MAZDA PROTEGE 1992 Workshop Manual
Manufacturer: MAZDA, Model Year: 1992, Model line: PROTEGE, Model: MAZDA PROTEGE 1992Pages: 1164, PDF Size: 81.9 MB
Page 381 of 1164
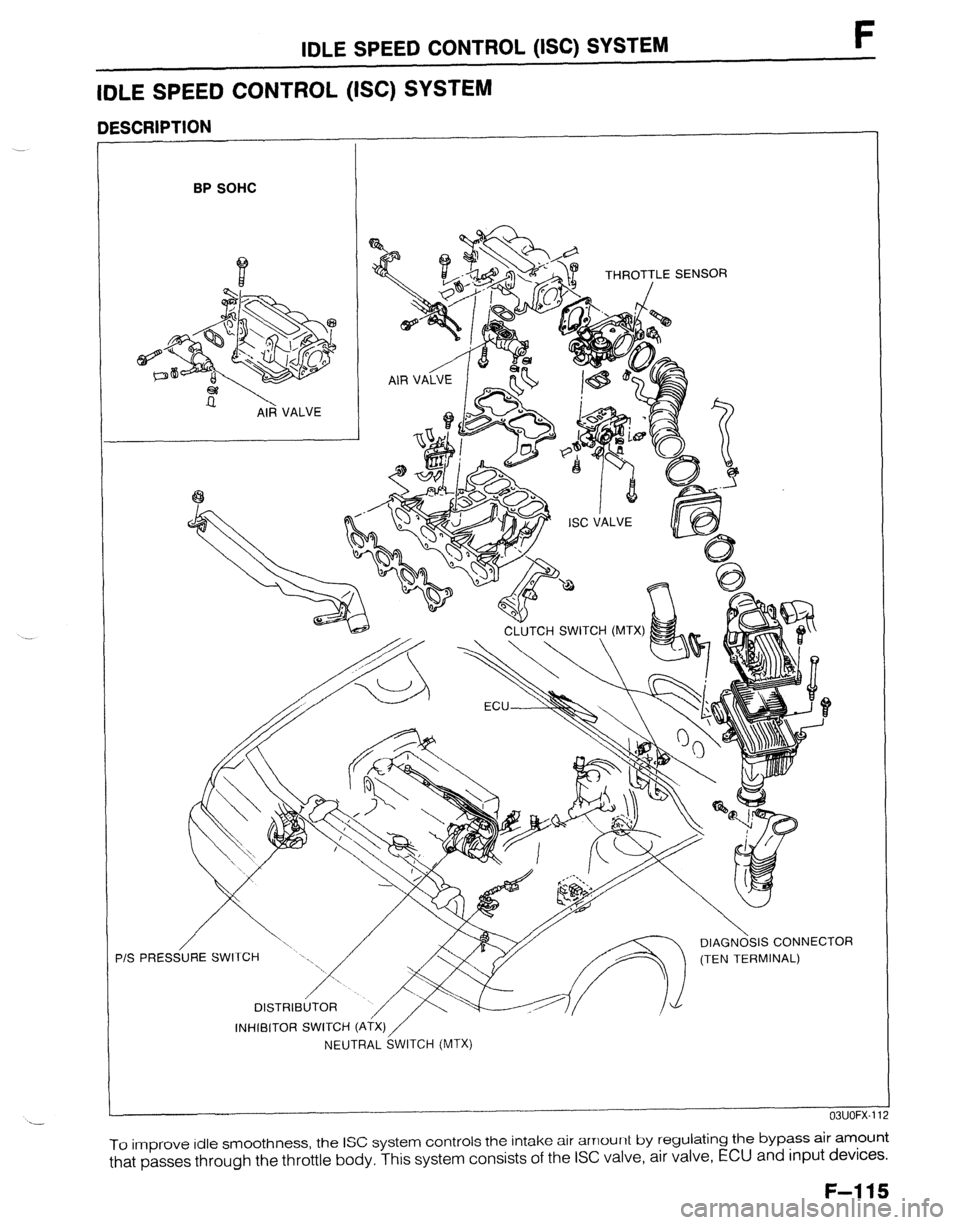
.-
IDLE SPEED CONTROL (ISC) SYSTEM I-
IDLE SPEED CONTROL (ISC) SYSTEM
DESCRIPTION
BP SOHC
AIR VALVE THROTTLE SENSOR
CLUTCH SWITCT (MTX)
‘IS PRESS/URE SWITCH ‘x.
. , SIS CONNECTt
(TEN TERMINAL)
DISTRIBUTOR
INHIEITOR SWITCH (ATX)/
NEUTRAL SWITCH (MTX) 3R
To improve idle smoothness, the ISC system controls the intake air amount by regulating the bypass air amount
that passes through the throttle body. This system consists of the ISC valve, air valve, ECU and input devices.
F-115
Page 382 of 1164
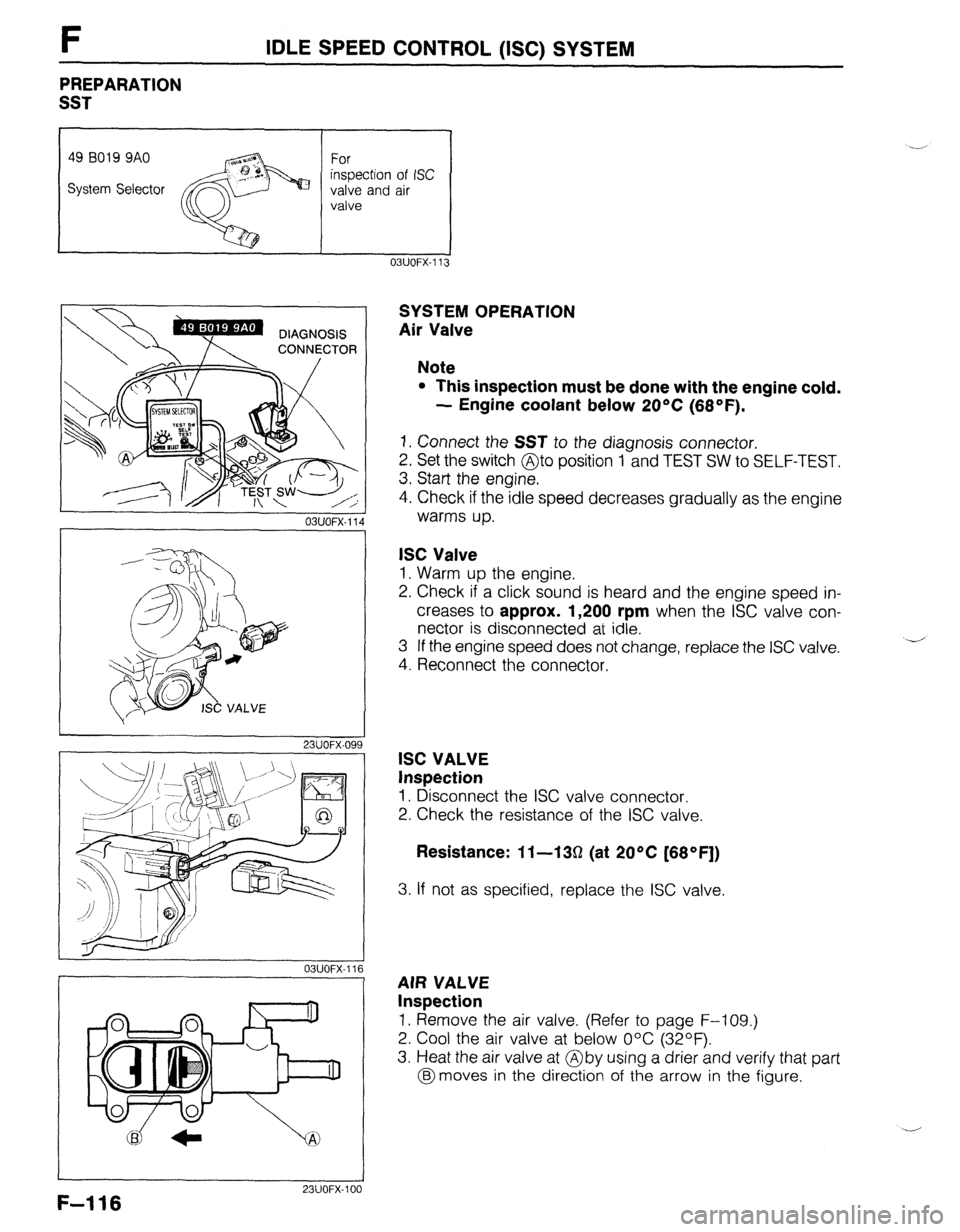
F IDLE SPEED CONTROL (ISC) SYSTEM
PREPARATION
SST
OBUOFX-113
OSUOFX-I 14
I
23UOFX-095
J 03UOFX-1 lf
23UOFX-101
F-116
SYSTEM OPERATION
Air Valve
Note
l This inspection must be done with the engine cold.
- Engine coolant below 20°C (68°F).
1. Connect the SST to the diagnosis connector.
2. Set the switch @to position 1 and TEST SW to SELF-TEST.
3. Start the engine.
4. Check if the idle speed decreases gradually as the engine
warms up.
ISC Valve
1. Warm up the engine.
2. Check if a click sound is heard and the engine speed in-
creases to approx. 1,200 rpm when the ISC valve con-
nector is disconnected at idle.
3 If the engine speed does not change, replace the ISC valve.
4. Reconnect the connector.
ISC VALVE
Inspection
1. Disconnect the ISC valve connector.
2. Check the resistance of the ISC valve.
Resistance: 11-130 (at 20°C [68*F])
3. If not as specified, replace the ISC valve.
AIR VALVE
Inspection
1. Remove the air valve. (Refer to page F-109.)
2. Cool the air valve at below O°C (32OF).
3. Heat the air valve at @by using a drier and verify that part
@moves in the direction of the arrow in the figure.
Page 383 of 1164
![MAZDA PROTEGE 1992 Workshop Manual VARIABLE INERTIA CHARGING SYSTEM (VI-)
VARIABLE INERTIA
CHARGING SYSTEM (VICS) [DOHC]
DESCRIPTION
VACUUM CHAMBER
SHUTTER VALVE ACTUATOR
F
THREE-WAY VALVE CLOSED
5,000 rpm
SHUTTER VALVE
BELOW MAZDA PROTEGE 1992 Workshop Manual VARIABLE INERTIA CHARGING SYSTEM (VI-)
VARIABLE INERTIA
CHARGING SYSTEM (VICS) [DOHC]
DESCRIPTION
VACUUM CHAMBER
SHUTTER VALVE ACTUATOR
F
THREE-WAY VALVE CLOSED
5,000 rpm
SHUTTER VALVE
BELOW](/img/28/57077/w960_57077-382.png)
VARIABLE INERTIA CHARGING SYSTEM (VI-)
VARIABLE INERTIA
CHARGING SYSTEM (VICS) [DOHC]
DESCRIPTION
VACUUM CHAMBER
SHUTTER VALVE ACTUATOR
F
THREE-WAY VALVE CLOSED
5,000 rpm
SHUTTER VALVE
BELOW 5,000 rpm ABOVE 5,000 rpm
SHUTTER VALVE CLOSED SHUTTER VALVE OPEN
By varying the length of the intake air path in the intake manifold and dynamic chamber, the resonance
induced inertia charging effect is improved, yielding higher torque and a wider torque band.
The length of the intake track is controlled within the intake manifold and dynamic chamber by opening and
closing the shutter valve at 5,000 rpm.
l-R; FCZz consists of the shutter valves, shutter valve actuator, three-way solenoid valve, vacuum chamber,
F-117
Page 384 of 1164
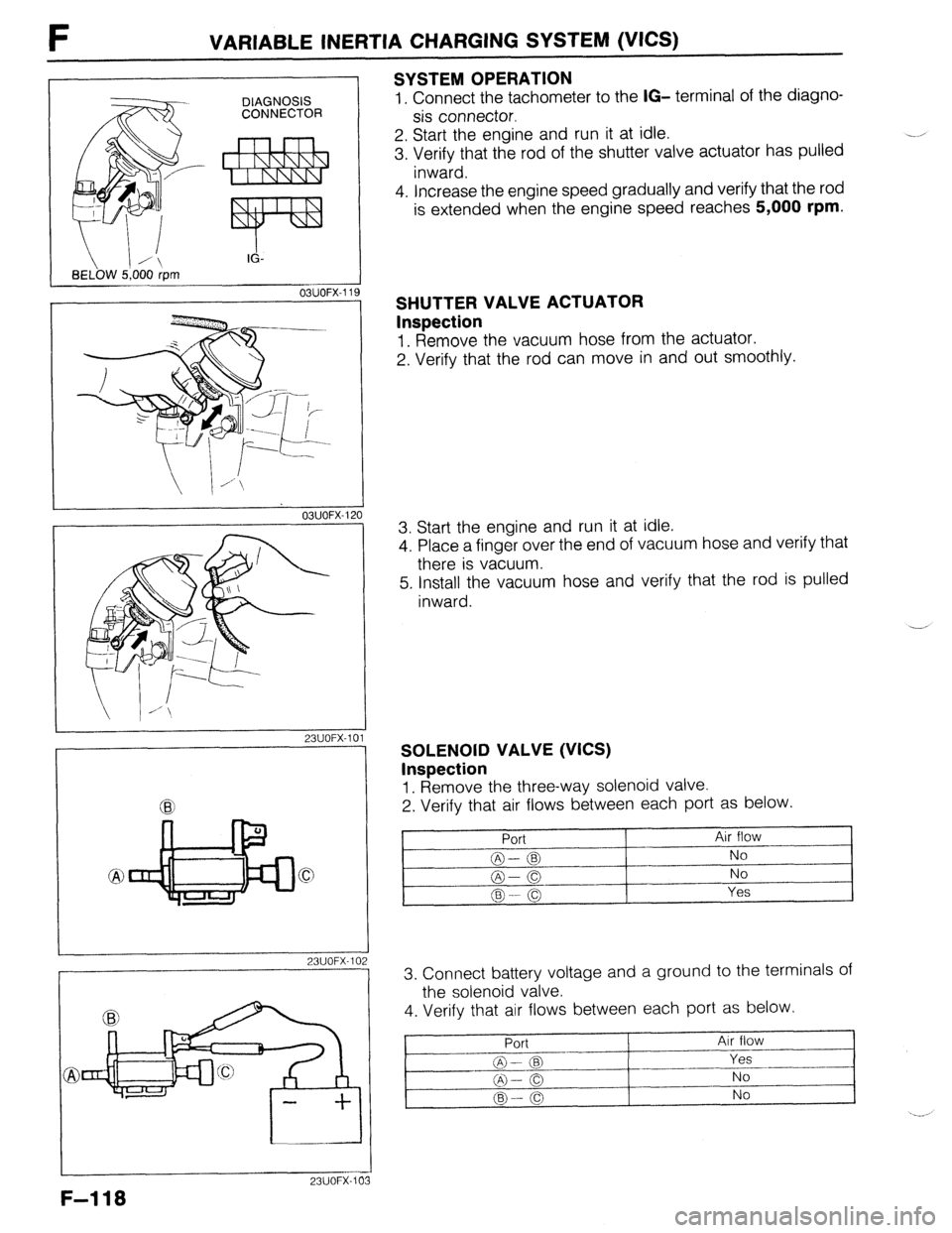
VARIABLE INERTIA CHARGING SYSTEM (VICS)
SYSTEM OPERATION
DIAGNOSIS 1. Connect the tachometer to the IG- terminal of the diagno- CONNECTOR sis connector.
2. Start the engine and run it at idle.
3. Verify that the rod of the shutter valve actuator has pulled -
inward.
OSUOFX-I 19
F-118
i-..
1”
03UOFX-I 2
23UOFX-1 C
23UOFX-1 C
23UOFX-IC
4. increase the engine speed gradually and verify that the rod
is extended when the engine speed reaches 5,000 rpm.
SHUTTER VALVE ACTUATOR
Inspection
1. Remove the vacuum hose from the actuator.
2. Verify that the rod can move in and out smoothly.
3. Start the engine and run it at idle.
4. Place a finger over the end of vacuum hose and verify that
there is vacuum.
5. Install the vacuum hose and verify that the rod is pulled
inward.
SOLENOID VALVE (VICS)
Inspection
1. Remove the three-way solenoid valve.
2. Verify that air flows between each port as below.
Port
@--@ - -
@-0
@ --- (g Air flow
No
No
Yes
3. Connect battery voltage and a ground to the terminals of
the solenoid valve.
4. Verify that air flows between each port as below.
Port Air flow
-_I
-I_
@- 03 Yes
@l-o No
@--0 No
Page 385 of 1164

VARIABLE INERTIA CHARGING SYSTEM (VICS) F
VACUUM CHAMBER
Inspection
1. Remove the vacuum chamber.
2. Blow through the vacuum chamber from the port @and
verify that air does not flow.
3. Blow through the vacuum chamber from the port @and
verify that air flows.
03UOFX-12
F-119
Page 386 of 1164
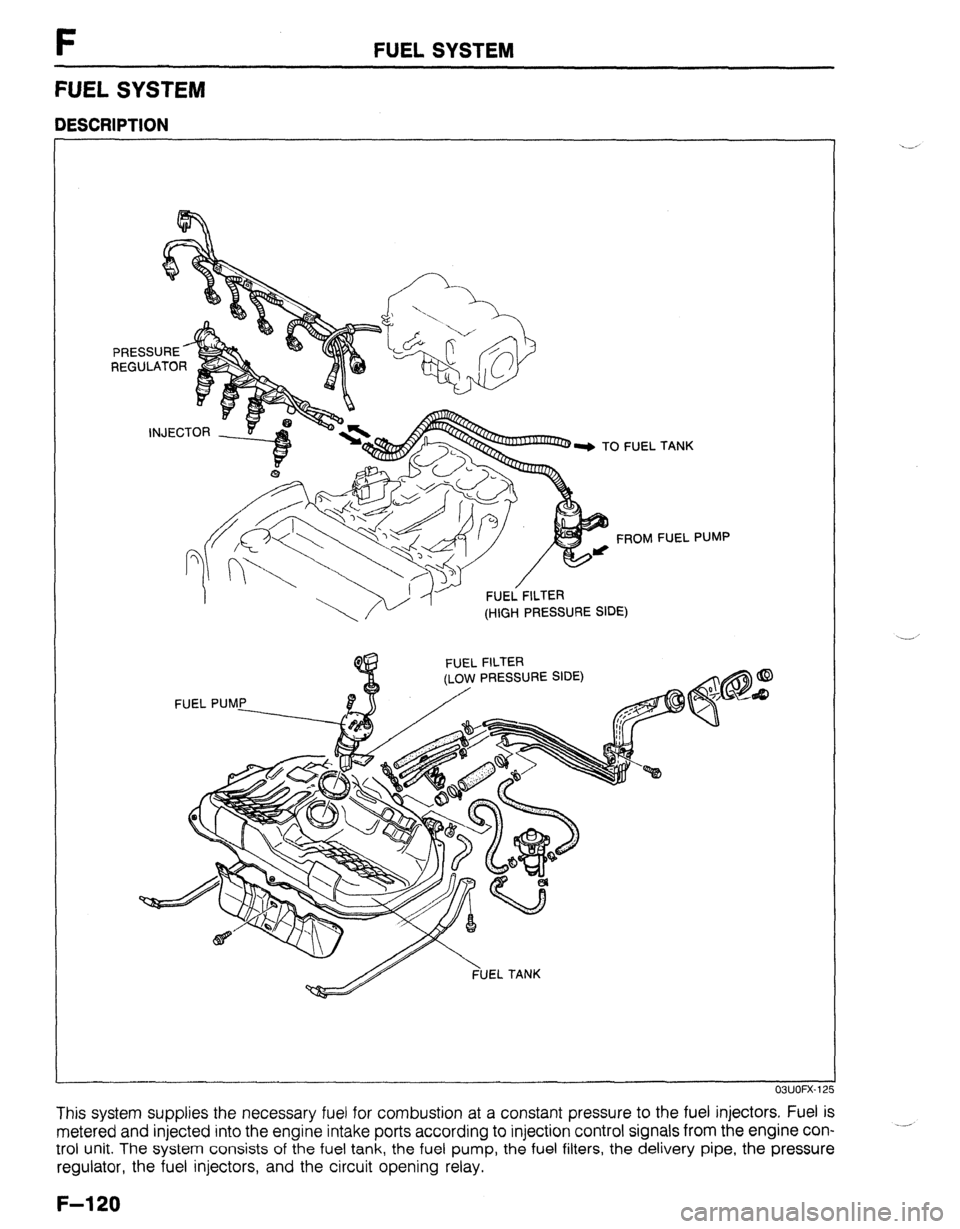
F FUEL SYSTEM
FUEL SYSTEM
DESCRIPTION
FUEL FILTER
(HIGH PRESSURE SIDE) . TANK
FUEL PUMP
PRESSURE SIDE)
OWOFX-12
This system supplies the necessary fuel for combustion at a constant pressure to the fuel injectors. Fuel is
metered and injected into the engine intake ports according to injection control signals from the engine con-
trol unit. The system consists of the fuel tank, the fuel pump, the fuel filters, the delivery pipe, the pressure
regulator, the fuel injectors, and the circuit opening relay. ._*
F-l 20
Page 387 of 1164
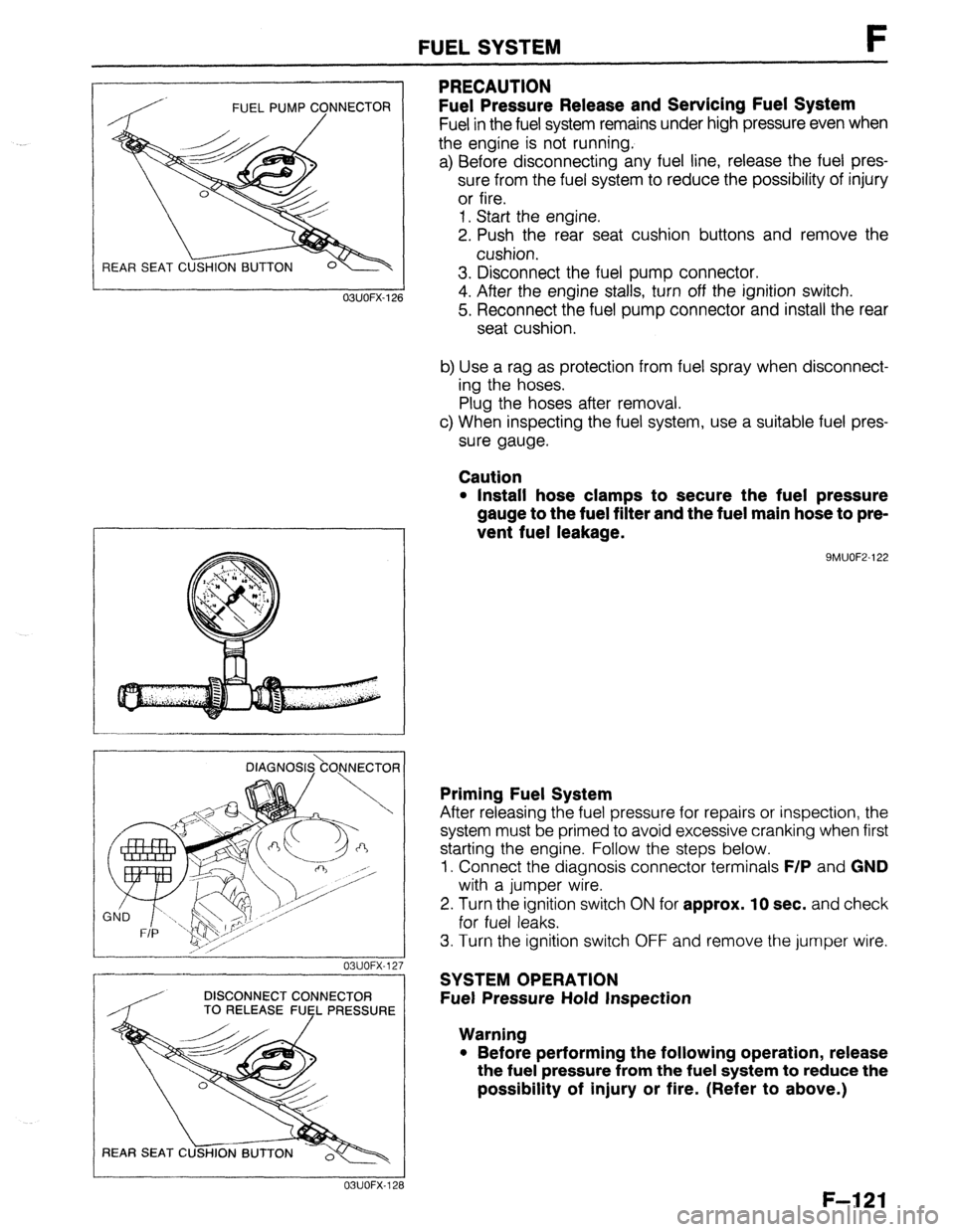
FUEL PUMP CONNECTOR
/
REAR SEAT C
FUEL SYSTEM F
PRECAUTION
Fuel Pressure Release and Servicing Fuel System
Fuel in the fuel system remains under high pressure even when
the engine is not running.
a) Before disconnecting any fuel line, release the fuel pres-
sure from the fuel system to reduce the possibility of injury
or fire.
1. Start the engine.
2. Push the rear seat cushion buttons and remove the
cushion.
3. Disconnect the fuel pump connector.
4. After the engine stalls, turn off the ignition switch.
5. Reconnect the fuel pump connector and install the rear
seat cushion.
b) Use a rag as protection from fuel spray when disconnect-
ing the hoses.
Plug the hoses after removal.
c) When inspecting the fuel system, use a suitable fuel pres-
sure gauge.
Caution
l Install hose clamps to secure the fuel pressure
gauge to the fuel filter and the fuel main hose to pre-
vent fuel leakage.
9MUOF2-122 OBUOFX-126
DlAGNOS&O,NNECTOR
03UOFX-12.
-
DISCONNECT CONNECTOR
/ TO RELEASE FUEL PRESSURE
03UOFX-12;
Priming Fuel System
After releasing the fuel pressure for repairs or inspection, the
system must be primed to avoid excessive cranking when first
starting the engine. Follow the steps below.
1. Connect the diagnosis connector terminals
F/P and GND
with a jumper wire.
2. Turn the ignition switch
ON for approx. 10 sec. and check
for fuel leaks.
3. Turn the ignition switch OFF and remove the jumper wire.
SYSTEM OPERATION
Fuel Pressure Hold Inspection
Warning
l Before performing the following operation, release
the fuel pressure from the fuel system to reduce the
possibility of injury or fire. (Refer to above.)
F-121
Page 388 of 1164
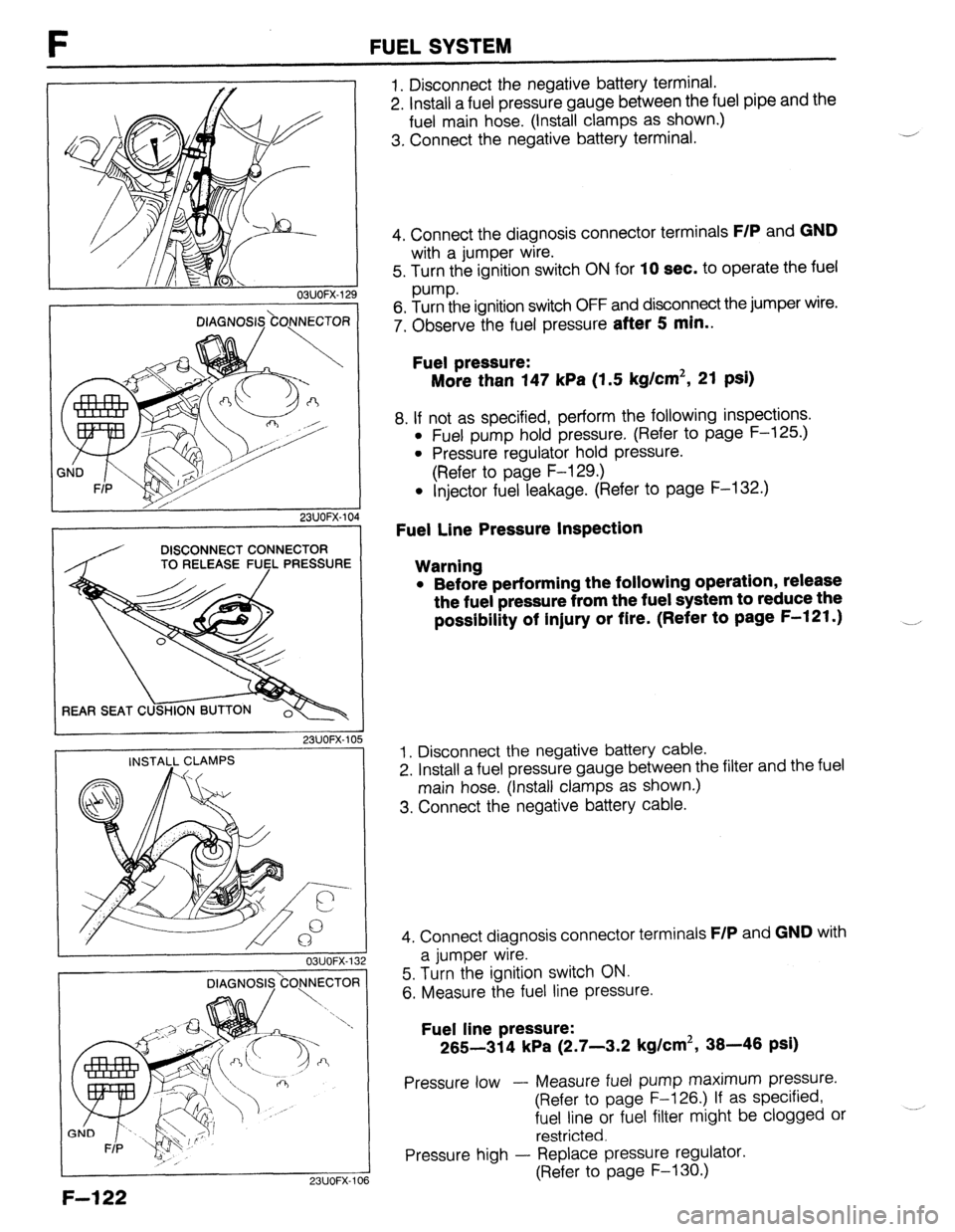
F FUEL SYSTEM
OSUOFX-129
DIAGNOSIS.\CO.NNECTOR j
/, I 23UOFX-104
DISCONNECT CONNECTOR
TO RELEASE FlJsL PRESSURE
L 23UOFX-105
INSTALL CLAMPS
DIAGNOSI$kO)lNECTOfl
I
23UOFX-ll
F-l 22
1. Disconnect the negative battery terminal.
2. Install a fuel pressure gauge between the fuel pipe and the
fuel main hose. (Install clamps as shown.)
3. Connect the negative battery terminal. J
4. Connect the diagnosis connector terminals
F/P and GND
with a jumper wire.
5. Turn the ignition switch ON for
10 sec. to operate the fuel
pump.
6. Turn the ignition switch OFF and disconnect the jumper wire.
7. Observe the fuel pressure
after 5 min..
Fuel pressure:
More than 147 kPa (1.5 kg/cm2, 21 psi)
8. If not as specified, perform the following inspections.
l Fuel pump hold pressure. (Refer to page F-125.)
l Pressure regulator hold pressure.
(Refer to page F-129.)
l Injector fuel leakage. (Refer to page F-132.)
Fuel Line Pressure Inspection
Warning
l Before performing the following operation, release
the fuel pressure from the fuel system to reduce the
possibility of injury or fire. (Refer to page F-121.) __,
1. Disconnect the negative battery cable.
2. Install a fuel pressure gauge between the filter and the fuel
main hose. (Install clamps as shown.)
3. Connect the negative battery cable.
4. Connect diagnosis connector terminals
F/P and GND with
a jumper wire.
5. Turn the ignition switch ON.
6. Measure the fuel line pressure.
Fuel line pressure:
265-314 kPa (2.7-3.2 kg/cm2, 38-46 psi)
Pressure low - Measure fuel pump maximum pressure.
(Refer to page F-126.) If as specified,
fuel line or fuel filter might be clogged or
restricted.
Pressure high - Replace pressure regulator.
(Refer to page F-130.)
Page 389 of 1164
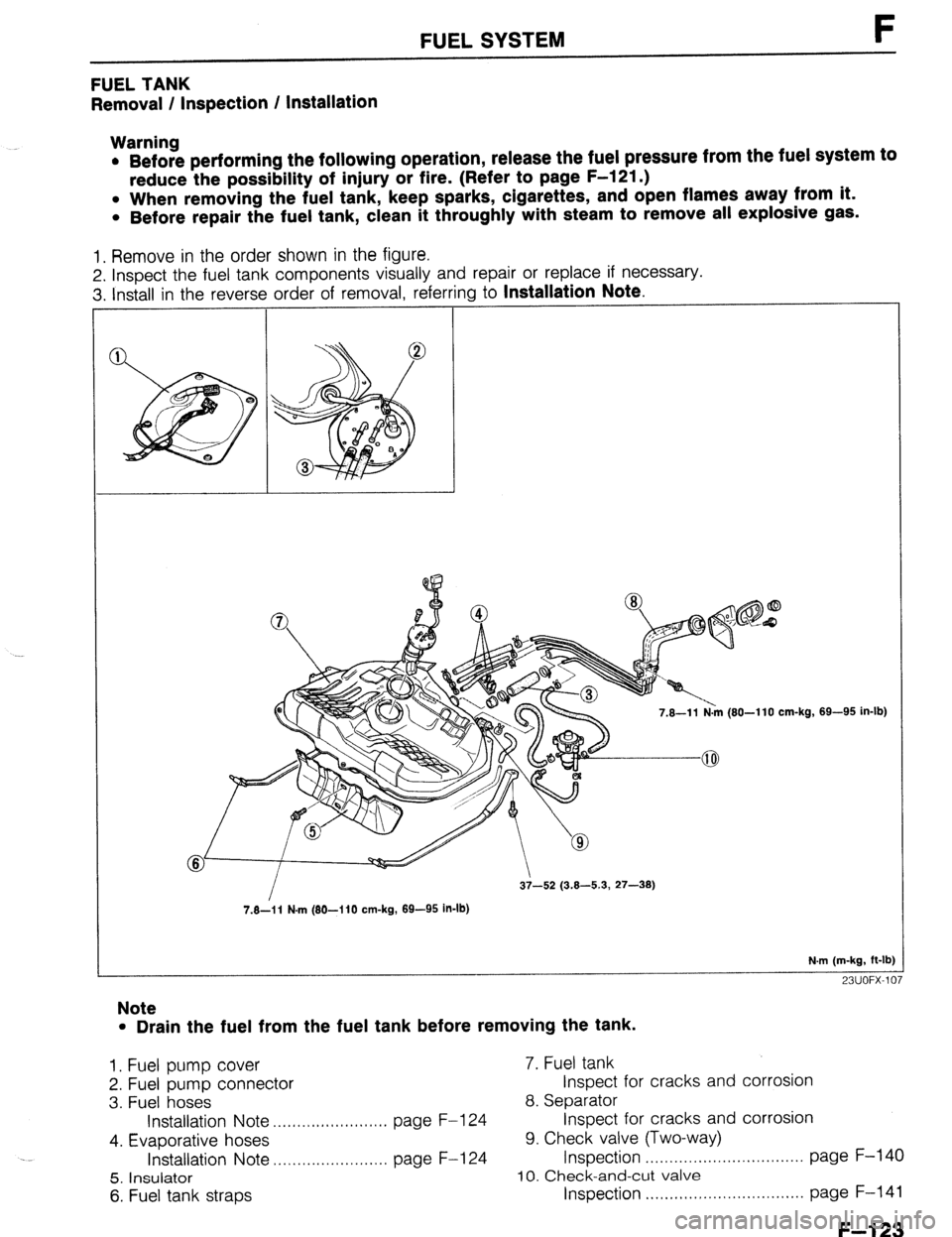
FUEL SYSTEM F
FUEL TANK
Removal / Inspection / Installation
Warning
l Before performing the following operation, release the fuel pressure from the fuel system to
reduce the possibility of injury or fire. (Refer to page F-121 .)
l When removing the fuel tank, keep sparks, cigarettes, and open flames away from it.
l Before repair the fuel tank, clean it throughly with steam to remove all explosive gas.
1. Remove in the order shown in the figure.
2. Inspect the fuel tank components visually and repair or replace if necessary.
3. Install in the reverse order of removal, referring to
Installation Note.
7.8-l 1 N.m (80-l 10 cm-kg,
7.8-i 1 N-m (80-I 10 cm-kg, 89-95 in-lb) 69-95 in-lb)
N.m (m-kg, ft-lb]
23UOFX-107
Note
l Drain the fuel from the fuel tank before removing the tank.
1. Fuel pump cover 7. Fuel tank
2. Fuel pump connector Inspect for cracks and corrosion
3. Fuel hoses 8. Separator
Installation Note . ..., I .I,,,,I,I,.,.I.,,. page F-l 24 Inspect for cracks and corrosion
4. Evaporative hoses 9. Check valve (Two-way)
Installation Note ,..,..,................. page F-l 24 Inspection . . . . . . . . . . . . . . . . . . . . . . . . . . . . . . . . . page F-140
5. Insulator 10. Check-and-cut valve
6. Fuel tank straps Inspection . . . . . . . . . . . . . . . . . . . . . . . . . . . page F-141
F--l 23
Page 390 of 1164
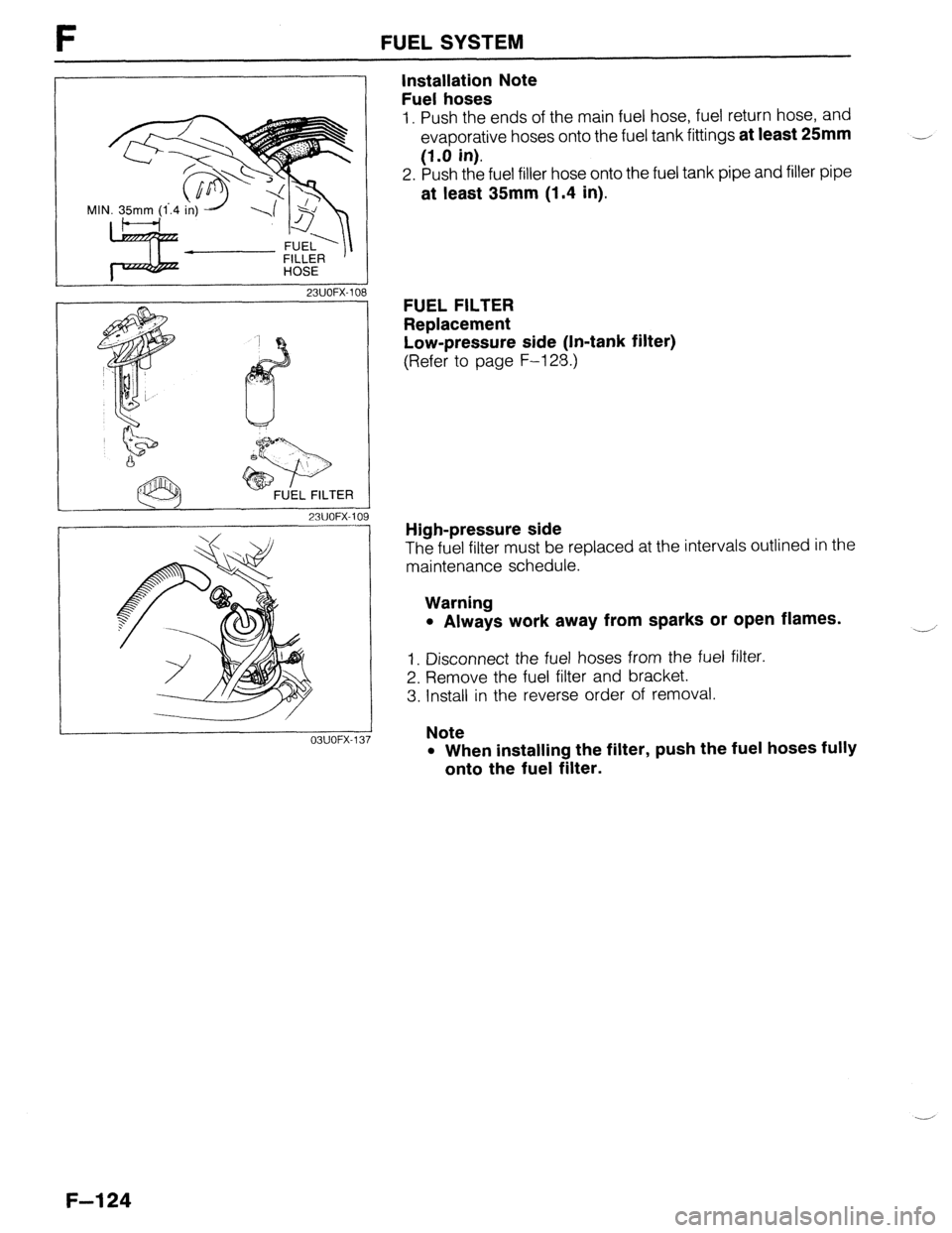
F FUEL SYSTEM
MIN. 35mm (1..4 in) -/
23UOFX-10
NJ
23UOFX-l(
OBUOFX-1:
Installation Note
Fuel hoses
1. Push the ends of the main fuel hose, fuel return hose, and
evaporative hoses onto the fuel tank fittings at least 25mm
(1.0 in).
2. Push the fuel filler hose onto the fuel tank pipe and filler pipe
at least 35mm (1.4 in).
FUEL FILTER
Replacement
Low-pressure side (In-tank filter)
(Refer to page F-128.)
High-pressure side
The fuel filter must be replaced at the intervals outlined in the
maintenance schedule.
Warning
l Always work away from sparks or open flames.
1. Disconnect the fuel hoses from the fuel filter.
2. Remove the fuel filter and bracket.
3. Install in the reverse order of removal.
Note
l When installing the filter, push the fuel hoses fully
onto the fuel filter.
F-l 24