NISSAN X-TRAIL 2003 Electronic Repair Manual
Manufacturer: NISSAN, Model Year: 2003, Model line: X-TRAIL, Model: NISSAN X-TRAIL 2003Pages: 3066, PDF Size: 51.47 MB
Page 2841 of 3066
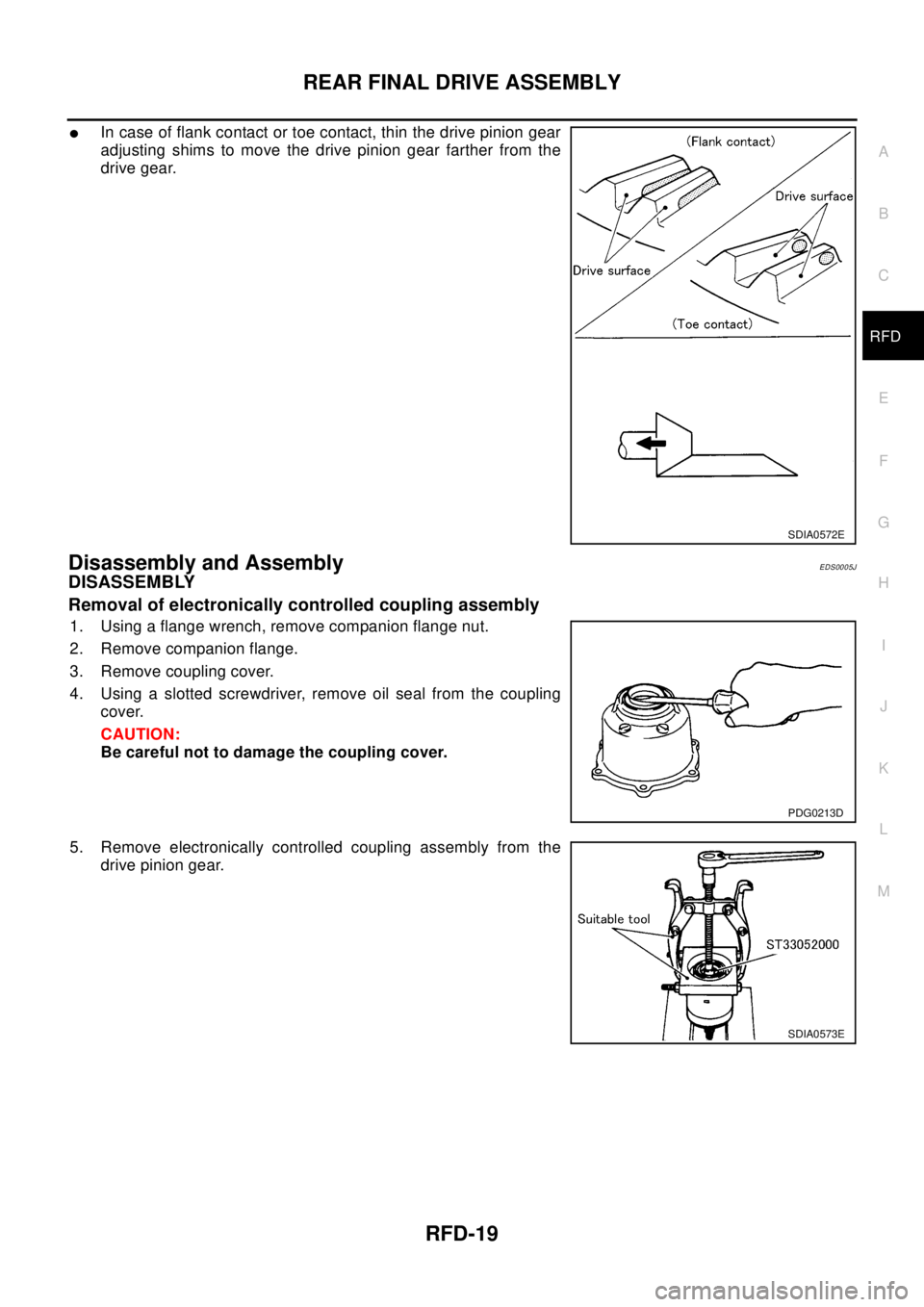
REAR FINAL DRIVE ASSEMBLY
RFD-19
C
E
F
G
H
I
J
K
L
MA
B
RFD
lIn case of flank contact or toe contact, thin the drive pinion gear
adjusting shims to move the drive pinion gear farther from the
drive gear.
Disassembly and AssemblyEDS0005J
DISASSEMBLY
Removal of electronically controlled coupling assembly
1. Using a flange wrench, remove companion flange nut.
2. Remove companion flange.
3. Remove coupling cover.
4. Using a slotted screwdriver, remove oil seal from the coupling
cover.
CAUTION:
Be careful not to damage the coupling cover.
5. Remove electronically controlled coupling assembly from the
drive pinion gear.
SDIA0572E
PDG0213D
SDIA0573E
Page 2842 of 3066
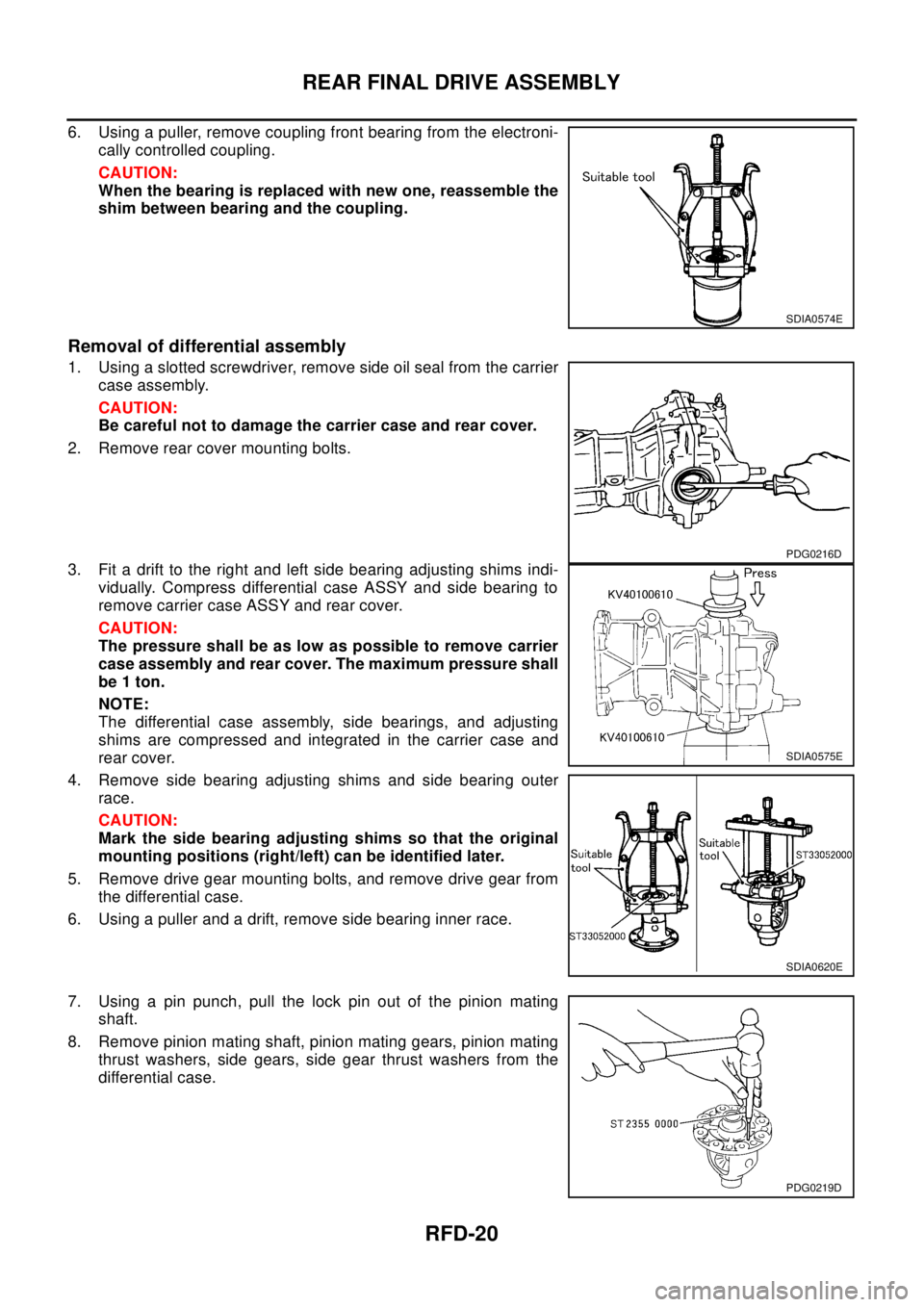
RFD-20
REAR FINAL DRIVE ASSEMBLY
6. Using a puller, remove coupling front bearing from the electroni-
cally controlled coupling.
CAUTION:
When the bearing is replaced with new one, reassemble the
shim between bearing and the coupling.
Removal of differential assembly
1. Using a slotted screwdriver, remove side oil seal from the carrier
case assembly.
CAUTION:
Be careful not to damage the carrier case and rear cover.
2. Remove rear cover mounting bolts.
3. Fit a drift to the right and left side bearing adjusting shims indi-
vidually. Compress differential case ASSY and side bearing to
remove carrier case ASSY and rear cover.
CAUTION:
The pressure shall be as low as possible to remove carrier
case assembly and rear cover. The maximum pressure shall
be 1 ton.
NOTE:
The differential case assembly, side bearings, and adjusting
shims are compressed and integrated in the carrier case and
rear cover.
4. Remove side bearing adjusting shims and side bearing outer
race.
CAUTION:
Mark the side bearing adjusting shims so that the original
mounting positions (right/left) can be identified later.
5. Remove drive gear mounting bolts, and remove drive gear from
the differential case.
6. Using a puller and a drift, remove side bearing inner race.
7. Using a pin punch, pull the lock pin out of the pinion mating
shaft.
8. Remove pinion mating shaft, pinion mating gears, pinion mating
thrust washers, side gears, side gear thrust washers from the
differential case.
SDIA0574E
PDG0216D
SDIA0575E
SDIA0620E
PDG0219D
Page 2843 of 3066
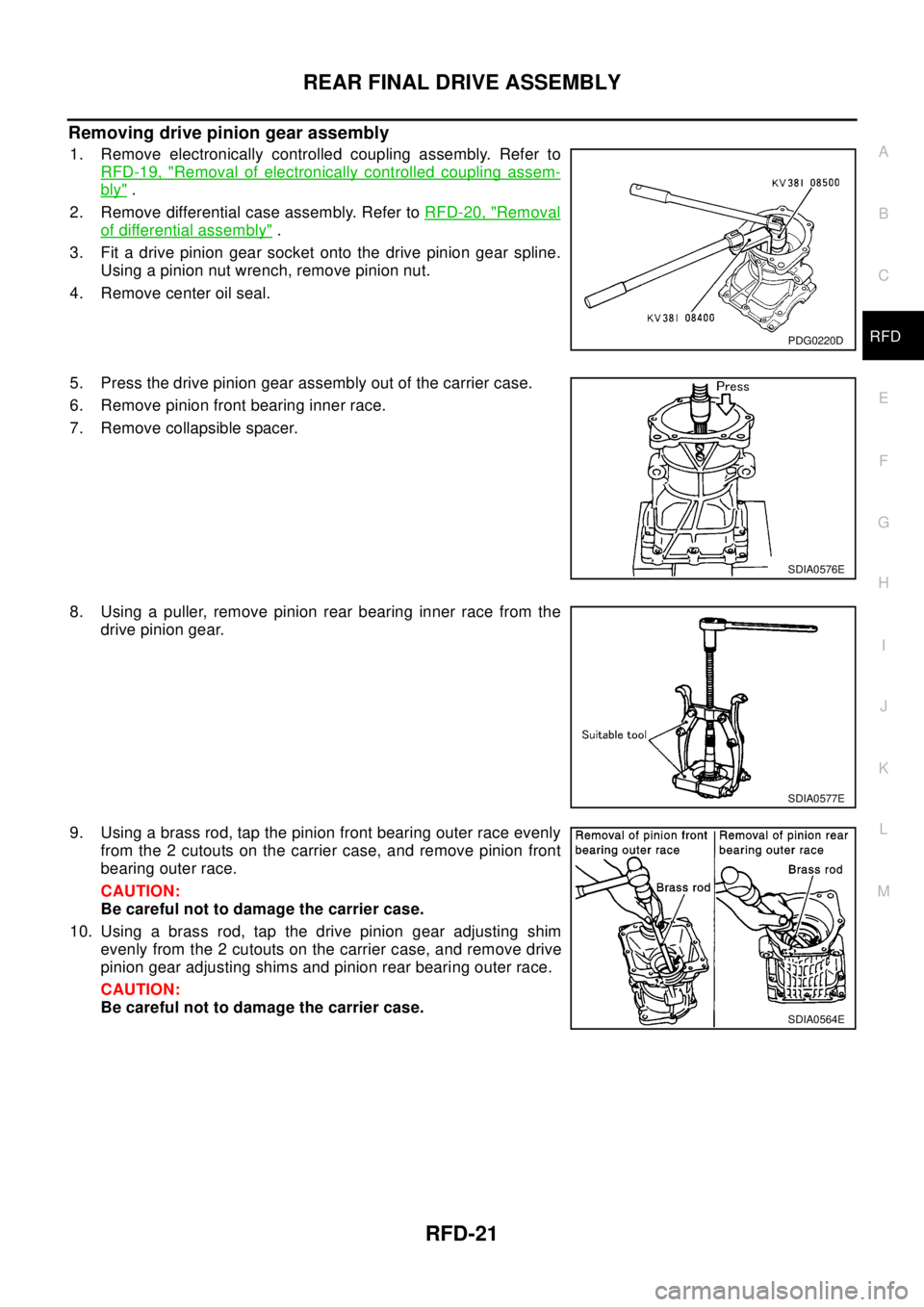
REAR FINAL DRIVE ASSEMBLY
RFD-21
C
E
F
G
H
I
J
K
L
MA
B
RFD
Removing drive pinion gear assembly
1. Remove electronically controlled coupling assembly. Refer to
RFD-19, "
Removal of electronically controlled coupling assem-
bly".
2. Remove differential case assembly. Refer toRFD-20, "
Removal
of differential assembly".
3. Fit a drive pinion gear socket onto the drive pinion gear spline.
Using a pinion nut wrench, remove pinion nut.
4. Remove center oil seal.
5. Press the drive pinion gear assembly out of the carrier case.
6. Remove pinion front bearing inner race.
7. Remove collapsible spacer.
8. Using a puller, remove pinion rear bearing inner race from the
drive pinion gear.
9. Using a brass rod, tap the pinion front bearing outer race evenly
from the 2 cutouts on the carrier case, and remove pinion front
bearing outer race.
CAUTION:
Be careful not to damage the carrier case.
10. Using a brass rod, tap the drive pinion gear adjusting shim
evenly from the 2 cutouts on the carrier case, and remove drive
pinion gear adjusting shims and pinion rear bearing outer race.
CAUTION:
Be careful not to damage the carrier case.
PDG0220D
SDIA0576E
SDIA0577E
SDIA0564E
Page 2844 of 3066
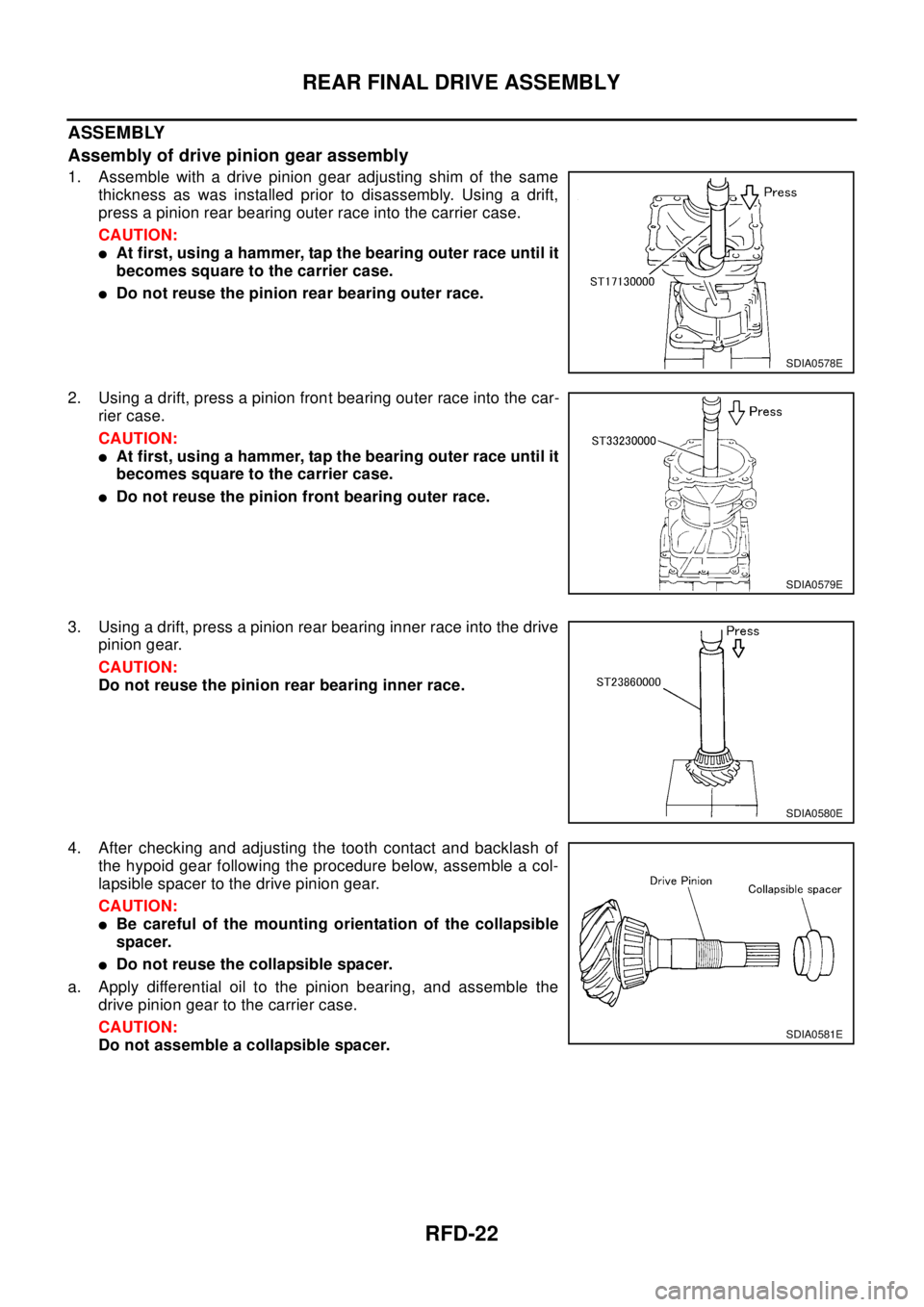
RFD-22
REAR FINAL DRIVE ASSEMBLY
ASSEMBLY
Assembly of drive pinion gear assembly
1. Assemble with a drive pinion gear adjusting shim of the same
thickness as was installed prior to disassembly. Using a drift,
press a pinion rear bearing outer race into the carrier case.
CAUTION:
lAt first, using a hammer, tap the bearing outer race until it
becomes square to the carrier case.
lDo not reuse the pinion rear bearing outer race.
2. Using a drift, press a pinion front bearing outer race into the car-
rier case.
CAUTION:
lAt first, using a hammer, tap the bearing outer race until it
becomes square to the carrier case.
lDo not reuse the pinion front bearing outer race.
3. Using a drift, press a pinion rear bearing inner race into the drive
pinion gear.
CAUTION:
Do not reuse the pinion rear bearing inner race.
4. After checking and adjusting the tooth contact and backlash of
the hypoid gear following the procedure below, assemble a col-
lapsible spacer to the drive pinion gear.
CAUTION:
lBe careful of the mounting orientation of the collapsible
spacer.
lDo not reuse the collapsible spacer.
a. Apply differential oil to the pinion bearing, and assemble the
drive pinion gear to the carrier case.
CAUTION:
Do not assemble a collapsible spacer.
SDIA0578E
SDIA0579E
SDIA0580E
SDIA0581E
Page 2845 of 3066
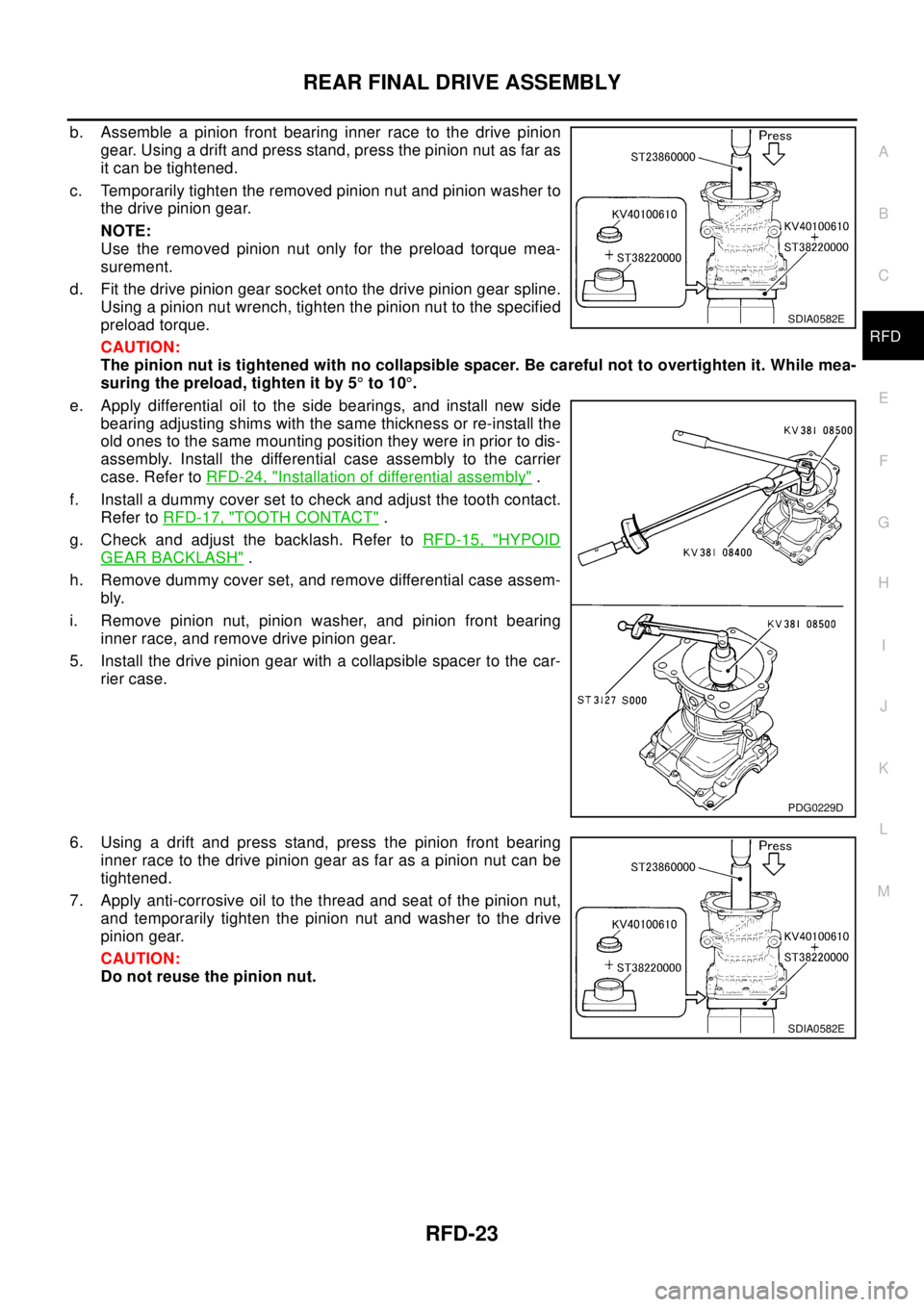
REAR FINAL DRIVE ASSEMBLY
RFD-23
C
E
F
G
H
I
J
K
L
MA
B
RFD
b. Assemble a pinion front bearing inner race to the drive pinion
gear. Using a drift and press stand, press the pinion nut as far as
it can be tightened.
c. Temporarily tighten the removed pinion nut and pinion washer to
the drive pinion gear.
NOTE:
Use the removed pinion nut only for the preload torque mea-
surement.
d. Fit the drive pinion gear socket onto the drive pinion gear spline.
Using a pinion nut wrench, tighten the pinion nut to the specified
preload torque.
CAUTION:
The pinion nut is tightened with no collapsible spacer. Be careful not to overtighten it. While mea-
suring the preload, tighten it by 5°to 10°.
e. Apply differential oil to the side bearings, and install new side
bearing adjusting shims with the same thickness or re-install the
old ones to the same mounting position they were in prior to dis-
assembly. Install the differential case assembly to the carrier
case. Refer toRFD-24, "
Installation of differential assembly".
f. Install a dummy cover set to check and adjust the tooth contact.
Refer toRFD-17, "
TOOTH CONTACT".
g. Check and adjust the backlash. Refer toRFD-15, "
HYPOID
GEAR BACKLASH".
h. Remove dummy cover set, and remove differential case assem-
bly.
i. Remove pinion nut, pinion washer, and pinion front bearing
inner race, and remove drive pinion gear.
5. Install the drive pinion gear with a collapsible spacer to the car-
rier case.
6. Using a drift and press stand, press the pinion front bearing
inner race to the drive pinion gear as far as a pinion nut can be
tightened.
7. Apply anti-corrosive oil to the thread and seat of the pinion nut,
and temporarily tighten the pinion nut and washer to the drive
pinion gear.
CAUTION:
Do not reuse the pinion nut.
SDIA0582E
PDG0229D
SDIA0582E
Page 2846 of 3066
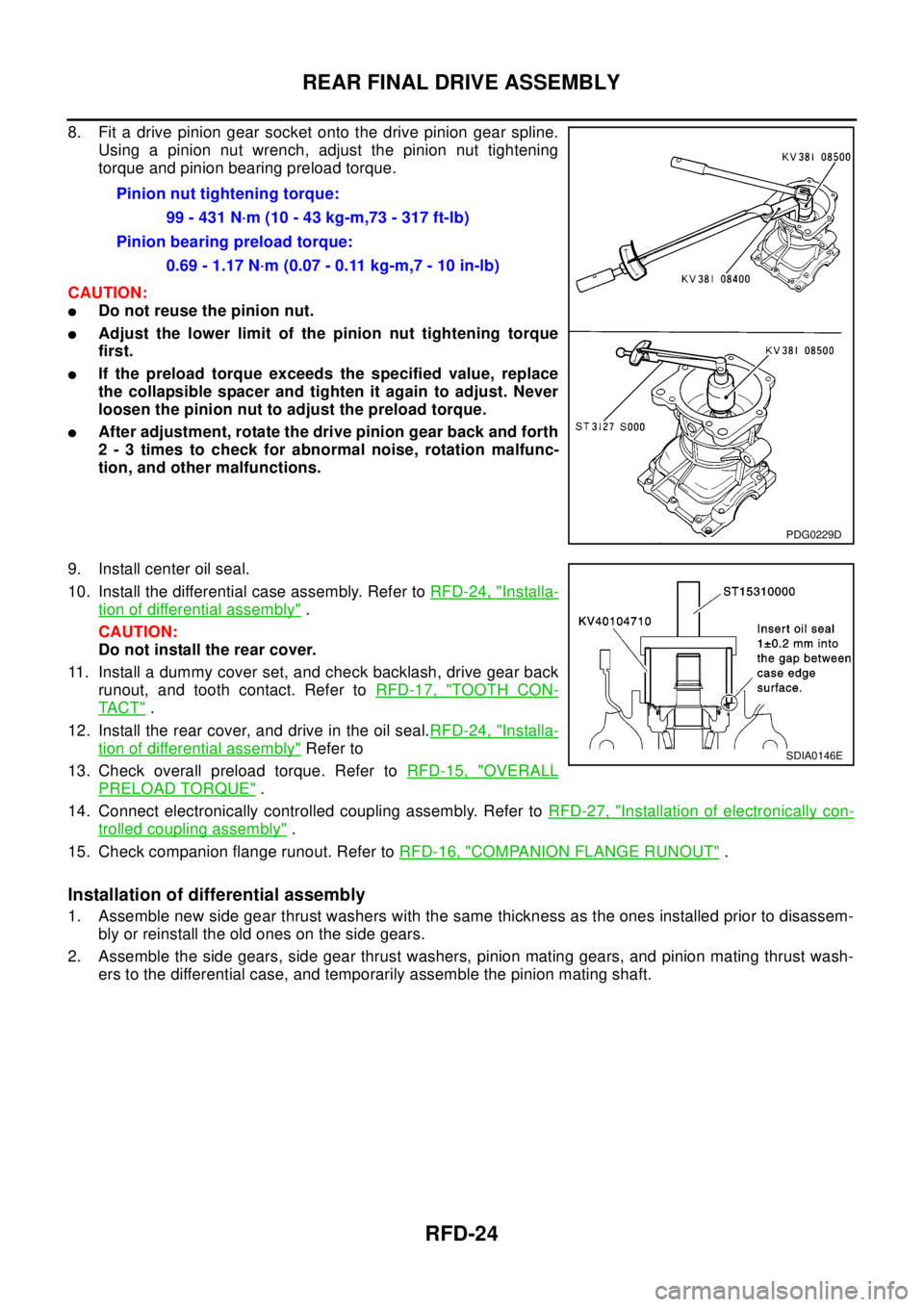
RFD-24
REAR FINAL DRIVE ASSEMBLY
8. Fit a drive pinion gear socket onto the drive pinion gear spline.
Using a pinion nut wrench, adjust the pinion nut tightening
torque and pinion bearing preload torque.
CAUTION:
lDo not reuse the pinion nut.
lAdjust the lower limit of the pinion nut tightening torque
first.
lIf the preload torque exceeds the specified value, replace
the collapsible spacer and tighten it again to adjust. Never
loosen the pinion nut to adjust the preload torque.
lAfter adjustment, rotate the drive pinion gear back and forth
2 - 3 times to check for abnormal noise, rotation malfunc-
tion, and other malfunctions.
9. Install center oil seal.
10. Install the differential case assembly. Refer toRFD-24, "
Installa-
tion of differential assembly".
CAUTION:
Do not install the rear cover.
11. Install a dummy cover set, and check backlash, drive gear back
runout, and tooth contact. Refer toRFD-17, "
TOOTH CON-
TA C T".
12. Install the rear cover, and drive in the oil seal.RFD-24, "
Installa-
tion of differential assembly"Refer to
13. Check overall preload torque. Refer toRFD-15, "
OVERALL
PRELOAD TORQUE".
14. Connect electronically controlled coupling assembly. Refer toRFD-27, "
Installation of electronically con-
trolled coupling assembly".
15. Check companion flange runout. Refer toRFD-16, "
COMPANION FLANGE RUNOUT".
Installation of differential assembly
1. Assemble new side gear thrust washers with the same thickness as the ones installed prior to disassem-
bly or reinstall the old ones on the side gears.
2. Assemble the side gears, side gear thrust washers, pinion mating gears, and pinion mating thrust wash-
ers to the differential case, and temporarily assemble the pinion mating shaft.Pinion nut tightening torque:
99 - 431 N·m (10 - 43 kg-m,73 - 317 ft-lb)
Pinion bearing preload torque:
0.69 - 1.17 N·m (0.07 - 0.11 kg-m,7 - 10 in-lb)
PDG0229D
SDIA0146E
Page 2847 of 3066
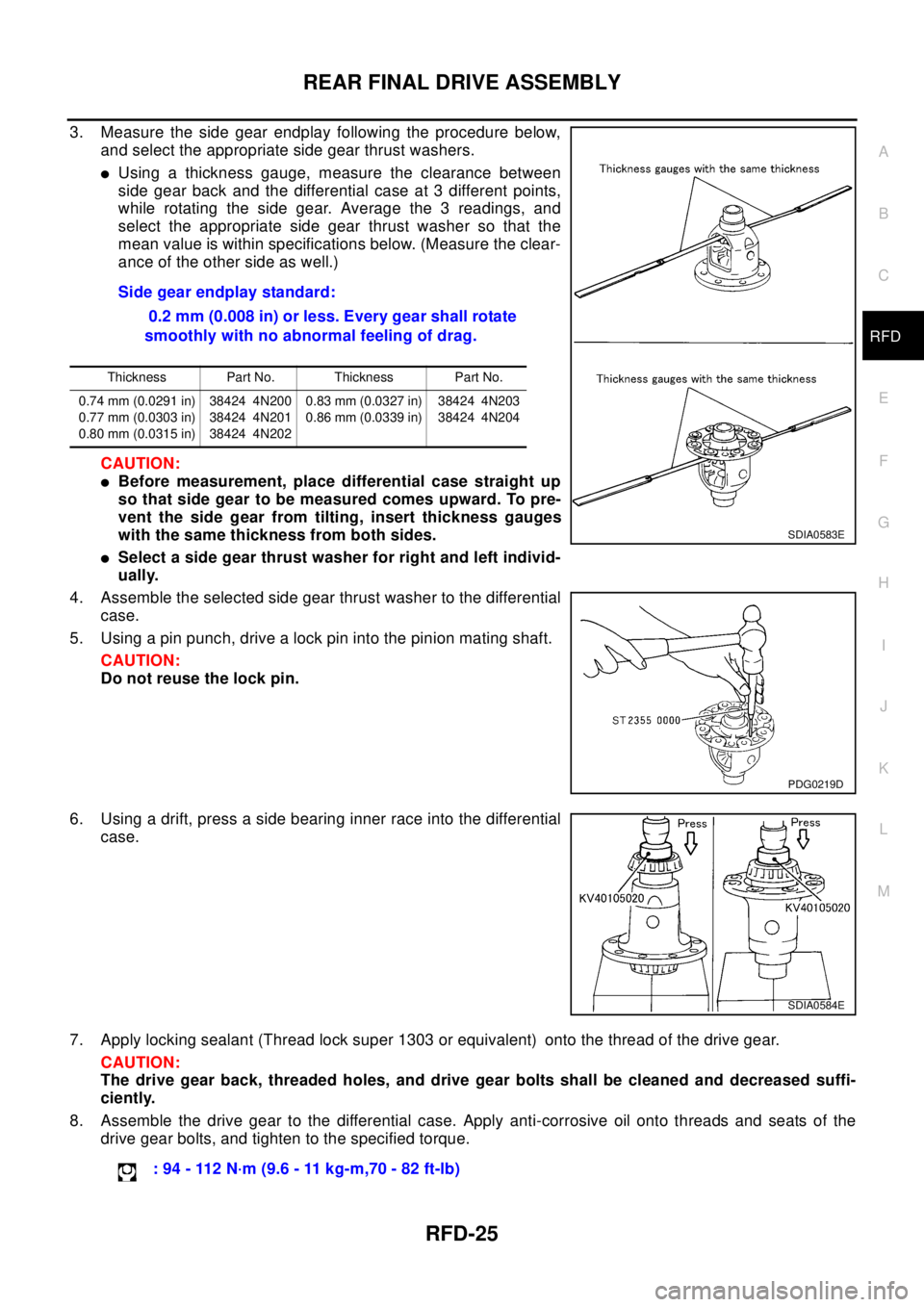
REAR FINAL DRIVE ASSEMBLY
RFD-25
C
E
F
G
H
I
J
K
L
MA
B
RFD
3. Measure the side gear endplay following the procedure below,
and select the appropriate side gear thrust washers.
lUsing a thickness gauge, measure the clearance between
side gear back and the differential case at 3 different points,
while rotating the side gear. Average the 3 readings, and
select the appropriate side gear thrust washer so that the
mean value is within specifications below. (Measure the clear-
ance of the other side as well.)
CAUTION:
lBefore measurement, place differential case straight up
so that side gear to be measured comes upward. To pre-
vent the side gear from tilting, insert thickness gauges
with the same thickness from both sides.
lSelect a side gear thrust washer for right and left individ-
ually.
4. Assemble the selected side gear thrust washer to the differential
case.
5. Using a pin punch, drive a lock pin into the pinion mating shaft.
CAUTION:
Do not reuse the lock pin.
6. Using a drift, press a side bearing inner race into the differential
case.
7. Apply locking sealant (Thread lock super 1303 or equivalent) onto the thread of the drive gear.
CAUTION:
The drive gear back, threaded holes, and drive gear bolts shall be cleaned and decreased suffi-
ciently.
8. Assemble the drive gear to the differential case. Apply anti-corrosive oil onto threads and seats of the
drive gear bolts, and tighten to the specified torque.Side gear endplay standard:
0.2 mm (0.008 in) or less. Every gear shall rotate
smoothly with no abnormal feeling of drag.
Thickness Part No. Thickness Part No.
0.74 mm (0.0291 in)
0.77 mm (0.0303 in)
0.80 mm (0.0315 in)38424 4N200
38424 4N201
38424 4N2020.83 mm (0.0327 in)
0.86 mm (0.0339 in)38424 4N203
38424 4N204
SDIA0583E
PDG0219D
SDIA0584E
:94-112N·m(9.6-11kg-m,70-82ft-lb)
Page 2848 of 3066
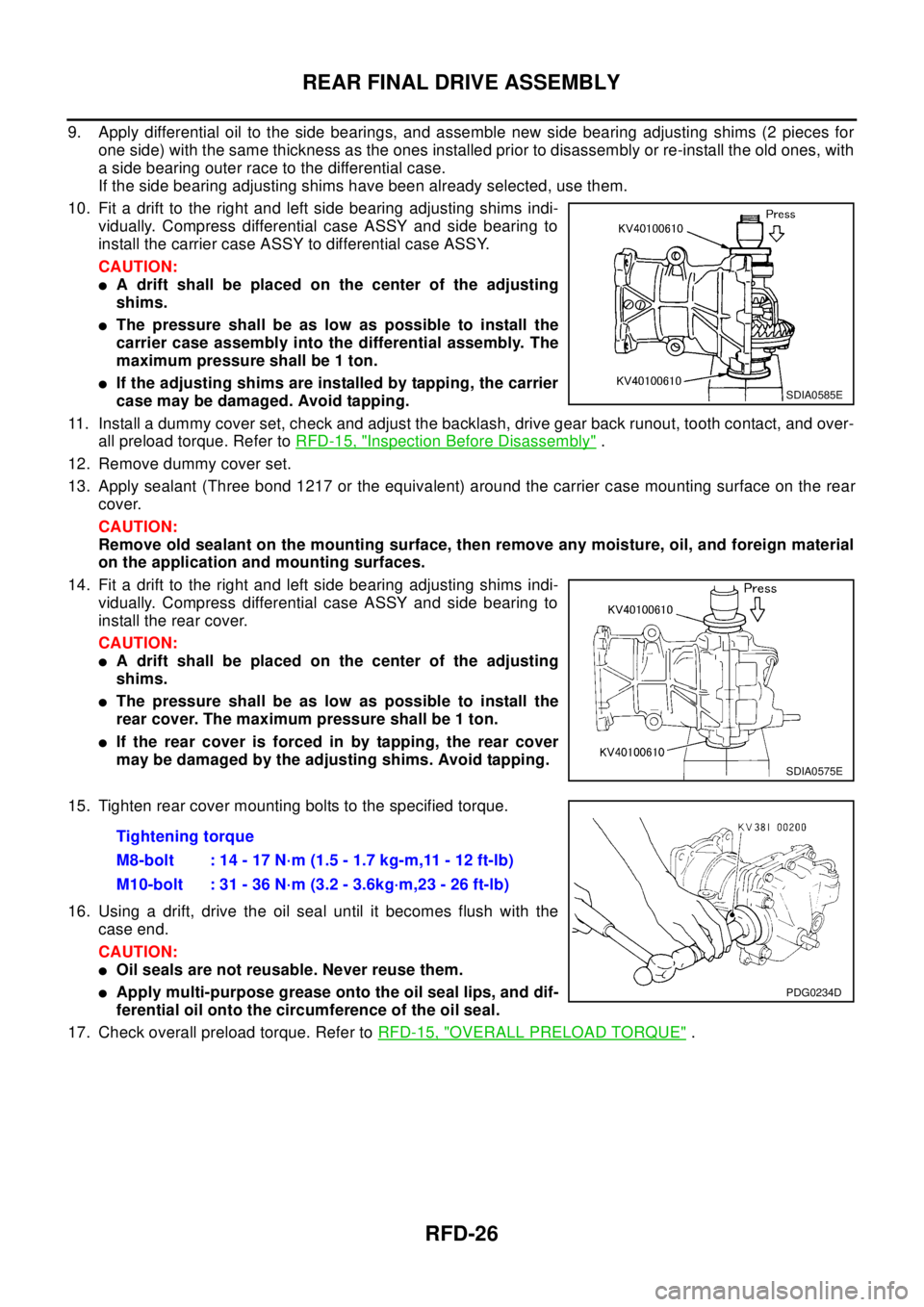
RFD-26
REAR FINAL DRIVE ASSEMBLY
9. Apply differential oil to the side bearings, and assemble new side bearing adjusting shims (2 pieces for
one side) with the same thickness as the ones installed prior to disassembly or re-install the old ones, with
a side bearing outer race to the differential case.
If the side bearing adjusting shims have been already selected, use them.
10. Fit a drift to the right and left side bearing adjusting shims indi-
vidually. Compress differential case ASSY and side bearing to
install the carrier case ASSY to differential case ASSY.
CAUTION:
lA drift shall be placed on the center of the adjusting
shims.
lThepressureshallbeaslowaspossibletoinstallthe
carrier case assembly into the differential assembly. The
maximum pressure shall be 1 ton.
lIf the adjusting shims are installed by tapping, the carrier
case may be damaged. Avoid tapping.
11. Install a dummy cover set, check and adjust the backlash, drive gear back runout, tooth contact, and over-
all preload torque. Refer toRFD-15, "
Inspection Before Disassembly".
12. Remove dummy cover set.
13. Apply sealant (Three bond 1217 or the equivalent) around the carrier case mounting surface on the rear
cover.
CAUTION:
Remove old sealant on the mounting surface, then remove any moisture, oil, and foreign material
on the application and mounting surfaces.
14. Fit a drift to the right and left side bearing adjusting shims indi-
vidually. Compress differential case ASSY and side bearing to
install the rear cover.
CAUTION:
lA drift shall be placed on the center of the adjusting
shims.
lThepressureshallbeaslowaspossibletoinstallthe
rear cover. The maximum pressure shall be 1 ton.
lIf the rear cover is forced in by tapping, the rear cover
may be damaged by the adjusting shims. Avoid tapping.
15. Tighten rear cover mounting bolts to the specified torque.
16. Using a drift, drive the oil seal until it becomes flush with the
case end.
CAUTION:
lOil seals are not reusable. Never reuse them.
lApply multi-purpose grease onto the oil seal lips, and dif-
ferential oil onto the circumference of the oil seal.
17. Check overall preload torque. Refer toRFD-15, "
OVERALL PRELOAD TORQUE".
SDIA0585E
SDIA0575E
Tightening torque
M8-bolt : 14 - 17 N·m (1.5 - 1.7 kg-m,11 - 12 ft-lb)
M10-bolt : 31 - 36 N·m (3.2 - 3.6kg·m,23 - 26 ft-lb)
PDG0234D
Page 2849 of 3066
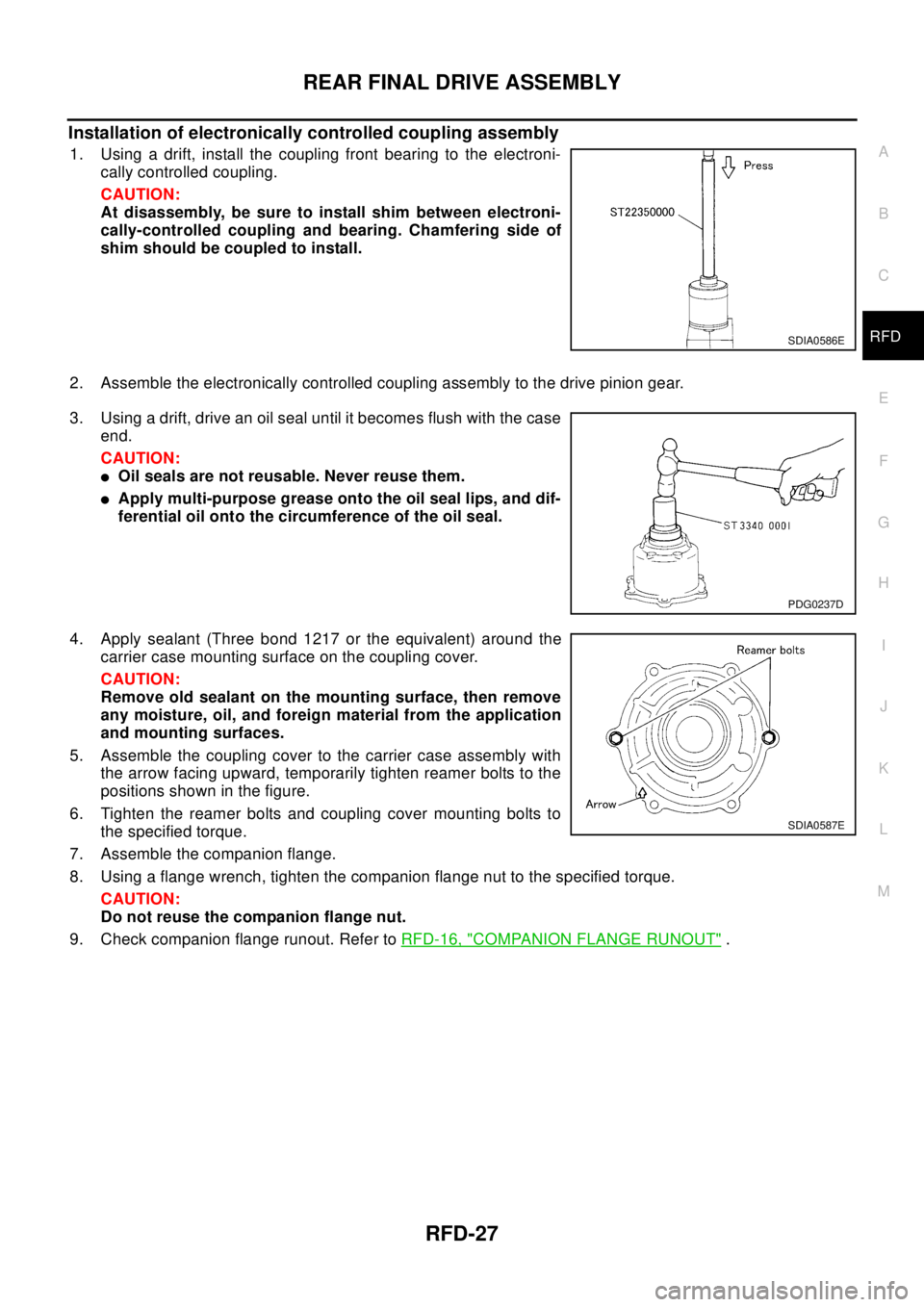
REAR FINAL DRIVE ASSEMBLY
RFD-27
C
E
F
G
H
I
J
K
L
MA
B
RFD
Installation of electronically controlled coupling assembly
1. Using a drift, install the coupling front bearing to the electroni-
cally controlled coupling.
CAUTION:
At disassembly, be sure to install shim between electroni-
cally-controlled coupling and bearing. Chamfering side of
shim should be coupled to install.
2. Assemble the electronically controlled coupling assembly to the drive pinion gear.
3. Using a drift, drive an oil seal until it becomes flush with the case
end.
CAUTION:
lOil seals are not reusable. Never reuse them.
lApply multi-purpose grease onto the oil seal lips, and dif-
ferential oil onto the circumference of the oil seal.
4. Apply sealant (Three bond 1217 or the equivalent) around the
carrier case mounting surface on the coupling cover.
CAUTION:
Remove old sealant on the mounting surface, then remove
any moisture, oil, and foreign material from the application
and mounting surfaces.
5. Assemble the coupling cover to the carrier case assembly with
the arrow facing upward, temporarily tighten reamer bolts to the
positions shown in the figure.
6. Tighten the reamer bolts and coupling cover mounting bolts to
the specified torque.
7. Assemble the companion flange.
8. Using a flange wrench, tighten the companion flange nut to the specified torque.
CAUTION:
Do not reuse the companion flange nut.
9. Check companion flange runout. Refer toRFD-16, "
COMPANION FLANGE RUNOUT".
SDIA0586E
PDG0237D
SDIA0587E
Page 2850 of 3066
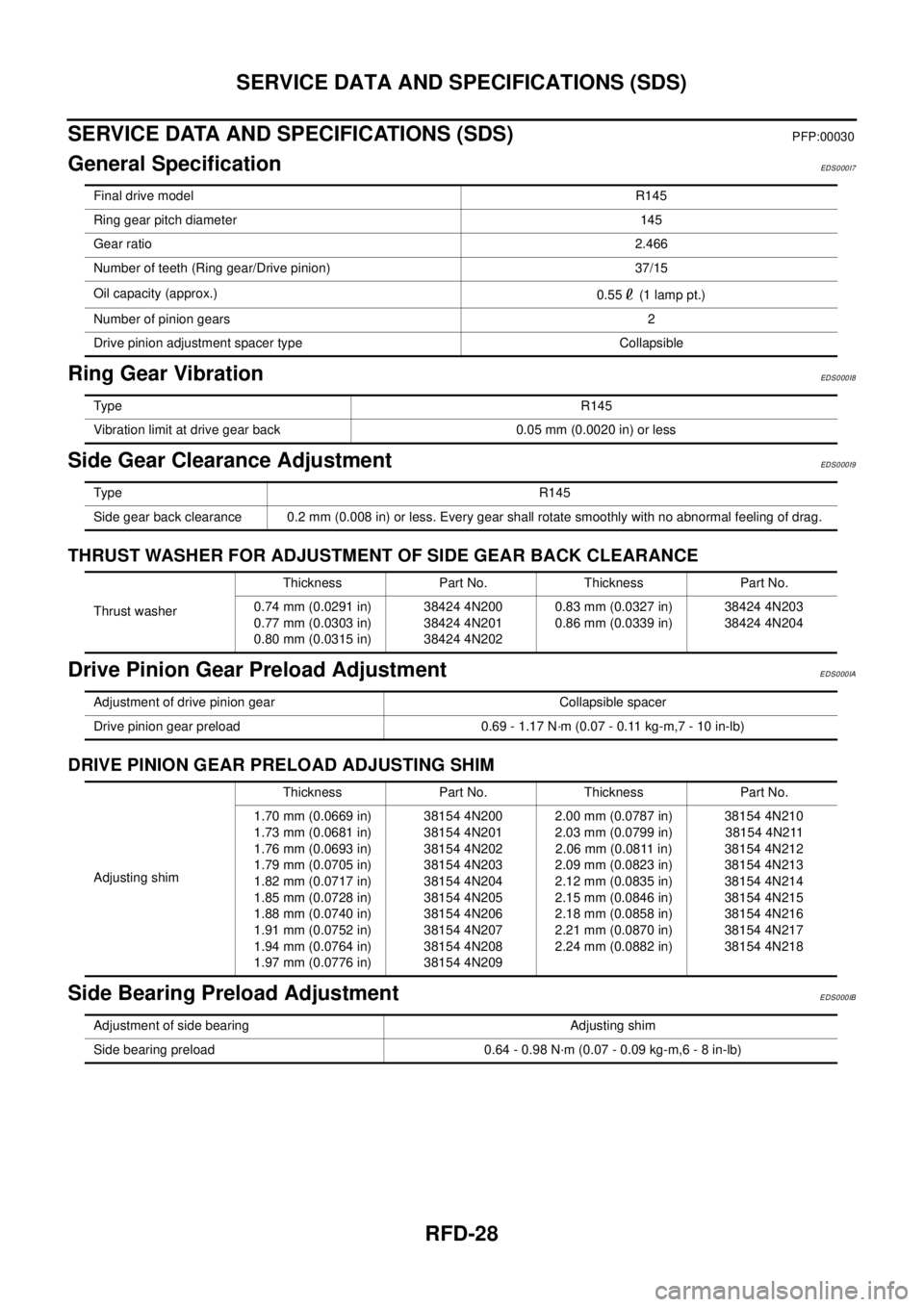
RFD-28
SERVICE DATA AND SPECIFICATIONS (SDS)
SERVICE DATA AND SPECIFICATIONS (SDS)
PFP:00030
General SpecificationEDS0 00 I7
Ring Gear VibrationEDS0 00 I8
Side Gear Clearance AdjustmentEDS0 00 I9
THRUST WASHER FOR ADJUSTMENT OF SIDE GEAR BACK CLEARANCE
Drive Pinion Gear Preload AdjustmentEDS000IA
DRIVE PINION GEAR PRELOAD ADJUSTING SHIM
Side Bearing Preload AdjustmentEDS000IB
Final drive modelR145
Ring gear pitch diameter 145
Gear ratio2.466
Number of teeth (Ring gear/Drive pinion) 37/15
Oil capacity (approx.)
0.55 (1 lamp pt.)
Number of pinion gears2
Drive pinion adjustment spacer type Collapsible
Typ eR145
Vibration limit at drive gear back 0.05 mm (0.0020 in) or less
Type R145
Side gear back clearance 0.2 mm (0.008 in) or less. Every gear shall rotate smoothly with no abnormal feeling of drag.
Thrust washerThickness Part No. Thickness Part No.
0.74 mm (0.0291 in)
0.77 mm (0.0303 in)
0.80 mm (0.0315 in)38424 4N200
38424 4N201
38424 4N2020.83 mm (0.0327 in)
0.86 mm (0.0339 in)38424 4N203
38424 4N204
Adjustment of drive pinion gear Collapsible spacer
Drivepiniongearpreload 0.69-1.17N·m(0.07-0.11kg-m,7-10in-lb)
Adjusting shimThickness Part No. Thickness Part No.
1.70 mm (0.0669 in)
1.73 mm (0.0681 in)
1.76 mm (0.0693 in)
1.79 mm (0.0705 in)
1.82 mm (0.0717 in)
1.85 mm (0.0728 in)
1.88 mm (0.0740 in)
1.91 mm (0.0752 in)
1.94 mm (0.0764 in)
1.97 mm (0.0776 in)38154 4N200
38154 4N201
38154 4N202
38154 4N203
38154 4N204
38154 4N205
38154 4N206
38154 4N207
38154 4N208
38154 4N2092.00 mm (0.0787 in)
2.03 mm (0.0799 in)
2.06 mm (0.0811 in)
2.09 mm (0.0823 in)
2.12 mm (0.0835 in)
2.15 mm (0.0846 in)
2.18 mm (0.0858 in)
2.21 mm (0.0870 in)
2.24 mm (0.0882 in)38154 4N210
38154 4N211
38154 4N212
38154 4N213
38154 4N214
38154 4N215
38154 4N216
38154 4N217
38154 4N218
Adjustment of side bearing Adjusting shim
Side bearing preload 0.64 - 0.98 N·m (0.07 - 0.09 kg-m,6 - 8 in-lb)