MITSUBISHI DIAMANTE 1900 Repair Manual
Manufacturer: MITSUBISHI, Model Year: 1900, Model line: DIAMANTE, Model: MITSUBISHI DIAMANTE 1900Pages: 408, PDF Size: 71.03 MB
Page 151 of 408
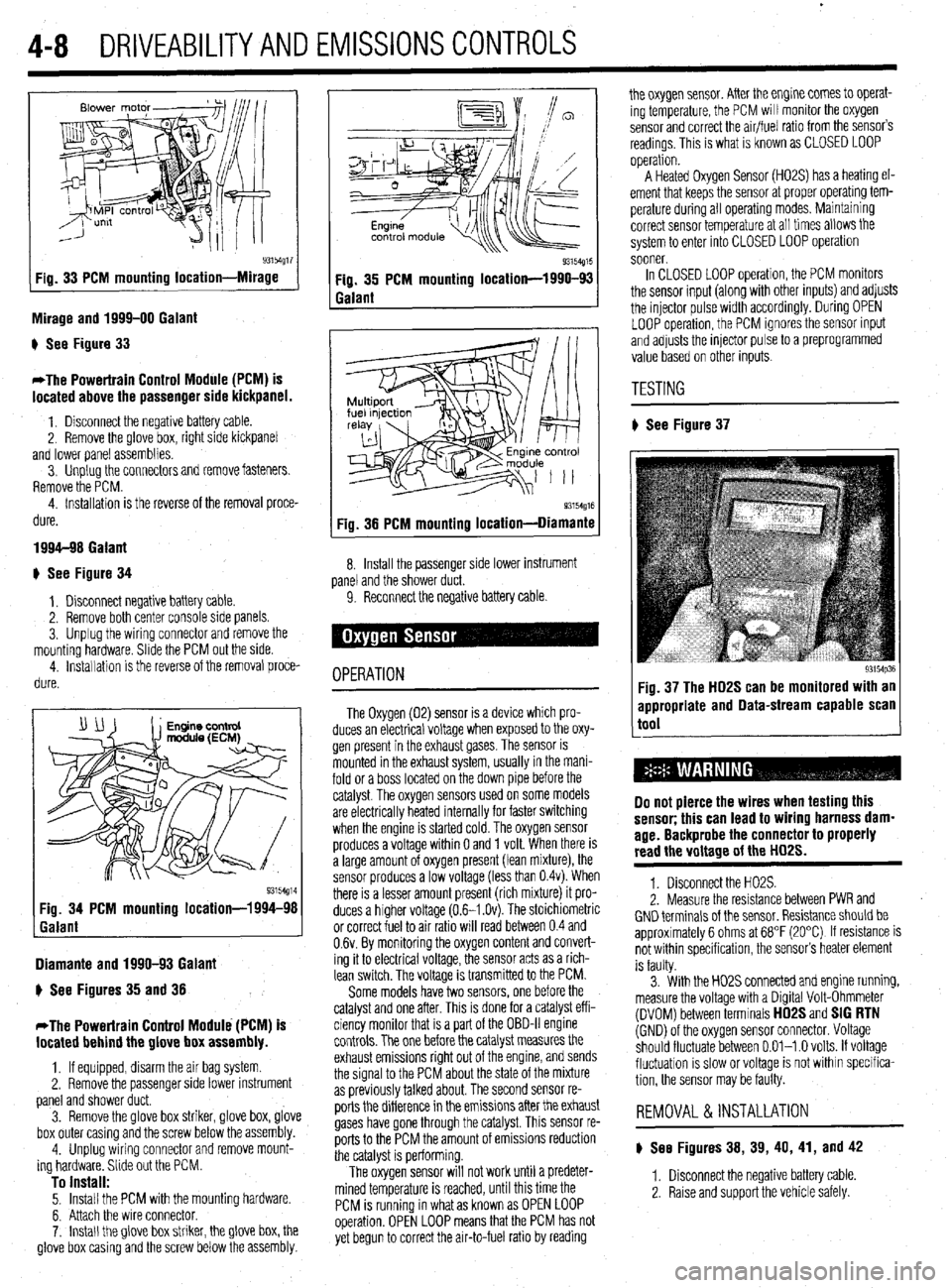
.
4-8 DRIVEABILITYAND EMISSIONS CONTROLS
93154g17 Fig. 33 PCM mounting location-Mirage
Mirage and 1999-00 Galant
) See Figure 33
*The Powertrain Control Module (PCM) is
located above the passenger side kickpanel.
1. Disconnect the negative battery cable.
2. Remove the @love box, right side kickpanel
and lower panel assemblies.
3. Unplug the connectors and remove fasteners.
Remove the PCM.
4. Installation is the reverse of the removal proce-
dure.
1994-98 Galant
+ See Figure 34
1, Disconnect negative battery cable.
2. Remove both center console side panels.
3. Unplug the wiring connector and remove the
mounting hardware. Slide the PCM out the side.
4. installation is the reverse of the removal proce-
dure.
Diamante and 1990-93 Galant
) See Figures 35 and 38
*The Powertrain Control Module (PCM) is
located behind the glove box assembly.
1, If equipped, disarm the air bag system
2. Remove the passenger side lower instrument
panel and shower duct.
3. Remove the glove box striker, glove box, glove
box outer casing and the screw below the assembly.
4. Unplug wiring connector and remove mount-
ing hardware. Slide out the PCM.
To install: 5. Install the PCM with the mounting hardware.
6. Attach the wire connector.
7. Install the glove box striker, the glove box, the
glove box casing and the screw below the assembly.
Q3154g15 Fig. 35 PCM mounting location-1990-93
Galant
93154g16 Fig. 38 PCM mounting location-Diamante
8. Install the passenger side lower instrument
panel and the shower duct.
9. Reconnect the negative battery cable
OPERATION
The Oxygen (02) sensor is a device which pro-
duces an electrical voltage when exposed to the oxy-
gen present in the exhaust gases. The sensor is
mounted in the exhaust system, usually in the mani-
fold or a boss located on the down pipe before the
catalyst. The oxygen sensors used on some models
are electrically heated internally for faster switching
when the engine is started cold. The oxygen sensor
produces a voltage within 0 and 1 volt. When there is
a large amount of oxygen present (lean mixture), the
sensor produces a low voltage (less than 0.4~). When
there is a lesser amount present (rich mixture) it pro-
duces a higher voltage (0.6-I .Ov). The stoichiometric
or correct fuel to air ratio will read between 0.4 and
0.6~. By monitoring the oxygen content and convert-
ing it to electrical voltage, the sensor acts as a rich-
lean switch. The voltage is transmitted to the PCM.
Some models have two sensors, one before the
catalyst and one after. This is done for a catalyst eff i-
ciency monitor that is a part of the OBD-II engine
controls. The one before the catalyst measures the
exhaust emissions right out of the engine, and sends
the signal to the PCM about the state of the mixture
as previously talked about. The second sensor re-
ports the difference in the emissions after the exhaust
gases have gone through the catalyst. This sensor re-
ports to the PCM the amount of emissions reduction
the catalyst is performing.
The oxygen sensor will not work until a predeter-
mined temperature is reached, until this time the
PCM is running in what as known as OPEN LOOP
operation. OPEN LOOP means that the PCM has not
yet begun to correct the air-to-fuel ratio by reading the oxygen sensor. After the engine comes to operat-
ing temperature, the PCM will monitor the oxygen
sensor and correct the air/fuel ratio from the sensor’s
readings. This is what is known as CLOSED LOOP
operation.
A Heated Oxygen Sensor (H02S) has a heating el-
ement that keeps the sensor at proper operatmg tem-
perature during all operating modes. Maintaining
correct sensor temperature at all times allows the
system to enter into CLOSED LOOP operation
sooner.
In CLOSED LOOP operation, the PCM monitors
the sensor input (along with other inputs) and adjusts
the injector pulse width accordingly. During OPEN
LOOP operation, the PCM ignores the sensor input
and adjusts the injector pulse to a preprogrammed
value based on other inputs.
TESTING
# See Figure 37
93154p36 Fig. 37 The HD2S can be monitored with an
appropriate and Data-stream capable scan
tool
Do not pierce the wires when testing this
sensor; this can lead to wiring harness dam-
age. Backprobe the connector to properly
read the voltage of the HD2S.
1. Disconnect the H02S.
2. Measure the resistance between PWR and
GND terminals of the sensor. Resistance should be
approximately 6 ohms at 68°F (20°C) If resistance is
not within specification, the sensor’s heater element
is faulty.
3. With the H02S connected and engine running,
measure the voltage with a Digital Volt-Ohmmeter
(DVOM) between terminals
HD2S and SIG RTN (GND) of the oxygen sensor connector. Voltage
should fluctuate between 0.01-l .O volts. If voltage
fluctuation is slow or voltage is not within specifica-
tion, the sensor may be faulty.
REMOVAL &INSTALLATION
) See Figures 38, 39, 40, 41, and 42
1. Disconnect the negative battery cable
2. Raise and support the vehicle safely.
Page 152 of 408
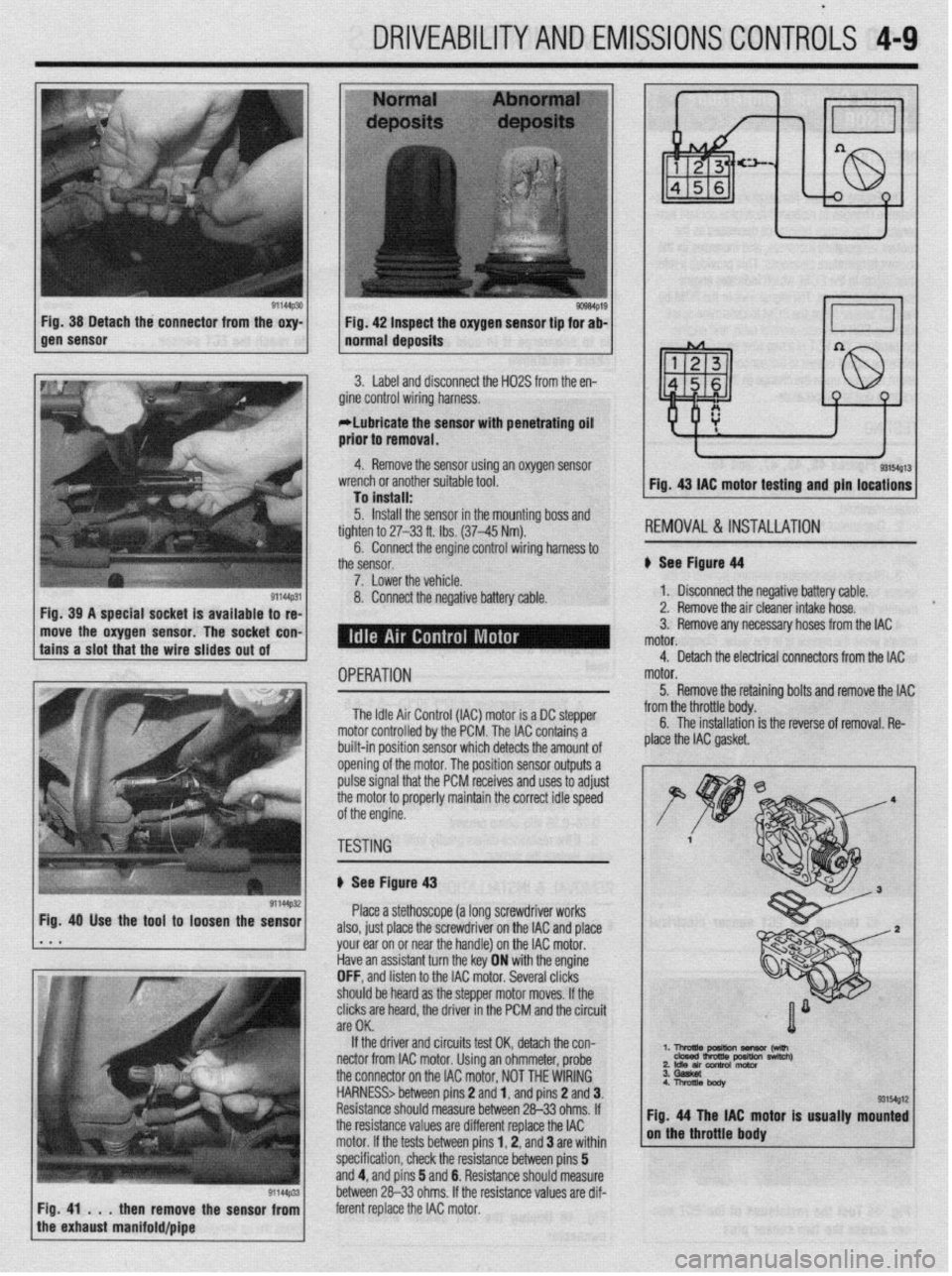
DRIVEABILITYAND EMISSIOP JSCONTRiLS 4-9
3. Label and disconnect the H02S from the en-
gine control wiring harness.
*Lubricate the sensor with penetrating oil
prior to removal.
4. Remove the sensor using an oxygen sensor
I To install: - -v- -- ---- ..----. ----...= -..- r... *-
5. Install the sensor in the mounting boss and
hl-li)r\,,.l 0 ,.l.-.f.l, .T‘fi.LI wrench or another suitable tool.
tighten to 27-33 ft. Ibs. (37-45 Nm).
6. Connect the engine control wiring harness to 1 Fia. 43 IAC mntnr tnfitinn and nin Incations 1
KtMUVHL i% IN3 I ALLA I IUN
See Fiaurr! d4
1. Disconnect the negative battery cable.
2. Remove the air cleaner intake hose.
move the oxygen sensor. The socket con- 3. Remove any necessary hoses from the IAC
OPERATION
The Idle Air Control (IAC) motor is a DC stepper
motor controlled by the PCM. The IAC contains a
built-in position sensor which detects the amount of
opening of the motor. The position sensor outputs a
pulse signal that the PCM receives and uses to adjust
the motor to properly maintain the correct idle speed
of the engine. motor.
5. Remove the retainino bolts and remove the IAC
y -_.._ -..- ._... -._ . .._ ._ from the throttle body. C The inc.hllrrti~n a 11o IIIJL(IIIoLIuII is the reverse of removal. Re-
plaie the IAC gasket.
TESTING
I
ti See Figure 43
Place a stethoscope (a long screwdriver works
also, just place the screwdriver on the IAC and place
your ear on or near the handle) on the IAC motor.
Have an assistant turn the key ON with the engine
OFF, and listen to the IAC motor. Several clicks
should be heard as the steooer motor moves. If the
clicks are heard, the driver in the PCM and the circuit
are OK.
If the driver and circuits test OK, detach the con-
nectar from IAC motor. Using an ohmmeter, probe ‘. l-!AEz?rn~ -w
2 Idle an conh0l motor nswltch)
the connector on the IAC motor, NOT THE WIRING
HARNESS> between pins 2 and 1, and pins 2 and 3.
Resistance should measure between 26-33 ohms. If
the resistance values are different replace the IAC tor is usually mounted
motor. If the tests between pins 1,2, and 3 are within
specification, check the resistance between pins 5
and 4, and pins 5 and 6. Resistance should measure
between 26-33 ohms. If the resistance values are dif-
then remove the sensor from ferent replace the IAC motor.
Page 153 of 408
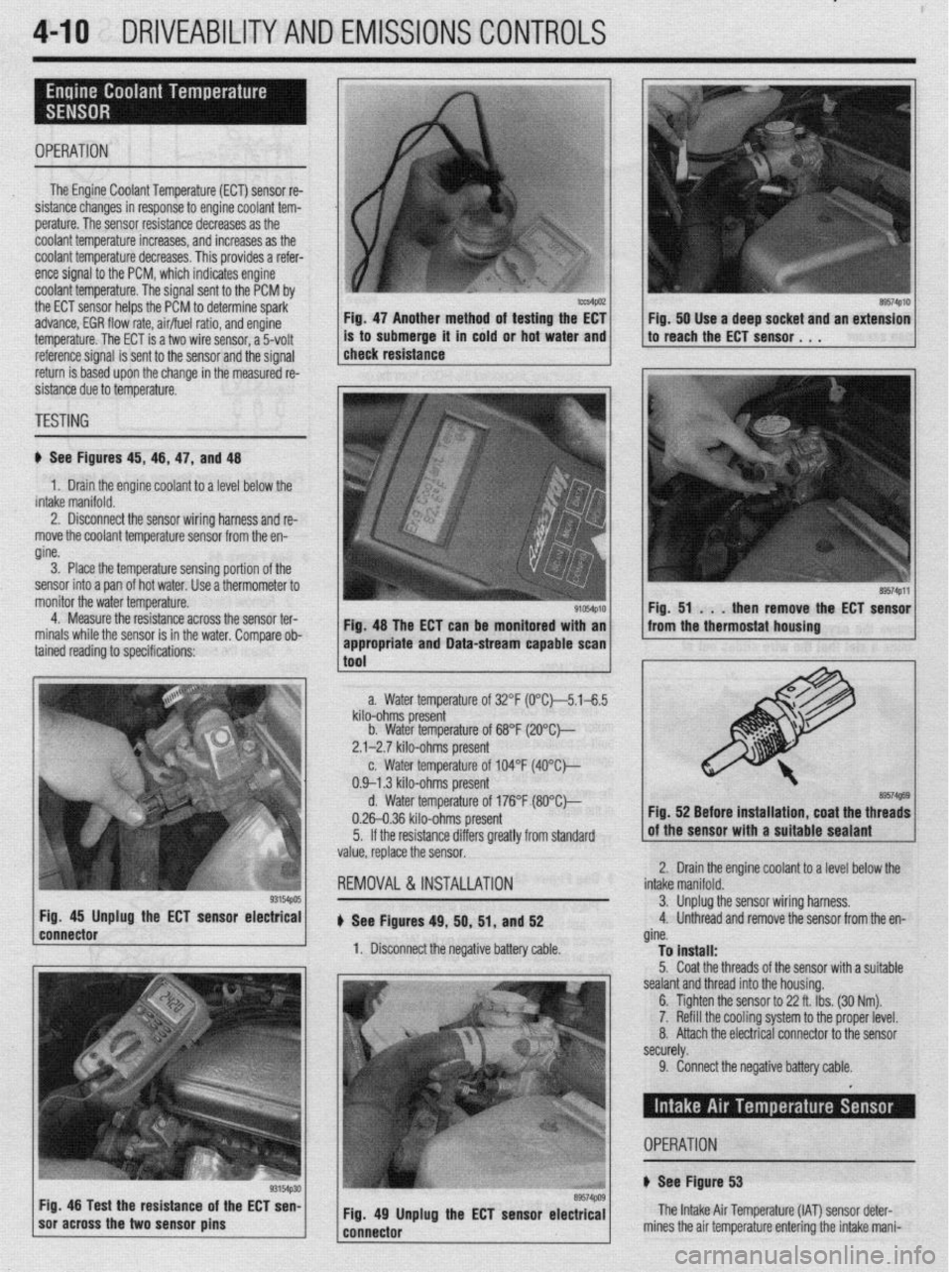
4-10 DRIVEABILITYAND EMISSIONS CONTROLS
I
OPERATION
The Engine Coolant Temperature (ECT) sensor re-
sistance changes in response to engine coolant tem-
perature. The sensor resistance decreases as the
coolant temperature increases, and increases as the
coolant temperature decreases. This provides a refer-
ence signal to the PCM, which indicates engine
coolant temperature. The signal sent to the PCM by
the ECT sensor helps the PCM to determine spark-
advance, EGR flow rate, air/fuel ratio, and engine
temperature. The ECT is a two wire sensor, a 5volt
3. Place the temperature sensing portion of the
sensor into a pan of hot water. Use a thermometer to
monitor the water temperature.
4. Measure the resistance across the sensor ter-
minals while the sensor is in the water. Comoare ob- Fig. 47 Another method of testing the EC1 Fig. 50 Use a deep socket and an extension
is to submerge it in cold or hot water and to reach the ECT sensor. 1 ,
reference signal is sent to the sensor and the signal
return is based upon the change in the measured re-
sistance due to temperature. 1 check resistance
TESTING
ti See Figures 45, 46, 47, and 48
1. Drain the engine coolant to a level below the
intake manifold.
2. Disconnect the sensor wiring harness and re-
move the coolant temperature sensor from the en-
gine.
Fig. 48 The ECT can be monitored with an
tained reading to specifications: ’
93154pos Fig. 45 Unplug the ECT sensor electrical
connector
1 soracross the two sensor pins g3154p30 Fig 48 Test the resistance of the ECT sen-
89574PlO
89574Pll
Fig. 51 . . .
then remove the ECT sensor
from the thermostat housing
a. Water temperature of 32°F (0°C~5.1-6.5
kilo-ohms present
b. Water temperature of 68°F (2O”C)--
2.1-2.7 kilo-ohms present
c. Water temperature of 104°F (4O”C)---
0.9-l .3 kilo-ohms present
d. Water temperature of 176°F (8O”Ck,
0.26-0.36 kilo-ohms present
5. If the resistance differs greatly from standard
value, replace the sensor.
REMOVAL &INSTALLATION
u See Figures 49, 50, 51, and 52
1. Disconnect the negative battery cable. Fig. 52 Before installation, coat the threads
Iolant to a level below the 2. Drain the engine c(
intake manifold.
3. Unplug1 the sensor wiring harness,
4. Unthreac
d and remove the sensor from the en-
gine.
To install:
5. Coat the threads of the sensor with a suitable
sealant and thread into the housing.
6. Tighten the sensor to 22 ft. Ibs. (30 Nm).
7. Refill the cooling system to the proper level.
8. Attach the electrical connector to the sensor
securely. appropriate and Data-stream capable scan 1
1
tnnl
9. Connect the negative battery cable.
Fig. 49 Unplug the ECT sensor electrical
---..^-s-- The Intake Air Temperature (IAT) sensor det
mines the air temnerature enterinn the! intake n er-
- ._ r_ -.-._ _. ._. J . _ ..-. ._
iani- OPERATION
+ See Figure 53
Page 154 of 408
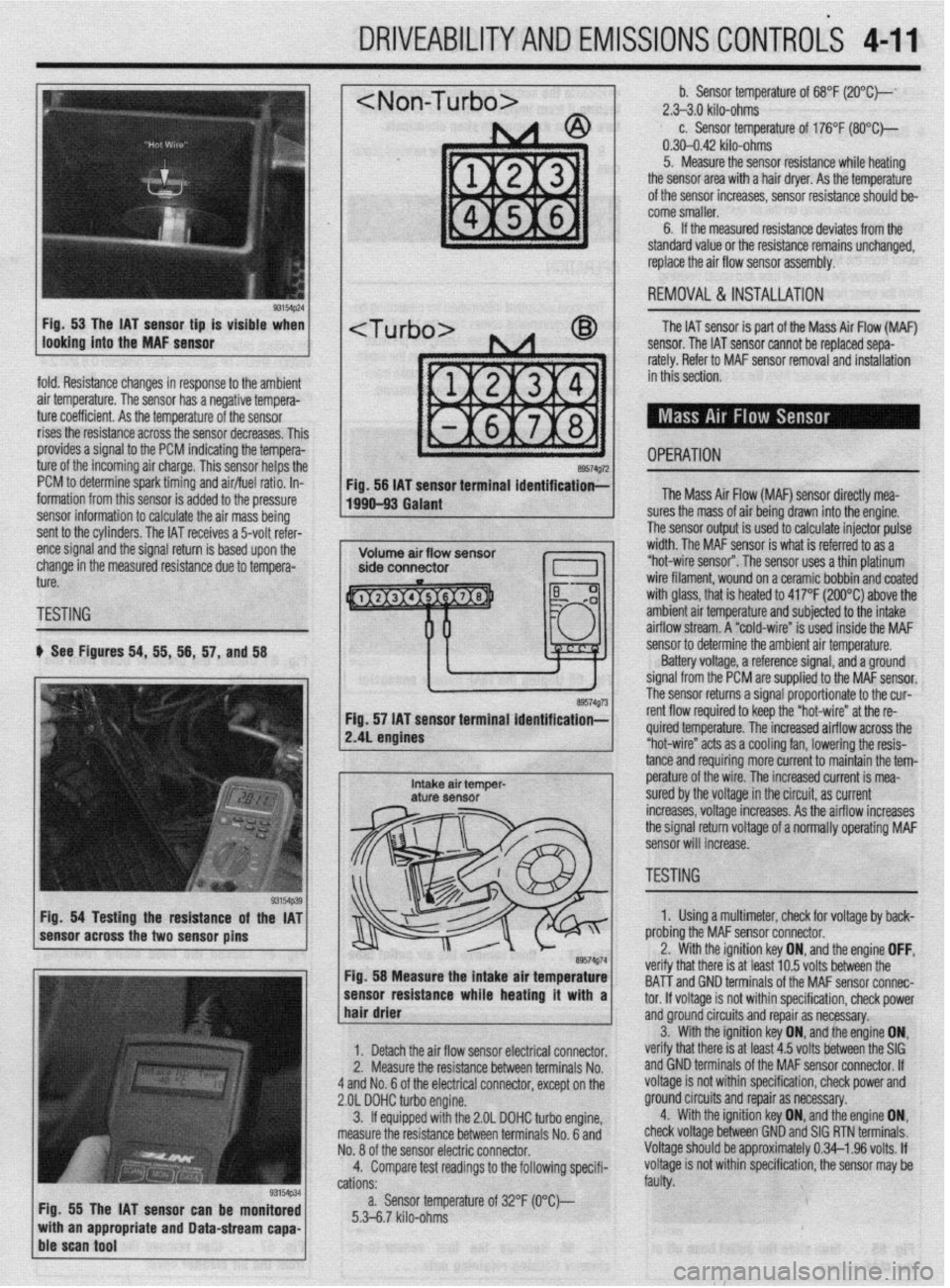
DRIVEABILITYAND EMISSIONS CONTROLi 4-11
fold. Resistance changes in response to the ambient
air temperature. The sensor has a negative tempera-
ture coefficient. As the temperature of the sensor
rises the resistance across the sensor decreases. Thil
provides a signal to the PCM indicating the tempera-
ture of the incoming air charge. This sensor helps the
PCM to determine spark timing and air/fuel ratio. In-
formation from this sensor is added to the pressure
sensor information to calculate the air mass being
sent to the cylinders. The IAT receives a 5-volt refer-
ence signal and the signal return is based upon the
change in the measured resistance due to tempera-
ture.
TESTING
b See Figures 54, 55, 56, 57, and 58
Fig. 54 Testing the resistance of the IAT
sensor across the two sensor pins
Fig. 55 The IAT sensor can be monitored
with an appropriate and Data-stream capa-
ble scan tool
~1 b. Sensor temperature of 68°F (2O”C)--‘ 2.>3.0 kilo-ohms c. Sensor temperature of 176°F (SO*C)-
0.30-0.42 kilo-ohms
5. Measure the sensor resistance while heating
the sensor area with a hair dryer. As the temperature
of the sensor increases, sensor resistance should be-
come smaller.
6. If the measured resistance deviates from the
standard value or the resistance remains unchanged,
replace the air flow sensor assembly.
1 REMOVAL&INSTALLATION
The IAT sensor is part of the Mass Air Flow (MAF)
sensor. The IAT sensor cannot be replaced sepa-
rately. Refer to MAF sensor removal and installation
in this section.
- OPERATION a9574g72 Fig. 56 IAT sensor terminal identification;-
1990-93 Galant The Mass Air Flow (MAF) sensor directly mea-
lres the mass of air being drawn into the engine.
I ?he sensor output is used to calculate injector pulse
width. The MAF sensor is what is referred to as a
“hot-wire sensor”. The sensor uses a thin platinum
wire filament, wound on a ceramic bobbin and coated
with glass, that is heated to 417°F (200°C) above the
amh+en+ nir +PmnPrfijre and subiected to the intake
..I._ ~ ..-.. .“..‘r-,u.. ai mow stream. A “cold-wire” is used inside the MAF
sensor resuirance wnoe nearmg ir wnn a 1
hair drier ‘hat melt: IS al I~“< ,“.., lvllQ UtiLnbtill ,,,=
tnd GND terminals of the MAF sensor connec-
tor. If voltaae is not within specification, check power
1. Detach the air flow sensor electrical connector.
2. Measure the resistance between terminals No.
4 and No. 6 of the electrical connector, except on the
2.OL DOHC turbo engine.
3. ff equipped with the 2.OL DOHC turbo engine,
measure the resistance between terminals No. 6 and
No. 8 of the sensor electric connector.
4. Compare test readings to the following specifi-
cations:
a. Sensor temperature of 32°F (O“C)--
5.3-6.7 kilo-ohms and groundcircuits and repair as necessary.
verify that there is at least 4.5 volts between the SIG 3. With the ignition key ON, and,the engine ON,
and GND terminals of the MAF sensor connector. If
voltage is not within specification, check power and
ground circuits and repair as necessary.
4. With the ignition key ON, and the engine ON,
check voltage between GND and SIG RTN terminals.
Voltage should be approximately 0.34-l .96 volts. If
voltage is not within specification, the sensor may be
faulty.
/ sensor to determine the ambient air temperature.
Battery voltage, a reference signal, and a ground
signal from the PCM are supplied to the MAF sensor.
rho ~pn**r rp+++rns a signal proportionate to the cur-
re. The increased airflow across the
s a cooling fan, lowering the resis-
mo more current to maintain the tem- tance and requir
e^-‘.._^ ^I LL^
I
Intake air temper- pe~a+ure UI me wire. The increased current is mea- aturf sensor sured by the voltage in the circuit, as current
increases, voltage increases. As the airflow increases
the signal return voltage of a normally operating MAF
sensor will increase.
, ~~1 TESTING - II ire” at the re-
89574g74 Fig. 58 Measure the intake air temperature
-----_ ---1-a---- L..- L--1. . . .*a 1. Using a multimeter, check for voltage by back-
nrr\hinn +hn MAF sensor connector.
the ignition key ON, and the engine OFF, .^-^ :- -’ ‘.txt In E; \mltr hahrman tha veriry t
BAT-T i
Page 155 of 408
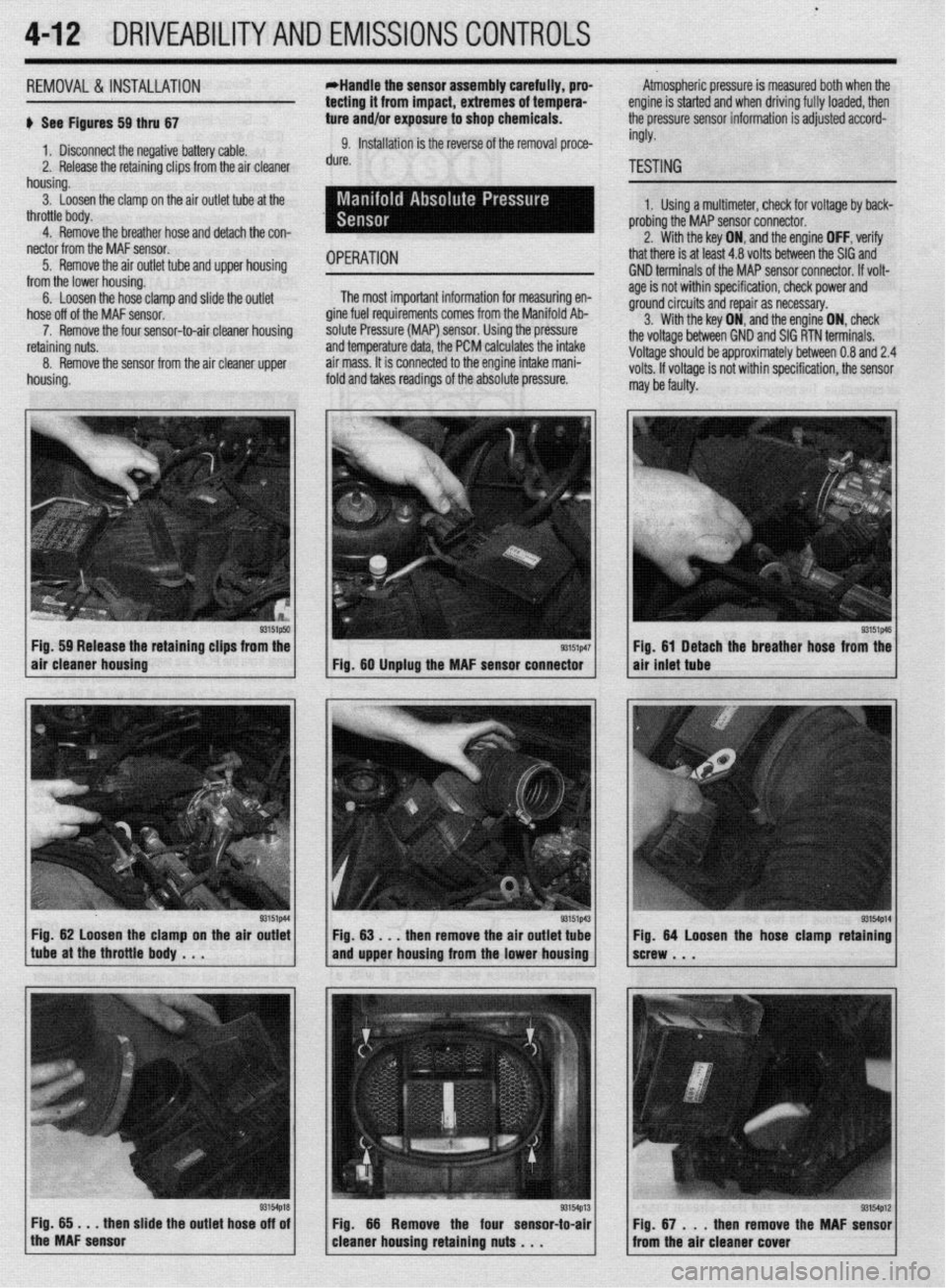
4112 DRIVEABILITYAND EMISSIONS CONTROLS
.
REMOVAL&INSTALLATION
+ See Figures 59 thru 67
1, Disconnect the negative battery cable.
2. Release the retaining clips from the air cleaner
housing.
3. Loosen the clamp on the air outlet tube at the
throttle body.
4. Remove the breather hose and detach the con-
nector from the MAF sensor.
5. Remove the air outlet tube and upper housing
from the lower housing.
6. Loosen the hose clamp and slide the outlet
hose off of the MAF sensor.
7. Remove the four sensor-to-air cleaner housing
retaining nuts.
8. Remove the sensor from the air cleaner upper
housing. Atmospheric pressure is measured both when the
engine is started and when driving fully loaded, then
the oressure sensor information is adiusted accord- *Handle the sensor assembly carefully, pro-
tecting it from impact, extremes of tempera-
ture and/or exposure to shop chemicals.
9. Installation is the reverse of the removal proce-
dure.
OPERATION
The most important information for measuring en-
gine fuel requirements comes from the Manifold Ab-
solute Pressure (MAP) sensor. Using the pressure
and temperature data, the PCM calculates the intake
air mass. It is connected to the engine intake mani-
fold and takes readings of the absolute pressure. ingly.
TESTING
1. Using a multimeter, check for voltage by back-
probing the MAP sensor connector.
2. With the key ON, and the engine OFF, verify
that there is at least 4.8 volts between the SIG and
GND terminals of the MAP sensor connector. If volt-
age is not within specification, check power and
ground circuits and repair as necessary.
3. With the key ON, and the engine ON, check
the voltage between GND and SIG RTN terminals.
Voltage should be approximately between 0.8 and 2.4
volts. If voltage is not within specification, the sensor
r nay be faulty.
Fig. 59 Release the retaining clips from the
air cleaner housing
Fig. 62 loosen the clamp on the air outlet
tube at the throttle body . . .
then slide the outlet hose off of Fig. 61 Detach the breather hose from the
air inlet tube
53154p12 Fig. 67 . . . then remove the MAF sensor
from the air cleaner cover
Page 156 of 408
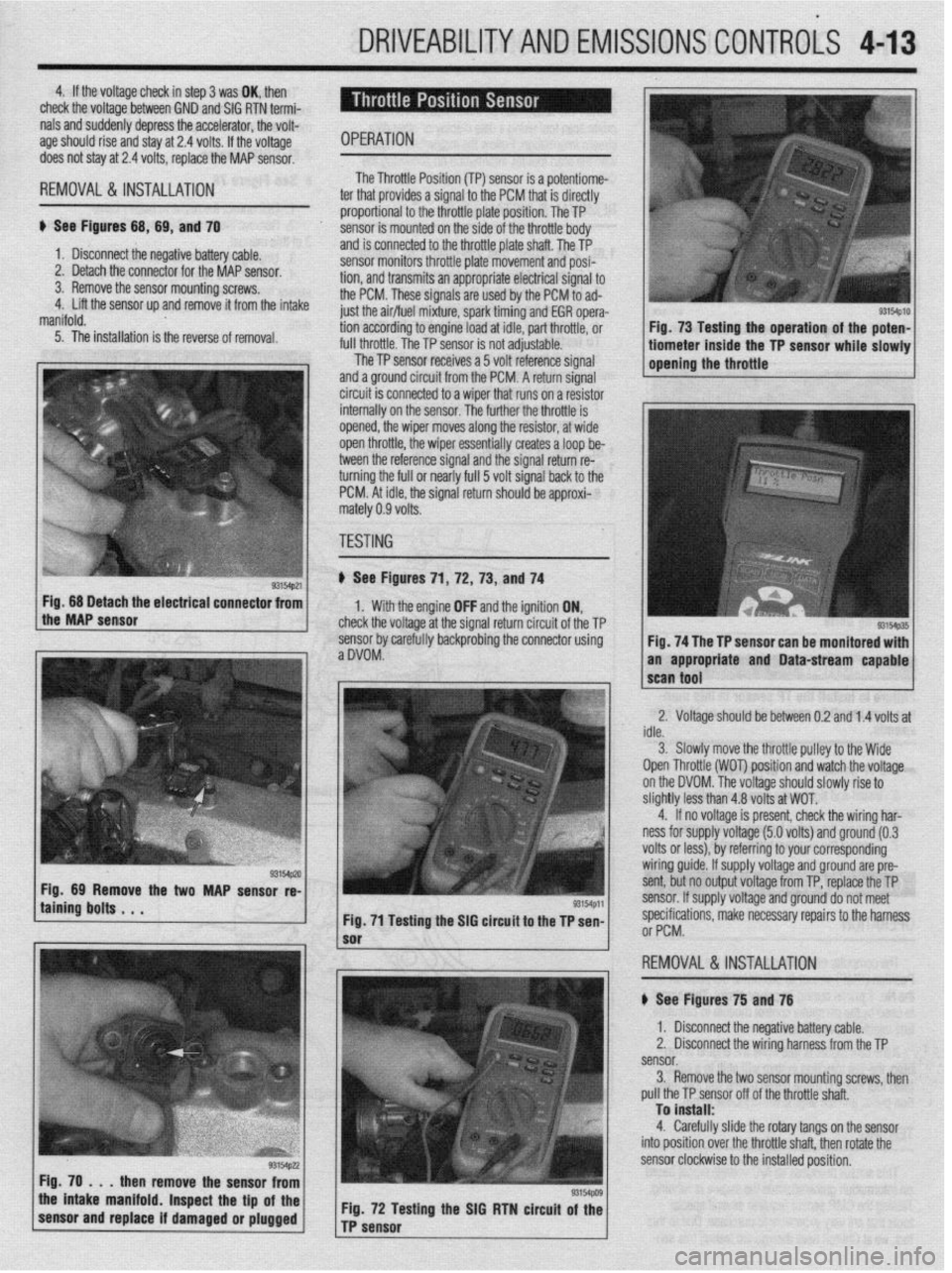
DRIVEABILITYAND EMISSIONS CONTROiS 4-13
4. If the voltaoe check in sbo 3 was OK. then
check the voltage-between GND’and SIG RTN termi-
nals and suddenly depress the accelerator, the volt-
age should rise and stay at 2.4 volts. If the voltage
OPERATION does not stay at 2.4 volts, replace the MAP sensor.
REMOVAL&INSTALLATION '
ti See Figures 68, 69, and 70
1. Disconnect the negative bat lery cable.
2. Detach the connector for thl e MAP sensor.
3. Remove the sensor mountir ig screws.
4. Lift the sensor up and remove it from the intake
manifold. The Throttle Posii
ti-* \*. Inn ITPl smsnr is 8 Dotentiome- , WI...,". *., . ter that provides a si gnal to the PCM that is directly
proportion: il to the throttle plate position. The TP
sensor is rr iounted on the side of the throttle body
and is connected to the throttle plate shaft. The TP
sensor monitors throttle plate movement and posi-
tion, and transmits an appropriate electrical signal to
the PCM. These signals grp IIQX-I hv rho PCM to ad-
just the air/flnI mivtlI “-- ------li
5. The installation is the reverse of removal. WI I dLfUl U full throttle The TP c
UyI ,,,,,,,:re, spark timing and EGR opera-
ng to engine load at idle, part throttle, or
The TP sensor is not adjustable.
..-
lensor receives a 5 volt reference signal
and a ground circuit from the PCM. A return signal
circuit is connected to a wiper that runs on a resistor
internally on the sensnr ThP fmth@r rho throttle is
opined the winnr mr oP -*lY”, .I,” ..,y’V, 111 Jves along the resistor, at wide
en throttle, the wiper essentially creates a loop be-
tween the reference signal and the signal return re-
turning the full or nearly full 5 volt signal back to the
PCM. At idle, the signal return should be approxi-
rnz
rtely 0.9 volts.
TF
iSTING
) See Figures 71 ,72, 73, and 74
1. With the engine OFF and the ignition ON,
check the voltage at the signal return circuit of the TP
sensor bv carefullv backorobina the connector using
aDVOM: . ” Fig. 68 Detach the electrical connector from
the MAP sensor
taining bolts . . . WMp,l
Fig. 71 Testing the SIG circuit to the TP sen-
then remove the sensor from
the intake manifold. Inspect the tip of the
sensor and replace if damaged or plugged Fig. 72 Testing the SIG RTN circuit of the
TP sensor
sm4p10 I Fig. 73 Testing the operation of the poten- 1
tiometer inside the TP sensor while slowly 1
opening the throttle
Fig. 74 The TP sensor can be monitored with
an appropriate and Data-stream capable
2. Voltage should be between 0.2 and 1.4 volts at
idle.
3. Slowlv move the throttle oullev to the Wide
Open Throttle (WOT) position and watch the voltage
on the DVOM. The voltage should slowly rise to
slightly less than 4.8 volts at WOT.
4. If no voltage is present, check the wiring har-
ness for supply voltage (5.0 volts) and ground (0.3
volts or less), by referring to your corresponding
wiring guide. If supply voltage and ground are pre-
sent, but no output voltage from TP, replace the TP
sensor. If supply voltage and ground do not meet
specifications, make necessarv reoairs to the harness
or PCM.
,
REMOVAL&INSTALLATION
# See Figures 75 and 76
1. Disconnect the negative battery cable.
2. Disconnect the wiring harness from the TP
sensor.
3. Remove the two sensor mounting screws, then
pull the TP sensor off of the throttle shaft.
To install:
4. Carefully slide the rotary tangs on the sensor
into position over the throttle shaft. then rotate the
sensor clockwise to the installed position.
Page 157 of 408

.
4-14 DRIVEABILITYAND EMISSIONS CONTROLS
93154pm Fig. 75 Unplug the TP sensor connector
Fig. 76 The TP sensor is secured with two
retaining bolts sor to be beyond the scope of the do-it-yourself me- The camshaft position sensor on these engines is
chanic. The sensor can be monitored with an appro2 located in the distributor. Refer to the distributor re-
oriate scan tool usina a data disolav or other data moval and installation procedure in Section 2.
stream information. hollow the instructions included
with the scan tool for information on accessing the
data.
REMOVAL &INSTALLATION 3.01 DDHC Engine
p See Figure 78
1. Disconnect the negative battery cable.
2. Remove the timing belt, as outlined in Section
1,6L, 2.01 DDHC and 1997-00 I .8L Engines
1 I Disconnect the negative battery cable.
2. Detach the electrical throttle body stay.
3. Remove the sensor retaining screws.
4. Remove the sensor assembly from the engine.
To install:
5. Install the sensor in the opening in the engine
and tighten the sensor retaining screws.
6. Install the throttle body stay.
7. Attach the electrical connector to the sensor.
8. Connect the negative battery cable.
1.5L, 2.41, 3.OL SDHC, 3.5L, and 1993-96
1.8L Engines
ti See Figure 77 3 of this manual.
3. Unplug the sensor connector.
4. Unfasten the retaining bolts, then remove the
sensor from the vehicle.
5. Installation is the reverse of the removal proce-
dure.
OPERATION
The Crankshaft Position (CKP) sensor (also re-
ferred to as the crank angle sensor) senses the crank
angle (piston position) of each cylinder and converts
Failure to install the TP sensor in this man-
ner may result in sensor damage or high idle
speeds.
,
*The TP sensor is not adjustable. camshaft position sensor)
=1541po9 5. Install and tighten the sensor mounting
“n,zw.m JU cw3, 6. Connect the wiring harness to the sensor.
7. Connect the negative battery cable. Fig. 77 The CMP sensor Is built into the distributor-l .8L engine shown
Camshaft position
sensor
OPERATION
I
The computer control module uses the Camshaft
.
Position (CMP) sensor to determine the position of
the No. 1 piston during its power stroke. This signal
is used by the computer control module to calculate
fuel injection mode of operation.
If the cam signal is lost while the engine is run-
ning, the fuel injection system will shiffto a calcu-
lated fuel injected mode based on the last fuel injec-
93154gll
tion pulse, and the engine will continue to run. Fig. 78 CMP sensor mounting-3.01 DDHC engine
TESTbiG
This sensor produces an A/C voltage signal based
on information gathered while the engine is running.
Testing the CMP sensor requires several special
tools that are very expensive to purchase. Due to this
fact, we at Chilton have determined testing this sen-
Page 158 of 408

DRIVEABILITYAND EMlSSlONSCONTROiS 4-15
it into a pulse signal. The PCM receiv
es this signal
and then computes the engine speed ad controls the
fuel injector timing and ignition timing based on this
input.
TESTING
This sensor produces a pulse signal based on in-
formation gathered while the engine is running. Test-
ing the CKP sensor requires several special tools that
are very expensive to purchase. Due to this fact, we at
Chilton have determined testing this sensor to be be-
yond the scope of the do-it-yourself mechanic. The
sensor can be monitored with an appropriate scan
tool using a data display or other data stream infor-
mation Follow the instructions included with the
scan tool for information on accessing the data.
REMOVAL<jSTALLATlON
2.OL SDHC and 1990-96 1.5L Engines are built
89574ga3 into the
9 See Figure 79
The CKP sensor on these engines is located in the
distributor. Refer to the distributor removal and in-
stallation procedure in Section 2.
1.6L and 2.OL DDHC Engines
b See Figure 80
1. Disconnect the negative battery cable.
2. Detach the electrical throttle body stay.
3. Remove the sensor retaining screws,
4. Remove the sensor assembly from the engine.
To install:
5. Install the sensor in the openina in the enaine
and tighten the sensor retaining’screvk -
6. Install the throttle body stay,
7. Attach the electrical connector to the sensor.
8. Connect the negative battery cable.
1.8L, 2.4L, 3.OL (SOHC and DOHC), 3.5L,
and 1997-00 1.5L Engines
b See Figures 81 and 82
1. Disconnect the negative battery cable.
2. Remove the timing belt, as outlined in Section
3 of this manual.
3. Unplug the sensor connector.
4. Unfasten the retaining bolts, then remove the
sensor from the vehicle.
5. Installation is the reverse of the removal proce-
dure. ’ Fig. 81 Remove the two CKP sensor retain-
Fig. 82 Remove the sensor and slide the re-
1 / gfne shown, others similar ’ -1 ing bolts-2 4L engine shown others sim-
ilar . ’ luctor wheel off of the crankshaft-2 4L en
Page 159 of 408
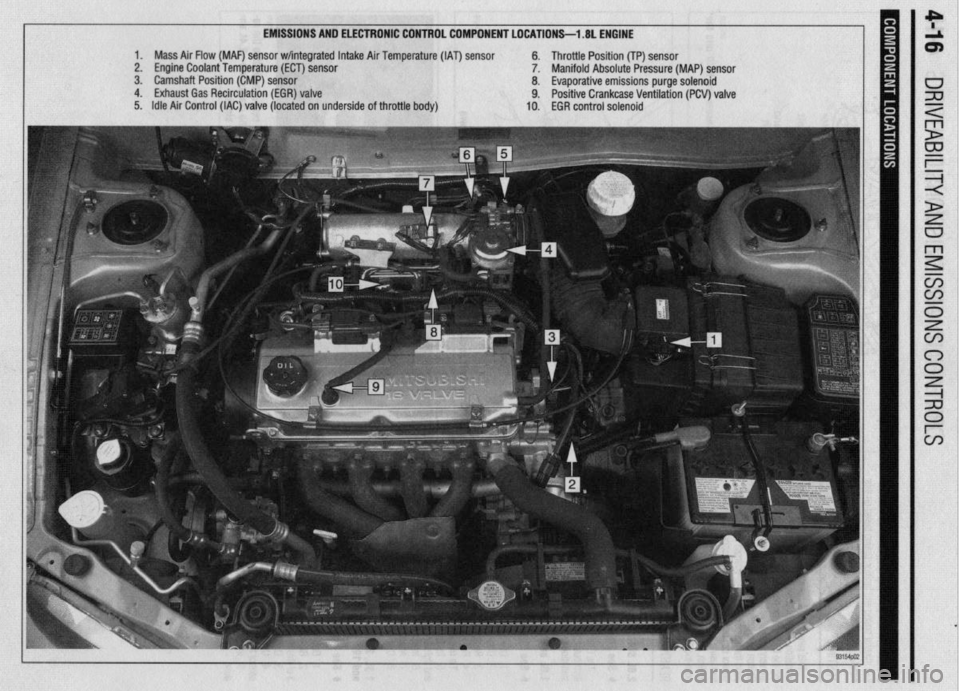
EMISSIONS AND ELECTRONIC CONTROL COMPONENT LOCATIONS-l .8L ENGINE
1. Mass Air Flow (MAF) sensor w/integrated Intake Air Temperature (IAT) sensor 6. Throttle Position (TP) sensor
2. Engine Coolant Temperature (ECT) sensor 7. Manifold Absolute Pressure (MAP) sensor
3. Camshaft Position (CMP) sensor 8. Evaporative emissions purge solenoid
4. Exhaust Gas Recirculation (EGR) valve 9. Positive Crankcase Ventilation (PCV) valve
5. Idle Air Control (IAC) valve (located on underside of throttle body) 10. EGR control solenoid
Page 160 of 408
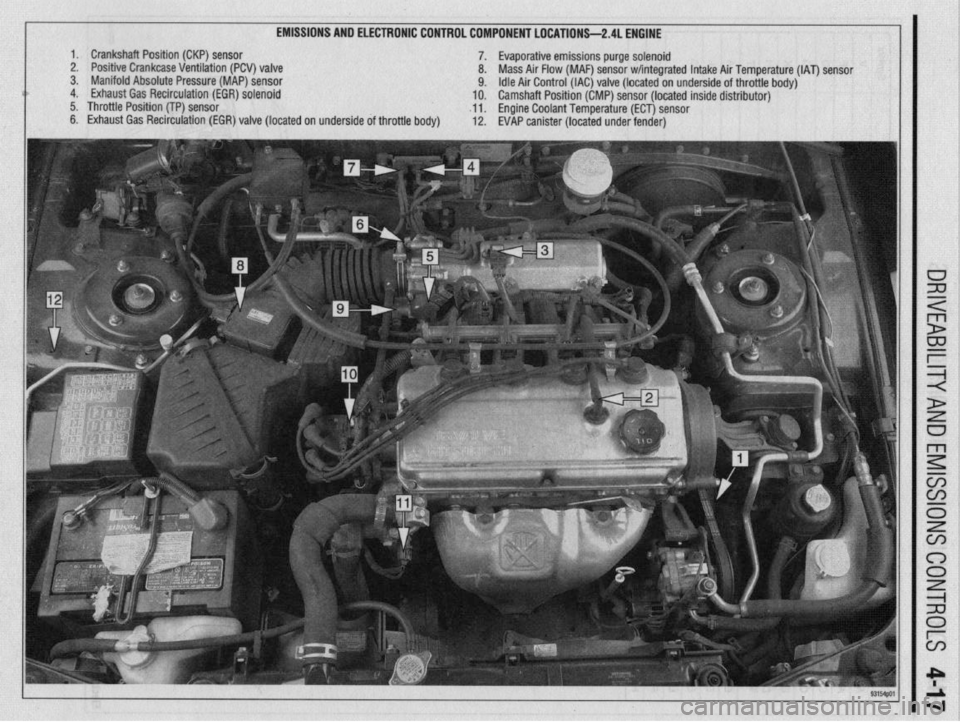
EMISSIONS AND ELECTRONIC CONTROL COMPONENT LOCATIONS-2.4L ENGINE
1. Crankshaft Position (CKP) sensor
7. Evaporative emissions purge solenoid
2. Positive Crankcase Ventilation (PCV) valve
8. Mass Air Flow (MAF) sensor w/integrated Intake Air Temperature (IAT) sensor
3. Manifold Absolute Pressure (MAP) sensor
9. Idle Air Control (IAC) valve (located on underside of throttle body)
4. Exhaust Gas Recirculation (EGR) solenoid
10. Camshaft Position (CMP) sensor (located inside distributor)
5. Throttle Position (TP) sensor
~11. Engine Coolant Temperature (ECT) sensor
6. Exhaust Gas Recirculation (EGR) valve (located on underside of throttle body)
12. EVAP canister (located under fender)