MAZDA PROTEGE 1992 Workshop Manual
Manufacturer: MAZDA, Model Year: 1992, Model line: PROTEGE, Model: MAZDA PROTEGE 1992Pages: 1164, PDF Size: 81.9 MB
Page 391 of 1164
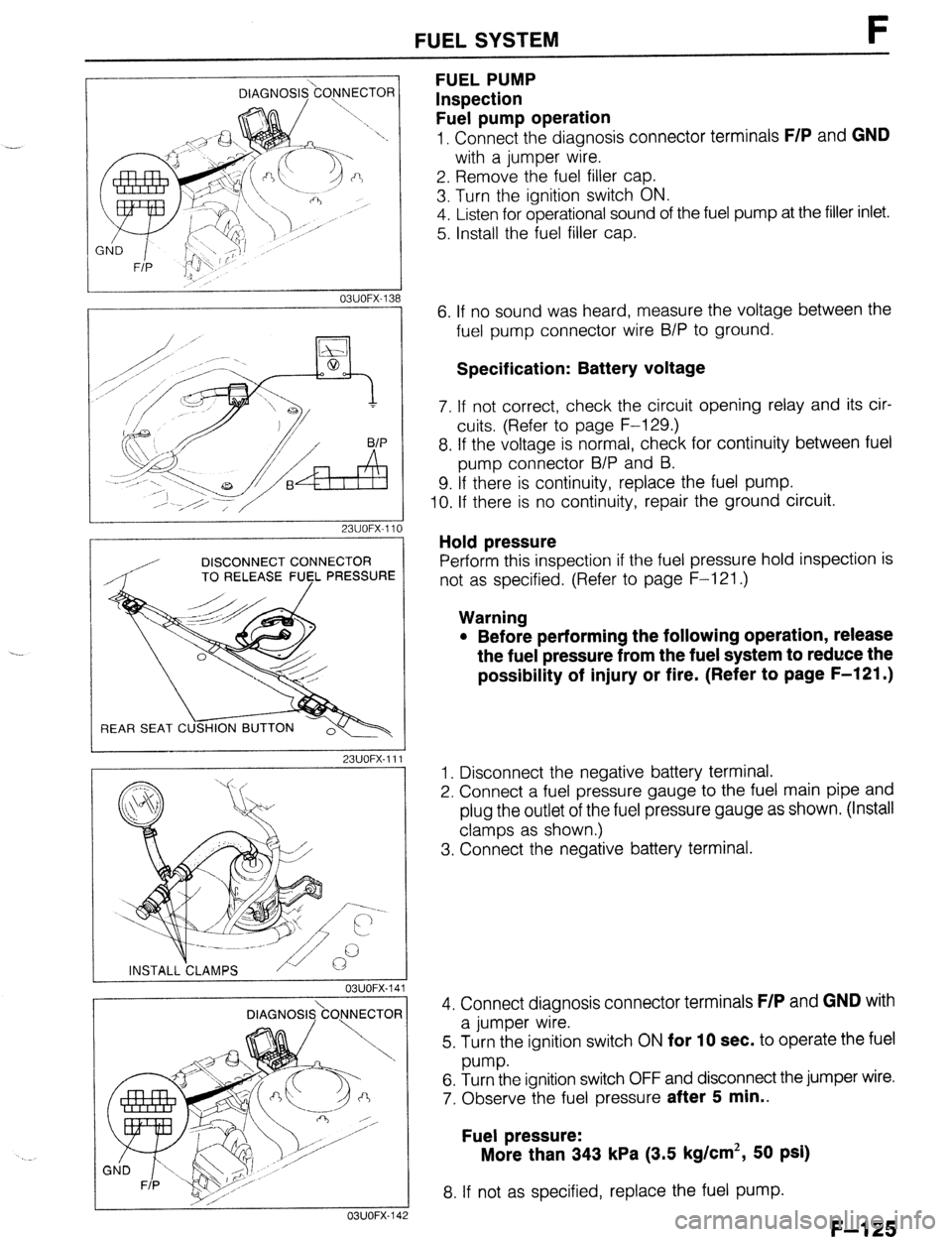
FUEL SYSTEM F
DIAGNOSI&ONNECTOR
03UOFX-138
I I 23UOFX-110
,
DISCONNECT CONNECTOR
REAR SEAT C
23UOFX-11
03UOFX-11
OBUOFX-11
FUEL PUMP
Inspection
Fuel pump operation
1, Connect the diagnosis connector terminals F/P and GND
with a jumper wire.
2. Remove the fuel filler cap.
3. Turn the ignition switch ON.
4. Listen for operational sound of the fuel pump at the filler inlet.
5. Install the fuel filler cap.
6. If no sound was heard, measure the voltage between the
fuel pump connector wire B/P to ground.
Specification: Battery voltage
7. If not correct, check the circuit opening relay and its cir-
cuits (Refer to page F-129.)
8. If the voltage is normal, check for continuity between fuel
pump connector B/P and B.
9. If there is continuity, replace the fuel pump.
IO. If there is no continuity, repair the ground circuit.
Hold pressure
Perform this inspection if the fuel pressure hold inspection is
not as specified. (Refer to page F-121 .)
Warning
l Before performing the following operation, release
the fuel pressure from the fuel system to reduce the
possibility of injury or fire. (Refer to page F-121 .)
1. Disconnect the negative battery terminal.
2. Connect a fuel pressure gauge to the fuel main pipe and
plug the outlet of the fuel pressure gauge as shown. (Install
clamps as shown.)
3. Connect the negative battery terminal.
4. Connect diagnosis connector terminals
F/P and GND with
a jumper wire.
5. Turn the ignition switch ON
for 10 sec. to operate the fuel
w-w.
6. Turn the ignition switch OFF and disconnect the jumper wire.
7. Observe the fuel pressure
after 5 min..
Fuel pressure:
More than 343 kPa (3.5 kg/cm’, 50 psi)
8. If not as specified, replace the fuel pump.
F-l 25
Page 392 of 1164
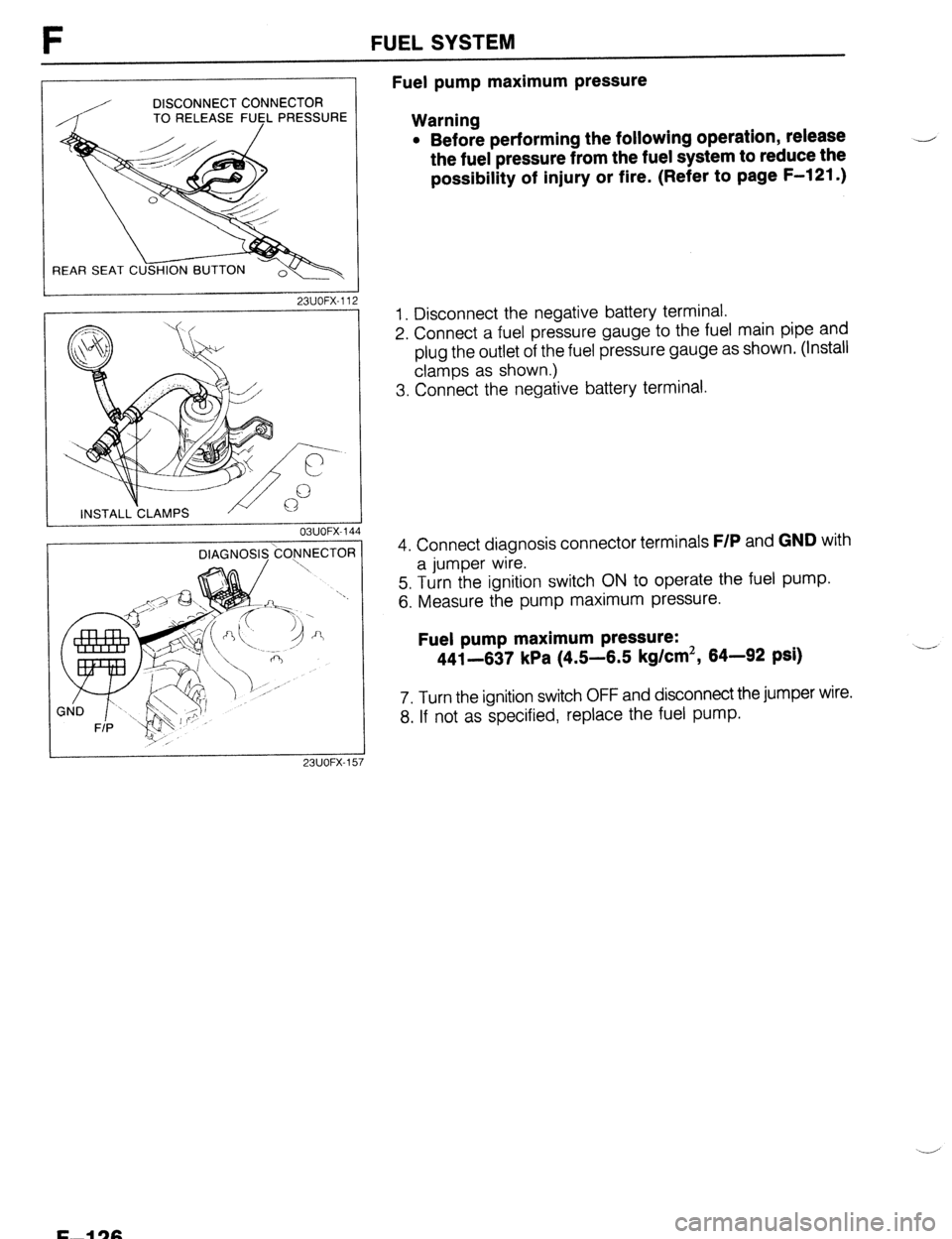
FUEL SYSTEM
Fuel pump maximum pressure
DISCONNECT CONNECTOR
TO RELEASE FUCL PRESSURE
Warning
23UOFX-11
OBUOFX-144 l
Before performing the following operation, release
the fuel pressure from the fuel system to reduce the
possibility of injury or fire. (Refer to page F-121 .) 4
1
2
23UOFX-15 7
1. Disconnect the negative battery terminal.
2. Connect a fuel pressure gauge to the fuel main pipe and
plug the outlet of the fuel pressure gauge as shown. (Install
clamps as shown.)
3. Connect the negative battery terminal.
4. Connect diagnosis connector terminals
F/P and GND with
a jumper wire.
5. Turn the ignition switch ON to operate the fuel pump.
6. Measure the pump maximum pressure.
Fuel pump maximum pressure:
441-637 kPa (4.5-6.5 kg/cm2, 64-92 psi) .--
7. Turn the ignition switch OFF and disconnect the jumper wire.
8. If not as specified, replace the fuel pump.
F-l 26
Page 393 of 1164
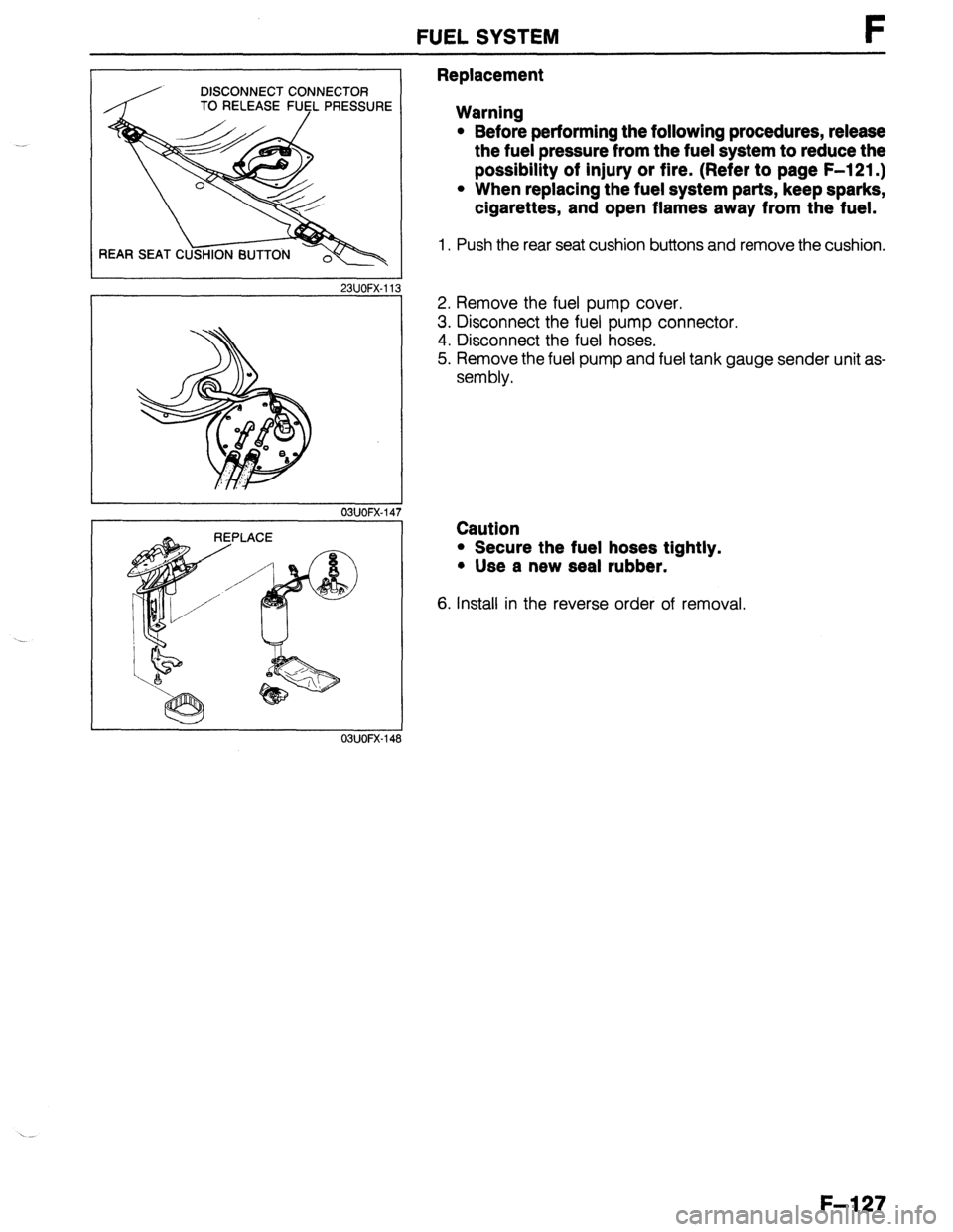
FUEL SYSTEM F
DISCONNECT CONNECTOR
TO RELEASE FU5L PRESSURE
REAR SEAT C
23UOFX-11:
REPLACE
03UOFX-14s Replacement
Warning
l Before performing the following procedures, release
the fuel pressure from the fuel system to reduce the
possibility of injury or fire. (Refer to page F-121 .)
l When replacing the fuel system parts, keep sparks,
cigarettes, and open flames away from the fuel.
1. Push the rear seat cushion buttons and remove the cushion.
2. Remove the fuel pump cover.
3. Disconnect the fuel pump connector.
4. Disconnect the fuel hoses.
5. Remove the fuel pump and fuel tank gauge sender unit as-
sembly.
Caution
l Secure the fuel hoses tightly.
+ Use a new seal rubber.
6. Install in the reverse order of removal.
F-l 27
Page 394 of 1164
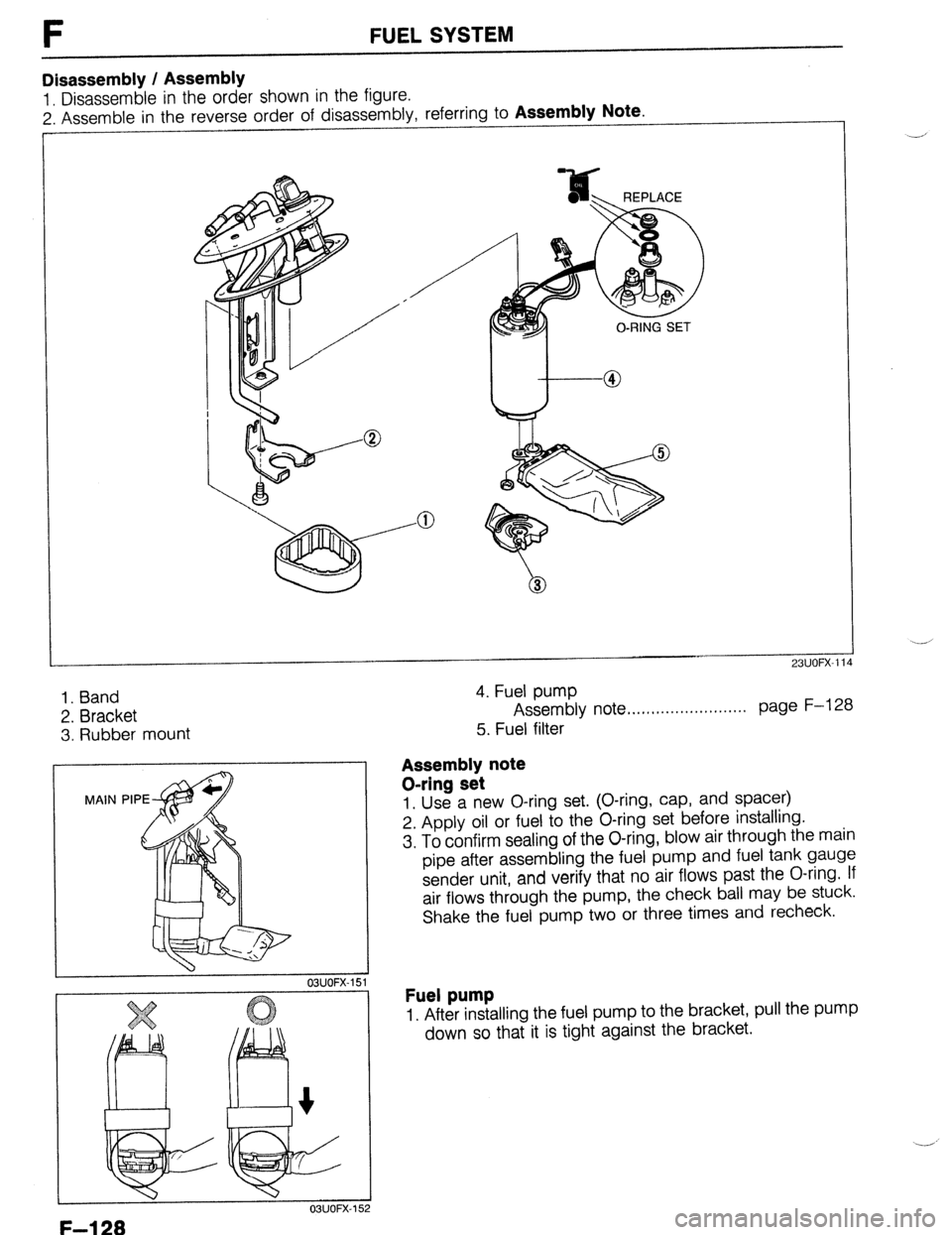
F FUELSYSTEM
Disassembly / Assembly
1. Disassemble in the order shown in the figure.
2. Assemble in the reverse order of disassembly, referring to
Assembly Note
1. Band
2. Bracket
3. Rubber mount
OSUOFX-152
4. Fuel pump
Assembly note ,..........,....,,....,.. page F-l 28
5. Fuel filter
Assembly note
O-ring set
1. Use a new O-ring set. (O-ring, cap, and spacer)
2. Apply oil or fuel to the O-ring set before installing.
3. To confirm sealing of the O-ring, blow air through the main
pipe after assembling the fuel pump and fuel tank gauge
sender unit, and verify that no air flows past the O-ring. If
air flows through the pump, the check ball may be stuck.
Shake the fuel pump two or three times and recheck.
Fuel pump
1. After installing the fuel pump to the bracket, pull the pump
down so that it is tight against the bracket.
F-l 28
Page 395 of 1164

FUEL SYSTEM F
STA
OBUOFX- 15
03UOFX-15
DISCONNECT CONNECTOR
TO RELEASE FUfL PRESSURE
REAR SEAT C
23UOFX-11
INSTALL CLAMPS
CIRCUIT OPENING RELAY
Inspection
Voltage inspection
I, Check voltage between the following terminals and a ground
using a voltmeter.
Ve: Battery voltage
Resistance inspection
1, Check resistance between the terminals using an ohmmeter.
Terminal Resistance (Q)
STA-El 21-43
B-Fc 109-226
B-Fp 00
Replacement
1, Remove the passenger side wall.
2. Disconnect the relay connector.
3. Remove the relay from ECU bracket.
4. Install in the reverse order of removal.
PRESSURE REGULATOR
Inspection
Fuel line pressure
Warning
l Before performing the following operation, release
the fuel pressure from the fuel system to reduce the
possibility of injury or fire. (Refer to page F-121.)
1, Disconnect the negative battery terminal.
2. Connect a fuel pressure gauge between the fuel filter and
the fuel main hose. (Install clamps as shown.)
3. Connect the negative battery terminal.
4. Start the engine and run it at idle.
5. Measure the fuel line pressure.
Fuel line pressure:
206-255 kPa (2.1-2.6 kg/cm2, 30-37 psi)
6. Disconnect the vacuum hose from the pressure regulator
and measure the fuel line pressure.
Fuel line pressure:
265-314 kPa (2.7-3.2 kg/cm2, 36-46 psi)
F-l 29
03UOFX-157
Page 396 of 1164
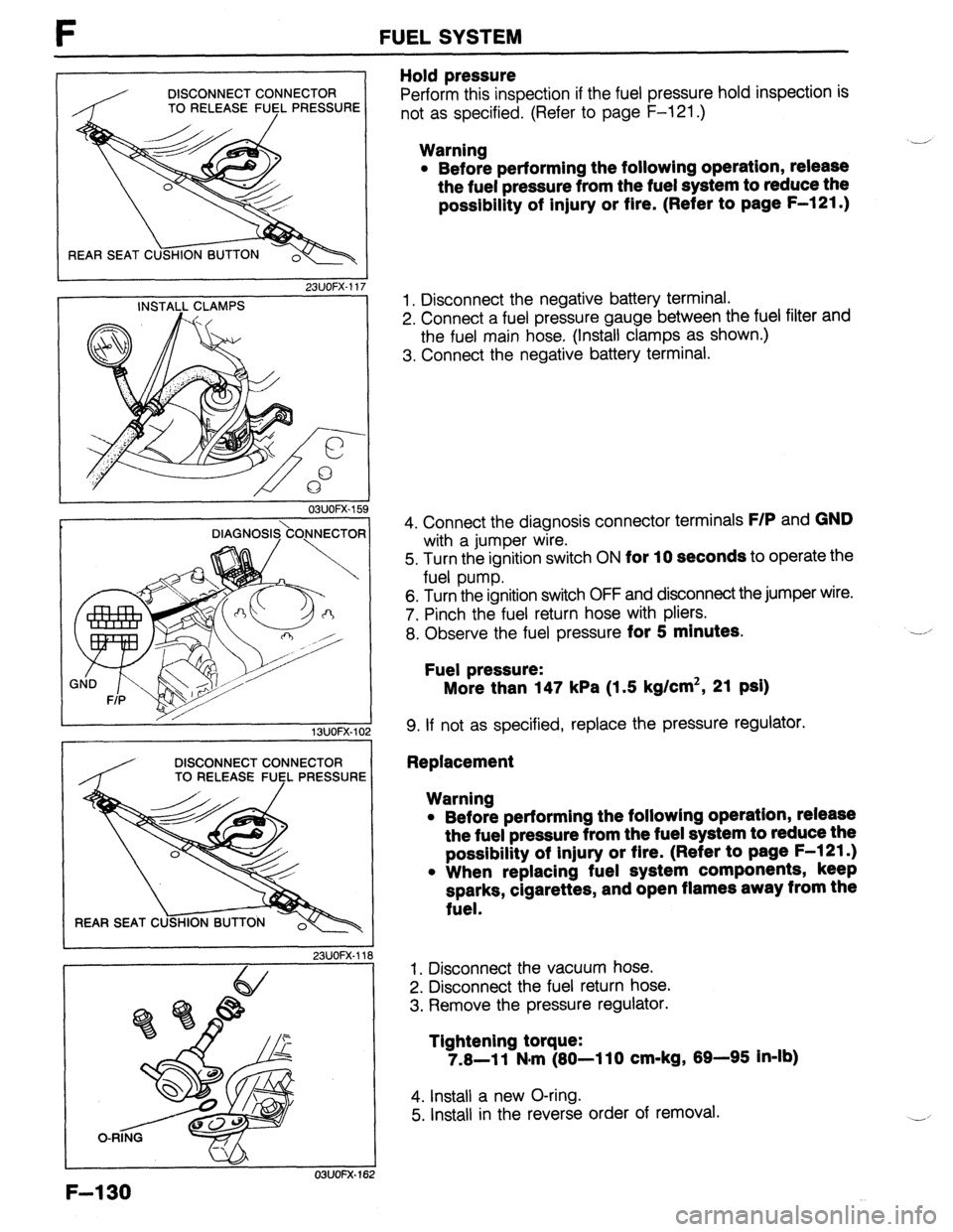
F FUELSYSTEM
DISCONNECT CONNECTOR
TO RELEASE FlJ$L PRESSURE
REAR SEAT C
23UOFX-11
INSTALL CLAMPS 7
03UOFX.I 59
F-l 30
DIAGNOSl&OJNECTOR
/ K
1 SUOFX-10
DISCONNECT CONNECTOR
TO RELEASE
FlJl$L PRESSURE
23UOFX-11
I
Hold pressure
Perform this inspection if the fuel pressure hold inspection is
not as specified. (Refer to page F-121 .)
Warning
l Before performing the following operation, release
the fuel pressure from the fuel system to reduce the
possibility of injury or fire. (Refer to page F-121 .) ,-
1. Disconnect the negative battery terminal.
2. Connect a fuel pressure gauge between the fuel filter and
the fuel main hose. (Install clamps as shown.)
3. Connect the negative battery terminal.
4. Connect the diagnosis connector terminals
F/P and GND
with a jumper wire.
5. Turn the ignition switch ON
for 10 seconds to operate the
fuel pump.
6. Turn the ignition switch OFF and disconnect the jumper wire.
7. Pinch the fuel return hose with pliers.
8. Observe the fuel pressure
for 5 minutes.
Fuel pressure:
More than 147 kPa (1.5 kg/cm2, 21 psi)
9. If not as specified, replace the pressure regulator.
Replacement
Warning
l Before performing the followlng operation, release
the fuel pressure from the fuel system to reduce the
possibility of injury or flre. (Refer to page F-l 21.)
l When replacing fuel system components, keep
sparks, cigarettes, and open flames away from the
fuel.
1. Disconnect the vacuum hose.
2. Disconnect the fuel return hose.
3. Remove the pressure regulator.
Tightening torque:
7.8-11 N#m (80-110 cm-kg, 89-95 In-lb)
4. Install a new O-ring.
5. Install in the reverse order of removal.
Page 397 of 1164
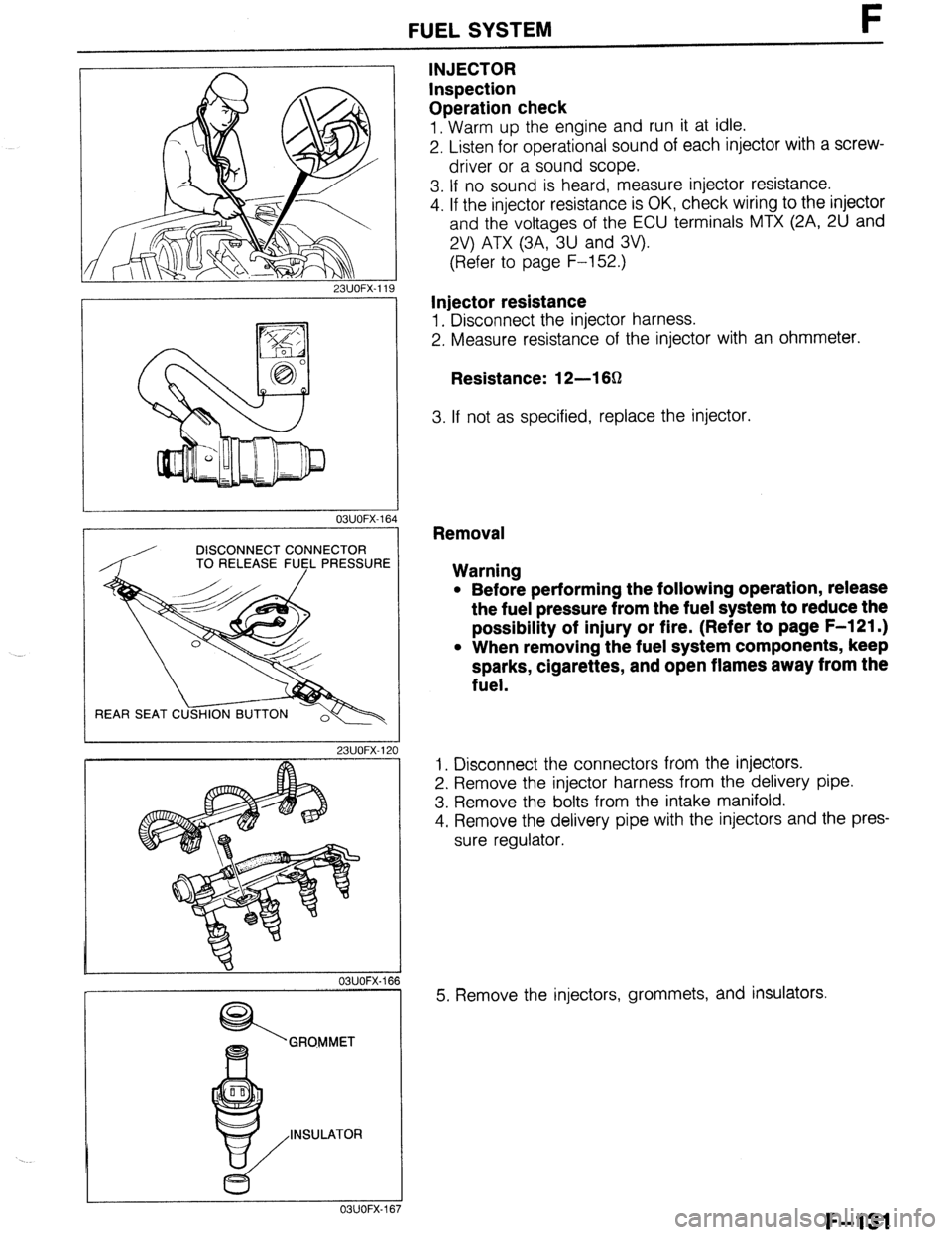
231JOFX-1
FUEL SYSTEM F
INJECTOR
Inspection
Operation check
1. Warm up the engine and run it at idle.
2. Listen for operational sound of each injector with a screw-
driver or a sound scope.
3. If no sound is heard, measure injector resistance.
4. If the injector resistance is OK, check wiring to the injector
and the voltages of the ECU terminals MTX (2A, 2U and
2V) ATX (3A, 3U and 3V).
(Refer to page F-152.)
Injector resistance
1. Disconnect the injector harness.
2. Measure resistance of the injector with an ohmmeter.
Resistance: 12-l 6Q
3. If not as specified, replace the injector.
03UOFX-1
DISCONNECT CONNECTOR
TO RELEASE FU5L PRESSUR
REAR SEAT C
23UOFX-1
OBUOFX-
GRQMMET
INSULATOR
c5
OSUOFX-
Removal
Warning
l Before performing the following operation, release
the fuel pressure from the fuel system to reduce the
possibility of injury or fire. (Refer to page F-121 .)
l When removing the fuel system components, keep
sparks, cigarettes, and open flames away from the
fuel.
1. Disconnect the connectors from the injectors.
2. Remove the injector harness from the delivery pipe.
3. Remove the bolts from the intake manifold.
4. Remove the delivery pipe with the injectors and the pres-
sure regulator.
5. Remove the injectors, grommets, and insulators.
F-131
Page 398 of 1164
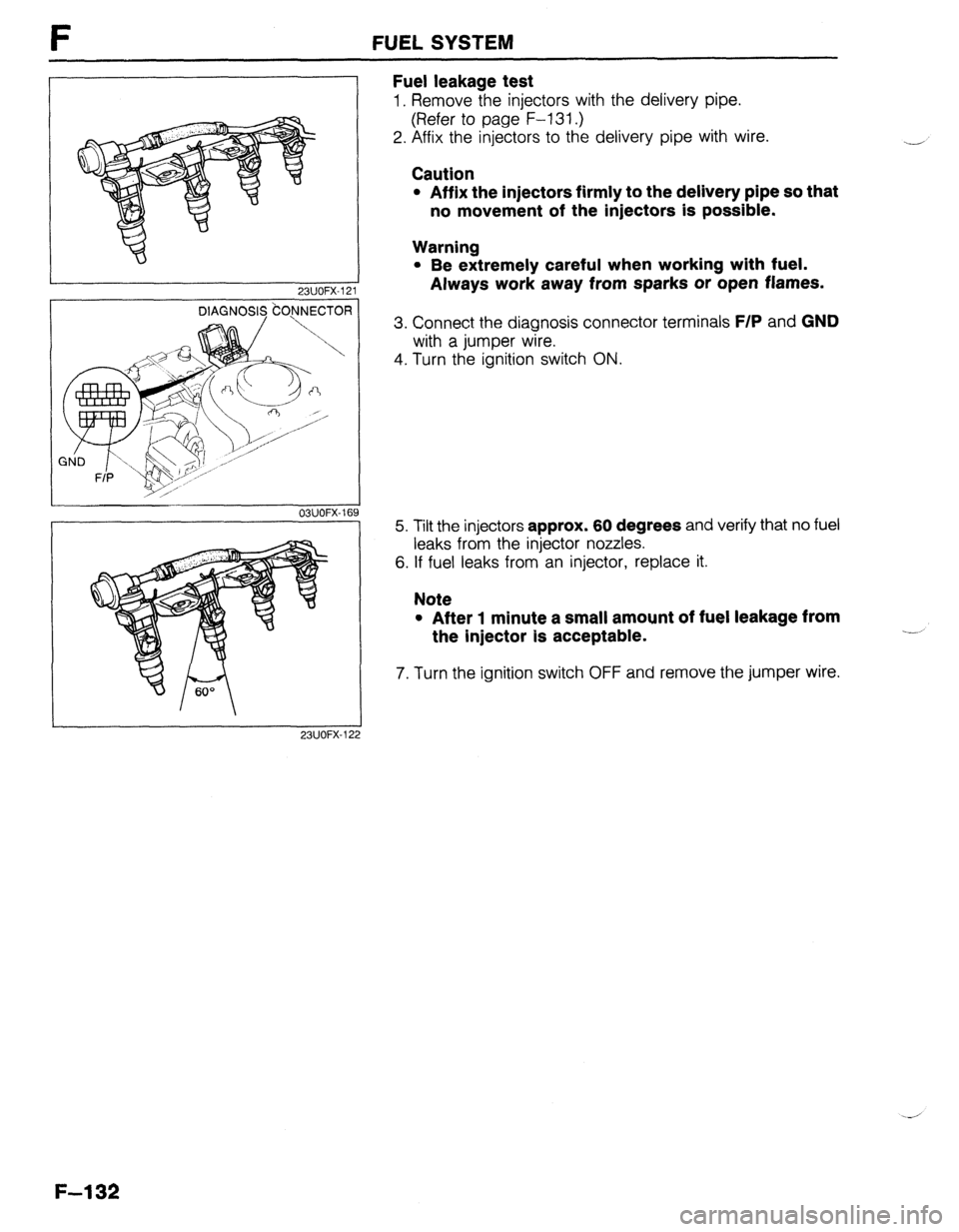
l Be extremely careful when working with fuel. I
23UOFX.121 Always work away from sparks or open flames.
3. Connect the diagnosis connector terminals F/P and GND
with a jumper wire.
FUEL SYSTEM
Fuel leakage test
1. Remove the injectors with the delivery pipe.
(Refer to page F-l 31.)
2. Affix the injectors to the delivery pipe with wire.
Caution
l Affix the injectors firmly to the delivery pipe so that
no movement of the injectors is possible.
-
Warning
4. Turn the ignition switch ON.
03UOFX-16’
23UOFX-12 9 5. Tilt the injectors approx. 60 degrees and verify that no fuel
leaks from the injector nozzles.
6. If fuel leaks from an injector, replace it.
Note
l After 1 minute a small amount of fuel leakage from
the injector Is acceptable.
7. Turn the ignition switch OFF and remove the jumper wire.
-i
F-l 32
Page 399 of 1164
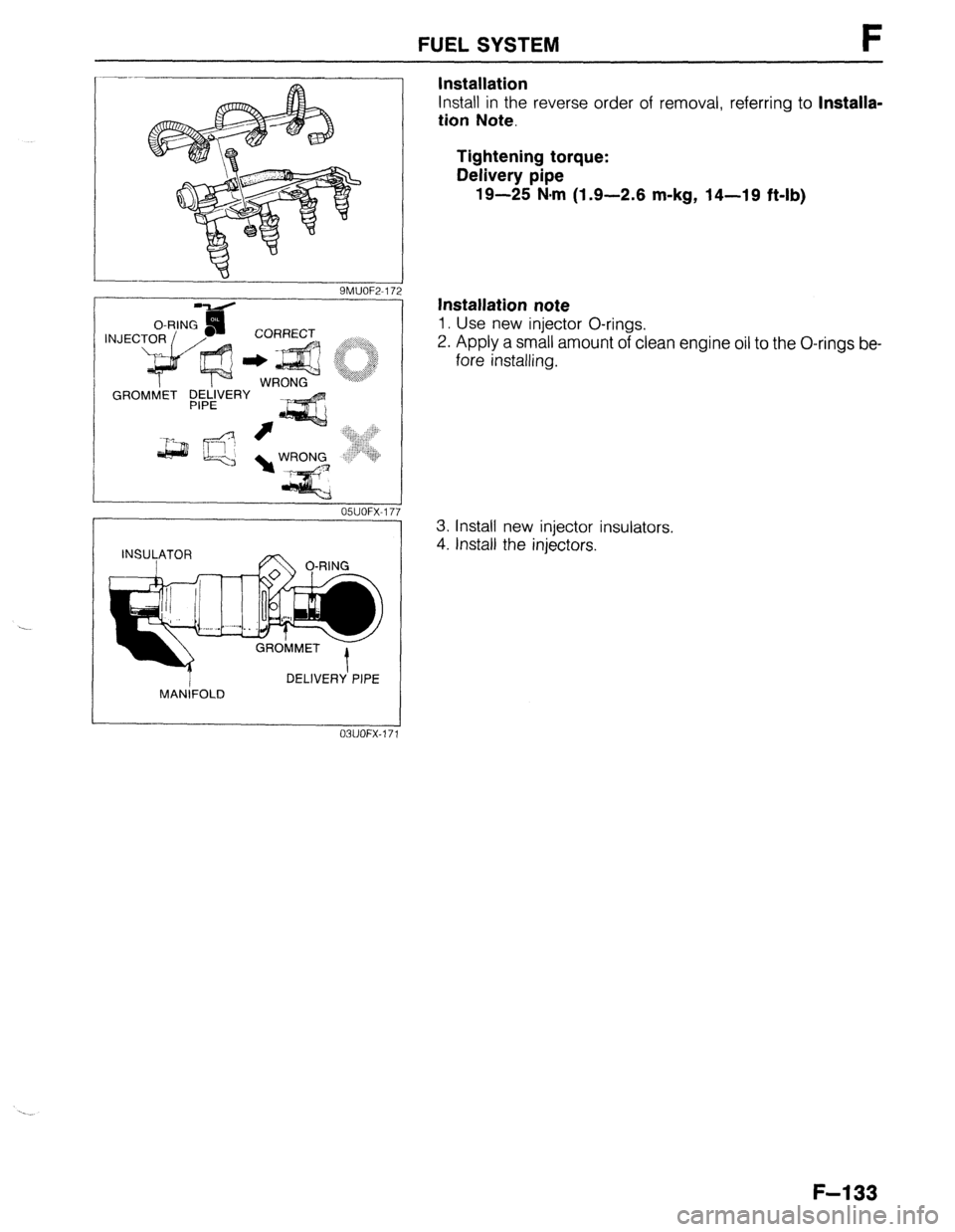
FUEL SYSTEM I-
9MUOF2-17
INJEC
GRO
,:.: ‘.L.. :
,;:y :.*‘.
+:: ..y&
..: .:: ,: ,:y>
‘$pID~~ :i
..,..:,:,
,.,i. :)I,
./[::/: :
. ...:;.
/jj,.‘, ;.::,::
.’ .::: ij!/ji..
OSUOFX-17
T MANIFOLD DELIVERY’ PIPE
MUOFX-17
Installation
Install in the reverse order of removal, referring to Installa-
tion Note.
Tightening torque:
Delivery pipe
19-25 N.m (1.9-2.6 m-kg, 14-19 ft-lb)
Installation note
1. Use new injector O-rings.
2. Apply a small amount of clean engine oil to the O-rings be-
fore installing.
3. Install new injector insulators.
4. Install the injectors.
F-l 33
Page 400 of 1164
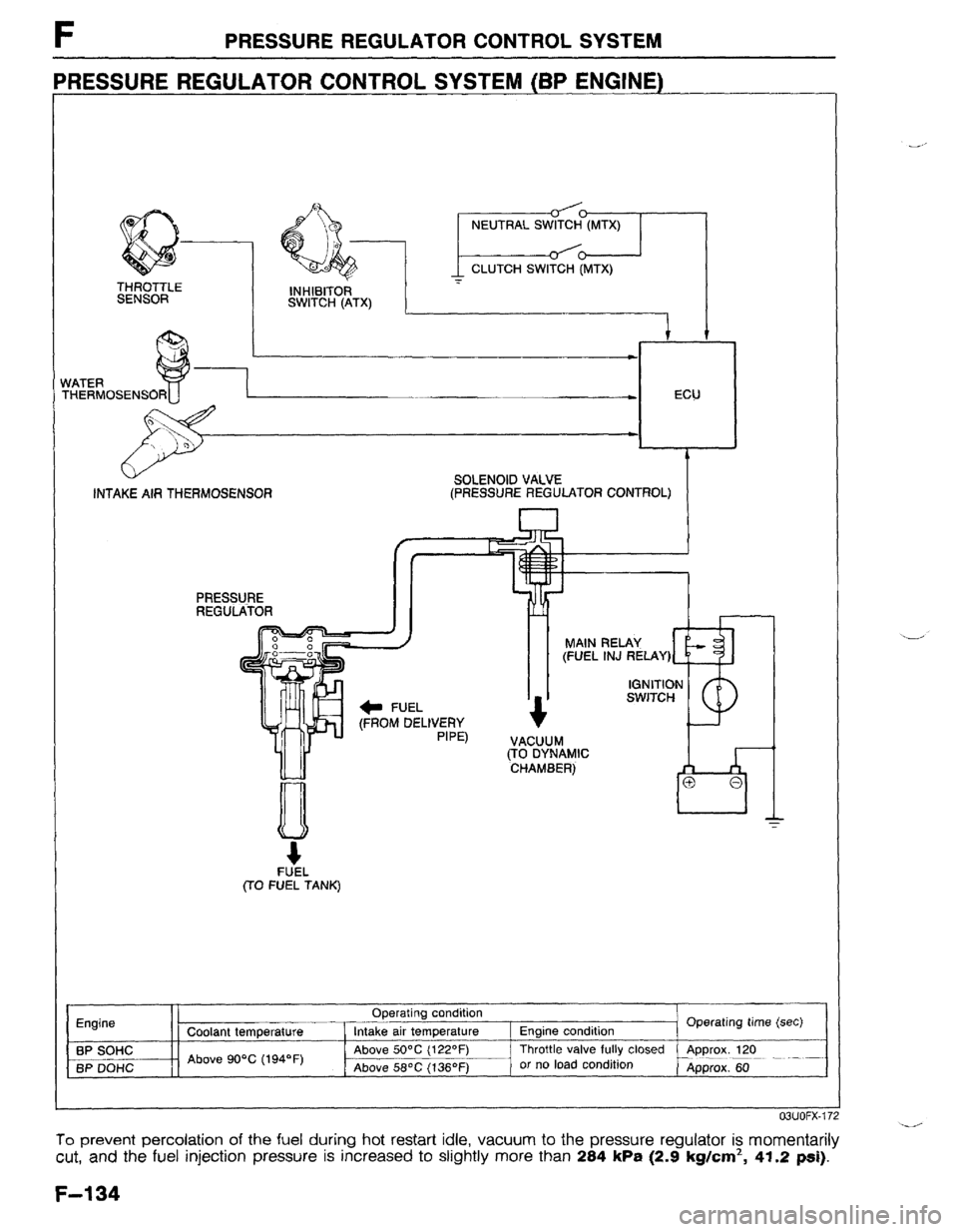
F PRESSURE REGULATOR CONTROL SYSTEM
PRESSURE REGULATOR CONTROL SYSTEM (BP ENGINE)
THERMOSEN
SOLENOID VALVE
(PRESSURE REGULATOR CONTROL)
(FROM DELIVERY
FUEL
(TO FUEL TANK)
Engine
BP SOHC
BP DOHC Coolant temperature
Above 90% (194*F) Operating condition
Intake air temperature
Above 50°C (122OF)
Above 58OC (136OF) Engine condition . Operating time (set)
Throttle valve fully closed
Approx. 120
or no load condition
Approx. 60
#.nr IAt-%/ 4 7
To prevent percolation of the fuel during hot restart idle, vacuum to the pressure regulator is momentarily
cut, and the fuel injection pressure is increased to slightly more than 284 kPa (2.9 kg/cm2, 41.2 psi).
F-l 34