ISUZU KB P190 2007 Workshop Repair Manual
Manufacturer: ISUZU, Model Year: 2007, Model line: KB P190, Model: ISUZU KB P190 2007Pages: 6020, PDF Size: 70.23 MB
Page 281 of 6020
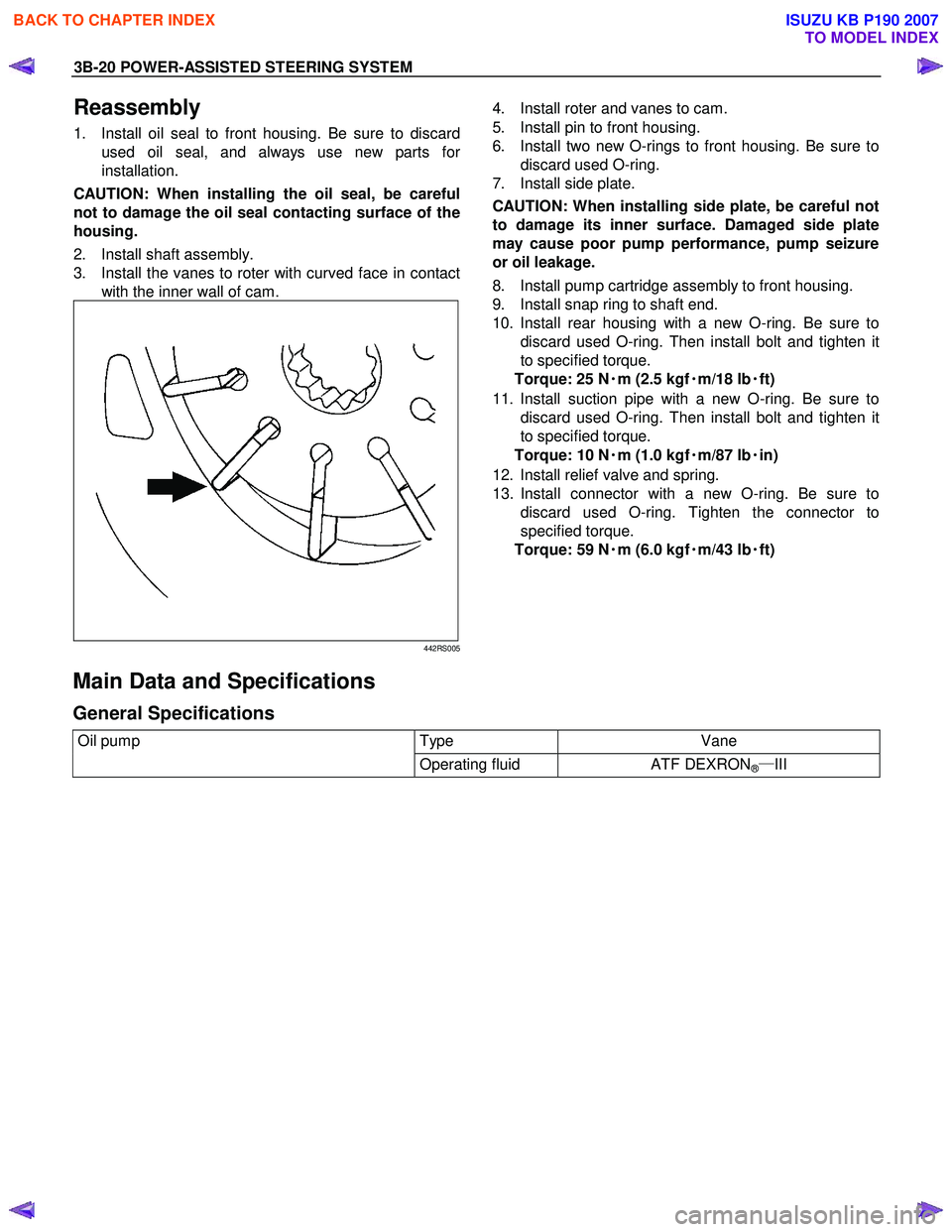
3B-20 POWER-ASSISTED STEERING SYSTEM
Reassembly
1. Install oil seal to front housing. Be sure to discard
used oil seal, and always use new parts fo
r
installation.
CAUTION: When installing the oil seal, be careful
not to damage the oil seal contacting surface of the
housing.
2. Install shaft assembly.
3. Install the vanes to roter with curved face in contact with the inner wall of cam.
442RS005
4. Install roter and vanes to cam.
5. Install pin to front housing.
6. Install two new O-rings to front housing. Be sure to discard used O-ring.
7. Install side plate.
CAUTION: When installing side plate, be careful not
to damage its inner surface. Damaged side plate
may cause poor pump performance, pump seizure
or oil leakage.
8. Install pump cartridge assembly to front housing.
9. Install snap ring to shaft end.
10. Install rear housing with a new O-ring. Be sure to discard used O-ring. Then install bolt and tighten it
to specified torque.
Torque: 25 N ・
・・
・
m (2.5 kgf ・
・・
・
m/18 lb ・
・・
・
ft)
11. Install suction pipe with a new O-ring. Be sure to discard used O-ring. Then install bolt and tighten it
to specified torque.
Torque: 10 N ・
・・
・
m (1.0 kgf ・
・・
・
m/87 lb ・
・・
・
in)
12. Install relief valve and spring.
13. Install connector with a new O-ring. Be sure to discard used O-ring. Tighten the connector to
specified torque.
Torque: 59 N ・
・・
・
m (6.0 kgf ・
・・
・
m/43 lb ・
・・
・
ft)
Main Data and Specifications
General Specifications
Oil pump Type Vane
Operating fluid
ATF DEXRON®―III
BACK TO CHAPTER INDEX
TO MODEL INDEX
ISUZU KB P190 2007
Page 282 of 6020
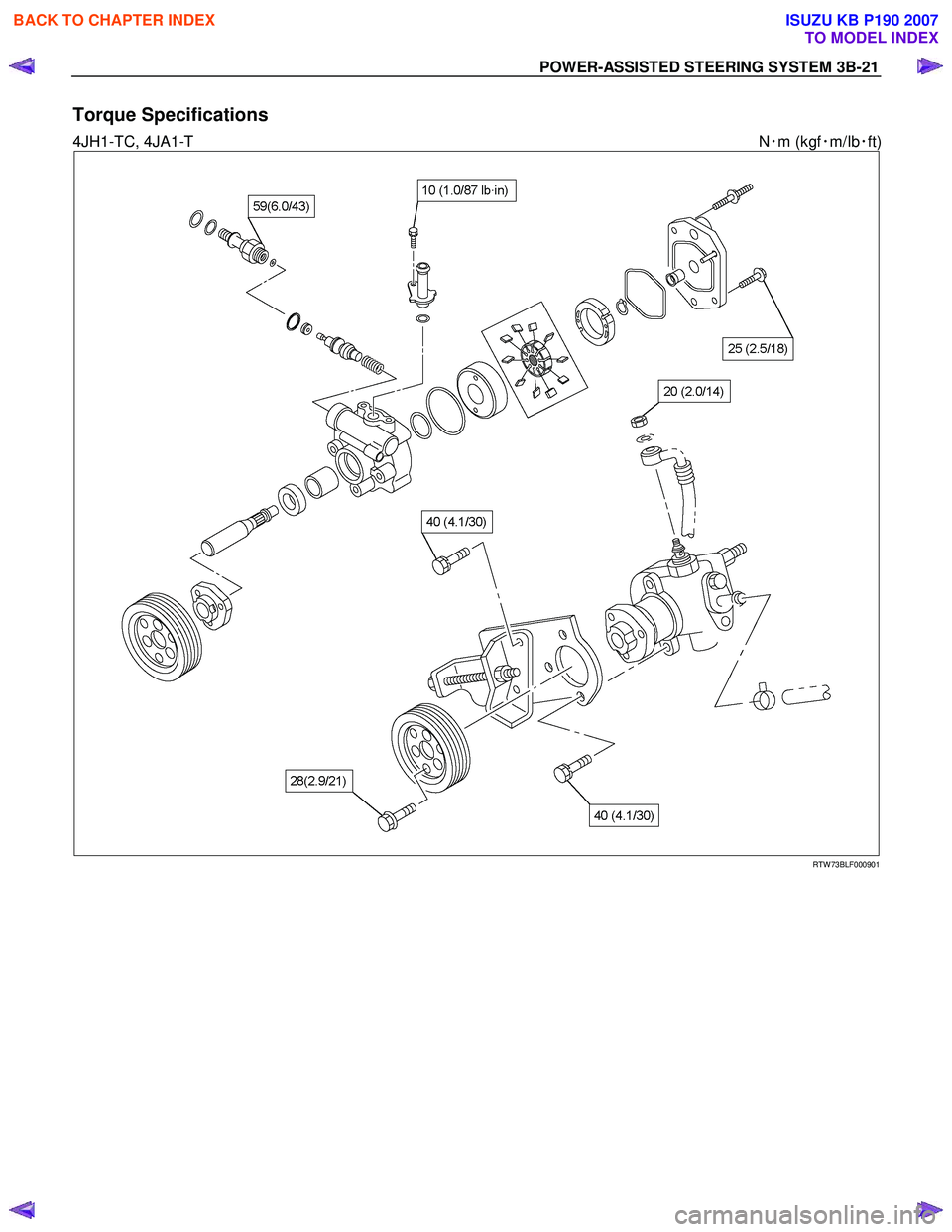
POWER-ASSISTED STEERING SYSTEM 3B-21
Torque Specifications
4JH1-TC, 4JA1-T N・m (kgf ・m/Ib ・ft)
RTW 73BLF000901
BACK TO CHAPTER INDEX
TO MODEL INDEX
ISUZU KB P190 2007
Page 283 of 6020
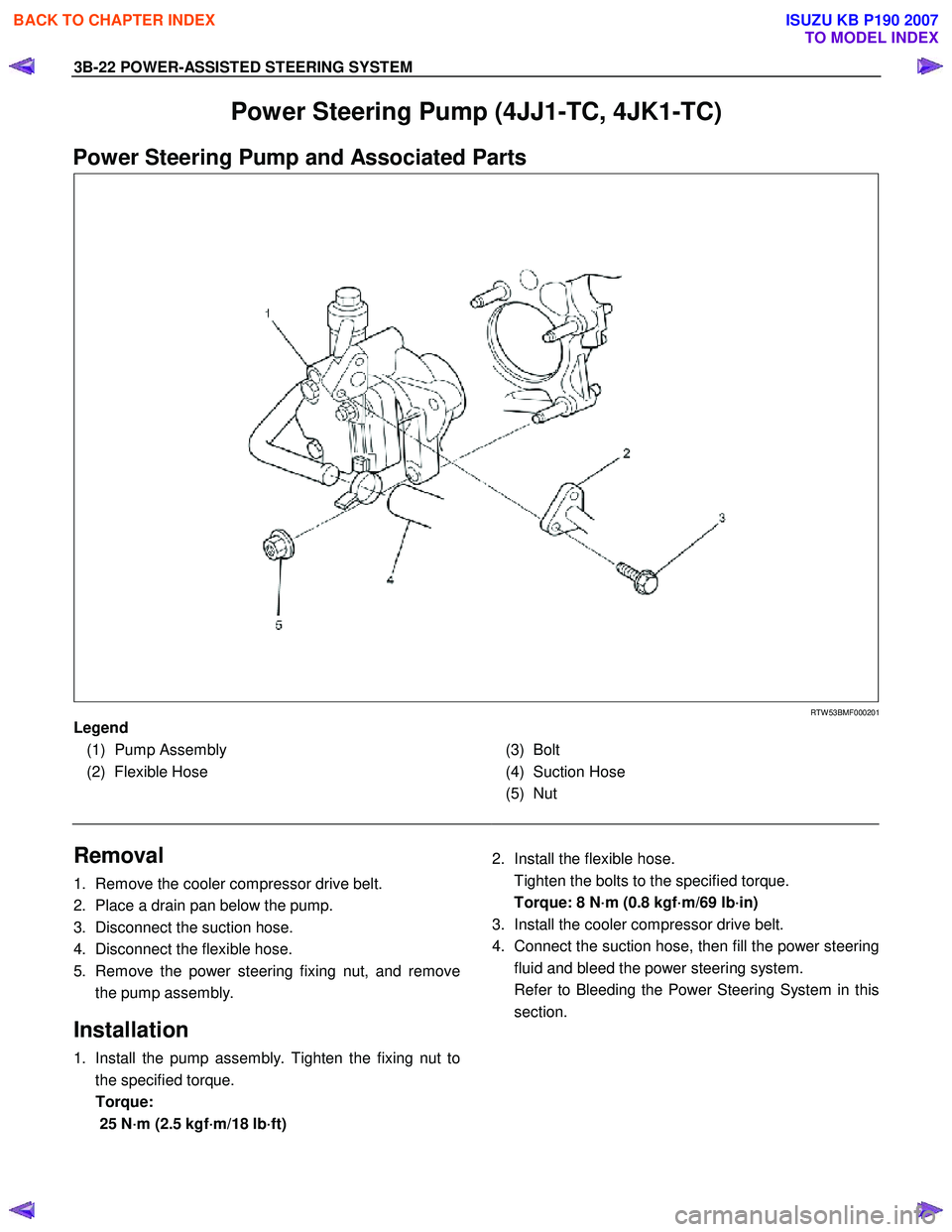
3B-22 POWER-ASSISTED STEERING SYSTEM
Power Steering Pump (4JJ1-TC, 4JK1-TC)
Power Steering Pump and Associated Parts
RTW 53BMF000201
Legend
(1) Pump Assembly
(2) Flexible Hose
(3) Bolt
(4) Suction Hose
(5) Nut
Removal
1. Remove the cooler compressor drive belt.
2. Place a drain pan below the pump.
3. Disconnect the suction hose.
4. Disconnect the flexible hose.
5. Remove the power steering fixing nut, and remove the pump assembly.
Installation
1. Install the pump assembly. Tighten the fixing nut to
the specified torque.
Torque: 25 N·m (2.5 kgf·m/18 lb·ft)
2. Install the flexible hose.
Tighten the bolts to the specified torque.
Torque: 8 N·m (0.8 kgf·m/69 lb·in)
3. Install the cooler compressor drive belt.
4. Connect the suction hose, then fill the power steering fluid and bleed the power steering system.
Refer to Bleeding the Power Steering System in this section.
BACK TO CHAPTER INDEX
TO MODEL INDEX
ISUZU KB P190 2007
Page 284 of 6020
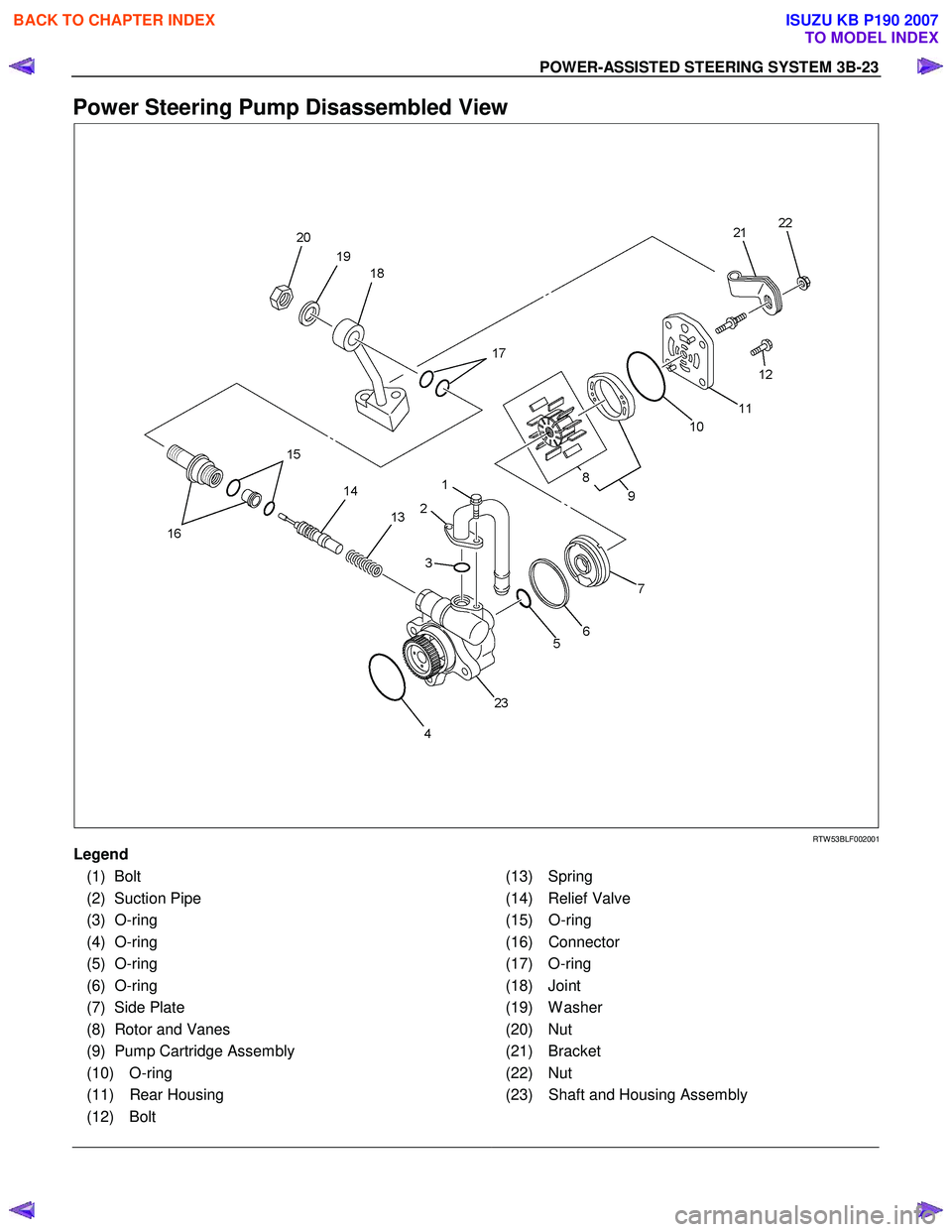
POWER-ASSISTED STEERING SYSTEM 3B-23
Power Steering Pump Disassembled View
RTW 53BLF002001
Legend (1) Bolt
(2) Suction Pipe
(3) O-ring
(4) O-ring
(5) O-ring
(6) O-ring
(7) Side Plate
(8) Rotor and Vanes
(9) Pump Cartridge Assembly
(10) O-ring
(11) Rear Housing
(12) Bolt
(13) Spring
(14) Relief Valve
(15) O-ring
(16) Connector
(17) O-ring
(18) Joint
(19) W asher
(20) Nut
(21) Bracket
(22) Nut
(23) Shaft and Housing Assembly
BACK TO CHAPTER INDEX
TO MODEL INDEX
ISUZU KB P190 2007
Page 285 of 6020
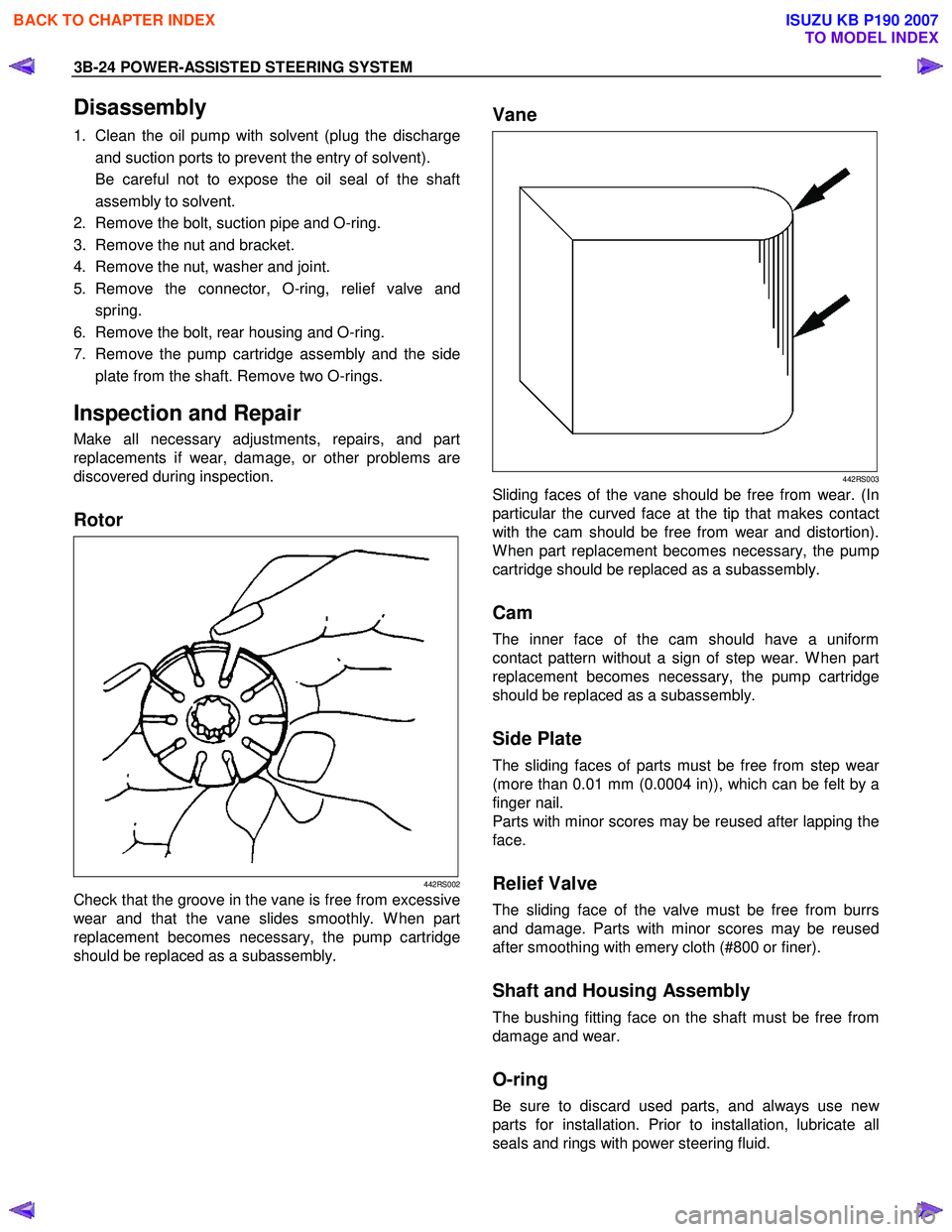
3B-24 POWER-ASSISTED STEERING SYSTEM
Disassembly
1. Clean the oil pump with solvent (plug the discharge
and suction ports to prevent the entry of solvent).
Be careful not to expose the oil seal of the shaft assembly to solvent.
2. Remove the bolt, suction pipe and O-ring.
3. Remove the nut and bracket.
4. Remove the nut, washer and joint.
5. Remove the connector, O-ring, relief valve and spring.
6. Remove the bolt, rear housing and O-ring.
7. Remove the pump cartridge assembly and the side plate from the shaft. Remove two O-rings.
Inspection and Repair
Make all necessary adjustments, repairs, and part
replacements if wear, damage, or other problems are
discovered during inspection.
Rotor
442RS002
Check that the groove in the vane is free from excessive
wear and that the vane slides smoothly. W hen part
replacement becomes necessary, the pump cartridge
should be replaced as a subassembly.
Vane
442RS003
Sliding faces of the vane should be free from wear. (In
particular the curved face at the tip that makes contact
with the cam should be free from wear and distortion).
W hen part replacement becomes necessary, the pump
cartridge should be replaced as a subassembly.
Cam
The inner face of the cam should have a uniform
contact pattern without a sign of step wear. W hen part
replacement becomes necessary, the pump cartridge
should be replaced as a subassembly.
Side Plate
The sliding faces of parts must be free from step wear
(more than 0.01 mm (0.0004 in)), which can be felt by a
finger nail.
Parts with minor scores may be reused after lapping the
face.
Relief Valve
The sliding face of the valve must be free from burrs
and damage. Parts with minor scores may be reused
after smoothing with emery cloth (#800 or finer).
Shaft and Housing Assembly
The bushing fitting face on the shaft must be free from
damage and wear.
O-ring
Be sure to discard used parts, and always use new
parts for installation. Prior to installation, lubricate all
seals and rings with power steering fluid.
BACK TO CHAPTER INDEX
TO MODEL INDEX
ISUZU KB P190 2007
Page 286 of 6020
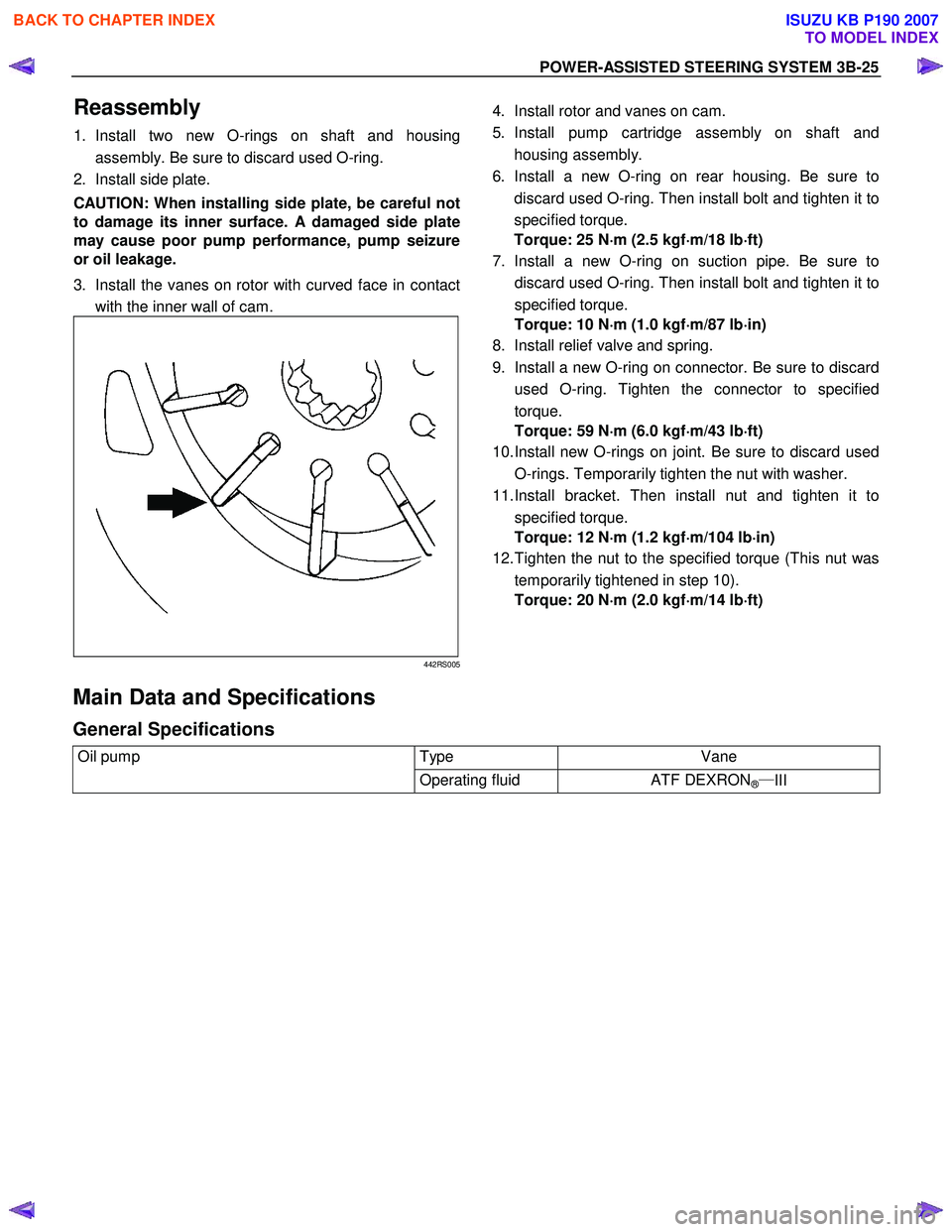
POWER-ASSISTED STEERING SYSTEM 3B-25
Reassembly
1. Install two new O-rings on shaft and housing
assembly. Be sure to discard used O-ring.
2. Install side plate.
CAUTION: When installing side plate, be careful not
to damage its inner surface. A damaged side plate
may cause poor pump performance, pump seizure
or oil leakage.
3. Install the vanes on rotor with curved face in contact with the inner wall of cam.
442RS005
4. Install rotor and vanes on cam.
5. Install pump cartridge assembly on shaft and housing assembly.
6. Install a new O-ring on rear housing. Be sure to discard used O-ring. Then install bolt and tighten it to
specified torque.
Torque: 25 N ⋅
⋅⋅
⋅
m (2.5 kgf ⋅
⋅⋅
⋅
m/18 lb ⋅
⋅⋅
⋅
ft)
7. Install a new O-ring on suction pipe. Be sure to
discard used O-ring. Then install bolt and tighten it to
specified torque.
Torque: 10 N ⋅
⋅⋅
⋅
m (1.0 kgf ⋅
⋅⋅
⋅
m/87 lb ⋅
⋅⋅
⋅
in)
8. Install relief valve and spring.
9. Install a new O-ring on connector. Be sure to discard used O-ring. Tighten the connector to specified
torque.
Torque: 59 N ⋅
⋅⋅
⋅
m (6.0 kgf ⋅
⋅⋅
⋅
m/43 lb ⋅
⋅⋅
⋅
ft)
10. Install new O-rings on joint. Be sure to discard used
O-rings. Temporarily tighten the nut with washer.
11. Install bracket. Then install nut and tighten it to specified torque.
Torque: 12 N ⋅
⋅⋅
⋅
m (1.2 kgf ⋅
⋅⋅
⋅
m/104 lb ⋅
⋅⋅
⋅
in)
12. Tighten the nut to the specified torque (This nut was
temporarily tightened in step 10).
Torque: 20 N ⋅
⋅⋅
⋅
m (2.0 kgf ⋅
⋅⋅
⋅
m/14 lb ⋅
⋅⋅
⋅
ft)
Main Data and Specifications
General Specifications
Oil pump Type Vane
Operating fluid
ATF DEXRON®―III
BACK TO CHAPTER INDEX
TO MODEL INDEX
ISUZU KB P190 2007
Page 287 of 6020

3B-26 POWER-ASSISTED STEERING SYSTEM
Torque Specifications
N⋅m (kgf ⋅m/Ib ⋅ft)
RTW 73BLF000701
BACK TO CHAPTER INDEX
TO MODEL INDEX
ISUZU KB P190 2007
Page 288 of 6020
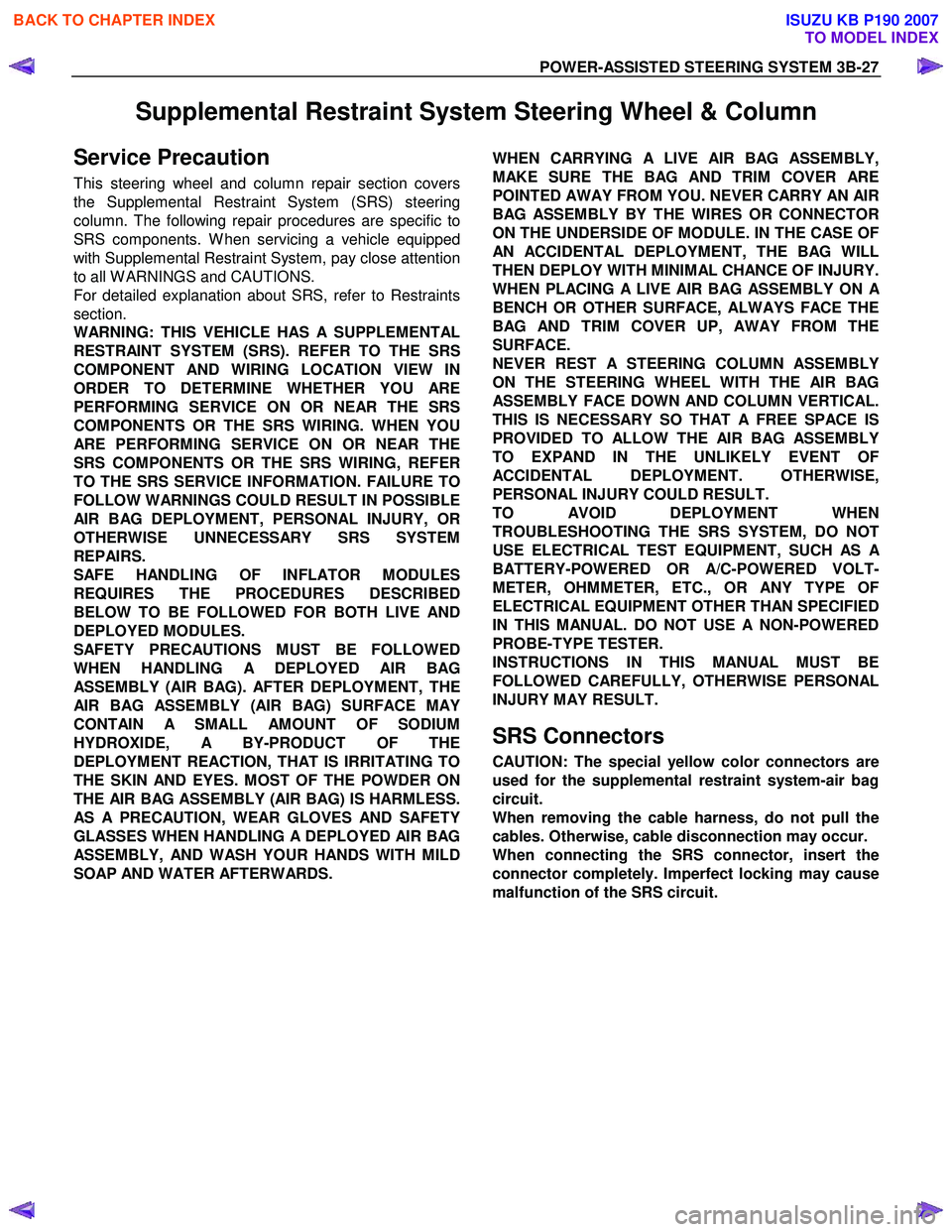
POWER-ASSISTED STEERING SYSTEM 3B-27
Supplemental Restraint System Steering Wheel & Column
Service Precaution
This steering wheel and column repair section covers
the Supplemental Restraint System (SRS) steering
column. The following repair procedures are specific to
SRS components. W hen servicing a vehicle equipped
with Supplemental Restraint System, pay close attention
to all W ARNINGS and CAUTIONS.
For detailed explanation about SRS, refer to Restraints
section.
WARNING: THIS VEHICLE HAS A SUPPLEMENTAL
RESTRAINT SYSTEM (SRS). REFER TO THE SRS
COMPONENT AND WIRING LOCATION VIEW IN
ORDER TO DETERMINE WHETHER YOU ARE
PERFORMING SERVICE ON OR NEAR THE SRS
COMPONENTS OR THE SRS WIRING. WHEN YOU
ARE PERFORMING SERVICE ON OR NEAR THE
SRS COMPONENTS OR THE SRS WIRING, REFER
TO THE SRS SERVICE INFORMATION. FAILURE TO
FOLLOW WARNINGS COULD RESULT IN POSSIBLE
AIR BAG DEPLOYMENT, PERSONAL INJURY, OR
OTHERWISE UNNECESSARY SRS SYSTEM
REPAIRS.
SAFE HANDLING OF INFLATOR MODULES
REQUIRES THE PROCEDURES DESCRIBED
BELOW TO BE FOLLOWED FOR BOTH LIVE AND
DEPLOYED MODULES.
SAFETY PRECAUTIONS MUST BE FOLLOWED
WHEN HANDLING A DEPLOYED AIR BAG
ASSEMBLY (AIR BAG). AFTER DEPLOYMENT, THE
AIR BAG ASSEMBLY (AIR BAG) SURFACE MAY
CONTAIN A SMALL AMOUNT OF SODIUM
HYDROXIDE, A BY-PRODUCT OF THE
DEPLOYMENT REACTION, THAT IS IRRITATING TO
THE SKIN AND EYES. MOST OF THE POWDER ON
THE AIR BAG ASSEMBLY (AIR BAG) IS HARMLESS.
AS A PRECAUTION, WEAR GLOVES AND SAFETY
GLASSES WHEN HANDLING A DEPLO
YED AIR BAG
ASSEMBLY, AND WASH YOUR HANDS WITH MILD
SOAP AND WATER AFTERWARDS.
WHEN CARRYING A LIVE AIR BAG ASSEMBLY,
MAKE SURE THE BAG AND TRIM COVER ARE
POINTED AWAY FROM YOU. NEVER CARRY AN AIR
BAG ASSEMBLY BY THE WIRES OR CONNECTOR
ON THE UNDERSIDE OF MODULE. IN THE CASE OF
AN ACCIDENTAL DEPLOYMENT, THE BAG WILL
THEN DEPLOY WITH MINIMAL CHANCE OF INJURY.
WHEN PLACING A LIVE AIR BAG ASSEMBLY ON
A
BENCH OR OTHER SURFACE, ALWAYS FACE THE
BAG AND TRIM COVER UP, AWAY FROM THE
SURFACE.
NEVER REST A STEERING COLUMN ASSEMBLY
ON THE STEERING WHEEL WITH THE AIR BAG
ASSEMBLY FACE DOWN AND COLUMN VERTICAL.
THIS IS NECESSARY SO THAT A FREE SPACE IS
PROVIDED TO ALLOW THE AIR BAG ASSEMBLY
TO EXPAND IN THE UNLIKELY EVENT OF
ACCIDENTAL DEPLOYMENT. OTHERWISE,
PERSONAL INJURY COULD RESULT.
TO AVOID DEPLOYMENT WHEN
TROUBLESHOOTING THE SRS SYSTEM, DO NOT
USE ELECTRICAL TEST EQUIPMENT, SUCH AS
A
BATTERY-POWERED OR A/C-POWERED VOLT-
METER, OHMMETER, ETC., OR ANY TYPE OF
ELECTRICAL EQUIPMENT OTHER THAN SPECIFIED
IN THIS MANUAL. DO NOT USE A NON-POWERED
PROBE-TYPE TESTER.
INSTRUCTIONS IN THIS MANUAL MUST BE
FOLLOWED CAREFULLY, OTHERWISE PERSONAL
INJURY MAY RESULT.
SRS Connectors
CAUTION: The special yellow color connectors are
used for the supplemental restraint system-air bag
circuit.
When removing the cable harness, do not pull the
cables. Otherwise, cable disconnection may occur.
When connecting the SRS connector, insert the
connector completely. Imperfect locking may cause
malfunction of the SRS circuit.
BACK TO CHAPTER INDEX
TO MODEL INDEX
ISUZU KB P190 2007
Page 289 of 6020
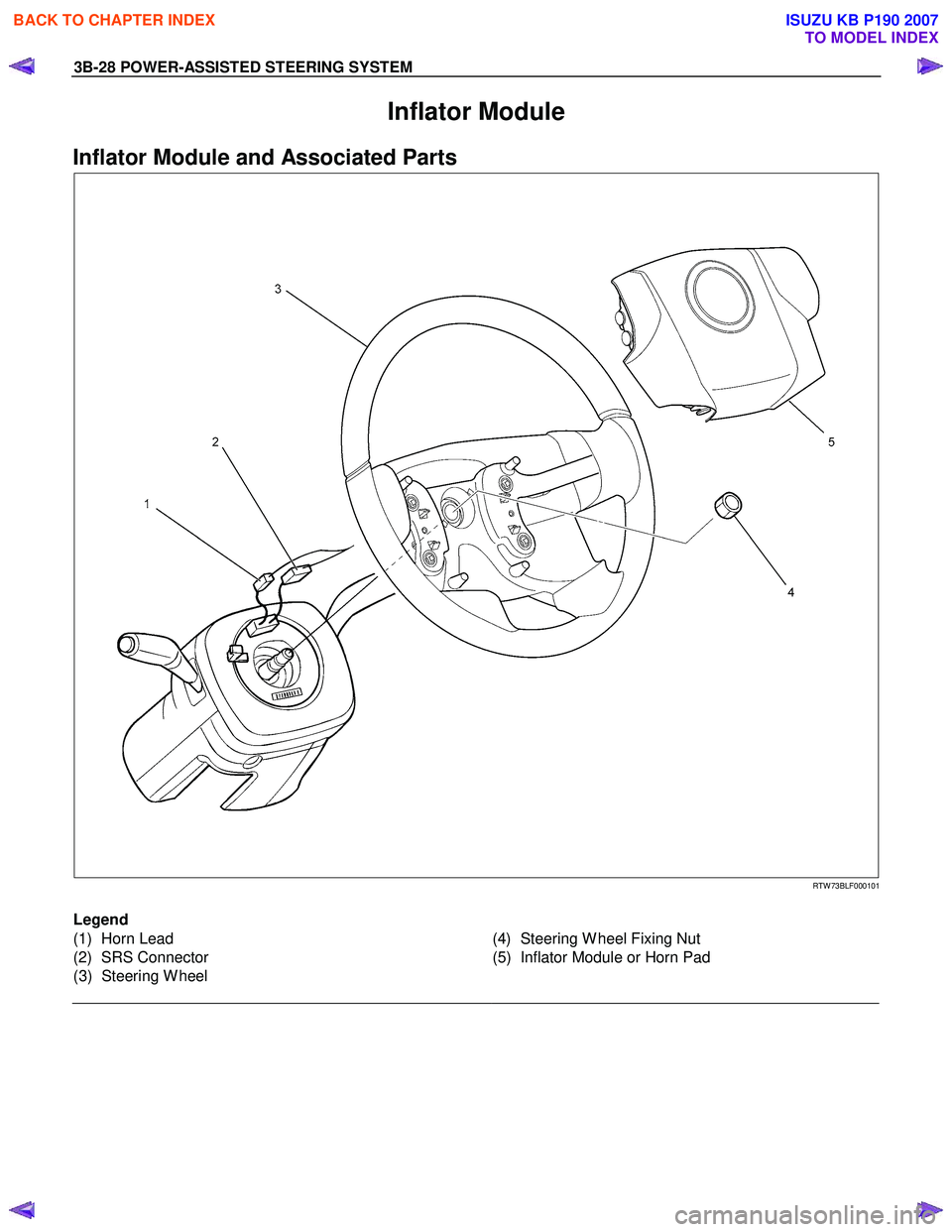
3B-28 POWER-ASSISTED STEERING SYSTEM
Inflator Module
Inflator Module and Associated Parts
RTW 73BLF000101
Legend
(1) Horn Lead
(2) SRS Connector
(3) Steering W heel
(4) Steering W heel Fixing Nut
(5) Inflator Module or Horn Pad
BACK TO CHAPTER INDEX
TO MODEL INDEX
ISUZU KB P190 2007
Page 290 of 6020
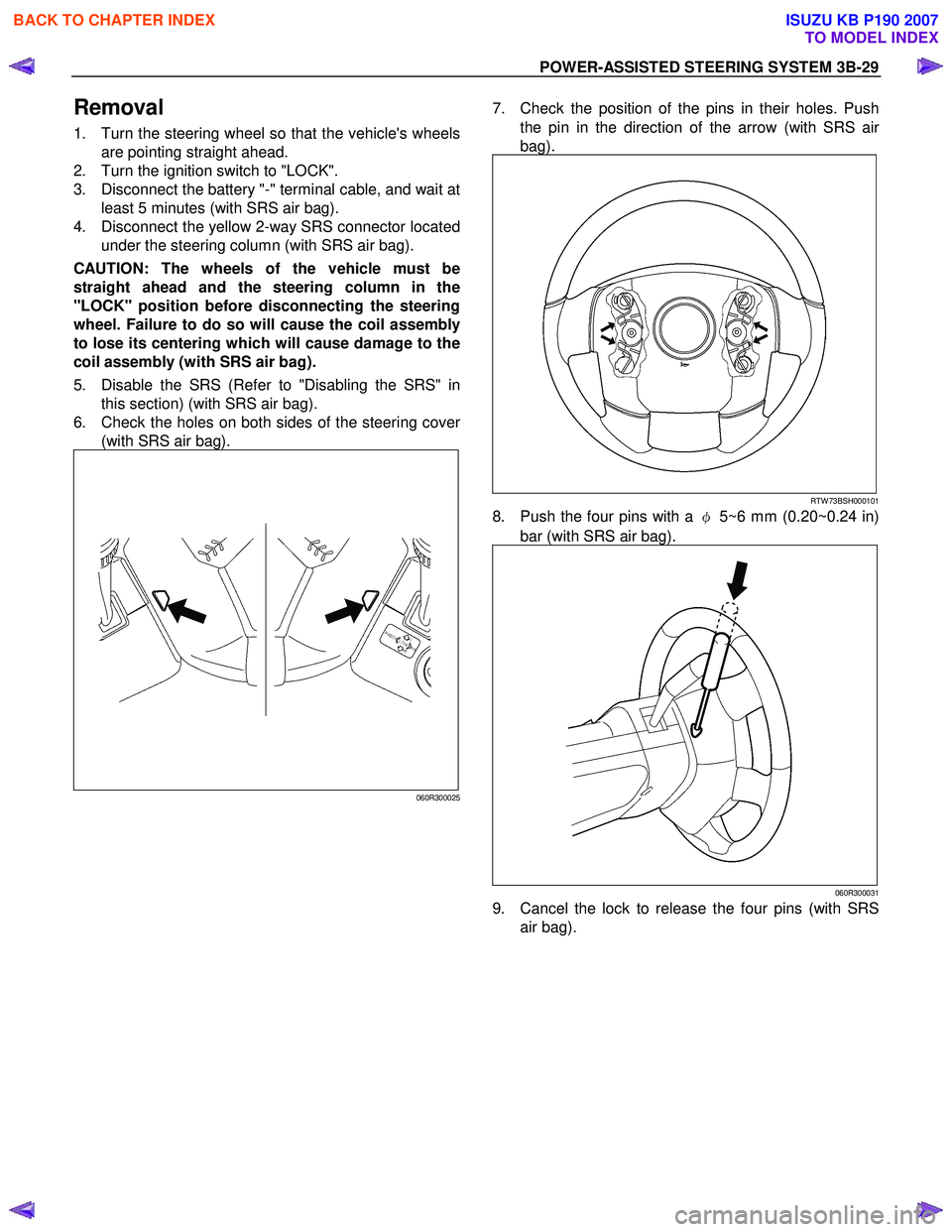
POWER-ASSISTED STEERING SYSTEM 3B-29
Removal
1. Turn the steering wheel so that the vehicle's wheels
are pointing straight ahead.
2. Turn the ignition switch to "LOCK".
3. Disconnect the battery "-" terminal cable, and wait at least 5 minutes (with SRS air bag).
4. Disconnect the yellow 2-way SRS connector located under the steering column (with SRS air bag).
CAUTION: The wheels of the vehicle must be
straight ahead and the steering column in the
"LOCK" position before disconnecting the steering
wheel. Failure to do so will cause the coil assembly
to lose its centering which will cause damage to the
coil assembly (with SRS air bag).
5. Disable the SRS (Refer to "Disabling the SRS" in this section) (with SRS air bag).
6. Check the holes on both sides of the steering cove
r
(with SRS air bag).
060R300025
7. Check the position of the pins in their holes. Push
the pin in the direction of the arrow (with SRS ai
r
bag).
RTW 73BSH000101
8. Push the four pins with a φ 5~6 mm (0.20~0.24 in)
bar (with SRS air bag).
060R300031
9. Cancel the lock to release the four pins (with SRS air bag).
BACK TO CHAPTER INDEX
TO MODEL INDEX
ISUZU KB P190 2007