OPEL GT-R 1973 Service Manual
Manufacturer: OPEL, Model Year: 1973, Model line: GT-R, Model: OPEL GT-R 1973Pages: 625, PDF Size: 17.22 MB
Page 301 of 625
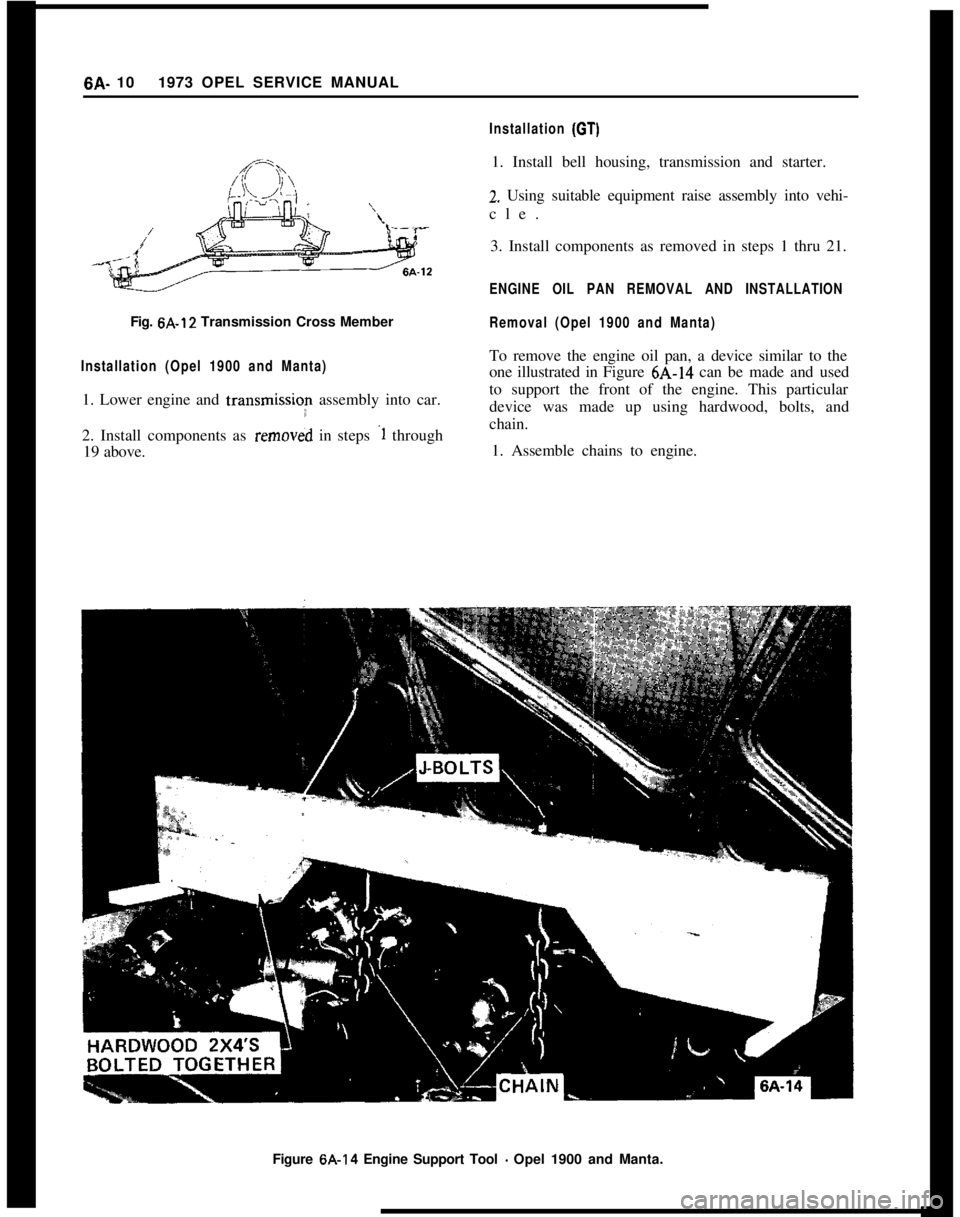
6A- 101973 OPEL SERVICE MANUAL
Fig. 6A.12 Transmission Cross MemberInstallation (Opel 1900 and Manta)1. Lower engine and transmissior assembly into car.
2. Install components as
remov&d in steps .1 through
19 above.
Installation (GT)1. Install bell housing, transmission and starter.
2. Using suitable equipment raise assembly into vehi-
cle.
3. Install components as removed in steps 1 thru 21.
ENGINE OIL PAN REMOVAL AND INSTALLATION
Removal (Opel 1900 and Manta)To remove the engine oil pan, a device similar to the
one illustrated in Figure 6A-14 can be made and used
to support the front of the engine. This particular
device was made up using hardwood, bolts, and
chain.
1. Assemble chains to engine.
Figure 6A-14 Engine Support Tool
- Opel 1900 and Manta.
Page 302 of 625
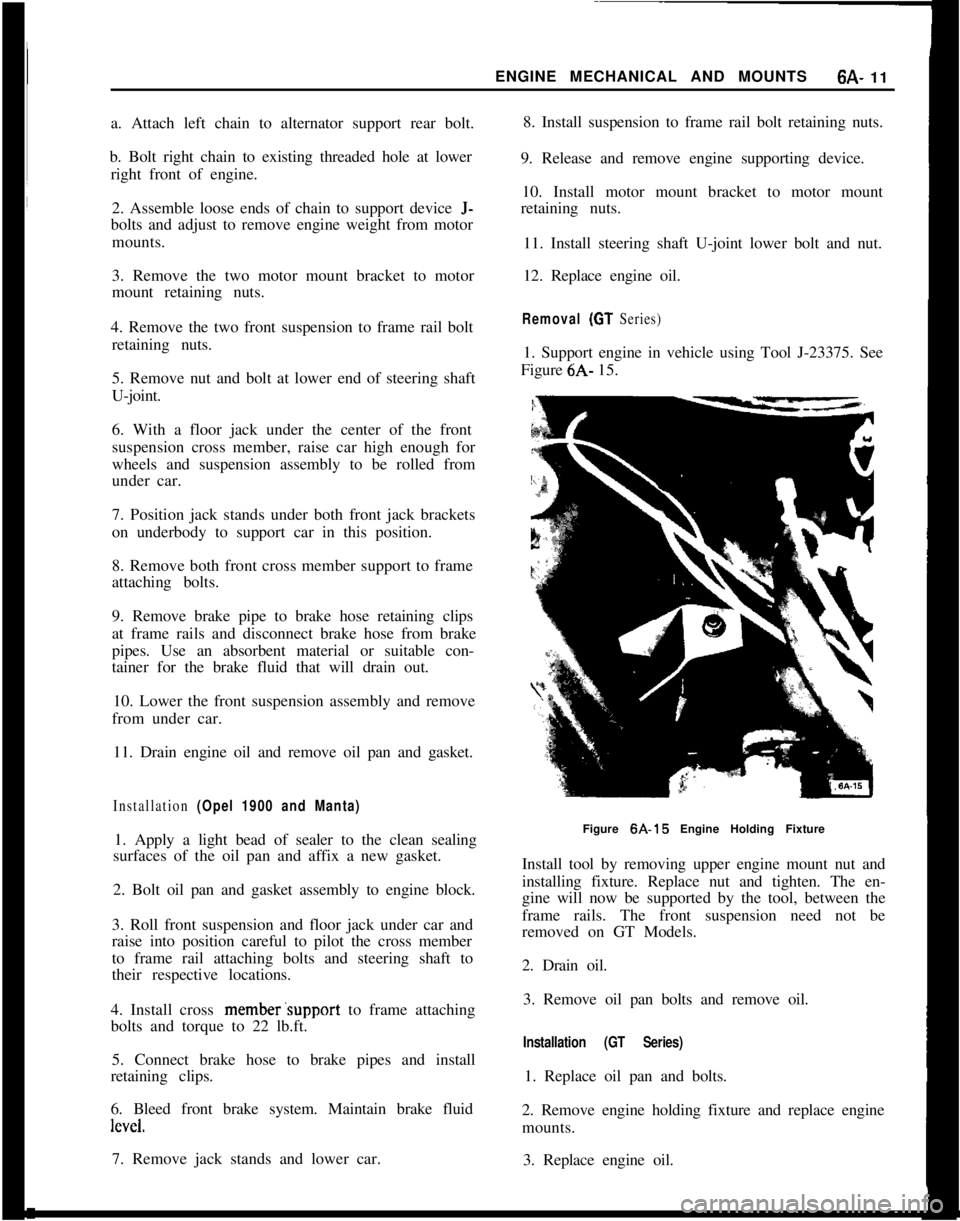
ENGINE MECHANICAL AND MOUNTS6A- 11
a. Attach left chain to alternator support rear bolt.
b. Bolt right chain to existing threaded hole at lower
right front of engine.
2. Assemble loose ends of chain to support device J-bolts and adjust to remove engine weight from motor
mounts.
3. Remove the two motor mount bracket to motor
mount retaining nuts.
4. Remove the two front suspension to frame rail bolt
retaining nuts.
5. Remove nut and bolt at lower end of steering shaft
U-joint.
6. With a floor jack under the center of the front
suspension cross member, raise car high enough for
wheels and suspension assembly to be rolled from
under car.
7. Position jack stands under both front jack brackets
on underbody to support car in this position.
8. Remove both front cross member support to frame
attaching bolts.
9. Remove brake pipe to brake hose retaining clips
at frame rails and disconnect brake hose from brake
pipes. Use an absorbent material or suitable con-
tainer for the brake fluid that will drain out.
10. Lower the front suspension assembly and remove
from under car.
11. Drain engine oil and remove oil pan and gasket.
Installation (Opel 1900 and Manta)1. Apply a light bead of sealer to the clean sealing
surfaces of the oil pan and affix a new gasket.
2. Bolt oil pan and gasket assembly to engine block.
3. Roll front suspension and floor jack under car and
raise into position careful to pilot the cross member
to frame rail attaching bolts and steering shaft to
their respective locations.
4. Install cross member’support to frame attaching
bolts and torque to 22 lb.ft.
5. Connect brake hose to brake pipes and install
retaining clips.
6. Bleed front brake system. Maintain brake fluid1Wd.
7. Remove jack stands and lower car.8. Install suspension to frame rail bolt retaining nuts.
9. Release and remove engine supporting device.
10. Install motor mount bracket to motor mount
retaining nuts.
11. Install steering shaft U-joint lower bolt and nut.
12. Replace engine oil.
Removal (GT Series)1. Support engine in vehicle using Tool J-23375. See
Figure 6A- 15.
Figure 6A-15 Engine Holding Fixture
Install tool by removing upper engine mount nut and
installing fixture. Replace nut and tighten. The en-
gine will now be supported by the tool, between the
frame rails. The front suspension need not be
removed on GT Models.
2. Drain oil.
3. Remove oil pan bolts and remove oil.
Installation (GT Series)1. Replace oil pan and bolts.
2. Remove engine holding fixture and replace engine
mounts.
3. Replace engine oil.
Page 303 of 625
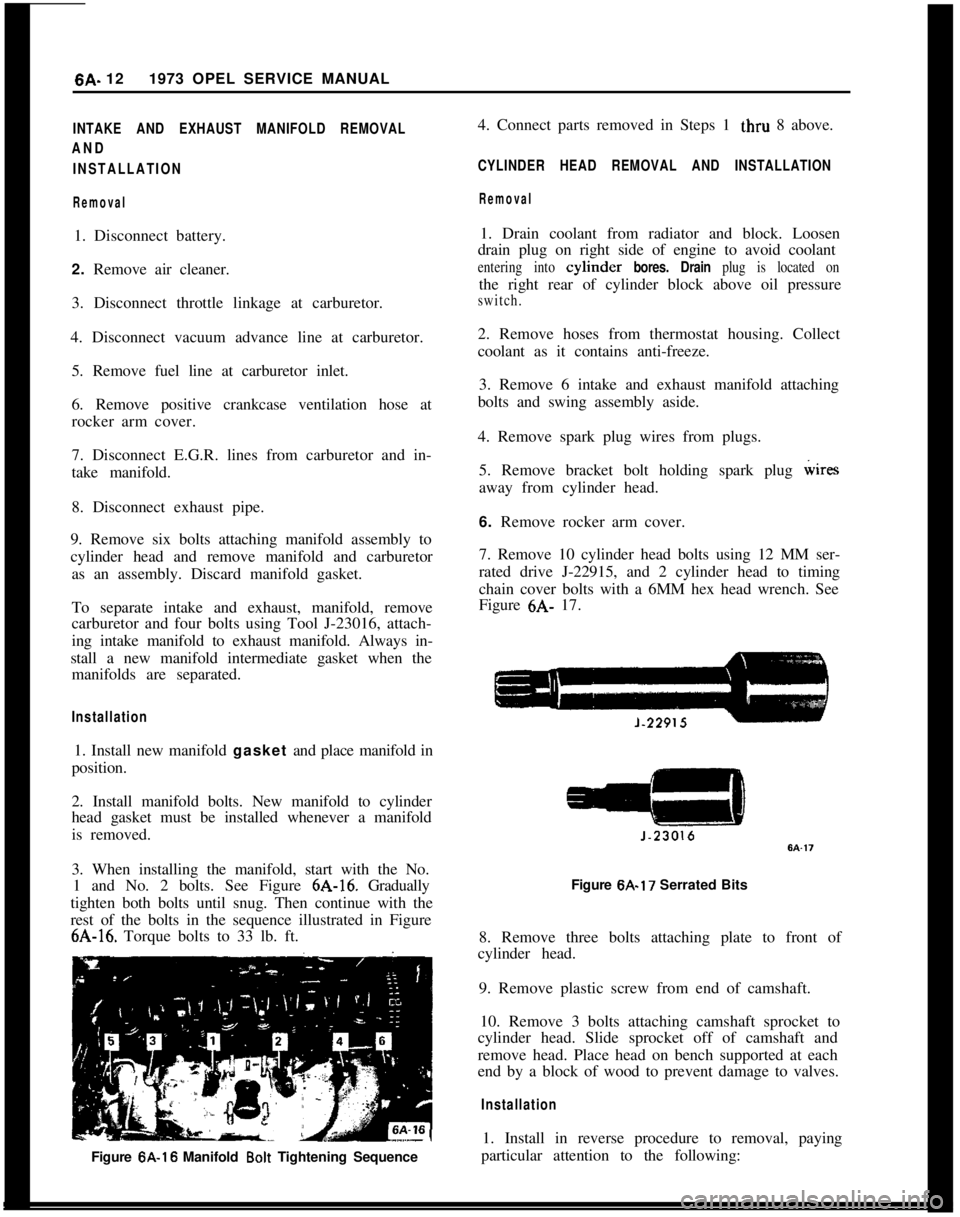
6A- 121973 OPEL SERVICE MANUALINTAKE AND EXHAUST MANIFOLD REMOVAL
AND
INSTALLATION
Removal1. Disconnect battery.
2. Remove air cleaner.
3. Disconnect throttle linkage at carburetor.
4. Disconnect vacuum advance line at carburetor.
5. Remove fuel line at carburetor inlet.
6. Remove positive crankcase ventilation hose at
rocker arm cover.
7. Disconnect E.G.R. lines from carburetor and in-
take manifold.
8. Disconnect exhaust pipe.
9. Remove six bolts attaching manifold assembly to
cylinder head and remove manifold and carburetor
as an assembly. Discard manifold gasket.
To separate intake and exhaust, manifold, remove
carburetor and four bolts using Tool J-23016, attach-
ing intake manifold to exhaust manifold. Always in-
stall a new manifold intermediate gasket when the
manifolds are separated.
Installation1. Install new manifold gasket and place manifold in
position.
2. Install manifold bolts. New manifold to cylinder
head gasket must be installed whenever a manifold
is removed.
3. When installing the manifold, start with the No.
1 and No. 2 bolts. See Figure 6A-16. Gradually
tighten both bolts until snug. Then continue with the
rest of the bolts in the sequence illustrated in Figure6A-16. Torque bolts to 33 lb. ft.
Figure 6A-16 Manifold
Bolt Tightening Sequence4. Connect parts removed in Steps 1 thru 8 above.
CYLINDER HEAD REMOVAL AND INSTALLATION
Removal1. Drain coolant from radiator and block. Loosen
drain plug on right side of engine to avoid coolant
entering into cylmder bores. Drain plug is located onthe right rear of cylinder block above oil pressure
switch.2. Remove hoses from thermostat housing. Collect
coolant as it contains anti-freeze.
3. Remove 6 intake and exhaust manifold attaching
bolts and swing assembly aside.
4. Remove spark plug wires from plugs.
5. Remove bracket bolt holding spark plug wires
away from cylinder head.
6. Remove rocker arm cover.
7. Remove 10 cylinder head bolts using 12 MM ser-
rated drive J-22915, and 2 cylinder head to timing
chain cover bolts with a 6MM hex head wrench. See
Figure 6A- 17.
Figure 6A-17 Serrated Bits
8. Remove three bolts attaching plate to front of
cylinder head.
9. Remove plastic screw from end of camshaft.
10. Remove 3 bolts attaching camshaft sprocket to
cylinder head. Slide sprocket off of camshaft and
remove head. Place head on bench supported at each
end by a block of wood to prevent damage to valves.
Installation1. Install in reverse procedure to removal, paying
particular attention to the following:
Page 304 of 625
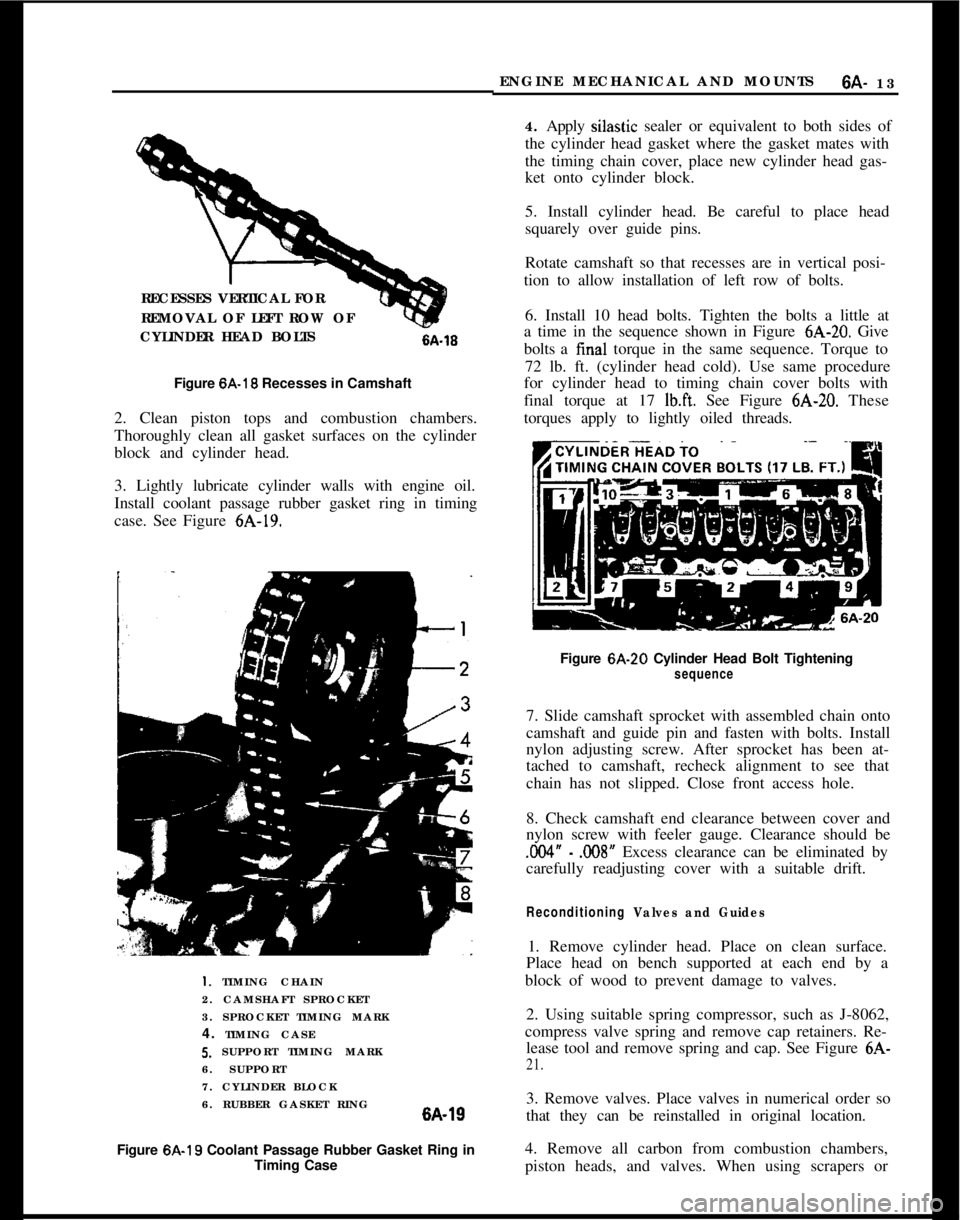
RECESSES VERTICAL FOR
REMOVAL OF LEFT ROW OF
CYLINDER HEAD BOLTS6A-16
Figure 6A-18 Recesses in Camshaft
2. Clean piston tops and combustion chambers.
Thoroughly clean all gasket surfaces on the cylinder
block and cylinder head.
3. Lightly lubricate cylinder walls with engine oil.
Install coolant passage rubber gasket ring in timing
case. See Figure 6A-19.I. TIMING CHAIN
2. CAMSHAFT SPROCKET
3. SPROCKET TIMING MARK
4. TIMING CASE5. SUPPORT TIMING MARK
6. SUPPORT
7. CYLINDER BLOCK
6. RUBBER GASKET RING6A-19
Figure 6A-19 Coolant Passage Rubber Gasket Ring in
Timing CaseENGINE MECHANICAL AND MOUNTS
6A- 13
4. Apply silastic sealer or equivalent to both sides of
the cylinder head gasket where the gasket mates with
the timing chain cover, place new cylinder head gas-
ket onto cylinder block.
5. Install cylinder head. Be careful to place head
squarely over guide pins.
Rotate camshaft so that recesses are in vertical posi-
tion to allow installation of left row of bolts.
6. Install 10 head bolts. Tighten the bolts a little at
a time in the sequence shown in Figure 6A-20. Give
bolts a final torque in the same sequence. Torque to
72 lb. ft. (cylinder head cold). Use same procedure
for cylinder head to timing chain cover bolts with
final torque at 17
lb.ft. See Figure 6A-20. These
torques apply to lightly oiled threads.
Figure 6A-20 Cylinder Head Bolt Tightening
sequence7. Slide camshaft sprocket with assembled chain onto
camshaft and guide pin and fasten with bolts. Install
nylon adjusting screw. After sprocket has been at-
tached to camshaft, recheck alignment to see that
chain has not slipped. Close front access hole.
8. Check camshaft end clearance between cover and
nylon screw with feeler gauge. Clearance should be
.004” - .008” Excess clearance can be eliminated by
carefully readjusting cover with a suitable drift.
Reconditioning Valves and Guides1. Remove cylinder head. Place on clean surface.
Place head on bench supported at each end by a
block of wood to prevent damage to valves.
2. Using suitable spring compressor, such as J-8062,
compress valve spring and remove cap retainers. Re-
lease tool and remove spring and cap. See Figure 6A-
21.3. Remove valves. Place valves in numerical order so
that they can be reinstalled in original location.
4. Remove all carbon from combustion chambers,
piston heads, and valves. When using scrapers or
Page 305 of 625
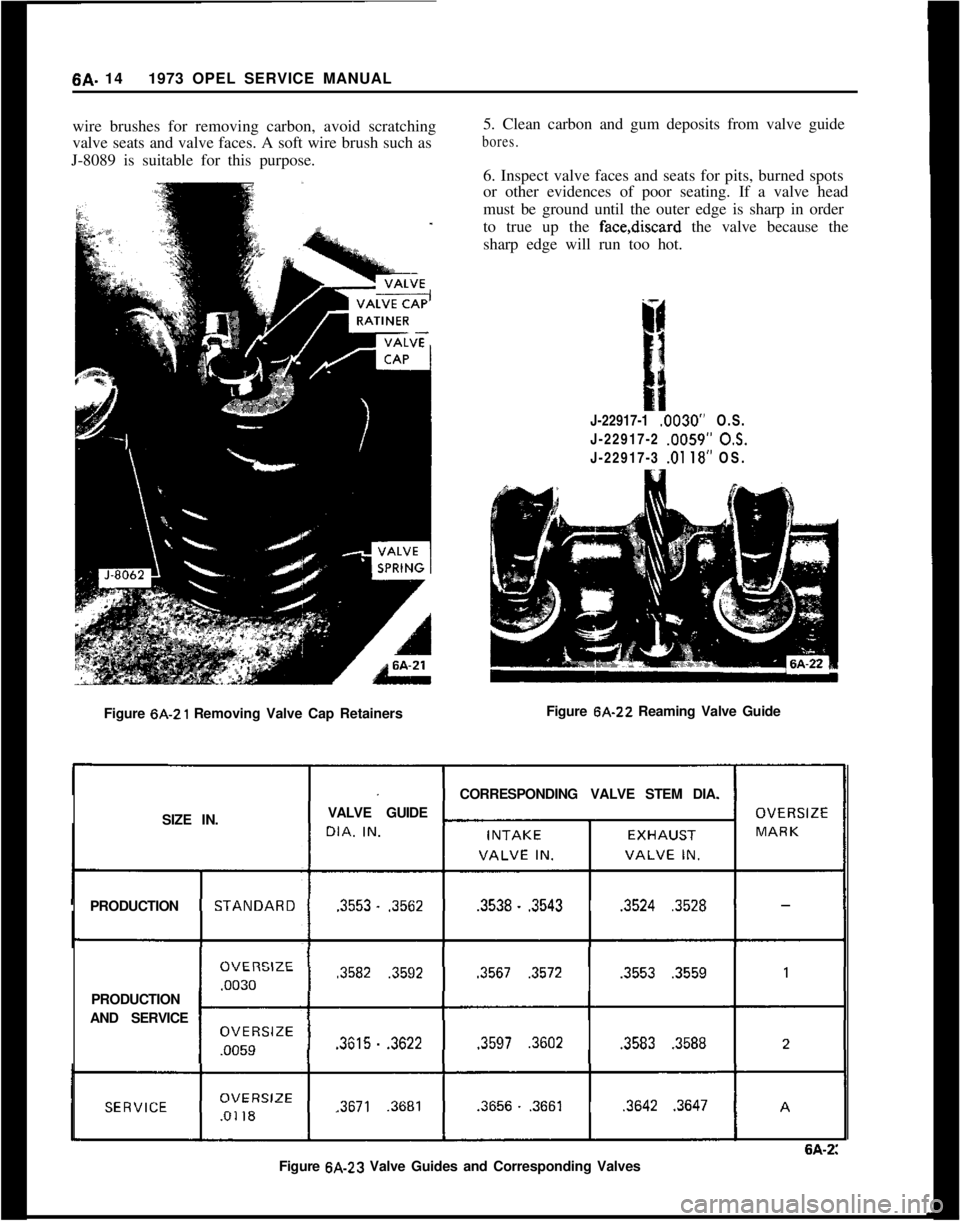
6A. 141973 OPEL SERVICE MANUAL
wire brushes for removing carbon, avoid scratching
valve seats and valve faces. A soft wire brush such as
J-8089 is suitable for this purpose.
Figure 6A-21 Removing Valve Cap Retainers5. Clean carbon and gum deposits from valve guide
bores.6. Inspect valve faces and seats for pits, burned spots
or other evidences of poor seating. If a valve head
must be ground until the outer edge is sharp in order
to true up the face,discard the valve because the
sharp edge will run too hot.
J-22917-1 .0030” O.S.
J-22917-2 .0059”
05.J-22917-3 .Ol 18” OS.
Figure 6A-22 Reaming Valve Guide
CORRESPONDINGVALVE STEM DIA.
SIZE IN.VALVE GUIDE
PRODUCTION.3553.
.3562.3538..3543.3524.3528PRODUCTION
AND SERVICE
.3582.3592.3567.3572.3553.3559.3615.
.3622.3597.3602.3583.3588
.3671.3681.3656..3661.3642.3647
6A-2:Figure 6A-23 Valve Guides and Corresponding Valves
Page 306 of 625
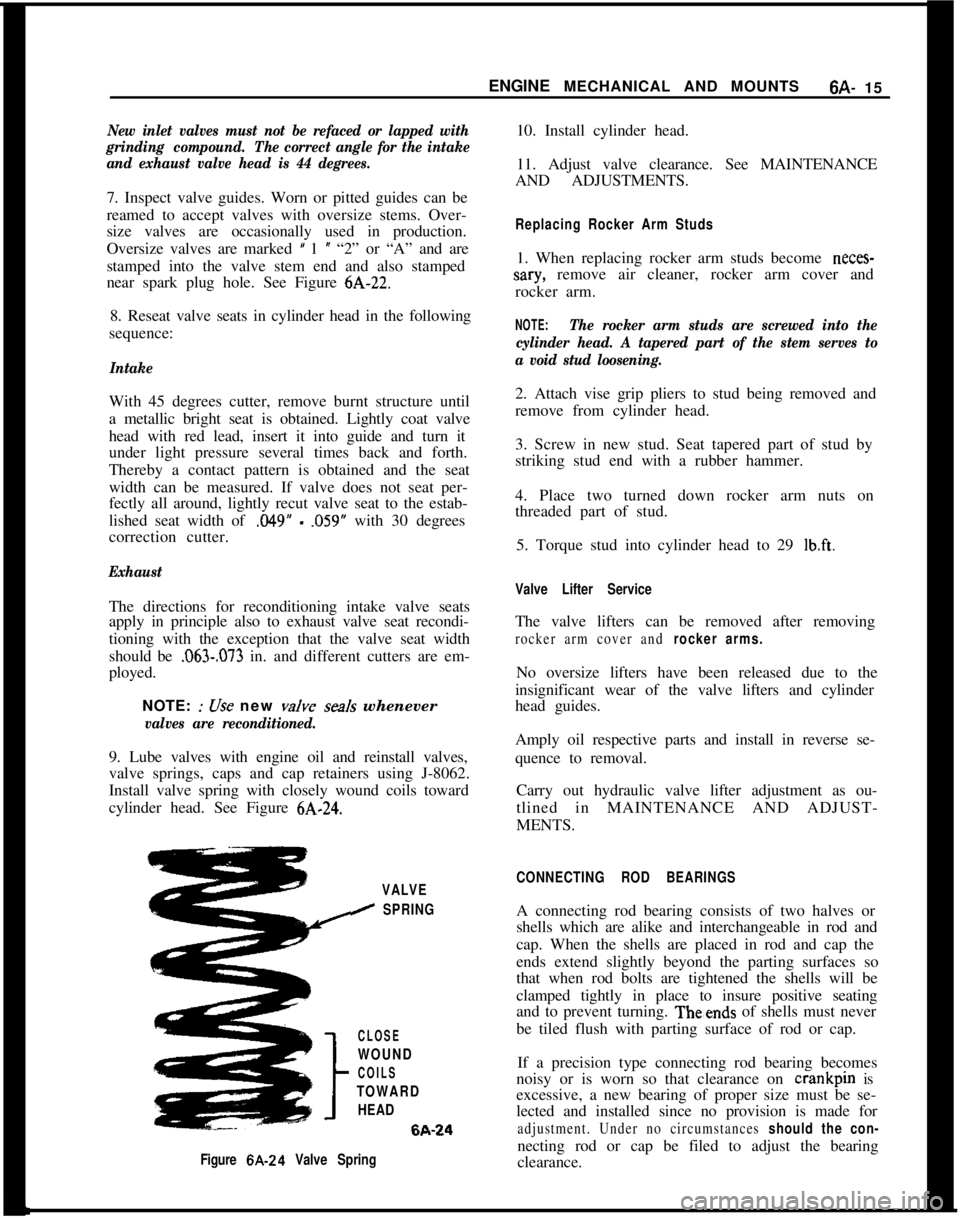
ENGINE MECHANICAL AND MOUNTS6A- 15New inlet valves must not be refaced or lapped with
grinding compound.The correct angle for the intake
and exhaust valve head is 44 degrees.10. Install cylinder head.
11. Adjust valve clearance. See MAINTENANCE
AND ADJUSTMENTS.
7. Inspect valve guides. Worn or pitted guides can be
reamed to accept valves with oversize stems. Over-
size valves are occasionally used in production.
Oversize valves are marked
’ 1 u “2” or “A” and are
stamped into the valve stem end and also stamped
near spark plug hole. See Figure 6A-22.
Replacing Rocker Arm Studs1. When replacing rocker arm studs become
neces-
sary, remove air cleaner, rocker arm cover and
rocker arm.
8. Reseat valve seats in cylinder head in the following
sequence:
Intake
NOTE:The rocker arm studs are screwed into the
cylinder head. A tapered part of the stem serves to
a void stud loosening.With 45 degrees cutter, remove burnt structure until
a metallic bright seat is obtained. Lightly coat valve
head with red lead, insert it into guide and turn it
under light pressure several times back and forth.
Thereby a contact pattern is obtained and the seat
width can be measured. If valve does not seat per-
fectly all around, lightly recut valve seat to the estab-
lished seat width of
,049” - .059” with 30 degrees
correction cutter.
ExhaustThe directions for reconditioning intake valve seats
apply in principle also to exhaust valve seat recondi-
tioning with the exception that the valve seat width
should be
.063-,073 in. and different cutters are em-
ployed.
NOTE:
: OTse new valve seals whenever
valves are reconditioned.9. Lube valves with engine oil and reinstall valves,
valve springs, caps and cap retainers using J-8062.
Install valve spring with closely wound coils toward
cylinder head. See Figure
6A-24.2. Attach vise grip pliers to stud being removed and
remove from cylinder head.
3. Screw in new stud. Seat tapered part of stud by
striking stud end with a rubber hammer.
4. Place two turned down rocker arm nuts on
threaded part of stud.
5. Torque stud into cylinder head to 29
lb.ft.
Valve Lifter ServiceThe valve lifters can be removed after removing
rocker arm cover and rocker arms.No oversize lifters have been released due to the
insignificant wear of the valve lifters and cylinder
head guides.
Amply oil respective parts and install in reverse se-
quence to removal.
Carry out hydraulic valve lifter adjustment as ou-
tlined in MAINTENANCE AND ADJUST-
MENTS.
VALVE
I SPRING
CLOSE
WOUND
COILS
TOWARD
HEAD6A-24
Figure 6A-24 Valve SpringCONNECTING ROD BEARINGSA connecting rod bearing consists of two halves or
shells which are alike and interchangeable in rod and
cap. When the shells are placed in rod and cap the
ends extend slightly beyond the parting surfaces so
that when rod bolts are tightened the shells will be
clamped tightly in place to insure positive seating
and to prevent turning. Theends of shells must never
be tiled flush with parting surface of rod or cap.
If a precision type connecting rod bearing becomes
noisy or is worn so that clearance on crankpin is
excessive, a new bearing of proper size must be se-
lected and installed since no provision is made for
adjustment. Under no circumstances should the con-necting rod or cap be filed to adjust the bearing
clearance.
Page 307 of 625
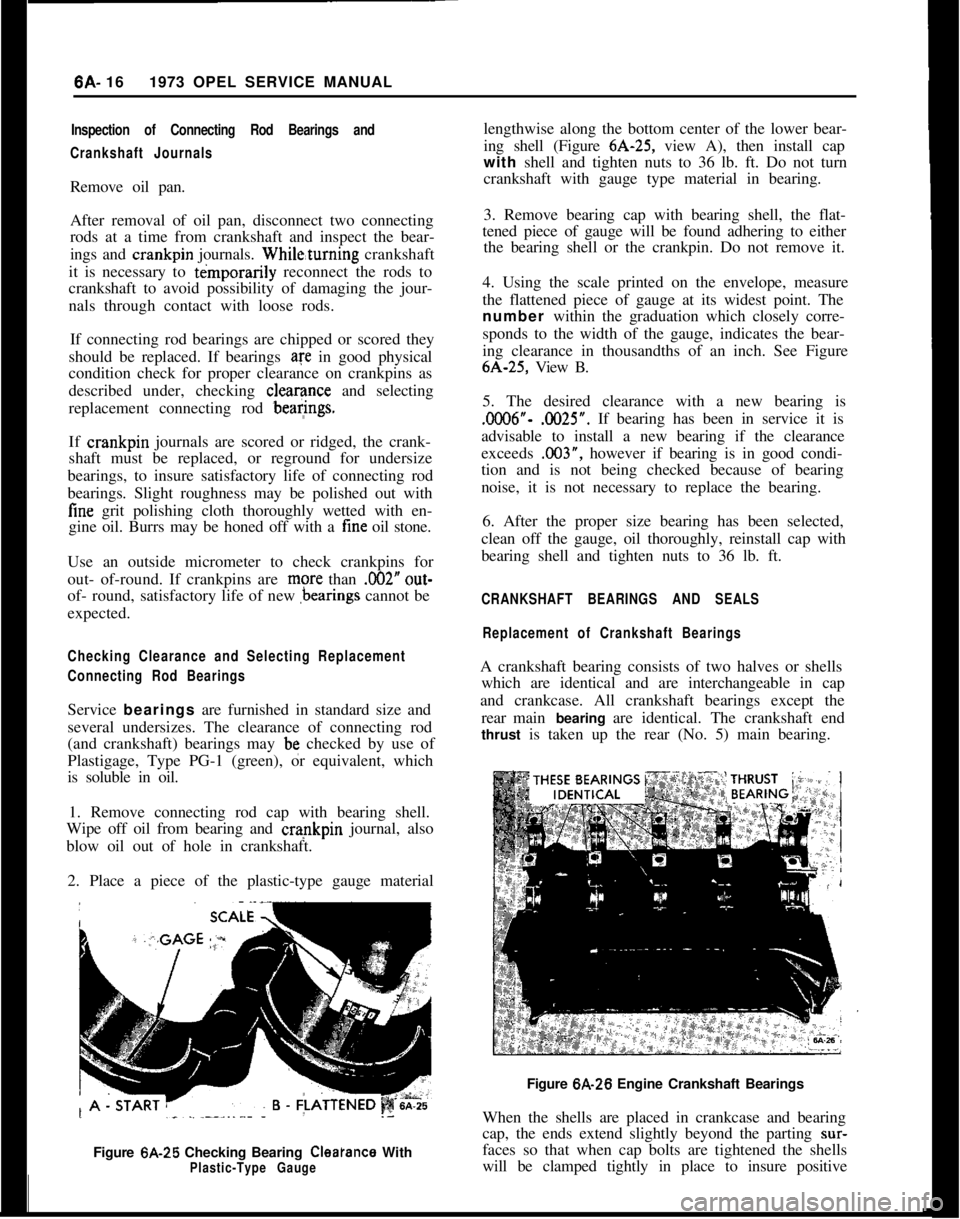
6A- 161973 OPEL SERVICE MANUALInspection of Connecting Rod Bearings and
Crankshaft JournalsRemove oil pan.
After removal of oil pan, disconnect two connecting
rods at a time from crankshaft and inspect the bear-
ings and crankpin journals. While,tuming crankshaft
it is necessary to
t&porarily reconnect the rods to
crankshaft to avoid possibility of damaging the jour-
nals through contact with loose rods.
If connecting rod bearings are chipped or scored they
should be replaced. If bearings
are in good physical
condition check for proper clearance on crankpins as
described under, checking clear$nce and selecting
replacement connecting rod beartngs.
If crankpin journals are scored or ridged, the crank-
shaft must be replaced, or reground for undersize
bearings, to insure satisfactory life of connecting rod
bearings. Slight roughness may be polished out withfine grit polishing cloth thoroughly wetted with en-
gine oil. Burrs may be honed off with a fine oil stone.
Use an outside micrometer to check crankpins for
out- of-round. If crankpins are mpre than
,002” out-
of- round, satisfactory life of new ,bearings cannot be
expected.
Checking Clearance and Selecting Replacement
Connecting Rod BearingsService bearings are furnished in standard size and
several undersizes. The clearance of connecting rod
(and crankshaft) bearings may be checked by use of
Plastigage, Type PG-1 (green), or equivalent, which
is soluble in oil.
1. Remove connecting rod cap with bearing shell.
Wipe off oil from bearing and crankpin journal, also
blow oil out of hole in crankshaft.
2. Place a piece of the plastic-type gauge material
Figure 6A-25 Checking Bearing
Cleatance WithPlastic-Type Gaugelengthwise along the bottom center of the lower bear-
ing shell (Figure 6A-25, view A), then install cap
with shell and tighten nuts to 36 lb. ft. Do not turn
crankshaft with gauge type material in bearing.
3. Remove bearing cap with bearing shell, the flat-
tened piece of gauge will be found adhering to either
the bearing shell or the crankpin. Do not remove it.
4. Using the scale printed on the envelope, measure
the flattened piece of gauge at its widest point. The
number within the graduation which closely corre-
sponds to the width of the gauge, indicates the bear-
ing clearance in thousandths of an inch. See Figure6A-25, View B.
5. The desired clearance with a new bearing is.0006”- .0025”. If bearing has been in service it is
advisable to install a new bearing if the clearance
exceeds .003”, however if bearing is in good condi-
tion and is not being checked because of bearing
noise, it is not necessary to replace the bearing.
6. After the proper size bearing has been selected,
clean off the gauge, oil thoroughly, reinstall cap with
bearing shell and tighten nuts to 36 lb. ft.
CRANKSHAFT BEARINGS AND SEALS
Replacement of Crankshaft BearingsA crankshaft bearing consists of two halves or shells
which are identical and are interchangeable in cap
and crankcase. All crankshaft bearings except the
rear main bearing are identical. The crankshaft end
thrust is taken up the rear (No. 5) main bearing.
Figure 6A-26 Engine Crankshaft Bearings
When the shells are placed in crankcase and bearing
cap, the ends extend slightly beyond the parting
sur-faces so that when cap bolts are tightened the shells
will be clamped tightly in place to insure positive
Page 308 of 625
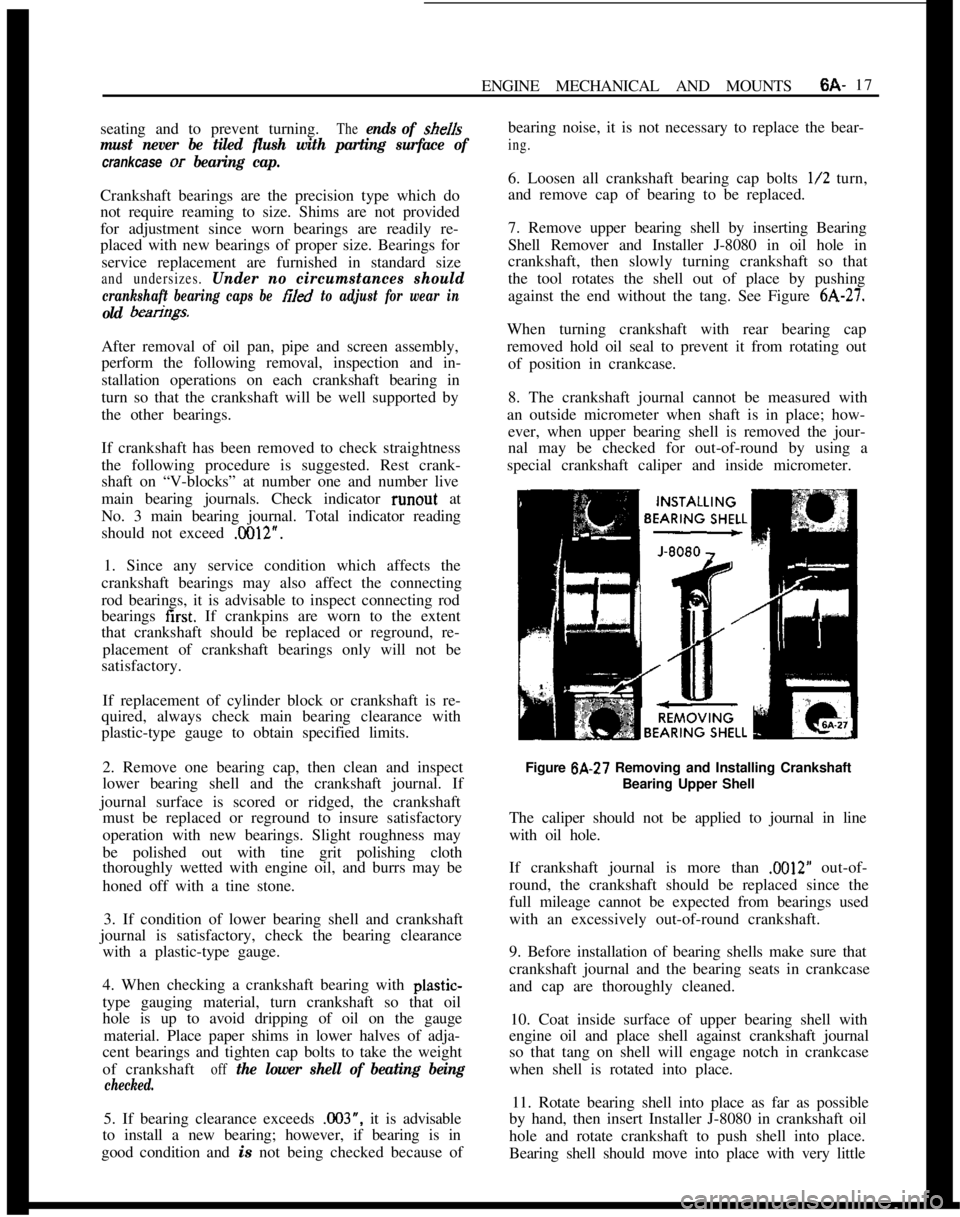
ENGINE MECHANICAL AND MOUNTS6A- 17
seating and to prevent turning.The ends of she//s
must never be tiled flush with parting surface of
crankcase or bearing cap.Crankshaft bearings are the precision type which do
not require reaming to size. Shims are not provided
for adjustment since worn bearings are readily re-
placed with new bearings of proper size. Bearings for
service replacement are furnished in standard size
and undersizes. Under no circumstances should
crankshaft bearing caps be tiIed to adjust for wear in
old bearing.After removal of oil pan, pipe and screen assembly,
perform the following removal, inspection and in-
stallation operations on each crankshaft bearing in
turn so that the crankshaft will be well supported by
the other bearings.
If crankshaft has been removed to check straightness
the following procedure is suggested. Rest crank-
shaft on “V-blocks” at number one and number live
main bearing journals. Check indicator runout at
No. 3 main bearing journal. Total indicator reading
should not exceed
.C012”.1. Since any service condition which affects the
crankshaft bearings may also affect the connecting
rod bearings, it is advisable to inspect connecting rod
bearings
first. If crankpins are worn to the extent
that crankshaft should be replaced or reground, re-
placement of crankshaft bearings only will not be
satisfactory.
If replacement of cylinder block or crankshaft is re-
quired, always check main bearing clearance with
plastic-type gauge to obtain specified limits.
2. Remove one bearing cap, then clean and inspect
lower bearing shell and the crankshaft journal. If
journal surface is scored or ridged, the crankshaft
must be replaced or reground to insure satisfactory
operation with new bearings. Slight roughness may
be polished out with tine grit polishing cloth
thoroughly wetted with engine oil, and burrs may be
honed off with a tine stone.
3. If condition of lower bearing shell and crankshaft
journal is satisfactory, check the bearing clearance
with a plastic-type gauge.
4. When checking a crankshaft bearing with plastic-
type gauging material, turn crankshaft so that oil
hole is up to avoid dripping of oil on the gauge
material. Place paper shims in lower halves of adja-
cent bearings and tighten cap bolts to take the weight
of crankshaft
off the lower shell of beating being
checked.5. If bearing clearance exceeds
.C03”, it is advisable
to install a new bearing; however, if bearing is in
good condition and is not being checked because ofbearing noise, it is not necessary to replace the bear-
ing.6. Loosen all crankshaft bearing cap bolts
l/2 turn,
and remove cap of bearing to be replaced.
7. Remove upper bearing shell by inserting Bearing
Shell Remover and Installer J-8080 in oil hole in
crankshaft, then slowly turning crankshaft so that
the tool rotates the shell out of place by pushing
against the end without the tang. See Figure
6A-27.When turning crankshaft with rear bearing cap
removed hold oil seal to prevent it from rotating out
of position in crankcase.
8. The crankshaft journal cannot be measured with
an outside micrometer when shaft is in place; how-
ever, when upper bearing shell is removed the jour-
nal may be checked for out-of-round by using a
special crankshaft caliper and inside micrometer.
Figure 6A-27 Removing and Installing Crankshaft
Bearing Upper Shell
The caliper should not be applied to journal in line
with oil hole.
If crankshaft journal is more than
.M)12” out-of-
round, the crankshaft should be replaced since the
full mileage cannot be expected from bearings used
with an excessively out-of-round crankshaft.
9. Before installation of bearing shells make sure that
crankshaft journal and the bearing seats in crankcase
and cap are thoroughly cleaned.
10. Coat inside surface of upper bearing shell with
engine oil and place shell against crankshaft journal
so that tang on shell will engage notch in crankcase
when shell is rotated into place.
11. Rotate bearing shell into place as far as possible
by hand, then insert Installer J-8080 in crankshaft oil
hole and rotate crankshaft to push shell into place.
Bearing shell should move into place with very little
Page 309 of 625
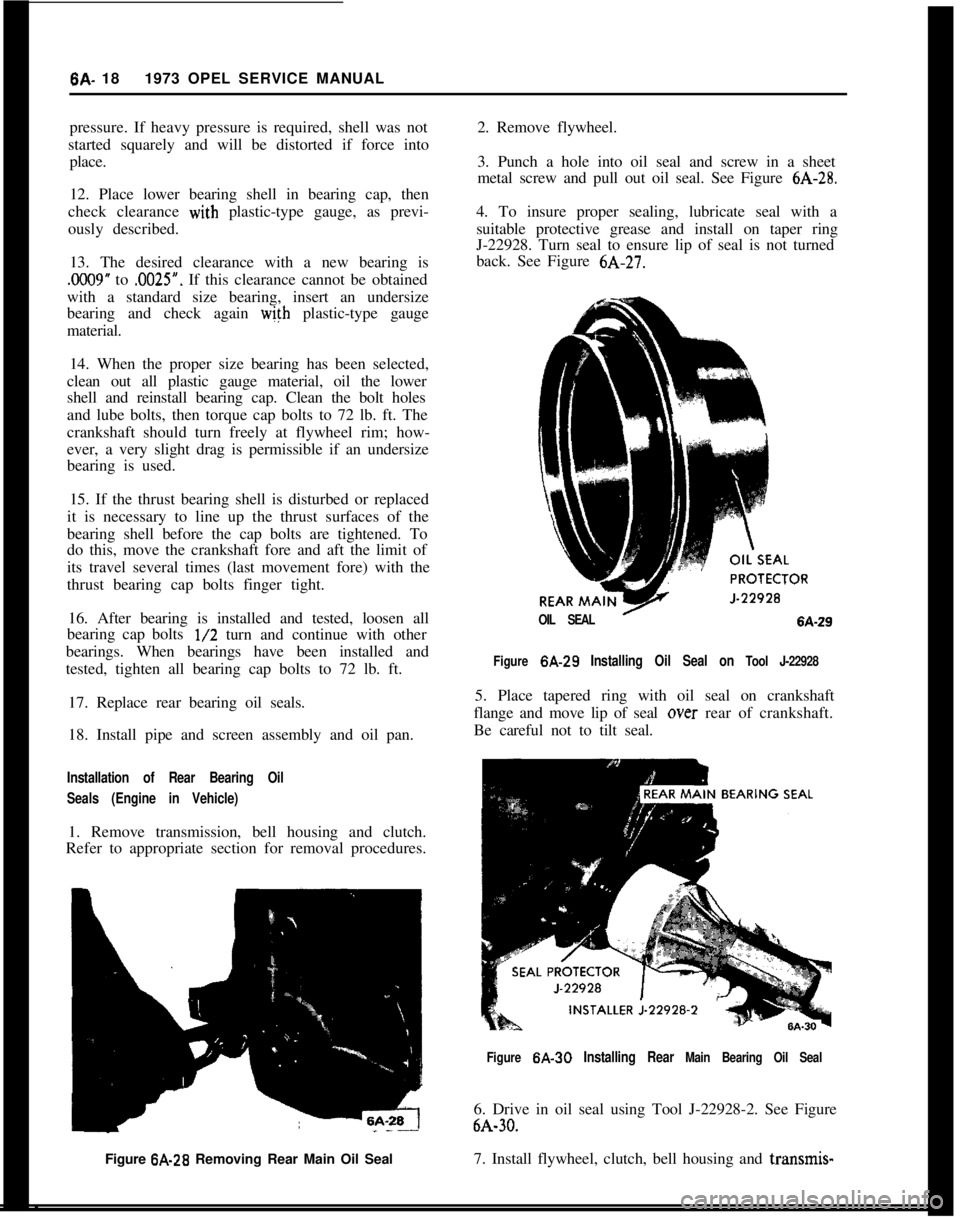
6A- 18 1973 OPEL SERVICE MANUAL
pressure. If heavy pressure is required, shell was not
started squarely and will be distorted if force into place.
12. Place lower bearing shell in bearing cap, then
check clearance
with plastic-type gauge, as previ-
ously described.
13. The desired clearance with a new bearing is
.0009” to .0025”. If this clearance cannot be obtained
with a standard size bearing, insert an undersize
bearing and check again
w&h plastic-type gauge
material.
14. When the proper size bearing has been selected,
clean out all plastic gauge material, oil the lower
shell and reinstall bearing cap. Clean the bolt holes
and lube bolts, then torque cap bolts to 72 lb. ft. The
crankshaft should turn freely at flywheel rim; how-
ever, a very slight drag is permissible if an undersize
bearing is used.
15. If the thrust bearing shell is disturbed or replaced
it is necessary to line up the thrust surfaces of the
bearing shell before the cap bolts are tightened. To
do this, move the crankshaft fore and aft the limit of
its travel several times (last movement fore) with the
thrust bearing cap bolts finger tight.
16. After bearing is installed and tested, loosen all
bearing cap bolts
l/2 turn and continue with other
bearings. When bearings have been installed and
tested, tighten all bearing cap bolts to 72 lb. ft.
17. Replace rear bearing oil seals.
18. Install pipe and screen assembly and oil pan.
Installation of Rear Bearing Oil
Seals (Engine in Vehicle)
1. Remove transmission, bell housing and clutch.
Refer to appropriate section for removal procedures.
Figure 6A-28 Removing Rear Main Oil Seal
2. Remove flywheel.
3. Punch a hole into oil seal and screw in a sheet
metal screw and pull out oil seal. See Figure
6A-28.
4. To insure proper sealing, lubricate seal with a
suitable protective grease and install on taper ring
J-22928. Turn seal to ensure lip of seal is not turned
back. See Figure
6A-27.
OIL SEAL’6A-29
Figure
6A-29 Installing Oil Seal on Tool J-22928
5. Place tapered ring with oil seal on crankshaft
flange and move lip of seal
over rear of crankshaft.
Be careful not to tilt seal.
Figure 6A-30 Installing Rear Main Bearing Oil Seal
6. Drive in oil seal using Tool J-22928-2. See Figure
6A-30.
7. Install flywheel, clutch, bell housing and transmis-
.
Page 310 of 625
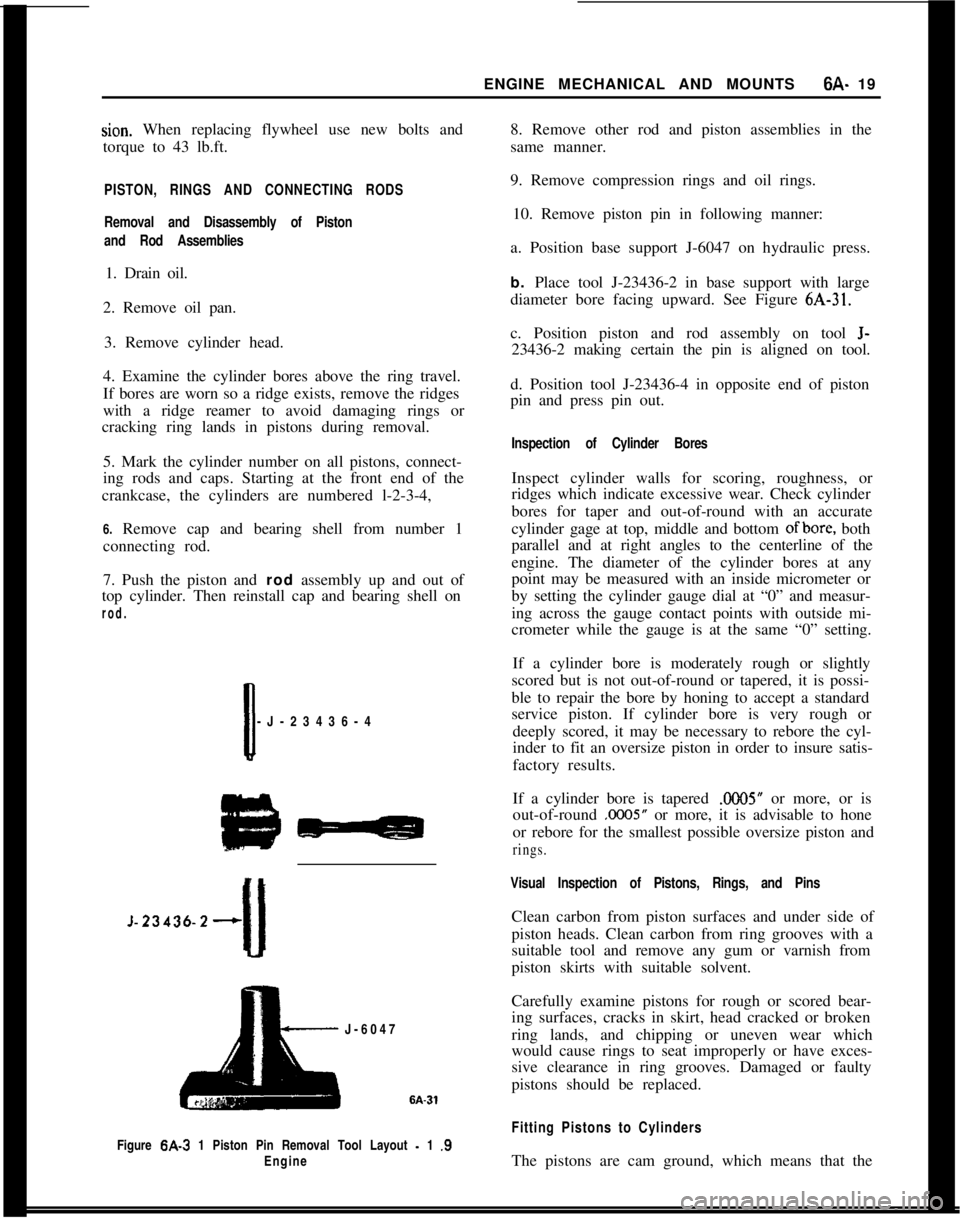
ENGINE MECHANICAL AND MOUNTS6A- 19
sion. When replacing flywheel use new bolts and
torque to 43 lb.ft.
PISTON, RINGS AND CONNECTING RODS
Removal and Disassembly of Piston
and Rod Assemblies
1. Drain oil.
2. Remove oil pan. 3. Remove cylinder head.
4. Examine the cylinder bores above the ring travel.
If bores are worn so a ridge exists, remove the ridges
with a ridge reamer to avoid damaging rings or
cracking ring lands in pistons during removal.
5. Mark the cylinder number on all pistons, connect-
ing rods and caps. Starting at the front end of the
crankcase, the cylinders are numbered l-2-3-4,
6. Remove cap and bearing shell from number 1
connecting rod.
7. Push the piston and
rod assembly up and out of
top cylinder. Then reinstall cap and bearing shell on
rod.
0
-J-23436-4
J-23436-2+
J-6047
Figure
6A-3 1 Piston Pin Removal Tool Layout - 1 .S
Engine
8. Remove other rod and piston assemblies in the
same manner.
9. Remove compression rings and oil rings.
10. Remove piston pin in following manner:
a. Position base support J-6047 on hydraulic press.
b. Place tool J-23436-2 in base support with large
diameter bore facing upward. See Figure
6A-31.
c. Position piston and rod assembly on tool
J-
23436-2 making certain the pin is aligned on tool.
d. Position tool J-23436-4 in opposite end of piston
pin and press pin out.
Inspection of Cylinder Bores
Inspect cylinder walls for scoring, roughness, or
ridges which indicate excessive wear. Check cylinder
bores for taper and out-of-round with an accurate
cylinder gage at top, middle and bottom
ofbore, both
parallel and at right angles to the centerline of the
engine. The diameter of the cylinder bores at any
point may be measured with an inside micrometer or
by setting the cylinder gauge dial at “0” and measur-
ing across the gauge contact points with outside mi-
crometer while the gauge is at the same “0” setting.
If a cylinder bore is moderately rough or slightly
scored but is not out-of-round or tapered, it is possi-
ble to repair the bore by honing to accept a standard
service piston. If cylinder bore is very rough or deeply scored, it may be necessary to rebore the cyl-
inder to fit an oversize piston in order to insure satis-
factory results.
If a cylinder bore is tapered
.ooO5” or more, or is
out-of-round
.0005” or more, it is advisable to hone
or rebore for the smallest possible oversize piston and
rings.
Visual Inspection of Pistons, Rings, and Pins
Clean carbon from piston surfaces and under side of
piston heads. Clean carbon from ring grooves with a
suitable tool and remove any gum or varnish from
piston skirts with suitable solvent.
Carefully examine pistons for rough or scored bear-
ing surfaces, cracks in skirt, head cracked or broken
ring lands, and chipping or uneven wear which
would cause rings to seat improperly or have exces-
sive clearance in ring grooves. Damaged or faulty
pistons should be replaced.
Fitting Pistons to Cylinders
The pistons are cam ground, which means that the