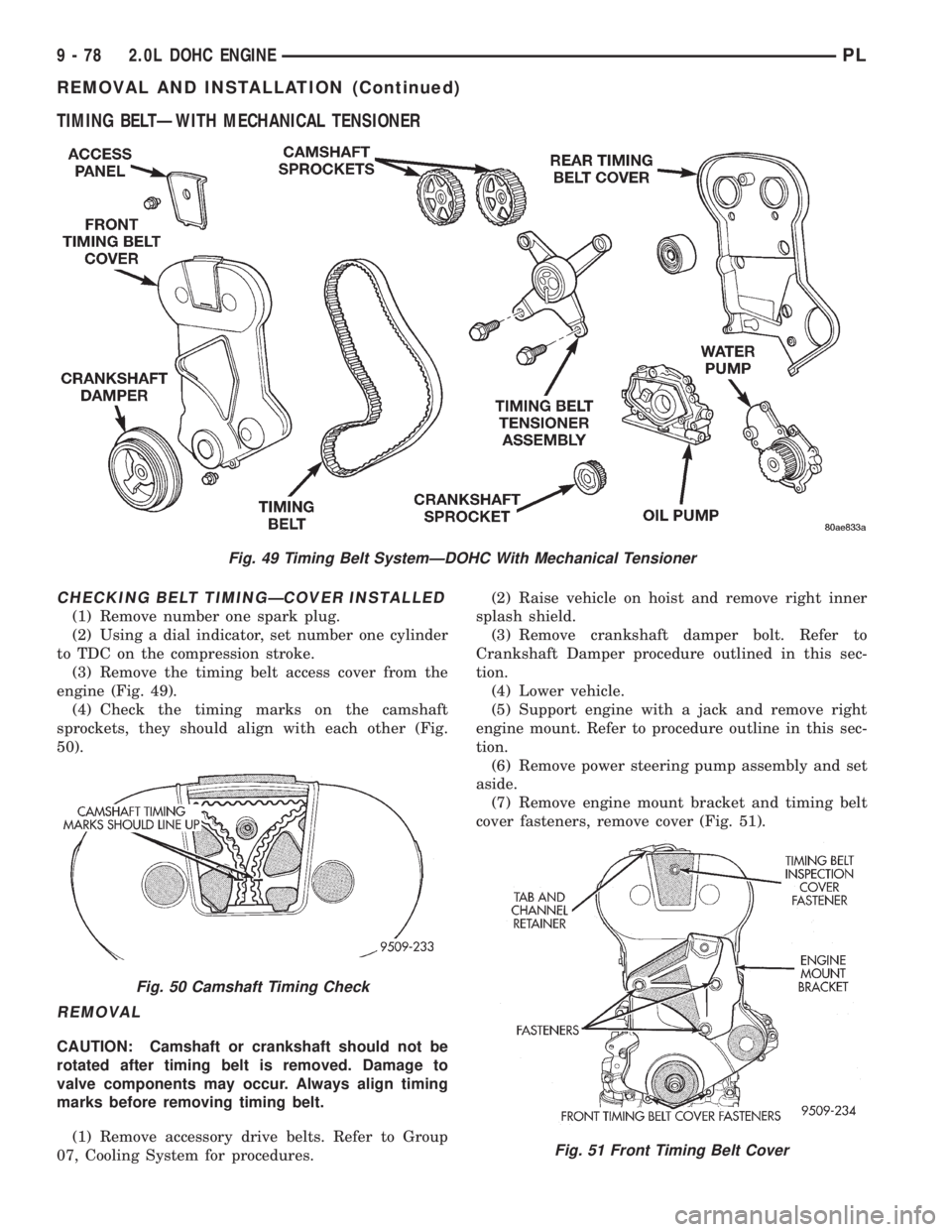
TIMING BELTÐWITH MECHANICAL TENSIONER
CHECKING BELT TIMINGÐCOVER INSTALLED
(1) Remove number one spark plug.
(2) Using a dial indicator, set number one cylinder
to TDC on the compression stroke.
(3) Remove the timing belt access cover from the
engine (Fig. 49).
(4) Check the timing marks on the camshaft
sprockets, they should align with each other (Fig.
50).
REMOVAL
CAUTION: Camshaft or crankshaft should not be
rotated after timing belt is removed. Damage to
valve components may occur. Always align timing
marks before removing timing belt.
(1) Remove accessory drive belts. Refer to Group
07, Cooling System for procedures.(2) Raise vehicle on hoist and remove right inner
splash shield.
(3) Remove crankshaft damper bolt. Refer to
Crankshaft Damper procedure outlined in this sec-
tion.
(4) Lower vehicle.
(5) Support engine with a jack and remove right
engine mount. Refer to procedure outline in this sec-
tion.
(6) Remove power steering pump assembly and set
aside.
(7) Remove engine mount bracket and timing belt
cover fasteners, remove cover (Fig. 51).
Fig. 49 Timing Belt SystemÐDOHC With Mechanical Tensioner
Fig. 50 Camshaft Timing Check
Fig. 51 Front Timing Belt Cover
9 - 78 2.0L DOHC ENGINEPL
REMOVAL AND INSTALLATION (Continued)
Page 792 of 1200
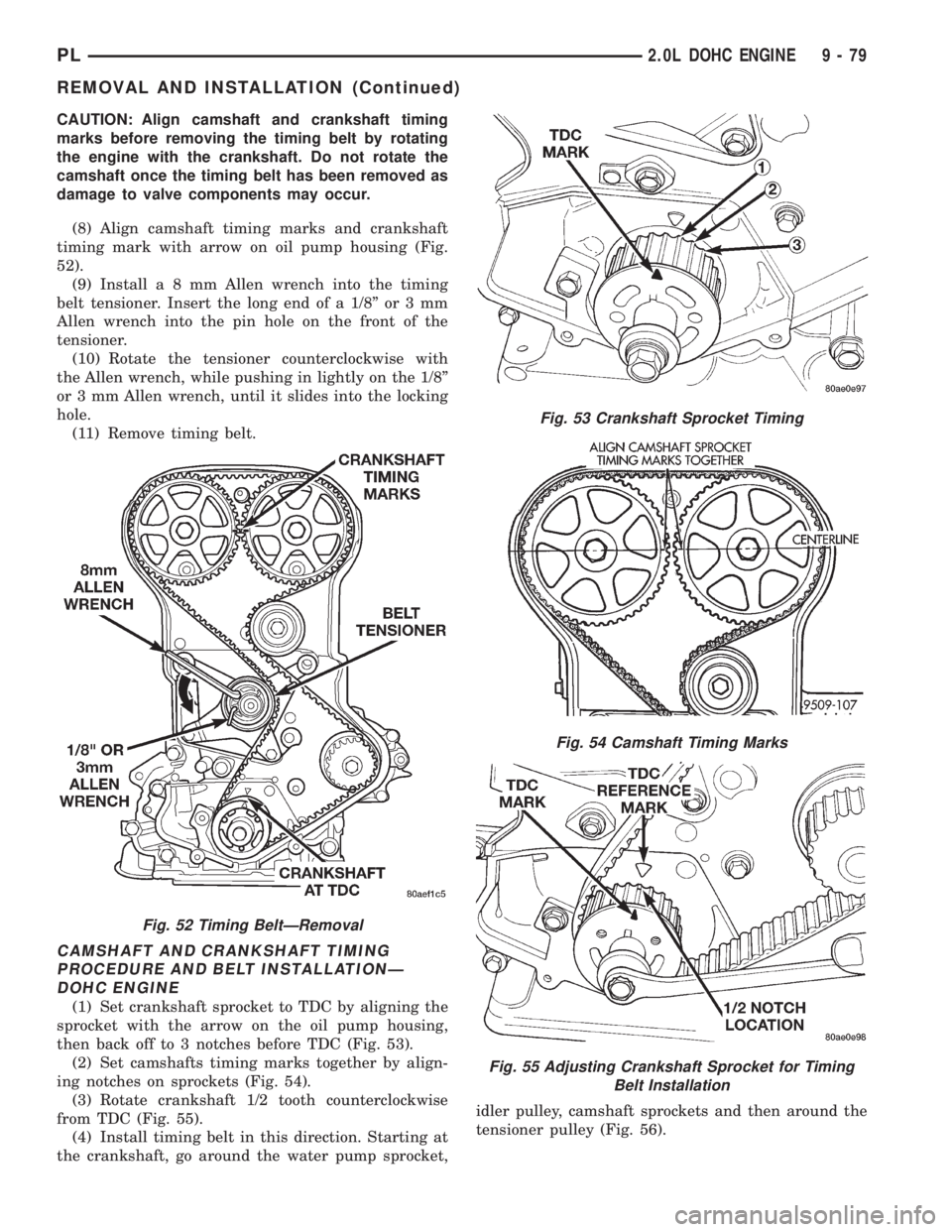
CAUTION: Align camshaft and crankshaft timing
marks before removing the timing belt by rotating
the engine with the crankshaft. Do not rotate the
camshaft once the timing belt has been removed as
damage to valve components may occur.
(8) Align camshaft timing marks and crankshaft
timing mark with arrow on oil pump housing (Fig.
52).
(9) Installa8mmAllen wrench into the timing
belt tensioner. Insert the long end of a 1/8º or 3 mm
Allen wrench into the pin hole on the front of the
tensioner.
(10) Rotate the tensioner counterclockwise with
the Allen wrench, while pushing in lightly on the 1/8º
or 3 mm Allen wrench, until it slides into the locking
hole.
(11) Remove timing belt.
CAMSHAFT AND CRANKSHAFT TIMING
PROCEDURE AND BELT INSTALLATIONÐ
DOHC ENGINE
(1) Set crankshaft sprocket to TDC by aligning the
sprocket with the arrow on the oil pump housing,
then back off to 3 notches before TDC (Fig. 53).
(2) Set camshafts timing marks together by align-
ing notches on sprockets (Fig. 54).
(3) Rotate crankshaft 1/2 tooth counterclockwise
from TDC (Fig. 55).
(4) Install timing belt in this direction. Starting at
the crankshaft, go around the water pump sprocket,idler pulley, camshaft sprockets and then around the
tensioner pulley (Fig. 56).
Fig. 52 Timing BeltÐRemoval
Fig. 53 Crankshaft Sprocket Timing
Fig. 54 Camshaft Timing Marks
Fig. 55 Adjusting Crankshaft Sprocket for Timing
Belt Installation
PL2.0L DOHC ENGINE 9 - 79
REMOVAL AND INSTALLATION (Continued)
Page 793 of 1200
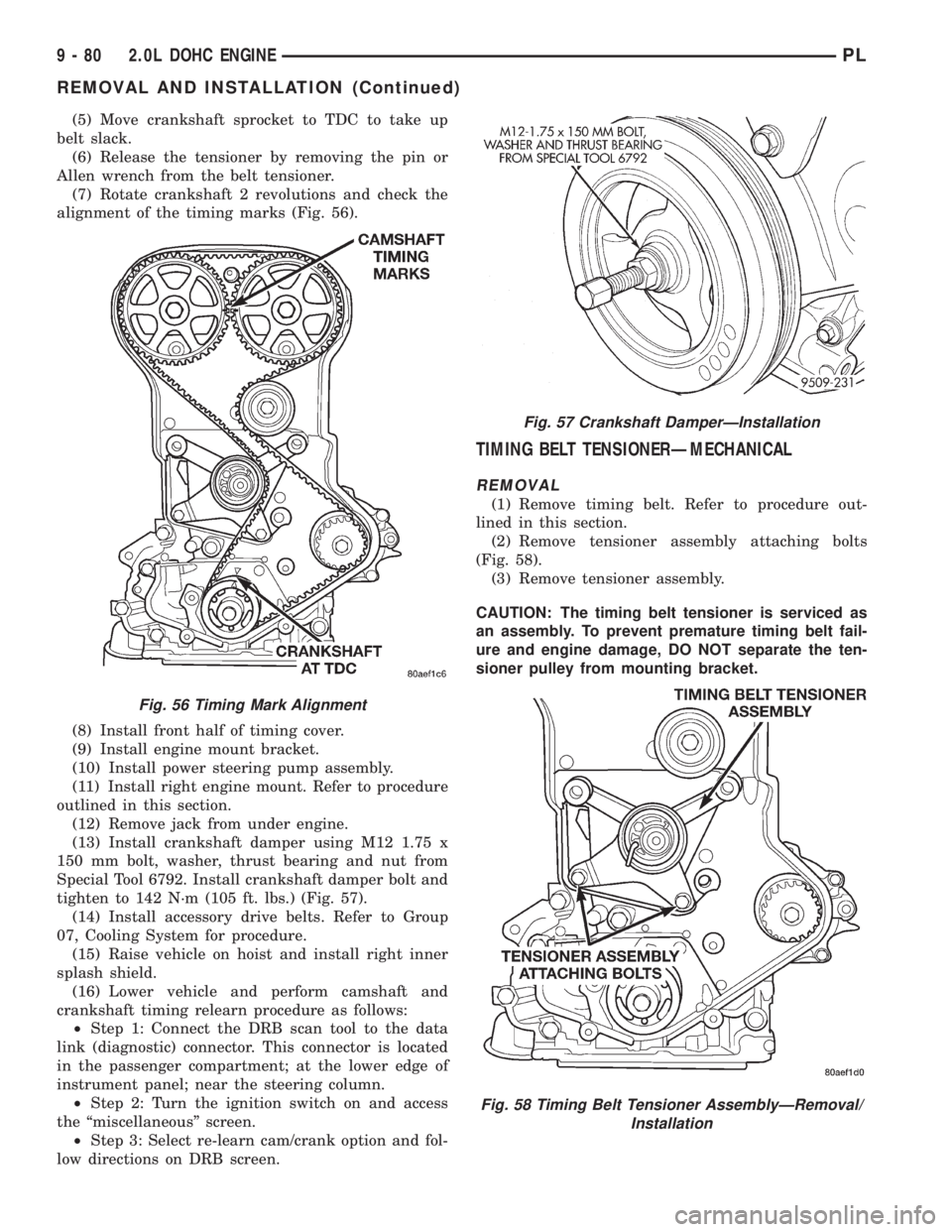
(5) Move crankshaft sprocket to TDC to take up
belt slack.
(6) Release the tensioner by removing the pin or
Allen wrench from the belt tensioner.
(7) Rotate crankshaft 2 revolutions and check the
alignment of the timing marks (Fig. 56).
(8) Install front half of timing cover.
(9) Install engine mount bracket.
(10) Install power steering pump assembly.
(11) Install right engine mount. Refer to procedure
outlined in this section.
(12) Remove jack from under engine.
(13) Install crankshaft damper using M12 1.75 x
150 mm bolt, washer, thrust bearing and nut from
Special Tool 6792. Install crankshaft damper bolt and
tighten to 142 N´m (105 ft. lbs.) (Fig. 57).
(14) Install accessory drive belts. Refer to Group
07, Cooling System for procedure.
(15) Raise vehicle on hoist and install right inner
splash shield.
(16) Lower vehicle and perform camshaft and
crankshaft timing relearn procedure as follows:
²Step 1: Connect the DRB scan tool to the data
link (diagnostic) connector. This connector is located
in the passenger compartment; at the lower edge of
instrument panel; near the steering column.
²Step 2: Turn the ignition switch on and access
the ªmiscellaneousº screen.
²Step 3: Select re-learn cam/crank option and fol-
low directions on DRB screen.
TIMING BELT TENSIONERÐMECHANICAL
REMOVAL
(1) Remove timing belt. Refer to procedure out-
lined in this section.
(2) Remove tensioner assembly attaching bolts
(Fig. 58).
(3) Remove tensioner assembly.
CAUTION: The timing belt tensioner is serviced as
an assembly. To prevent premature timing belt fail-
ure and engine damage, DO NOT separate the ten-
sioner pulley from mounting bracket.
Fig. 56 Timing Mark Alignment
Fig. 57 Crankshaft DamperÐInstallation
Fig. 58 Timing Belt Tensioner AssemblyÐRemoval/
Installation
9 - 80 2.0L DOHC ENGINEPL
REMOVAL AND INSTALLATION (Continued)
Page 794 of 1200
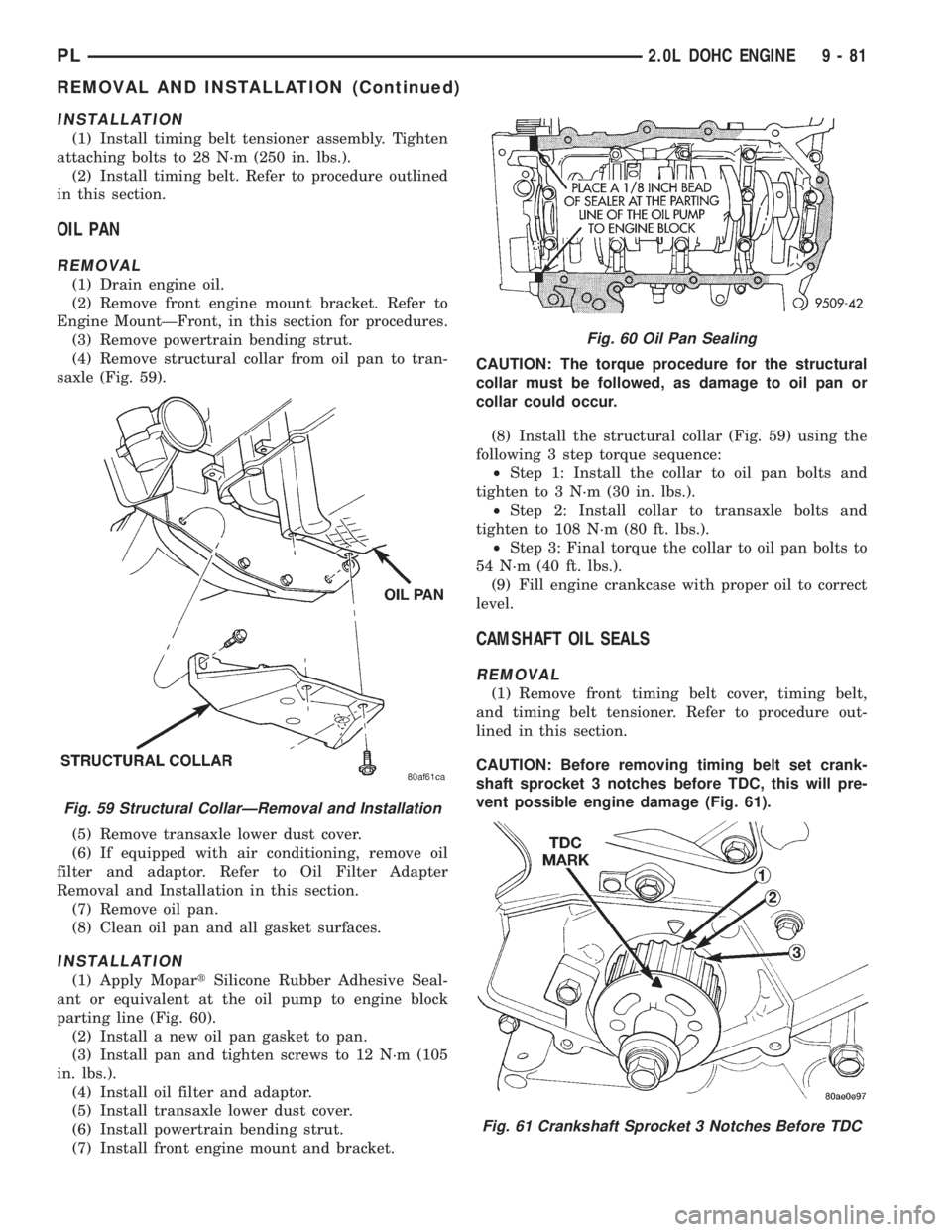
INSTALLATION
(1) Install timing belt tensioner assembly. Tighten
attaching bolts to 28 N´m (250 in. lbs.).
(2) Install timing belt. Refer to procedure outlined
in this section.
OIL PAN
REMOVAL
(1) Drain engine oil.
(2) Remove front engine mount bracket. Refer to
Engine MountÐFront, in this section for procedures.
(3) Remove powertrain bending strut.
(4) Remove structural collar from oil pan to tran-
saxle (Fig. 59).
(5) Remove transaxle lower dust cover.
(6) If equipped with air conditioning, remove oil
filter and adaptor. Refer to Oil Filter Adapter
Removal and Installation in this section.
(7) Remove oil pan.
(8) Clean oil pan and all gasket surfaces.
INSTALLATION
(1) Apply MopartSilicone Rubber Adhesive Seal-
ant or equivalent at the oil pump to engine block
parting line (Fig. 60).
(2) Install a new oil pan gasket to pan.
(3) Install pan and tighten screws to 12 N´m (105
in. lbs.).
(4) Install oil filter and adaptor.
(5) Install transaxle lower dust cover.
(6) Install powertrain bending strut.
(7) Install front engine mount and bracket.CAUTION: The torque procedure for the structural
collar must be followed, as damage to oil pan or
collar could occur.
(8) Install the structural collar (Fig. 59) using the
following 3 step torque sequence:
²Step 1: Install the collar to oil pan bolts and
tighten to 3 N´m (30 in. lbs.).
²Step 2: Install collar to transaxle bolts and
tighten to 108 N´m (80 ft. lbs.).
²Step 3: Final torque the collar to oil pan bolts to
54 N´m (40 ft. lbs.).
(9) Fill engine crankcase with proper oil to correct
level.
CAMSHAFT OIL SEALS
REMOVAL
(1) Remove front timing belt cover, timing belt,
and timing belt tensioner. Refer to procedure out-
lined in this section.
CAUTION: Before removing timing belt set crank-
shaft sprocket 3 notches before TDC, this will pre-
vent possible engine damage (Fig. 61).
Fig. 59 Structural CollarÐRemoval and Installation
Fig. 60 Oil Pan Sealing
Fig. 61 Crankshaft Sprocket 3 Notches Before TDC
PL2.0L DOHC ENGINE 9 - 81
REMOVAL AND INSTALLATION (Continued)
Page 795 of 1200
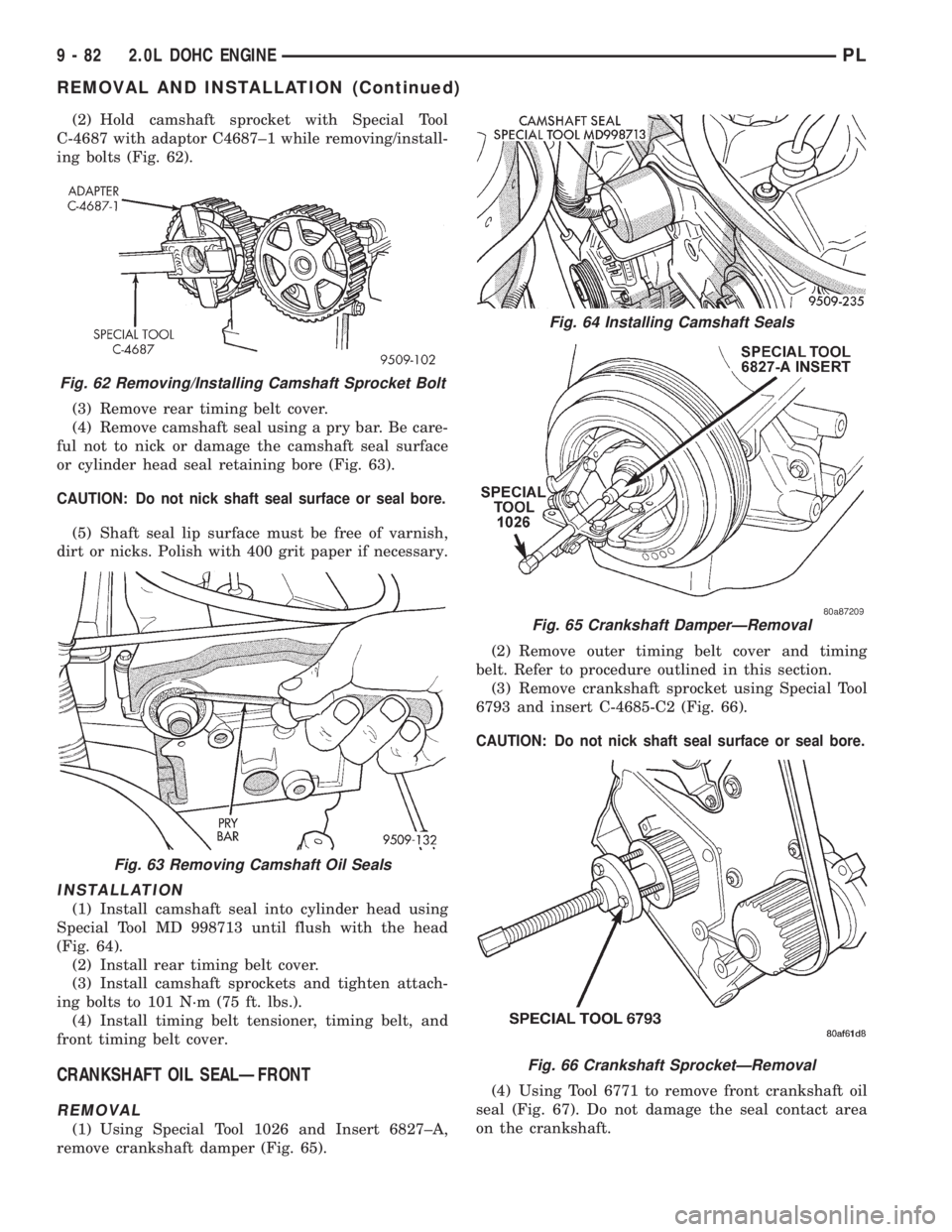
(2) Hold camshaft sprocket with Special Tool
C-4687 with adaptor C4687±1 while removing/install-
ing bolts (Fig. 62).
(3) Remove rear timing belt cover.
(4) Remove camshaft seal using a pry bar. Be care-
ful not to nick or damage the camshaft seal surface
or cylinder head seal retaining bore (Fig. 63).
CAUTION: Do not nick shaft seal surface or seal bore.
(5) Shaft seal lip surface must be free of varnish,
dirt or nicks. Polish with 400 grit paper if necessary.
INSTALLATION
(1) Install camshaft seal into cylinder head using
Special Tool MD 998713 until flush with the head
(Fig. 64).
(2) Install rear timing belt cover.
(3) Install camshaft sprockets and tighten attach-
ing bolts to 101 N´m (75 ft. lbs.).
(4) Install timing belt tensioner, timing belt, and
front timing belt cover.
CRANKSHAFT OIL SEALÐFRONT
REMOVAL
(1) Using Special Tool 1026 and Insert 6827±A,
remove crankshaft damper (Fig. 65).(2) Remove outer timing belt cover and timing
belt. Refer to procedure outlined in this section.
(3) Remove crankshaft sprocket using Special Tool
6793 and insert C-4685-C2 (Fig. 66).
CAUTION: Do not nick shaft seal surface or seal bore.
(4) Using Tool 6771 to remove front crankshaft oil
seal (Fig. 67). Do not damage the seal contact area
on the crankshaft.
Fig. 62 Removing/Installing Camshaft Sprocket Bolt
Fig. 63 Removing Camshaft Oil Seals
Fig. 64 Installing Camshaft Seals
Fig. 65 Crankshaft DamperÐRemoval
Fig. 66 Crankshaft SprocketÐRemoval
9 - 82 2.0L DOHC ENGINEPL
REMOVAL AND INSTALLATION (Continued)
Page 796 of 1200
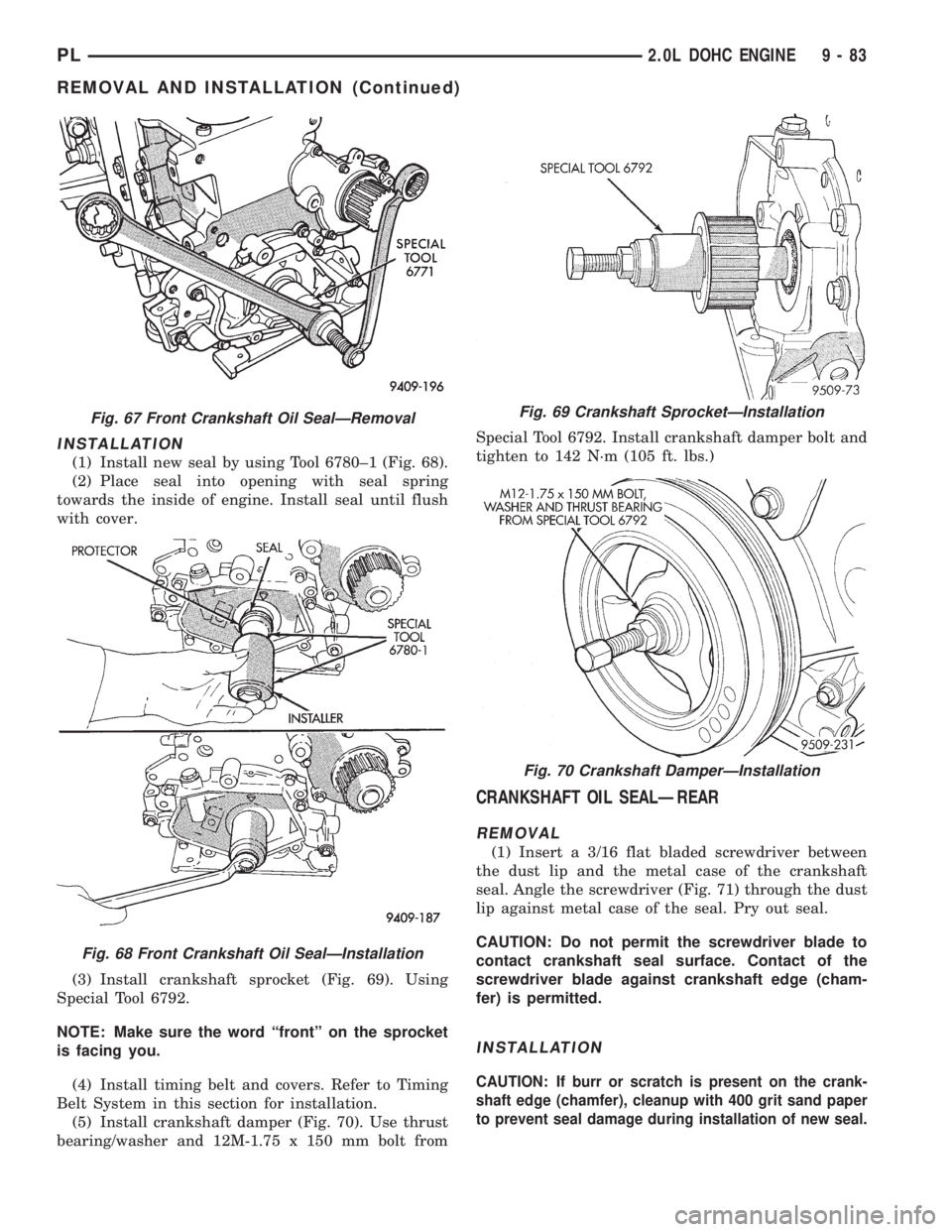
INSTALLATION
(1) Install new seal by using Tool 6780±1 (Fig. 68).
(2) Place seal into opening with seal spring
towards the inside of engine. Install seal until flush
with cover.
(3) Install crankshaft sprocket (Fig. 69). Using
Special Tool 6792.
NOTE: Make sure the word ªfrontº on the sprocket
is facing you.
(4) Install timing belt and covers. Refer to Timing
Belt System in this section for installation.
(5) Install crankshaft damper (Fig. 70). Use thrust
bearing/washer and 12M-1.75 x 150 mm bolt fromSpecial Tool 6792. Install crankshaft damper bolt and
tighten to 142 N´m (105 ft. lbs.)
CRANKSHAFT OIL SEALÐREAR
REMOVAL
(1) Insert a 3/16 flat bladed screwdriver between
the dust lip and the metal case of the crankshaft
seal. Angle the screwdriver (Fig. 71) through the dust
lip against metal case of the seal. Pry out seal.
CAUTION: Do not permit the screwdriver blade to
contact crankshaft seal surface. Contact of the
screwdriver blade against crankshaft edge (cham-
fer) is permitted.
INSTALLATION
CAUTION: If burr or scratch is present on the crank-
shaft edge (chamfer), cleanup with 400 grit sand paper
to prevent seal damage during installation of new seal.
Fig. 67 Front Crankshaft Oil SealÐRemoval
Fig. 68 Front Crankshaft Oil SealÐInstallation
Fig. 69 Crankshaft SprocketÐInstallation
Fig. 70 Crankshaft DamperÐInstallation
PL2.0L DOHC ENGINE 9 - 83
REMOVAL AND INSTALLATION (Continued)
Page 797 of 1200
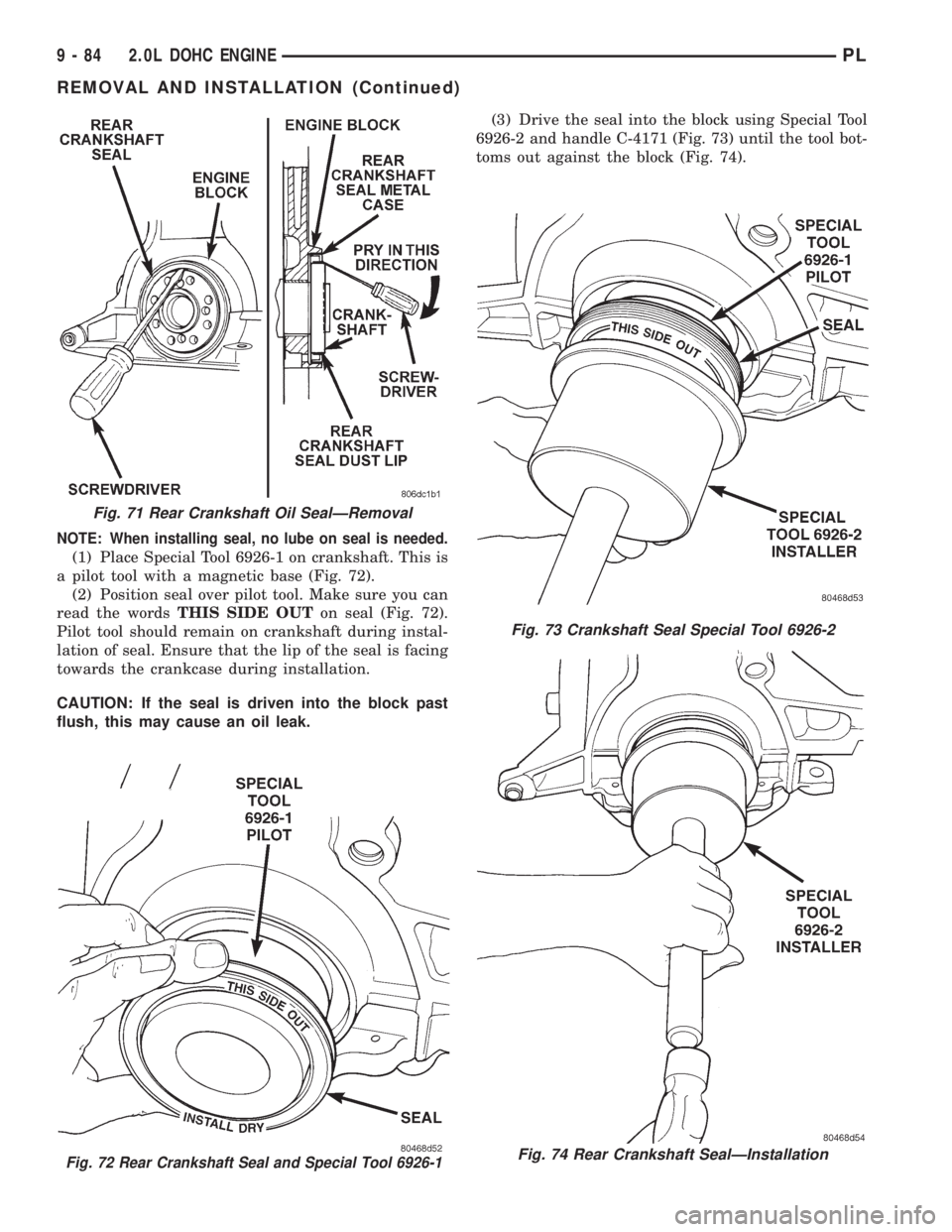
NOTE: When installing seal, no lube on seal is needed.
(1) Place Special Tool 6926-1 on crankshaft. This is
a pilot tool with a magnetic base (Fig. 72).
(2) Position seal over pilot tool. Make sure you can
read the wordsTHIS SIDE OUTon seal (Fig. 72).
Pilot tool should remain on crankshaft during instal-
lation of seal. Ensure that the lip of the seal is facing
towards the crankcase during installation.
CAUTION: If the seal is driven into the block past
flush, this may cause an oil leak.(3) Drive the seal into the block using Special Tool
6926-2 and handle C-4171 (Fig. 73) until the tool bot-
toms out against the block (Fig. 74).
Fig. 71 Rear Crankshaft Oil SealÐRemoval
Fig. 72 Rear Crankshaft Seal and Special Tool 6926-1
Fig. 73 Crankshaft Seal Special Tool 6926-2
Fig. 74 Rear Crankshaft SealÐInstallation
9 - 84 2.0L DOHC ENGINEPL
REMOVAL AND INSTALLATION (Continued)
Page 798 of 1200
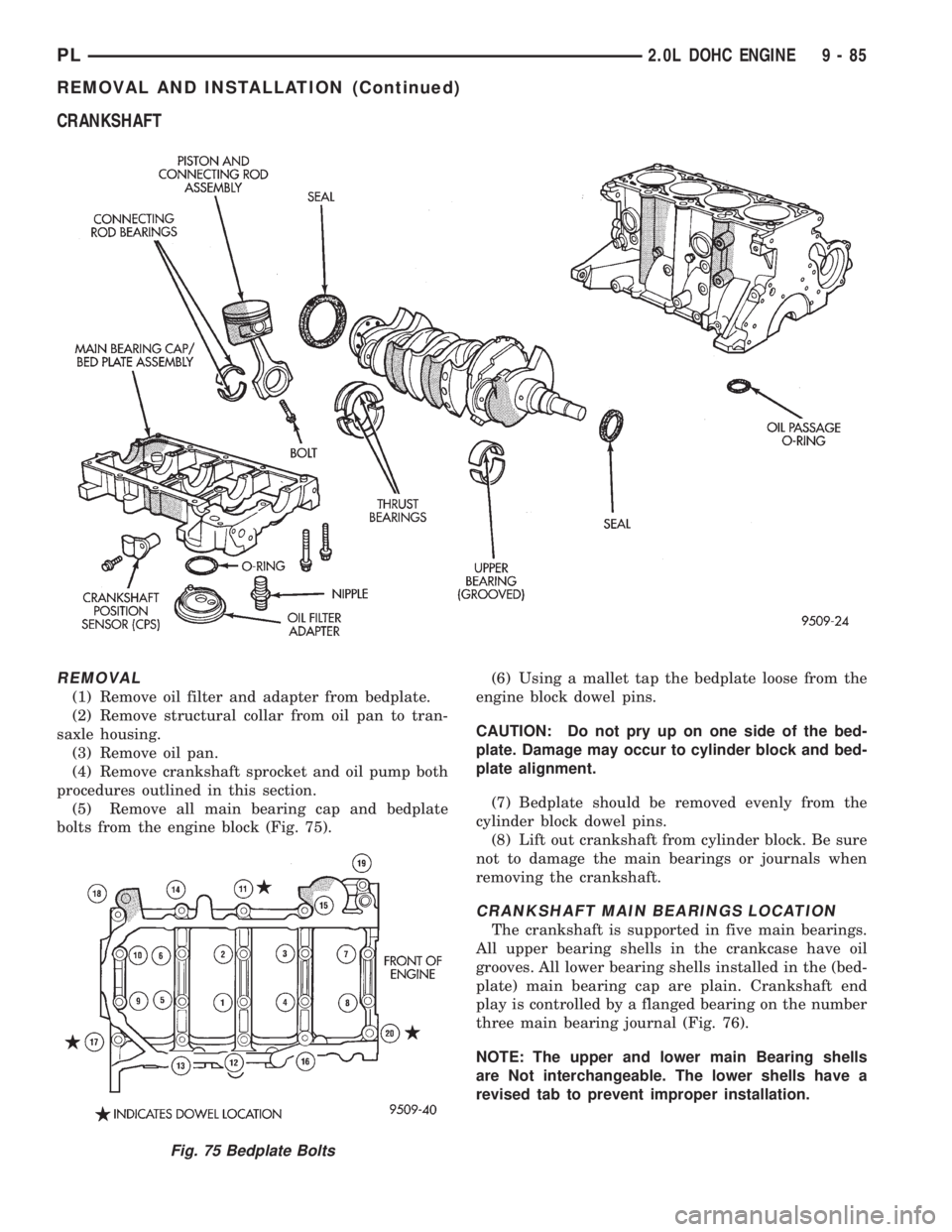
CRANKSHAFT
REMOVAL
(1) Remove oil filter and adapter from bedplate.
(2) Remove structural collar from oil pan to tran-
saxle housing.
(3) Remove oil pan.
(4) Remove crankshaft sprocket and oil pump both
procedures outlined in this section.
(5) Remove all main bearing cap and bedplate
bolts from the engine block (Fig. 75).(6) Using a mallet tap the bedplate loose from the
engine block dowel pins.
CAUTION: Do not pry up on one side of the bed-
plate. Damage may occur to cylinder block and bed-
plate alignment.
(7) Bedplate should be removed evenly from the
cylinder block dowel pins.
(8) Lift out crankshaft from cylinder block. Be sure
not to damage the main bearings or journals when
removing the crankshaft.
CRANKSHAFT MAIN BEARINGS LOCATION
The crankshaft is supported in five main bearings.
All upper bearing shells in the crankcase have oil
grooves. All lower bearing shells installed in the (bed-
plate) main bearing cap are plain. Crankshaft end
play is controlled by a flanged bearing on the number
three main bearing journal (Fig. 76).
NOTE: The upper and lower main Bearing shells
are Not interchangeable. The lower shells have a
revised tab to prevent improper installation.
Fig. 75 Bedplate Bolts
PL2.0L DOHC ENGINE 9 - 85
REMOVAL AND INSTALLATION (Continued)
Page 799 of 1200
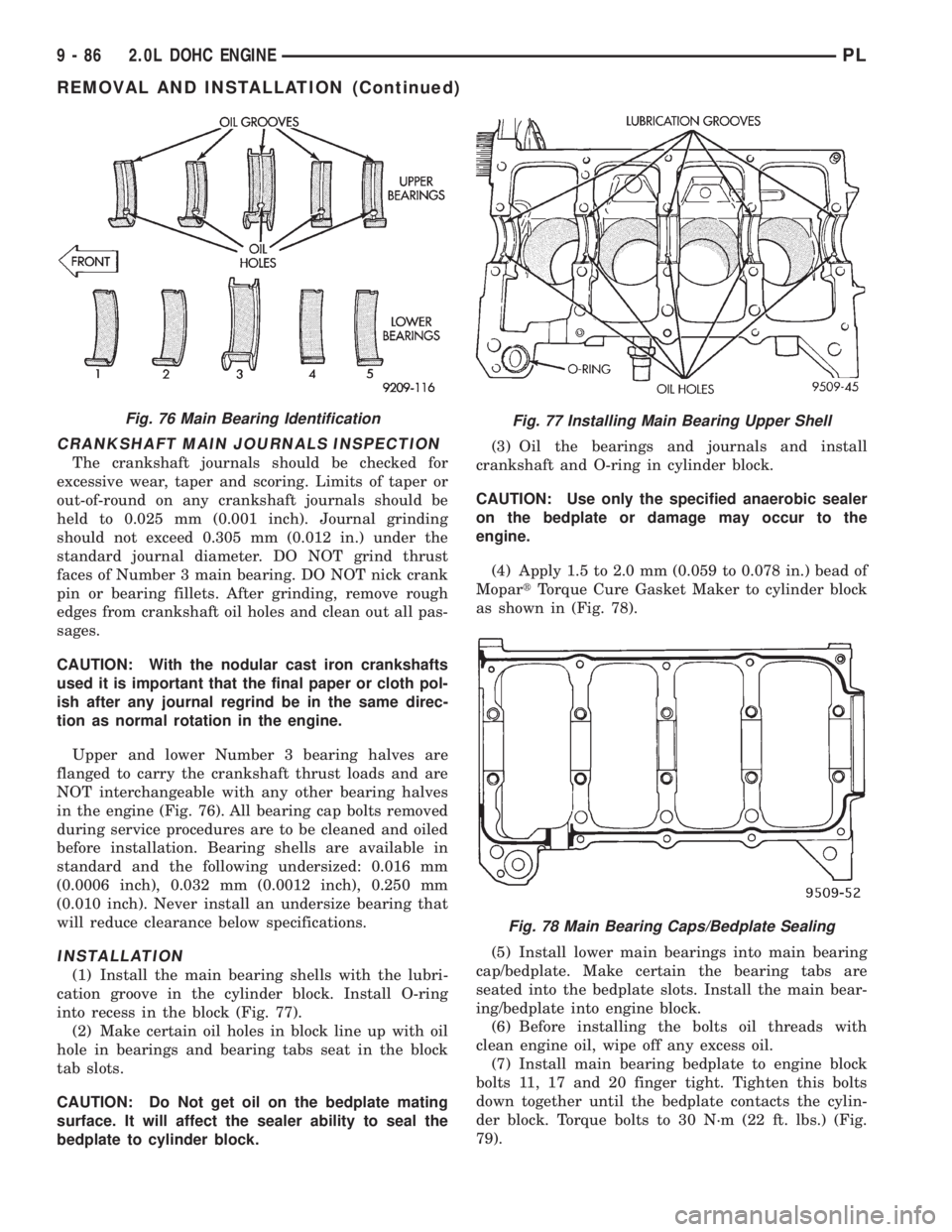
CRANKSHAFT MAIN JOURNALS INSPECTION
The crankshaft journals should be checked for
excessive wear, taper and scoring. Limits of taper or
out-of-round on any crankshaft journals should be
held to 0.025 mm (0.001 inch). Journal grinding
should not exceed 0.305 mm (0.012 in.) under the
standard journal diameter. DO NOT grind thrust
faces of Number 3 main bearing. DO NOT nick crank
pin or bearing fillets. After grinding, remove rough
edges from crankshaft oil holes and clean out all pas-
sages.
CAUTION: With the nodular cast iron crankshafts
used it is important that the final paper or cloth pol-
ish after any journal regrind be in the same direc-
tion as normal rotation in the engine.
Upper and lower Number 3 bearing halves are
flanged to carry the crankshaft thrust loads and are
NOT interchangeable with any other bearing halves
in the engine (Fig. 76). All bearing cap bolts removed
during service procedures are to be cleaned and oiled
before installation. Bearing shells are available in
standard and the following undersized: 0.016 mm
(0.0006 inch), 0.032 mm (0.0012 inch), 0.250 mm
(0.010 inch). Never install an undersize bearing that
will reduce clearance below specifications.
INSTALLATION
(1) Install the main bearing shells with the lubri-
cation groove in the cylinder block. Install O-ring
into recess in the block (Fig. 77).
(2) Make certain oil holes in block line up with oil
hole in bearings and bearing tabs seat in the block
tab slots.
CAUTION: Do Not get oil on the bedplate mating
surface. It will affect the sealer ability to seal the
bedplate to cylinder block.(3) Oil the bearings and journals and install
crankshaft and O-ring in cylinder block.
CAUTION: Use only the specified anaerobic sealer
on the bedplate or damage may occur to the
engine.
(4) Apply 1.5 to 2.0 mm (0.059 to 0.078 in.) bead of
MopartTorque Cure Gasket Maker to cylinder block
as shown in (Fig. 78).
(5) Install lower main bearings into main bearing
cap/bedplate. Make certain the bearing tabs are
seated into the bedplate slots. Install the main bear-
ing/bedplate into engine block.
(6) Before installing the bolts oil threads with
clean engine oil, wipe off any excess oil.
(7) Install main bearing bedplate to engine block
bolts 11, 17 and 20 finger tight. Tighten this bolts
down together until the bedplate contacts the cylin-
der block. Torque bolts to 30 N´m (22 ft. lbs.) (Fig.
79).
Fig. 76 Main Bearing IdentificationFig. 77 Installing Main Bearing Upper Shell
Fig. 78 Main Bearing Caps/Bedplate Sealing
9 - 86 2.0L DOHC ENGINEPL
REMOVAL AND INSTALLATION (Continued)
Page 800 of 1200
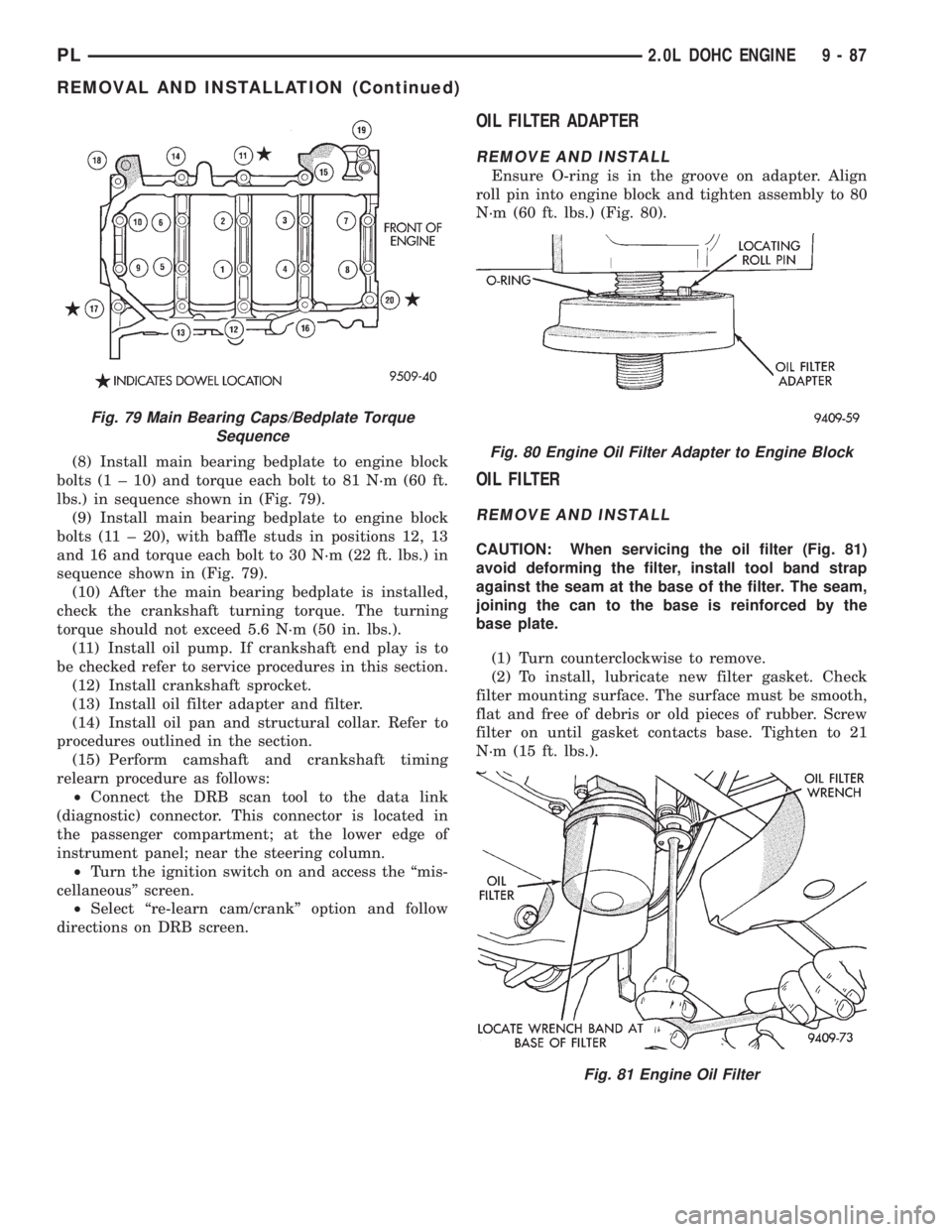
(8) Install main bearing bedplate to engine block
bolts (1 ± 10) and torque each bolt to 81 N´m (60 ft.
lbs.) in sequence shown in (Fig. 79).
(9) Install main bearing bedplate to engine block
bolts (11 ± 20), with baffle studs in positions 12, 13
and 16 and torque each bolt to 30 N´m (22 ft. lbs.) in
sequence shown in (Fig. 79).
(10) After the main bearing bedplate is installed,
check the crankshaft turning torque. The turning
torque should not exceed 5.6 N´m (50 in. lbs.).
(11) Install oil pump. If crankshaft end play is to
be checked refer to service procedures in this section.
(12) Install crankshaft sprocket.
(13) Install oil filter adapter and filter.
(14) Install oil pan and structural collar. Refer to
procedures outlined in the section.
(15) Perform camshaft and crankshaft timing
relearn procedure as follows:
²Connect the DRB scan tool to the data link
(diagnostic) connector. This connector is located in
the passenger compartment; at the lower edge of
instrument panel; near the steering column.
²Turn the ignition switch on and access the ªmis-
cellaneousº screen.
²Select ªre-learn cam/crankº option and follow
directions on DRB screen.
OIL FILTER ADAPTER
REMOVE AND INSTALL
Ensure O-ring is in the groove on adapter. Align
roll pin into engine block and tighten assembly to 80
N´m (60 ft. lbs.) (Fig. 80).
OIL FILTER
REMOVE AND INSTALL
CAUTION: When servicing the oil filter (Fig. 81)
avoid deforming the filter, install tool band strap
against the seam at the base of the filter. The seam,
joining the can to the base is reinforced by the
base plate.
(1) Turn counterclockwise to remove.
(2) To install, lubricate new filter gasket. Check
filter mounting surface. The surface must be smooth,
flat and free of debris or old pieces of rubber. Screw
filter on until gasket contacts base. Tighten to 21
N´m (15 ft. lbs.).
Fig. 79 Main Bearing Caps/Bedplate Torque
Sequence
Fig. 80 Engine Oil Filter Adapter to Engine Block
Fig. 81 Engine Oil Filter
PL2.0L DOHC ENGINE 9 - 87
REMOVAL AND INSTALLATION (Continued)