OPEL GT-R 1973 Service Manual
Manufacturer: OPEL, Model Year: 1973, Model line: GT-R, Model: OPEL GT-R 1973Pages: 625, PDF Size: 17.22 MB
Page 321 of 625
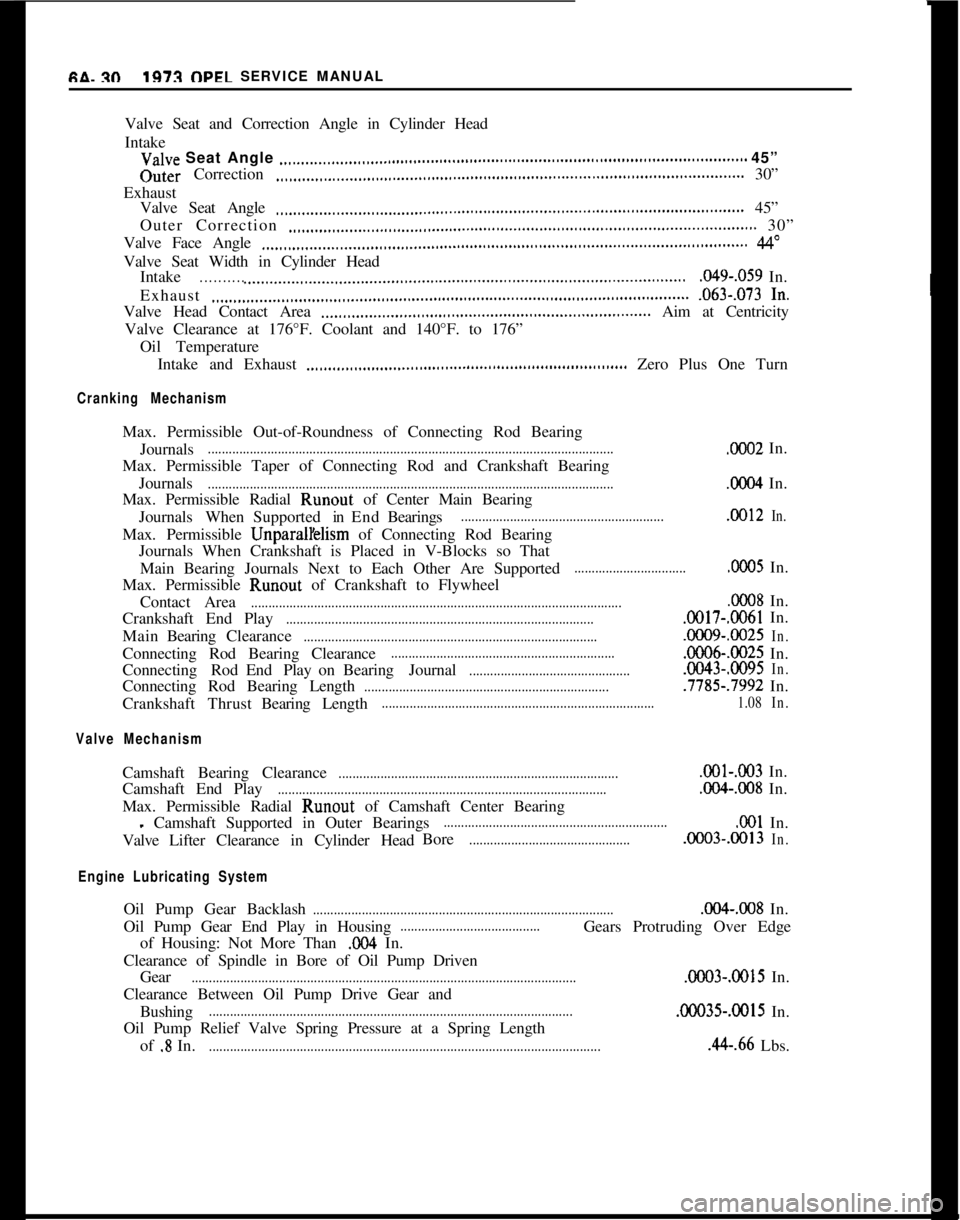
GA. xl1973 OPEL SERVICE MANUAL
Valve Seat and Correction Angle in Cylinder Head
Intake
Valve Seat Angle ..,._,..__....,,..,,,..,.,.,.,..............,............................................................... 45”Outer Correction
.,,,.,,._.,._..___,,,.,,,,,.......,,.,..,...,,..,..,,..,,..,,,.............................................. 30”
Exhaust
Valve Seat Angle
,,,.,,.__,.__..___.,..,,..,...,,....,..,..,..,,..,..,...,..,,,...,,......................................... 45”
Outer Correction
.,,..,,...,._.,.__....,,,.....,,,........................................................................... 30”
Valve Face Angle
,,..,,,..,.__..__.._..,,,..,,...,,......,.,..,..,..,,.,,,..,..,,,..,,,..,,,...,,................................ 44”Valve Seat Width in Cylinder Head
Intake
. . . . . . . . . . .._..._._.................,,..,.....,,..,............,...,..,,,..,,..,,...,,...,,,..,..................049-,059 In.
Exhaust
.,..,,,..,,.___..,,..,,...,..,,,..,,...,,...,,...............,,..,,..........,,....,,...,..................... .063-,073 In.Valve Head Contact Area
,,..,,,..,,___.__.,,..,,..,.,,..........,...,,..,,............,,,...,....... Aim at Centricity
Valve Clearance at 176°F. Coolant and 140°F. to 176”
Oil Temperature
Intake and Exhaust
_.,,..,,,,,,..,,....,...,,,.,.,,,.,..........................,,,..,,,,.... Zero Plus One Turn
Cranking MechanismMax. Permissible Out-of-Roundness of Connecting Rod Bearing
Journals
.....................................................................................................................OC02 In.
Max. Permissible Taper of Connecting Rod and Crankshaft Bearing
Journals
.....................................................................................................................ooO4 In.
Max. Permissible Radial Runout of Center Main Bearing
JournalsWhenSupportedinEndBearings
...........................................................0012In.Max. Permissible UnparalYelism of Connecting Rod Bearing
Journals When Crankshaft is Placed in V-Blocks so That
Main Bearing Journals Next to Each Other Are Supported
................................0005 In.
Max. Permissible Runout of Crankshaft to Flywheel
Contact Area
...........................................................................................................0008 In.
Crankshaft End Play
.........................................................................................GOl7-.CO61 In.
MainBearingClearance
.....................................................................................ooO9-.@I25In.Connecting Rod Bearing Clearance
.................................................................ooO6-.0025 In.
Connecting RodEnd PlayonBearing Journal
...............................................0043-.0095In.Connecting Rod Bearing Length
.......................................................................7785-.7992 In.
CrankshaftThrustBearingLength
..............................................................................1.08In.
Valve MechanismCamshaft Bearing Clearance
.................................................................................OOl-,003 In.
Camshaft End Play
...............................................................................................004-038 In.
Max. Permissible Radial Runout of Camshaft Center Bearing
- Camshaft Supported in Outer Bearings................................................................,001 In.
ValveLifter Clearance in Cylinder HeadBore
...............................................0003-.OOl3In.
Engine Lubricating SystemOil Pump Gear Backlash
......................................................................................0%.008 In.
Oil Pump Gear End Play in Housing
........................................Gears Protruding Over Edge
of Housing: Not More Than
,004 In.
Clearance of Spindle in Bore of Oil Pump Driven
Gear
...............................................................................................................OCO3-.0015 In.
Clearance Between Oil Pump Drive Gear and
Bushing
.........................................................................................................00035-.OOl5 In.
Oil Pump Relief Valve Spring Pressure at a Spring Length
of
.8 In..................................................................................................................44-.66 Lbs.
Page 322 of 625
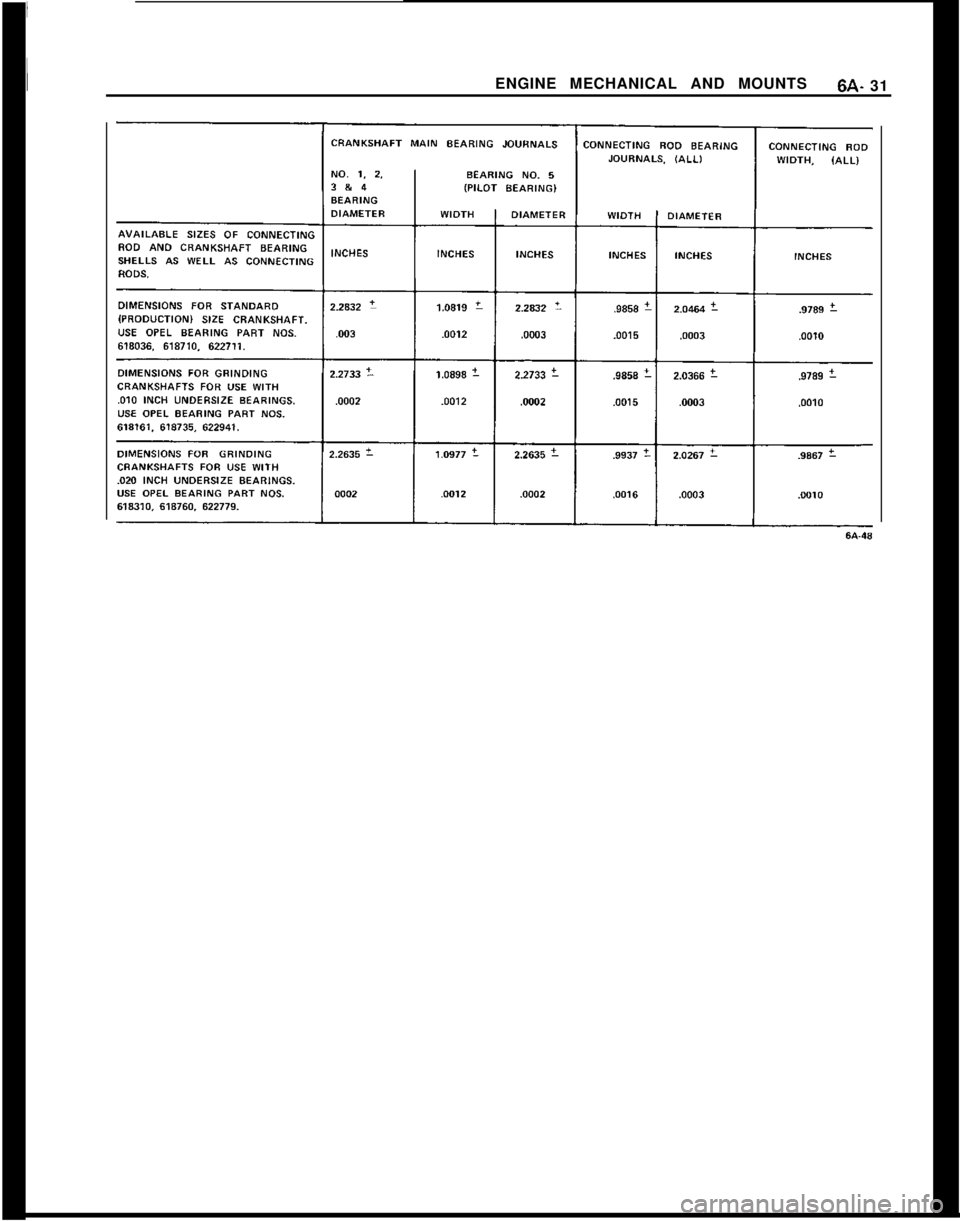
ENGINE MECHANICAL AND MOUNTS6A- 31
Page 323 of 625
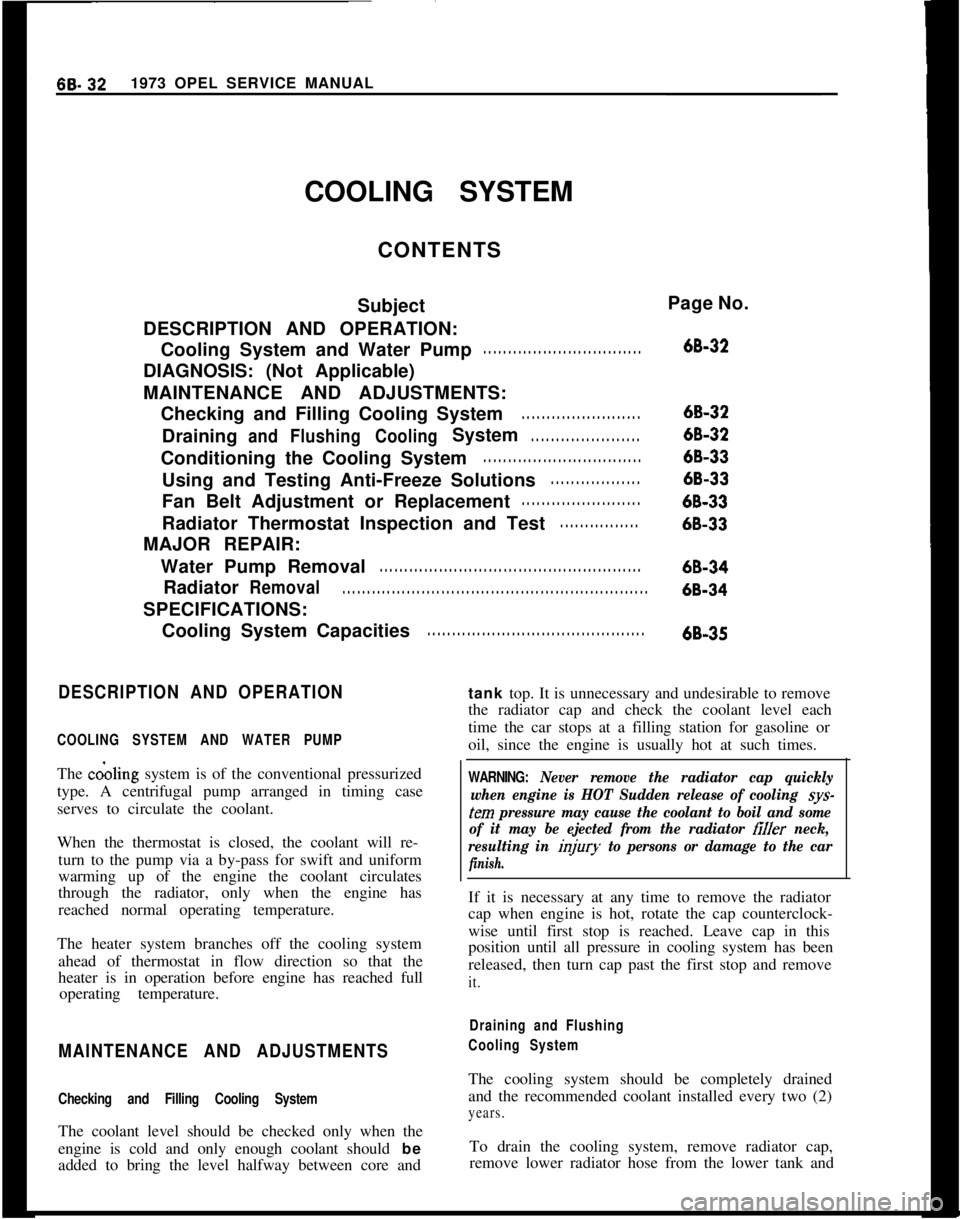
66.321973 OPEL SERVICE MANUAL
COOLING SYSTEM
CONTENTS
Subject
DESCRIPTION AND OPERATION:
Cooling System and Water Pump
. . . . . . . . . . . . . . . . . . . . . . . . . . . . . . . .DIAGNOSIS: (Not Applicable)
MAINTENANCE AND ADJUSTMENTS:
Checking and Filling Cooling System
. . . . . . . . . . . . . . . . . . . . . . . .Draining
andFlushingCoolingSystem. . . . . . . . . . . . . . . . . . . . . .Conditioning the Cooling System
. . . . . . . . . . . . . . . . . . . . . . . . . . . . . . . .Using and Testing Anti-Freeze Solutions
. . . . . . . . . . . . . . . . . .Fan Belt Adjustment or Replacement
. . . . . . . . . . . . . . . . . . . . . . . .Radiator Thermostat Inspection and Test
. . . . . . . . . . . . . . . .MAJOR REPAIR:
Water Pump Removal
. . . . . . . . . . . . . . . . . . . . . . . . . . . . . . . . . . . . . . . . . . . . . . . . . . . . .Radiator
Removal. . . . . . . . . . . . . . . . . . . . . . . . . . . . . . . . . . . . . . . . . . . . . . . . . . . . . . . . . . . . . .SPECIFICATIONS:
Cooling System Capacities
. . . . . . . . . . . . . . . . . . . . . . . . . . . . . . . . . . . . . . . . . . . .Page No.
68-32
6B-32
68-32
68-33
68-33
68-33
68-33
68-34
68-34
6B-35
DESCRIPTION AND OPERATION
COOLING SYSTEM AND WATER PUMPThe coiling system is of the conventional pressurized
type. A centrifugal pump arranged in timing case
serves to circulate the coolant.
When the thermostat is closed, the coolant will re-
turn to the pump via a by-pass for swift and uniform
warming up of the engine the coolant circulates
through the radiator, only when the engine has
reached normal operating temperature.
The heater system branches off the cooling system
ahead of thermostat in flow direction so that the
heater is in operation before engine has reached full
operating temperature.
MAINTENANCE AND ADJUSTMENTS
Checking and Filling Cooling SystemThe coolant level should be checked only when the
engine is cold and only enough coolant should be
added to bring the level halfway between core andtank top. It is unnecessary and undesirable to remove
the radiator cap and check the coolant level each
time the car stops at a filling station for gasoline or
oil, since the engine is usually hot at such times.
WARNING: Never remove the radiator cap quickly
when engine is HOT Sudden release of cooling
sys-
tern pressure may cause the coolant to boil and some
of it may be ejected from the radiator
filler neck,
resulting in
inl’ury to persons or damage to the car
finish.If it is necessary at any time to remove the radiator
cap when engine is hot, rotate the cap counterclock-
wise until first stop is reached. Leave cap in this
position until all pressure in cooling system has been
released, then turn cap past the first stop and remove
it.
Draining and Flushing
Cooling SystemThe cooling system should be completely drained
and the recommended coolant installed every two (2)
years.To drain the cooling system, remove radiator cap,
remove lower radiator hose from the lower tank and
Page 324 of 625
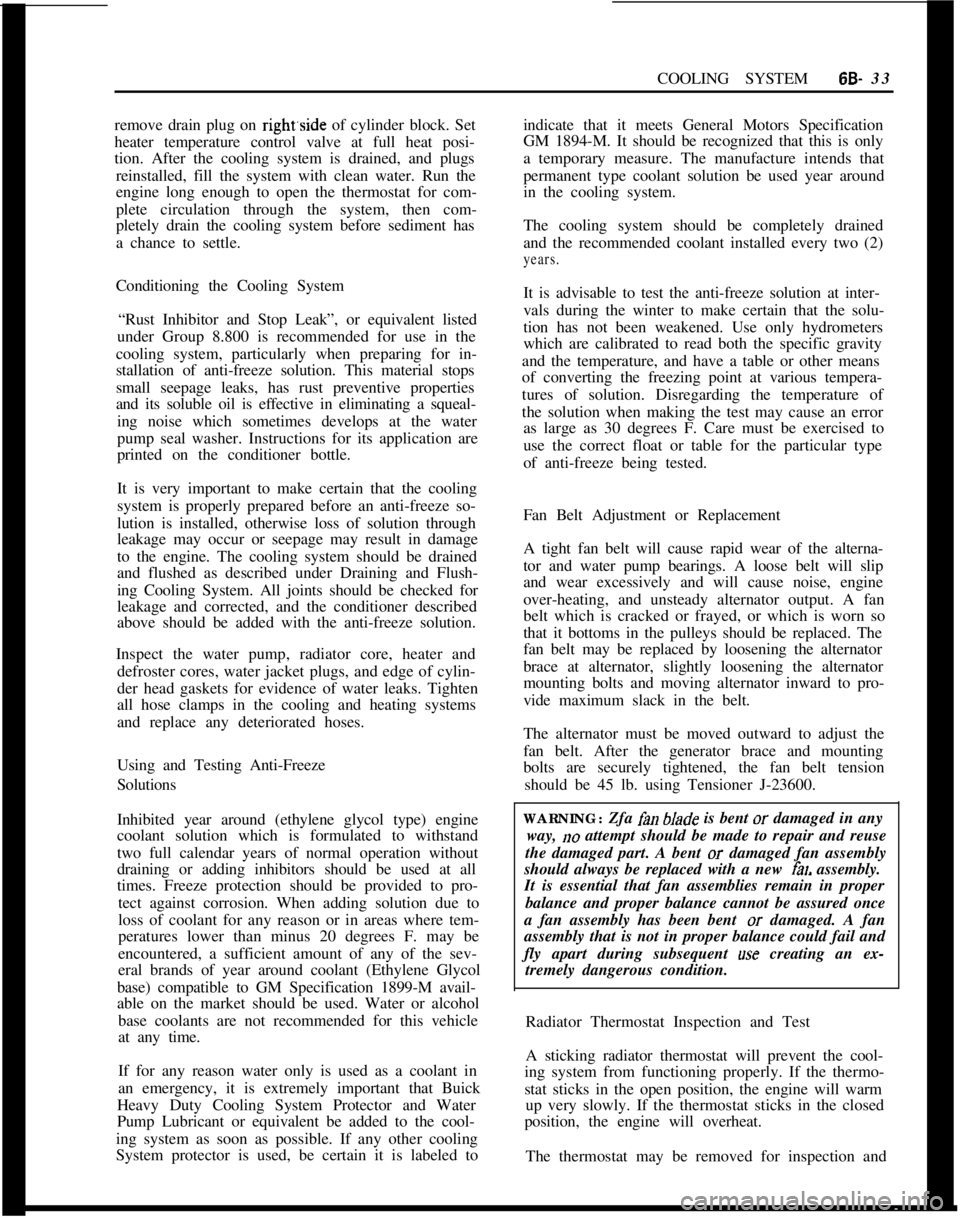
COOLING SYSTEM6B- 33
remove drain plug on right.side of cylinder block. Set
heater temperature control valve at full heat posi-
tion. After the cooling system is drained, and plugs
reinstalled, fill the system with clean water. Run the
engine long enough to open the thermostat for com-
plete circulation through the system, then com-
pletely drain the cooling system before sediment has
a chance to settle.
Conditioning the Cooling System
“Rust Inhibitor and Stop Leak”, or equivalent listed
under Group 8.800 is recommended for use in the
cooling system, particularly when preparing for in-
stallation of anti-freeze solution. This material stops
small seepage leaks, has rust preventive properties
and its soluble oil is effective in eliminating a squeal-
ing noise which sometimes develops at the water
pump seal washer. Instructions for its application are
printed on the conditioner bottle.
It is very important to make certain that the cooling
system is properly prepared before an anti-freeze so-
lution is installed, otherwise loss of solution through
leakage may occur or seepage may result in damage
to the engine. The cooling system should be drained
and flushed as described under Draining and Flush-
ing Cooling System. All joints should be checked for
leakage and corrected, and the conditioner described
above should be added with the anti-freeze solution.
Inspect the water pump, radiator core, heater and
defroster cores, water jacket plugs, and edge of cylin-
der head gaskets for evidence of water leaks. Tighten
all hose clamps in the cooling and heating systems
and replace any deteriorated hoses.
Using and Testing Anti-Freeze
Solutions
Inhibited year around (ethylene glycol type) engine
coolant solution which is formulated to withstand
two full calendar years of normal operation without
draining or adding inhibitors should be used at all
times. Freeze protection should be provided to pro-
tect against corrosion. When adding solution due to
loss of coolant for any reason or in areas where tem-
peratures lower than minus 20 degrees F. may be
encountered, a sufficient amount of any of the sev-
eral brands of year around coolant (Ethylene Glycol
base) compatible to GM Specification 1899-M avail-
able on the market should be used. Water or alcohol
base coolants are not recommended for this vehicle
at any time.
If for any reason water only is used as a coolant in
an emergency, it is extremely important that Buick
Heavy Duty Cooling System Protector and Water
Pump Lubricant or equivalent be added to the cool-
ing system as soon as possible. If any other cooling
System protector is used, be certain it is labeled toindicate that it meets General Motors Specification
GM 1894-M. It should be recognized that this is only
a temporary measure. The manufacture intends that
permanent type coolant solution be used year around
in the cooling system.
The cooling system should be completely drained
and the recommended coolant installed every two (2)years.It is advisable to test the anti-freeze solution at inter-
vals during the winter to make certain that the solu-
tion has not been weakened. Use only hydrometers
which are calibrated to read both the specific gravity
and the temperature, and have a table or other means
of converting the freezing point at various tempera-
tures of solution. Disregarding the temperature of
the solution when making the test may cause an error
as large as 30 degrees F. Care must be exercised to
use the correct float or table for the particular type
of anti-freeze being tested.
Fan Belt Adjustment or Replacement
A tight fan belt will cause rapid wear of the alterna-
tor and water pump bearings. A loose belt will slip
and wear excessively and will cause noise, engine
over-heating, and unsteady alternator output. A fan
belt which is cracked or frayed, or which is worn so
that it bottoms in the pulleys should be replaced. The
fan belt may be replaced by loosening the alternator
brace at alternator, slightly loosening the alternator
mounting bolts and moving alternator inward to pro-
vide maximum slack in the belt.
The alternator must be moved outward to adjust the
fan belt. After the generator brace and mounting
bolts are securely tightened, the fan belt tension
should be 45 lb. using Tensioner J-23600.
WARNING: Zfa
fan blade is bent or damaged in any
way, no attempt should be made to repair and reuse
the damaged part. A bent or damaged fan assembly
should always be replaced with a new
fal. assembly.
It is essential that fan assemblies remain in proper
balance and proper balance cannot be assured once
a fan assembly has been bent or damaged. A fan
assembly that is not in proper balance could fail and
fly apart during subsequent
we creating an ex-
tremely dangerous condition.
Radiator Thermostat Inspection and Test
A sticking radiator thermostat will prevent the cool-
ing system from functioning properly. If the thermo-
stat sticks in the open position, the engine will warm
up very slowly. If the thermostat sticks in the closed
position, the engine will overheat.
The thermostat may be removed for inspection and
Page 325 of 625
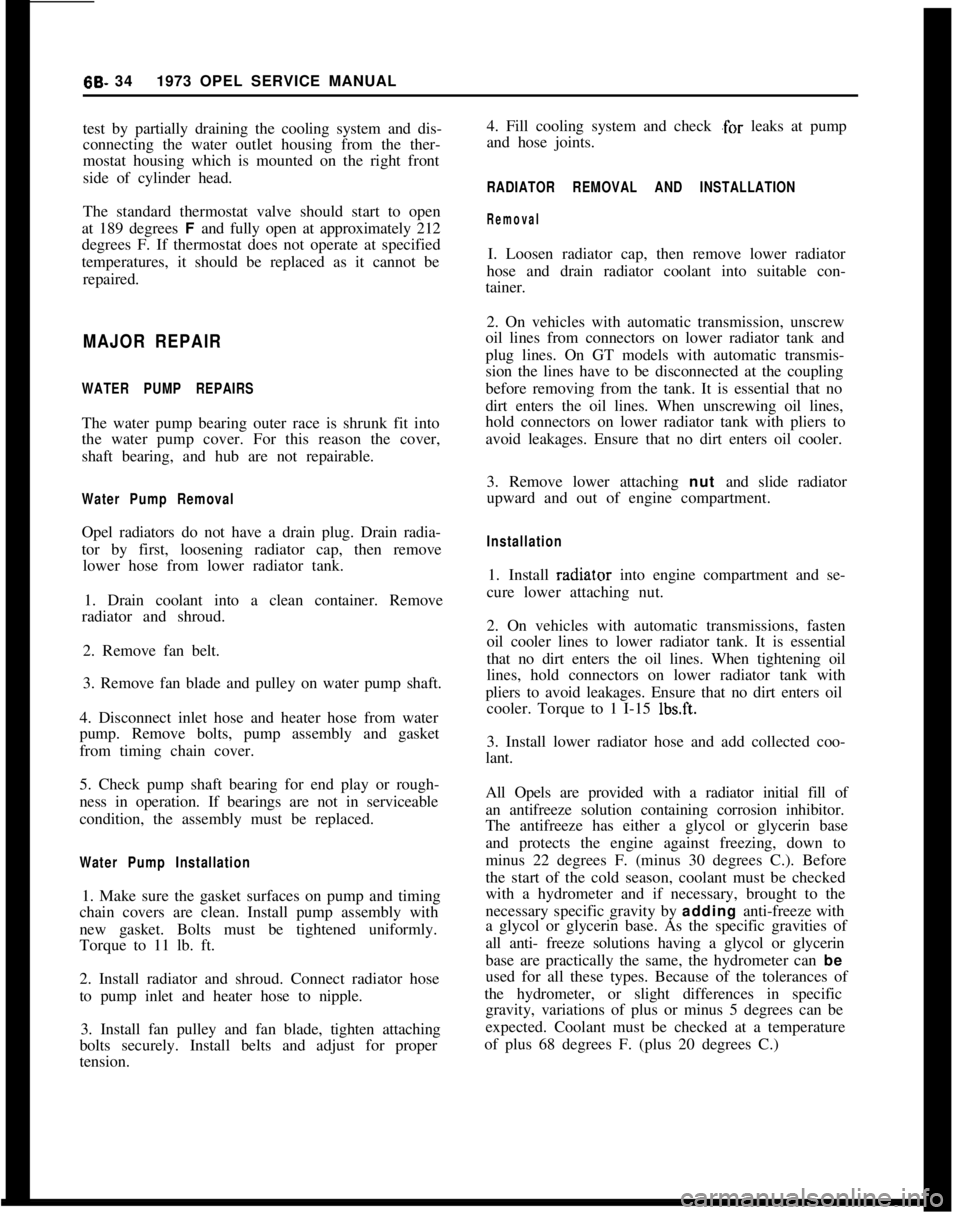
6B- 341973 OPEL SERVICE MANUAL
test by partially draining the cooling system and dis-
connecting the water outlet housing from the ther-
mostat housing which is mounted on the right front
side of cylinder head.
The standard thermostat valve should start to open
at 189 degrees F and fully open at approximately 212
degrees F. If thermostat does not operate at specified
temperatures, it should be replaced as it cannot be
repaired.MAJOR REPAIR
WATER PUMP REPAIRSThe water pump bearing outer race is shrunk fit into
the water pump cover. For this reason the cover,
shaft bearing, and hub are not repairable.
Water Pump RemovalOpel radiators do not have a drain plug. Drain radia-
tor by first, loosening radiator cap, then remove
lower hose from lower radiator tank.
1. Drain coolant into a clean container. Remove
radiator and shroud.
2. Remove fan belt.
3. Remove fan blade and pulley on water pump shaft.
4. Disconnect inlet hose and heater hose from water
pump. Remove bolts, pump assembly and gasket
from timing chain cover.
5. Check pump shaft bearing for end play or rough-
ness in operation. If bearings are not in serviceable
condition, the assembly must be replaced.
Water Pump Installation1. Make sure the gasket surfaces on pump and timing
chain covers are clean. Install pump assembly with
new gasket. Bolts must be tightened uniformly.
Torque to 11 lb. ft.
2. Install radiator and shroud. Connect radiator hose
to pump inlet and heater hose to nipple.
3. Install fan pulley and fan blade, tighten attaching
bolts securely. Install belts and adjust for proper
tension.4. Fill cooling system and check
,for leaks at pump
and hose joints.
RADIATOR REMOVAL AND INSTALLATION
RemovalI. Loosen radiator cap, then remove lower radiator
hose and drain radiator coolant into suitable con-
tainer.
2. On vehicles with automatic transmission, unscrew
oil lines from connectors on lower radiator tank and
plug lines. On GT models with automatic transmis-
sion the lines have to be disconnected at the coupling
before removing from the tank. It is essential that no
dirt enters the oil lines. When unscrewing oil lines,
hold connectors on lower radiator tank with pliers to
avoid leakages. Ensure that no dirt enters oil cooler.
3. Remove lower attaching nut and slide radiator
upward and out of engine compartment.
Installation1. Install radiat,or into engine compartment and se-
cure lower attaching nut.
2. On vehicles with automatic transmissions, fasten
oil cooler lines to lower radiator tank. It is essential
that no dirt enters the oil lines. When tightening oil
lines, hold connectors on lower radiator tank with
pliers to avoid leakages. Ensure that no dirt enters oil
cooler. Torque to 1 I-15
lbs.ft.3. Install lower radiator hose and add collected coo-
lant.
All Opels are provided with a radiator initial fill of
an antifreeze solution containing corrosion inhibitor.
The antifreeze has either a glycol or glycerin base
and protects the engine against freezing, down to
minus 22 degrees F. (minus 30 degrees C.). Before
the start of the cold season, coolant must be checked
with a hydrometer and if necessary, brought to the
necessary specific gravity by adding anti-freeze with
a glycol or glycerin base. As the specific gravities of
all anti- freeze solutions having a glycol or glycerin
base are practically the same, the hydrometer can be
used for all these types. Because of the tolerances of
the hydrometer, or slight differences in specific
gravity, variations of plus or minus 5 degrees can be
expected. Coolant must be checked at a temperature
of plus 68 degrees F. (plus 20 degrees C.)
Page 326 of 625
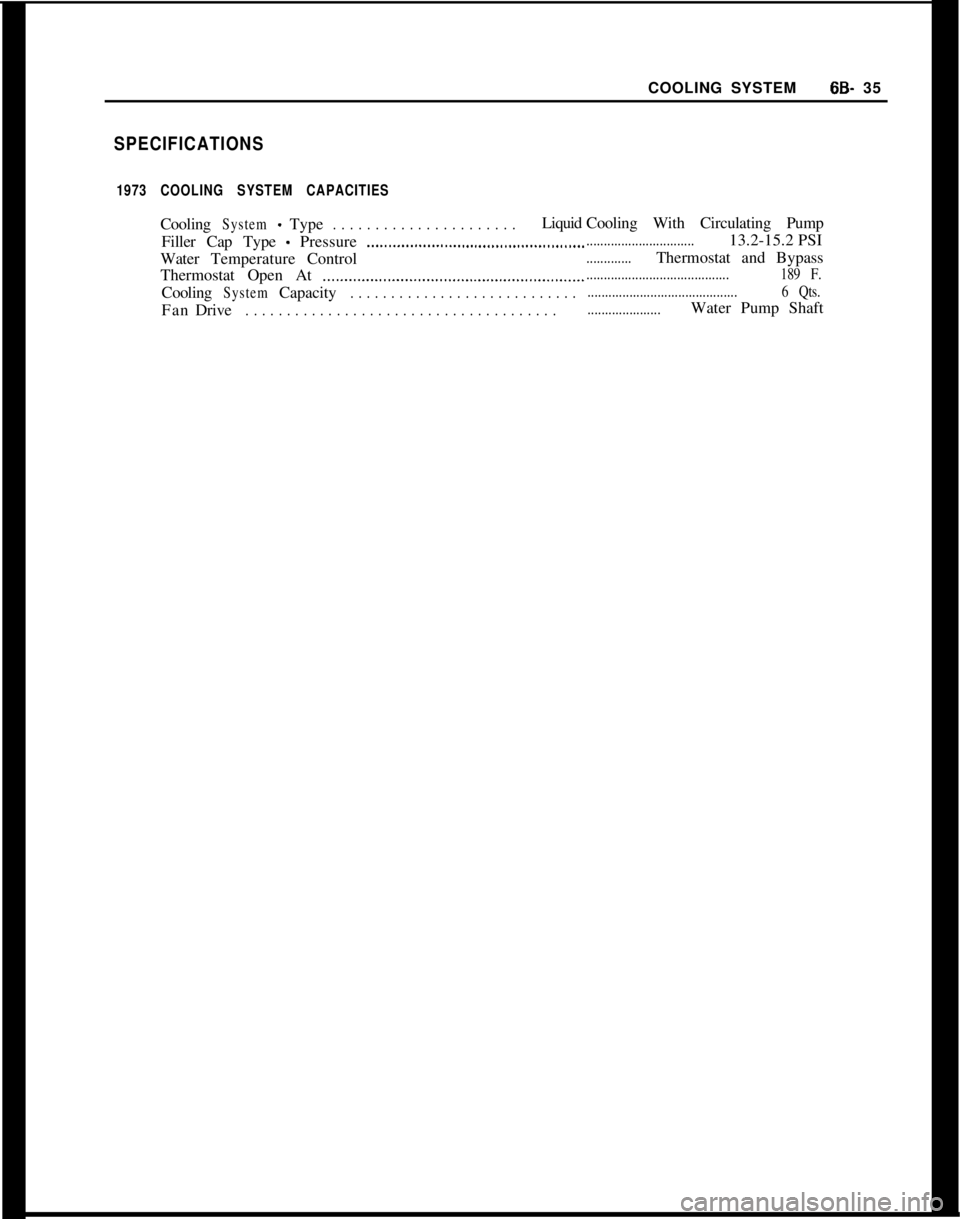
COOLING SYSTEM6B- 35SPECIFICATIONS
1973 COOLING SYSTEM CAPACITIESCooling
System-Type. . . . . . . . . . . . . . . . . . . . . .Liquid
Filler Cap Type
- Pressure _.._..__........_.._.,,.,,..,,.,,..,.,,..,,,.,,,..,WaterTemperatureControl
Thermostat Open At
__..__.,_..,.,,,__,,..,,,..,,..,,.,,..,,.,.,,,.,,,..,,,.,,,..Cooling
SystemCapacity. . . . . . . . . . . . . . . . . . . . . . . . . . . .FanDrive
. . . . . . . . . . . . . . . . . . . . . . . . . . . . . . . . . . . . . .Cooling With Circulating Pump
...............................13.2-15.2 PSI
.............Thermostat and Bypass
.........................................189 F.
...........................................6 Qts.
.....................Water Pump Shaft
Page 327 of 625
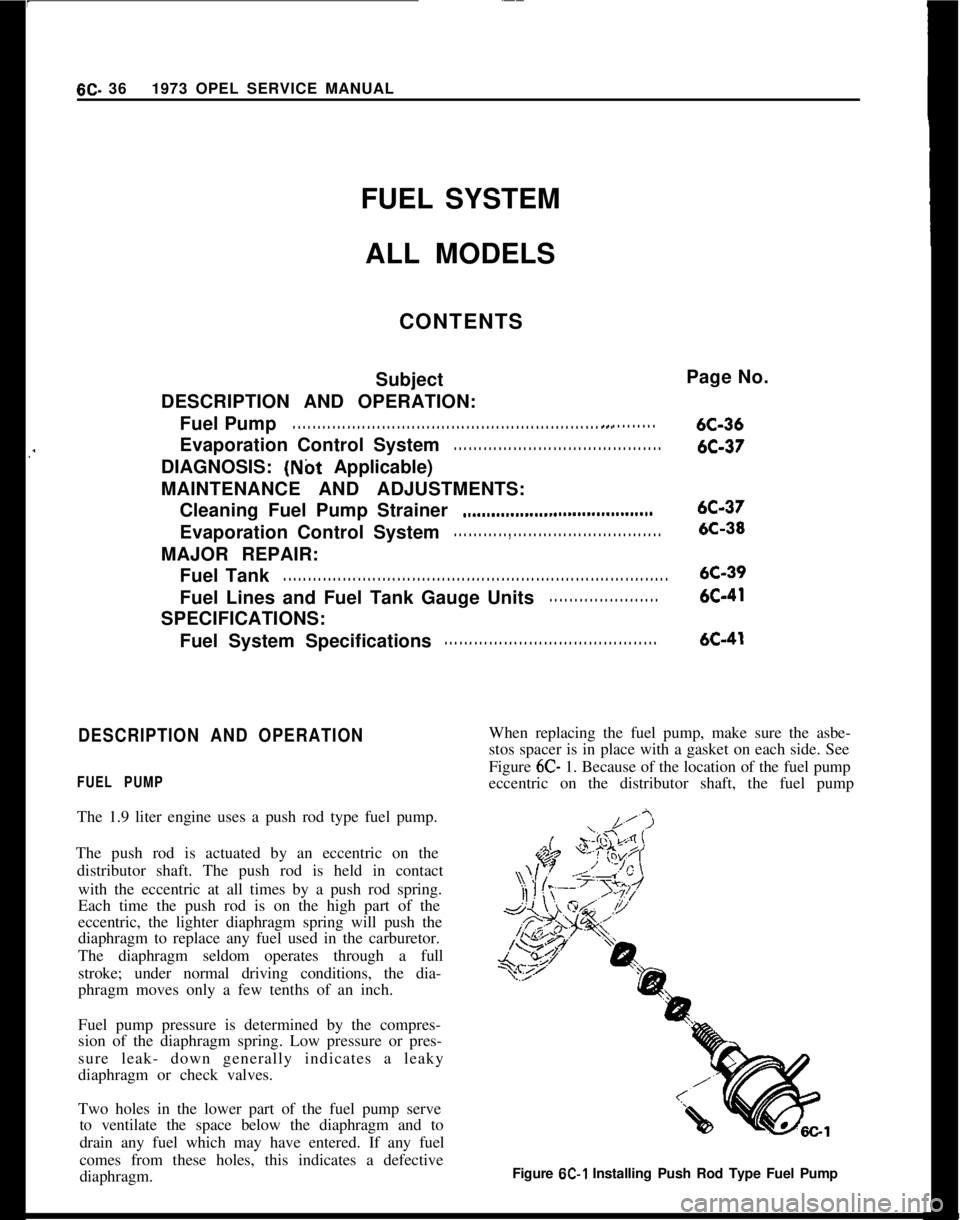
6C- 361973 OPEL SERVICE MANUAL
FUEL SYSTEM
ALL MODELS
CONTENTS
Subject
DESCRIPTION AND OPERATION:
Fuel Pump. . . . . . . . . . . . . . . . . . . . . . . . . . . . . . . . . . . . . . . . . . . . . . . . . . . . . . . . . . . . . . . . .. . . . . . . . . . .Evaporation Control System
. . . . . . . . . . . . . . . . . . . . . . . . . . . . . . . . . . . . . . . . . .DIAGNOSIS:
(Not Applicable)
MAINTENANCE AND ADJUSTMENTS:
Cleaning Fuel Pump Strainer.,....................................
*.Evaporation Control System
. . . . . . . . . . . , . . . . . . . . . . . . . . . . . . . . . . . . . . . . . .MAJOR REPAIR:
Fuel Tank
. . . . . . . . . . . . . . . . . . . . . . . . . . . . . . . . . . . . . . . . . . . . . . . . . . . . . . . . . . . . . . . . . . . . . . . . . . . . . .Fuel Lines and Fuel Tank Gauge Units
. . . . . . . . . . . . . . . . . . . . . .SPECIFICATIONS:
Fuel System Specifications
. . . . . . . . . . . . . . . . . . . . . . . . . . . . . . . . . . . . . . . . . . .Page No.6C-366C-376C-376C-386C-396C-416C-41
DESCRIPTION AND OPERATION
FUEL PUMPThe 1.9 liter engine uses a push rod type fuel pump.
The push rod is actuated by an eccentric on the
distributor shaft. The push rod is held in contact
with the eccentric at all times by a push rod spring.
Each time the push rod is on the high part of the
eccentric, the lighter diaphragm spring will push the
diaphragm to replace any fuel used in the carburetor.
The diaphragm seldom operates through a full
stroke; under normal driving conditions, the dia-
phragm moves only a few tenths of an inch.
Fuel pump pressure is determined by the compres-
sion of the diaphragm spring. Low pressure or pres-
sure leak- down generally indicates a leaky
diaphragm or check valves.
Two holes in the lower part of the fuel pump serve
to ventilate the space below the diaphragm and to
drain any fuel which may have entered. If any fuel
comes from these holes, this indicates a defective
diaphragm.When replacing the fuel pump, make sure the asbe-
stos spacer is in place with a gasket on each side. See
Figure 6C- 1. Because of the location of the fuel pump
eccentric on the distributor shaft, the fuel pump
Figure
6C-1 Installing Push Rod Type Fuel Pump
Page 328 of 625
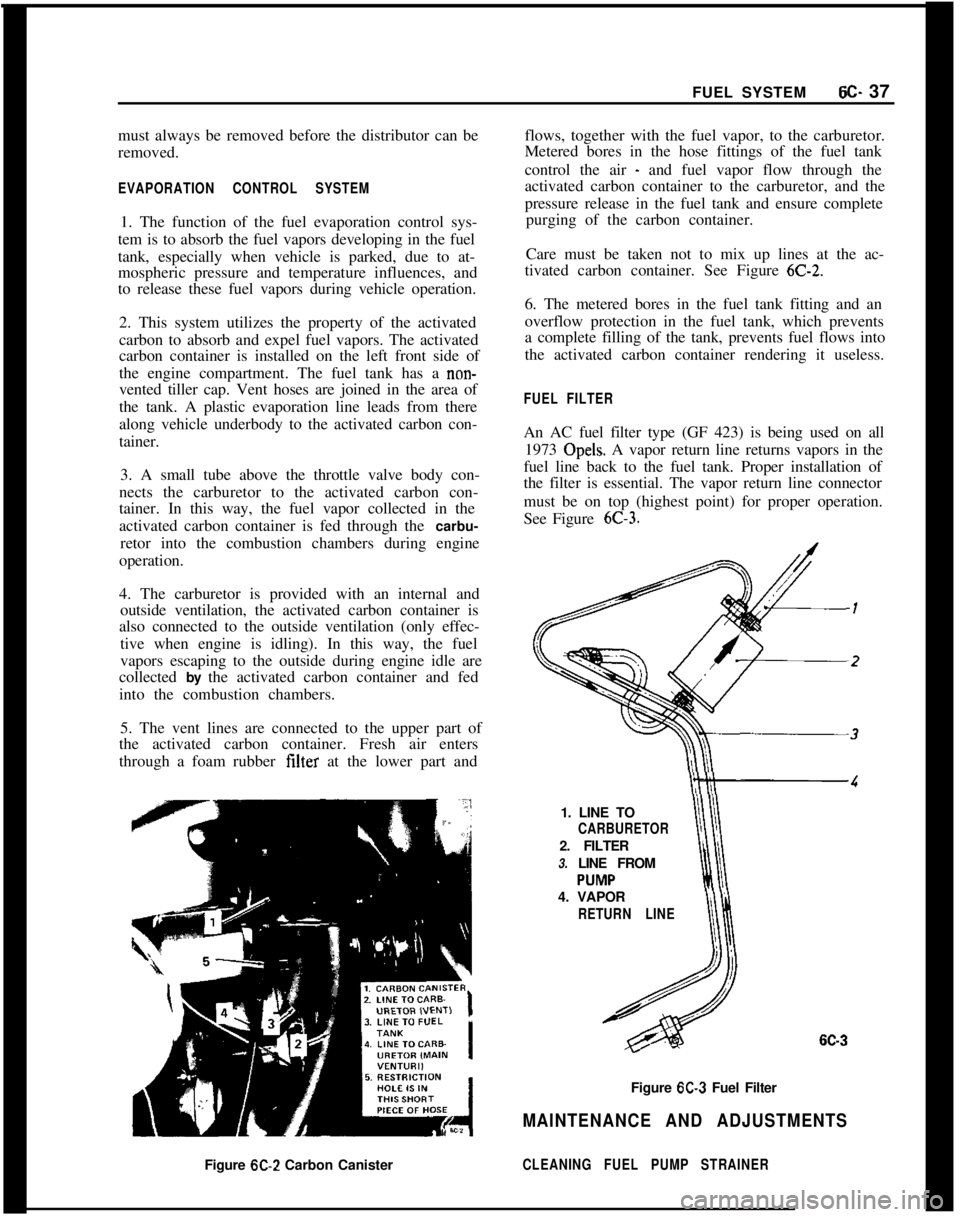
FUEL SYSTEMSC- 37
must always be removed before the distributor can be
removed.
EVAPORATION CONTROL SYSTEM1. The function of the fuel evaporation control sys-
tem is to absorb the fuel vapors developing in the fuel
tank, especially when vehicle is parked, due to at-
mospheric pressure and temperature influences, and
to release these fuel vapors during vehicle operation.
2. This system utilizes the property of the activated
carbon to absorb and expel fuel vapors. The activated
carbon container is installed on the left front side of
the engine compartment. The fuel tank has a
non-vented tiller cap. Vent hoses are joined in the area of
the tank. A plastic evaporation line leads from there
along vehicle underbody to the activated carbon con-
tainer.
3. A small tube above the throttle valve body con-
nects the carburetor to the activated carbon con-
tainer. In this way, the fuel vapor collected in the
activated carbon container is fed through the carbu-
retor into the combustion chambers during engine
operation.
4. The carburetor is provided with an internal and
outside ventilation, the activated carbon container is
also connected to the outside ventilation (only effec-
tive when engine is idling). In this way, the fuel
vapors escaping to the outside during engine idle are
collected by the activated carbon container and fed
into the combustion chambers.
5. The vent lines are connected to the upper part of
the activated carbon container. Fresh air enters
through a foam rubber filter at the lower part andflows, together with the fuel vapor, to the carburetor.
Metered bores in the hose fittings of the fuel tank
control the air
- and fuel vapor flow through the
activated carbon container to the carburetor, and the
pressure release in the fuel tank and ensure complete
purging of the carbon container.
Care must be taken not to mix up lines at the ac-
tivated carbon container. See Figure
6C-2.6. The metered bores in the fuel tank fitting and an
overflow protection in the fuel tank, which prevents
a complete filling of the tank, prevents fuel flows into
the activated carbon container rendering it useless.
FUEL FILTERAn AC fuel filter type (GF 423) is being used on all
1973 Opels. A vapor return line returns vapors in the
fuel line back to the fuel tank. Proper installation of
the filter is essential. The vapor return line connector
must be on top (highest point) for proper operation.
See Figure
6C-3.1. LINE TO
CARBURETOR2. FILTER
3. LINE FROM
4. VAPOR
RETURN LINE
6C-3Figure
6C-3 Fuel Filter
MAINTENANCE AND ADJUSTMENTSFigure
6C-2 Carbon CanisterCLEANING FUEL PUMP STRAINER
Page 329 of 625
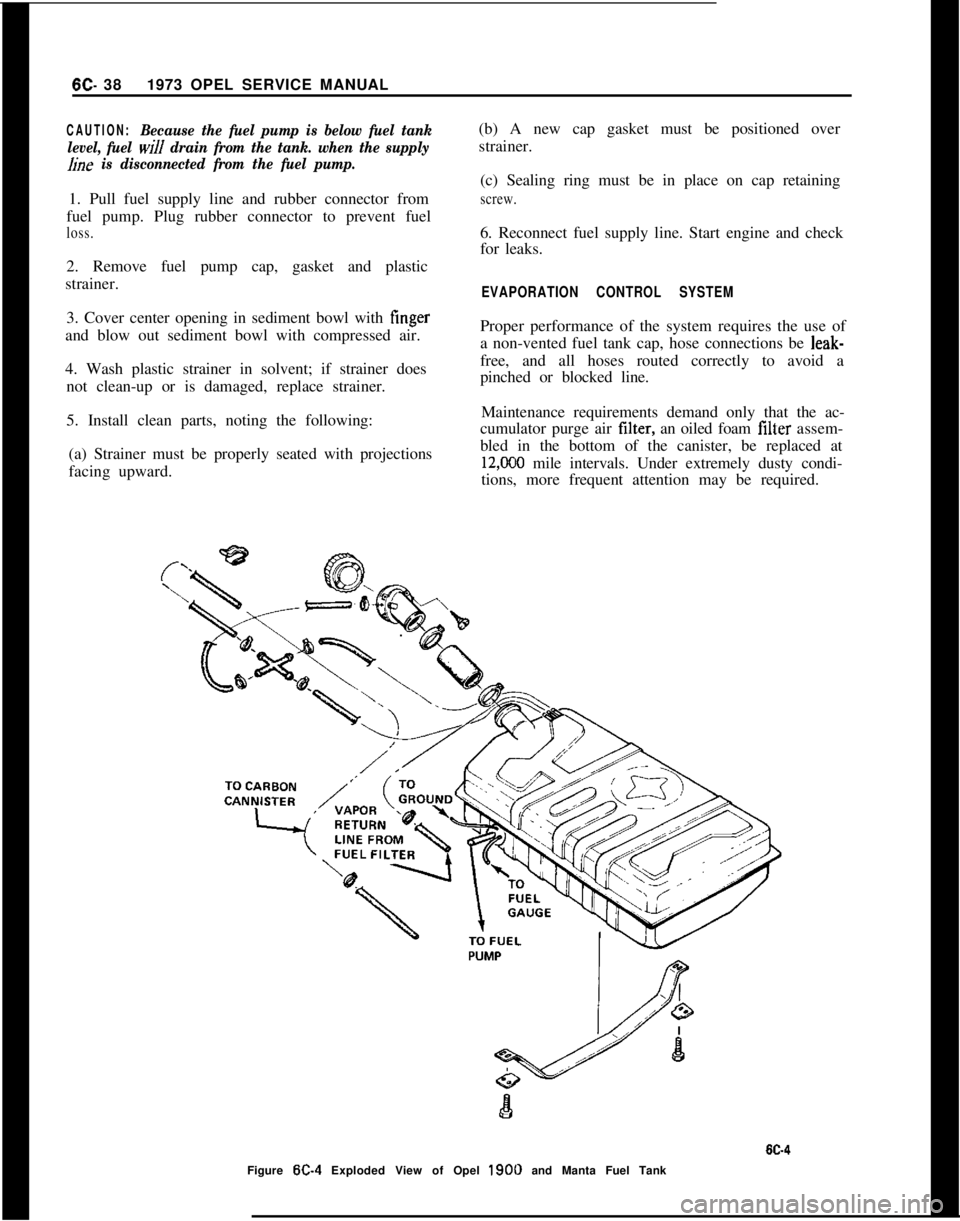
6C- 381973 OPEL SERVICE MANUALCAUTION:Because the fuel pump is below fuel tank
level, fuel
will drain from the tank. when the supply
hne is disconnected from the fuel pump.1. Pull fuel supply line and rubber connector from
fuel pump. Plug rubber connector to prevent fuel
loss.2. Remove fuel pump cap, gasket and plastic
strainer.
3. Cover center opening in sediment bowl with finger
and blow out sediment bowl with compressed air.
4. Wash plastic strainer in solvent; if strainer does
not clean-up or is damaged, replace strainer.
5. Install clean parts, noting the following:
(a) Strainer must be properly seated with projections
facing upward.(b) A new cap gasket must be positioned over
strainer.
(c) Sealing ring must be in place on cap retaining
screw.6. Reconnect fuel supply line. Start engine and check
for leaks.
EVAPORATION CONTROL SYSTEMProper performance of the system requires the use of
a non-vented fuel tank cap, hose connections be leak-
free, and all hoses routed correctly to avoid a
pinched or blocked line.
Maintenance requirements demand only that the ac-
cumulator purge air tilter, an oiled foam filter assem-
bled in the bottom of the canister, be replaced at
12,CKO mile intervals. Under extremely dusty condi-
tions, more frequent attention may be required.
Figure
W-4 Exploded View of Opel 1900 and Manta Fuel Tank
Page 330 of 625
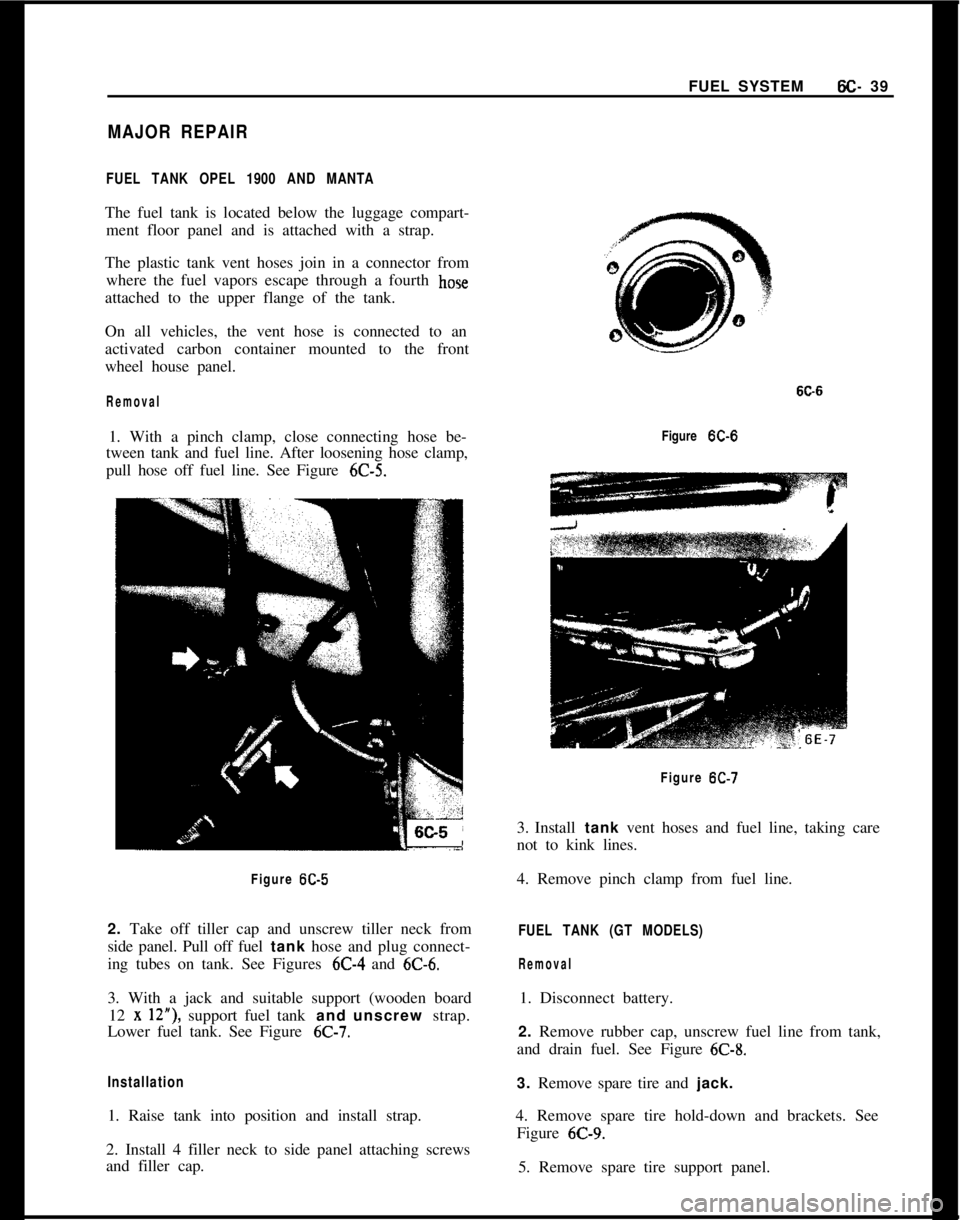
FUEL SYSTEMSC- 39
MAJOR REPAIR
FUEL TANK OPEL 1900 AND MANTAThe fuel tank is located below the luggage compart-
ment floor panel and is attached with a strap.
The plastic tank vent hoses join in a connector from
where the fuel vapors escape through a fourth
ho%attached to the upper flange of the tank.
On all vehicles, the vent hose is connected to an
activated carbon container mounted to the front
wheel house panel.
Removal1. With a pinch clamp, close connecting hose be-
tween tank and fuel line. After loosening hose clamp,
pull hose off fuel line. See Figure
6C-5.Figure
6C-52. Take off tiller cap and unscrew tiller neck from
side panel. Pull off fuel tank hose and plug connect-
ing tubes on tank. See Figures 6C-4 and
6C-6.3. With a jack and suitable support (wooden board
12
x 12”), support fuel tank and unscrew strap.
Lower fuel tank. See Figure
6C-7.
Installation1. Raise tank into position and install strap.
2. Install 4 filler neck to side panel attaching screws
and filler cap.Figure
K-6Figure
6C-73. Install tank vent hoses and fuel line, taking care
not to kink lines.
4. Remove pinch clamp from fuel line.
FUEL TANK (GT MODELS)
Removal1. Disconnect battery.
2. Remove rubber cap, unscrew fuel line from tank,
and drain fuel. See Figure
6C-8.3. Remove spare tire and jack.
4. Remove spare tire hold-down and brackets. See
Figure
6C-9.5. Remove spare tire support panel.