MITSUBISHI DIAMANTE 1900 Repair Manual
Manufacturer: MITSUBISHI, Model Year: 1900, Model line: DIAMANTE, Model: MITSUBISHI DIAMANTE 1900Pages: 408, PDF Size: 71.03 MB
Page 201 of 408
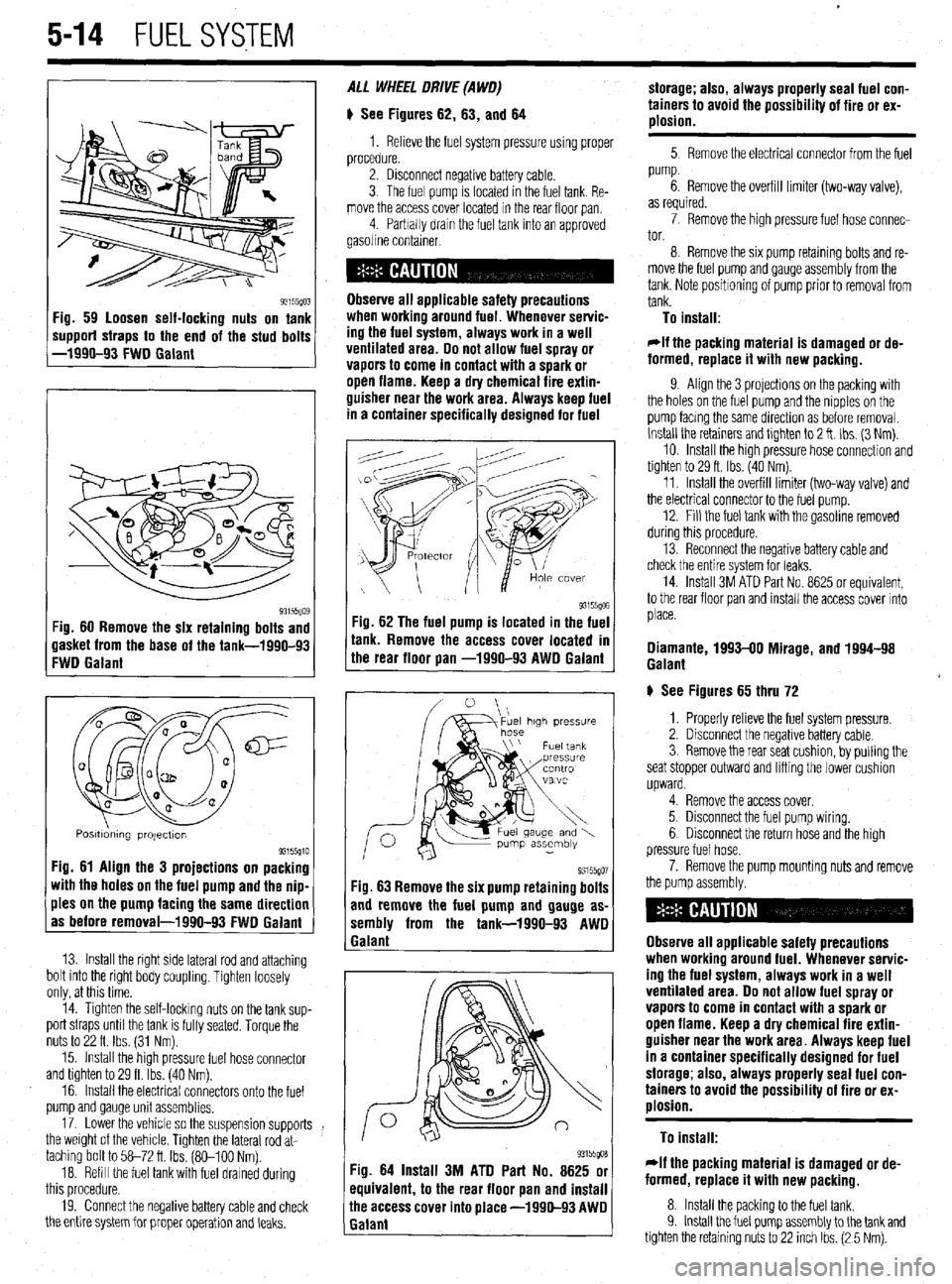
.
5-14 FUEL SYSTEM
93155(10: ‘ig. 59 loosen self-locking nuts on tank
mpporf straps to the end of the stud bolts
-1990-93 FWD Galant
93i55Qo$ :ig. 60 Remove the six retaining bolts and
lasket from the base of the tank-1990-93
:WD Galant
Q m
0 a
cl@=
u a-
a al2
0
0
Q
a a
Posmdmng projectton 93155910 Fig. 61 Align the 3 projections on packing
with the holes on the fuel pump and the nip-
ples on the pump facing the same direction
as before removal-1990-93 FWD Galant
13. Install the right side lateral rod and attaching
bolt into the right body coupling. Tighten loosely
only, at this time.
14. Tighten the self-locking nuts on the tank sup-
port straps until the tank is fully seated. Torque the
nuts to 22 ft. Ibs. (31 Nm).
15. Install the high pressure fuel hose connector
and tighten to 29 ft. Ibs. (40 Nm).
16. Install the electrical connectors onto the fuel
pump and gauge unit assemblies.
17. Lower the vehicle so the suspension supports
the weight of the vehicle. Tighten the lateral rod at-
taching bolt to 58-72 ft Ibs. (So-100 Nm).
18. Refill the fuel tank with fuel drained during
this procedure.
19. Connect the negative battery cable and check
the entire system for proper operation and leaks. ALL WHEEL DRIVE (A WO)
# See Figures 62, 63, and 64
1. Relieve the fuel system pressure using proper
procedure.
2. Disconnect negative battery cable.
3. The fuel pump is located in the fuel tank. Re-
move the access cover located in the rear floor pan
4 Parbally drain the fuel tank into an approved
gasoline container.
Observe all applicable safety precautions
when workina around fuel. Whenever servic-
ing the fuel system, always work in a well
ventilated area. Do not allow fuel spray or
vapors to come in contact with a spark or
open flame. Keep a dry chemical fire extin-
guisher near the work area. Always keep fuel
in a container specifically designed for fuel
-ig. 62 The fuel pump is located in the fuel
r
ank. Remove the access cover located m
he rear floor pan -1990-93 AWD Galant
93155go7 Fig. 63 Remove the six pump retaining bolts
and remove the fuel pump and gauge as-
sembly from the tank-1990-93 AWD
1 Galant
93155goa Fig. 64 Install 3M ATD Part No. 8625 or
equivalent, to the rear floor pan and install
ihe access cover into place -1990-93 AWD
Ealant storage; also, always properly seal fuel con-
tainers to avoid the possibility of fire or ex-
plosion.
5 Remove the electrical connector from the fuel
pump.
6. Remove the overfill limiter (two-way valve),
as required.
7. Remove the high pressure fuel hose connec-
tor.
8. Remove the six pump retaming bolts and re-
move the fuel pump and gauge assembly from the
tank. Note positioning of pump prior to removal from
tank.
To install:
*If the packing material is damaged or de-
formed, replace it with new packing.
9. Align the 3 projections on the packing with
the holes on the fuel pump and the nipples on the
pump facmg the same direction as before removal.
Install the retainers and tlghten to 2 ft. Ibs. (3 Nm).
10. Install the high pressure hose connection and
tighten to 29 ft. Ibs. (40 Nm).
11. Install the overfill limiter (two-way valve) and
the electrical connector to the fuel pump.
12. Fill the fuel tank with the gasoline removed
during this procedure.
13. Reconnect the negative battery cable and
check the entire system for leaks.
14. Install 3M ATD Part No. 8625 or equivalent,
to the rear floor pan and install the access cover into
place.
Diamante, 1993-00 Mirage, and 1994-98
Galant
# See Figures 65 thru 72
1. Properly relieve the fuel system pressure.
2. Disconnect the negative battery cable.
3. Remove the rear seat cushion, by pulling the
seat stopper outward and lifting the lower cushion
upward.
4. Remove the access cover.
5. Disconnect the fuel pump wiring.
6. Disconnect the return hose and the high
pressure fuel hose.
7. Remove the pump mounting nuts and remove
the pump assembly.
Observe all applicable safety precautions
when working around fuel. Whenever servic-
ing the fuel system, always work in a well
ventilated area. Do not allow fuel spray or
vapors to come in contact with a spark or
open flame. Keep a dry chemical fire extin-
guisher near the work area. Always keep fuel
in a container specifically designed for fuel
storage; also, always properly seal fuel con-
tainers to avoid the possibility of fire or ex-
plosion.
To install:
rlf the packing material is damaged or de-
formed, replace it with new packing.
8. Install the packing to the fuel tank.
9. Install the fuel pump assembly to the tank and
tighten the retaining nuts to 22 inch Ibs. (2 5 Nm).
Page 202 of 408
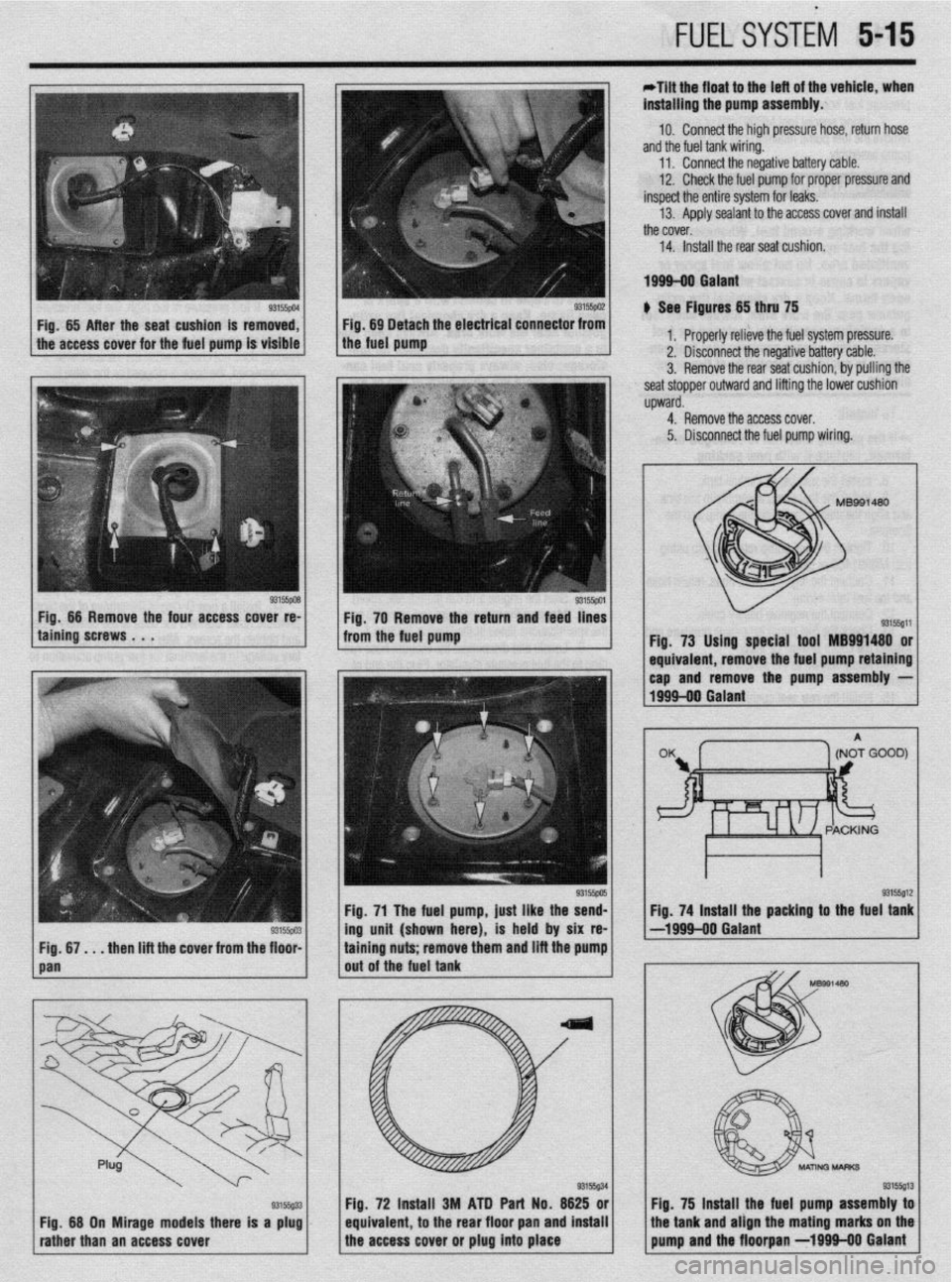
FUELSYSTEM 5-15
*Tilt the float to the left of the vehicle, when
installing the pump assembly..
10. Connect the high pressure hose, return hose
and the fuel tank wiring.
11. Connect the negative battery cable.
12. Check the fuel pump for proper pressure and
inspect the entire system for leaks.
13. Apply sealant to the access cover and install
the cover.
14. Install the rear seat cushion.
1999-M Galant
b See Figures 65 thru 75 ’
1. Properly relieve the fuel system pressure.
2. Disconnect the negative battery cable.
3. Remove the rear seat cushion, by pulling the
seat stopper outward and lifting the lower cushion
upward.
4. Remove the access cover.
Fig. 73 Using special tool MB991480 or
1 equivaler It, remove the fuel pump retaining
I I
Fig. 71 The fuel pump, just like the send- Fig. 74 Install the packing to the fuel tank
-- 93155~03 ing unit (shown here), is held by six re- -1999-00 Galant
. _. ._. .
-. m and lift the pump
. . . then lift the cover from tne floor- tammg nuts; remove tne
out of the fuel tank
J I A/ -p,486
I
Fig. 75 lnsta
, II the fuel pump assembly toi
equivalent 72 Ins$ll 3M ATD Part No. 6625 ori /’
to the rear floor pan and install the tank and align the mating marks on the
the access cover or plug into place pump and the floorpan -1999110 Galant Fig, 68 On Mirage models there is a plug
rather than an access cover
Page 203 of 408
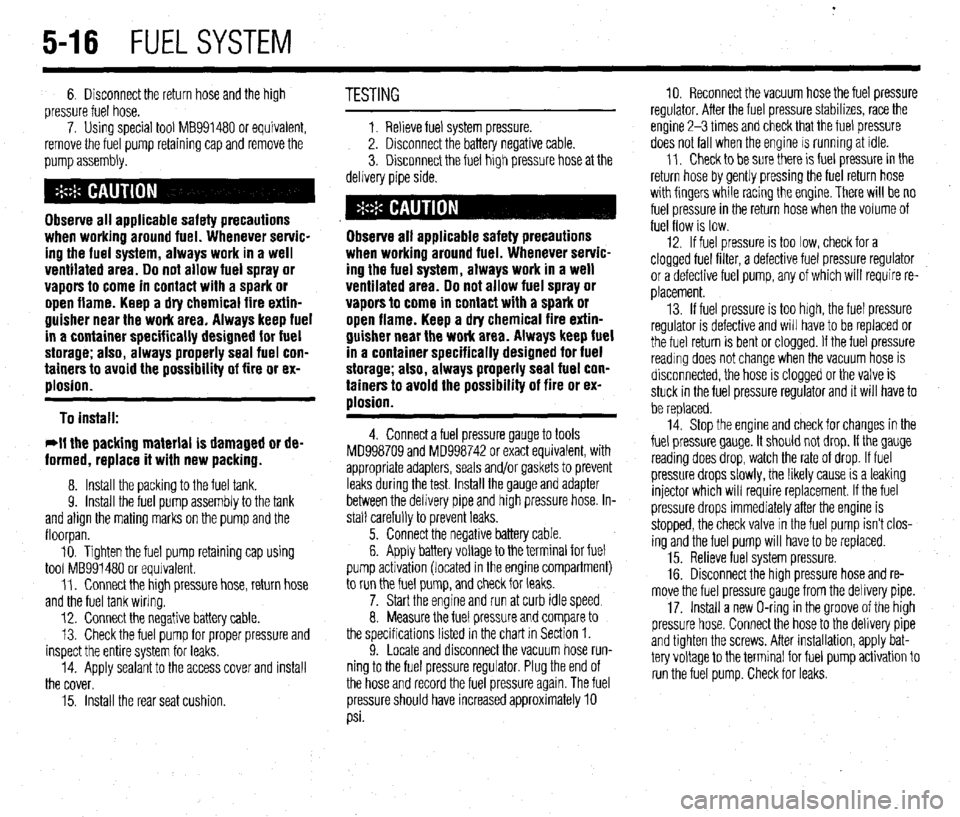
.
5-16 FUELSYSTEM
6. Disconnect the return hose and the high
pressure fuel hose.
7. Using special tool MB991480 or equivalent,
remove the fuel pump retaining cap and remove the
pump assembly.
Observe all applicable safety precautions
when working around fuel. Whenever servic-
ing the fuel system, always work in a well
ventilated area. Do not allow fuel spray or
vapors to come in contact with a spark or
open flame. Keep a dry chemical fire extin-
guisher near the work area. Always keep fuel
in a container specifically designed for fuel
storage; also, always properly seal fuel con-
tainers to avoid the possibility of fire or ex-
plosion.
To install:
*If the packing material is damaged or de-
formed, replace it with new packing.
8. Install the packing to the fuel tank.
9. Install the fuel pump assembly to the tank
and align the mating marks on the pump and the
floorpan.
10. Tighten the fuel pump retaining cap using
tool MB991480 or equrvalent.
11. Connect the high pressure hose, return hose
and the fuel tank wirmg.
12. Connect the negative battery cable.
13. Check the fuel pump for proper pressure and
inspect the entire system for leaks.
14. Apply sealant to the access cover and install
the cover.
15. Install the rear seat cushion.
TESTING
1. Relieve fuel system pressure.
2. Disconnect the battery negative cable.
3. Disconnect the fuel hrgh pressure hose at the
delivery pipe side.
Observe all applicable safety precautions
when working around fuel. Whenever servic-
ing the fuel system, always work in a well
ventilated area. Do not allow fuel spray or
vapors to come in contact with a spark or
open flame. Keep a dry chemical fire extin-
guisher near the work area. Always keep fuel
in a container specifically designed for fuel
storage; also, always properly seal fuel con-
tainers to avoid the possibility of fire or ex-
alosion.
4. Connect a fuel pressure gauge to tools
MD998709 and MD998742 or exact equivalent, with
appropriate adapters, seals and/or gaskets to prevent
leaks during the test. Install the gauge and adapter
between the delivery pipe and high pressure hose. In-
stall carefully to prevent leaks.
5. Connect the negative battery cable.
6. Apply battery voltage to the terminal for fuel
pump activation (located in the engine compartment)
to run the fuel pump, and check for leaks.
7. Start the engine and run at curb idle speed.
8. Measure the fuel pressure and compare to
the specifications listed in the chart in Section 1.
9. Locate and disconnect the vacuum hose run-
ning to the fuel pressure regulator. Plug the end of
the hose and record the fuel pressure again. The fuel
pressure should have increased approximately IO
psi. 10. Reconnect the vacuum hose the fuel pressure
regulator. After the fuel pressure stabilizes, race the
engine 2-3 times and check that the fuel pressure
does not fall when the engine is running at idle.
il. Check to be sure there is fuel pressure in the
return hose by gently pressing the fuel return hose
with fingers while racing the engine. There will be no
fuel pressure in the return hose when the volume of
fuel flow is low.
12. If fuel pressure is too low, check for a
clogged fuel filter, a defective fuel pressure regulator
or a defective fuel pump, any of which will require re-
placement.
13. If fuel pressure is too high, the fuel pressure
regulator is defective and will have to be replaced or
the fuel return is bent or clogged. If the fuel pressure
readmg does not change when the vacuum hose is
disconnected, the hose is clogged or the valve is
stuck in the fuel pressure regulator and it will have to
be replaced.
14. Stop the engine and check for changes in the
fuel pressure gauge. It should not drop. If the gauge
reading does drop, watch the rate of drop. If fuel
pressure drops slowly, the likely cause is a leaking
injector which will require replacement. If the fuel
pressure drops immediately after the engine is
stopped, the check valve in the fuel pump isn’t clos-
ing and the fuel pump will have to be replaced.
15. Relieve fuel system pressure.
16. Disconnect the high pressure hose and re-
move the fuel pressure gauge from the delivery pipe.
17. Install a new O-ring in the groove of the high
pressure hose. Connect the hose to the delivery pipe
and tighten the screws. After Installation, apply bat-
tery voltage to the terminal for fuel pump activation to
run the fuel pump. Check for leaks.
Page 204 of 408
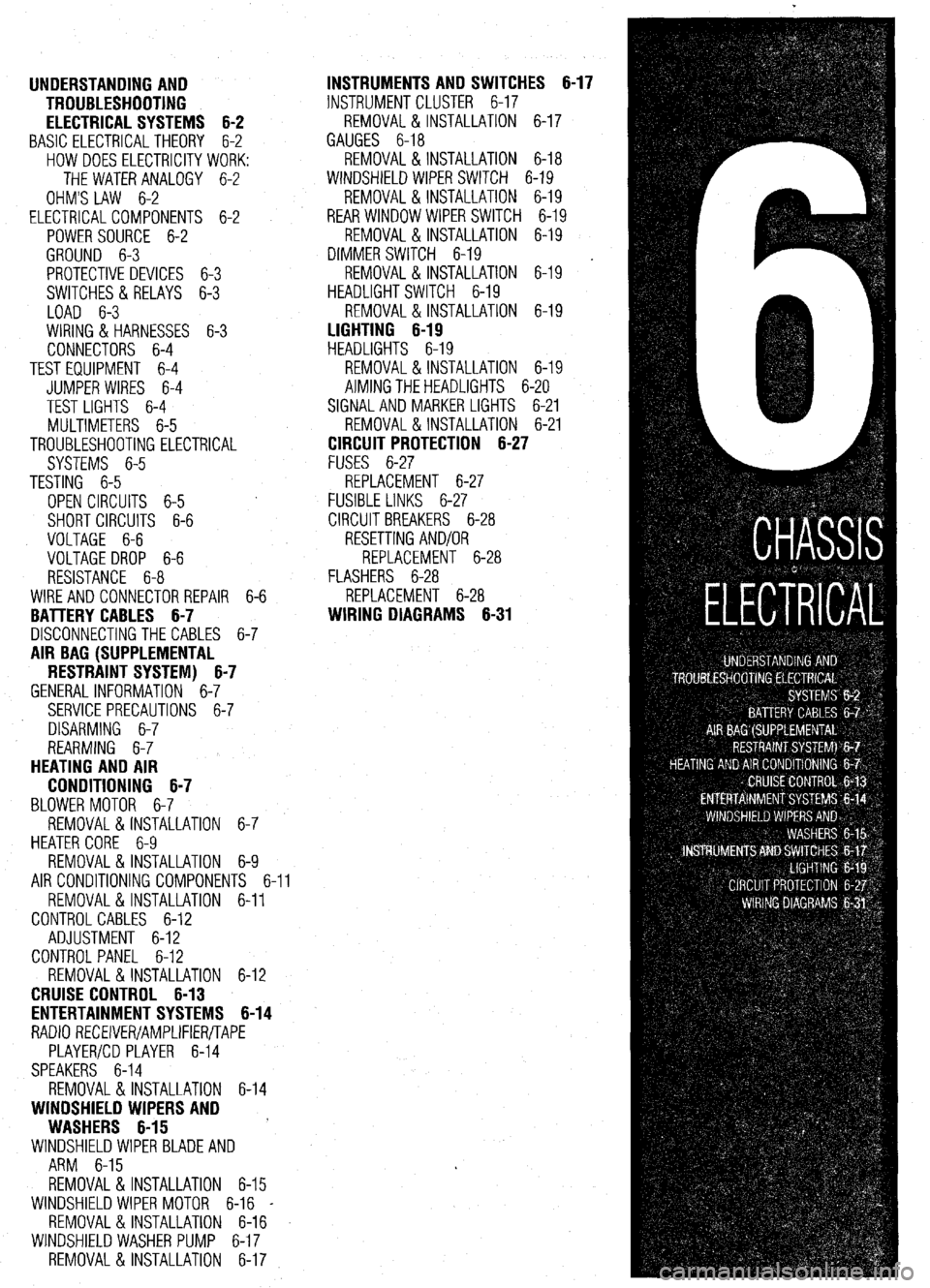
UNDERSTANDING AND
TROUBLESHOOTING
ELECTRICAL SYSTEMS 6-2
BASIC ELECTRICALTHEORY 6-2
HOW DOES ELECTRICITY WORK:
THEWATERANALOGY 6-2
OHM'S LAW 6-2
ELECTRICALCOMPONENTS 6-2
POWERSOURCE 6-2
GROUND 6-3
PROTECTIVE DEVICES 6-3
SWITCHES&RELAYS 6-3
LOAD 6-3
WIRING & HARNESSES 6-3
CONNECTORS 6-4
TEST EQUIPMENT 6-4
JUMPER WIRES 6-4
TEST LIGHTS 6-4
MULTIMETERS 6-5
TROUBLESHOOTING ELECTRICAL
SYSTEMS 6-5
TESTING 6-5
OPEN CIRCUITS 6-5
SHORT CIRCUITS 6-6
VOLTAGE 6-6
VOLTAGE DROP 6-6
RESISTANCE 6-8
WIRE AND CONNECTORREPAIR 6-6
BATTERY CABLES 6-7
DISCONNECTING THE CABLES 6-7
AIR BAG (SUPPLEMENTAL
RESTRAINT SYSTEM) 6-7
GENERALINFORMATION 6-7
SERVICE PRECAUTIONS 6-7
DISARMING 6-7
REARMING 6-7
HEATING AND AIR
CONDITIONING 6-7
BLOWER MOTOR 6-7
REMOVAL &INSTALLATION 6-7
HEATER CORE 6-9 INSTRUMENTS AND SWITCHES 6-17
INSTRUMENTCLUSTER 6-17
REMOVAL &INSTALLATION 6-17
GAUGES 6-18
REMOVAL&INSTALLATION 6-18
WINDSHIELD WIPER SWITCH 6-19
REMOVAL&INSTALLATION 6-19
REARWINDOWWIPERSWITCH 6-19
REMOVAL &INSTALLATION 6-19
DIMMER SWITCH 6-19
REMOVAL & INSTALLATION 6-19 .
HEADLIGHT SWITCH 6-19
REMOVAL & INSTALLATION 6-19
LIGHTING 6-19
HEADLIGHTS 6-19
REMOVAL &INSTALLATION 6-19
AIMINGTHEHEADLIGHTS 6-20
SIGNAL AND MARKER LIGHTS 6-21
REMOVAL &INSTALLATION 6-21
CIRCUIT PROTECTION 6-27
FUSES 6-27
REPLACEMENT 6-27
FUSIBLE LINKS 6-27
CIRCUIT BREAKERS 6-28
RESETTING AND/OR
REPLACEMENT 6-28
FLASHERS 6-28
REPLACEMENT 6-28
WIRING DIAGRAMS 6-31
REMOVAL & INSTALLATION 6-9
AIR CONDITIONING COMPONENTS 6-11
REMOVAL & INSTALLATION 6-11
CONTROLCABLES 6-12
ADJUSTMENT 6-12
CONTROL PANEL 6-12
REMOVAL & INSTALLATION 6-12
CRUISE CONTROL 6-13
ENTERTAINMENT SYSTEMS 6-14
RADIO RECEIVER/AMPLIFIER/TAPE
PLAYER/CD PLAYER 6-14
SPEAKERS 6-14
REMOVAL & INSTALLATION 6-14
WINDSHIELD WIPERS AND
WASHERS 6-15
WINDSHIELD WIPER BLADE AND
ARM 6-15
REMOVAL & INSTALLATION 6-15
WINDSHIELD WIPER MOTOR 6-16 _
REMOVAL &INSTALLATION 6-16
WINDSHIELD WASHER PUMP 6-17
REMOVAL &INSTALLATION 6-17
Page 205 of 408
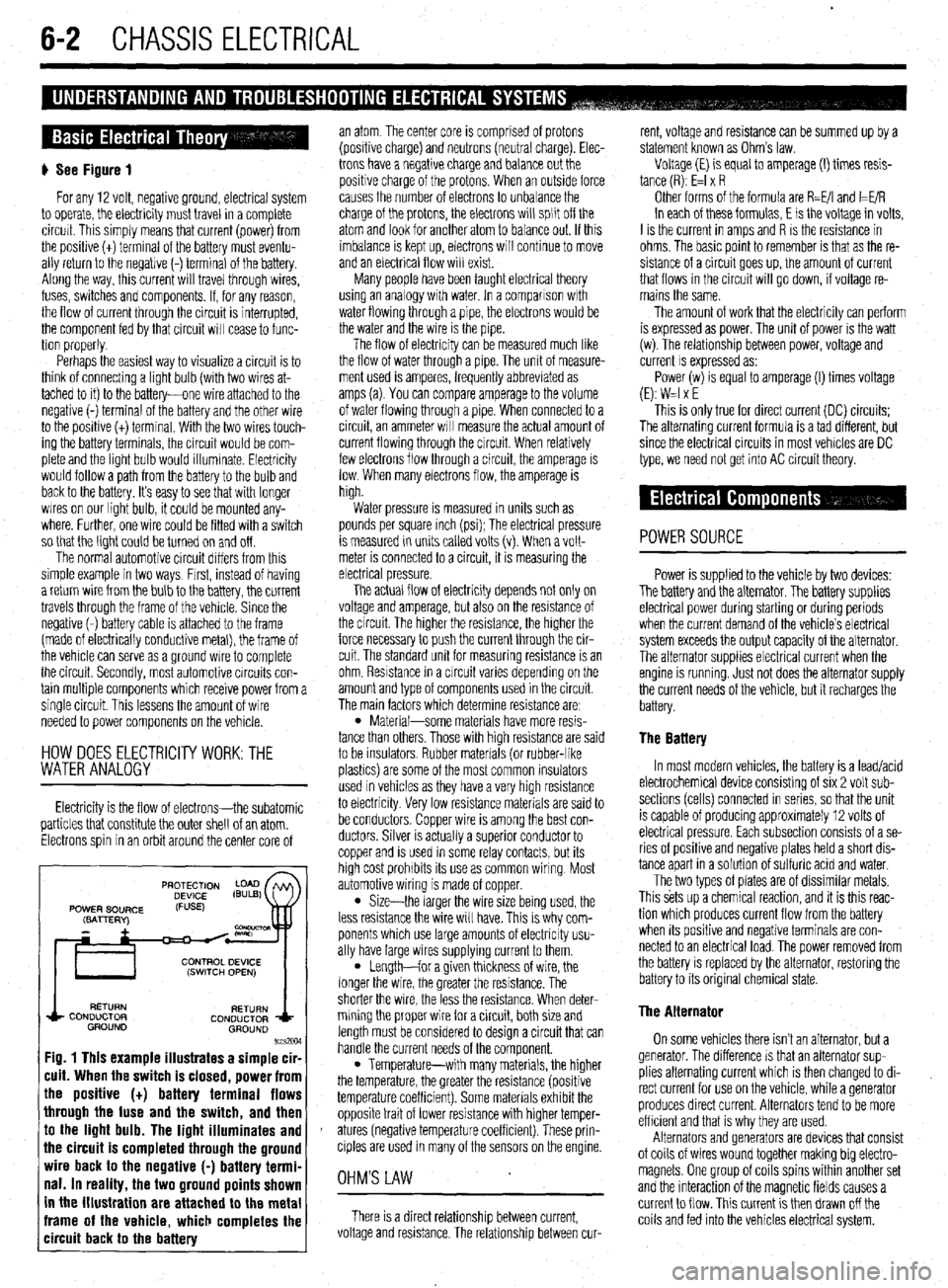
6-2 CHASSIS ELECTRICAL
) See Figure 1
For any 12 volt, negative ground, electrical system
to operate, the electricity must travel in a complete
circurt. This simply means that current (power) from
the posibve (t) terminal of the battery must eventu-
ally return to the negative (-) terminal of the battery.
Along the way, this current will travel through wires,
fuses, switches and components. If, for any reason,
the flow of current through the circuit is interrupted,
the component fed by that circuit will cease to func-
tion properly.
Perhaps the easiest way to visualize a circuit is to
think of connecting a light bulb (with two wires at-
tached to it) to the battery-one wire attached to the
negative (-) terminal of the battery and the other wire
to the positive (t) terminal. With the two wires touch-
ing the battery terminals, the circuit would be com-
plete and the light bulb would illummate. Electricity
would follow a path from the battery to the bulb and
back to the battery. It’s easy to see that wrth longer
wires on our light bulb, it could be mounted any-
where. Further, one wire could be fitted with a switch
so that the light could be turned on and off.
The normal automotive circuit differs from this
simple example in two ways, Frrst, instead of having
a return wire from the bulb to the battery, the current
travels through the frame of the vehicle. Since the
negative (-) battery cable is attached to the frame
(made of electrically conductive metal), the frame of
the vehicle can serve as a ground wire to complete
the circuit. Secondly, most automotive circuits con-
tain multiple components which receive power from a
single circuit. This lessens the amount of wire
needed to power components on the vehicle.
HOW DOES ELECTRlClTYWORK:THE
WATER ANALOGY
Electricity is the flow of electrons-the subatomic
particles that constitute the outer shell of an atom.
Electrons spin in an orbit around the center core of
RETURN
RETURN
CONDUCTOR
CONDUCTOR
GROUND
GROUND
lccs2w
Fig. 1 This example illustrates a simple cir-
cuit. When the switch is closed, power from
the positive (t) battery terminal flows
through the fuse and the switch, and then
to the light bulb. The light illuminates and
the circuit is completed through the ground
wire back to the negative (-) battery termi-
nal. In reality, the two ground points shown
in the illustration are attached to the metal
frame of the vehicle, which completes the
circuit back to the battery
an atom The center core is comprised of protons
(positive charge) and neutrons (neutral charge). Elec-
trons have a negative charge and balance
out the
positive charge of the protons. When an outside force
causes the number of electrons to unbalance the
charge of the protons, the electrons will split off the
atom and look for another atom to balance out. If this
imbalance is kept up, electrons will continue to move
and an electrical flow will exist.
Many people have been taught electrical theory
using an analogy with water. In a comparison wrth
water flowing through a pipe, the electrons would be
the water and the wire is the pipe.
The flow of electricity can be measured much like
the flow of water through a pipe. The unit of measure-
ment used is amperes, frequently abbreviated as
amps (a). You can compare amperage to the volume
of water flowing through a pipe. When connected to a
circuit, an ammeter WIII measure the actual amount of
current flowing through the circuit. When relatively
few electrons flow through a circuit, the amperage is
low. When many electrons flow, the amperage is
high.
Water pressure is measured in units such as
pounds per square inch (psi); The electrical pressure
is measured in unrts called volts (v). When a volt-
meter is connected to a circuit, it is measuring the
electrical pressure.
The actual flow of electricity depends not only on
voltage and amperage, but also on the resistance of
the circuit The higher the resistance, the higher the
force necessary to push the current through the cir-
cuit. The standard unit for measuring resistance is an
ohm. Resistance in a crrcuit varies dependmg on the
amount and type of components used in the circuit.
The main factors which determine resistance are:
l Material-some materials have more resis-
tance than others Those with high resistance are said
to be insulators Rubber materials (or rubber-like
plashcs) are some of the most common insulators
used in vehicles as they have a very high resistance
to electricity Very low resistance materials are said to
be conductors. Copper wire is among the best con-
ductors. Silver is actually a superior conductor to
copper and is used in some relay contacts, but its
high cost prohibits its use as common wiring Most
automotive wiring is made of copper.
l Size-the larger the wire size being used, the
less resistance the wire will have. This IS why com-
ponents which use large amounts of electricity usu-
ally have large wires supplying current to them.
l Length-for a given thickness of wire, the
longer the wire, the greater the resistance. The
shorter the wire, the less the resistance. When deter-
mining the proper wire for a circuit, both size and
length must be considered to design a circuit that can
handle the current needs of the component.
l Temperature-with many materials, the higher
the temperature, the greater the resistance (positive
temperature coefficient). Some materials exhibit the
opposite trait of lower resistance with higher temper-
atures (negative temperature coefficient). These prin-
ciples are used in many of the sensors on the engine
OHM'S LAW
There is a direct relationship between current,
voltage and resistance. The relationship between cur- rent, voltage and resistance can be summed up by a
statement known as Ohm’s law.
Voltage (E) is equal to amperage (I) times resis-
tance (R): E=l x R
Other forms of the formula are R=E/I and I=E/R
In each of these formulas, E is the voltage in volts,
I is the current in amps and R IS the resistance in
ohms. The basic point to remember is that as the re-
sistance of a circuit goes up, the amount of current
that flows in the circuit will go down, if voltage re-
mains the same.
The amount of work that the electricity can perform
is expressed as power. The unit of power is the watt
(w). The relationship between power, voltage and
current
IS expressed as:
Power(w) is equal to amperage (I) times voltage
(E): W=l x E
This is only true for direct current (DC) circuits:
The alternating current formula is a tad different, but
since the electrical circuits in most vehicles are DC
type, we need not get into AC circuit theory.
POWERSOURCE
Power is supplied to the vehicle by two devices:
The battery and the alternator. The battery supplies
electrical power during starting or during periods
when the current demand of the vehicle’s electrical
system exceeds the output capacity of the alternator.
The alternator supplies electrical current when the
engine is running
Just not does the alternator supply
the current needs of the vehicle, but it recharges the
battery.
The Battery
In most modern vehicles, the battery is a lead/acid
electrochemical device consisting of six 2 volt sub-
sections (cells) connected in series, so that the unit
is capable of producing approximately 12 volts of
electrical pressure. Each subsection consists of a se-
ries of positive and negative plates held a short dis-
tance apart in a solutron of sulfuric acid and water.
The two types of plates are of dissimilar metals,
This sets up a chemrcal reaction, and it is this reac-
tion which produces current flow from the battery
when Its positive and negattve terminals are con-
nected to an electrical load. The power removed from
the battery is replaced by the alternator, restoring the
battery to its original chemical state.
The Alternator
On some vehicles there isn’t an alternator, but a
generator. The difference IS that an alternator sup-
plies alternating current which is then changed to di-
rect current for
use on the vehicle, while a generator
produces direct current. Alternators tend to be more
efficient and that is why they are used.
Alternators and generators are devices that consist
of coils of wires wound together making big electro-
magnets. One group of coils spins within another set
and the interaction of the magnetic fields causes a
current to flow. This current is then drawn off the
coils and fed into the vehicles electrical system.
Page 206 of 408
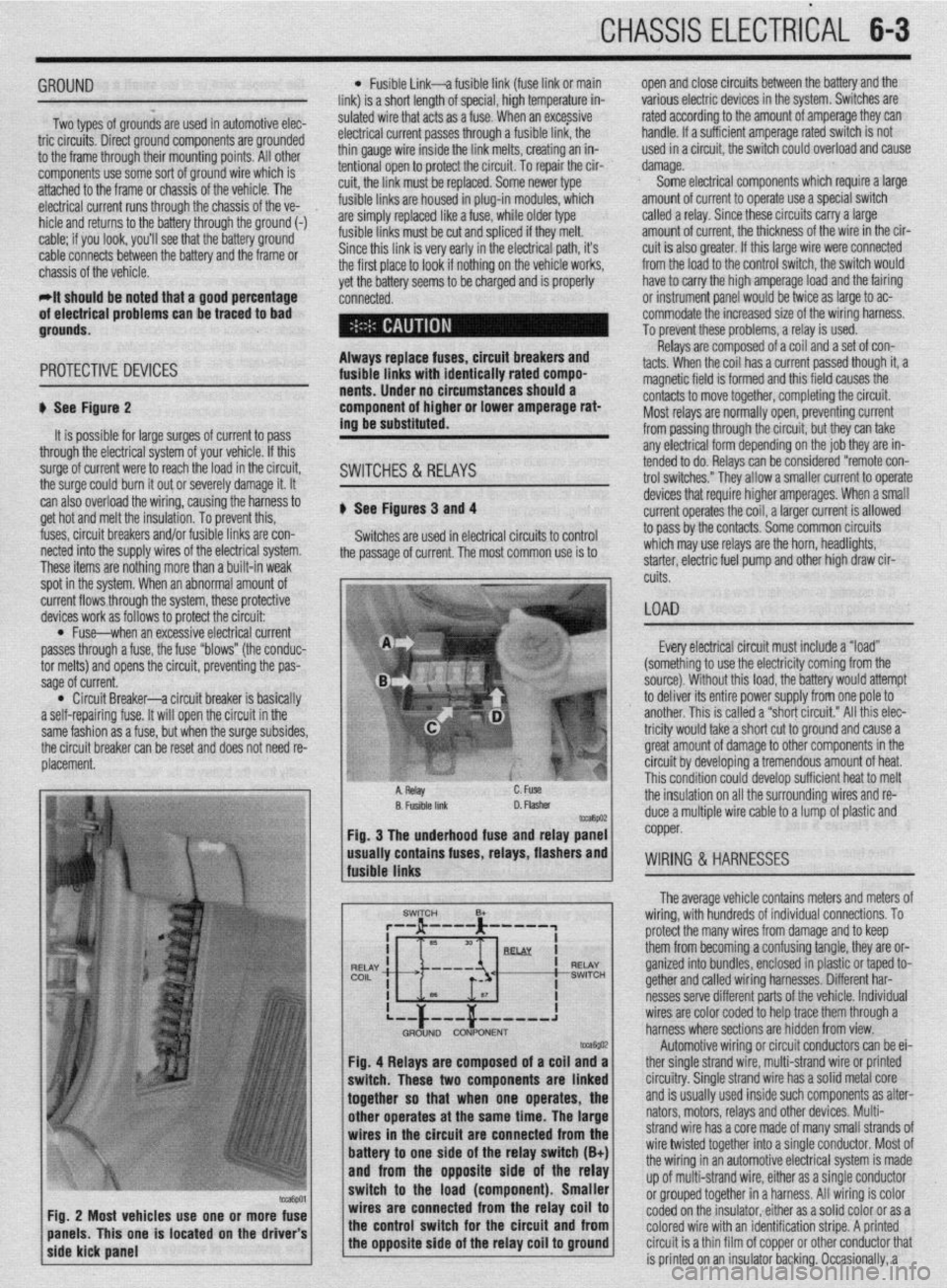
CHASSIS ELECTRliAL 6-3
SWITCH
&--; r-- ----
-~~ 85 M
I
-M-L RELAY
SWITCH 86 87
i
---
----w-J
tcca6go2 Fig. 4 Relays are composed of a coil and a
switch. These two components are linked
together so that when one operates, the
other operates at the same time. The large
wires in the circuit are connected from the
battery to one side of the relay switch (B+)
and from the opposite side of the relay
switch to the load (component). Smaller
wires are connected from the relay coil to
the control switch for the circuit and from
the opposite side of the relay coil to ground
The average vehicle contains meters and meters of
wiring, with hundreds of individual connections. To
protect the many wires from damage and to keep
them from becoming a confusing tangle, they are or-
ganized into bundles, enclosed in plastic or taped to-
gether and called wiring harnesses. Different har-
nesses serve different parts of the vehicle. Individual
wires are color coded to help trace them through a
harness where sections are hidden from view.
Automotive wiring or circuit conductors can be ei-
ther single strand wire, multi-strand wire or printed
circuitry. Single strand wire has a solid metal core
and is usually used inside such components as alter-
nators, motors, relays and other devices. Multi-
strand wire has a core made of many small strands of
wire twisted together into a single conductor. Most of
the wiring in an automotive electrical system is made
up of multi-strand wire, either as a single conductor
or grouped together in a harness. All wiring is color
coded on the insulator,,either as a solid color or as a
colored wire with an identification stripe. A printed
circuit is a thin film of copper or other conductor that
is printed on an insulator backing. Occasionally, a
Page 207 of 408
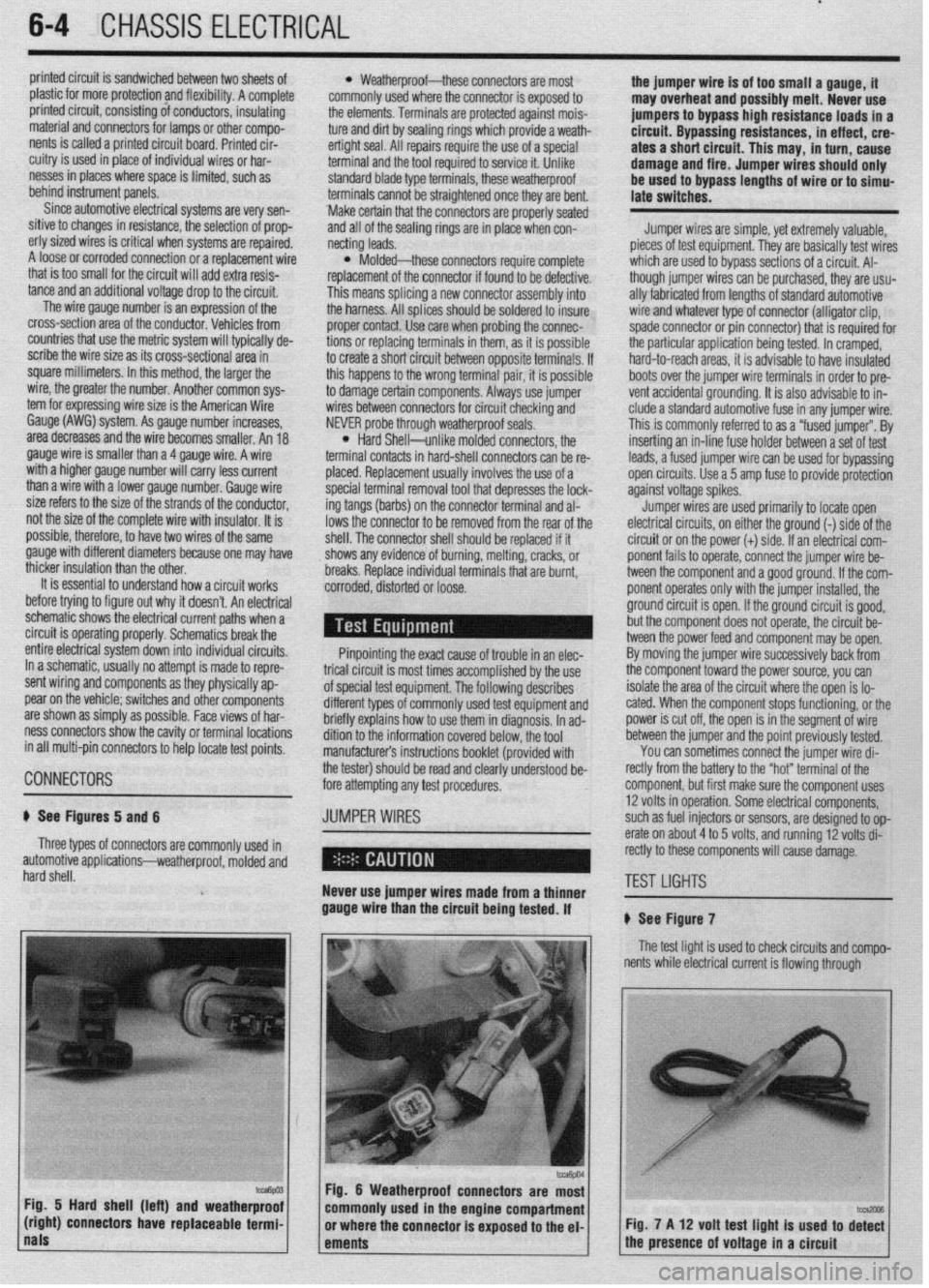
I
6-4 CHASSIS ELECTRICAL
I
printed circuit is sandwiched between two sheets of
plastic for more protection and flexibility. A complete l Weatherproof-these connectors are most the jumper wire is of too small a gauge, it
printed circuit, consisting of conductors, insulating commonly used where the connector is exposed to
may overheat and possibly melt. Never use
material and connectors for lamps or other compo- the elements. Terminals are protected against mois-
nents is called a printed circuit board. Printed cir- ture and dirt by sealing rings which provide a weath- jumpers to bypass high resistance loads in a
et-tight seal. All repairs require the use of a special circuit. Bypassing resistances, in effect, cre-
cuitry is used in place of individual wires or har- ates a short circuit. This may, in turn, cause
nesses in places where space is limited, such as terminal and the tool required to service it. Unlike
behind instrument panels. standard blade type terminals, these weatherproof damage and fire. Jumper wires should only
be used to bypass lengths of wire or to simu-
Since automotive electrical systems are very sen- terminals cannot be straightened once they are bent. late switches.
sitive to changes in resistance, the selection of prop- ‘Make certain that the connectors are properly seated
erly sized wires is critical when systems are repaired, and all of the sealing rings are in place when con-
netting leads. Jumper wires are simple, yet extremely valuable,
A loose or corroded connection or a replacement wire pieces of test equipment. They are basically test wires
that is too small for the circuit will add extra resis-
l Molded-these connectors require complete which are used to bypass sections of a circuit. Al-
replacement of the connector if found to be defective.
tance and an additional voltage drop to the circuit. though jumper wires can be purchased, they are usu-
The wire gauge number is an expression of the This means splicing a new connector assembly into ally fabricated from lengths of standard automotive
cross-section area of the conductor. Vehicles from the harness. All splices should be soldered to insure
proper contact. Use care when probing the connec- wire and whatever type of connector (alligator clip,
countries that use the metric system will typically de- spade connector or pin connector) that is required for
scribe the wire size as its cross-sectional area in tions or replacing terminals in them, as it is possible
square millimeters. In this method, the larger the to create a short circuit between opposite terminals. If the particular application being tested. In cramped,
hard-to-reach areas, it is advisable to have insulated
wire, the greater the number. Another common sys- this happens to the wrong terminal pair, it is possible
to damage certain components. Always use jumper boots over the jumper wire terminals in order to pre-
tern for expressing wire size is the American Wire vent accidental grounding. It is also advisable to in-
Gauge (AWG) system. As gauge number increases, wires between connectors for circuit checking and
NEVER probe through weatherproof seals. elude a standard automotive fuse in any jumper wire.
area decreases and the wire becomes smaller. An 18
gauge wire is smaller than a 4 gauge wire. A wire
l Hard Shell-unlike molded connectors, the This is commonly referred to as a “fused jumper”. By
inserting an in-line fuse holder between a set of test
terminal contacts in hard-shell connectors can be re-
with a higher gauge number will carry less current
placed. Replacement usually involves the use of a leads, a fused jumper wire can be used for bypassing :
than a wire with a lower gauge number. Gauge wire open circuits. Use a 5 amp fuse to provide protection
size refers to the size of the strands of the conductor, special terminal removal tool that depresses the lock- against voltage spikes.
not the size of the complete wire with insulator. It is ing tangs (barbs) on the connector terminal and al-
lows the connector to be removed from the rear of the Jumper wires are used primarily to locate open
possible, therefore, to have two wires of the same
shell. The connector shell should be replaced if it electrical circuits, on either the ground (-) side of the
gauge with different diameters because one may have
thicker insulation than the other. shows any evidence of burning, melting, cracks, or circuit or on the power (+) side. If an electrical corn-
breaks. Replace individual terminals that are burnt, ponent fails to operate, connect the jumper wire be-
It is essential to understand how a circuit works
corroded, distorted or loose. tween the component and a good ground. If the corn-
before trying to figure out why it doesn’t. An electrical ponent operates only with the jumper installed, the
schematic shows the electrical current paths when a ground circuit is open. If the ground circuit is good,
circuit is operating properly. Schematics break the but the component does not operate, the circuit be-
entire electrical system down into individual circuits. tween the power feed and component may be open. ’
In a schematic, usually no attempt is made to repre- Pinpointing the exact cause of trouble in an elec- By moving the jumper wire successively back from
trical circuit is most times accomplished by the use the component toward the power source, you can
; : sent wiring and components as they physically ap-
pear on the vehicle; switches and other components of special test equipment. The following describes isolate the area of the circuit where the open is lo-
are shown as simply as possible. Face views of har- different types of commonly used test equipment and cated. When the component stops functioning, or the f
j
ness connectors show the cavity or terminal locations briefly explains how to use them in diagnosis. In ad- power is cut off, the open is in the segment of wire j
in all multi-pin connectors to help locate test points. dition to the information covered below, the tool between the jumper and the point previously tested.
! manufacturer’s instructions booklet (provided with You can sometimes connect the jumper wire di-
the tester) should be read and clearly under.$ood be- rectly from the battery to the “hot” terminal of the I
CONNECTORS 1 fore attempting any test procedures. component, but first make sure the component uses 1
# See Figures 5 and 6 JUMPER WIRES 12 volts in operation. Some electrical components, i
such as fuel injectors or sensors, are designed to op-
Three types of connectors are commonly used in erate on about 4 to 5 volts, and running 12 volts di- j
)
automotive applications-weatherproof, molded and rectly to these components will cause damage.
hard shell.
Never use jumper wires made from a thinner TEST LIGHTS I
gauge wire than the circuit being tested. If
# See Figure 7
The test light is used to check circuits and compo-
I nents while electrical current is flowing through
Fig. 5 Hard shell (left) and weatherproof
(right) connectors have replaceable termi- Fig. 7 A 12 volt test light is used to di%
nals
ements 1 the presence of voltage in a circuit
Page 208 of 408
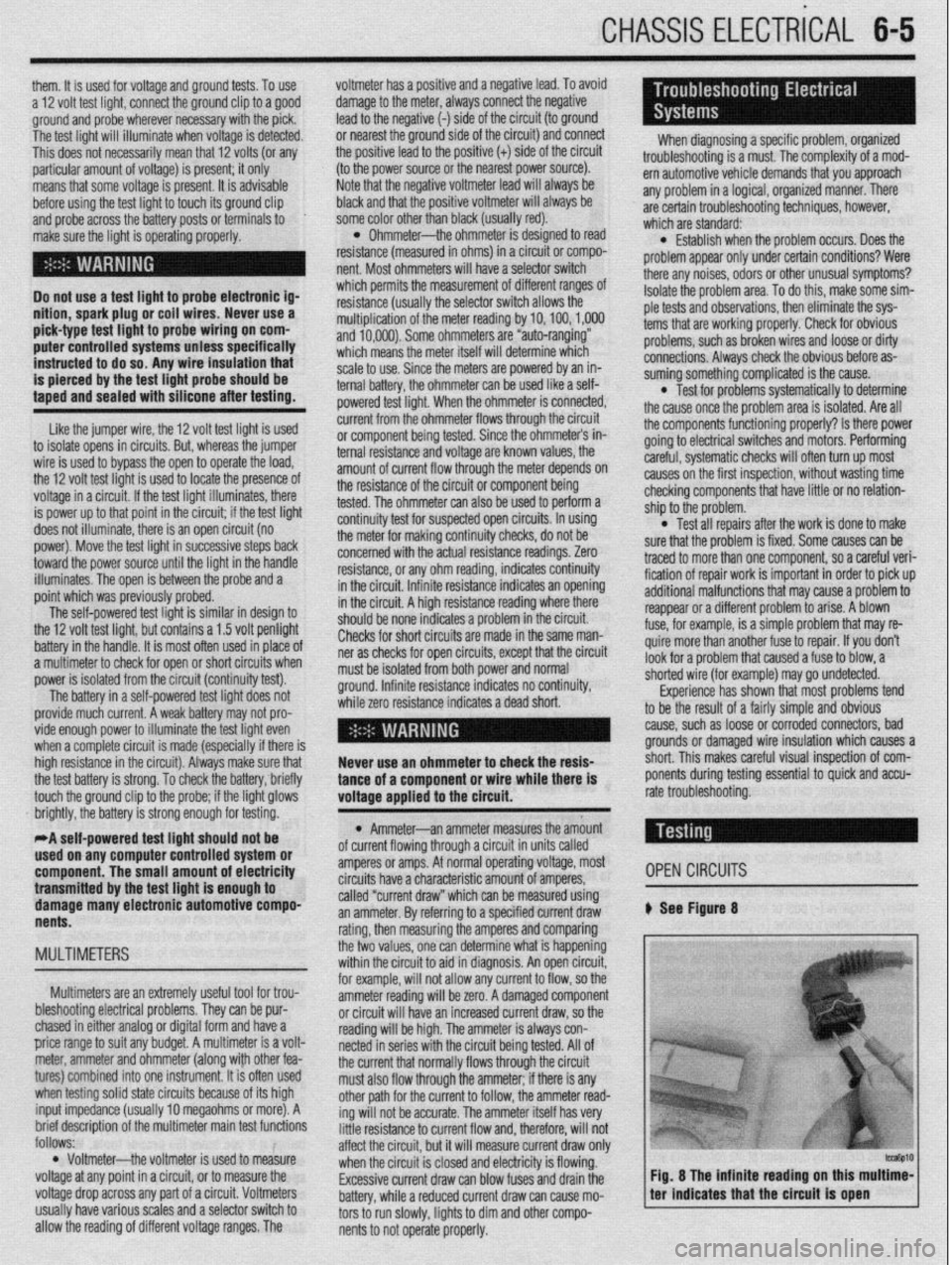
CHASSIS ELECTRiCAL 6-5
them. It is used for voltage and ground tests. To use voltmeter has a positive and a negative lead. To avoid
a 12 volt test light, connect the ground clip to a good damage to the meter, always connect the negative
ground and probe wherever necessary with the pick. lead to the negative (-) side of the circuit (to ground
The test light will illuminate when voltage is detected. or nearest the ground side of the circuit) and connect
This
does not necessarily mean that 12 volts (or any the positive lead to the positive(t) side of the circuit When diagnosing a specific problem, organized
troubleshooting is a must. The complexity of a mod-
particular amount of voltage) is present; it only (to the power source or the nearest power source).
means that some voltage is present. It is advisable Note that the negative voltmeter lead will always be ern automotive vehicle demands that you approach
before using the test light to touch its ground clip black and that the positive voltmeter will always be any problem in a logical, organized manner. There
and probe across the battery posts or terminals to some color other than black (usually red). are certain troubleshooting techniques, however,
which are standard:
make sure the light is operating properly.
l Ohmmeter-the ohmmeter is designed to read l Establish when the problem occurs. Does the
resistance (measured in ohms) in a circuit or compo-
nent. Most ohmmeters will have a selector switch problem appear only under certain conditions? Were
there any noises, odors or other unusual symptoms?
Do not use a test light to probe electronic ig- which permits the measurement of different ranges of
Isolate the problem area. To do this, make some sim-
nition, spark plug or coil wires. Never use a resistance (usually the selector switch allows the
multiplication of the meter reading by 10,100,1,000 ple tests and observations, then eliminate the sys-
pick-type test light to probe wiring on com- terns that are working properly. Check for obvious
puter controlled systems unless specifically and 10,000). Some ohmmeters are “auto-ranging”
which means the meter itself will determine which problems, such as broken wires and loose or dirty
instructed to do so. Any wire insulation that
scale to use. Since the meters are powered by an in- connections. Always check the obvious before as-
is pierced by the test light probe should be
ternal battery, the ohmmeter can be used like a self- suming something complicated is the cause.
taped and sealed with silicone after testing.
l Test for problems systematically to determine
powered test light. When the ohmmeter is connected,
the cause once the problem area is isolated. Are all
Like the jumper wire, the 12 volt test light is used current from the ohmmeter flows through the circuit
the components functioning properly? Is there power
to isolate opens in circuits. But, whereas the jumper or component being tested. Since the ohmmeter’s in-
ternal resistance and voltage are known values, the going to electrical switches and motors. Performing
wire is used to bypass the open to operate the load,
amount of current flow through the meter depends on careful, systematic checks will often turn up most
the 12 volt test light is used to locate the presence of
the resistance of the circuit or component being causes on the first inspection, without wasting time
voltage in a circuit. If the test light illuminates, there
tested. The ohmmeter can also be used to perform a checking components that have little or no relation-
is power up to that point in the circuit; if the test light ship to the problem.
does not illuminate, there is an open circuit (no continuity test for suspected open circuits. In using
the meter for making continuity checks, do not be
l Test all repairs after the work is done to make
power). Move the test light in successive steps back
concerned with the
actual resistance readings. Zero sure that the problem is fixed. Some causes can be
toward the power source until the light in the handle traced to more than one component, so a careful veri-
illuminates. The open is between the probe and a resistance, or any ohm reading, indicates continuity
fication of repair work is important in order to pick up
point which was previously probed. in the circuit, Infinite resistance indicates an opening
in the circuit. A high resistance reading where there additional malfunctions that may cause a problem to
The self-powered test light is similar in design to
should be none indicates a problem in the circuit. reappear or a different problem to arise. A blown
the 12 volt test light, but contains a 1.5 volt penlight
Checks for short circuits are made in the same man- fuse, for example, is a simple problem that may re-
battery in the handle. It is most often used in place of
ner as checks for open circuits, except that the circuit quire more than another fuse to repair. If you don’t
a multimeter to check for open or short circuits when look for a problem that caused a fuse to blow, a
power is isolated from the circuit (continuity test). must be isolated from both power and normal
ground. Infinite resistance indicates no continuity, shorted wire (for example) may go undetected.
The battery in a self-powered test light does not Experience has shown that most problems tend
provide much current. A weak battery may not pro- while zero resistance indicates a dead short.
to be the result of a fairly simple and obvious
vide enough power to illuminate the test light even I ’ cause, such as loose or corroded connectors, bad
when a complete circuit is made (especially if there is grounds or damaged wire insulation which causes a
high resistance in the circuit). Always make sure that Never use an ohmmeter to check the resis- short. This makes careful visual inspection of com-
the test battery is strong. To check the battery, briefly tance of a component or wire while there is ponents during testing essential to quick and accu-
touch the ground clip to the probe; if the light glows voltage applied to the circuit. rate troubleshooting.
brightly, the battery is strong enough for testing.
*A self-powered test light should not be
l Ammeter-an ammeter measures the amount
- I
used on any computer controlled system or of current flowing through a circuit in units called
component. The small amount of electricity amperes or amps. At normal operating voltage, most
circuits have a characteristic amount of amperes, OPEN CIRCUITS
transmitted by the test light is enough to
damage many electronic automotive compo- called “current draw” which can be measured using
an ammeter. By referring to a specified current draw # See Figure 8
nents.
rating, then measuring the amperes and comparing
MULTIMETERS the two values, one can determine what is happening
within the circuit to aid in diagnosis. An open circuit,
for example, will not allow any current to flow, so the
Multimeters are an extremely useful tool for trou-
bleshooting electrical problems. They can be pur- ammeter reading will be zero. A damaged component
or circuit will have an increased current draw, so the
chased in either analog or digital form and have a
reading will be high. The ammeter is always con-
price range to suit any budget. A multimeter is a volt-
netted in series with the circuit being tested. All of
meter, ammeter and ohmmeter (along with other fea-
the current that normally flows through the circuit
tures) combined into one instrument. It is often used
must also flow through the ammeter; if there is any
when testing solid state circuits because of its high
other path for the current to follow, the ammeter read-
input impedance (usually 10 megaohms or more). A
ing will not be accurate. The ammeter itself has very
brief description of the multiieter main test functions
follows: little resistance to current flow and, therefore, will not
affect the circuit, but it will measure current draw only
l Voltmeter--the voltmeter is used to measure
when the circuit is closed and electricity is flowing.
voltage at any point in a circuit, or to measure the
Excessive current draw can blow fuses and drain the
voltage drop across any part of a circuit. Voltmeters
battery, while a reduced current draw can cause mo-
usually have various scales and a selector switch to
tors to run slowly, lights to dim and other compo-
allow the reading of different voltage ranges. The
nents to not operate properly.
Page 209 of 408
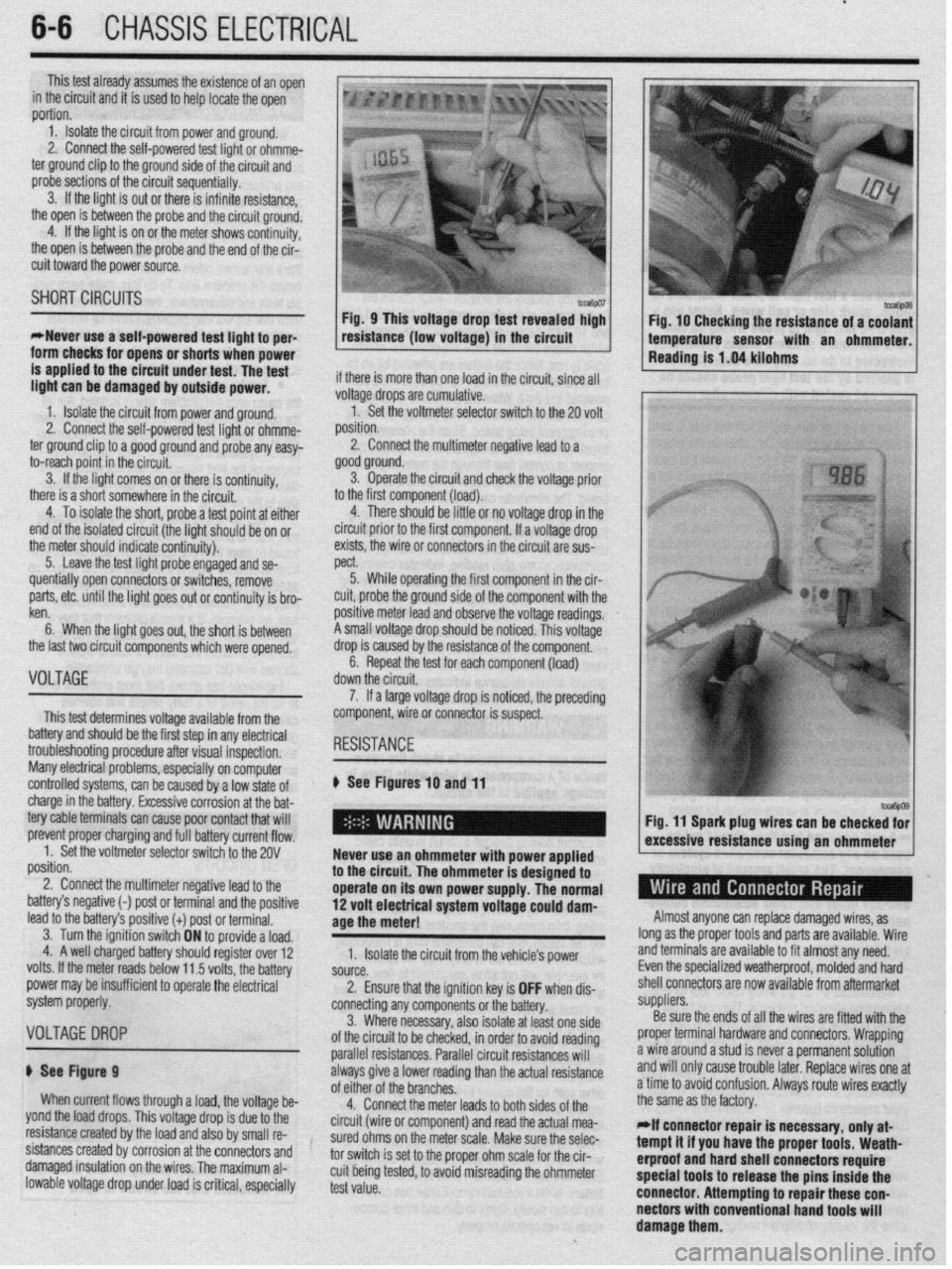
.
6-6 CHASSIS ELECTRICAL
This test already assumes the existence of an open
in the circuit and it is used to help locate the open
portion
1. Isolate the circuit from power and ground.
2. Connect the self-powered test light or ohmme-
ter ground clip to the ground side of the circuit and
probe sections of the circuit sequentially.
3. If the light is out or there is infinite resistance,
the open is between the probe and the circuit ground.
4. If the light is on or the meter shows continuity,
the open is between the probe and the end of the cir-
cuit toward the power source.
SHORT CIRCUITS
*Never use a self-powered test tight to per-
form checks for opens or shorts when power Fig. 10 Checking the resistance of a coolant
temperature sensor with an ohmmeter.
Reading is 1.04 kilohms
is applied to the circuit under test. The test
linht man he dmn~nsrl hu nutnitls nnuva~ if there is more than one load in the circuit, since all m.3.m. “Y.. “1 “ulll”y”” u, ““..7IYG p”“lz’.
1. Isolate the circuit from power and ground.
2. Connect the self-powered ’ .,.*. ,
ted ugnt or onmme-
ter ground clip to a good ground
and probe any easy-
to-reach point in the circuit.
3. If the light comes on or there is continuity,
there is a short somewhere in the circuit.
4. To isolate the short, probe a test point at either
end of the isolated circuit (the light should be on or
the meter should indicate continuity).
5. Leave the test light probe engaged and se- voltage drops are cumulative.
1. Set the voltmeter selector switch to the 20 volt
^,.^X^..
pJbl1IUII.
2. Connect the multimeter negative lead to a
good ground.
3. Operate the circuit and check the voltage prior
.
to the hrst component (load).
4. There should be little or no voltage drop in the
circuit prior to the first component. If a voltage drop
exists, the wire or connectors in the circuit are sus-
WY.+
)JGW 5. While operating the first component in the cir-
.
positive meter lead and observe the voltage readings.
A small voltage drop should be noticed. This voltage
drop is caused by the resistance of the component.
6. Repeat the test for each component (load)
de .-IL- .‘.. .I
uuwn me crrcun. quentially open connectors or switches, remove
parts, etc. until the light goes out or continuity is bro-
ken
6. When the light goes out, the short is between
the last two circuit components which were opened,
nl -r*l?I-
VuLlHbt
This test determines voltage available from the
battery and should be the first step in any electrical
troubleshooting procedure after visual inspection,
Many electrical problems, esoeciallv on comouter
controlled systems, can be caused by a low state of 7. If a large voltage drop is noticed, the preceding
component, wire or connector is suspect.
# See Figures
10 and 11
charge in the battery. Excessive corrosion at the bat-
tery cable terminals can cause poor contact that will
prevent proper charging and full battery current flow,
1. Set the voltmeter selector switch to the 20V
position.
2. Connect the multimeter negative lead to the
h*+tnn,‘n nnn,,,;~,,. , ..^,a ^-L.--:^^l --_I ‘I- ---!I?... Never use an ohmmeter with power applied
to the circuit. The ohmmeter is designed to
operate on its 0 wn power supply. The normal
1^
. . . . . Fig. 11 Spark plug wires can be checke;
MW~ 3 IlG~dllYt: t-1 pUSI UI Lellllllldl allU lilt, pUSlIlVe lead to the battery’s positive (t) post or terminal.
3. Turn the ignition switch ON to provide a load,
4. A well charged battery should register over 12
volts. If the meter reads below 11 5 vnlts tha hq*anr
_ _ .-, . power may be insufficient to operate the eler ii! volt electrical system voltage could dam-
age the meter!
1. Isolate the circuit from the vehicle’s power
CnlOrAn I)““IW. 2. Ensure that the ignition key is OFF when dis- Almost anyone can replace damaged wires, as
long as the proper tools and parts are available. Wire
and terminals are available to fit almost any need.
Even the specialized weatherproof, molded and hard
shell connectors are now cl mdicm available from aftermarket
system properly.
connecting any components or the battery. ““yp,8w’“.
3. Where necessary, also isolate at least one side Be sure the ends of all the wires are fitted with the
VOLTAGEDROP of the circuit to be checked, in order to avoid reading proper terminal hardware and connectors. Wrapping
parallel resistances. Parallel circuit resistances will a wire around a stud is never a permanent solution
# See Figure 9 always give a lower reading than the actual resistance and will only cause trouble later. Replace wires one at
When current flows through a load, the voltage be- of eifhy n< +hn hmnnh-r
GI “I II It: “I a lb1 It?>. a time to avoid confusion. Always route wires exactly
4.
Connect the meter leads to both sides of the the same as the factory.
yond the load drops. This voltage drop is due to the
resistance created by the load and also by small re- circuit (wire or component) and read the actual mea-
sured ohms on the meter scale. Make sure the selec- *If connector repair is necessary, only at-
sistances created by corrosion at the connectors and
tor switch is set to the proper ohm scale for the cir- tempt it if you have the proper tools. Weath-
damaged insulation on the wires. The maximum al- erproof and hard shell connectors require
lowable voltage drop under load is critical, especially cuit being tested, to avoid misreading the ohmmeter
test value. spectal tools to release the pins inside the
connector. Attempting to repair these con-
nectors with conventional hand tools will
damage them.
Page 210 of 408
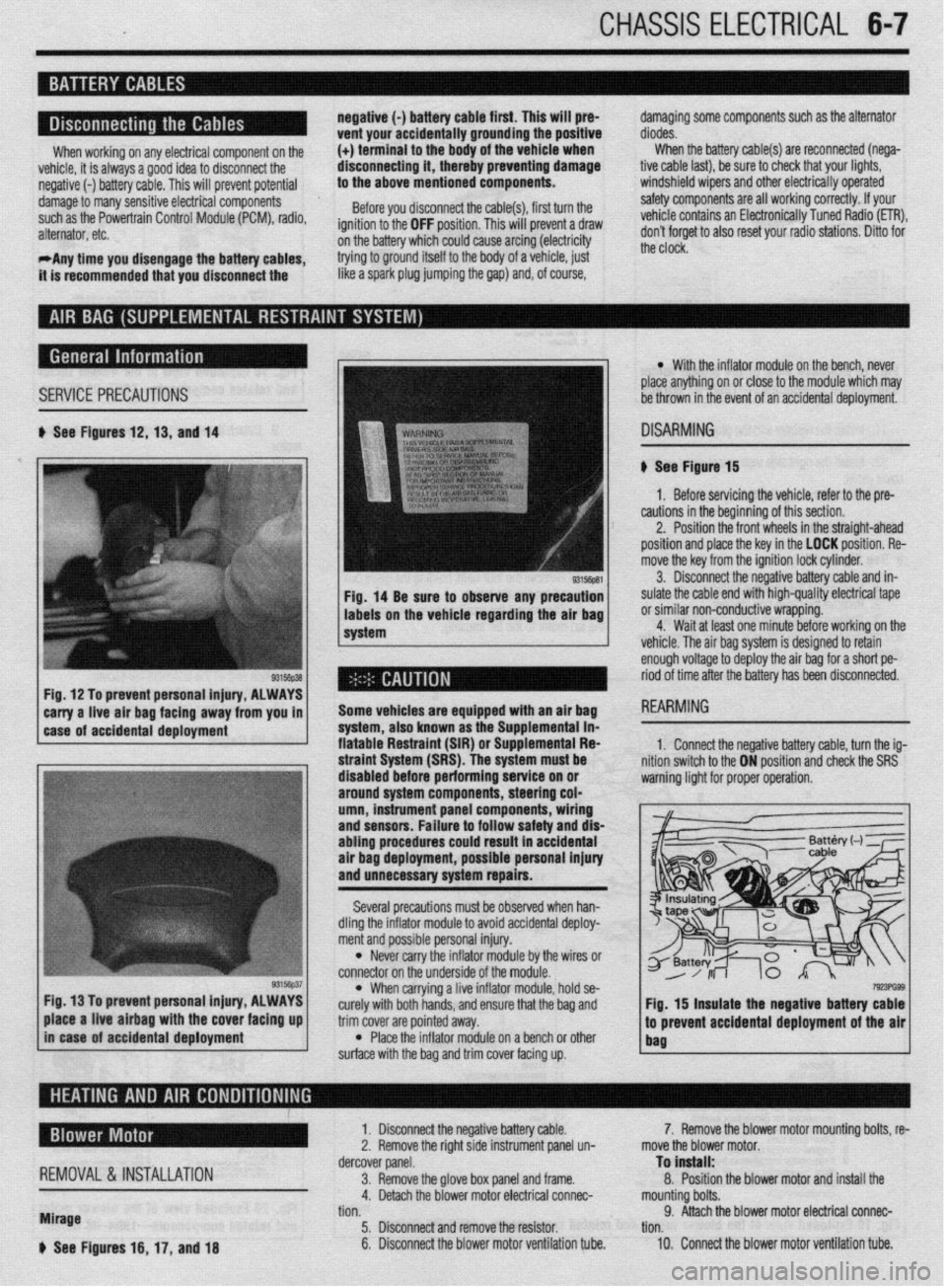
I I
CHASSIS ELECTRICAL 6-7
When working on any electrical component on the
vehicle, it is always a good idea to disconnect the
negative (-) battery cable. This will prevent potential
damage to many sensitive electrical components
such as the Powertrain Control Module (PCM), radio,
alternator, etc.
*Any time you disengage the battery cables,
it is recommended that you disconnect the negative (-) battery cable first. This will pre-
vent your accidentally grounding the positive
(+) terminal to the body of the vehicle when
disconnecting it, thereby preventing damage
to the above mentioned components.
Before you disconnect the cable(s), first turn the
ignition to the OFF position. This will prevent a draw
on the battery which could cause arcing (electricity
trying to ground itself to the body of a vehicle, just
like a spark plug jumping the gap) and, of course, damaging some components such as the alternator
diodes.
When the battery cable(s) are reconnected (nega-
tive cable last), be sure to check that your lights,
windshield wipers and other electrically operated
safety components are all working correctly. If your
vehicle contains an Electronically Tuned Radio (ETR),
don’t forget to also reset your radio stations. Ditto for
the clock.
SERVICE PRECAUTIONS
b See Figures 12,13, and 14
Fig, 14 Be sure to observe any precaution
labels on the vehicle regarding the air bag
system
Fig. 12 To prevent personal injury, ALWAYS
*
carry a-live -ah bag fac!ng away from you in 1
1 case of accidental deployment Some vehicles are equipped wtth an air bag
-.-‘--
syr1em, aiscl Known as I11 -I-- ‘------- -- sLe Supplemental in- fiatable Restraint (SIR) o r Suouiementai Fiea
l With the inflator module on the bench, never
place anything on or close to the module which may
be thrown in the event of an accidental deployment.
DISARMING
# See Figure 15
1. Before servicing the vehicle, refer to the pre-
cautions in the beginning of this section.
2. Position the front wheels in the straight-ahead
position and place the key in the LOCK position. Re-
move the key from the ignition lock cylinder.
3. Disconnect the negative battery cable and in-
sulate the cable end with high-quality electrical tape
or similar non-conductive wrapping.
4. Wait at least one minute before working on the
vehicle. The air baa svstem is desianed to retain
enough voltage to deploy the air bag for a short pe-
riod of time after the battery has been disconnected.
1. Connect the neoative batters cable. turn the ia-
3, hold se-
e bag and
trim cover are pointed away.
l Place the inflator module on a bench or other
surface with the bag and trim cover facing up.
7!r!3PG93 Fig. 15 insulate the negative battery cable
.I
to prevent accidental deployment of the air
bag place a live airbag with the cover facing up
in case of accidental deployment
REMOVAL &INSTALLATION
Mirage
b See Figures 16, 17, and 18 1. Disconnect the negative battery cable.
2. Remove the right side instrument panel un-
dercover panel.
3. Remove the glove box panel and frame.
4. Detach the blower motor electrical connec-
tion.
5. Disconnect and remove the resistor.
6. Disconnect the blower motor ventilation tube. 7. Remove the blower motor mounting bolts, re-
move the blower motor.
To install:
8. Position the blower motor and install the
mounting bolts.
9. Attach the blower motor electrical connec-
tion.
10. Connect the blower motor ventilation tube.