JAGUAR X308 1998 2.G Workshop Manual
Manufacturer: JAGUAR, Model Year: 1998, Model line: X308, Model: JAGUAR X308 1998 2.GPages: 2490, PDF Size: 69.81 MB
Page 301 of 2490
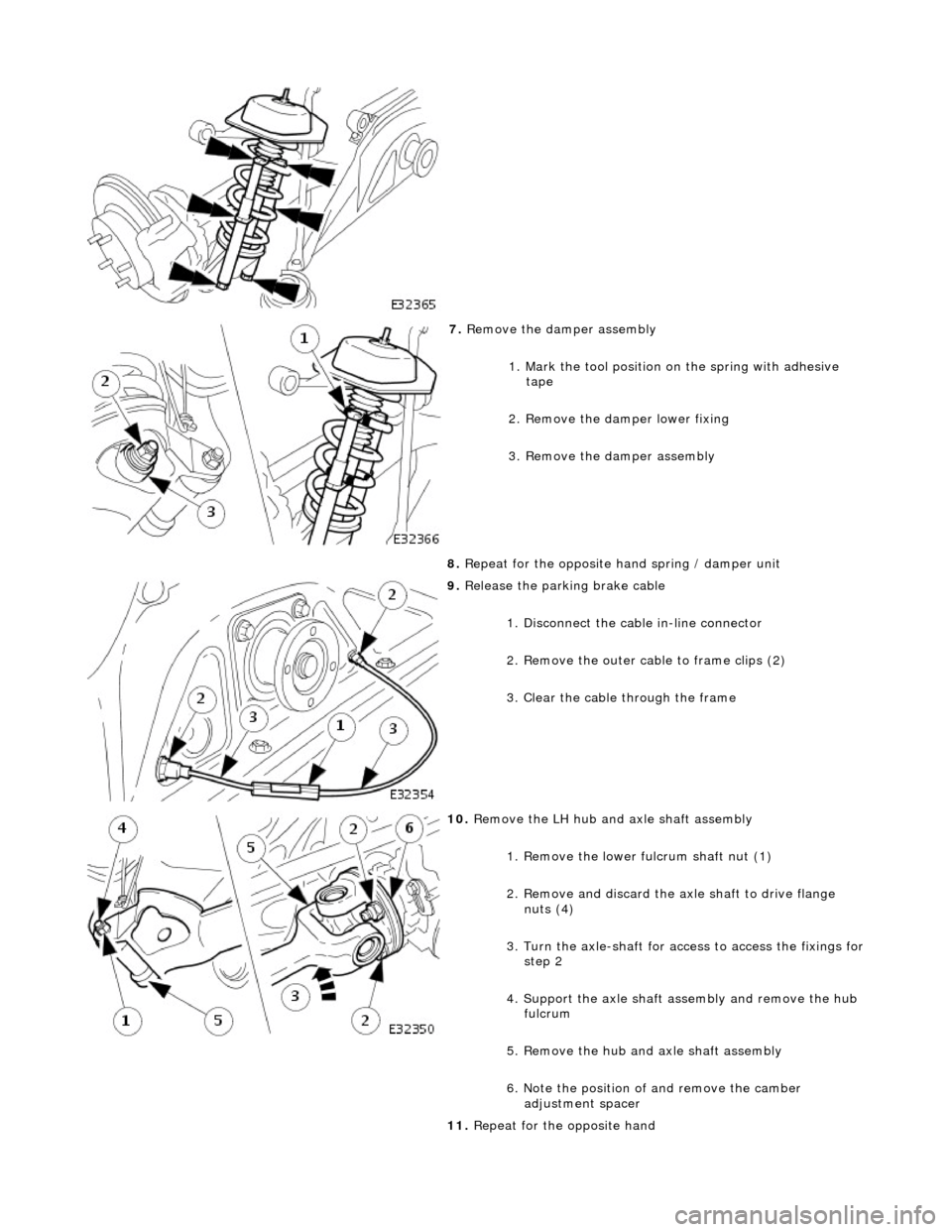
7. Re
move the damper assembly
1. Mark the tool position on the spring with adhesive
tape
2. Remove the damper lower fixing
3. Remove the damper assembly
8. Repeat for the opposite hand spring / damper unit
9. Relea
se the parking brake cable
1. Disconnect the cable in-line connector
2. Remove the outer cable to frame clips (2)
3. Clear the cable through the frame
10
.
Remove the LH hub and axle shaft assembly
1. Remove the lower fulcrum shaft nut (1)
2. Remove and discard the axle shaft to drive flange nuts (4)
3. Turn the axle-shaft for ac cess to access the fixings for
step 2
4. Support the axle shaft a ssembly and remove the hub
fulcrum
5. Remove the hub and axle shaft assembly
6. Note the position of and remove the camber adjustment spacer
11. Repeat for the opposite hand
Page 302 of 2490
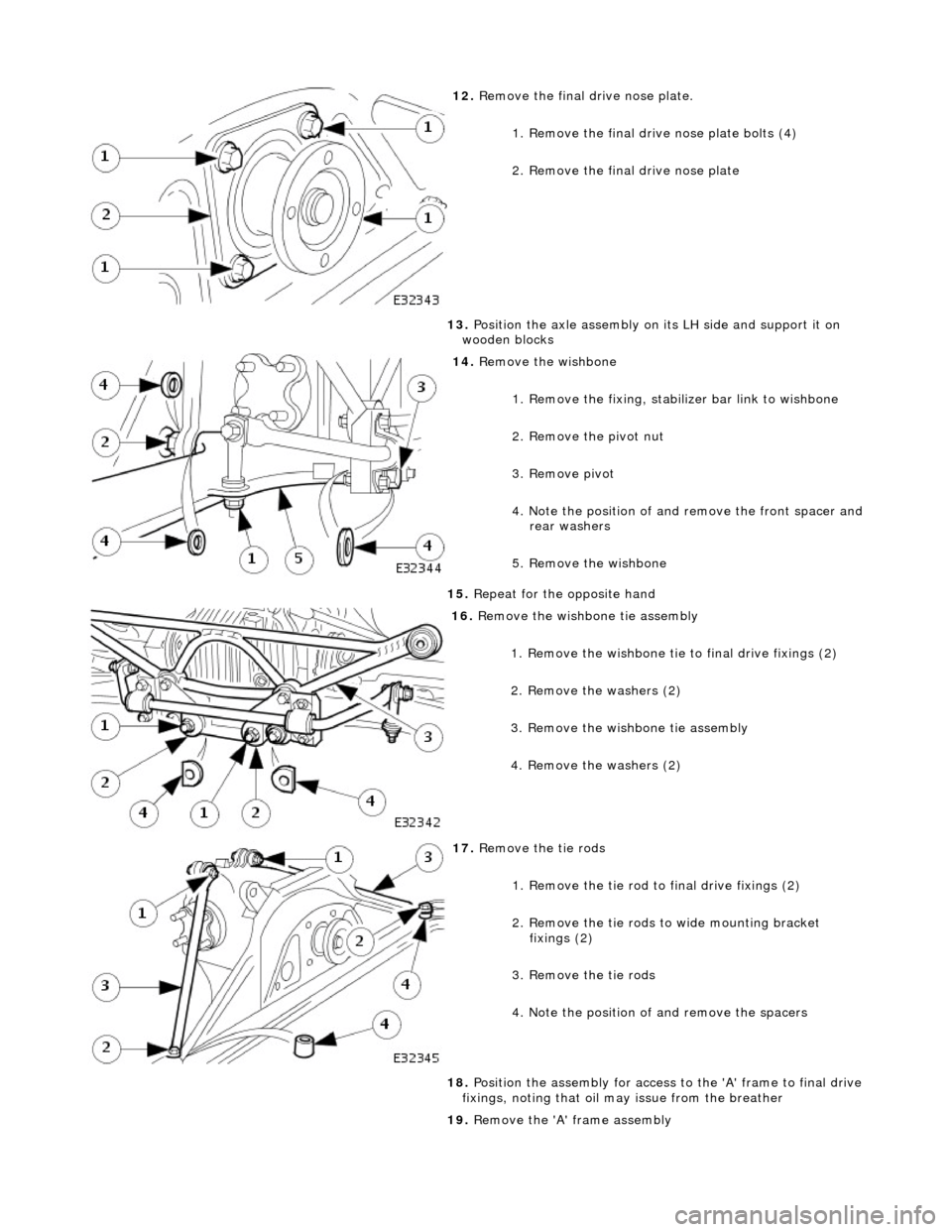
12. R
emove the final dr
ive nose plate.
1. Remove the final drive nose plate bolts (4)
2. Remove the final drive nose plate
13. Position the axle assembly on its LH side and support it on
wooden blocks
14 . Re
move the wishbone
1. Remove the fixing, stabilizer bar link to wishbone
2. Remove the pivot nut
3. Remove pivot
4. Note the position of and remove the front spacer and
rear washers
5. Remove the wishbone
15. Repeat for the opposite hand
16 . R
emove the wishbone tie assembly
1. Remove the wishbone tie to final drive fixings (2)
2. Remove the washers (2)
3. Remove the wishbone tie assembly
4. Remove the washers (2)
17. R
emove the tie rods
1. Remove the tie rod to final drive fixings (2)
2. Remove the tie rods to wide mounting bracket
fixings (2)
3. Remove the tie rods
4. Note the position of and remove the spacers
18. Position the assembly for access to the 'A' frame to final drive
fixings, noting that oil may issue from the breather
19. Remove the 'A' frame assembly
Page 303 of 2490
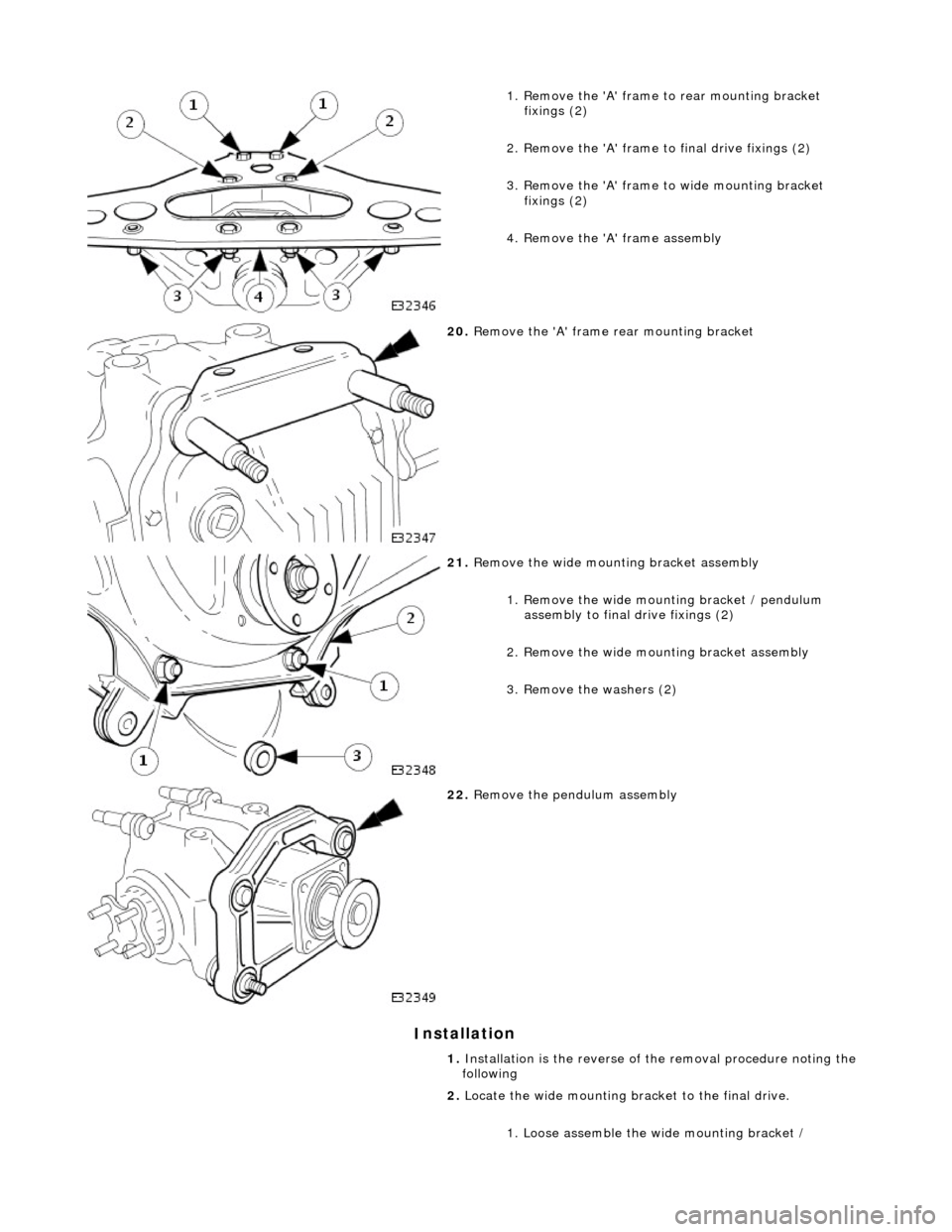
I
nstallation
1
. Remove the 'A' frame to rear mounting bracket
fixings (2)
2. Remove the 'A' frame to final drive fixings (2)
3. Remove the 'A' frame to wide mounting bracket fixings (2)
4. Remove the 'A' frame assembly
20
.
Remove the 'A' frame rear mounting bracket
21
.
Remove the wide mounting bracket assembly
1. Remove the wide mounting bracket / pendulum assembly to final drive fixings (2)
2. Remove the wide mounting bracket assembly
3. Remove the washers (2)
22
.
Remove the pendulum assembly
1. Installation is the re verse of the removal procedure noting the
following
2. Locate the wide mounting br acket to the final drive.
1. Loose assemble the wide mounting bracket /
Page 304 of 2490
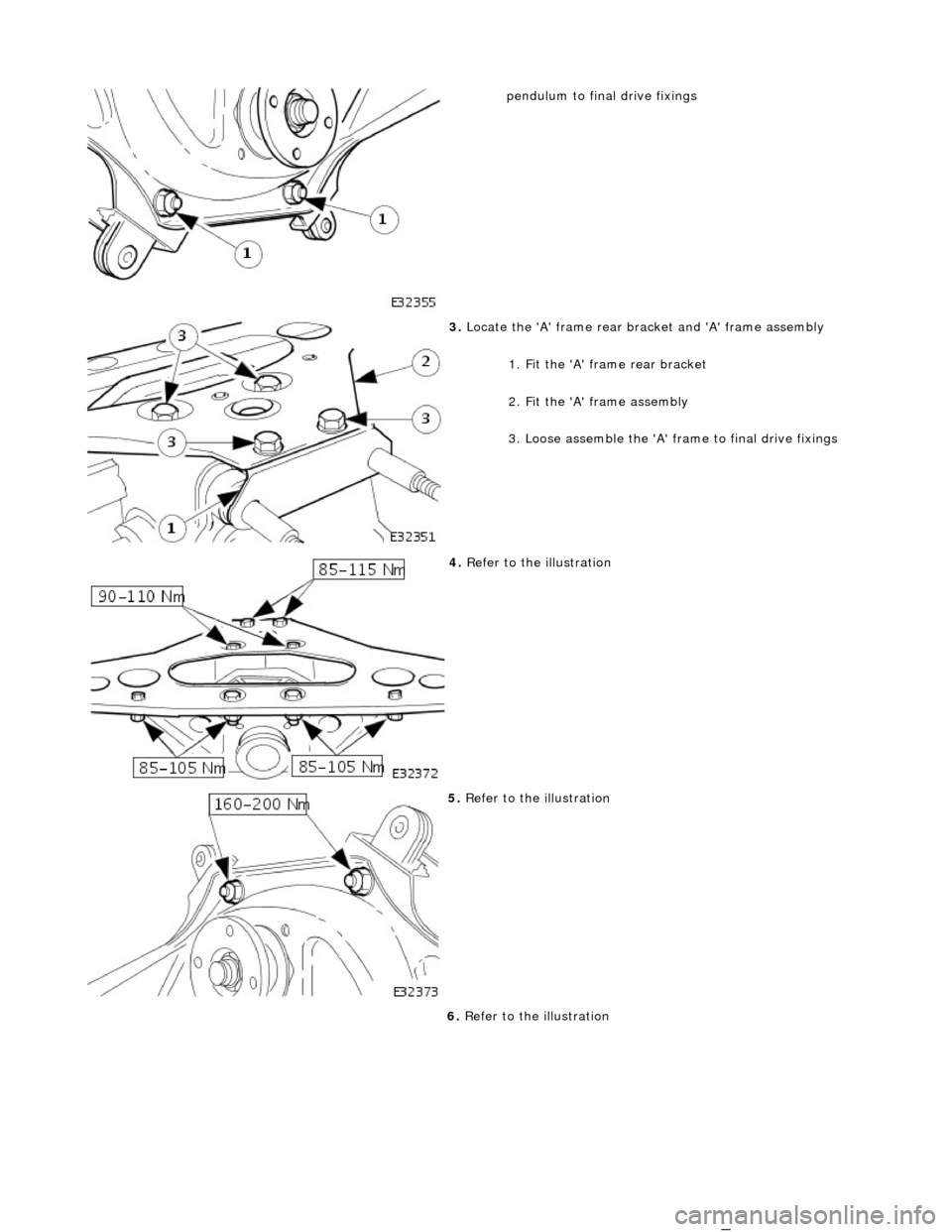
pe
ndulum to final drive fixings
3. Locate th
e 'A' frame rear bracket and 'A' frame assembly
1. Fit the 'A' frame rear bracket
2. Fit the 'A' frame assembly
3. Loose assemble the 'A' frame to final drive fixings
4. Re
fer to the illustration
5. Re
fer to the illustration
6. Refer to the illustration _
Page 305 of 2490
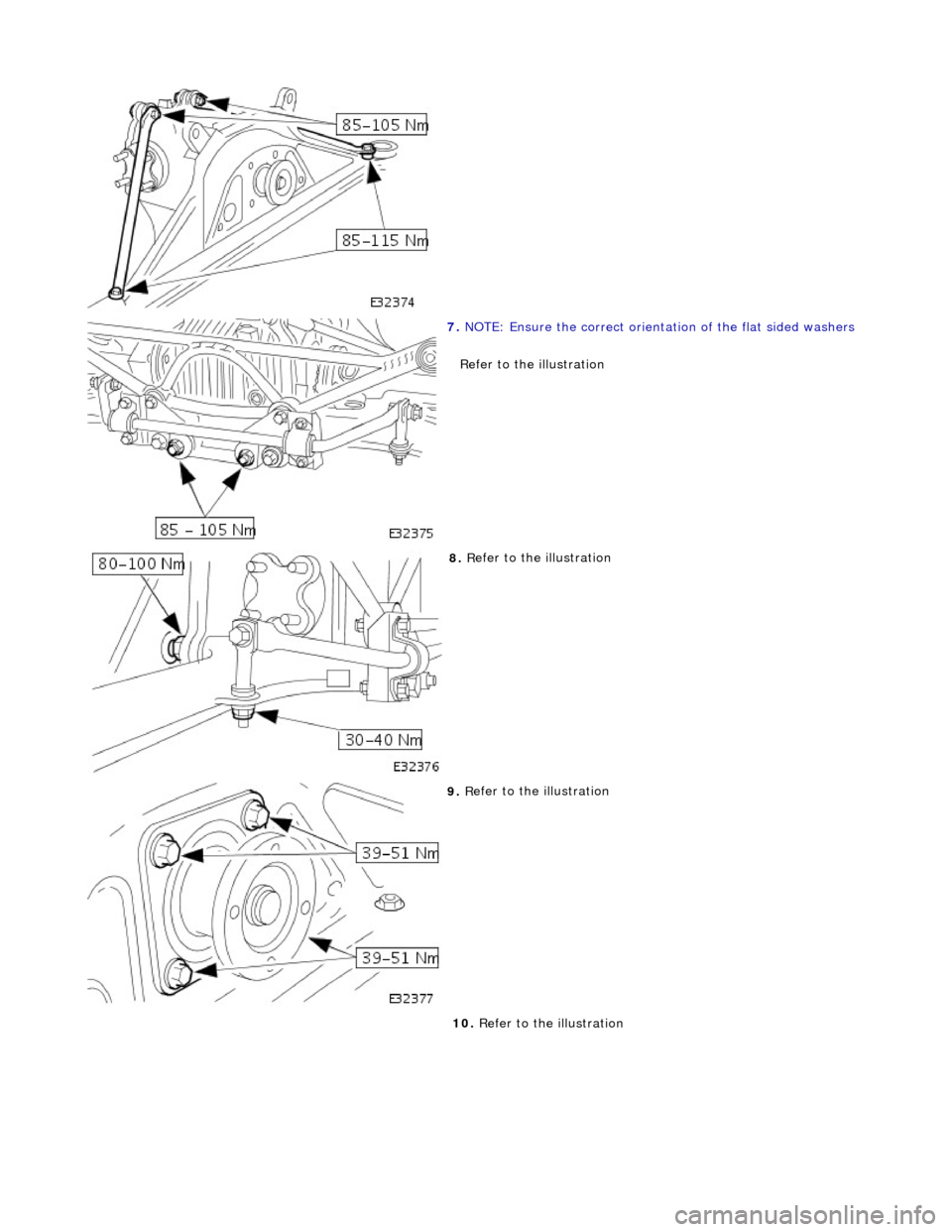
7. N
OTE: Ensure
the correct orientation of the flat sided washers
Refer to the illustration
8. R
efer to the illustration
9. R
efer to the illustration
10. Refer to the illustration
Page 306 of 2490
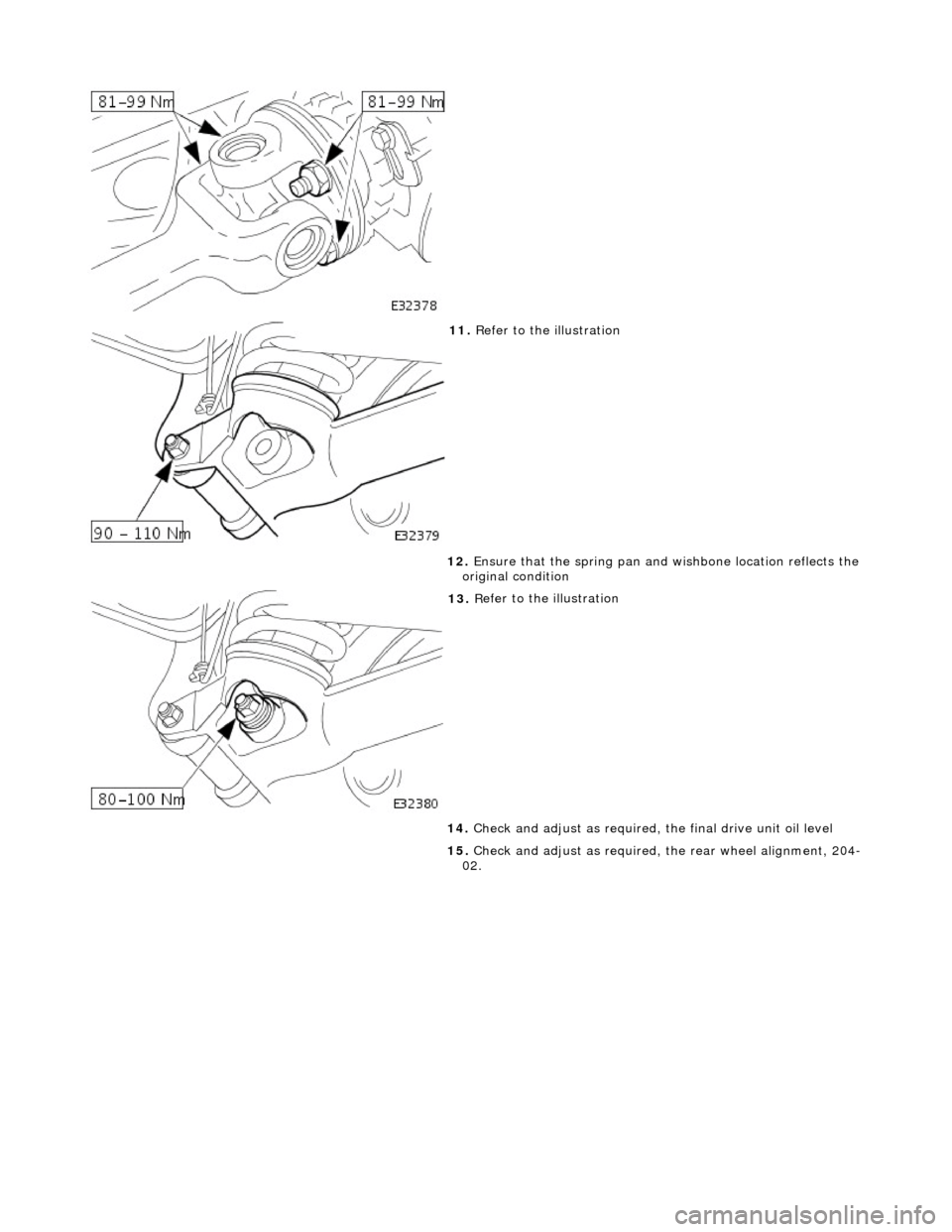
11
. R
efer to the illustration
12. Ensure that the spring pan and wishbone location reflects the
original condition
13 . R
efer to the illustration
14. Check and adjust as required, the final drive unit oil level
15. Check and adjust as required, the rear wheel alignment, 204-
02.
Page 307 of 2490
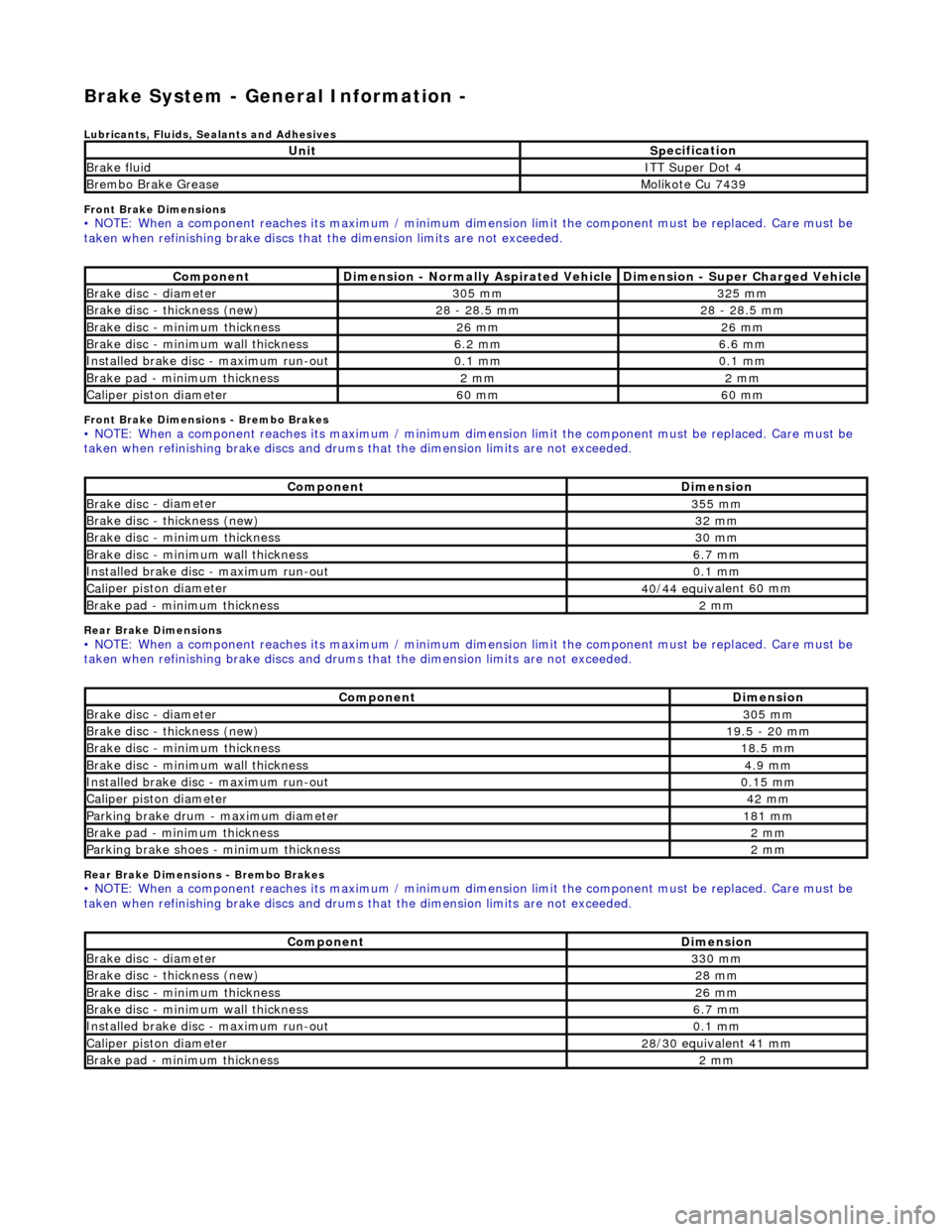
Brake S
ystem - General Information -
Lu
bricants, Fluids, Sealants and Adhesives
Front Brake Dimensions
• NO
TE: When a component reaches its maximum / minimum dimension limit the component must be replaced. Care must be
taken when refinishing brake discs that the dimension limits are not exceeded.
F
ront Brake Dimensions - Brembo Brakes
• NO
TE: When a component reaches its maximum / minimum dimension limit the component must be replaced. Care must be
taken when refinishing brake discs and drums that the dimension limits are not exceeded.
R
ear Brake Dimensions
• NO
TE: When a component reaches its maximum / minimum dimension limit the component must be replaced. Care must be
taken when refinishing brake discs and drums that the dimension limits are not exceeded.
R
ear Brake Dimensions - Brembo Brakes
• NO
TE: When a component reaches its maximum / minimum dimension limit the component must be replaced. Care must be
taken when refinishing brake discs and drums that the dimension limits are not exceeded.
UnitSp
ecification
Bra
ke fluid
IT
T Super Dot 4
Brembo Br
ake Grease
M
olikote Cu 7439
Co
mponent
Dimension - Normall
y Aspirated Vehicle
Dimension
- Super Charged Vehicle
Brake disc
- diameter
305 mm325 mm
Brake disc
- thickness (new)
28
- 28.5 mm
28 -
28.5 mm
B
rake disc - minimum thickness
26 mm26 mm
B
rake disc - minimum wall thickness
6.2 mm6.6 mm
I
nstalled brake disc - maximum run-out
0.1 mm0.1 mm
B
rake pad - minimum thickness
2 mm2 mm
Cal
iper piston diameter
60 mm60 mm
Co
mponent
Dimension
Brake disc
- diameter
355 mm
Brake disc
- thickness (new)
32 mm
B
rake disc - minimum thickness
30 mm
B
rake disc - minimum wall thickness
6.7 mm
I
nstalled brake disc - maximum run-out
0.1 mm
Cal
iper piston diameter
40/44 equiv
alent 60 mm
B
rake pad - minimum thickness
2 mm
Co
mponent
Dimension
Brake disc
- diameter
305 mm
Brake disc
- thickness (new)
19.5
- 20 mm
B
rake disc - minimum thickness
18.5 mm
B
rake disc - minimum wall thickness
4.9 mm
I
nstalled brake disc - maximum run-out
0.15 mm
Cal
iper piston diameter
42 mm
Pa
rking brake drum - maximum diameter
181 mm
B
rake pad - minimum thickness
2 mm
Pa
rking brake shoes - minimum thickness
2 mm
Co
mponent
Dimension
Brake disc
- diameter
330 mm
Brake disc
- thickness (new)
28 mm
B
rake disc - minimum thickness
26 mm
B
rake disc - minimum wall thickness
6.7 mm
I
nstalled brake disc - maximum run-out
0.1 mm
Cal
iper piston diameter
28/30 equiv
alent 41 mm
B
rake pad - minimum thickness
2 mm
Page 308 of 2490
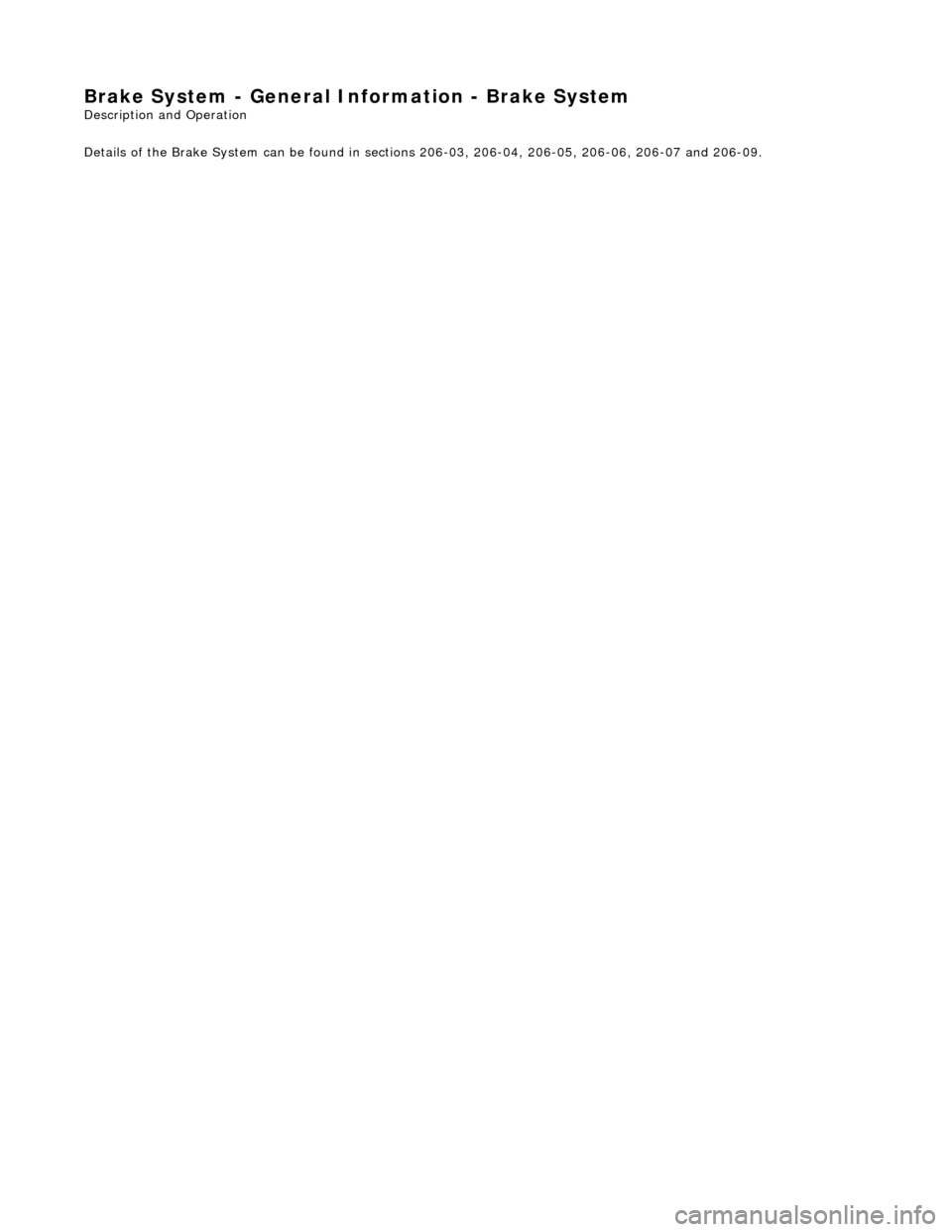
Brake System - Gener
al Information - Brake System
Description an
d Operation
Details of the Brake System can be found in sections 206-03, 206-04, 206-05, 206-06, 206-07 and 206-09.
Page 309 of 2490
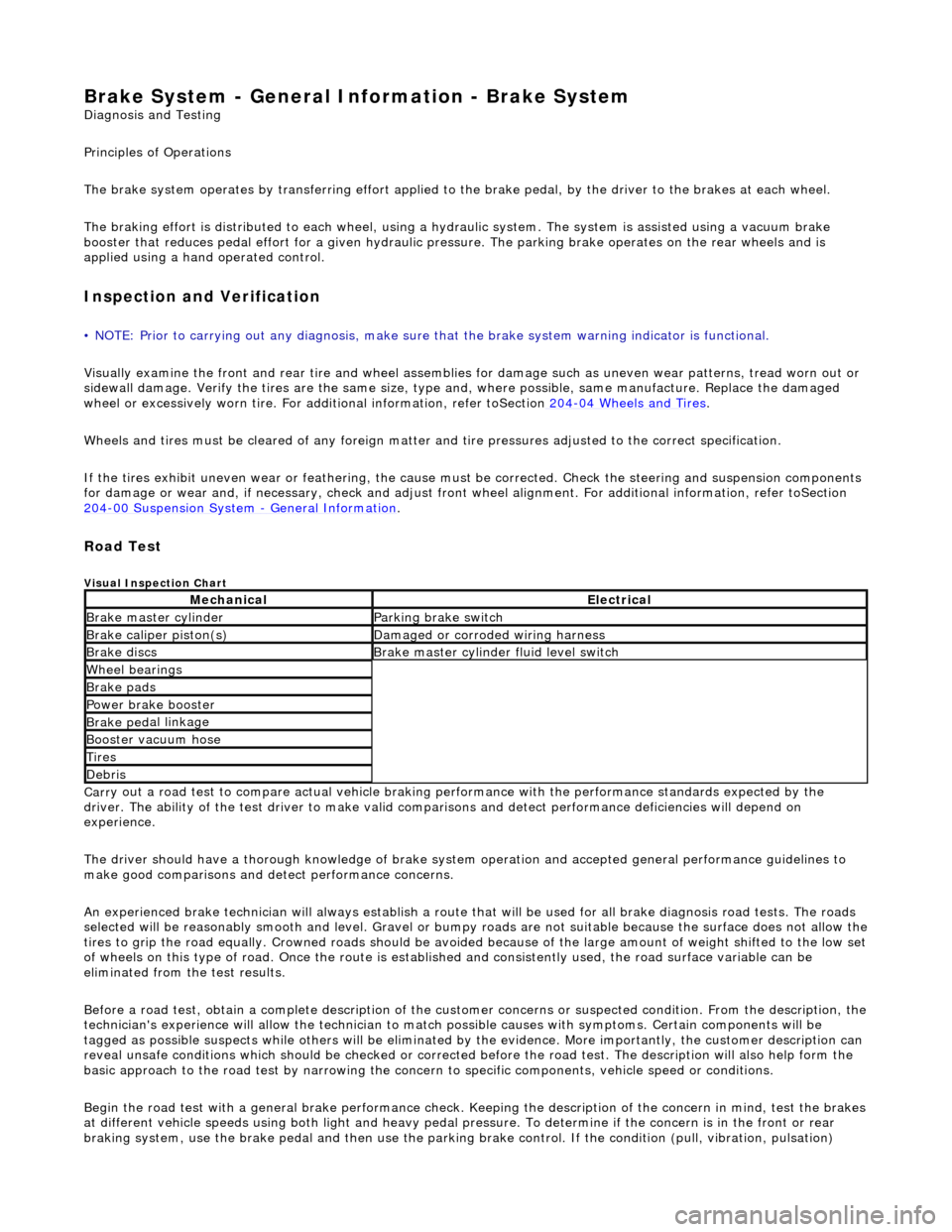
Brake System - General Inform
ation - Brake System
D
iagnosis and Testing
Principles of Operations
The brake system operates by transferring effort applied to th e brake pedal, by the driver to the brakes at each wheel.
The braking effort is distributed to each wheel, using a hydraulic system. The system is assisted using a vacuum brake
booster that reduces pedal effort for a given hydraulic pressure. The parking brake operates on the rear wheels and is
applied using a hand operated control.
I
nspection and Verification
•
NOTE: Prior to carrying out any diagno
sis, make sure that the brake system warning indicator is functional.
Visually examine the front and rear tire and wheel assemblies for damage such as un even wear patterns, tread worn out or
sidewall damage. Verify the tires are th e same size, type and, where possible, same manufacture. Replace the damaged
wheel or excessively worn tire. For a dditional information, refer toSection 204
-0
4 Wheels and Tires
.
W
heels and tires must be cleared of an
y foreign matter and tire pressures ad justed to the correct specification.
If the tires exhibit uneven wear or feathering, the cause must be corrected. Check the steering and suspension components
for damage or wear and, if ne cessary, check and adjust front wheel alignment. For additional information, refer toSection
204
-00 Suspen
sion System
- General Informati
on
.
Road Test
V
isual Inspection Chart
Carr
y out a road test to compare actual vehicle braking performance with the
performance standards expected by the
driver. The ability of the test driver to make valid compar isons and detect performance deficiencies will depend on
experience.
The driver should have a thorough knowledge of brake system operation and accepted general performance guidelines to
make good comparisons and de tect performance concerns.
An experienced brake technician will always establish a route that will be used for all br ake diagnosis road tests. The roads
selected will be reasonably smooth and level. Gravel or bump y roads are not suitable because the surface does not allow the
tires to grip the road equally. Crowned roads should be avoide d because of the large amount of weight shifted to the low set
of wheels on this type of road. Once th e route is established and consistently used, the road surface variable can be
eliminated from the test results.
Before a road test, obtain a complete description of the customer concerns or suspec ted condition. From the description, the
technician's experience will allow the te chnician to match possible causes with symptoms. Certain components will be
tagged as possible suspects while others wi ll be eliminated by the evidence. More importantly, the customer description can
reveal unsafe conditions which should be ch ecked or corrected before the road test. The description will also help form the
basic approach to the road test by narrowing the concern to specific components, vehicle speed or conditions.
Begin the road test with a general brake performance check. Keeping the description of the concern in mind, test the brakes
at different vehicle speeds using both ligh t and heavy pedal pressure. To determine if the concern is in the front or rear
braking system, use the brake pe dal and then use the parking brake control. If the condition (pull, vibration, pulsation)
MechanicalElectrical
Brake m
aster cylinder
Parkin
g brake switch
Brake ca
liper piston(s)
D
amaged or corroded wiring harness
Brake di
scs
B
rake master cylinder fluid level switch
Wh
eel bearin
gs
Brake pads
Power brake booster
Brake ped
al linkage
Boost
er vacuum hose
Tire
s
De
bris
Page 310 of 2490
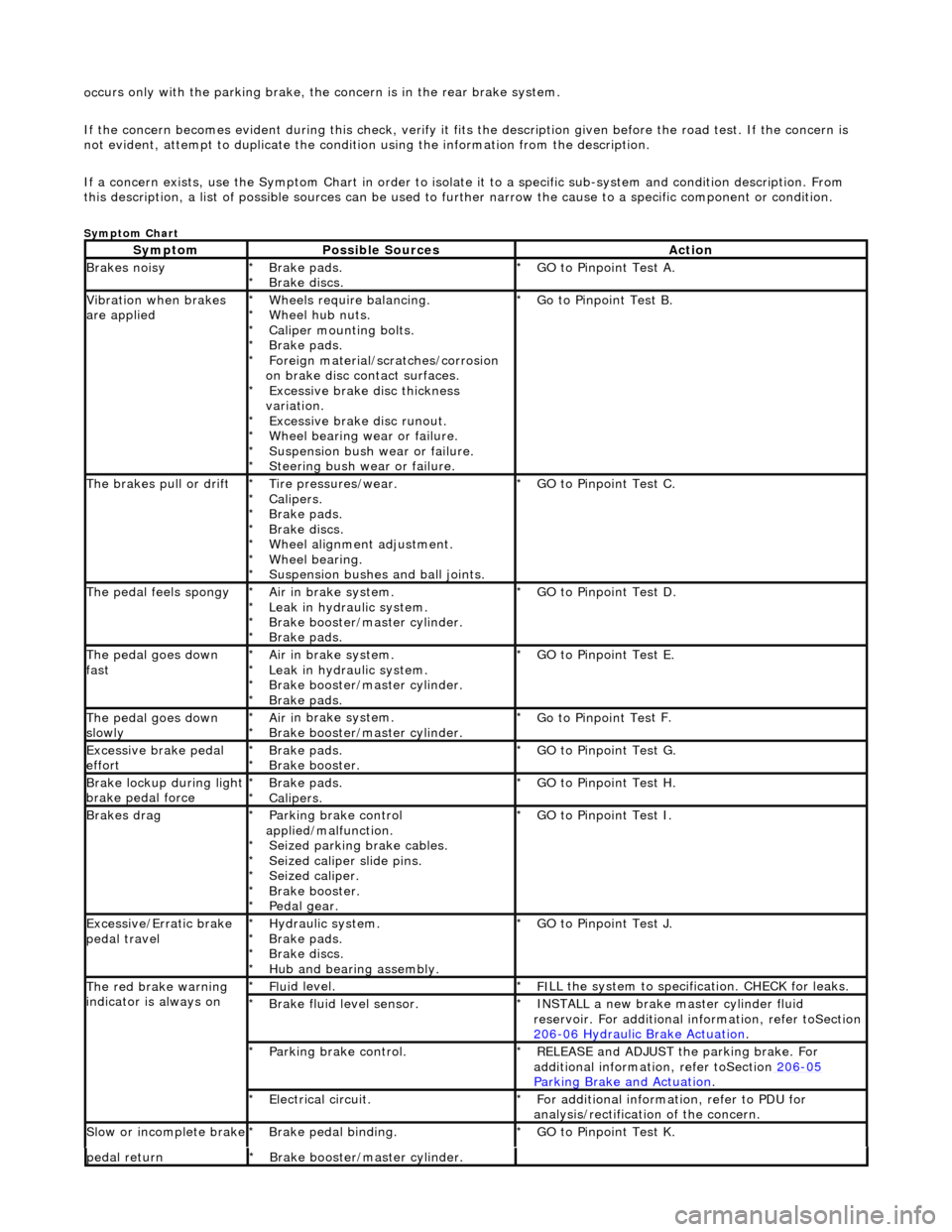
oc
curs only with the parking brake, th
e concern is in the rear brake system.
If the concern becomes evident during this check, verify it fits the description given before the road test. If the concern is
not evident, attempt to duplicate the condition using the information from the description.
If a concern exists, use the Symptom Chart in order to isolate it to a specific sub-system and condition description. From
this description, a list of possible sources can be used to further narrow the cause to a specific component or condition.
Sym
ptom Chart
Sy
m
ptom
Possib
l
e Sources
Acti
o
n
Brakes
n
oisy
Brake pads.
Brake di
scs
.
*
*
GO to Pinpoint
Tes
t A.
*
Vibration wh
en brakes
are applied
Wh eels require bala
ncing.
Wheel hub nuts.
Caliper mounting bolts.
Brake pads.
Foreign material/scr atches/corrosion
on brake disc contact surfaces. Excessive brake disc thickness
variation. Excessive brake disc runout.
Wheel bearing wear or failure.
Suspension bush wear or failure.
Steering bush wear or failure.
*
*
*
*
*
*
*
*
*
*
Go to Pinpoint
Tes
t B.
*
The brakes pull or drif tTire pressures/wear.
Calipers.
Brake pads.
Brake di
scs.
Wheel alignment adjustment.
Wheel bearing.
Suspension bushes and ball joints.
*
*
*
*
*
*
*
GO to Pinpoint
Tes
t C.
*
The pedal feels spongyAir i
n brake system.
Leak in hydraulic system.
Brake booster/master cylinder.
Brake pads.
*
*
*
*
GO to Pinpoint Tes
t D.
*
The pedal goes down
fa s
t
Ai
r i
n brake system.
Leak in hydraulic system.
Brake booster/master cylinder.
Brake pads.
*
*
*
*
GO to Pinpoint
Tes
t E.
*
The pedal goes down
slowl yAir i
n brake system.
Brake booster/master cylinder.
*
*
Go to Pinpoint
Tes
t F.
*
Excessive brake pedal
effor tBrake pads.
Brake booster.
*
*GO to Pinpoint
Tes
t G.
*
Brake lockup du ring ligh
t
brake pedal force
Brake pads.
Calipers.
*
*GO to Pinpoint
Tes
t H.
*
Brakes d r
ag
Parkin
g brake con
trol
applied/malfunction. Seized parking brake cables.
Seized caliper slide pins.
Seized caliper.
Brake booster.
Pedal gear.
*
*
*
*
*
*
GO to Pinpoint
Tes
t I.
*
Exce ssi
ve/Erratic brake
pedal travel
Hydrau li
c system.
Brake pads.
Brake discs.
Hub and bearing assembly.
*
*
*
*
GO to Pinpoint
Tes
t J.
*
The red brak e warning
indi
cator is always on
Fl
ui
d level.
*
F I
LL the system to specification. CHECK for leaks.
*
Brake flu i
d level sensor.
*
I N
STALL a new brake master cylinder fluid
reservoir. For additional in formation, refer toSection
206
-0 6
Hydraulic Brake Actuation
.
*
Parkin
g brake con
trol.
*
REL
E
ASE and ADJUST the parking brake. For
additional information, refer toSection 206
-05
Parkin g Brake an
d Actuation
.
*
E
l
ectrical circuit.
*
F or additional
information, refer to PDU for
analysis/rectification of the concern.
*
Sl
ow or i
ncomplete brake
Brake peda
l binding.
*
GO to Pinpoint Tes
t K.
*
pedal retu rnBr
ake booster/master cylinder.
*