MITSUBISHI 3000GT 1991 Workshop Manual
Manufacturer: MITSUBISHI, Model Year: 1991, Model line: 3000GT, Model: MITSUBISHI 3000GT 1991Pages: 1146, PDF Size: 76.68 MB
Page 41 of 1146
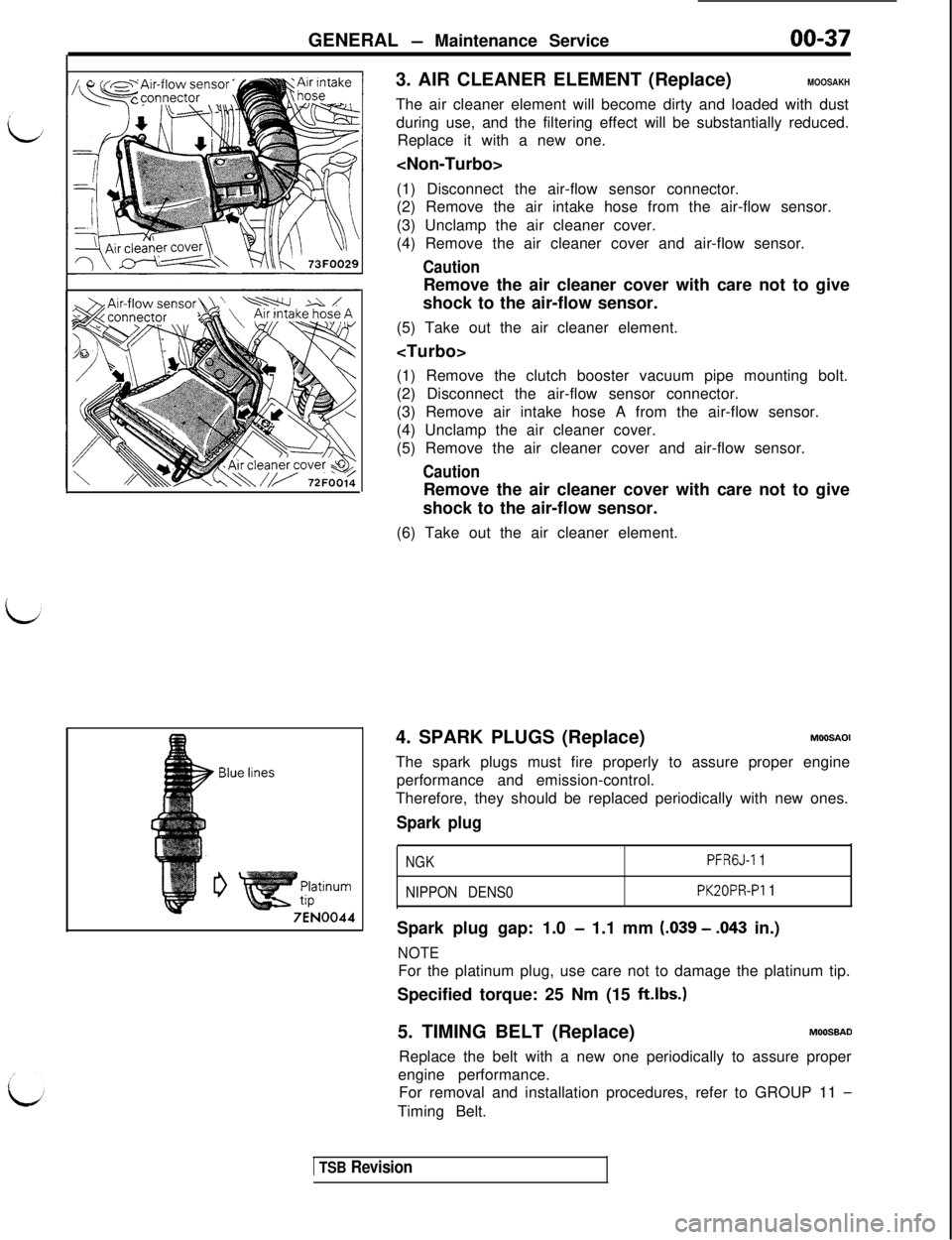
GENERAL - Maintenance Service00-37
3. AIR CLEANER ELEMENT (Replace)
MOOSAKHThe air cleaner element will become dirty and loaded with dust
during use, and the filtering effect will be substantially reduced.
Replace it with a new one.
(1) Disconnect the air-flow sensor connector.
(2) Remove the air intake hose from the air-flow sensor.
(3) Unclamp the air cleaner cover.
(4) Remove the air cleaner cover and air-flow sensor.
CautionRemove the air cleaner cover with care not to give
shock to the air-flow sensor.
(5) Take out the air cleaner element.
(1) Remove the clutch booster vacuum pipe mounting bolt.
(2) Disconnect the air-flow sensor connector.
(3) Remove air intake hose A from the air-flow sensor.
(4) Unclamp the air cleaner cover.
(5) Remove the air cleaner cover and air-flow sensor.
CautionRemove the air cleaner cover with care not to give
shock to the air-flow sensor.
(6) Take out the air cleaner element.
4. SPARK PLUGS (Replace)
MOOSAOIThe spark plugs must fire properly to assure proper engine
performance and emission-control.
Therefore, they should be replaced periodically with new ones.
Spark plug
NGKPFRGJ-1 1
NIPPON DENS0
PK20PR-PI 1Spark plug gap: 1.0
- 1.1 mm LO39 - -043 in.)
NOTEFor the platinum plug, use care not to damage the platinum tip.
Specified torque: 25 Nm (15
ft.lbs.15. TIMING BELT (Replace)
MOOSBADReplace the belt with a new one periodically to assure proper
engine performance.
For removal and installation procedures, refer to GROUP 11
-Timing Belt.
1 TSB Revision
Page 42 of 1146
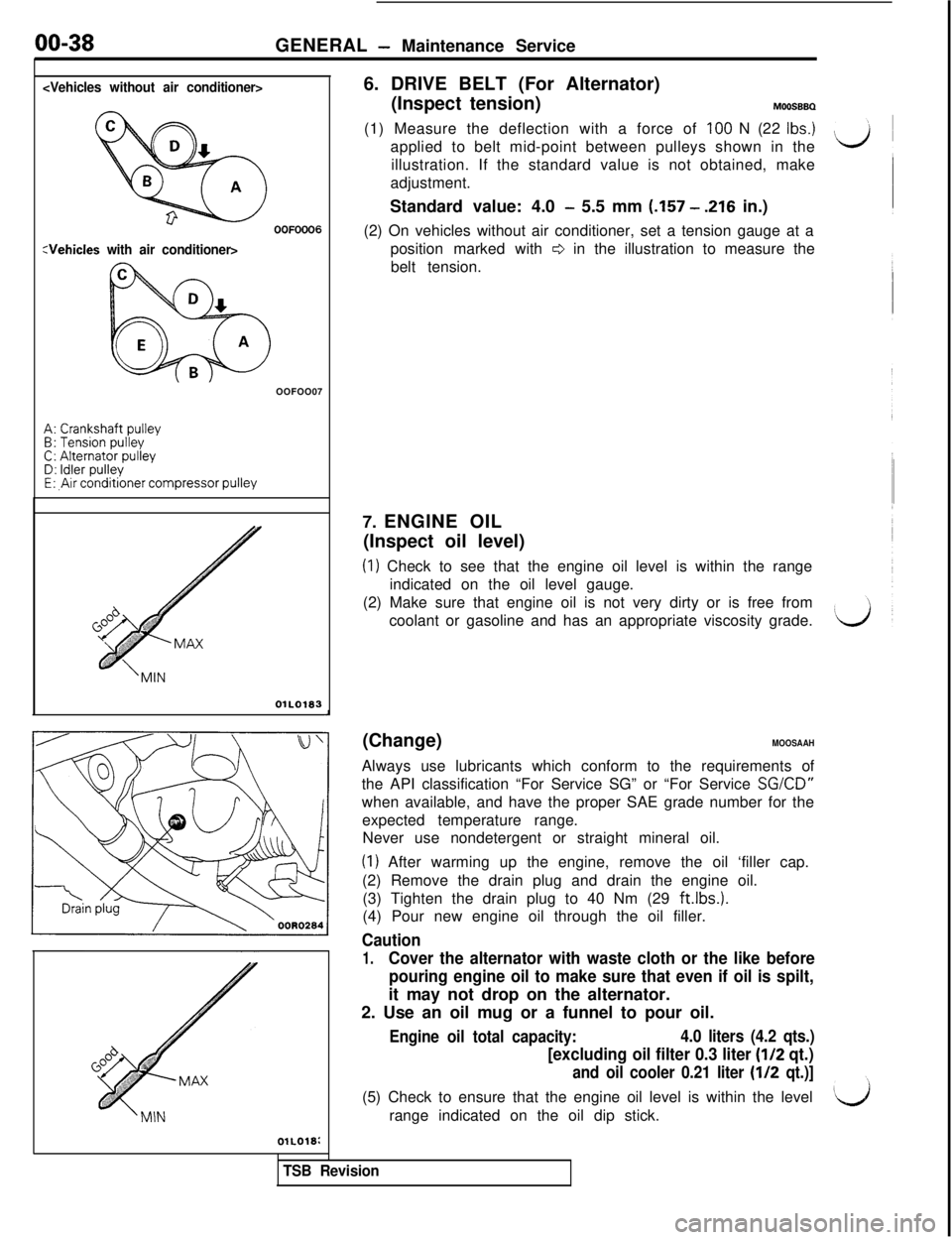
00-38GENERAL - Maintenance Service
00F0006
:Vehicles with air conditioner>OOFOO07
A: Crankshaft pulleyB: Tension pulleyC: Alternator pulleyD: Idler pulleyE: ,Air conditioner compressor pulley
OlLO183
OlLO18:(Inspect tension)
MOOS88(1(1) Measure the deflection with a force of
100 N (22 Ibs.)applied to belt mid-point between pulleys shown in the
illustration. If the standard value is not obtained, make
adjustment.
Standard value: 4.0
- 5.5 mm (.157 - 216 in.)
(2) On vehicles without air conditioner, set a tension gauge at a
position marked with
r3 in the illustration to measure the
belt tension.
7. ENGINE OIL
(Inspect oil level)
(I) Check to see that the engine oil level is within the range
indicated on the oil level gauge.
(2) Make sure that engine oil is not very dirty or is free from
coolant or gasoline and has an appropriate viscosity grade.J
(Change)
MOOSAAHAlways use lubricants which conform to the requirements of
the API classification “For Service SG” or “For Service
SGKD”when available, and have the proper SAE grade number for the
expected temperature range.
Never use nondetergent or straight mineral oil.
(1) After warming up the engine, remove the oil ‘filler cap.
(2) Remove the drain plug and drain the engine oil.
(3) Tighten the drain plug to 40 Nm (29 ft.lbs.).
(4) Pour new engine oil through the oil filler.
Caution
1.Cover the alternator with waste cloth or the like before
pouring engine oil to make sure that even if oil is spilt,it may not drop on the alternator.
2. Use an oil mug or a funnel to pour oil.
Engine oil total capacity:4.0 liters (4.2 qts.)
[excluding oil filter 0.3 liter (l/2 qt.)
and oil cooler 0.21 liter (l/2 qt.)](5) Check to ensure that the engine oil level is within the level
range indicated on the oil dip stick.
TSB Revision
Page 43 of 1146
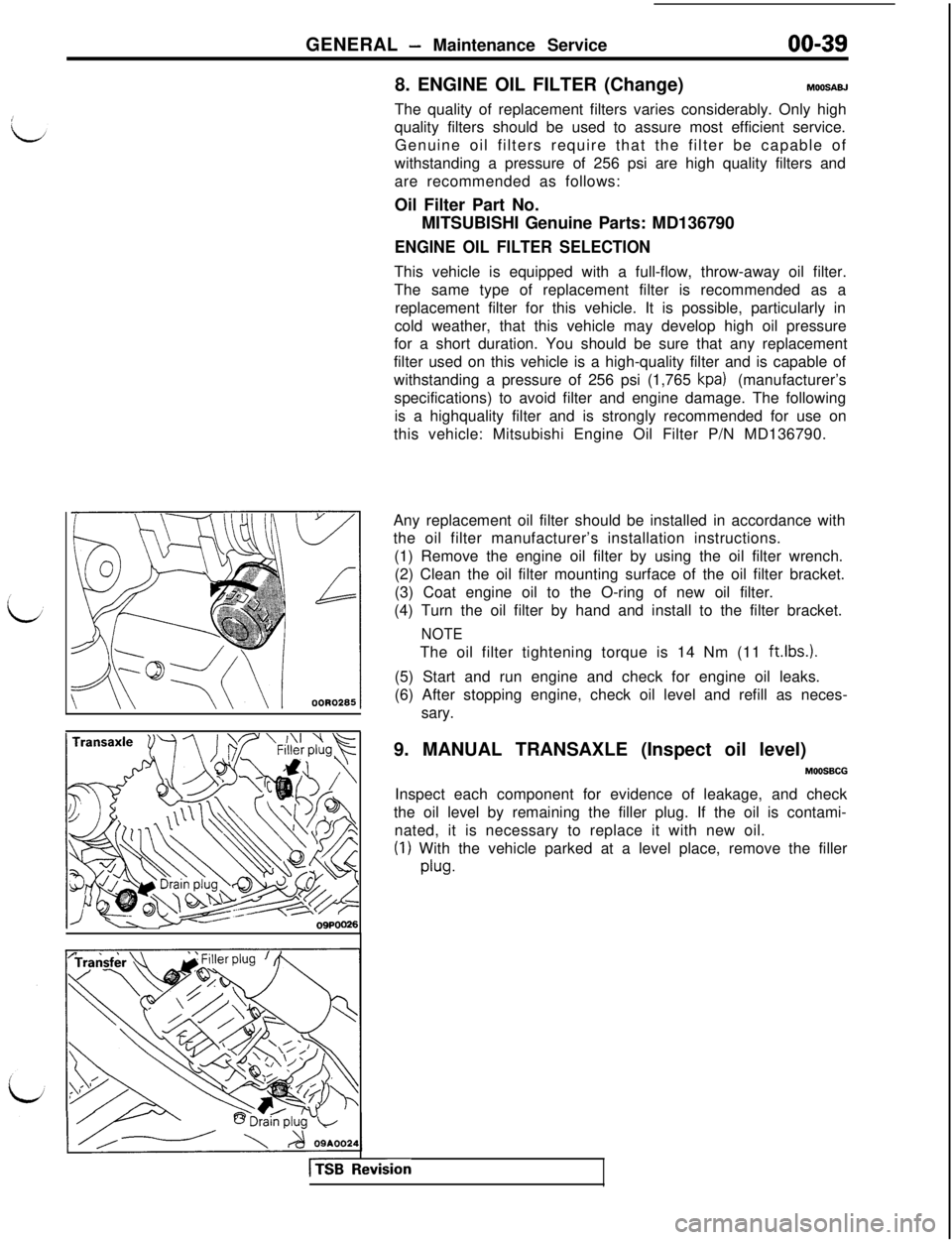
GENERAL - Maintenance Service00-39ogPOO268. ENGINE OIL FILTER (Change)
MOOEAEJThe quality of replacement filters varies considerably. Only high
quality filters should be used to assure most efficient service.
Genuine oil filters require that the filter be capable of
withstanding a pressure of 256 psi are high quality filters and
are recommended as follows:
Oil Filter Part No.
MITSUBISHI Genuine Parts: MD136790
ENGINE OIL FILTER SELECTIONThis vehicle is equipped with a full-flow, throw-away oil filter.
The same type of replacement filter is recommended as a
replacement filter for this vehicle. It is possible, particularly in
cold weather, that this vehicle may develop high oil pressure
for a short duration. You should be sure that any replacement
filter used on this vehicle is a high-quality filter and is capable of
withstanding a pressure of 256 psi (1,765
kpa) (manufacturer’s
specifications) to avoid filter and engine damage. The following
is a highquality filter and is strongly recommended for use on
this vehicle: Mitsubishi Engine Oil Filter P/N MD136790.
Any replacement oil filter should be installed in accordance with
the oil filter manufacturer’s installation instructions.
(1) Remove the engine oil filter by using the oil filter wrench.
(2) Clean the oil filter mounting surface of the oil filter bracket.
(3) Coat engine oil to the O-ring of new oil filter.
(4) Turn the oil filter by hand and install to the filter bracket.
NOTEThe oil filter tightening torque is 14 Nm (11
ft.lbs.1.(5) Start and run engine and check for engine oil leaks.
(6) After stopping engine, check oil level and refill as neces-
sary.
9. MANUAL TRANSAXLE (Inspect oil level)
MOOSBCGInspect each component for evidence of leakage, and check
the oil level by remaining the filler plug. If the oil is contami-
nated, it is necessary to replace it with new oil.
(1) With the vehicle parked at a level place, remove the filler
plug.
-Revision
Page 44 of 1146
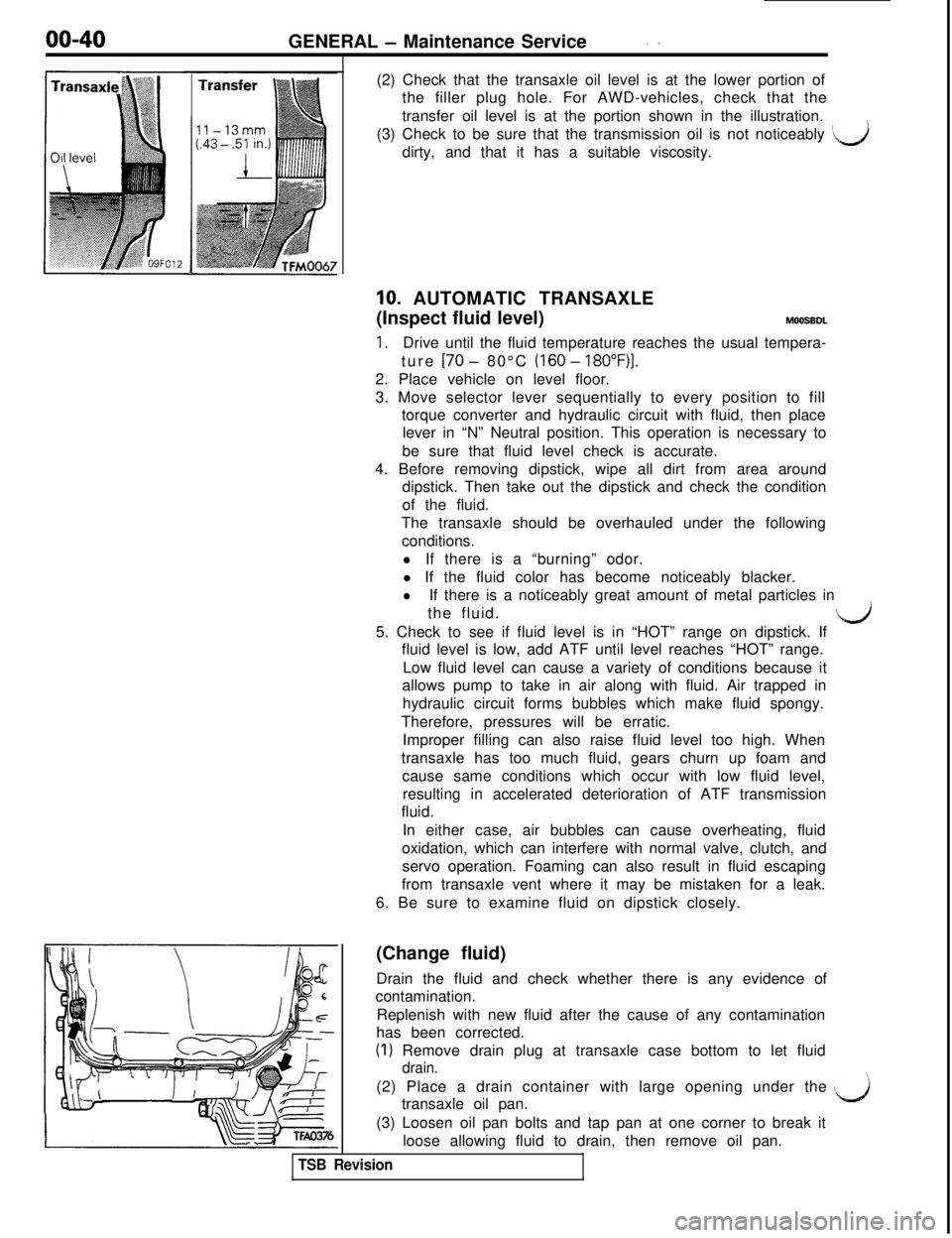
00-40
GENERAL - Maintenance Service
(2) Check that the transaxle oil level is at the lower portion of
the filler plug hole. For AWD-vehicles, check that the
transfer oil level is at the portion shown in the illustration.
(3) Check to be sure that the transmission oil is not noticeably
‘ddirty, and that it has a suitable viscosity.
10. AUTOMATIC TRANSAXLE
(Inspect fluid level)
MOOSEDL
1.Drive until the fluid temperature reaches the usual tempera-
ture
[70 - 80°C (160 - 18O”F)I.2. Place vehicle on level floor.
3. Move selector lever sequentially to every position to fill
torque converter and hydraulic circuit with fluid, then place
lever in “N” Neutral position. This operation is necessary to
be sure that fluid level check is accurate.
4. Before removing dipstick, wipe all dirt from area around
dipstick. Then take out the dipstick and check the condition
of the fluid.
The transaxle should be overhauled under the following
conditions.
l If there is a “burning” odor.
l If the fluid color has become noticeably blacker.
lIf there is a noticeably great amount of metal particles in
the fluid.
5. Check to see if fluid level is in “HOT” range on dipstick. If
fluid level is low, add ATF until level reaches “HOT” range.
Low fluid level can cause a variety of conditions because it
allows pump to take in air along with fluid. Air trapped in
hydraulic circuit forms bubbles which make fluid spongy.
Therefore, pressures will be erratic.
Improper filling can also raise fluid level too high. When
transaxle has too much fluid, gears churn up foam and
cause same conditions which occur with low fluid level,
resulting in accelerated deterioration of ATF transmission
fluid.
In either case, air bubbles can cause overheating, fluid
oxidation, which can interfere with normal valve, clutch, and
servo operation. Foaming can also result in fluid escaping
from transaxle vent where it may be mistaken for a leak.
6. Be sure to examine fluid on dipstick closely.
L/(Change fluid)
Drain the fluid and check whether there is any evidence of
contamination.
Replenish with new fluid after the cause of any contamination
has been corrected.
(1) Remove drain plug at transaxle case bottom to let fluid
drain.(2) Place a drain container with large opening under the
transaxle oil pan.
(3) Loosen oil pan bolts and tap pan at one corner to break it
loose allowing fluid to drain, then remove oil pan.
d
TSB Revision
Page 45 of 1146
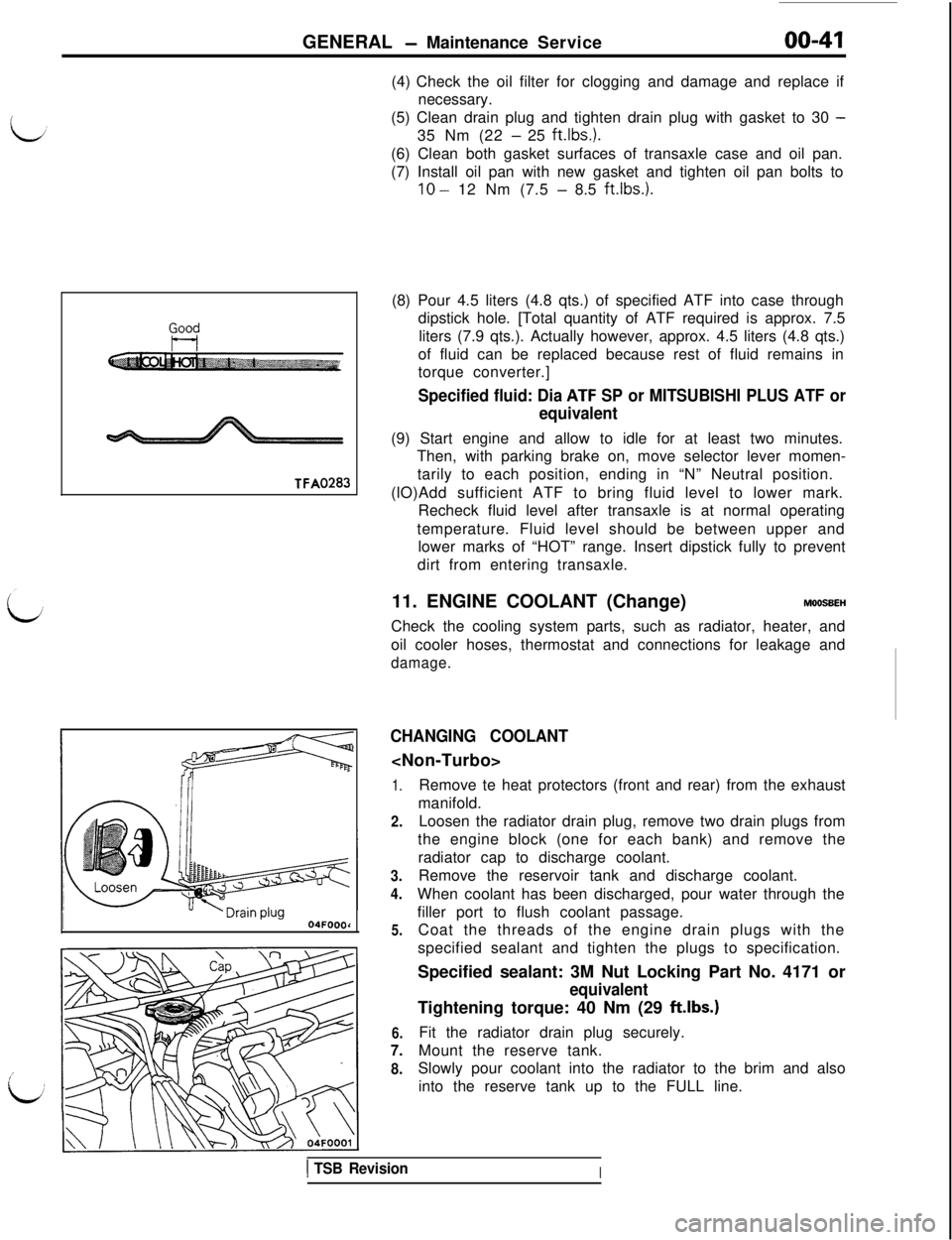
GENERAL - Maintenance Service00-41
Good
t-lVA0283
I04FOOOd(4) Check the oil filter for clogging and damage and replace if
necessary.
(5) Clean drain plug and tighten drain plug with gasket to 30
-35 Nm (22
- 25 ft.lbs.).
(6) Clean both gasket surfaces of transaxle case and oil pan.
(7) Install oil pan with new gasket and tighten oil pan bolts to
10 - 12 Nm (7.5 - 8.5 ft.lbs.).
(8) Pour 4.5 liters (4.8 qts.) of specified ATF into case through
dipstick hole. [Total quantity of ATF required is approx. 7.5
liters (7.9 qts.). Actually however, approx. 4.5 liters (4.8 qts.)
of fluid can be replaced because rest of fluid remains in
torque converter.]
Specified fluid: Dia ATF SP or MITSUBISHI PLUS ATF or
equivalent(9) Start engine and allow to idle for at least two minutes.
Then, with parking brake on, move selector lever momen-
tarily to each position, ending in “N” Neutral position.
(lO)Add sufficient ATF to bring fluid level to lower mark.
Recheck fluid level after transaxle is at normal operating
temperature. Fluid level should be between upper and
lower marks of “HOT” range. Insert dipstick fully to prevent
dirt from entering transaxle.
11. ENGINE COOLANT (Change)
MOOSBEHCheck the cooling system parts, such as radiator, heater, and
oil cooler hoses, thermostat and connections for leakage and
damage.
CHANGING COOLANT
1.
2.
3.
4.
5.
6.
7.
8.Remove te heat protectors (front and rear) from the exhaust
manifold.
Loosen the radiator drain plug, remove two drain plugs from
the engine block (one for each bank) and remove the
radiator cap to discharge coolant.
Remove the reservoir tank and discharge coolant.
When coolant has been discharged, pour water through the
filler port to flush coolant passage.
Coat the threads of the engine drain plugs with the
specified sealant and tighten the plugs to specification.
Specified sealant: 3M Nut Locking Part No. 4171 or
equivalentTightening torque: 40 Nm (29
ftlbs.)Fit the radiator drain plug securely.
Mount the reserve tank.
Slowly pour coolant into the radiator to the brim and also
into the reserve tank up to the FULL line.
1 TSB RevisionI
Page 46 of 1146
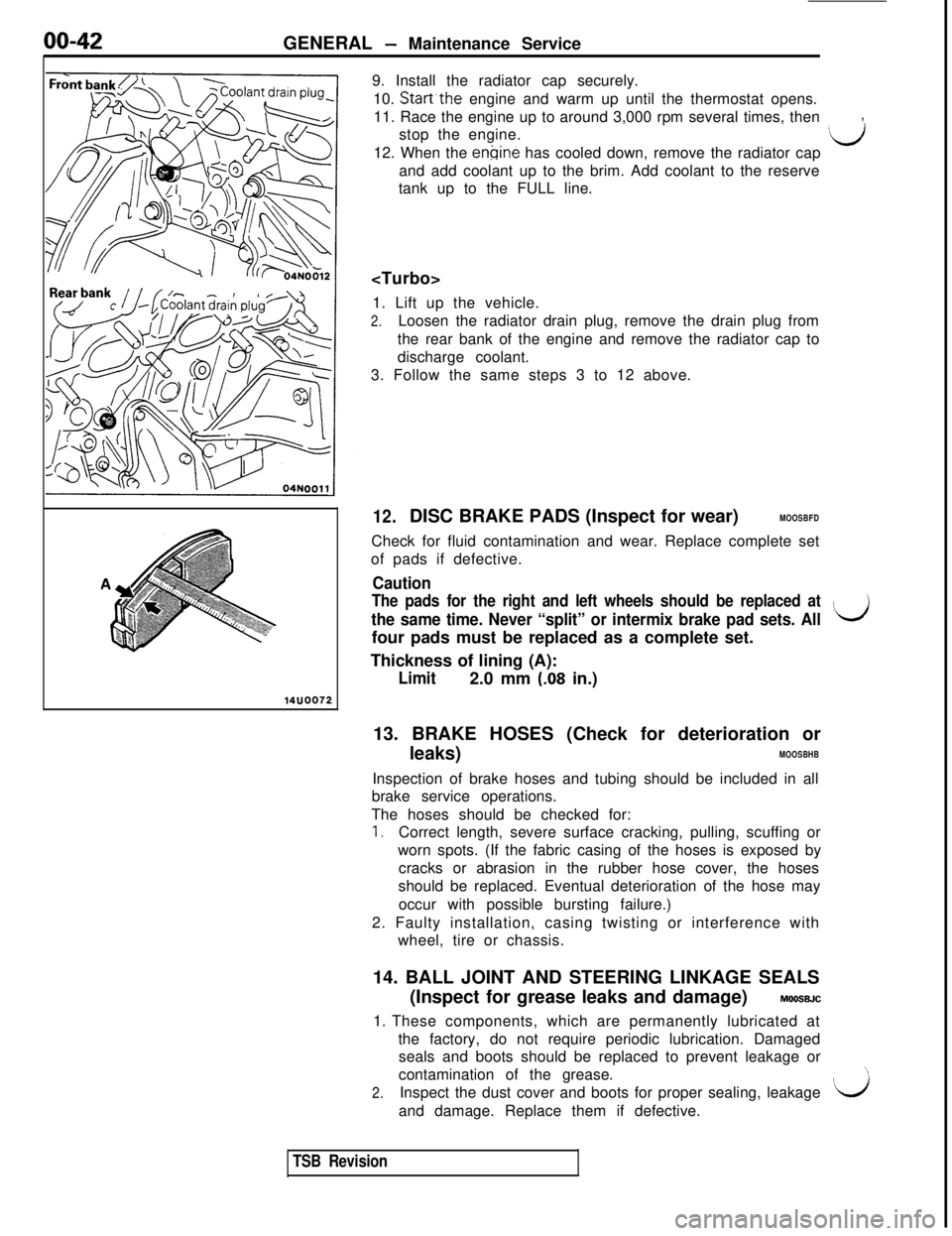
00-42GENERAL - Maintenance Service
14UOO729. Install the radiator cap securely.
10.
Start’the engine and warm up until the thermostat opens.
11. Race the engine up to around 3,000 rpm several times, then
stop the engine.,12. When the enkine has cooled down, remove the radiator cap
L/and add coolant up to the brim. Add coolant to the reserve
tank up to the FULL line.
1. Lift up the vehicle.
2.Loosen the radiator drain plug, remove the drain plug from
the rear bank of the engine and remove the radiator cap to
discharge coolant.
3. Follow the same steps 3 to 12 above.
12.DISC BRAKE PADS (Inspect for wear)MOOSBFDCheck for fluid contamination and wear. Replace complete set
of pads if defective.
Caution
The pads for the right and left wheels should be replaced atIIthe same time. Never “split” or intermix brake pad sets. AllUfour pads must be replaced as a complete set.
Thickness of lining (A):
Limit2.0 mm (.08 in.)
13. BRAKE HOSES (Check for deterioration or
leaks)
MOOSBHBInspection of brake hoses and tubing should be included in all
brake service operations.
The hoses should be checked for:
1.Correct length, severe surface cracking, pulling, scuffing or
worn spots. (If the fabric casing of the hoses is exposed by
cracks or abrasion in the rubber hose cover, the hoses
should be replaced. Eventual deterioration of the hose may
occur with possible bursting failure.)
2. Faulty installation, casing twisting or interference with
wheel, tire or chassis.
14. BALL JOINT AND STEERING LINKAGE SEALS
(Inspect for grease leaks and damage)
MOOSglC1. These components, which are permanently lubricated at
the factory, do not require periodic lubrication. Damaged
seals and boots should be replaced to prevent leakage or
contamination of the grease.
2.Inspect the dust cover and boots for proper sealing, leakageIdand damage. Replace them if defective.
TSB Revision
Page 47 of 1146
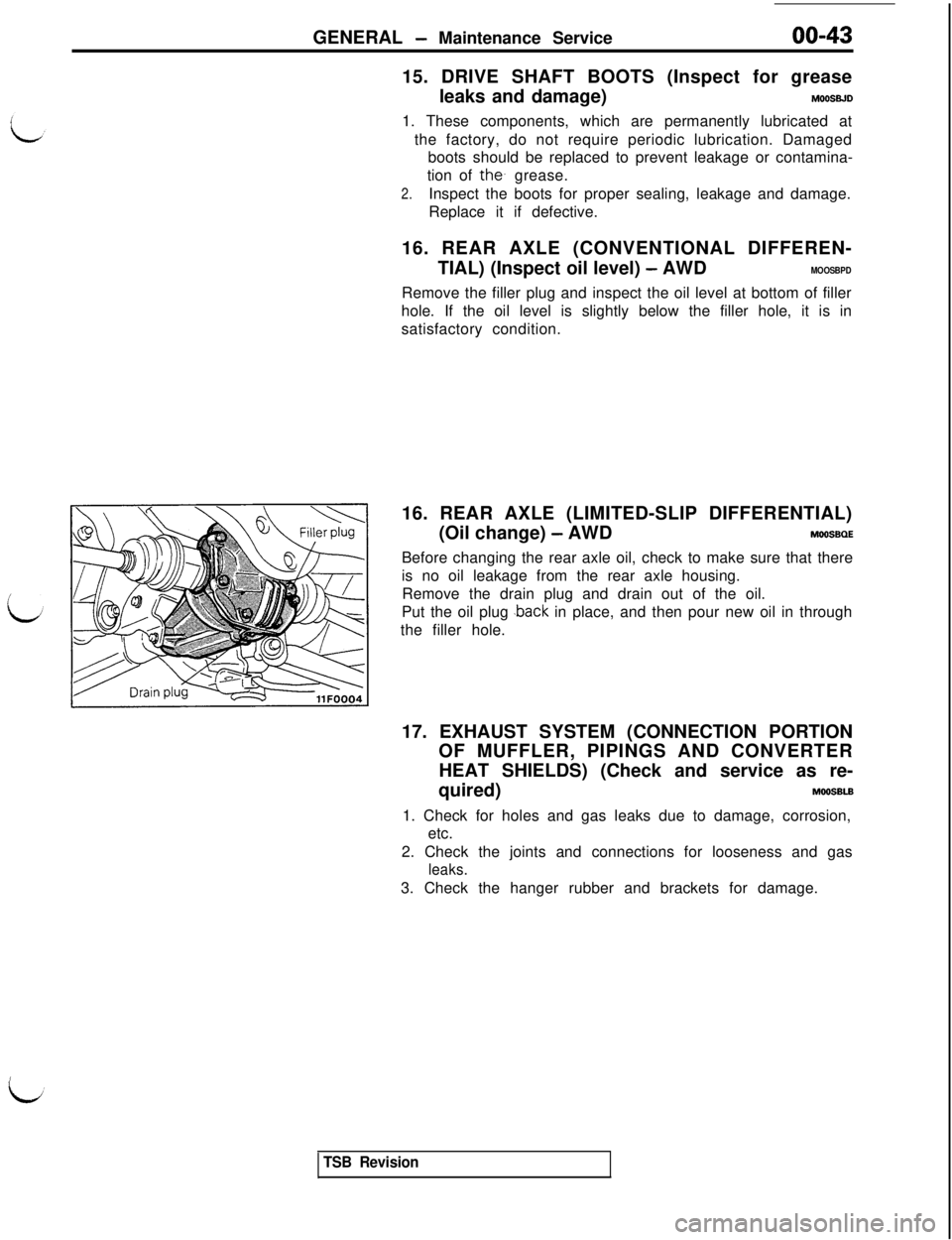
GENERAL - Maintenance Service00-43
15. DRIVE SHAFT BOOTS (Inspect for grease
leaks and damage)
MOOSBJD1. These components, which are permanently lubricated at
the factory, do not require periodic lubrication. Damaged
boots should be replaced to prevent leakage or contamina-
tion of the, grease.
2.Inspect the boots for proper sealing, leakage and damage.
Replace it if defective.
16. REAR AXLE (CONVENTIONAL DIFFEREN-
TIAL) (Inspect oil level)
- AWDMOOSBPDRemove the filler plug and inspect the oil level at bottom of filler
hole. If the oil level is slightly below the filler hole, it is in
satisfactory condition.
16. REAR AXLE (LIMITED-SLIP DIFFERENTIAL)
(Oil change)
- AWDMOOSBQEBefore changing the rear axle oil, check to make sure that there
is no oil leakage from the rear axle housing.
Remove the drain plug and drain out of the oil.
Put the oil plug
,back in place, and then pour new oil in through
the filler hole.
17. EXHAUST SYSTEM (CONNECTION PORTION
OF MUFFLER, PIPINGS AND CONVERTER
HEAT SHIELDS) (Check and service as re-
quired)
MOOSBLB1. Check for holes and gas leaks due to damage, corrosion,
etc.
2. Check the joints and connections for looseness and gas
leaks.3. Check the hanger rubber and brackets for damage.
TSB Revision
Page 48 of 1146
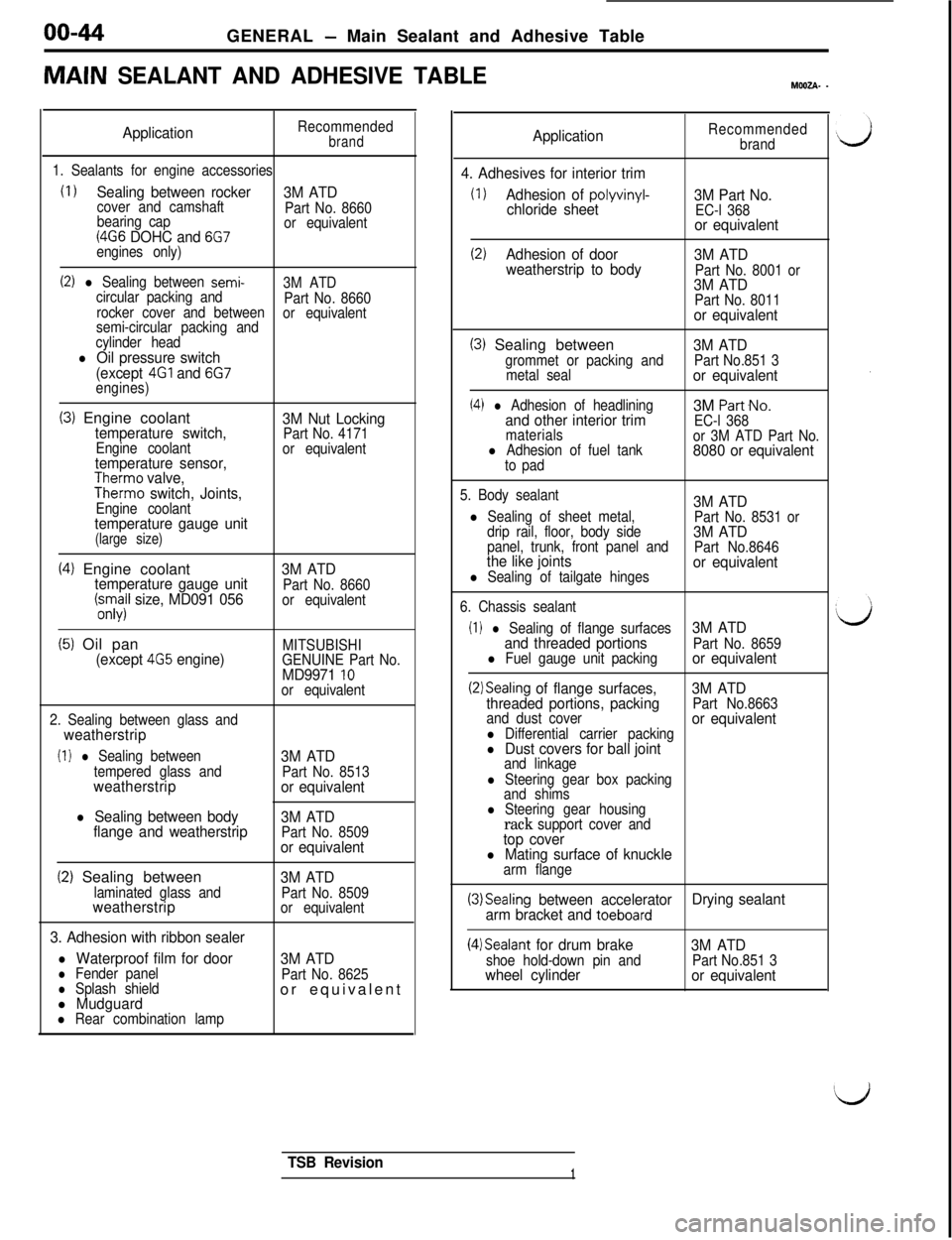
00-44
GENERAL - Main Sealant and Adhesive Table
MAIN SEALANT AND ADHESIVE TABLEMWZA- -
ApplicationRecommendedbrand
1. Sealants for engine accessories
(I 1Sealing between rocker
3M ATDcover and camshaft
Part No. 8660
bearing cap
(4G6 DOHC and 6G7or equivalent
engines only)
(2) l Sealing between semi-3M ATD
circular packing and
Part No. 8660
rocker cover and between
semi-circular packing andor equivalent
cylinder head
l Oil pressure switch
(except 4Gl and 6G7engines)
(3) Engine coolanttemperature switch,Engine coolanttemperature sensor,Therm0 valve,Therm0 switch, Joints,Engine coolanttemperature gauge unit(large size)
3M Nut LockingPart No. 4171
or equivalent
(4) Engine coolanttemperature gauge unit(;.s;il size, MD091 0563M ATDPart No. 8660
or equivalent
(5) Oil pan(except 4G5 engine)MITSUBISHI
GENUINE Part No.
MD9971 10or equivalent
2. Sealing between glass and
weatherstrip
(I 1 l Sealing between
tempered glass and
weatherstrip
l Sealing between body
flange and weatherstrip3M ATD
Part No. 8513or equivalent
3M ATD
Part No. 8509or equivalent
(2) Sealing betweenlaminated glass andweatherstrip
3. Adhesion with ribbon sealer
l Waterproof film for doorl Fender panell Splash shieldl Mudguardl Rear combination lamp
3M ATDPart No. 8509
or equivalent
3M ATDPart No. 8625or equivalent
ApplicationRecommended
brand
4. Adhesives for interior trim
(1)Adhesion of polyvinyl-chloride sheet3M Part No.EC-l 368or equivalent
(2)Adhesion of door
3M ATD
weatherstrip to body
Part No. 8001 or3M ATDPart No. 8011or equivalent
(3) Sealing betweengrommet or packing and
metal seal
(4) l Adhesion of headliningand other interior trimmaterialsl Adhesion of fuel tank
to pad
3M ATDPart No.851 3or equivalent3M
Part-No.
EC-l 368
or 3M ATD Part No.
8080 or equivalent
5. Body sealant3M ATDl Sealing of sheet metal,
Part No. 8531 or
drip rail, floor, body side3M ATDpanel, trunk, front panel and
Part No.8646the like jointsl Sealing of tailgate hingesor equivalent
6. Chassis sealant
(I 1 l Sealing of flange surfaces3M ATD
and threaded portions
Part No. 8659l Fuel gauge unit packingor equivalent
(2)Sealing of flange surfaces,3M ATD
threaded portions, packingPart No.8663
and dust cover
l Differential carrier packingor equivalent
l Dust covers for ball jointand linkage
l Steering gear box packing
and shims
l Steering gear housingrack support cover andtop coverl Mating surface of knucklearm flange
(3)Sealing between accelerator
arm bracket and toeboardDrying sealant
(4)Sealant for drum brakeshoe hold-down pin andwheel cylinder3M ATDPart No.851 3or equivalent
TSB Revision1
Page 49 of 1146
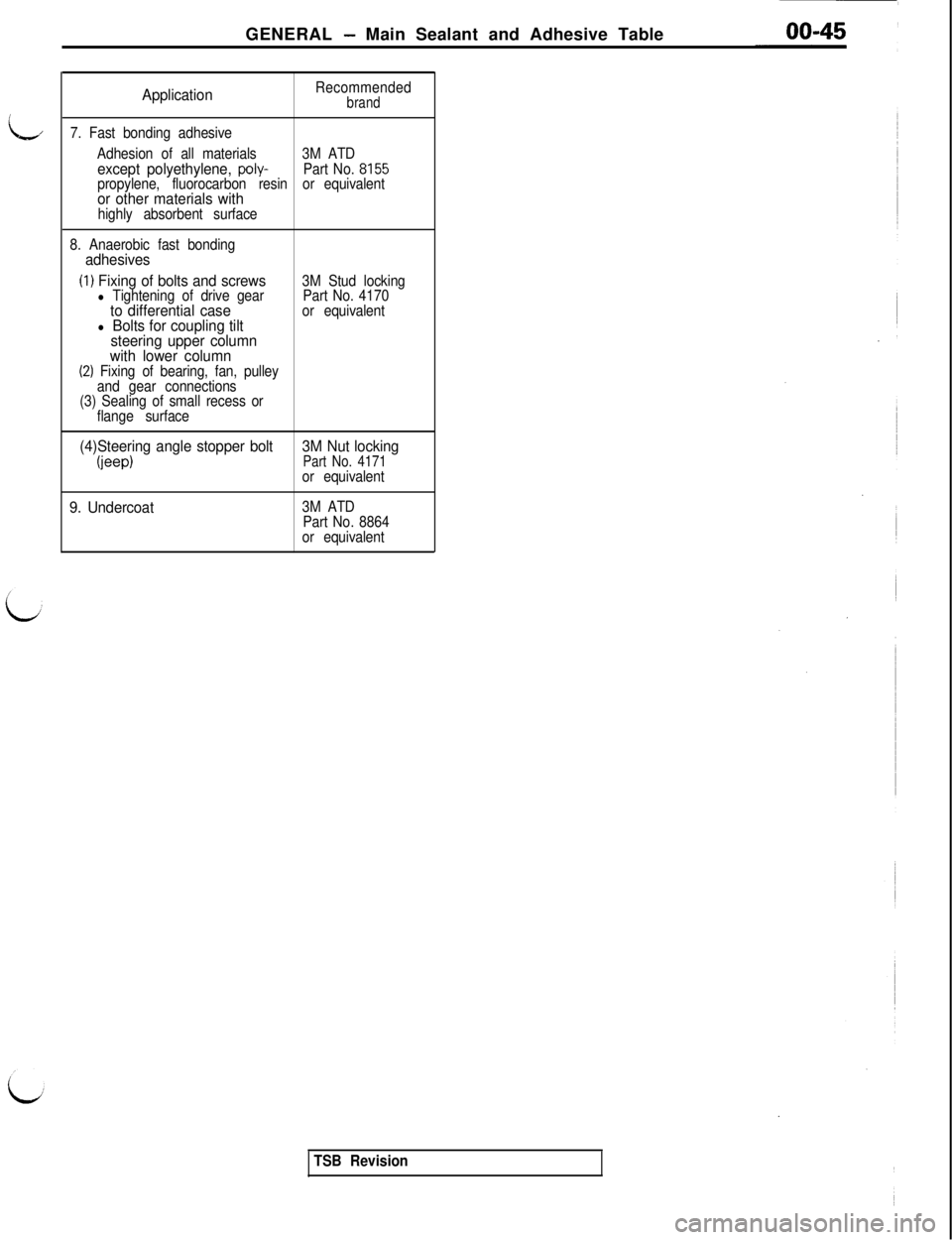
GENERAL - Main Sealant and Adhesive Table
I,i
ApplicationRecommendedbrand
7. Fast bonding adhesive
Adhesion of all materials3M ATD
except polyethylene, poly-Part No. 8155propylene, fluorocarbon resinor equivalentor other materials withhighly absorbent surface
8. Anaerobic fast bonding
adhesives
(I) Fixing of bolts and screws3M Stud lockingl Tightening of drive gearPart No. 4170to differential caseor equivalentl Bolts for coupling tilt
steering upper column
with lower column
(2) Fixing of bearing, fan, pulley
and gear connections
(3) Sealing of small recess or
flange surface
(4)Steering angle stopper bolt
(jeep)
3M Nut lockingPart No. 4171or equivalent
9. Undercoat3M ATD
Part No. 8864
or equivalent
TSB Revision
Page 50 of 1146
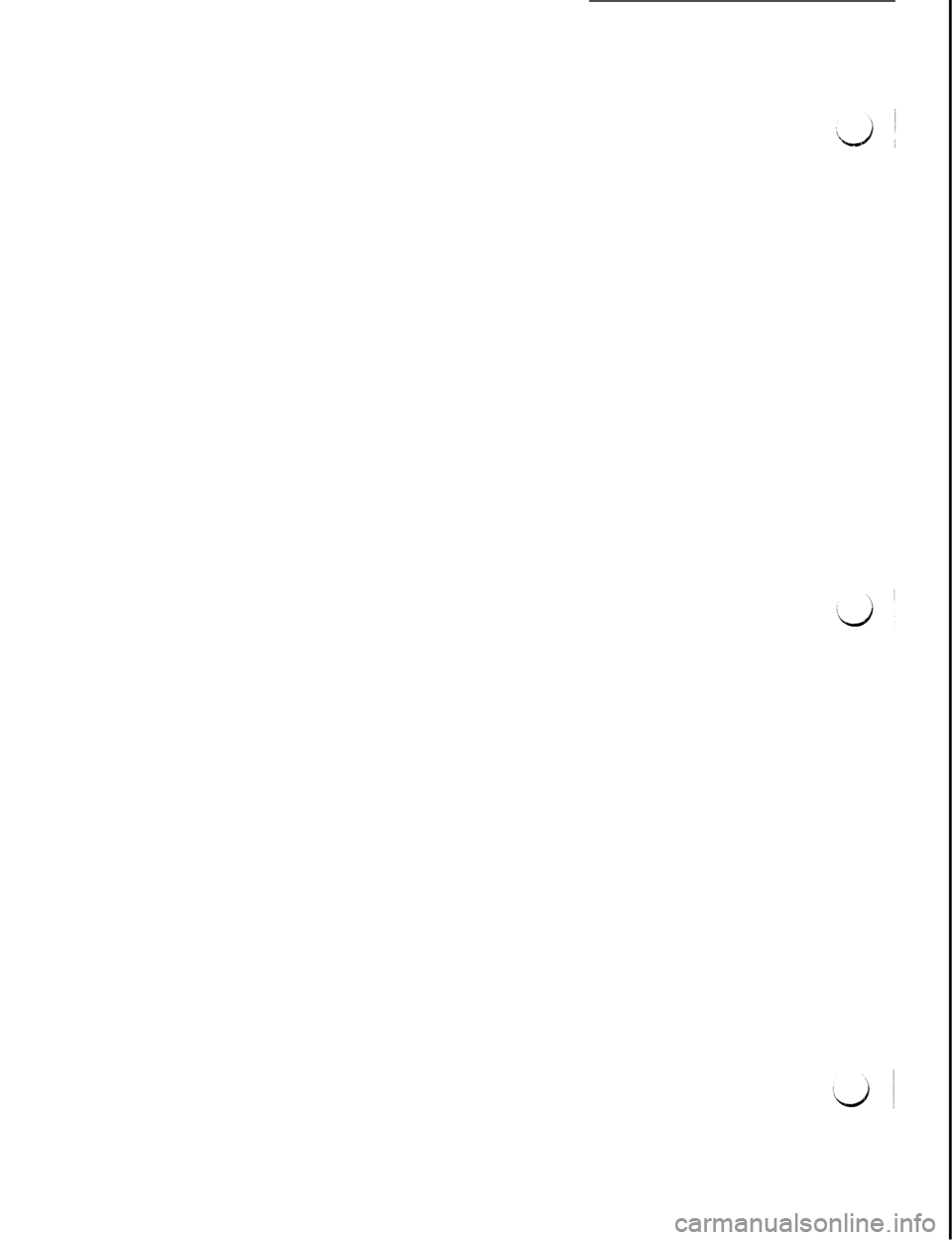