OPEL GT-R 1973 Service Manual
Manufacturer: OPEL, Model Year: 1973, Model line: GT-R, Model: OPEL GT-R 1973Pages: 625, PDF Size: 17.22 MB
Page 311 of 625
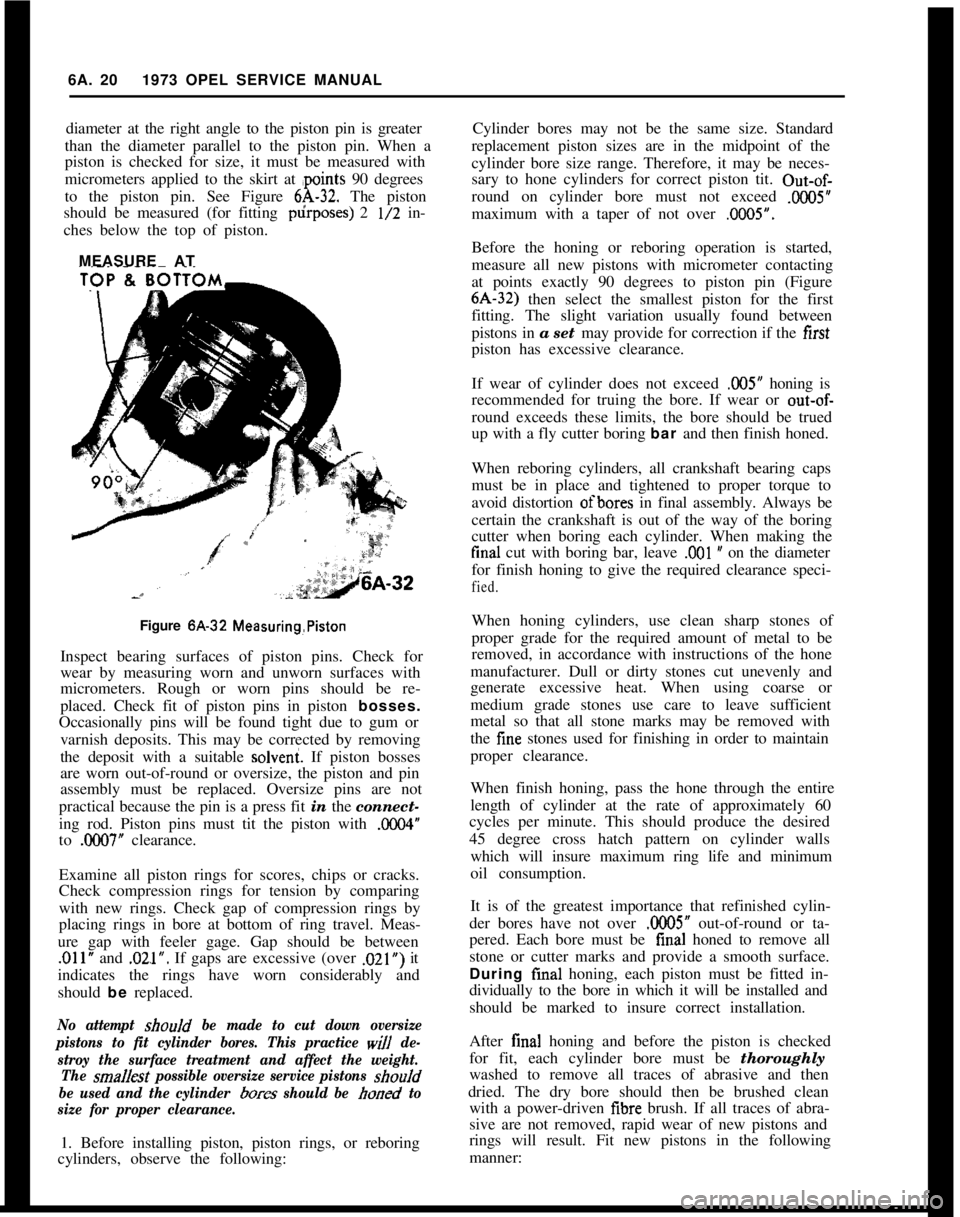
6A. 201973 OPEL SERVICE MANUAL
diameter at the right angle to the piston pin is greater
than the diameter parallel to the piston pin. When a
piston is checked for size, it must be measured with
micrometers applied to the skirt at ,points 90 degrees
to the piston pin. See Figure
6A-32. The piston
should be measured (for fitting p&poses) 2
l/2 in-
ches below the top of piston.
MEASURE AT
Figure 6A-32
Measuring,PistonInspect bearing surfaces of piston pins. Check for
wear by measuring worn and unworn surfaces with
micrometers. Rough or worn pins should be re-
placed. Check fit of piston pins in piston bosses.
Occasionally pins will be found tight due to gum or
varnish deposits. This may be corrected by removing
the deposit with a suitable solveni. If piston bosses
are worn out-of-round or oversize, the piston and pin
assembly must be replaced. Oversize pins are not
practical because the pin is a press fit in the connect-
ing rod. Piston pins must tit the piston with
0X4”to
.OCHl7” clearance.
Examine all piston rings for scores, chips or cracks.
Check compression rings for tension by comparing
with new rings. Check gap of compression rings by
placing rings in bore at bottom of ring travel. Meas-
ure gap with feeler gage. Gap should be between
,011” and .02.1”. If gaps are excessive (over .021”) it
indicates the rings have worn considerably and
should be replaced.
No attempt should be made to cut down oversize
pistons to fit cylinder bores. This practice
will de-
stroy the surface treatment and affect the weight.
The
sma/Jest possible oversize service pistons shouId
be used and the cylinder
bores should be honed to
size for proper clearance.1. Before installing piston, piston rings, or reboring
cylinders, observe the following:Cylinder bores may not be the same size. Standard
replacement piston sizes are in the midpoint of the
cylinder bore size range. Therefore, it may be neces-
sary to hone cylinders for correct piston tit. Out-of-
round on cylinder bore must not exceed
.ooO5”maximum with a taper of not over
.OilO5”.Before the honing or reboring operation is started,
measure all new pistons with micrometer contacting
at points exactly 90 degrees to piston pin (Figure6A-32) then select the smallest piston for the first
fitting. The slight variation usually found between
pistons in a set may provide for correction if the first
piston has excessive clearance.
If wear of cylinder does not exceed
.005” honing is
recommended for truing the bore. If wear or
out-of-round exceeds these limits, the bore should be trued
up with a fly cutter boring bar and then finish honed.
When reboring cylinders, all crankshaft bearing caps
must be in place and tightened to proper torque to
avoid distortion ofbores in final assembly. Always be
certain the crankshaft is out of the way of the boring
cutter when boring each cylinder. When making thefinal cut with boring bar, leave
,001 w on the diameter
for finish honing to give the required clearance speci-
fied.When honing cylinders, use clean sharp stones of
proper grade for the required amount of metal to be
removed, in accordance with instructions of the hone
manufacturer. Dull or dirty stones cut unevenly and
generate excessive heat. When using coarse or
medium grade stones use care to leave sufficient
metal so that all stone marks may be removed with
the fine stones used for finishing in order to maintain
proper clearance.
When finish honing, pass the hone through the entire
length of cylinder at the rate of approximately 60
cycles per minute. This should produce the desired
45 degree cross hatch pattern on cylinder walls
which will insure maximum ring life and minimum
oil consumption.
It is of the greatest importance that refinished cylin-
der bores have not over
.0005” out-of-round or ta-
pered. Each bore must be final honed to remove all
stone or cutter marks and provide a smooth surface.
During final honing, each piston must be fitted in-
dividually to the bore in which it will be installed and
should be marked to insure correct installation.
After final honing and before the piston is checked
for fit, each cylinder bore must be thoroughly
washed to remove all traces of abrasive and then
dried. The dry bore should then be brushed clean
with a power-driven iibre brush. If all traces of abra-
sive are not removed, rapid wear of new pistons and
rings will result. Fit new pistons in the following
manner:
Page 312 of 625
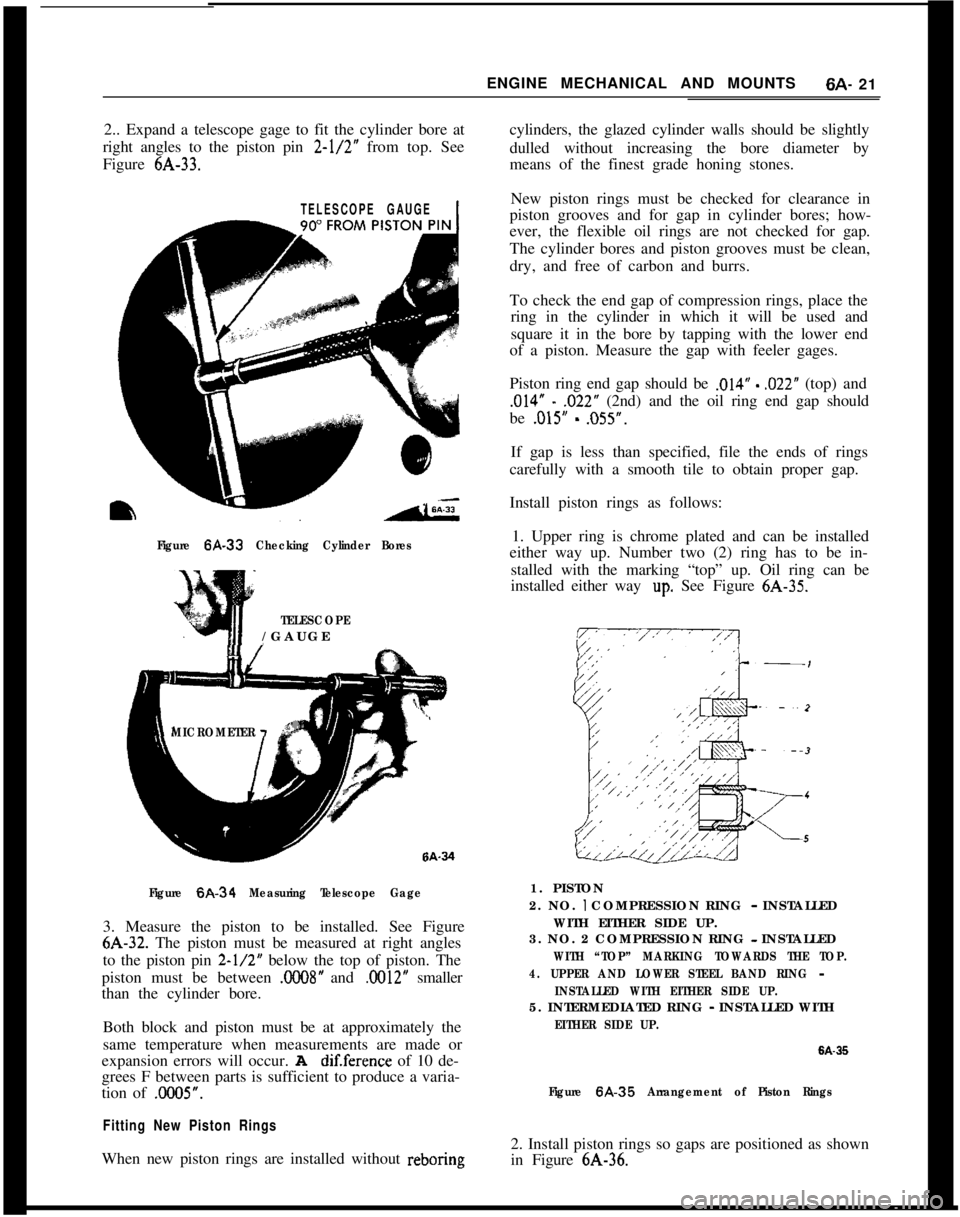
ENGINE MECHANICAL AND MOUNTS6A- 21
2.. Expand a telescope gage to fit the cylinder bore at
right angles to the piston pin 2-l/2” from top. See
Figure 6A-33.cylinders, the glazed cylinder walls should be slightly
dulled without increasing the bore diameter by
means of the finest grade honing stones.
TELESCOPE GAUGE1
Figure 6A-33 Checking Cylinder Bores
TELESCOPE/GAUGE
MICROMETER
Figure
6A-34 Measuring Telescope Gage3. Measure the piston to be installed. See Figure6A-32. The piston must be measured at right angles
to the piston pin
2-l/2” below the top of piston. The
piston must be between
.C008” and .0012” smaller
than the cylinder bore.
Both block and piston must be at approximately the
same temperature when measurements are made or
expansion errors will occur. A
dif.ference of 10 de-
grees F between parts is sufficient to produce a varia-
tion of .0005”.
Fitting New Piston RingsWhen new piston rings are installed without reboringNew piston rings must be checked for clearance in
piston grooves and for gap in cylinder bores; how-
ever, the flexible oil rings are not checked for gap.
The cylinder bores and piston grooves must be clean,
dry, and free of carbon and burrs.
To check the end gap of compression rings, place the
ring in the cylinder in which it will be used and
square it in the bore by tapping with the lower end
of a piston. Measure the gap with feeler gages.
Piston ring end gap should be
,014” - ,022” (top) and
,014” - ,022” (2nd) and the oil ring end gap should
be
.015” - ,055”.
If gap is less than specified, file the ends of rings
carefully with a smooth tile to obtain proper gap.
Install piston rings as follows:
1. Upper ring is chrome plated and can be installed
either way up. Number two (2) ring has to be in-
stalled with the marking “top” up. Oil ring can be
installed either way
up. See Figure 6A-35.
1. PISTON
2. NO.
I COMPRESSION RING - INSTALLED
WITH EITHER SIDE UP.
3. NO. 2 COMPRESSION RING - INSTALLED
WITH “TOP” MARKING TOWARDS THE TOP.
4. UPPER AND LOWER STEEL BAND RING
-
INSTALLED WITH EITHER SIDE UP.5. INTERMEDIATED RING
- INSTALLED WITH
EITHER SIDE UP.
6A-35
Figure 6A.35 Arrangement of Piston Rings2. Install piston rings so gaps are positioned as shown
in Figure 6A-36.
Page 313 of 625
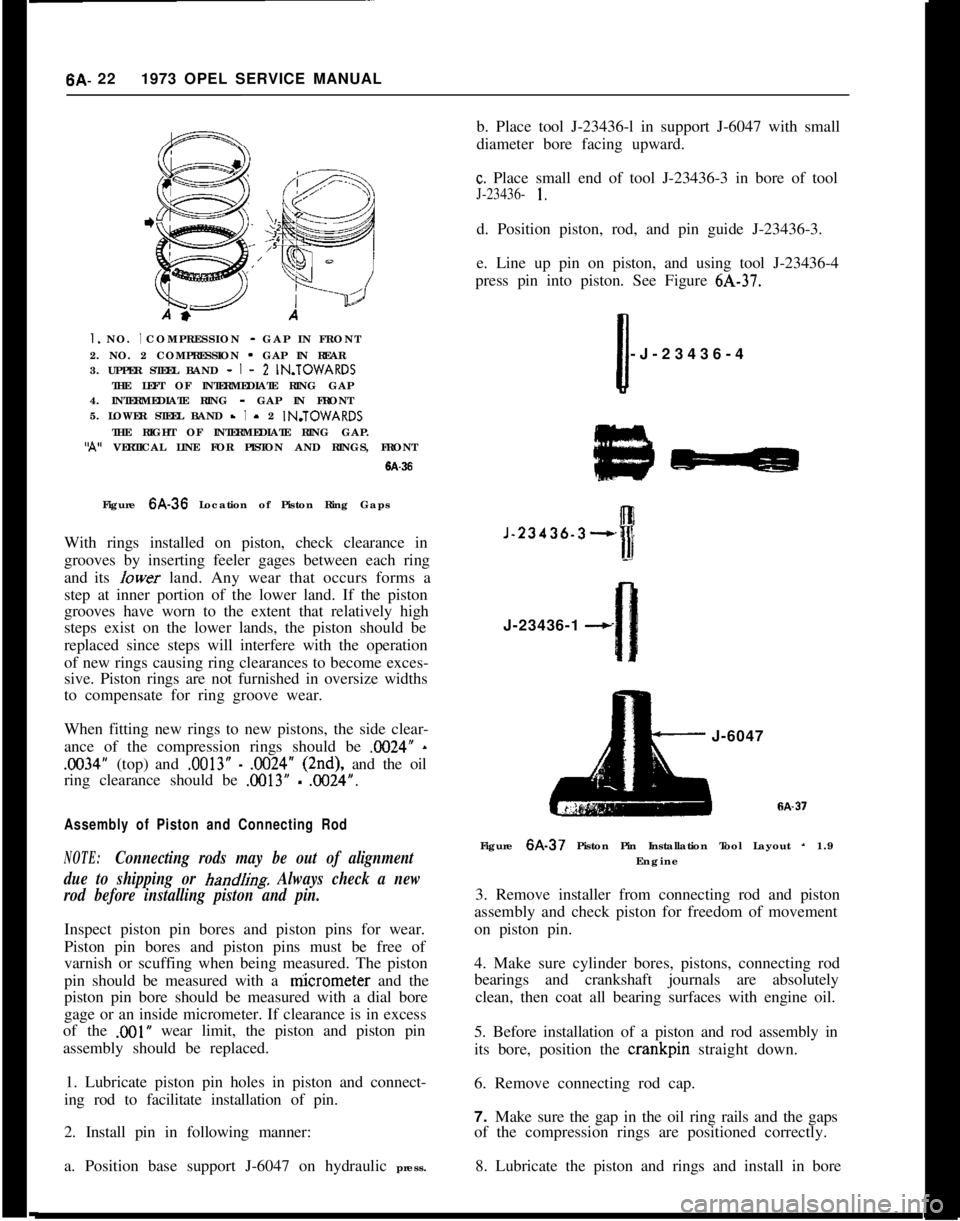
6A- 221973 OPEL SERVICE MANUALI. NO. I COMPRESSION - GAP IN FRONT
2. NO. 2 COMPRESSION - GAP IN REAR
3. UPPER STEEL BAND -
I - 2 IN.TOWARDS
THE LEFT OF INTERMEDIATE RING GAP
4. INTERMEDIATE RING - GAP IN FRONT
5. LOWER STEEL BAND -
I - 2 IN.TOWARDS
THE RIGHT OF INTERMEDIATE RING GAP.‘A” VERTICAL LINE FOR PISTON AND RINGS, FRONT
6A-36Figure 6A-36 Location of Piston Ring Gaps
With rings installed on piston, check clearance in
grooves by inserting feeler gages between each ring
and its Iower land. Any wear that occurs forms a
step at inner portion of the lower land. If the piston
grooves have worn to the extent that relatively high
steps exist on the lower lands, the piston should be
replaced since steps will interfere with the operation
of new rings causing ring clearances to become exces-
sive. Piston rings are not furnished in oversize widths
to compensate for ring groove wear.
When fitting new rings to new pistons, the side clear-
ance of the compression rings should be X024”
-
.1X34” (top) and .0013” - .OO24” (2nd), and the oil
ring clearance should be
.OO13” - .0024”.
Assembly of Piston and Connecting Rod
NOTE:Connecting rods may be out of alignment
due to shipping or
hand/i& Always check a new
rod before installing piston and pin.Inspect piston pin bores and piston pins for wear.
Piston pin bores and piston pins must be free of
varnish or scuffing when being measured. The piston
pin should be measured with a niicrometer and the
piston pin bore should be measured with a dial bore
gage or an inside micrometer. If clearance is in excess
of the
,001” wear limit, the piston and piston pin
assembly should be replaced.
1. Lubricate piston pin holes in piston and connect-
ing rod to facilitate installation of pin.
2. Install pin in following manner:
a. Position base support J-6047 on hydraulic press.b. Place tool J-23436-l in support J-6047 with small
diameter bore facing upward.
c. Place small end of tool J-23436-3 in bore of tool
J-23436- 1.d. Position piston, rod, and pin guide J-23436-3.
e. Line up pin on piston, and using tool J-23436-4
press pin into piston. See Figure 6A-37.
Ii-J-23436-4
J-23436-3--,J-23436-1
--cJ-6047
Figure 6A-37 Piston Pin Installation Tool Layout
- 1.9
Engine
3. Remove installer from connecting rod and piston
assembly and check piston for freedom of movement
on piston pin.
4. Make sure cylinder bores, pistons, connecting rod
bearings and crankshaft journals are absolutely
clean, then coat all bearing surfaces with engine oil.
5. Before installation of a piston and rod assembly in
its bore, position the crankpin straight down.
6. Remove connecting rod cap.
7. Make sure the gap in the oil ring rails and the gaps
of the compression rings are positioned correctly.
8. Lubricate the piston and rings and install in bore
Page 314 of 625
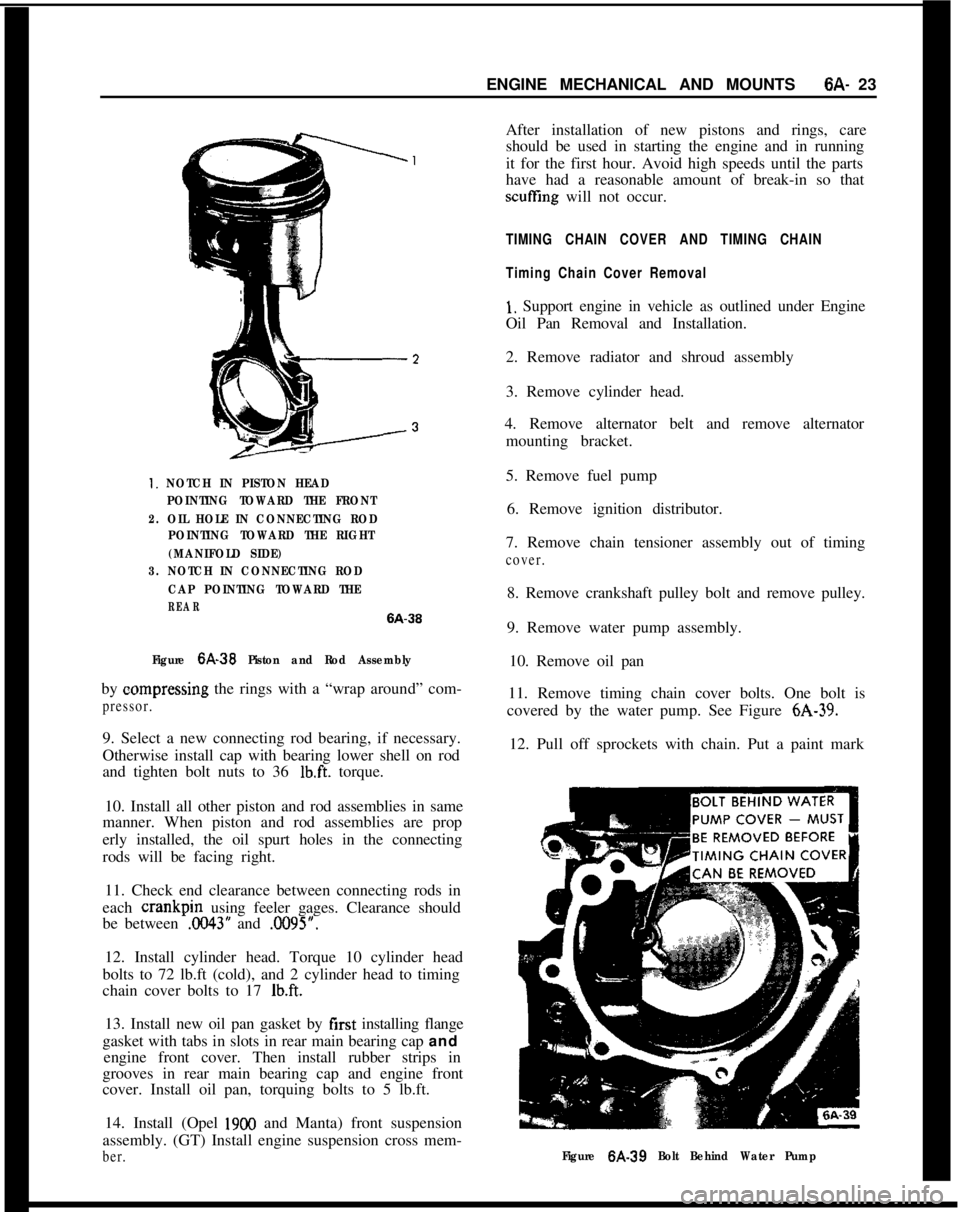
ENGINE MECHANICAL AND MOUNTS6A- 231. NOTCH IN PISTON HEAD
POINTING TOWARD THE FRONT
2. OIL HOLE IN CONNECTING ROD
POINTING TOWARD THE RIGHT
(MANIFOLD SIDE)
3. NOTCH IN CONNECTING ROD
CAP POINTING TOWARD THE
REAR6A-36
Figure
6A-39 Piston and Rod Assemblyby oompressing the rings with a “wrap around” com-
pressor.9. Select a new connecting rod bearing, if necessary.
Otherwise install cap with bearing lower shell on rod
and tighten bolt nuts to 36
lb.ft. torque.
10. Install all other piston and rod assemblies in same
manner. When piston and rod assemblies are prop
erly installed, the oil spurt holes in the connecting
rods will be facing right.
11. Check end clearance between connecting rods in
each crankpin using feeler gages. Clearance should
be between
.0043” and .0095”.
12. Install cylinder head. Torque 10 cylinder head
bolts to 72 lb.ft (cold), and 2 cylinder head to timing
chain cover bolts to 17
lb.ft.13. Install new oil pan gasket by first installing flange
gasket with tabs in slots in rear main bearing cap and
engine front cover. Then install rubber strips in
grooves in rear main bearing cap and engine front
cover. Install oil pan, torquing bolts to 5 lb.ft.
14. Install (Opel
1900 and Manta) front suspension
assembly. (GT) Install engine suspension cross mem-
ber.After installation of new pistons and rings, care
should be used in starting the engine and in running
it for the first hour. Avoid high speeds until the parts
have had a reasonable amount of break-in so that
scuffling will not occur.
TIMING CHAIN COVER AND TIMING CHAIN
Timing Chain Cover Removal
1, Support engine in vehicle as outlined under Engine
Oil Pan Removal and Installation.
2. Remove radiator and shroud assembly
3. Remove cylinder head.
4. Remove alternator belt and remove alternator
mounting bracket.
5. Remove fuel pump
6. Remove ignition distributor.
7. Remove chain tensioner assembly out of timing
cover.8. Remove crankshaft pulley bolt and remove pulley.
9. Remove water pump assembly.
10. Remove oil pan
11. Remove timing chain cover bolts. One bolt is
covered by the water pump. See Figure 6A-39.
12. Pull off sprockets with chain. Put a paint mark
Figure 6A-39 Bolt Behind Water Pump
Page 315 of 625
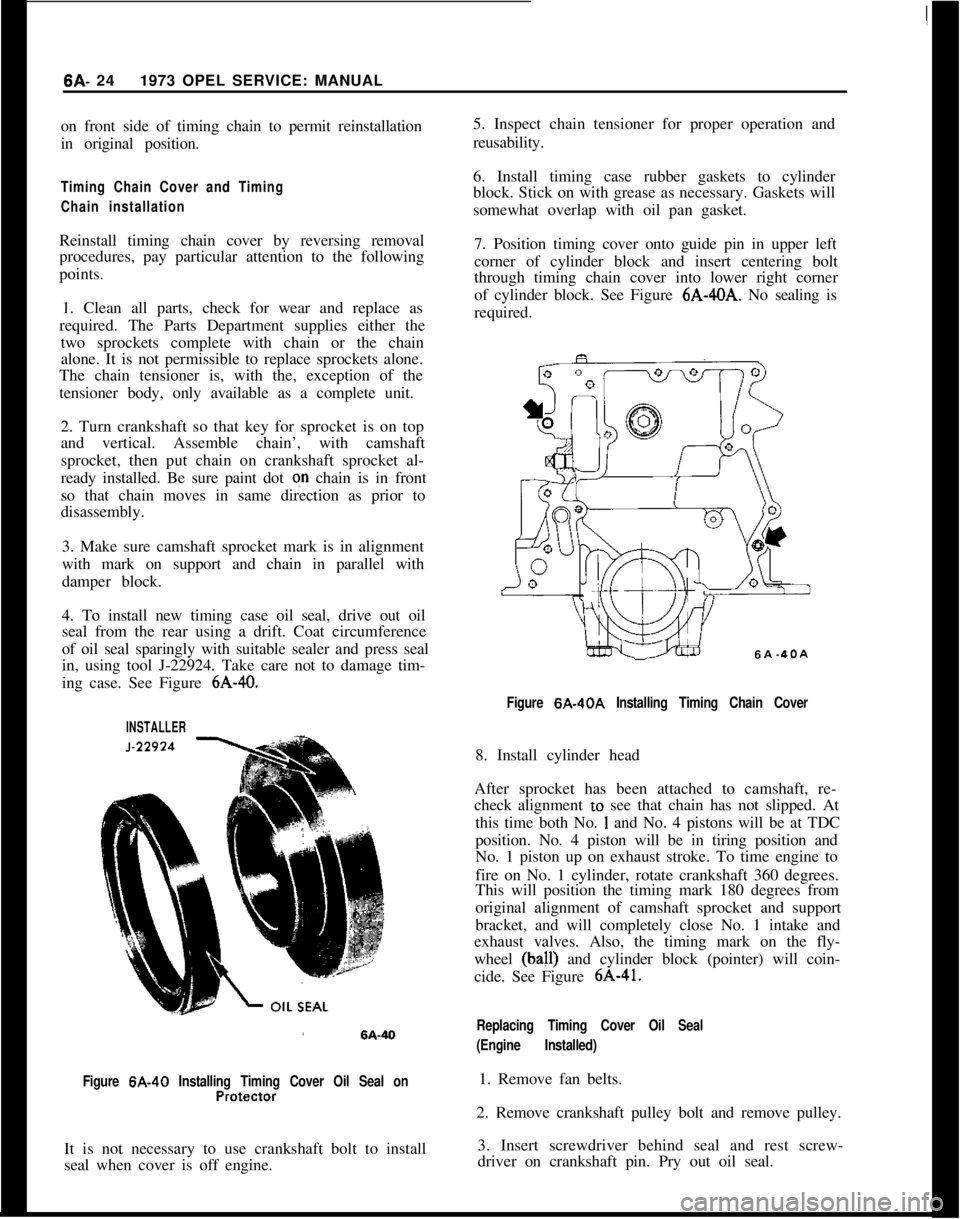
6A- 24 1973 OPEL SERVICE: MANUAL
on front side of timing chain to permit reinstallation
in original position.
Timing Chain Cover and Timing
Chain installation
Reinstall timing chain cover by reversing removal
procedures, pay particular attention to the following
points.
1. Clean all parts, check for wear and replace as
required. The Parts Department supplies either the two sprockets complete with chain or the chain
alone. It is not permissible to replace sprockets alone.
The chain tensioner is, with the, exception of the
tensioner body, only available as a complete unit.
2. Turn crankshaft so that key for sprocket is on top
and vertical. Assemble chain’, with camshaft
sprocket, then put chain on crankshaft sprocket al-
ready installed. Be sure paint dot
on chain is in front
so that chain moves in same direction as prior to
disassembly.
3. Make sure camshaft sprocket mark is in alignment
with mark on support and chain in parallel with
damper block.
4. To install new timing case oil seal, drive out oil
seal from the rear using a drift. Coat circumference
of oil seal sparingly with suitable sealer and press seal
in, using tool J-22924. Take care not to damage tim-
ing case. See Figure
6A-40. 5. Inspect chain tensioner for proper operation and
reusability.
6. Install timing case rubber gaskets to cylinder
block. Stick on with grease as necessary. Gaskets will
somewhat overlap with oil pan gasket.
7. Position timing cover onto guide pin in upper left
corner of cylinder block and insert centering bolt
through timing chain cover into lower right corner
of cylinder block. See Figure
6A-40A. No sealing is
required.
SA-40.4
Figure 6A-40A Installing Timing Chain Cover
INSTALLER
Figure 6A-40 Installing Timing Cover Oil Seal onProtector
It is not necessary to use crankshaft bolt to install
seal when cover is off engine. 8. Install cylinder head
After sprocket has been attached to camshaft, re-
check alignment
LO see that chain has not slipped. At
this time both No.
1 and No. 4 pistons will be at TDC
position. No. 4 piston will be in tiring position and
No. 1 piston up on exhaust stroke. To time engine to
fire on No. 1 cylinder, rotate crankshaft 360 degrees.
This will position the timing mark 180 degrees from
original alignment of camshaft sprocket and support
bracket, and will completely close No. 1 intake and
exhaust valves. Also, the timing mark on the fly-
wheel
(ball) and cylinder block (pointer) will coin-
cide. See Figure
6A-41.
Replacing Timing Cover Oil Seal
(Engine Installed)
1. Remove fan belts.
2. Remove crankshaft pulley bolt and remove pulley. 3. Insert screwdriver behind seal and rest screw-
driver on crankshaft pin. Pry out oil seal.
Page 316 of 625
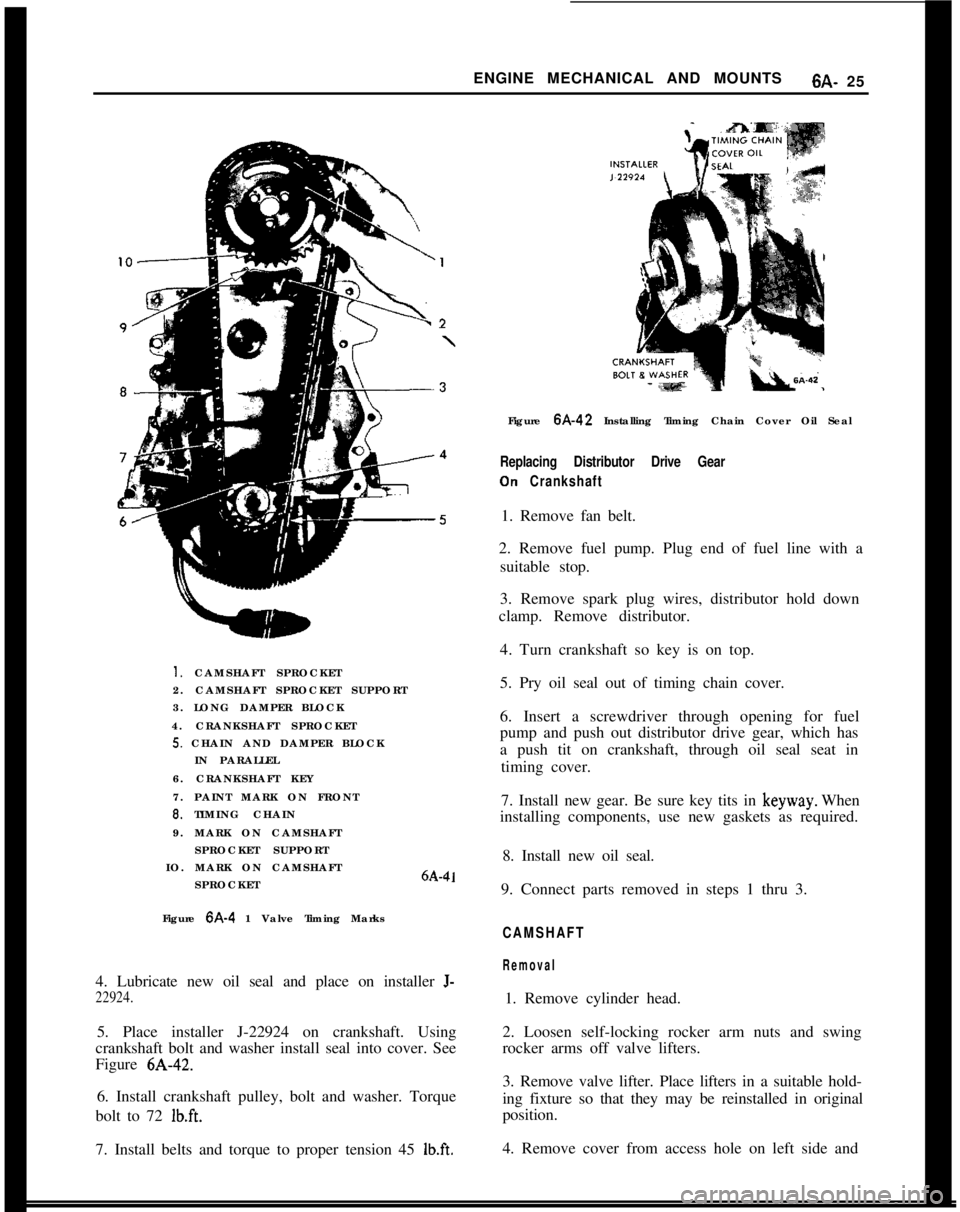
ENGINE MECHANICAL AND MOUNTS6A- 251, CAMSHAFT SPROCKET
2. CAMSHAFT SPROCKET SUPPORT
3. LONG DAMPER BLOCK
4. CRANKSHAFT SPROCKET
5. CHAIN AND DAMPER BLOCK
IN PARALLEL
6. CRANKSHAFT KEY
7. PAINT MARK ON FRONT
8. TIMING CHAIN
9. MARK ON CAMSHAFT
SPROCKET SUPPORT
IO. MARK ON CAMSHAFT
SPROCKET
6A-41Figure 6A-4 1 Valve Timing Marks
Removal4. Lubricate new oil seal and place on installer
J-
22924.1. Remove cylinder head.
5. Place installer J-22924 on crankshaft. Using
crankshaft bolt and washer install seal into cover. See
Figure 6A-42.2. Loosen self-locking rocker arm nuts and swing
rocker arms off valve lifters.
6. Install crankshaft pulley, bolt and washer. Torque
bolt to 72
Ib.ft.3. Remove valve lifter. Place lifters in a suitable hold-
ing fixture so that they may be reinstalled in original
position.
7. Install belts and torque to proper tension 45
lb.ft.4. Remove cover from access hole on left side andFigure 6A-42 Installing Timing Chain Cover Oil Seal
Replacing Distributor Drive Gear
On Crankshaft1. Remove fan belt.
2. Remove fuel pump. Plug end of fuel line with a
suitable stop.
3. Remove spark plug wires, distributor hold down
clamp. Remove distributor.
4. Turn crankshaft so key is on top.
5. Pry oil seal out of timing chain cover.
6. Insert a screwdriver through opening for fuel
pump and push out distributor drive gear, which has
a push tit on crankshaft, through oil seal seat in
timing cover.
7. Install new gear. Be sure key tits in
keyway. When
installing components, use new gaskets as required.
8. Install new oil seal.
9. Connect parts removed in steps 1 thru 3.
CAMSHAFT
Page 317 of 625
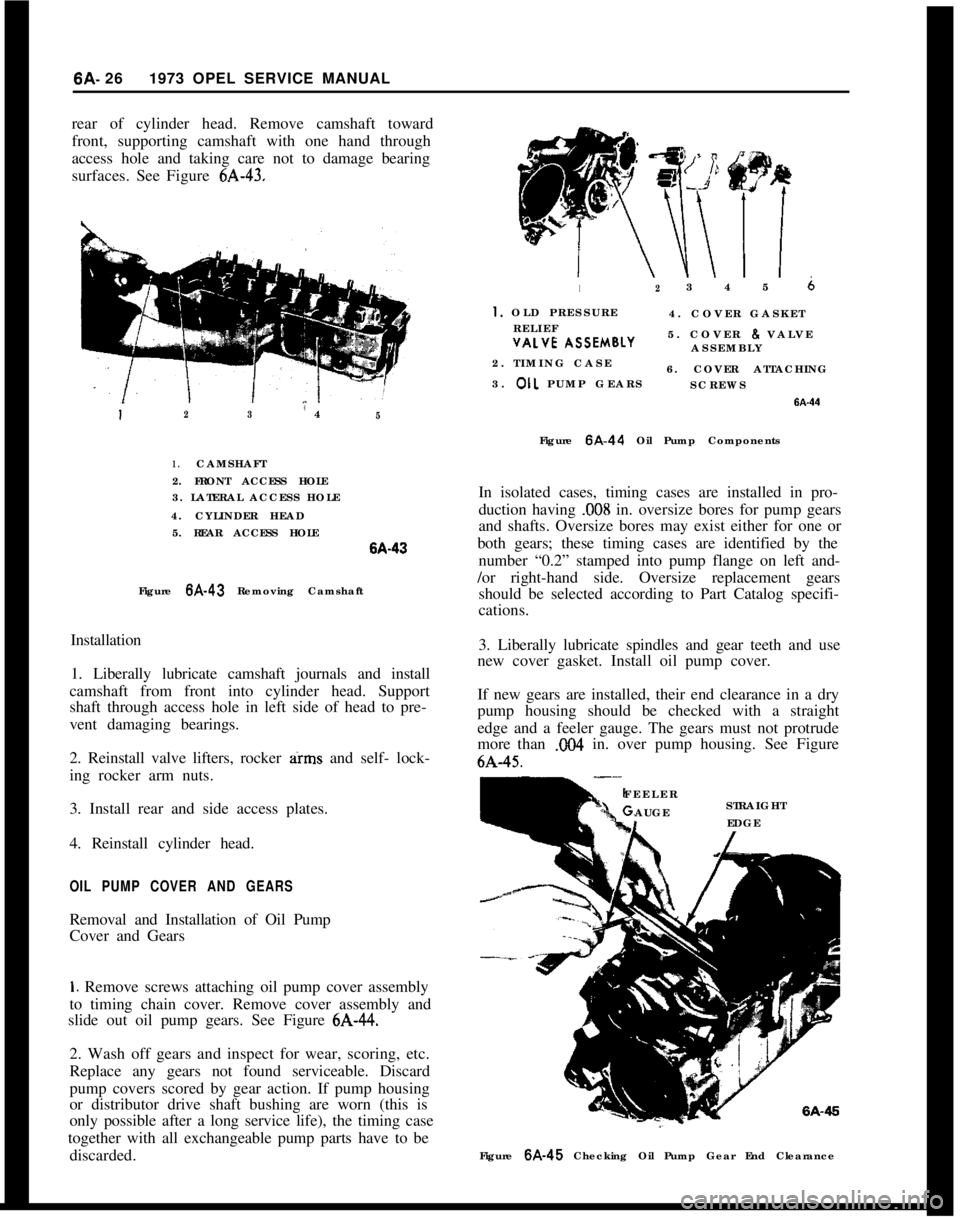
6A- 261973 OPEL SERVICE MANUAL
rear of cylinder head. Remove camshaft toward
front, supporting camshaft with one hand through
access hole and taking care not to damage bearing
surfaces. See Figure 6A-43.12345 6
I. OLD PRESSURE
4. COVER GASKET
RELIEF
~~- \SSEMBLY5. COVER 8 VALVE
ASSEMBLYVALVE I
2. TIMING CASE
6. COVER ATTACHING
3. OIL PUMP GEARS
SCREWS
123” 45Figure 6A-44 Oil Pump Components
1.CAMSHAFT
2. FRONT ACCESS HOLE
3. LATERAL ACCESS HOLE
4. CYLINDER HEAD
5. REAR ACCESS HOLEISA-43
Figure 6A-43 Removing Camshaft
Installation
1. Liberally lubricate camshaft journals and install
camshaft from front into cylinder head. Support
shaft through access hole in left side of head to pre-
vent damaging bearings.
2. Reinstall valve lifters, rocker arms and self- lock-
ing rocker arm nuts.
3. Install rear and side access plates.
4. Reinstall cylinder head.
OIL PUMP COVER AND GEARSRemoval and Installation of Oil Pump
Cover and Gears
1. Remove screws attaching oil pump cover assembly
to timing chain cover. Remove cover assembly and
slide out oil pump gears. See Figure 6A-44.
2. Wash off gears and inspect for wear, scoring, etc.
Replace any gears not found serviceable. Discard
pump covers scored by gear action. If pump housing
or distributor drive shaft bushing are worn (this is
only possible after a long service life), the timing case
together with all exchangeable pump parts have to be
discarded.In isolated cases, timing cases are installed in pro-
duction having
.008 in. oversize bores for pump gears
and shafts. Oversize bores may exist either for one or
both gears; these timing cases are identified by the
number “0.2” stamped into pump flange on left and-
/or right-hand side. Oversize replacement gears
should be selected according to Part Catalog specifi-
cations.
3. Liberally lubricate spindles and gear teeth and use
new cover gasket. Install oil pump cover.
If new gears are installed, their end clearance in a dry
pump housing should be checked with a straight
edge and a feeler gauge. The gears must not protrude
more than X04 in. over pump housing. See Figure6A-45.
FEELER
AUGESTRAIGHTIEDGE
Figure 6A-45 Checking Oil Pump Gear End Clearance
Page 318 of 625
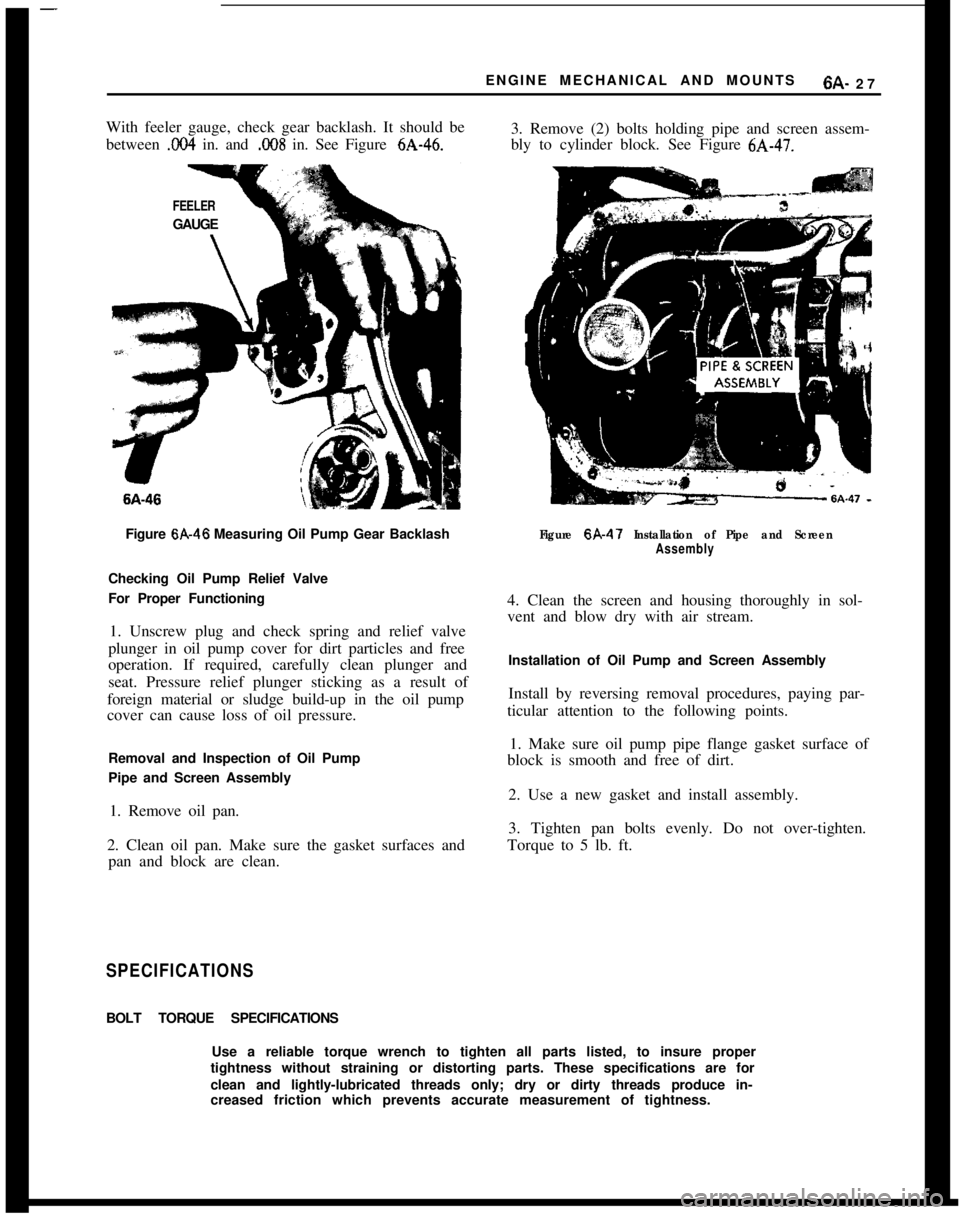
ENGINE MECHANICAL AND MOUNTS6A- 27
With feeler gauge, check gear backlash. It should be
between
.I?04 in. and .C!OS in. See Figure 6A-46.3. Remove (2) bolts holding pipe and screen assem-
bly to cylinder block. See Figure 6A-47.
FEELERGAUGE6A-46
Figure 6A-46 Measuring Oil Pump Gear Backlash
Checking Oil Pump Relief Valve
For Proper Functioning
1. Unscrew plug and check spring and relief valve
plunger in oil pump cover for dirt particles and free
operation. If required, carefully clean plunger and
seat. Pressure relief plunger sticking as a result of
foreign material or sludge build-up in the oil pump
cover can cause loss of oil pressure.
Removal and Inspection of Oil Pump
Pipe and Screen Assembly
1. Remove oil pan.
2. Clean oil pan. Make sure the gasket surfaces and
pan and block are clean.
Figure 6A-47 Installation of Pipe and Screen
Assembly4. Clean the screen and housing thoroughly in sol-
vent and blow dry with air stream.
Installation of Oil Pump and Screen Assembly
Install by reversing removal procedures, paying par-
ticular attention to the following points.
1. Make sure oil pump pipe flange gasket surface of
block is smooth and free of dirt.
2. Use a new gasket and install assembly.
3. Tighten pan bolts evenly. Do not over-tighten.
Torque to 5 lb. ft.
SPECIFICATIONSBOLT TORQUE SPECIFICATIONS
Use a reliable torque wrench to tighten all parts listed, to insure proper
tightness without straining or distorting parts. These specifications are for
clean and lightly-lubricated threads only; dry or dirty threads produce in-
creased friction which prevents accurate measurement of tightness.
Page 319 of 625
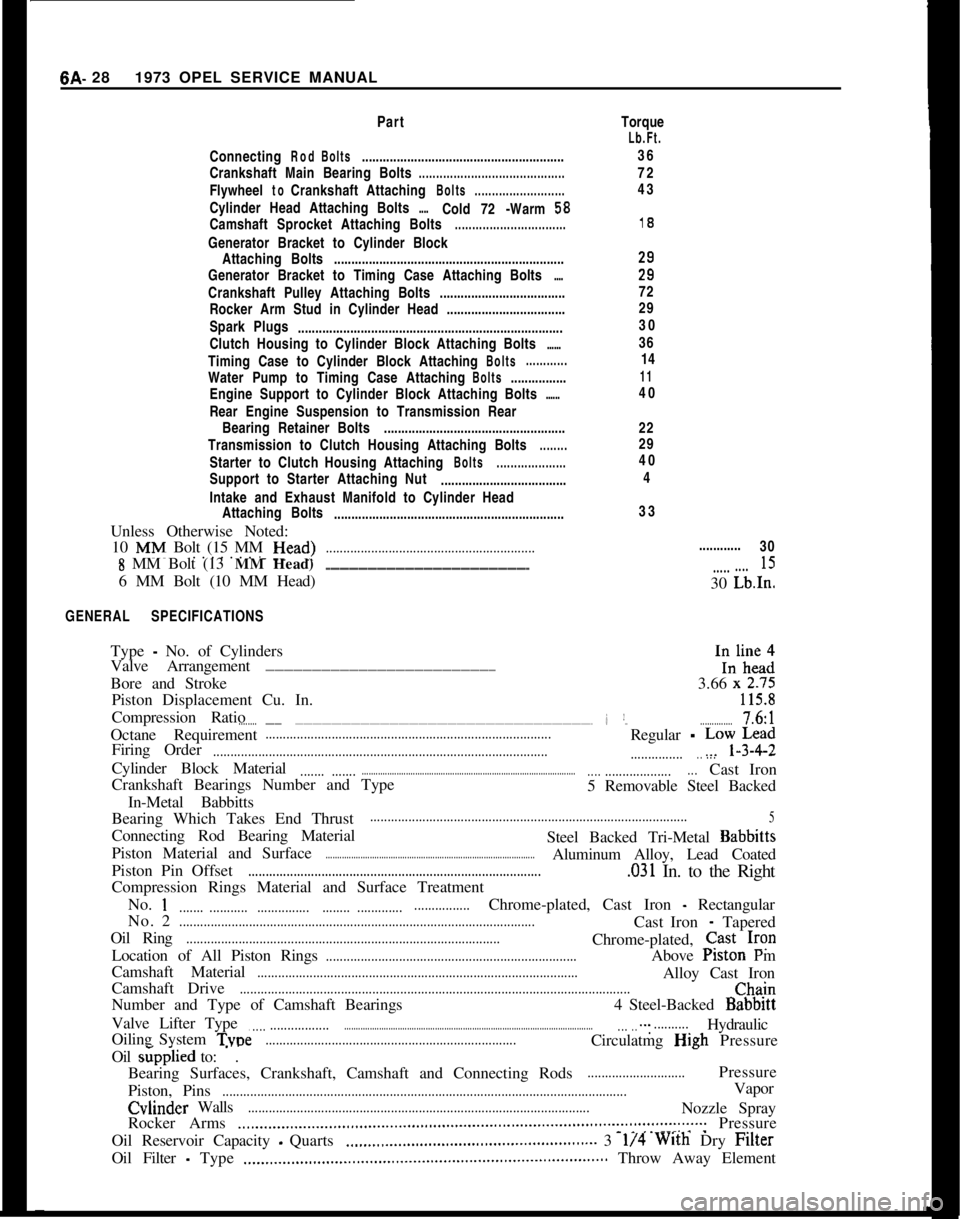
6A- 28 1973 OPEL SERVICE MANUAL
Part
ConnectingRod Bolts..........................................................
Crankshaft Main Bearing Bolts
..........................................
FlywheeltoCrankshaft AttachingBolts..........................
Cylinder Head Attaching Bolts....Cold 72 -Warm 58
Camshaft Sprocket Attaching Bolts................................
Generator Bracket to Cylinder Block
Attaching Bolts ..................................................................
Generator Bracket to Timing Case Attaching Bolts
....
Crankshaft Pulley Attaching Bolts ....................................
Rocker Arm Stud in Cylinder Head ..................................
Spark Plugs ........................................................................\
....
Clutch Housing to Cylinder Block Attaching Bolts
......
Timing Case to Cylinder Block AttachingBolts ............
Water Pump to Timing Case AttachingBolts................
Engine Support to Cylinder Block Attaching Bolts
......
Rear Engine Suspension to Transmission Rear Bearing Retainer Bolts ....................................................
Transmission to Clutch Housing Attaching Bolts
........
Starter to ClutchHousing AttachingBolts....................
Support to Starter Attaching Nut
....................................
Intake and Exhaust Manifold to Cylinder Head Attaching Bolts ..................................................................
Unless Otherwise Noted:
10
@i Bolt (15 MM Hall.....................................................................- -
36
72
43
18
;i
72
29
30
36
14
11
40
22
29
40
4
33 ............30
8 MM Bolt (13 MM Head)........................................................................\
........................................................................\
........................................15
6 MM Bolt (10 MM Head)
30 Lb.In.
Torque
Lb.Ft.
GENERAL SPECIFICATIONS
Type - No. of Cylinders
Valve Arrangement........................................................................\
........................................................................\
......................................................I;nlinzai
Bore and Stroke Piston Displacement Cu. In.
........
3.66 x1:;:;
Compression Ratio......................................................................................\
........................................................................\
........................................................................\
........................................ \fô \
²…..............7.6:1Octane Requirement........................................................................\
..........
Firing Order........................................................................\
........................
Regular - Lo;-?::
....................Cylinder Block Material....... ...............................................................................\
..............................................Cast Iron
Crankshaft Bearings Number and Type 5 Removable Steel Backed
In-Metal Babbitts
Bearing Which Takes End Thrust
........................................................................\
...................5
Connecting Rod Bearing Material
........................................................................\
..................
Steel Backed Tri-Metal Babbttts
Piston Material and Surface Aluminum Alloy, Lead Coated
Piston Pin Offset
........................................................................\
............,031 In. to the RightCompression Rings Material and Surface Treatment
No.
1....... ........... ............... ........ ............. ................Chrome-plated, Cast Iron
- Rectangular
No. 2
........................................................................\
..............................Cast Iron - Tapered
Oil Ring
........................................................................\
..................Chrome-plated, Cast Ir?n
Location of All Piston Rings
........................................................................\
Above Ptston Pm
Camshaft Material
........................................................................\
....................Alloy Cast Iron
Camshaft Drive........................................................................\
........................................Chajn
Number and Type of Camshaft Bearings 4 Steel-Backed Babbttt
Valve Lifter Type
..............................................................................................\
..........................................~..........Hydraulic
Oiling System Tvoe........................................................................\
Circulatmg High Pressure
Oil
&ppiied to: - .
Bearing Surfaces, Crankshaft, Camshaft and Connecting Rods............................Pressure
Piston, Pins
........................................................................\
............................................Vapor
Cvlinder Walls........................................................................\
..........................Nozzle Spray
Rocker Arms _,,,..,,....,._..___.,,..,,..............,,,,...,.......,..,,,.,.,,.....\
....,,...,.,.................~...... Pressure
Oil Reservoir Capacity
- Quarts .,,,...,,__.,,..,..,,..,...,..,,,...,,..............,,,... 3 l/4 With Dry Fdter
Oil Filter
- Type ,,....,__.,,...,....,....,,..,,,..,,...........,........................\
............ Throw Away Element
Page 320 of 625
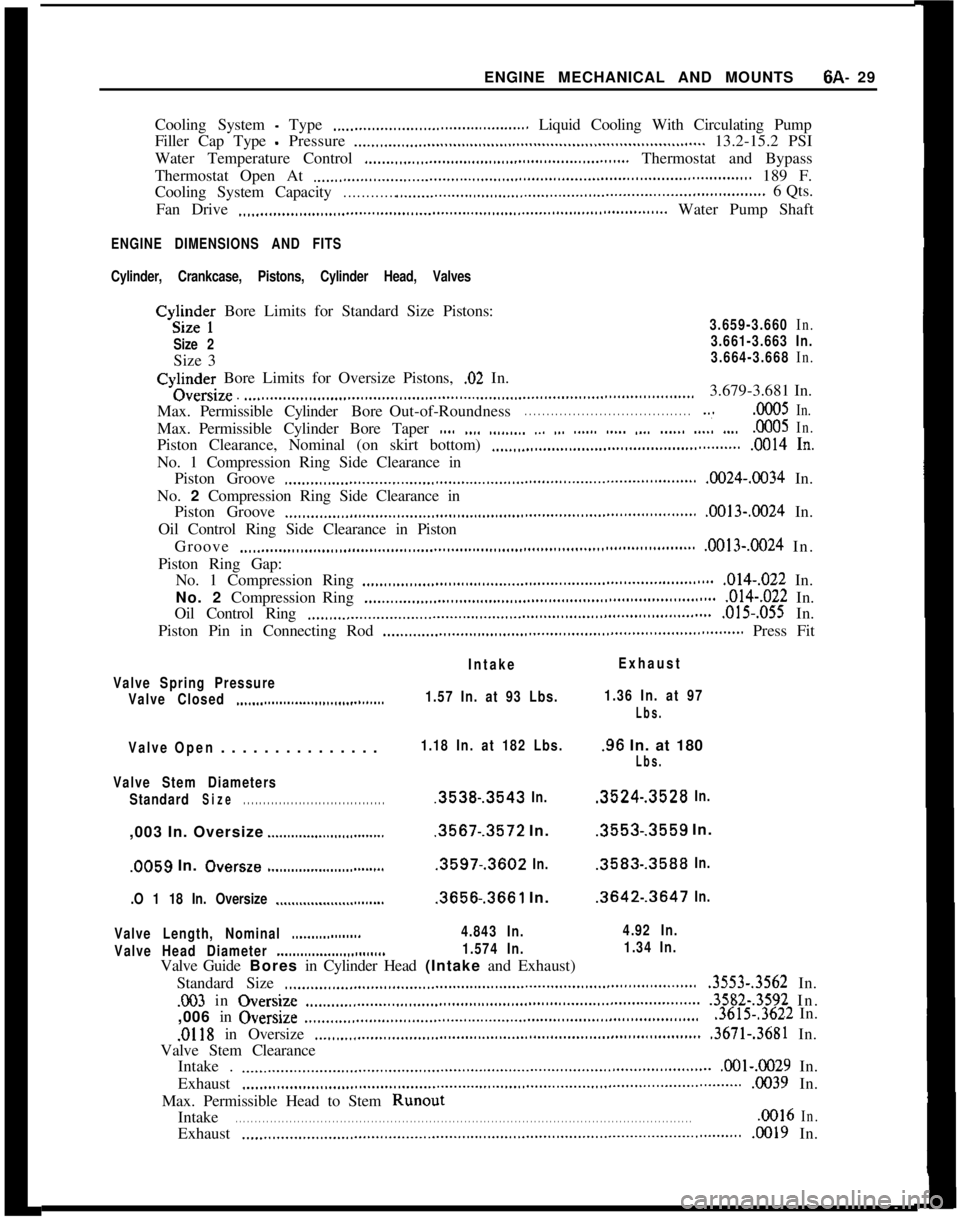
ENGINE MECHANICAL AND MOUNTS6A- 29
Cooling System - Type ,._...___..___..___........................... Liquid Cooling With Circulating Pump
Filler Cap Type
- Pressure _,._.,,._.,,...,,.........,..,.....,.,.................,,......................... 13.2-15.2 PSI
Water Temperature Control
._,..__,,._.,,__.,,...,.,.,,.,,.,,.,...............,,...,,,... Thermostat and Bypass
Thermostat Open At
._,,.,,.......,__.,.........,,...,...,,..,.,,.,,...................................................... 189 F.
Cooling System Capacity
. . . . . . . . . . . . .._...__..............,,.,,.,,..,...................................,,................6 Qts.
Fan Drive
.,,...,,,....,,.,..,..,,........,..,,..,,,.............,..,,.,..,,.................,,............... Water Pump Shaft
ENGINE DIMENSIONS AND FITS
Cylinder, Crankcase, Pistons, Cylinder Head, Valves
Cyg;te; Bore Limits for Standard Size Pistons:3.659-3.660 In.
Size 23.661-3.663 In.Size 3
3.664-3.668 In.Cylindey Bore Limits for Oversize Pistons,
.02 In.Oversm
. .._............,..,,...,................................,,.,,.,,.........................................3.679-3.681 In.
Max.PermissibleCylinderBoreOut-of-Roundness
. . . . . . . . . . . . . . . . . . . . . . . . . . . . . . . . . . . . . . ..~.OOO5In.Max.Permissible Cylinder Bore Taper
,.., ,.,, ,.,._,__. ,_, ,.. .__... ..__. ,__. .____. ..__. .._..0005In.Piston Clearance, Nominal (on skirt bottom)
_..__,,_.,.___.__.._...........,.......................... .0014 In.No. 1 Compression Ring Side Clearance in
Piston Groove
,...,,,.,,,.,,...,__..........,,..,,...,,...,..,.,,.,,..,,..,,..,,..................,,,..,,,..., .0024-.0034 In.
No. 2 Compression Ring Side Clearance in
Piston Groove
_..,,..,,,..,,..,,..,,....,.......,...,,,.,.,,,..,..,..,,..,,..,,,..,,,.,,,..,,,...,,,..,,,,..., .0013-.OO24 In.
Oil Control Ring Side Clearance in Piston
Groove
__..__..._..,,,..,...,,,..,....,..,,..,.........,..,,...,,.,,.,,..,..,,..,,...,,...,,,..,,,..,,,...,,..... .0013-X024 In.
Piston Ring Gap:
No. 1 Compression Ring
..,,.,,,..,,,..,,..,,,.,,.,,,..,......,,.,..............,......................... .014-,022 In.
No. 2 Compression Ring
_..___..__.,,..,,..,,,..,.,,,..,,.,,....................,......................... .014-,022 In.
Oil Control Ring
,...,,...,___.___.._..................,,,..,..,,..,,.,,,..,,,.,,..,,,..,,,...,,,,..,,,...,.... ,015.,055 In.
Piston Pin in Connecting Rod
..____.___..._,,__.,,,,,..,,.,,..,.................,,............................... Press Fit
IntakeExhaust
Valve Spring Pressure
Valve Closed
_______........___..,,,,,,............1.57 In. at 93 Lbs.1.36 In. at 97
Lbs.
ValveOpen. . . . . . . . . . . . . . .1.18 In. at 182 Lbs..96 In. at 180
Lbs.
Valve Stem Diameters
Standard
Size. . . . . . . . . . . . . . . . . . . . . . . . . . . . . . . . . . . ..3538-.3543 In..3524-.3528 In.,003 In. Oversize
____.....__.._..,,,,,,.........3567-.3572 In..3553-.3559 In..0059 In.
Oversze .__......_______...............3597-.3602 In..3583-.3588 In.
.O 1 18 In. Oversize
_._...._._____...............3656-.3661 In..3642-.3647 In.
Valve Length, Nominal
..___.............4.843 In.4.92 In.
Valve Head Diameter
___.......____...,,,........1.574 In.1.34 In.Valve Guide Bores in Cylinder Head (Intake and Exhaust)
Standard Size
,,...,,...,,..,,..,,,..,,....................................,..,,...,,.,,,,..,,,,..,,...,,,,.., .3553-.3562 In.003 in Oversjze
.,..__,,._.,__..___....,,...,,..,,...,,,,,,.,,.,,..,................,.....,................. .3582-.3592 In.
,006 in Overslze
..,...,,..,,.......................................,.........................................3615-.3622 In.
.0118 in Oversize ,._.,,..,............,,...,,........................................,,.................... .3671-.3681 In.
Valve Stem Clearance
Intake .
.._........___..___.....,............,...,,..........................................,,...................... .OOl-.0029 In.
Exhaust
._.,,........,,...,,..,,...........,,...,................,..,,..,,................,,.....,.,........................ 0039 In.
Max. Permissible Head to Stem Runout
Intake
. . . . . . . . . . . . . . . . . . . . . . . . . . . . . . . . . . . . . . . . . . . . . . . . . . . . . . . . . . . . . . . . . . . . . . . . . . . . . . . . . . . . . . . . . . . . . . . . . . . . . . . . . . . . . . . . . . . . . ..OO16In.Exhaust
.,...........,,...,...,.,,...........,,...,....,....,.,,,..,,.,,,........................................,.......... .0019 In.