NISSAN TERRANO 2004 Service Repair Manual
Manufacturer: NISSAN, Model Year: 2004, Model line: TERRANO, Model: NISSAN TERRANO 2004Pages: 1833, PDF Size: 53.42 MB
Page 141 of 1833
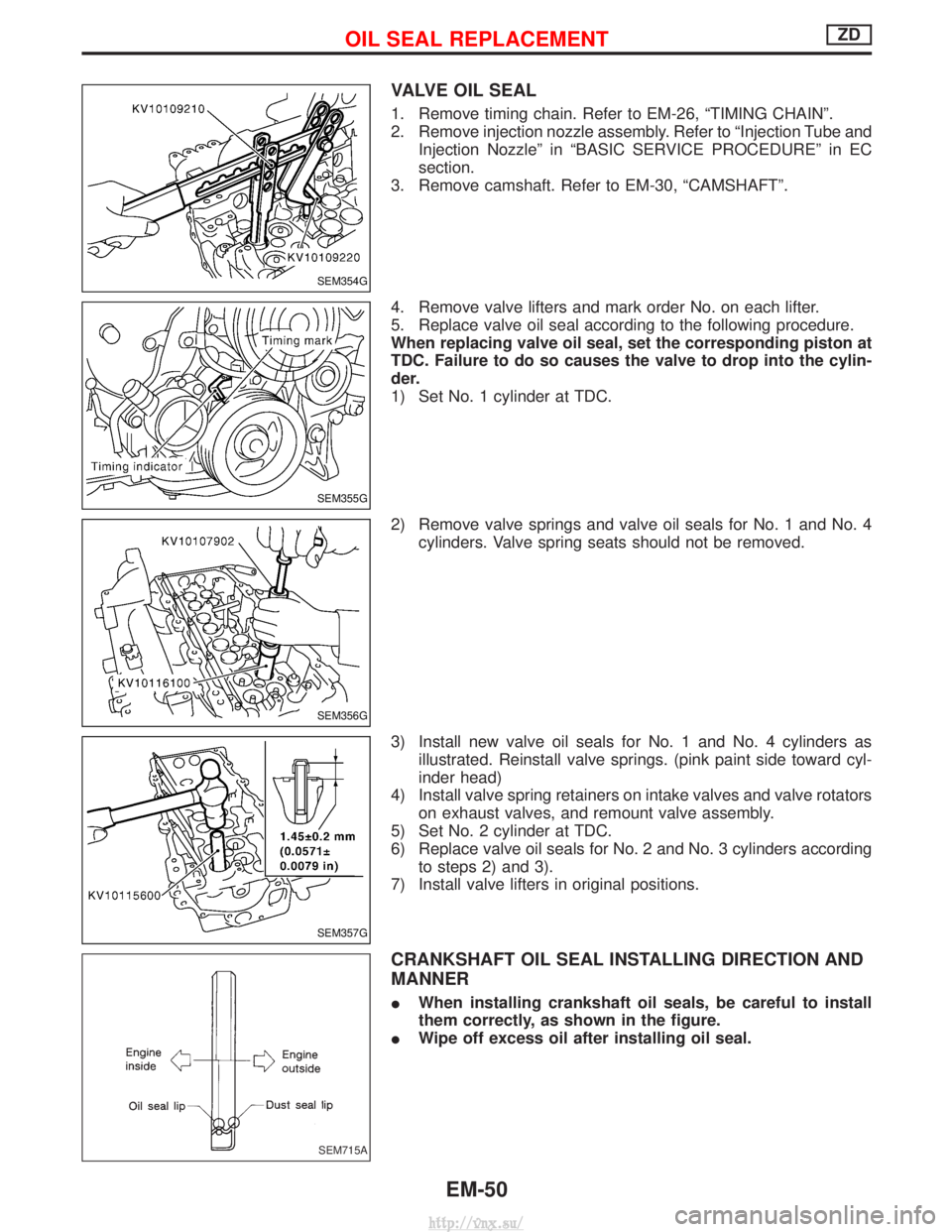
VALVE OIL SEAL
1. Remove timing chain. Refer to EM-26, ªTIMING CHAINº.
2. Remove injection nozzle assembly. Refer to ªInjection Tube andInjection Nozzleº in ªBASIC SERVICE PROCEDUREº in EC
section.
3. Remove camshaft. Refer to EM-30, ªCAMSHAFTº.
4. Remove valve lifters and mark order No. on each lifter.
5. Replace valve oil seal according to the following procedure.
When replacing valve oil seal, set the corresponding piston at
TDC. Failure to do so causes the valve to drop into the cylin-
der.
1) Set No. 1 cylinder at TDC.
2) Remove valve springs and valve oil seals for No. 1 and No. 4 cylinders. Valve spring seats should not be removed.
3) Install new valve oil seals for No. 1 and No. 4 cylinders as illustrated. Reinstall valve springs. (pink paint side toward cyl-
inder head)
4) Install valve spring retainers on intake valves and valve rotators on exhaust valves, and remount valve assembly.
5) Set No. 2 cylinder at TDC.
6) Replace valve oil seals for No. 2 and No. 3 cylinders according to steps 2) and 3).
7) Install valve lifters in original positions.
CRANKSHAFT OIL SEAL INSTALLING DIRECTION AND
MANNER
I When installing crankshaft oil seals, be careful to install
them correctly, as shown in the figure.
I Wipe off excess oil after installing oil seal.
SEM354G
SEM355G
SEM356G
SEM357G
SEM715A
OIL SEAL REPLACEMENTZD
EM-50
http://vnx.su/
Page 142 of 1833
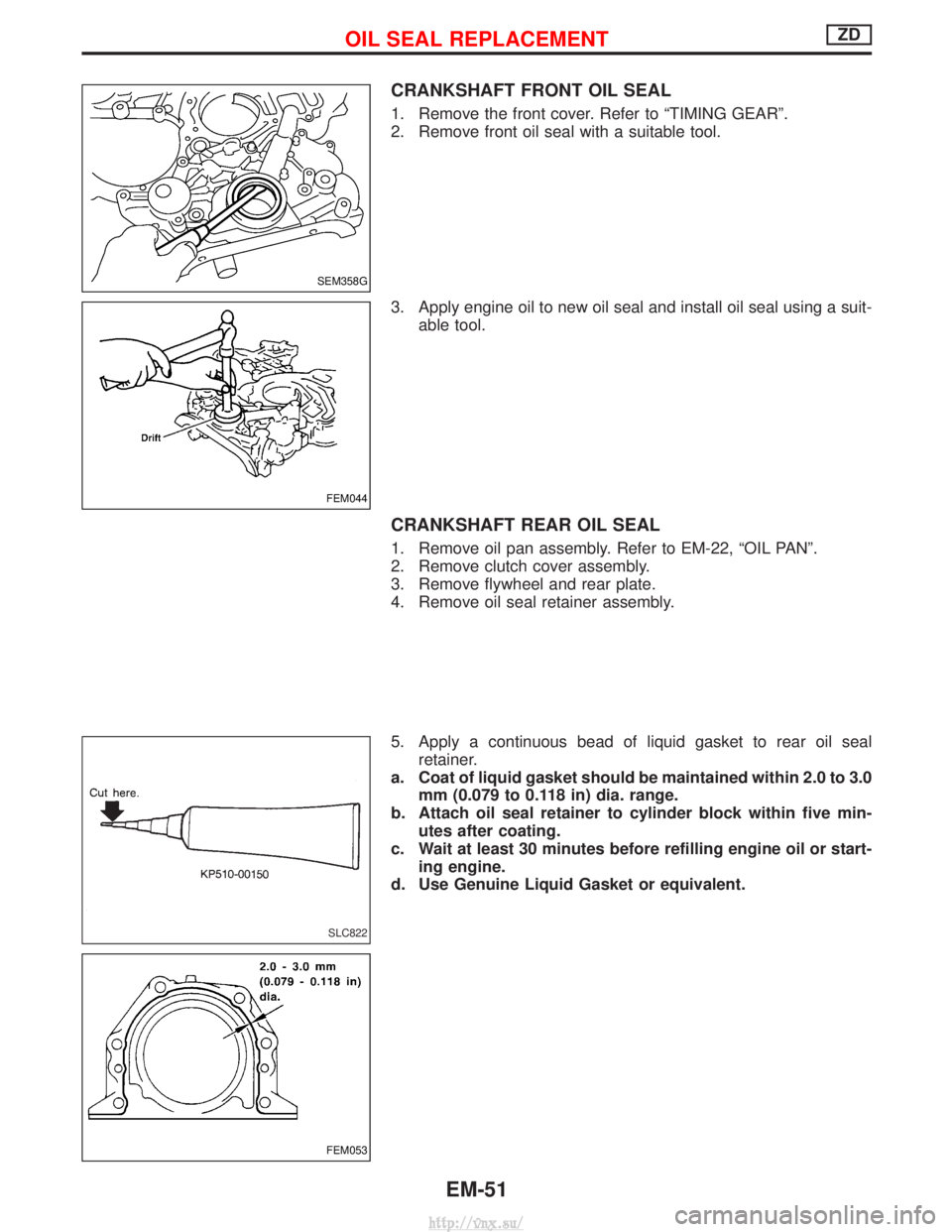
CRANKSHAFT FRONT OIL SEAL
1. Remove the front cover. Refer to ªTIMING GEARº.
2. Remove front oil seal with a suitable tool.
3. Apply engine oil to new oil seal and install oil seal using a suit-able tool.
CRANKSHAFT REAR OIL SEAL
1. Remove oil pan assembly. Refer to EM-22, ªOIL PANº.
2. Remove clutch cover assembly.
3. Remove flywheel and rear plate.
4. Remove oil seal retainer assembly.
5. Apply a continuous bead of liquid gasket to rear oil sealretainer.
a. Coat of liquid gasket should be maintained within 2.0 to 3.0 mm (0.079 to 0.118 in) dia. range.
b. Attach oil seal retainer to cylinder block within five min- utes after coating.
c. Wait at least 30 minutes before refilling engine oil or start- ing engine.
d. Use Genuine Liquid Gasket or equivalent.
SEM358G
FEM044
SLC822
FEM053
OIL SEAL REPLACEMENTZD
EM-51
http://vnx.su/
Page 143 of 1833
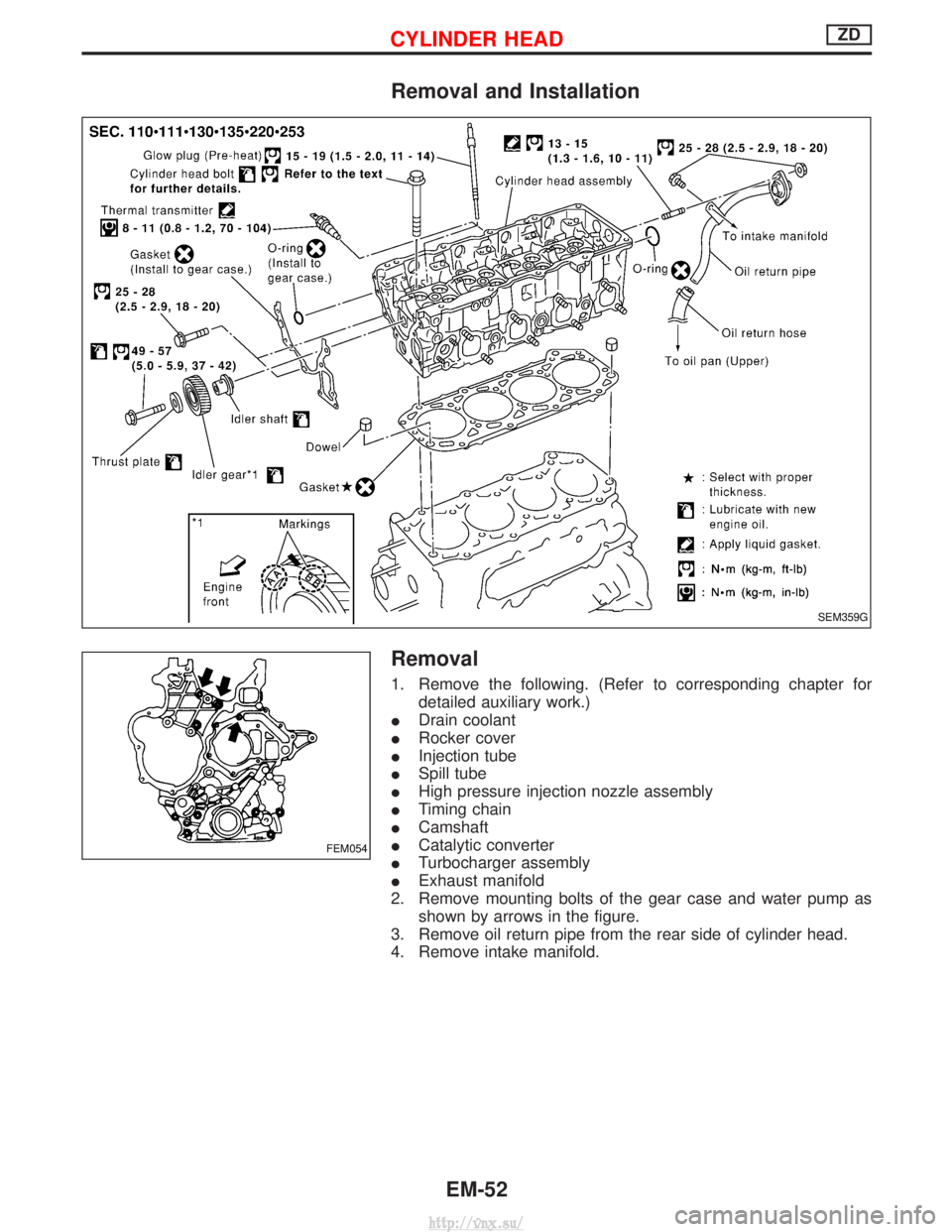
Removal and Installation
Removal
1. Remove the following. (Refer to corresponding chapter fordetailed auxiliary work.)
I Drain coolant
I Rocker cover
I Injection tube
I Spill tube
I High pressure injection nozzle assembly
I Timing chain
I Camshaft
I Catalytic converter
I Turbocharger assembly
I Exhaust manifold
2. Remove mounting bolts of the gear case and water pump as shown by arrows in the figure.
3. Remove oil return pipe from the rear side of cylinder head.
4. Remove intake manifold.
SEM359G
FEM054
CYLINDER HEADZD
EM-52
http://vnx.su/
Page 144 of 1833
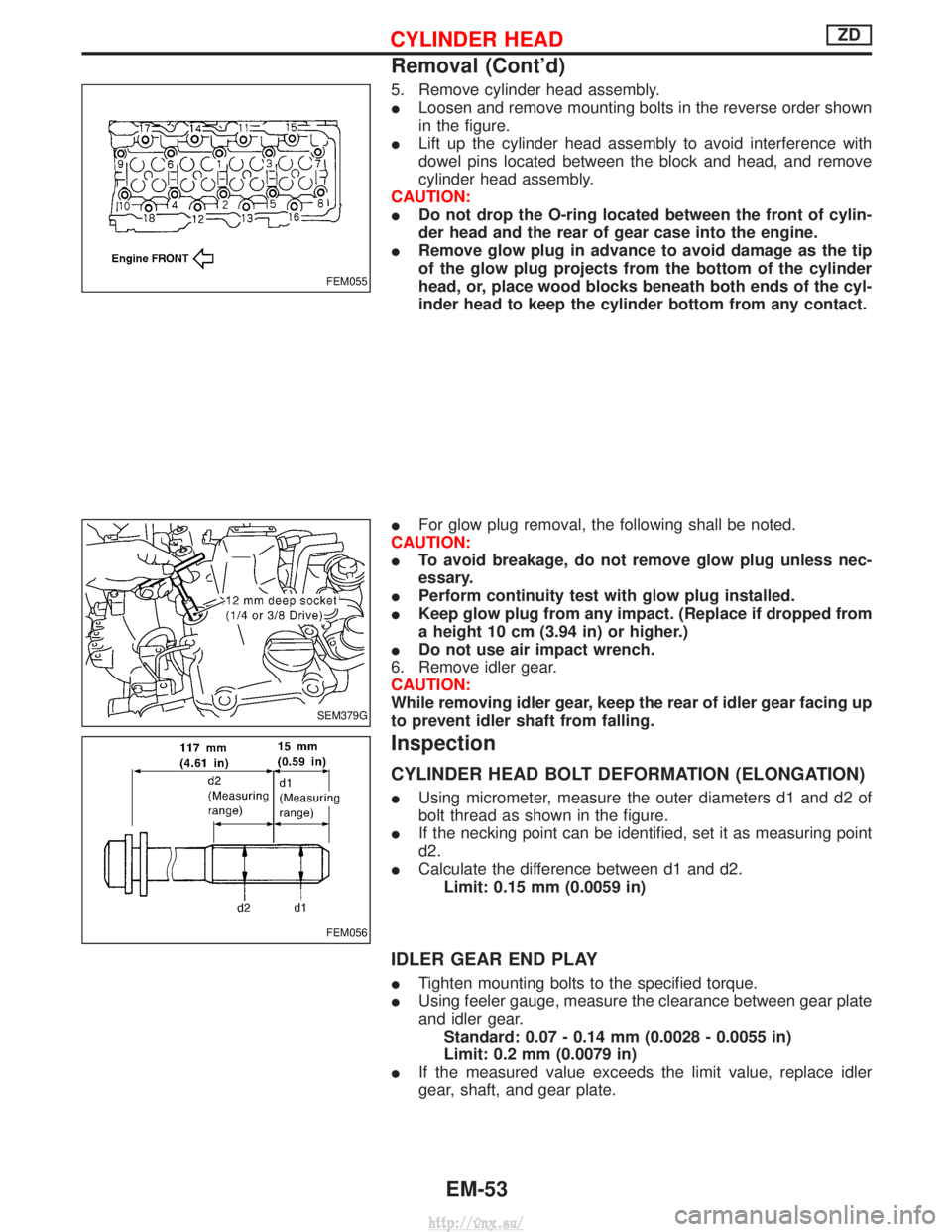
5. Remove cylinder head assembly.
ILoosen and remove mounting bolts in the reverse order shown
in the figure.
I Lift up the cylinder head assembly to avoid interference with
dowel pins located between the block and head, and remove
cylinder head assembly.
CAUTION:
I Do not drop the O-ring located between the front of cylin-
der head and the rear of gear case into the engine.
I Remove glow plug in advance to avoid damage as the tip
of the glow plug projects from the bottom of the cylinder
head, or, place wood blocks beneath both ends of the cyl-
inder head to keep the cylinder bottom from any contact.
I For glow plug removal, the following shall be noted.
CAUTION:
I To avoid breakage, do not remove glow plug unless nec-
essary.
I Perform continuity test with glow plug installed.
I Keep glow plug from any impact. (Replace if dropped from
a height 10 cm (3.94 in) or higher.)
I Do not use air impact wrench.
6. Remove idler gear.
CAUTION:
While removing idler gear, keep the rear of idler gear facing up
to prevent idler shaft from falling.
Inspection
CYLINDER HEAD BOLT DEFORMATION (ELONGATION)
I Using micrometer, measure the outer diameters d1 and d2 of
bolt thread as shown in the figure.
I If the necking point can be identified, set it as measuring point
d2.
I Calculate the difference between d1 and d2.
Limit: 0.15 mm (0.0059 in)
IDLER GEAR END PLAY
I Tighten mounting bolts to the specified torque.
I Using feeler gauge, measure the clearance between gear plate
and idler gear.
Standard: 0.07 - 0.14 mm (0.0028 - 0.0055 in)
Limit: 0.2 mm (0.0079 in)
I If the measured value exceeds the limit value, replace idler
gear, shaft, and gear plate.
FEM055
SEM379G
FEM056
CYLINDER HEADZD
Removal (Cont'd)
EM-53
http://vnx.su/
Page 145 of 1833
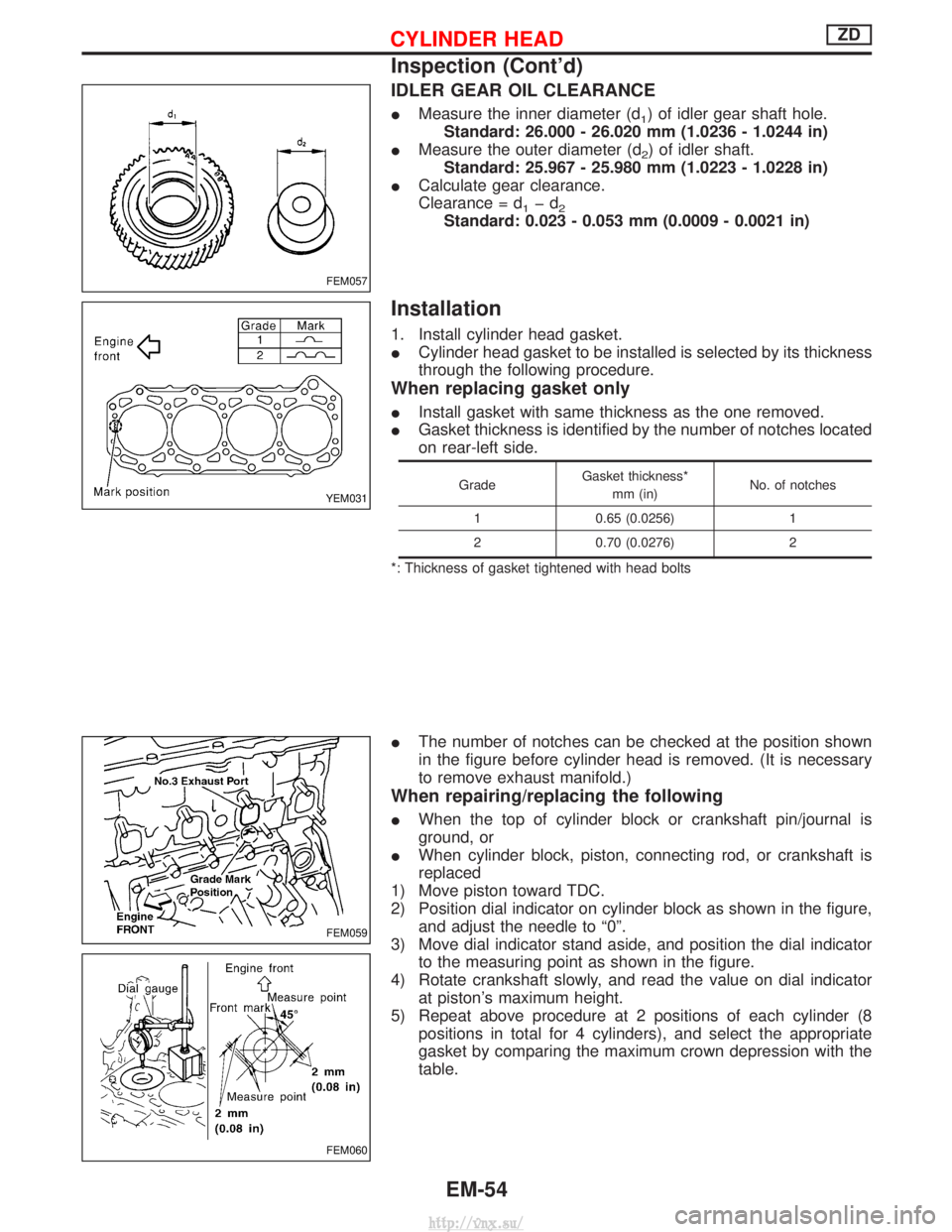
IDLER GEAR OIL CLEARANCE
IMeasure the inner diameter (d1) of idler gear shaft hole.
Standard: 26.000 - 26.020 mm (1.0236 - 1.0244 in)
I Measure the outer diameter (d
2) of idler shaft.
Standard: 25.967 - 25.980 mm (1.0223 - 1.0228 in)
I Calculate gear clearance.
Clearance = d
1þd2Standard: 0.023 - 0.053 mm (0.0009 - 0.0021 in)
Installation
1. Install cylinder head gasket.
ICylinder head gasket to be installed is selected by its thickness
through the following procedure.
When replacing gasket only
IInstall gasket with same thickness as the one removed.
I Gasket thickness is identified by the number of notches located
on rear-left side.
Grade Gasket thickness*
mm (in) No. of notches
1 0.65 (0.0256) 1
2 0.70 (0.0276) 2
*: Thickness of gasket tightened with head bolts
I The number of notches can be checked at the position shown
in the figure before cylinder head is removed. (It is necessary
to remove exhaust manifold.)
When repairing/replacing the following
IWhen the top of cylinder block or crankshaft pin/journal is
ground, or
I When cylinder block, piston, connecting rod, or crankshaft is
replaced
1) Move piston toward TDC.
2) Position dial indicator on cylinder block as shown in the figure, and adjust the needle to ª0º.
3) Move dial indicator stand aside, and position the dial indicator to the measuring point as shown in the figure.
4) Rotate crankshaft slowly, and read the value on dial indicator at piston's maximum height.
5) Repeat above procedure at 2 positions of each cylinder (8 positions in total for 4 cylinders), and select the appropriate
gasket by comparing the maximum crown depression with the
table.
FEM057
YEM031
FEM059
FEM060
CYLINDER HEADZD
Inspection (Cont'd)
EM-54
http://vnx.su/
Page 146 of 1833
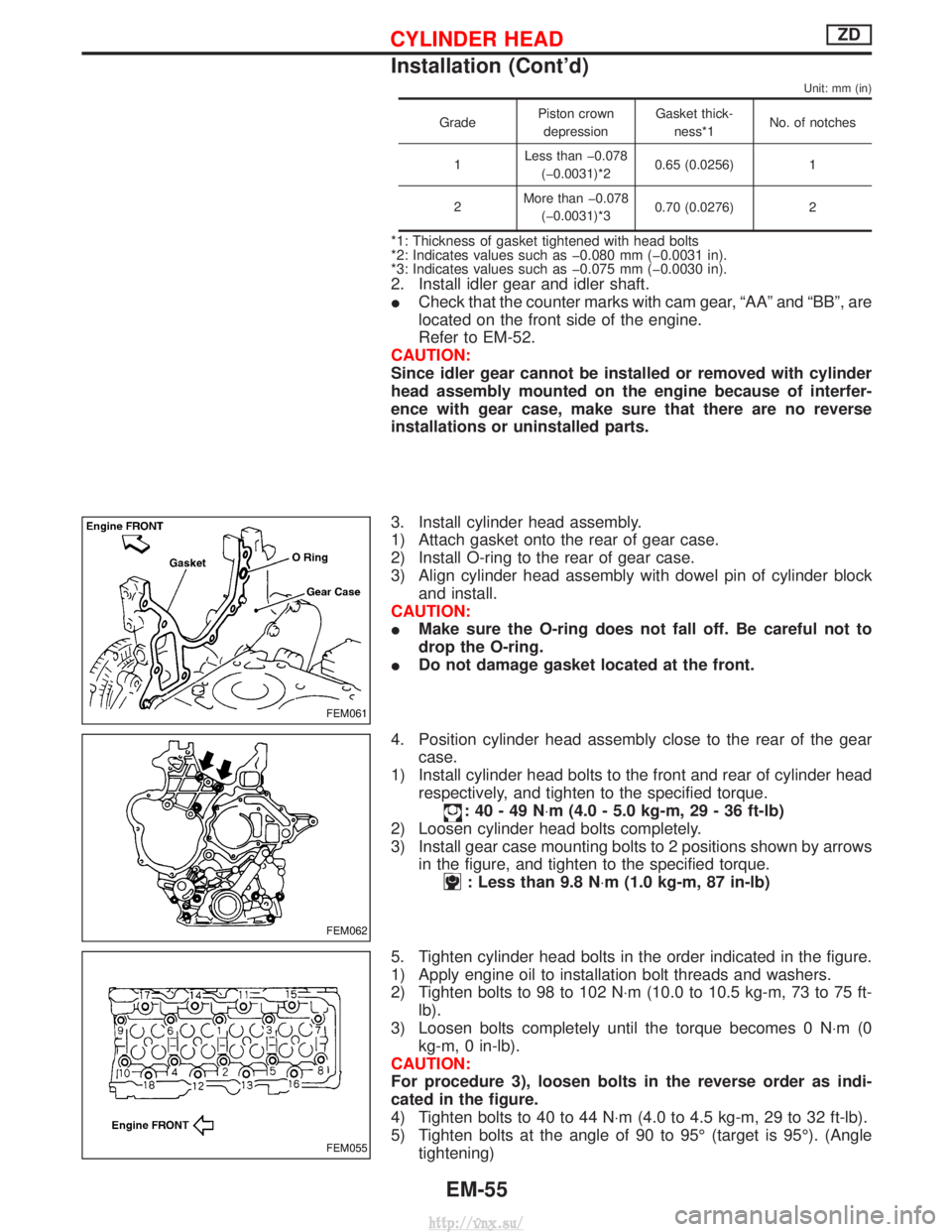
Unit: mm (in)
GradePiston crown
depression Gasket thick-
ness*1 No. of notches
1 Less than þ0.078
(þ0.0031)*2 0.65 (0.0256) 1
2 More than þ0.078
(þ0.0031)*3 0.70 (0.0276) 2
*1: Thickness of gasket tightened with head bolts
*2: Indicates values such as þ0.080 mm (þ0.0031 in).
*3: Indicates values such as þ0.075 mm (þ0.0030 in).
2. Install idler gear and idler shaft.
I
Check that the counter marks with cam gear, ªAAº and ªBBº, are
located on the front side of the engine.
Refer to EM-52.
CAUTION:
Since idler gear cannot be installed or removed with cylinder
head assembly mounted on the engine because of interfer-
ence with gear case, make sure that there are no reverse
installations or uninstalled parts.
3. Install cylinder head assembly.
1) Attach gasket onto the rear of gear case.
2) Install O-ring to the rear of gear case.
3) Align cylinder head assembly with dowel pin of cylinder block and install.
CAUTION:
I Make sure the O-ring does not fall off. Be careful not to
drop the O-ring.
I Do not damage gasket located at the front.
4. Position cylinder head assembly close to the rear of the gear case.
1) Install cylinder head bolts to the front and rear of cylinder head respectively, and tighten to the specified torque.
:40-49N ×m (4.0 - 5.0 kg-m, 29 - 36 ft-lb)
2) Loosen cylinder head bolts completely.
3) Install gear case mounting bolts to 2 positions shown by arrows in the figure, and tighten to the specified torque.
: Less than 9.8 N ×m (1.0 kg-m, 87 in-lb)
5. Tighten cylinder head bolts in the order indicated in the figure.
1) Apply engine oil to installation bolt threads and washers.
2) Tighten bolts to 98 to 102 N×m (10.0 to 10.5 kg-m, 73 to 75 ft- lb).
3) Loosen bolts completely until the torque becomes 0 N ×m(0
kg-m, 0 in-lb).
CAUTION:
For procedure 3), loosen bolts in the reverse order as indi-
cated in the figure.
4) Tighten bolts to 40 to 44 N ×m (4.0 to 4.5 kg-m, 29 to 32 ft-lb).
5) Tighten bolts at the angle of 90 to 95É (target is 95É). (Angle tightening)
FEM061
FEM062
FEM055
CYLINDER HEADZD
Installation (Cont'd)
EM-55
http://vnx.su/
Page 147 of 1833
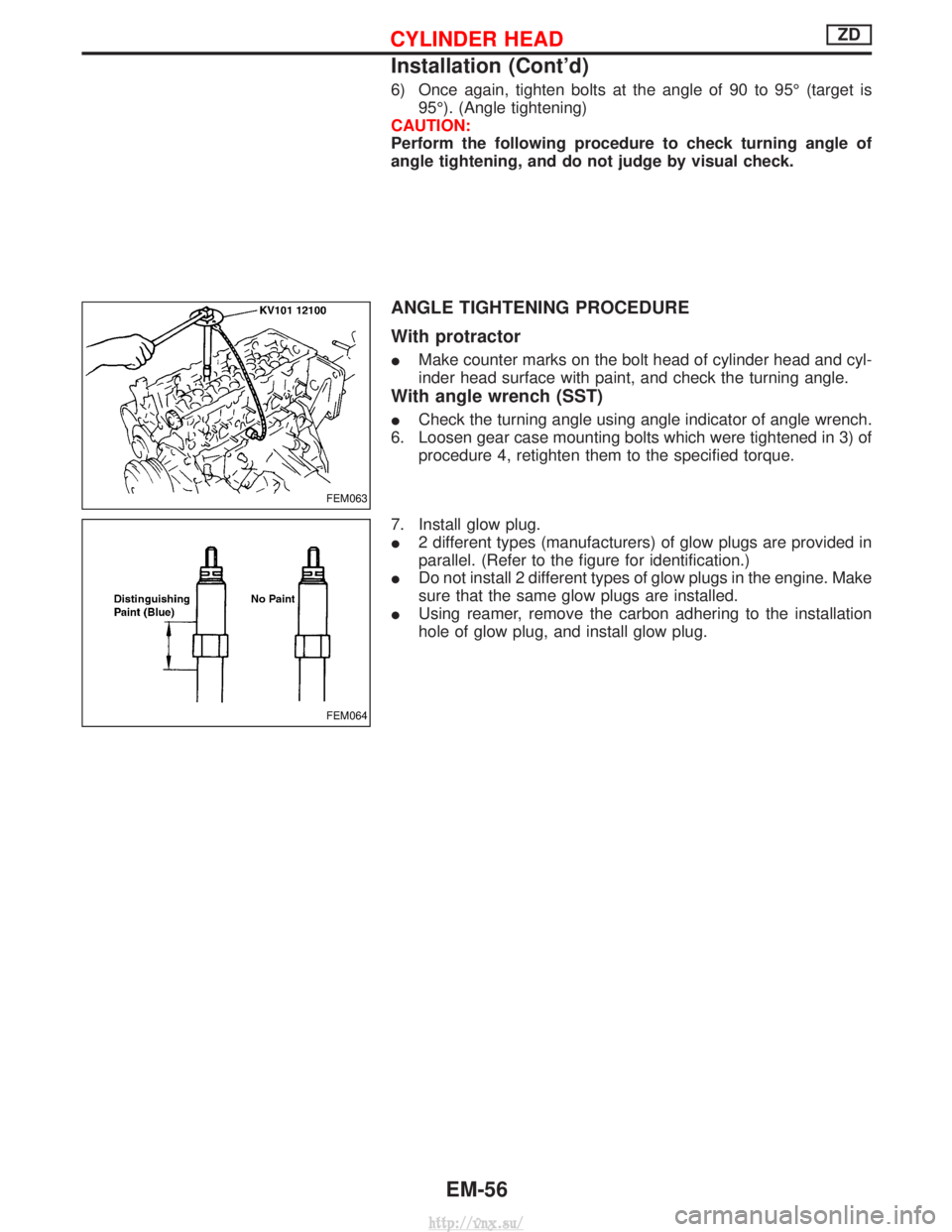
6) Once again, tighten bolts at the angle of 90 to 95É (target is95É). (Angle tightening)
CAUTION:
Perform the following procedure to check turning angle of
angle tightening, and do not judge by visual check.
ANGLE TIGHTENING PROCEDURE
With protractor
I Make counter marks on the bolt head of cylinder head and cyl-
inder head surface with paint, and check the turning angle.
With angle wrench (SST)
ICheck the turning angle using angle indicator of angle wrench.
6. Loosen gear case mounting bolts which were tightened in 3) of procedure 4, retighten them to the specified torque.
7. Install glow plug.
I 2 different types (manufacturers) of glow plugs are provided in
parallel. (Refer to the figure for identification.)
I Do not install 2 different types of glow plugs in the engine. Make
sure that the same glow plugs are installed.
I Using reamer, remove the carbon adhering to the installation
hole of glow plug, and install glow plug.
FEM063
FEM064
CYLINDER HEADZD
Installation (Cont'd)
EM-56
http://vnx.su/
Page 148 of 1833

8. Install oil return pipe to the rear side of the cylinder head.
IWhen reinstalling a stud bolt, apply Three Bond 1207C (KP510
00150) to the thread of the bolt.
Disassembly
1. Remove adjusting shims and valve lifters.
Check the installation positions, and keep them to avoid being
confused.
2. Using valve spring compressor (SST), compress valve spring. Using magnetic hand, remove valve collets.
3. Remove valve spring retainers and valve springs.
4. Remove valves as pressing valve stems toward combustion chamber.
I Before removing the valve, check the valve guide clearance.
(Refer to EM-58.)
I Check installation positions, and keep them to avoid being con-
fused.
I Refer to the figure for intake/exhaust valve positions. (Intake
and exhaust valve driving cams are provided alternately for
each camshaft.)
FEM081
SEM361G
FEM010
CYLINDER HEADZD
Installation (Cont'd)
EM-57
http://vnx.su/
Page 149 of 1833
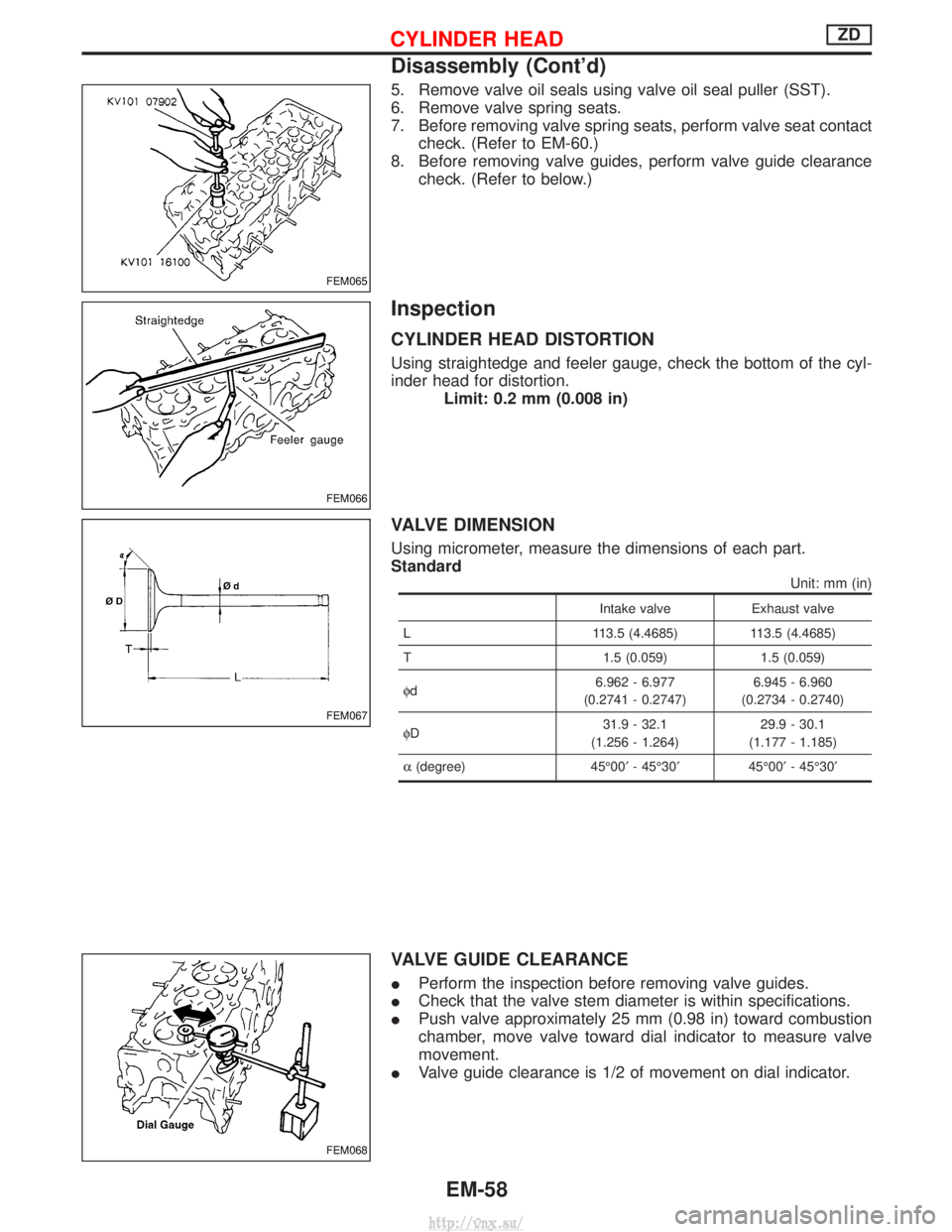
5. Remove valve oil seals using valve oil seal puller (SST).
6. Remove valve spring seats.
7. Before removing valve spring seats, perform valve seat contactcheck. (Refer to EM-60.)
8. Before removing valve guides, perform valve guide clearance check. (Refer to below.)
Inspection
CYLINDER HEAD DISTORTION
Using straightedge and feeler gauge, check the bottom of the cyl-
inder head for distortion. Limit: 0.2 mm (0.008 in)
VALVE DIMENSION
Using micrometer, measure the dimensions of each part.
Standard
Unit: mm (in)
Intake valve Exhaust valve
L 113.5 (4.4685)113.5 (4.4685)
T 1.5 (0.059)1.5 (0.059)
f d 6.962 - 6.977
(0.2741 - 0.2747) 6.945 - 6.960
(0.2734 - 0.2740)
f D 31.9 - 32.1
(1.256 - 1.264) 29.9 - 30.1
(1.177 - 1.185)
a (degree) 45É00¢- 45É30¢ 45É00¢- 45É30¢
VALVE GUIDE CLEARANCE
IPerform the inspection before removing valve guides.
I Check that the valve stem diameter is within specifications.
I Push valve approximately 25 mm (0.98 in) toward combustion
chamber, move valve toward dial indicator to measure valve
movement.
I Valve guide clearance is 1/2 of movement on dial indicator.
FEM065
FEM066
FEM067
FEM068
CYLINDER HEADZD
Disassembly (Cont'd)
EM-58
http://vnx.su/
Page 150 of 1833
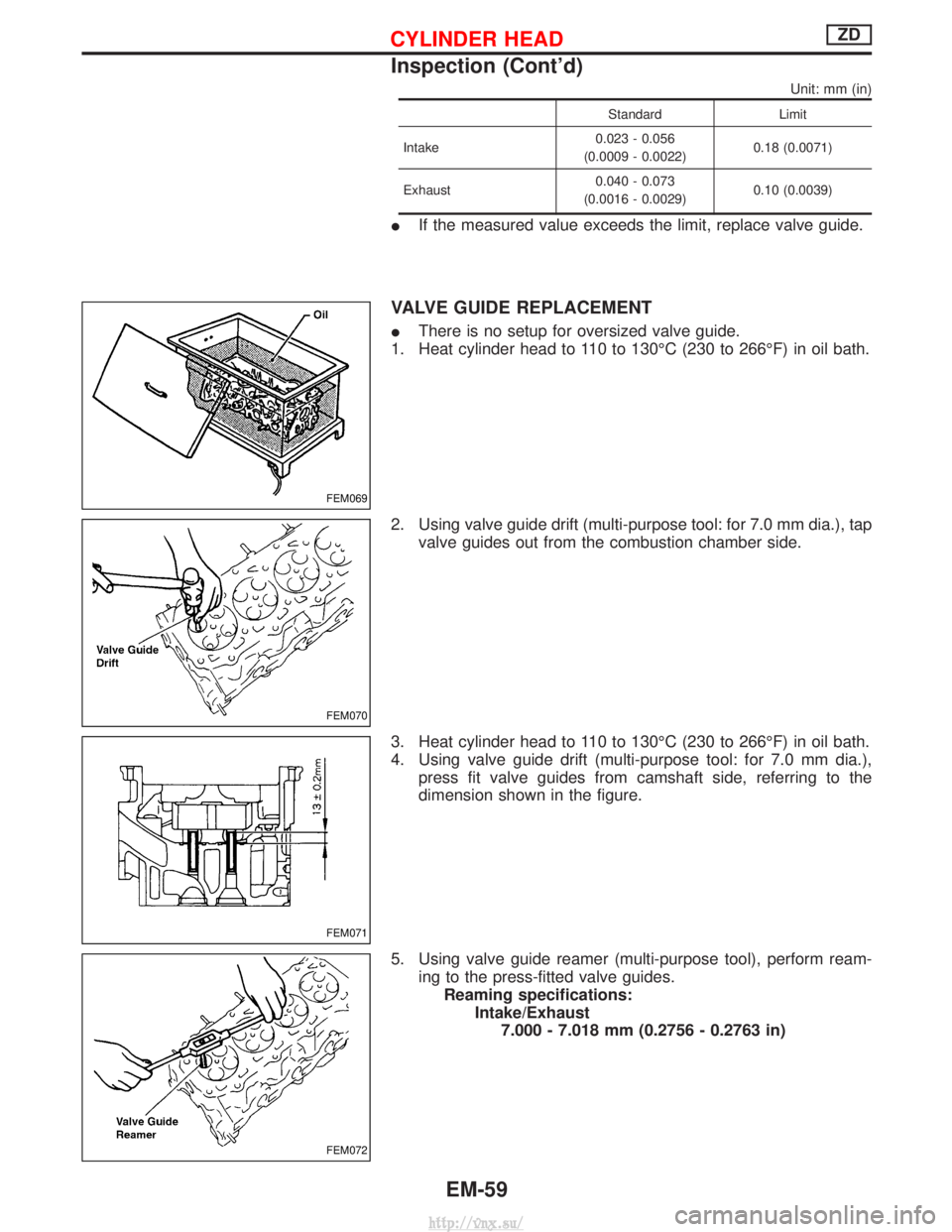
Unit: mm (in)
StandardLimit
Intake 0.023 - 0.056
(0.0009 - 0.0022) 0.18 (0.0071)
Exhaust 0.040 - 0.073
(0.0016 - 0.0029) 0.10 (0.0039)
I
If the measured value exceeds the limit, replace valve guide.
VALVE GUIDE REPLACEMENT
IThere is no setup for oversized valve guide.
1. Heat cylinder head to 110 to 130ÉC (230 to 266ÉF) in oil bath.
2. Using valve guide drift (multi-purpose tool: for 7.0 mm dia.), tap valve guides out from the combustion chamber side.
3. Heat cylinder head to 110 to 130ÉC (230 to 266ÉF) in oil bath.
4. Using valve guide drift (multi-purpose tool: for 7.0 mm dia.), press fit valve guides from camshaft side, referring to the
dimension shown in the figure.
5. Using valve guide reamer (multi-purpose tool), perform ream- ing to the press-fitted valve guides.Reaming specifications: Intake/Exhaust7.000 - 7.018 mm (0.2756 - 0.2763 in)
FEM069
FEM070
FEM071
FEM072
CYLINDER HEADZD
Inspection (Cont'd)
EM-59
http://vnx.su/