DATSUN 210 1979 Service Manual
Manufacturer: DATSUN, Model Year: 1979, Model line: 210, Model: DATSUN 210 1979Pages: 548, PDF Size: 28.66 MB
Page 381 of 548
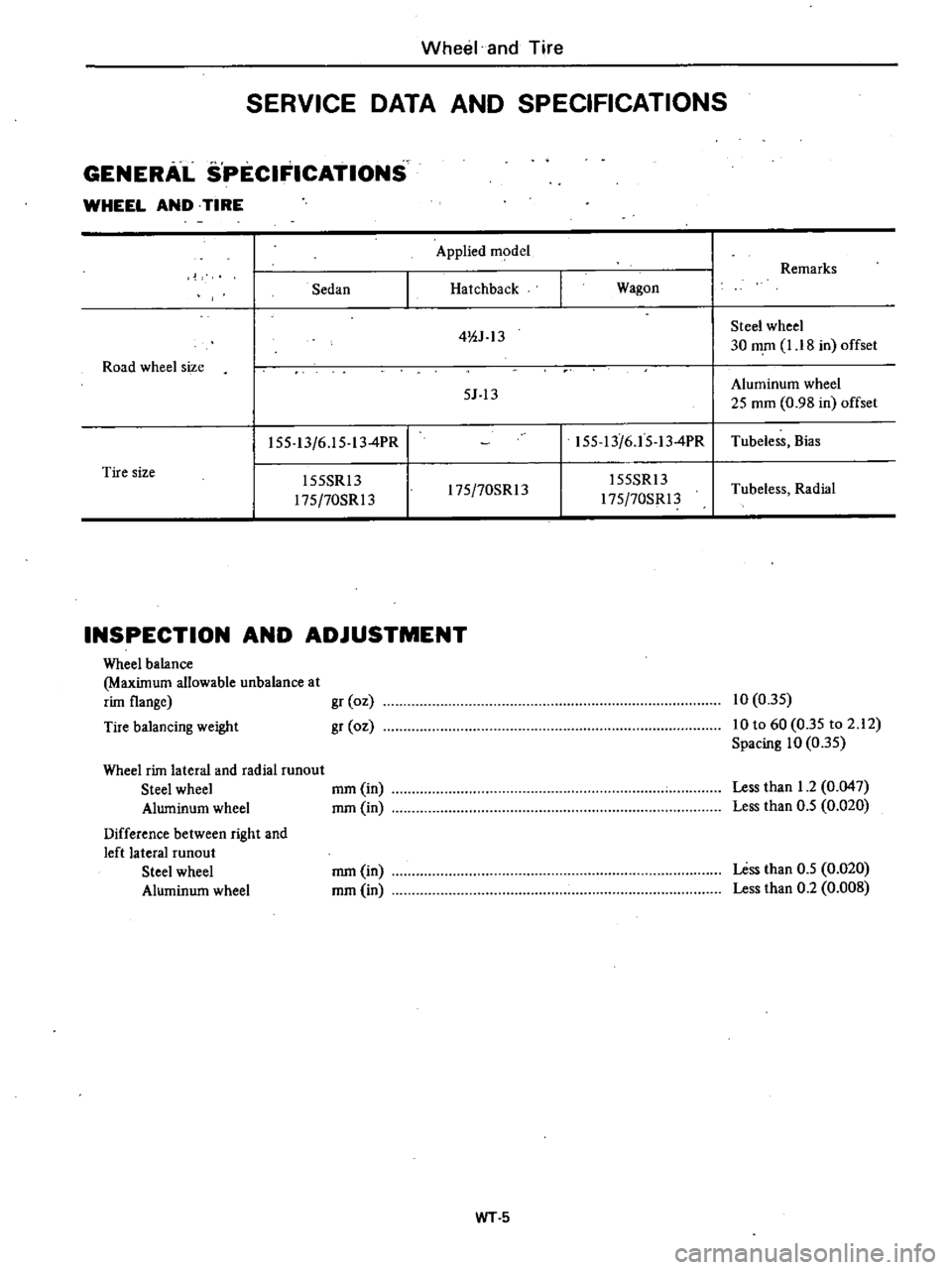
Wheel
and
Tire
SERVICE
DATA
AND
SPECIFICATIONS
GENERAL
SPECIFICATIONS
WHEEL
AND
TIRE
Road
wheel
size
Applied
m
del
Remarks
Sedan
Hatchback
Wagon
4
OJ
13
Steel
wheel
30
mm
I
I
8
in
offset
5J
13
Aluminum
wheel
25
mm
0
98
in
offset
155
13
6
1
5
13
4PR
155
13
6
1
5
13
4PR
Tubeless
Bias
l55SRl3
l75
70SR13
155SRl3
Tubeless
Radial
l75
70SR13
l75
70SR13
Tire
size
INSPECTION
AND
ADJUSTMENT
Wheel
balance
Maxilnum
allowable
unbalance
at
riln
flange
Tire
balancing
weight
gr
oz
gr
oz
10
0
35
10
to
60
0
35
to
2
12
Spacing
10
0
35
Wheel
riln
lateral
and
radial
runout
Steel
wheel
mm
in
Aluminum
wheel
mm
in
Difference
between
right
and
left
lateral
runout
Steel
wheel
Aluminum
wheel
Less
than
1
2
0
047
Less
than
0
5
0
020
mm
in
mm
in
Less
than
0
5
0
020
Less
than
0
2
0
008
WT5
Page 382 of 548
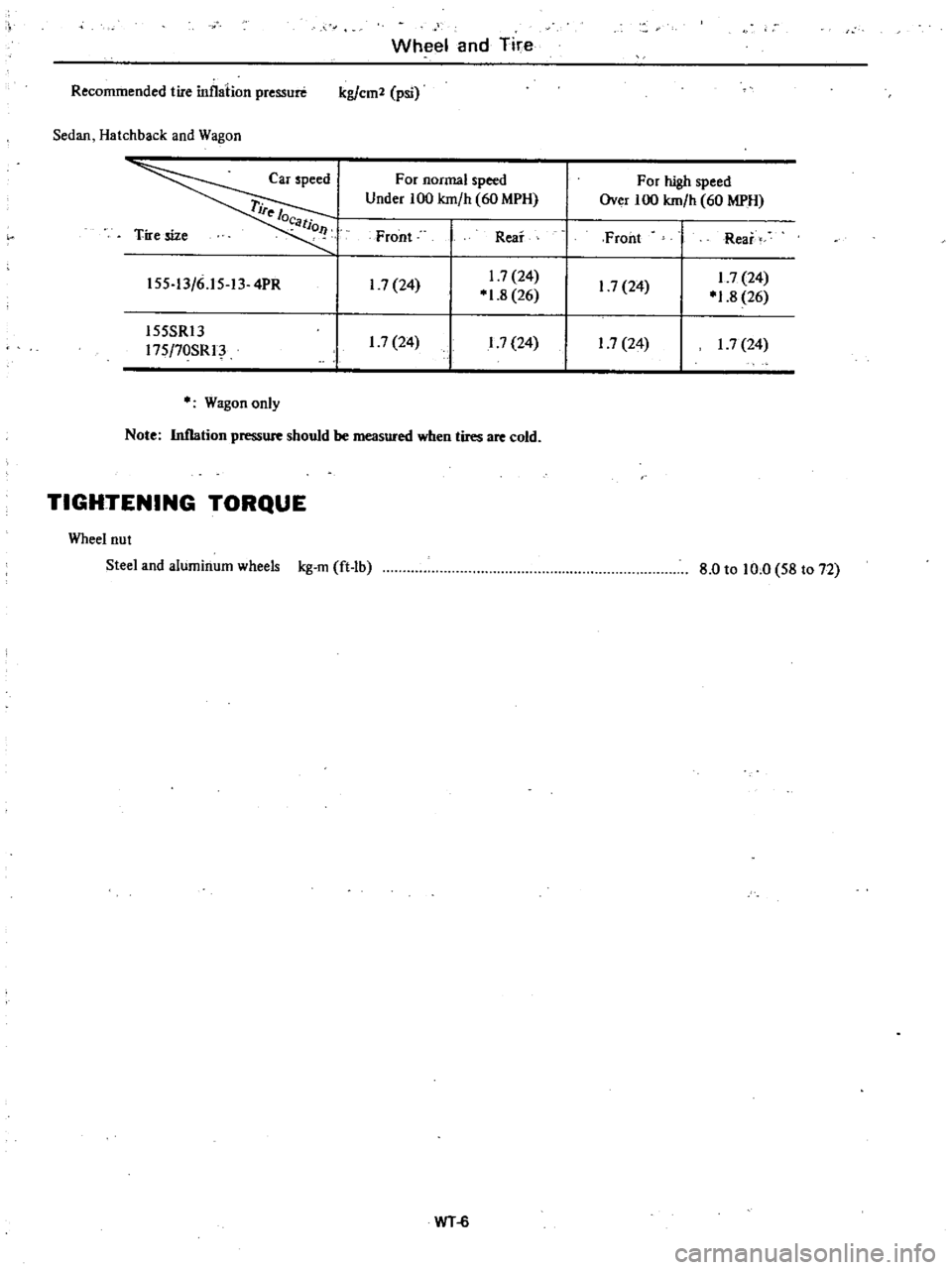
Wheel
and
Tire
Recommended
tire
inflation
pressure
kg
em
psi
Sedan
Hatchback
and
Wagon
Tire
size
Car
speed
rife
l
o
tio
l
For
normal
speed
For
high
speed
Under
100
km
h
60
MPH
Over
100
km
h
60
MPH
Front
Rear
Front
Rear
I
7
24
1
7
24
1
7
24
1
7
24
01
8
26
01
8
26
17
24
1
7
24
1
7
24
17
24
155
13
6
15
13
4PR
155SRl3
175
70SRI
o
Wagon
only
Note
Inflation
pressure
should
be
measured
when
tires
are
cold
TIGHTENING
TORQUE
Wheel
nut
Steel
and
aluminum
wheels
kg
m
ft
lb
8
0
to
10
0
58
to
72
WT
6
Page 383 of 548
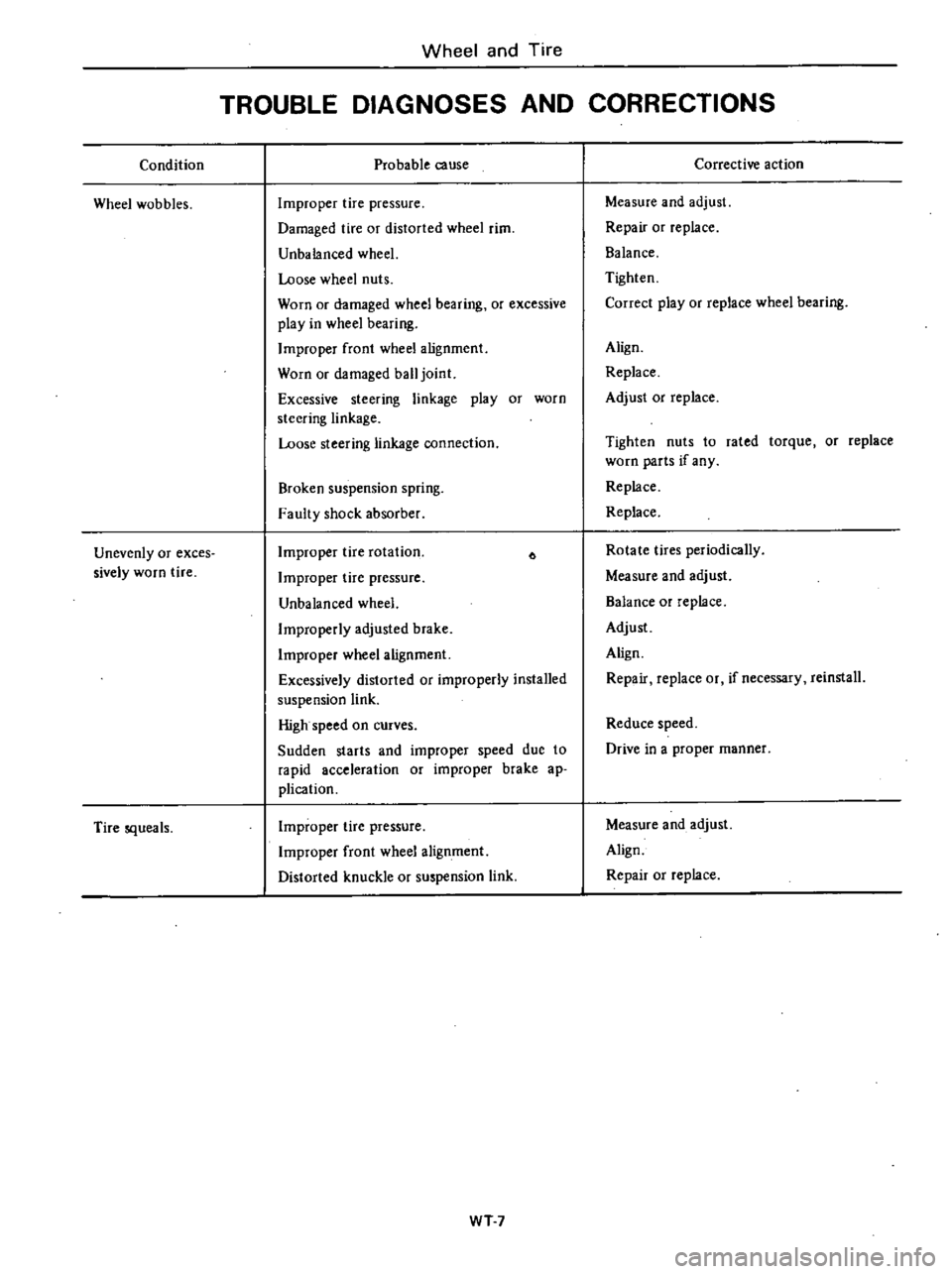
Condition
Wheel
wobbles
Unevenly
or
exces
sively
worn
tire
Tire
squeals
Wheel
and
Tire
TROUBLE
DIAGNOSES
AND
CORRECTIONS
Probable
cause
Improper
tire
pressure
Damaged
tire
or
distorted
wheel
rim
Unbalanced
wheel
Loose
wheel
nuts
Worn
or
damaged
wheel
bearing
or
excessive
play
in
wheel
bearing
Improper
front
wheel
alignment
Worn
or
damaged
ball
joint
Excessive
steering
linkage
play
or
worn
steering
linkage
Loose
steering
linkage
connection
Broken
suspension
spring
Faulty
shock
absorber
Improper
tire
rotation
Improper
tire
pressure
Unbalanced
wheel
Improperly
adjusted
brake
Improper
wheel
alignment
Excessively
distorted
or
improperly
installed
suspension
link
High
speed
on
curves
Sudden
starts
and
improper
speed
due
to
rapid
acceleration
or
improper
brake
ap
plication
Improper
tire
pressure
Improper
front
wheel
alignment
Distorted
knuckle
or
suspension
link
WT7
Corrective
action
Measure
and
adjust
Repair
or
replace
Balance
Tighten
Correct
play
or
replace
wheel
bearing
Align
Replace
Adjust
or
replace
Tighten
nuts
to
rated
torque
or
replace
worn
parts
if
any
Replace
Replace
Rotate
tires
periodically
Measure
and
adjust
Balance
or
replace
Adjust
Align
Repair
replace
or
if
necessary
reinstall
Reduce
speed
Drive
in
a
proper
manner
Measure
and
adjust
Align
Repair
or
replace
Page 384 of 548
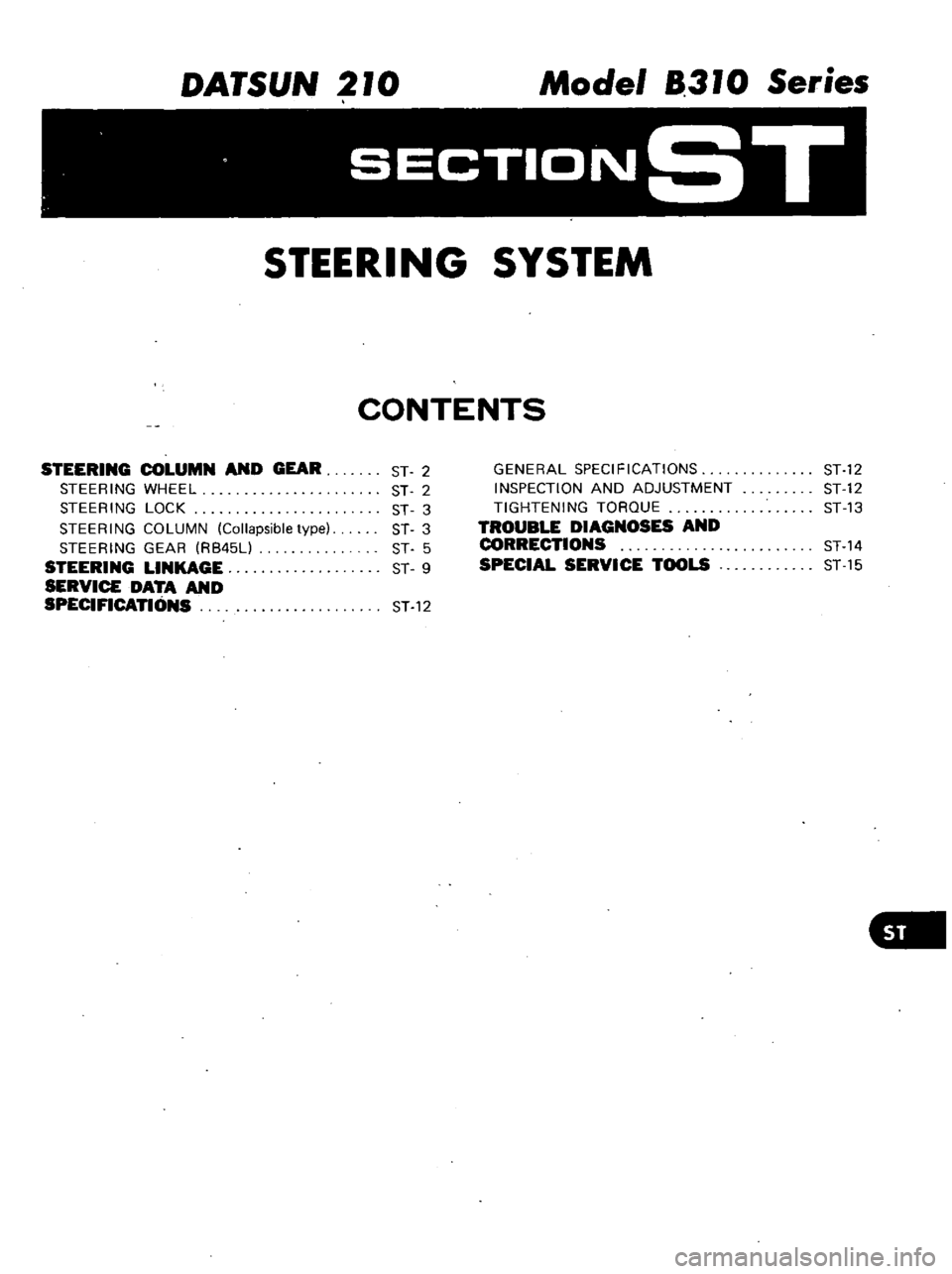
DATSUN
210
Model
8310
Series
SECTIONST
STEERING
SYSTEM
CONTENTS
STEERING
COLUMN
AND
GEAR
STEERING
WHEEL
STEERING
LOCK
STEERING
COLUMN
Collapsible
type
STEERING
GEAR
RB45L
STEERING
LINKAGE
SERVICE
DATA
AND
SPECIFICATIONS
ST
2
ST
2
ST
3
ST
3
ST
5
ST
9
GENERAL
SPECIFICATIONS
INSPECTION
AND
ADJUSTMENT
TIGHTENING
TORQUE
TROUBLE
DIAGNOSES
AND
CORRECTIONS
SPECIAL
SERVICE
TOOLS
ST
12
ST
12
ST
13
ST
14
ST
15
ST
12
Page 385 of 548
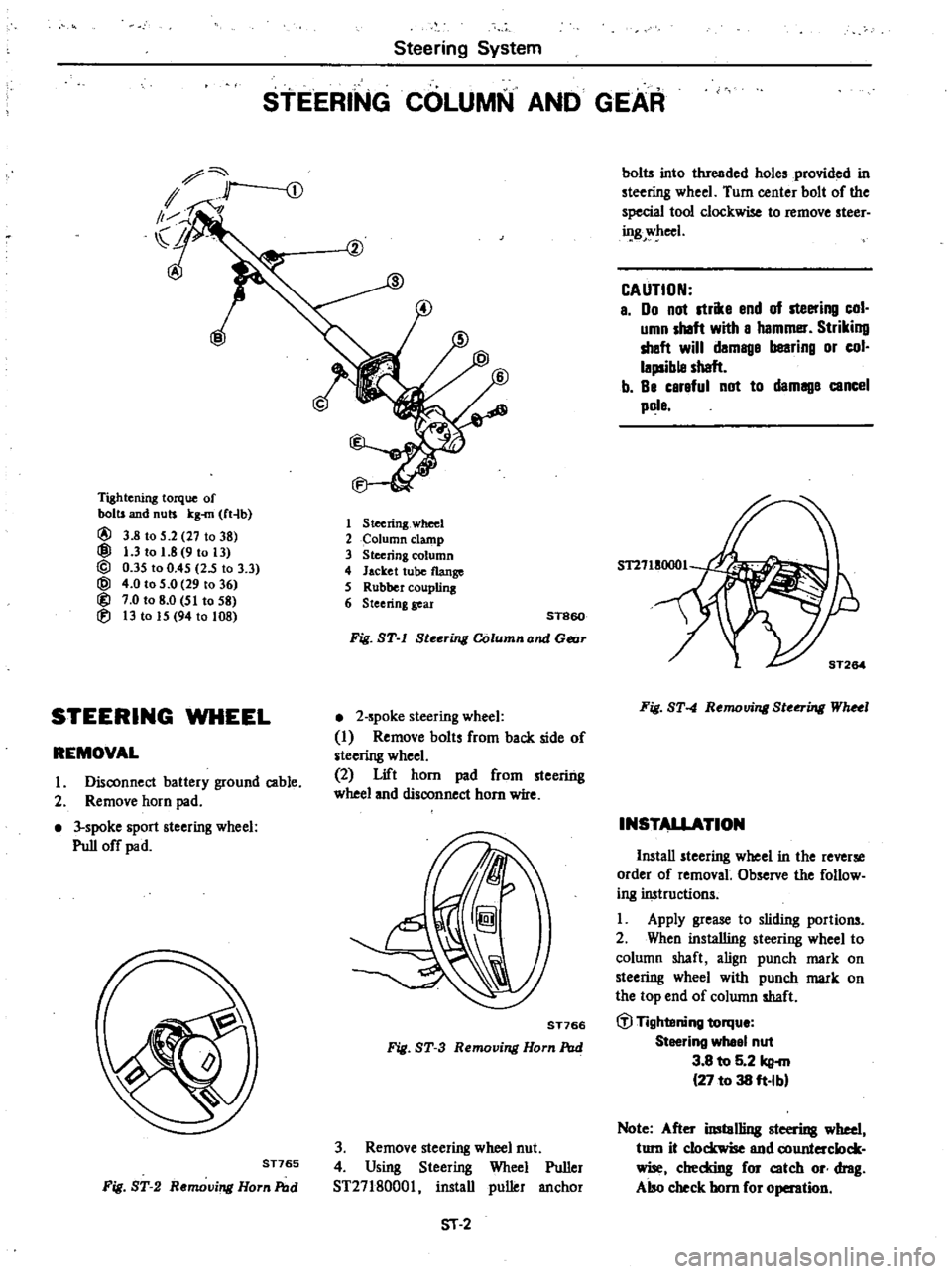
Steering
System
STEERING
COLUMN
AND
GEAR
Tightening
torque
of
bolts
and
nuts
kg
rn
ft4b
@
3
8
to
5
2
27
to
38
@
1
3
to
1
8
9
to
13
@
0
35
to
0
45
25
to
3
3
@
4
0
to
5
0
29
to
36
@
7
0
to
8
0
51
to
58
lEi
13
to
15
94
to
108
1
Steering
wheel
2
olumn
clamp
3
Steering
column
4
Jacket
tube
flange
S
RUbbercoupling
6
Steering
gear
ST860
Fig
ST
l
Steering
Column
and
Gear
STEERING
WHEEL
2
spoke
steering
wheel
I
Remove
bolts
from
back
side
of
steering
wheel
2
Lift
horn
pad
from
steering
wheel
and
disconnect
horn
wire
REMOVAL
I
Disconnect
battery
ground
cable
2
Remove
horn
pad
3
spoke
sport
steering
wheel
Pull
off
pad
ST766
Fig
ST
3
Removing
Horn
Pod
ST765
Fig
ST
2
Removing
Horn
Pod
3
Remove
steering
wheel
nut
4
Using
Steering
Wheel
Puller
ST2718000l
install
puller
anchor
51
2
bolts
into
threaded
holes
provided
in
steering
wheel
Turn
center
bolt
of
the
special
tool
clockwise
to
remove
steer
ing
wheel
CAUTION
a
00
not
strike
end
of
steering
col
umn
shaft
with
a
hammer
Striking
shaft
will
damage
bearing
or
col
lapsible
shaft
b
Be
careful
not
to
damage
cancel
pole
Fig
ST
4
Removing
Ste
ing
WhHl
INSTALLATION
Install
steering
wheel
in
the
reverse
order
of
removal
Observe
the
follow
ing
instructions
Apply
grease
to
sliding
portions
2
When
installing
steering
wheel
to
column
shaft
align
punch
mark
on
steering
wheel
with
punch
mark
on
the
top
end
of
column
shaft
til
Tightening
torqu
Steering
whee
nut
3
8
to
5
2
kg
27
to
38
ft
Ibl
Note
After
imtol1ing
steering
wheel
turn
it
clockwise
end
counterclock
wise
cheddng
for
catch
or
drag
Also
check
horn
for
operation
Page 386 of 548
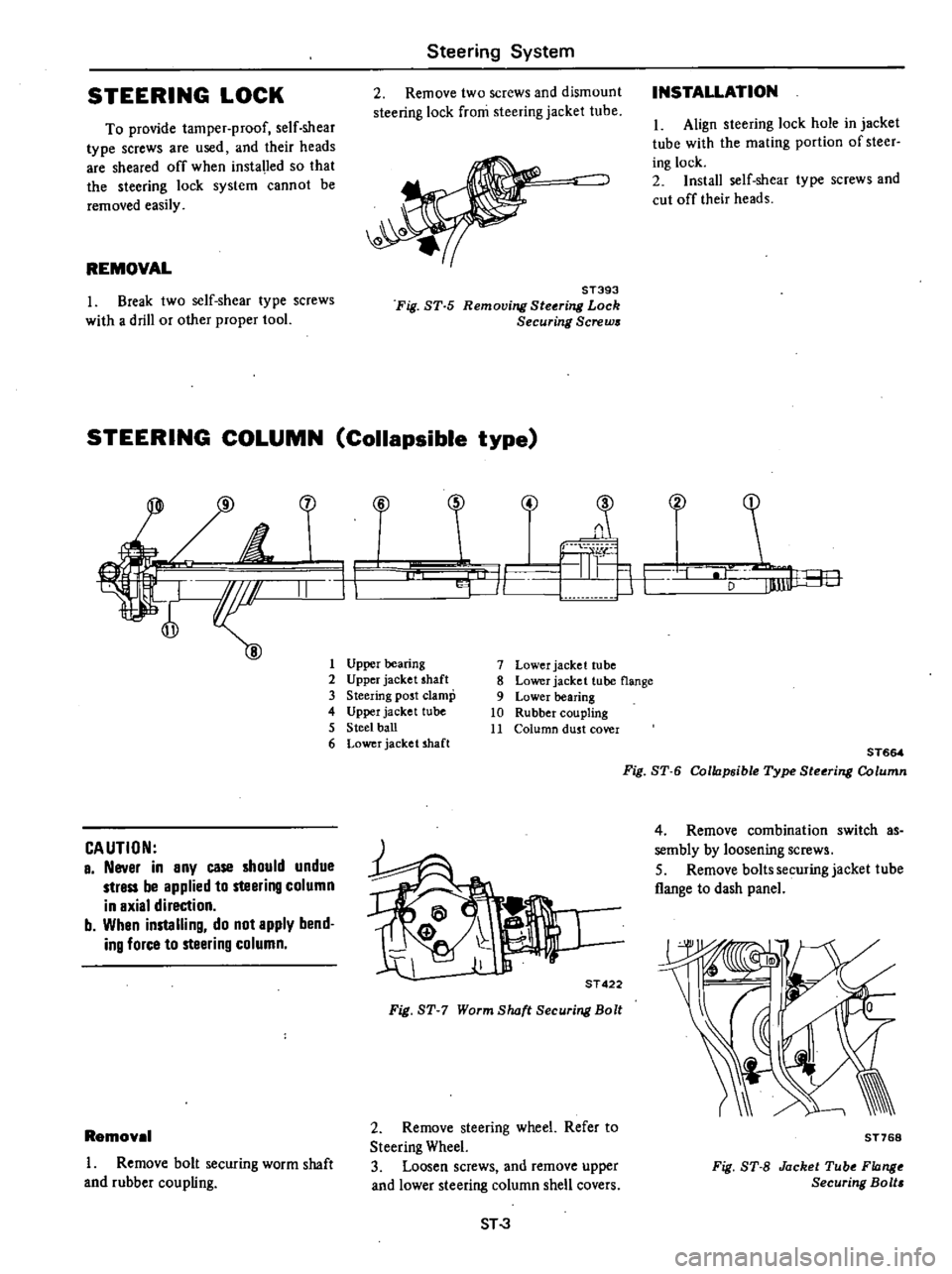
STEERING
LOCK
To
provide
tamper
proof
self
shear
type
screws
are
used
and
their
heads
are
sheared
off
when
installed
so
that
the
steering
lock
system
cannot
be
removed
easily
REMOVAL
I
Break
two
self
shear
type
screws
with
a
drill
or
other
proper
tool
Steering
System
2
Remove
two
screws
and
dismount
steering
lock
from
steering
jacket
tube
ST393
Fig
ST
5
Removing
Steering
Lock
Securing
Screw
STEERING
COLUMN
Collapsible
type
1
H
f
II
CAUTION
a
Never
in
any
case
should
undue
strass
be
applied
to
steering
column
in
axial
direction
b
Whan
installing
do
not
apply
bend
ing
force
to
steering
column
Removel
I
Remove
bolt
securing
worm
shaft
and
rubber
coupling
INSTALLATION
I
Align
steering
lock
hole
in
jacket
tube
with
the
mating
portion
of
steer
ing
lock
2
Install
self
shear
type
screws
and
cut
off
their
heads
i
4
T
C
F
Lu
J
r
1
V
F
1
Upper
bearing
2
Upper
jacket
shaft
3
Steering
post
clamp
4
Upper
jacket
tube
5
Steel
ball
6
Lower
jacket
shaft
7
Lower
jacket
tube
8
Lower
jacket
tube
flange
9
Lower
bearing
10
Rubber
coupling
11
Column
dust
cover
it
j
a
ST
422
Fig
ST
7
Worm
8lwft
Securing
Bolt
2
Remove
steering
wheel
Refer
to
Steering
Wheel
3
Loosen
screws
and
remove
upper
and
lower
steering
column
shell
covers
ST
3
ST664
Fig
8T
6
Collapsibte
Type
Steoring
Column
4
Remove
combination
switch
as
sembly
by
loosening
screws
5
Remove
baIts
securing
jacket
tube
flange
to
dash
panel
ST768
Fig
8T
8
Jacket
Tube
Flange
Securing
Bolt
Page 387 of 548
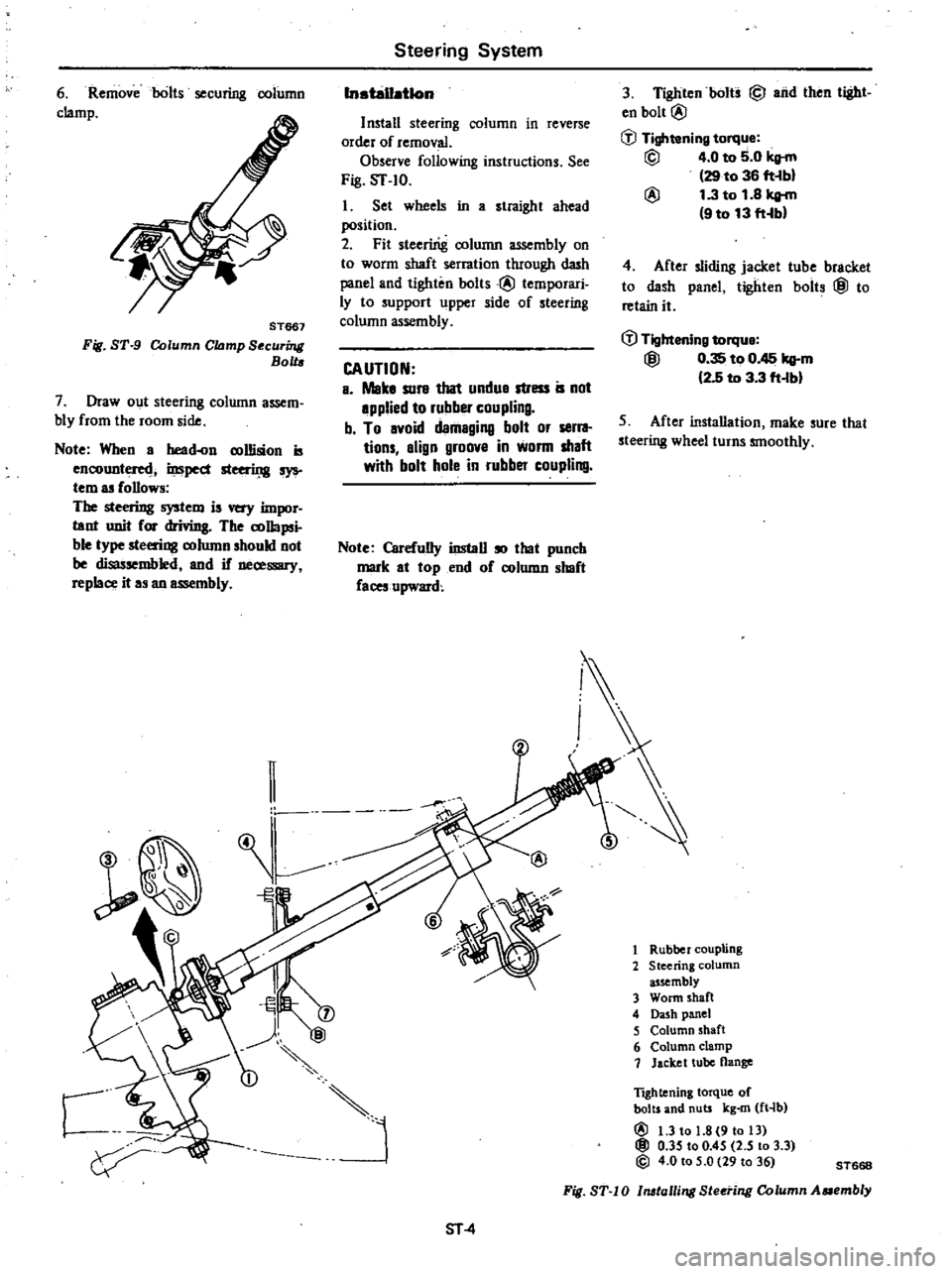
6
Removeoolts
securing
oolumn
clamp
ST661
Fig
ST
9
Column
CIDmp
Securing
BoU
7
Draw
out
steering
column
assem
bly
from
the
room
side
Note
When
a
head
n
rollision
is
encountere
inspect
steeriJ
tg
sys
tem
as
allow
The
steering
system
is
very
impor
lant
unit
or
driving
The
oollapsi
ble
type
steering
column
hould
not
be
disassembled
snd
if
necessary
replace
it
a
an
assembly
Steering
System
InstaU
tlon
Iostall
steering
column
in
reverse
order
of
removal
Observe
following
instructions
See
Fig
ST
IO
I
Set
wheels
in
a
straight
ahead
position
2
Fit
steeririg
column
assembly
on
to
worm
shaft
serration
through
dash
panel
and
tighti
bolts@
temporari
ly
to
support
upper
side
of
steering
column
assembly
CAUTION
a
Mata
sure
that
undue
stress
is
not
epplied
to
ruhber
coupling
b
To
evoid
damaging
bolt
or
serra
tions
align
groove
in
worm
shaft
with
bolt
hole
in
rubber
coupling
Note
Carefully
install
so
that
punch
mark
at
top
end
o
column
slmft
acesupwardc
C
VH
3
Tighten
bolts
@
rid
then
tight
en
bolt
@
liJ
Tightening
torque
@
4
0
to
5
0
kg
m
29
to
36
ft
lb
@
1
3
to
1
8
kg
m
9
to
13
ft
lbl
4
After
sliding
jacket
tube
bracket
to
dash
panel
tighten
bolt
@
to
retain
it
liJ
Tightening
torqu
@
0
35
to
0
45
kg
m
2
5
to
3
3
ft
lbl
5
After
installation
make
sure
that
steering
wheel
turns
smoothly
5
1
Rubber
coupling
2
Steering
column
8ncmbly
3
Worm
shaft
4
Dash
panel
5
Column
shaft
6
Column
clamp
1
Jacltct
tube
flange
Tightening
torque
of
bolts
and
nuts
kg
m
ft
lb
@
1
3
to
1
8
9
to
13
@
0
35
to
0
45
2
5
to
3
3
@
4
0
to
5
0
29
to
36
ST668
Fig
ST
IO
1
alling
Sleering
Column
Aaembly
ST
4
Page 388 of 548
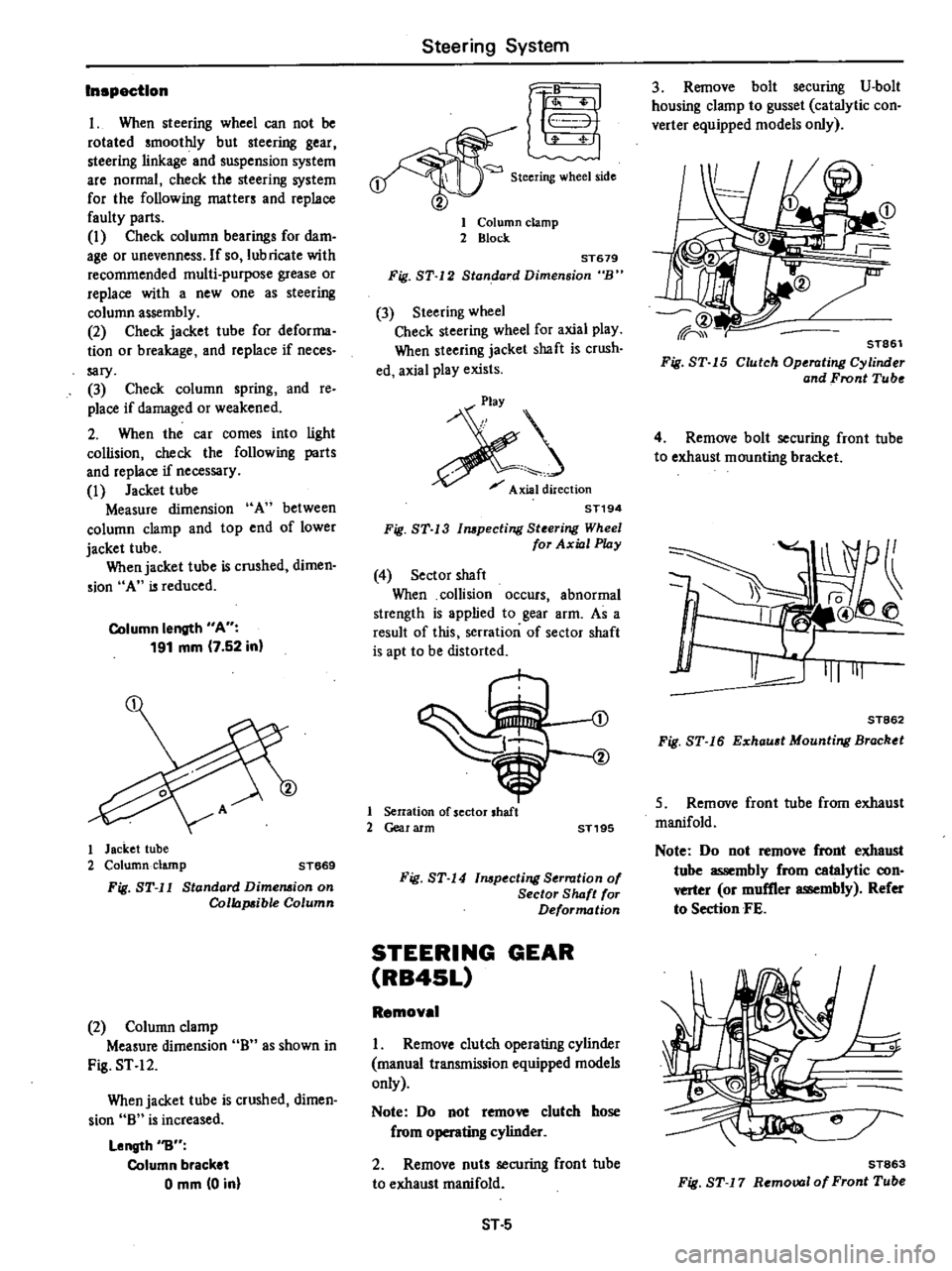
Inspection
I
When
steering
wheel
can
not
be
rotated
smoothly
but
steering
gear
steering
linkage
and
suspension
system
are
normal
check
the
steering
system
for
the
following
matters
and
replace
faulty
parts
I
Check
column
bearings
for
dam
age
or
unevenness
If
so
lubricate
with
recommended
multi
purpose
grease
or
replace
with
a
new
one
as
steering
column
assembly
2
Check
jacket
tube
for
deforma
tion
or
breakage
and
replace
if
neces
sary
3
Check
column
spring
and
re
place
if
damaged
or
weakened
2
When
the
car
comes
into
light
collision
check
the
following
parts
and
replace
if
necessary
I
Jacket
tube
Measure
dimension
A
between
column
clamp
and
top
end
of
lower
jacket
tube
When
jacket
tube
is
crushed
dimen
sion
A
is
reduced
Column
length
A
191
mm
7
52
in
1
Jacket
tube
2
Column
clamp
ST669
Fig
ST
l1
Standard
Dimension
on
Collapsible
Column
2
Column
clamp
Measure
dimension
0
as
shown
in
Fig
ST
12
When
jacket
tube
is
crushed
dimen
sion
0
is
increased
Length
1J
Column
bracket
o
mm
0
in
Steering
System
r
1
Steering
wheel
side
1
Column
clamp
2
Block
ST679
Fig
ST
12
Standard
Dimension
B
3
Steering
wheel
Check
steering
wheel
for
axial
play
When
steering
jacket
shaft
is
crush
ed
axial
play
exists
j
Axial
direction
ST194
Fig
ST
13
mpecting
Steering
Wheel
for
Axial
Play
4
Sector
shaft
When
collision
occurs
abnormal
strength
is
applied
to
gear
arm
As
a
result
of
this
serration
of
sector
shaft
is
apt
to
be
distorted
1
Serration
of
sector
shaft
2
Gear
arm
ST195
Fig
ST
14
mpeeting
Serration
of
Sector
S
IuJft
for
Deformation
STEERING
GEAR
RB4SL
Removal
I
Remove
clutch
operating
cylinder
manual
transmission
equipped
models
only
Note
Do
not
remove
clutch
hose
from
8
cylinder
2
Remove
nuts
securing
front
tube
to
exhaust
manifold
ST
5
3
Remove
bolt
securing
V
bolt
housing
clamp
to
gusset
catalytic
con
verter
equipped
models
only
STa6l
Fig
ST
5
Clutch
Operating
Cylinder
and
Front
Tube
4
Remove
bolt
securing
front
tube
to
exhaust
mounting
bracket
1
Q
I
II
@
J
111111
ST862
Fig
ST
16
Exhau
t
Mounting
Bracktt
5
Remove
front
tube
from
exhaust
manifold
Note
Do
not
remove
front
exhaust
tube
assembly
from
catalytic
con
verter
or
muffler
assembly
Refer
to
Section
FE
ST863
Fig
ST
7
Removal
of
Front
Tube
Page 389 of 548
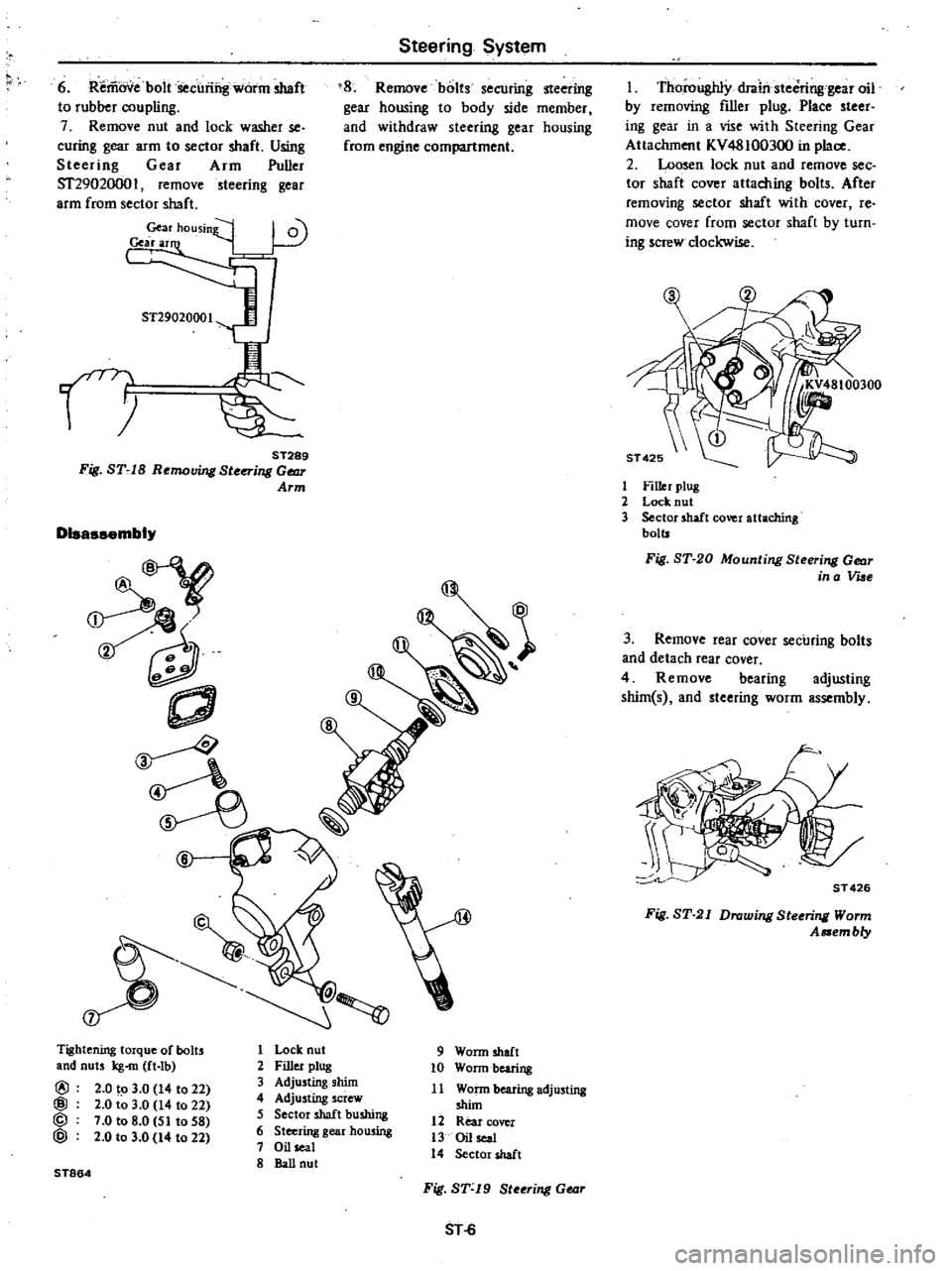
Steering
System
6
Reriiovebolt
Securing
worm
shaft
to
rubber
coupling
7
Remove
nut
and
lock
washer
se
curing
gear
arm
to
sector
shaft
Using
Steering
Gear
Arm
Puller
512902000
I
remove
steering
gear
arm
from
sector
shaft
Gear
housinif
I
0
Cearar
8
Remove
bolts
securing
steering
gear
housing
to
body
side
member
and
withdraw
steering
gear
housing
from
engine
compartment
n
ST289
Fig
ST
IB
Removing
Ste
i1l
Gear
Arm
Disassembly
f
Tightening
torque
of
bolts
and
nuts
kg
m
ft
Ib
@
2
0
to
3
0
14
to
22
@
2
0
to
3
0
14
to
22
@
7
0
to
8
0
51
to
58
@
2
0
to
3
0
14
to
22
ST864
1
Lock
nut
2
Filler
plug
3
Adjusting
shim
4
Adjusting
screw
5
Sector
shaft
bushing
6
Steering
gearhou
ing
7
Oil
seal
8
BaU
nut
9
Worm
shaft
10
Wonn
bearing
11
Wann
bearing
adjUsting
shim
12
Rear
cover
13
Oil
seal
14
Sector
shaft
Fig
ST
19
Steeri1l
Gear
SHi
Thoroughly
drail
steCring
gear
oil
by
removing
filler
plug
Place
steer
ing
gear
in
a
vise
with
Steering
Gear
Attachment
KV48100300
in
place
2
Loosen
lock
nut
and
remove
see
tor
shaft
cover
attaching
bolts
After
removing
sector
shaft
with
cover
re
move
cover
from
sector
shaft
by
turn
ing
screw
clockwise
1
Filler
plug
2
Lock
nut
3
Sector
shaft
cover
attaching
bolts
Fig
ST
20
Mounti1l
Steeri1l
Gear
in
a
Vue
3
Remove
rear
cover
securing
bolts
and
detach
rear
cover
4
Remove
bearing
adjusting
shim
s
and
steering
worm
assembly
ST
426
Fig
ST
21
Drawi1l
Steeri1l
Worm
A
em
b
y
Page 390 of 548
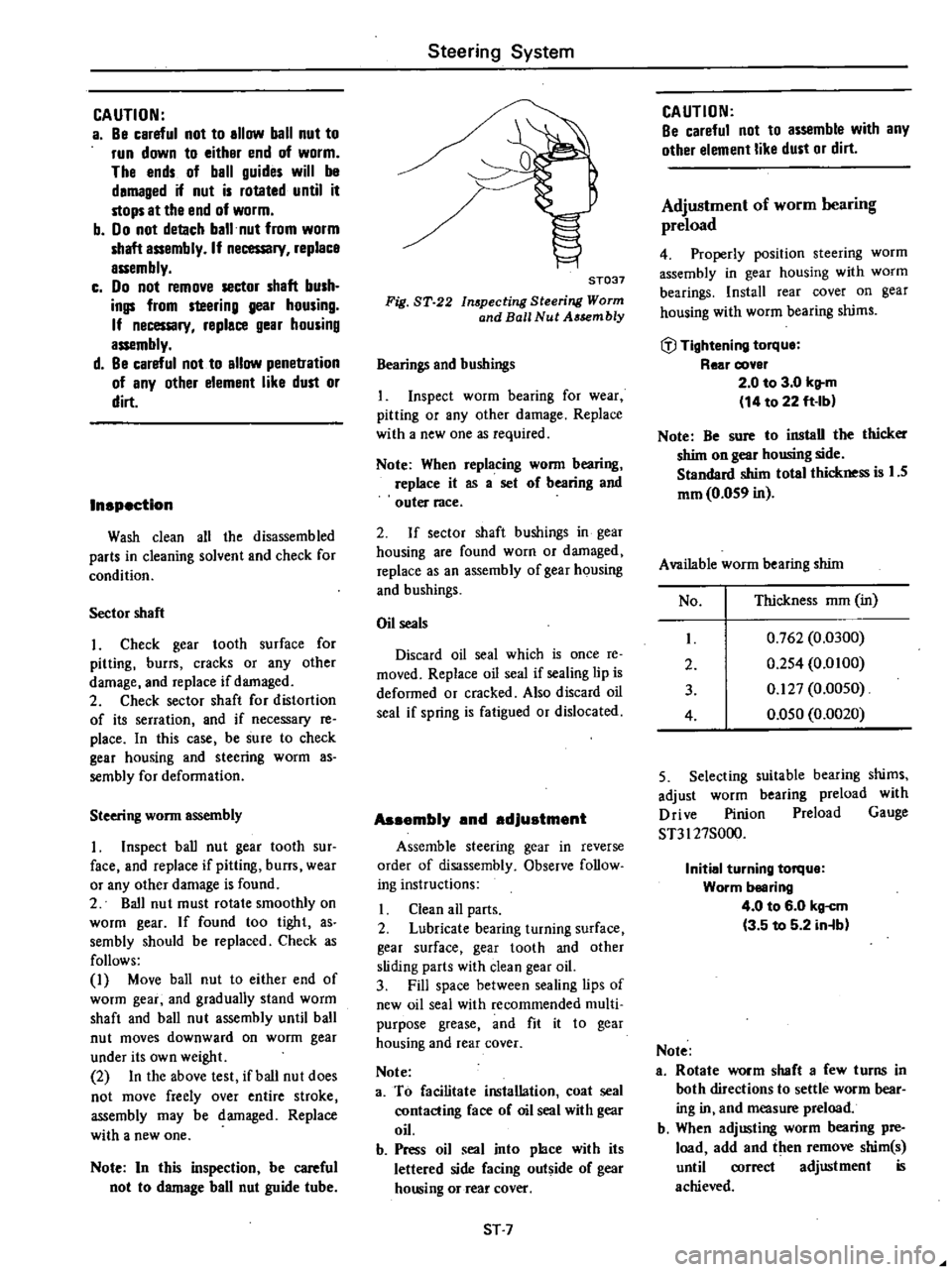
CAUTION
a
Be
careful
not
to
allow
ball
nut
to
run
down
to
either
end
of
worm
The
ends
of
ball
guides
will
be
damaged
if
nut
is
rotated
until
it
stops
at
the
end
of
worm
b
00
not
detach
ball
nut
from
worm
shaft
assembly
If
necessary
replace
assembly
c
Do
not
remove
sector
shaft
bush
ings
from
steering
gear
housing
If
necessary
replace
gear
housing
assembly
d
Be
careful
not
to
allow
penetration
of
any
other
element
like
dust
or
dirt
Inspection
Wash
clean
all
the
disassembled
parts
in
cleaning
solvent
and
check
for
condition
Sector
shaft
I
Check
gear
tooth
surface
for
pitting
burrs
cracks
or
any
other
damage
and
replace
if
damaged
2
Check
sector
shaft
for
distortion
of
its
serration
and
if
necessary
re
place
In
this
case
be
8ure
to
check
gear
housing
and
steering
worm
as
sembly
for
deformation
Steering
worm
assembly
I
Inspect
ball
nut
gear
tooth
sur
face
and
replace
if
pitting
burrs
wear
or
any
other
damage
is
found
2
Ball
nut
must
rotate
smoothly
on
worm
gear
If
found
too
tight
as
sembly
should
be
replaced
Check
as
follows
I
Move
ball
nut
to
either
end
of
worm
gear
and
gradually
stand
worm
shaft
and
ball
nut
assembly
until
ball
nut
moves
downward
on
worm
gear
under
its
own
weight
2
In
the
above
test
if
ball
nut
does
not
move
freely
over
entire
stroke
assembly
may
be
damaged
Replace
with
a
new
one
Note
In
this
inspection
be
careful
not
to
damage
ball
nut
guide
tube
Steering
System
ST037
Fig
ST
22
In
pecting
Steering
Worm
and
Ball
Nut
A8sembly
Bearings
and
bushings
I
Inspect
worm
bearing
for
wear
pitting
or
any
other
damage
Replace
with
a
new
one
as
required
Note
When
replacing
worm
bearing
replace
it
as
a
set
of
bearing
and
outer
race
2
If
sector
shaft
bushings
in
gear
housing
are
found
worn
or
damaged
replace
as
an
assembly
of
gear
housing
and
bushings
Oil
seals
Discard
oil
seal
which
is
once
re
moved
Replace
oil
seal
if
sealing
lip
is
deformed
or
cracked
Also
discard
oil
seal
if
spring
is
fatigued
or
dislocated
Assembly
snd
adjustment
Assemble
steering
gear
in
reverse
order
of
disassembly
Observe
follow
ing
instructions
Clean
all
parts
2
Lubricate
bearing
turning
surface
gear
surface
gear
tooth
and
other
sliding
parts
with
clean
gear
oil
3
Fill
space
between
sealing
lips
of
new
oil
seal
with
recommended
multi
purpose
grease
and
fit
it
to
gear
housing
and
rear
cover
Note
a
To
facilitate
installation
coat
seal
contacting
face
of
oil
seal
with
gear
oil
b
Press
oil
seal
into
place
with
its
lettered
side
facing
outside
of
gear
housing
or
rear
cover
5T
7
CAUTION
Be
careful
not
to
assemble
with
any
other
element
like
dust
or
dirt
Adjustment
of
worm
bearing
preload
4
Properly
position
steering
worm
assembly
in
gear
housing
with
worm
bearings
Install
rear
cover
on
gear
housing
with
worm
bearing
shims
fJ
Tightening
torqu
Rear
coyer
2
0
to
3
0
kltm
14
to
22
ft
Ibl
Note
Be
sure
to
install
the
thicker
shUn
on
gear
housing
side
Standard
shim
total
thickness
is
1
5
mm
0
059
in
Available
worm
bearing
shUn
No
Thickness
mm
in
I
0
762
0
0300
2
0
254
0
0100
3
0
127
0
0050
4
0
050
0
0020
5
Selecting
suitable
bearing
shims
adjust
worm
bearing
preload
with
Drive
Pinion
Preload
Gauge
ST3I
27S000
Initial
turning
torque
Worm
bearing
4
0
to
6
0
kg
m
3
5
to
5
2
in
bl
Note
a
Rotate
worm
shaft
a
few
turns
in
both
directions
to
settle
worm
bear
ing
in
and
measure
preload
b
When
adjusting
worm
bearing
pre
load
add
and
then
remove
shim
s
until
correct
adjustment
is
achieved