LAND ROVER FREELANDER 2001 Workshop Manual
Manufacturer: LAND ROVER, Model Year: 2001, Model line: FREELANDER, Model: LAND ROVER FREELANDER 2001Pages: 1007, PDF Size: 23.47 MB
Page 841 of 1007
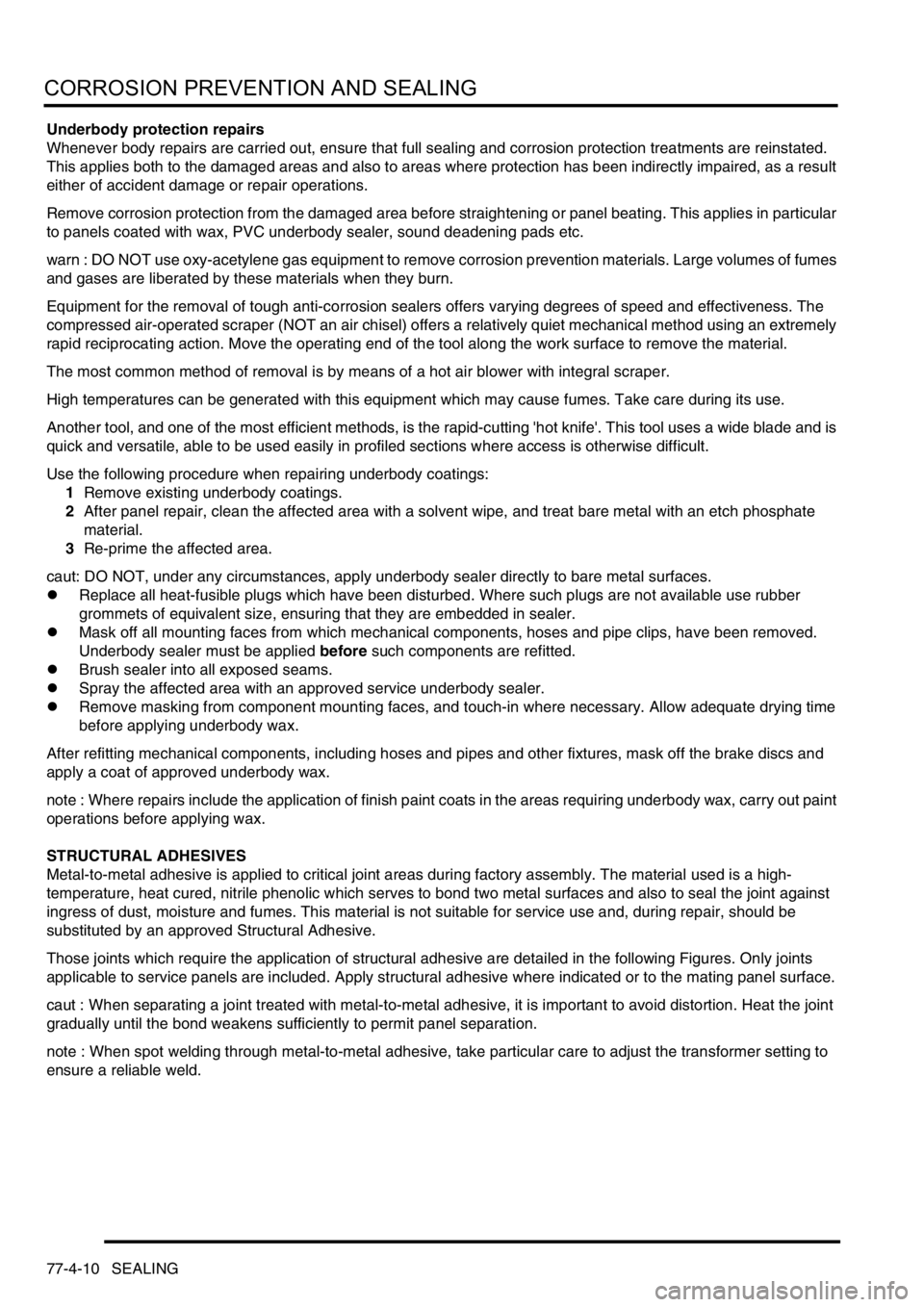
CORROSION PREVENTION AND SEALING
77-4-10 SEALING
Underbody protection repairs
Whenever body repairs are carried out, ensure that full sealing and corrosion protection treatments are reinstated.
This applies both to the damaged areas and also to areas where protection has been indirectly impaired, as a result
either of accident damage or repair operations.
Remove corrosion protection from the damaged area before straightening or panel beating. This applies in particular
to panels coated with wax, PVC underbody sealer, sound deadening pads etc.
warn : DO NOT use oxy-acetylene gas equipment to remove corrosion prevention materials. Large volumes of fumes
and gases are liberated by these materials when they burn.
Equipment for the removal of tough anti-corrosion sealers offers varying degrees of speed and effectiveness. The
compressed air-operated scraper (NOT an air chisel) offers a relatively quiet mechanical method using an extremely
rapid reciprocating action. Move the operating end of the tool along the work surface to remove the material.
The most common method of removal is by means of a hot air blower with integral scraper.
High temperatures can be generated with this equipment which may cause fumes. Take care during its use.
Another tool, and one of the most efficient methods, is the rapid-cutting 'hot knife'. This tool uses a wide blade and is
quick and versatile, able to be used easily in profiled sections where access is otherwise difficult.
Use the following procedure when repairing underbody coatings:
1Remove existing underbody coatings.
2After panel repair, clean the affected area with a solvent wipe, and treat bare metal with an etch phosphate
material.
3Re-prime the affected area.
caut: DO NOT, under any circumstances, apply underbody sealer directly to bare metal surfaces.
lReplace all heat-fusible plugs which have been disturbed. Where such plugs are not available use rubber
grommets of equivalent size, ensuring that they are embedded in sealer.
lMask off all mounting faces from which mechanical components, hoses and pipe clips, have been removed.
Underbody sealer must be applied before such components are refitted.
lBrush sealer into all exposed seams.
lSpray the affected area with an approved service underbody sealer.
lRemove masking from component mounting faces, and touch-in where necessary. Allow adequate drying time
before applying underbody wax.
After refitting mechanical components, including hoses and pipes and other fixtures, mask off the brake discs and
apply a coat of approved underbody wax.
note : Where repairs include the application of finish paint coats in the areas requiring underbody wax, carry out paint
operations before applying wax.
STRUCTURAL ADHESIVES
Metal-to-metal adhesive is applied to critical joint areas during factory assembly. The material used is a high-
temperature, heat cured, nitrile phenolic which serves to bond two metal surfaces and also to seal the joint against
ingress of dust, moisture and fumes. This material is not suitable for service use and, during repair, should be
substituted by an approved Structural Adhesive.
Those joints which require the application of structural adhesive are detailed in the following Figures. Only joints
applicable to service panels are included. Apply structural adhesive where indicated or to the mating panel surface.
caut : When separating a joint treated with metal-to-metal adhesive, it is important to avoid distortion. Heat the joint
gradually until the bond weakens sufficiently to permit panel separation.
note : When spot welding through metal-to-metal adhesive, take particular care to adjust the transformer setting to
ensure a reliable weld.
Page 842 of 1007
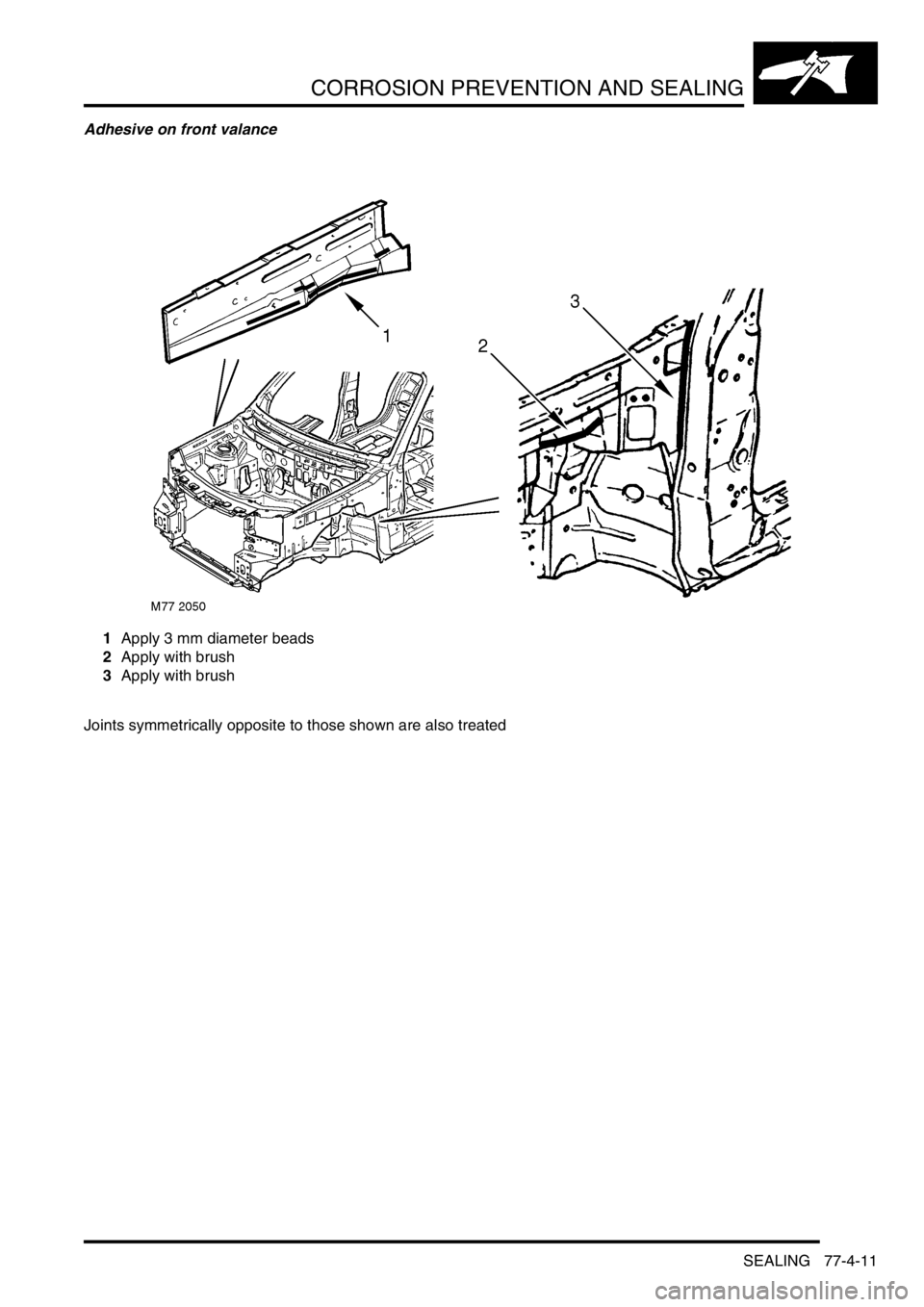
CORROSION PREVENTION AND SEALING
SEALING 77-4-11
Adhesive on front valance
1Apply 3 mm diameter beads
2Apply with brush
3Apply with brush
Joints symmetrically opposite to those shown are also treated
Page 843 of 1007
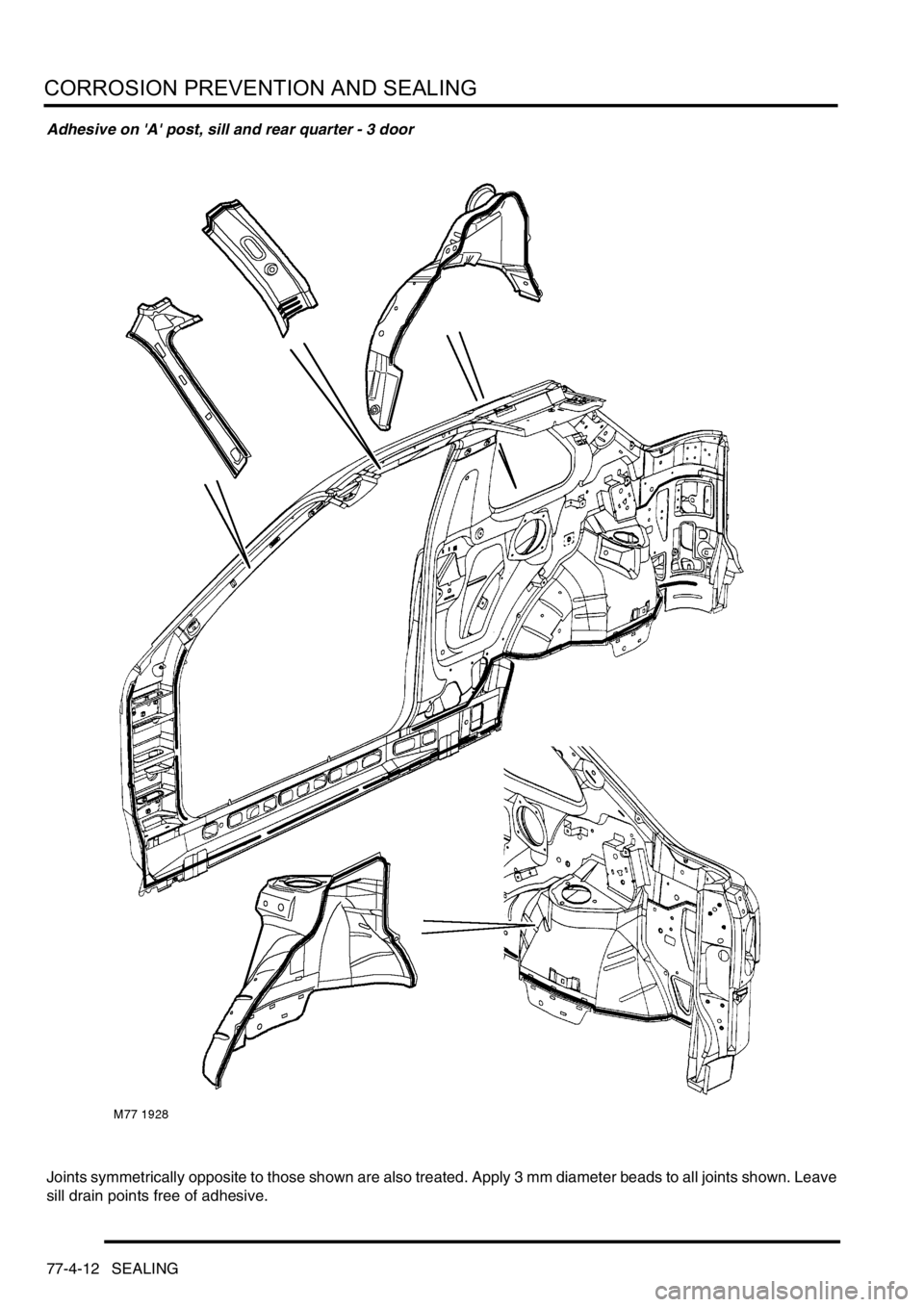
CORROSION PREVENTION AND SEALING
77-4-12 SEALING
Adhesive on 'A' post, sill and rear quarter - 3 door
Joints symmetrically opposite to those shown are also treated. Apply 3 mm diameter beads to all joints shown. Leave
sill drain points free of adhesive.
Page 844 of 1007
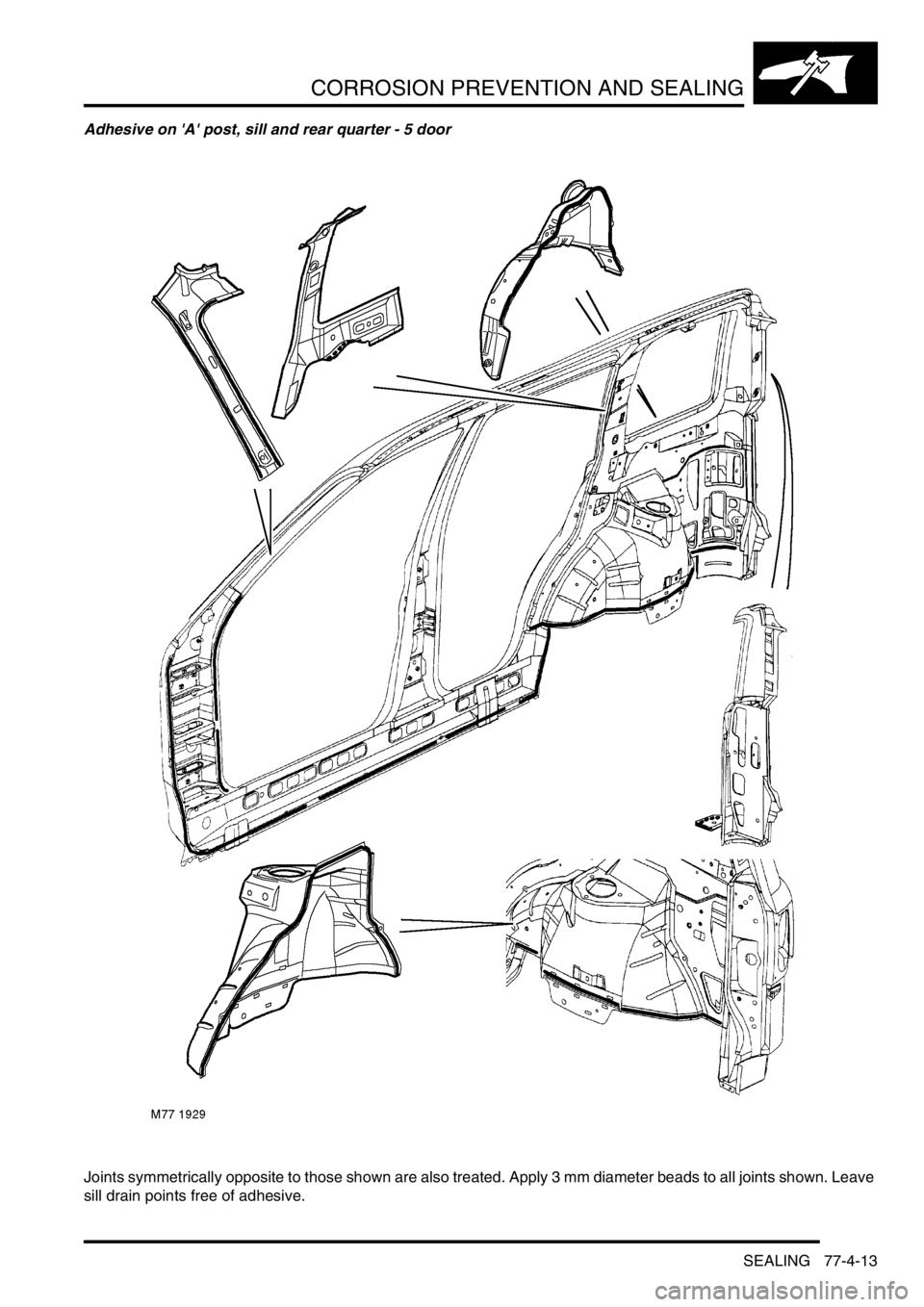
CORROSION PREVENTION AND SEALING
SEALING 77-4-13
Adhesive on 'A' post, sill and rear quarter - 5 door
Joints symmetrically opposite to those shown are also treated. Apply 3 mm diameter beads to all joints shown. Leave
sill drain points free of adhesive.
Page 845 of 1007
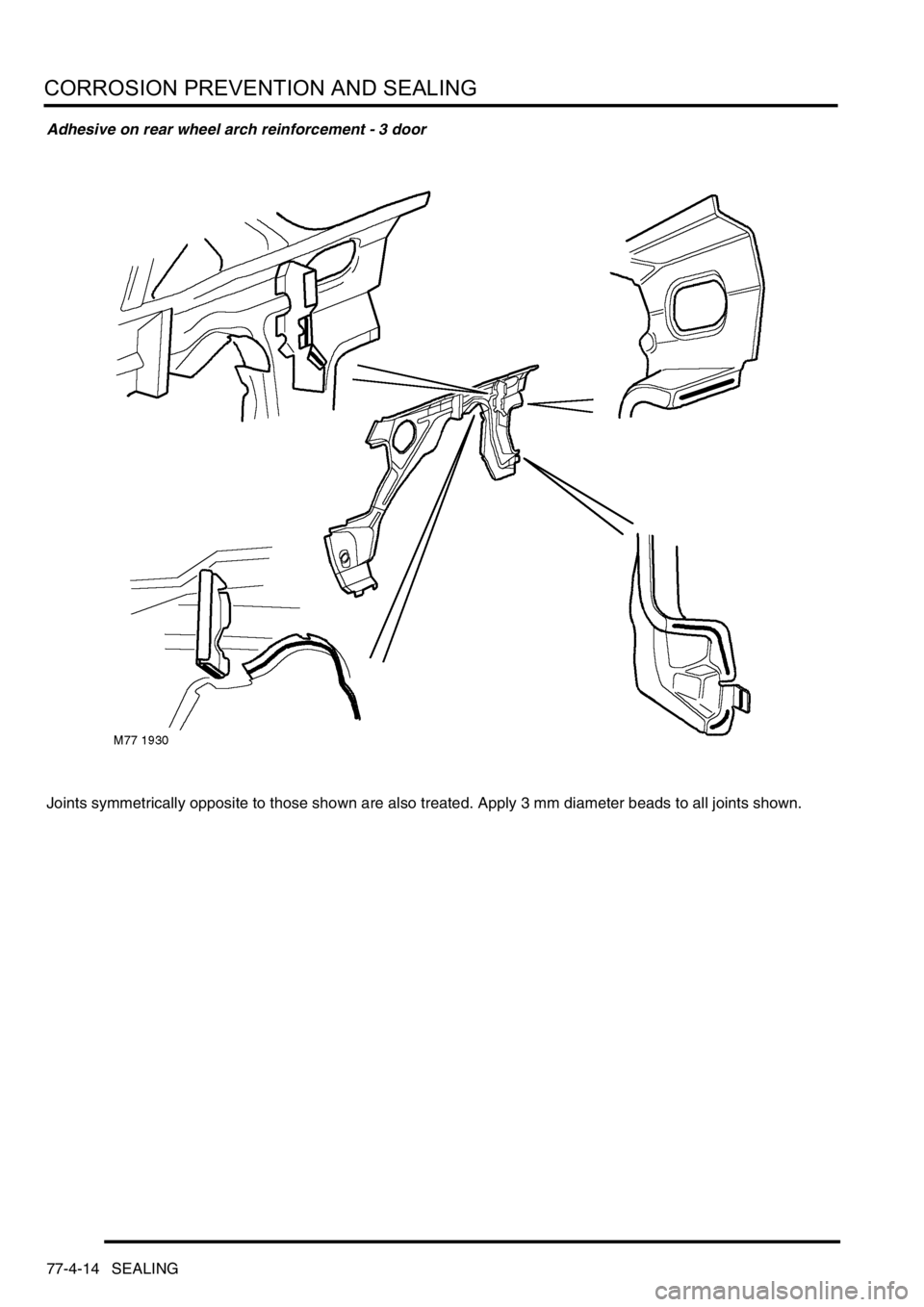
CORROSION PREVENTION AND SEALING
77-4-14 SEALING
Adhesive on rear wheel arch reinforcement - 3 door
Joints symmetrically opposite to those shown are also treated. Apply 3 mm diameter beads to all joints shown.
Page 846 of 1007
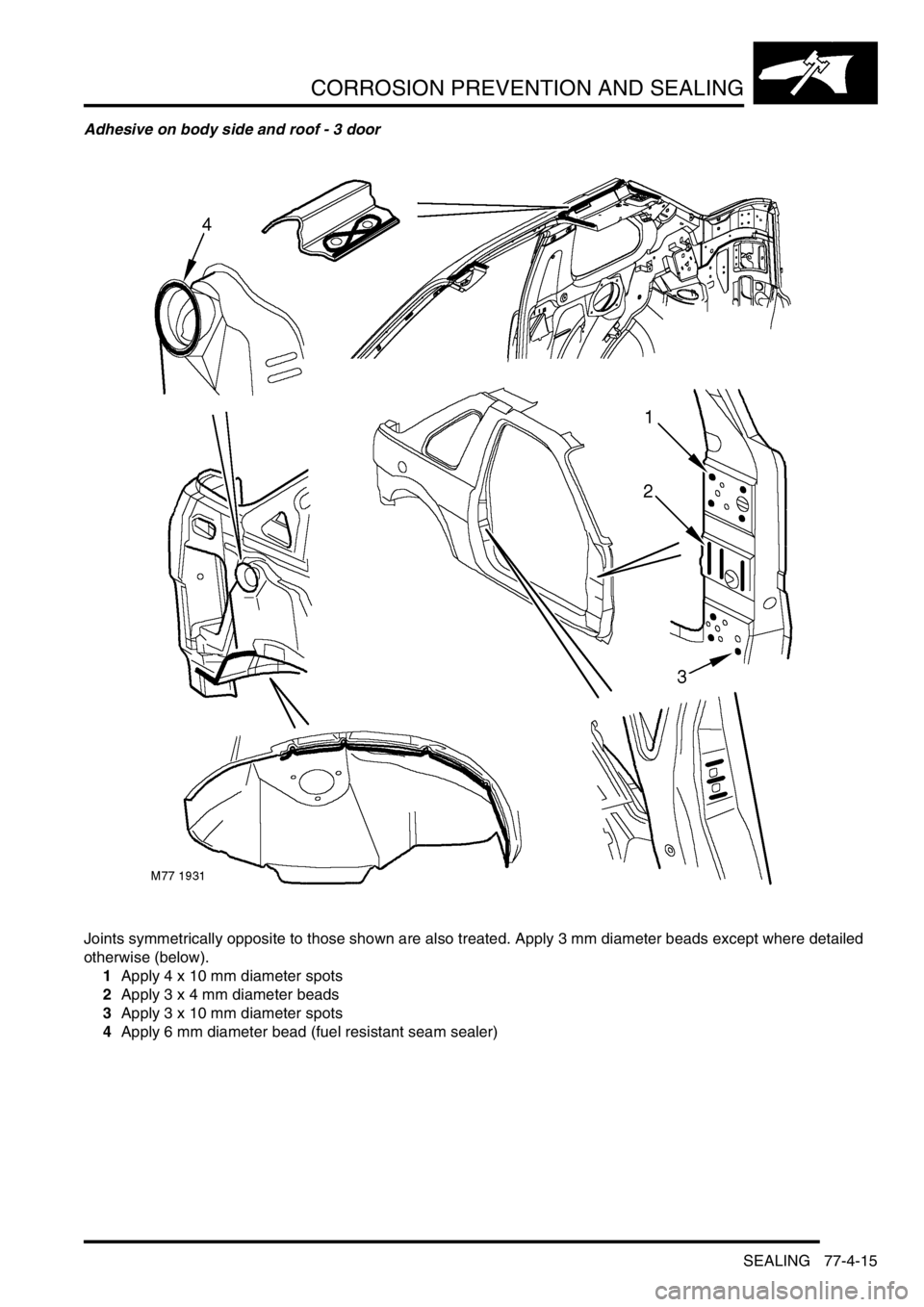
CORROSION PREVENTION AND SEALING
SEALING 77-4-15
Adhesive on body side and roof - 3 door
Joints symmetrically opposite to those shown are also treated. Apply 3 mm diameter beads except where detailed
otherwise (below).
1Apply 4 x 10 mm diameter spots
2Apply 3 x 4 mm diameter beads
3Apply 3 x 10 mm diameter spots
4Apply 6 mm diameter bead (fuel resistant seam sealer)
Page 847 of 1007
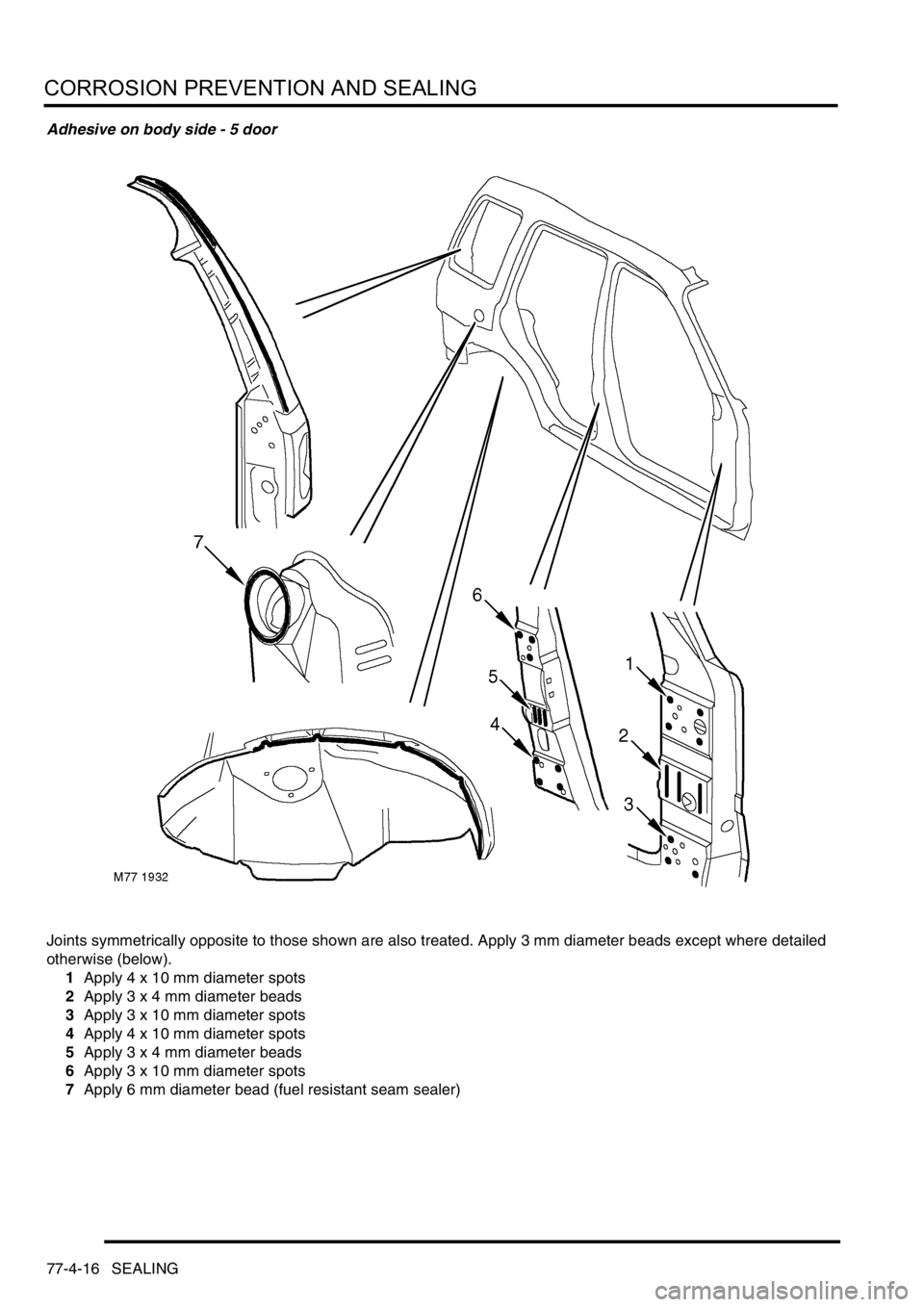
CORROSION PREVENTION AND SEALING
77-4-16 SEALING
Adhesive on body side - 5 door
Joints symmetrically opposite to those shown are also treated. Apply 3 mm diameter beads except where detailed
otherwise (below).
1Apply 4 x 10 mm diameter spots
2Apply 3 x 4 mm diameter beads
3Apply 3 x 10 mm diameter spots
4Apply 4 x 10 mm diameter spots
5Apply 3 x 4 mm diameter beads
6Apply 3 x 10 mm diameter spots
7Apply 6 mm diameter bead (fuel resistant seam sealer)
Page 848 of 1007
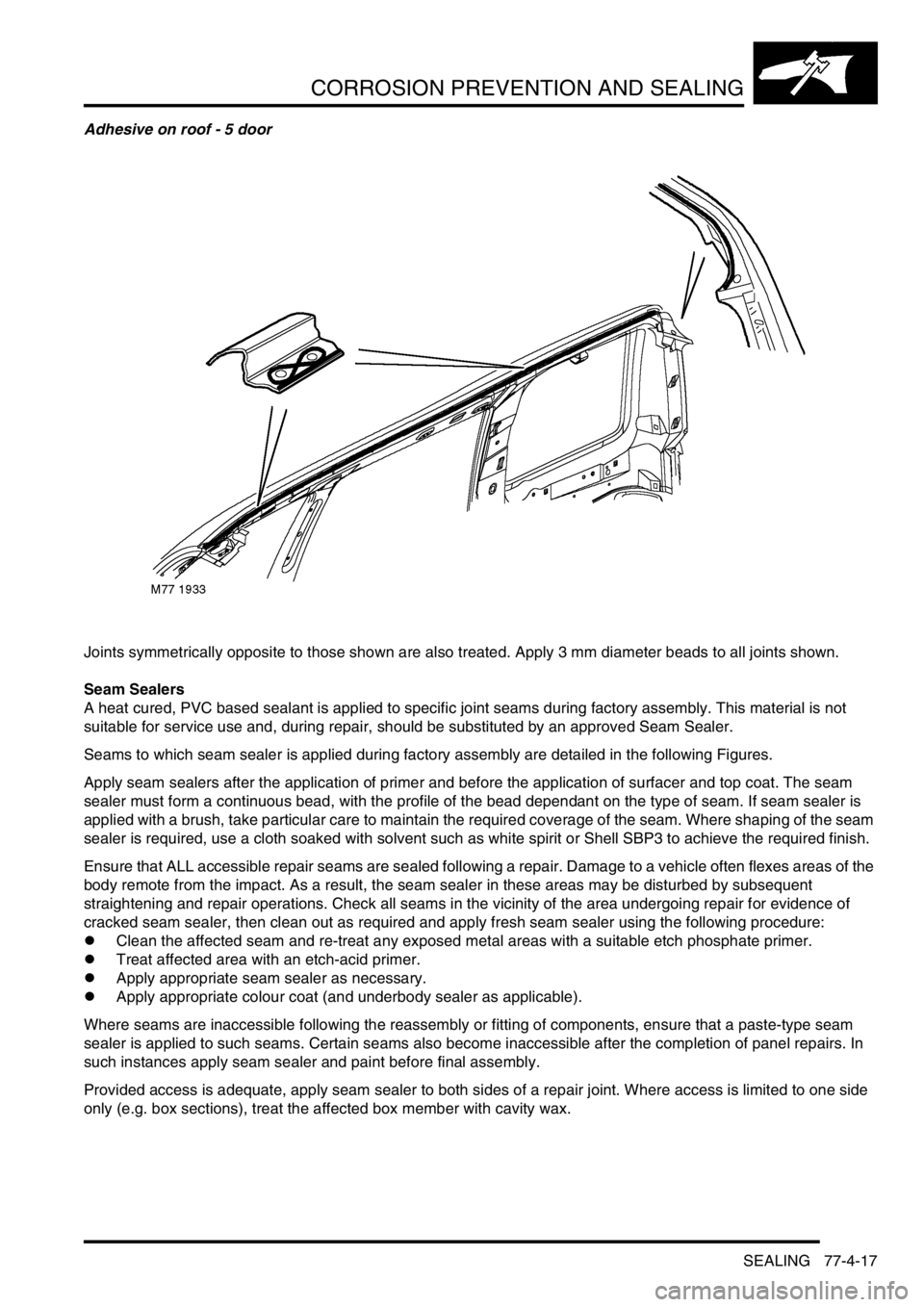
CORROSION PREVENTION AND SEALING
SEALING 77-4-17
Adhesive on roof - 5 door
Joints symmetrically opposite to those shown are also treated. Apply 3 mm diameter beads to all joints shown.
Seam Sealers
A heat cured, PVC based sealant is applied to specific joint seams during factory assembly. This material is not
suitable for service use and, during repair, should be substituted by an approved Seam Sealer.
Seams to which seam sealer is applied during factory assembly are detailed in the following Figures.
Apply seam sealers after the application of primer and before the application of surfacer and top coat. The seam
sealer must form a continuous bead, with the profile of the bead dependant on the type of seam. If seam sealer is
applied with a brush, take particular care to maintain the required coverage of the seam. Where shaping of the seam
sealer is required, use a cloth soaked with solvent such as white spirit or Shell SBP3 to achieve the required finish.
Ensure that ALL accessible repair seams are sealed following a repair. Damage to a vehicle often flexes areas of the
body remote from the impact. As a result, the seam sealer in these areas may be disturbed by subsequent
straightening and repair operations. Check all seams in the vicinity of the area undergoing repair for evidence of
cracked seam sealer, then clean out as required and apply fresh seam sealer using the following procedure:
lClean the affected seam and re-treat any exposed metal areas with a suitable etch phosphate primer.
lTreat affected area with an etch-acid primer.
lApply appropriate seam sealer as necessary.
lApply appropriate colour coat (and underbody sealer as applicable).
Where seams are inaccessible following the reassembly or fitting of components, ensure that a paste-type seam
sealer is applied to such seams. Certain seams also become inaccessible after the completion of panel repairs. In
such instances apply seam sealer and paint before final assembly.
Provided access is adequate, apply seam sealer to both sides of a repair joint. Where access is limited to one side
only (e.g. box sections), treat the affected box member with cavity wax.
Page 849 of 1007
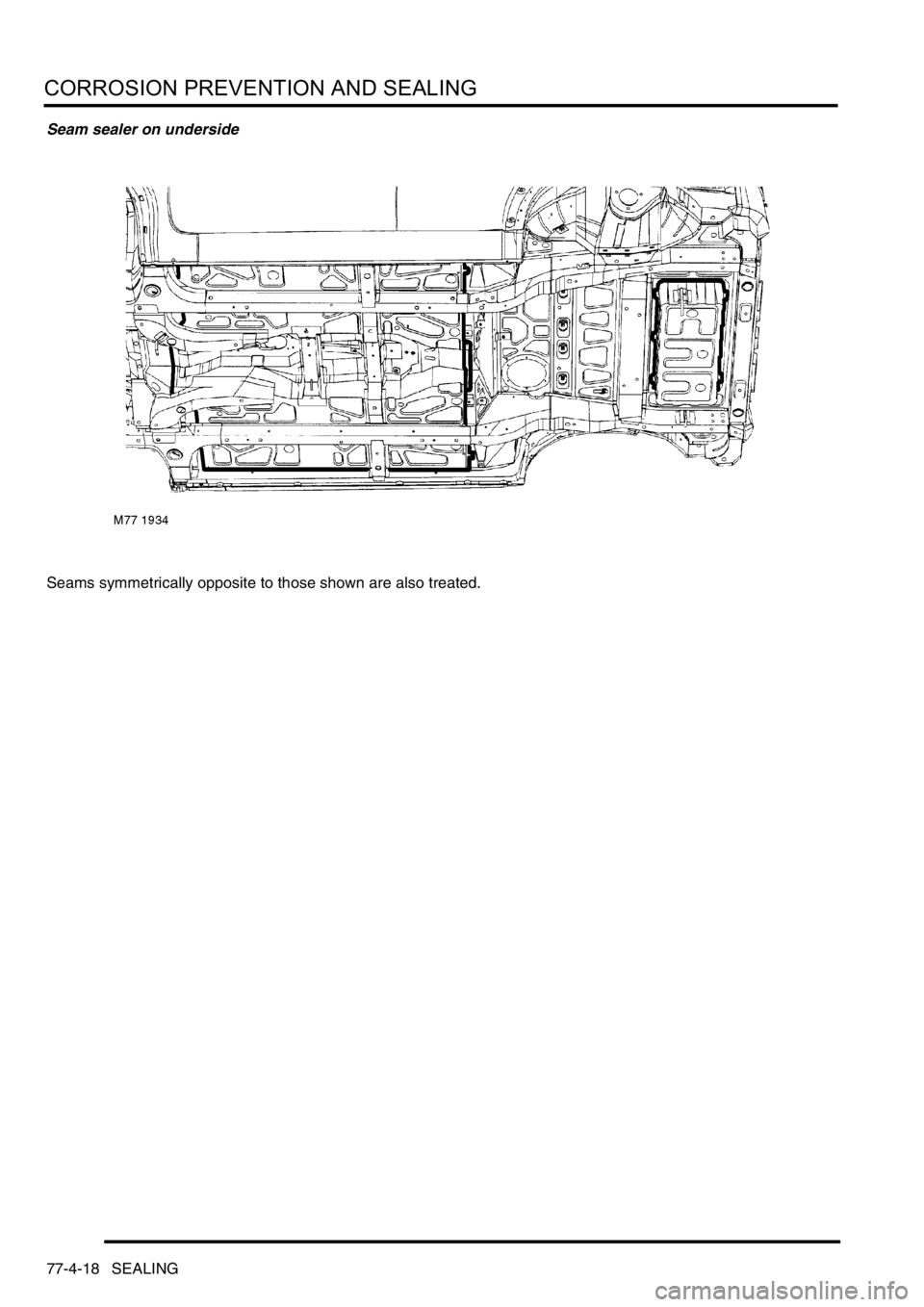
CORROSION PREVENTION AND SEALING
77-4-18 SEALING
Seam sealer on underside
Seams symmetrically opposite to those shown are also treated.
Page 850 of 1007
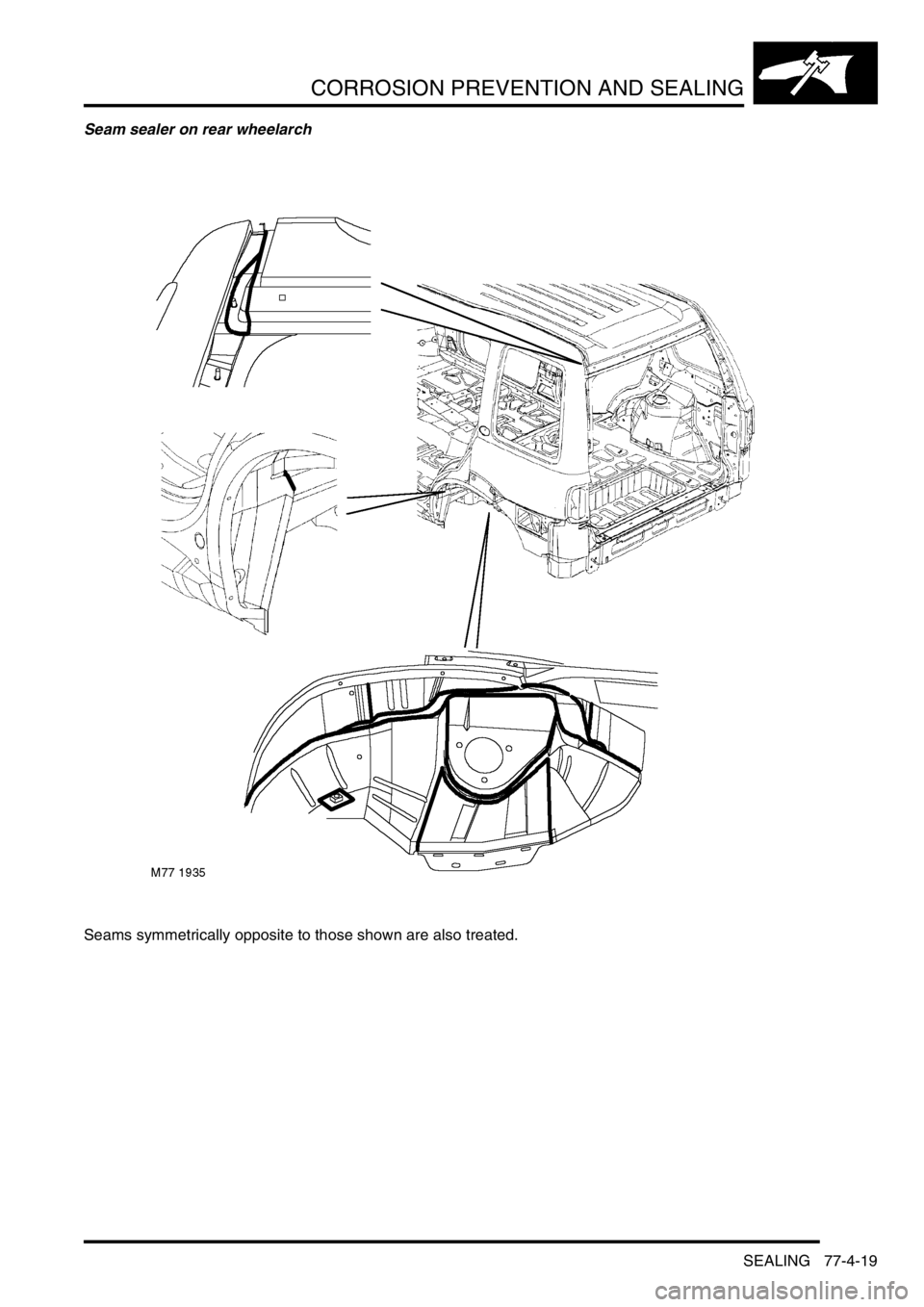
CORROSION PREVENTION AND SEALING
SEALING 77-4-19
Seam sealer on rear wheelarch
Seams symmetrically opposite to those shown are also treated.